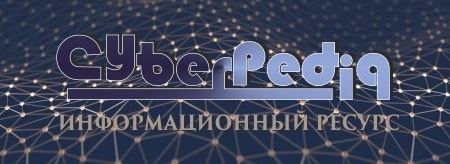
Организация стока поверхностных вод: Наибольшее количество влаги на земном шаре испаряется с поверхности морей и океанов (88‰)...
Папиллярные узоры пальцев рук - маркер спортивных способностей: дерматоглифические признаки формируются на 3-5 месяце беременности, не изменяются в течение жизни...
Топ:
Оценка эффективности инструментов коммуникационной политики: Внешние коммуникации - обмен информацией между организацией и её внешней средой...
Особенности труда и отдыха в условиях низких температур: К работам при низких температурах на открытом воздухе и в не отапливаемых помещениях допускаются лица не моложе 18 лет, прошедшие...
Определение места расположения распределительного центра: Фирма реализует продукцию на рынках сбыта и имеет постоянных поставщиков в разных регионах. Увеличение объема продаж...
Интересное:
Лечение прогрессирующих форм рака: Одним из наиболее важных достижений экспериментальной химиотерапии опухолей, начатой в 60-х и реализованной в 70-х годах, является...
Национальное богатство страны и его составляющие: для оценки элементов национального богатства используются...
Отражение на счетах бухгалтерского учета процесса приобретения: Процесс заготовления представляет систему экономических событий, включающих приобретение организацией у поставщиков сырья...
Дисциплины:
![]() |
![]() |
5.00
из
|
Заказать работу |
Содержание книги
Поиск на нашем сайте
|
|
В солоде определяют растворение (разрыхление структуры зерна) различными методами; влажность, содержание экстракта и продолжительность осахаривания; кислотность, растворимые углеводы и крахмал; пентозаны; диастатическую силу (ДС), общий и формольнотитруемый азот.
В лабораторном сусле, полученном по стандартному методу, определяют качество фильтрата, плотность, цветность, содержание мальтозы, сахарозы, декстринов, конечную степень сбраживания, белковые вещества, разделение азота на фракции по Лундину, кислотность, вязкость.
В солодах, применяемых для подкраски (жженом и карамельном), определяют влажность, экстрактивность и показатель цветности.
ГЛАВА V
ПОЛУЧЕНИЕ СУСЛА
Для изготовления пивного сусла используются ячменный солод, несоложеные материалы - ячменная и кукурузная мука, рисовая сечка и хмель.
Весь процесс получения пивного сусла состоит из следующих технологических операций:
1) подготовка и дробление ячменного солода;
2) затирание солода и несоложеных материалов с водой;
3) осахаривание затора;
4) фильтрация сусла;
5) кипячение и охмеление сусла.
Все эти операции проводятся на специальном оборудовании, установленном в варочном цехе пивоваренного завода.
ОСНОВНОЕ ТЕХНОЛОГИЧЕСКОЕ ОБОРУДОВАНИЕ ВАРОЧНЫХ ЦЕХОВ
Варочные цехи пивоваренных заводов располагаются в многоэтажных зданиях, и аппаратура в них размещается с таким расчетом, чтобы обеспечить передачу жидкостей и сыпучих материалов на всех технологических операциях самотеком и свести к минимуму протяженность паро- и суслопроводов.
Варочный цех по комплексу самостоятельных технологических операций делится на два отделения:
|
1) дробильное, где подготовляется и дробится солод;
2) варочное, где проводится затирание солода и несоложеных материалов, осахаривание затора, фильтрация сусла, кипячение его с хмелем и отделение от хмеля.
Дробильное отделение
Готовый отлежавшийся солод, несмотря на очистку его в солодовне перед складированием для хранения, содержит некоторое количество пыли, остатков ростков, неполноценных зерен и случайно попавшие металлические предметы.
Окончательная очистка солода проводится на полировочных машинах и магнитных аппаратах. После полировки солод имеет более чистый вид, а экстрактивность его незначительно (на 0,5%) повышается. Очищенный солод взвешивают и передают на дробилки.
Полировочная машина, магнитный аппарат, весы и дробилки находятся в дробильном отделении, расположенном над варочным цехом.
Полировочная машина (рис. 58). Основные части машины: сотрясательные сита, вращающийся барабан со щетками, рифленая дека и отсасывающий вентилятор.
Солод из приемной коробки полировочной машины поступает вначале на первое крупное сотрясательное сито. Зерно проходит через сито и попадает на второе, более мелкое сотрясательное сито. На первом сите задерживаются крупные примеси - камешки, обрывки веревок и т. д., которые сходом удаляются с сита. На втором сите задерживается солод, а через сито просыпаются в ситовую коробку мелкие примеси и пыль, отсасываемая вентилятором.
Солод со второго сотрясательного сита сходом сыплется на быстро вращающийся щеточный барабан. Зерно увлекается щетками, затем отбрасывается на рифленую поверхность деки и под действием ударов и трения очищается от загрязнений - полируется. Полированный солод падает в расширенную нижнюю часть полировочной машины и направляется к выходу. Потоком воздуха, всасываемого вентилятором, полированный солод очищается от остатков пыли.
Воздух из полировочной машины для удаления пыли направляют в пылевые фильтры и камеры или циклоны.
|
Полированный солод транспортируют в бункер. Из бункера он поступает на магнитные аппараты для очистки от ферропримесей и затем на автоматические весы для взвешивания.
Автоматические весы. На пивоваренных заводах наиболее распространены весы с отвешиванием солода порциями по 10 или 20 кг типа «Хронос». Они имеют специальный ковш с соответствующим противовесом. При наполнении солодом ковш опрокидывается и зерно высыпается. В последнее время выпускаются ковшовые автоматические весы марки Д, отличающиеся по конструкции от весов «Хронос». Весы Д имеют подвешенный на стальной проволоке ковш с автоматически открывающимся дном. Емкость ковша от 20 до 500 кг.
Схема весов изображена на рис. 59. К двойному равноплечему коромыслу I подвешены гиредержатели 2 и ковш 3 с открывающимся дном 4. Над ковшом неподвижно закреплена воронка 5, нижнее отверстие которой закрывается заслонкой 6. Дно ковша 4 может поворачиваться вокруг оси 7. С одной стороны его (по рисунку-слева) имеется противовес 8, который закрывает дно после опорожнения ковша. Справа от оси на дне укреплен крючок 9, который заходит выступом за выступ собачки 10 и удерживает дно при заполнении ковша. Собачка сидит на оси 11, закрепленной на боковой стенке ковша.
Работают весы следующим образом.
При наполнении ковша взвешиваемым продуктом заслонка 6 открыта и удерживается в этом положении специальным механизмом (не показанным на рисунке). Из воронки 5 продукт течет в ковш весов и заставляет его постепенно опускаться (см, рис. 59, а). Когда установится равновесие между ковшом и гиредержателем, последний воздействует на механизм, удерживающий заслонку 6 она падает и прекращает наполнение ковша (см. рис. 59, б).
По инерции ковш продолжает опускаться; при этом собачка 10 левым концом упирается в неподвижный выступ станины (на рисунке не показан) и выходит из зацепления с крючком 9. После этого дно ковша открывается и продукт высыпается из ковша (см. рис. 59, в). Когда весь продукт высыпется, противовес 8 закрывает дно ковша и крючок 9 снова входит в зацепление с собачкой 10. Одновременно пустой ковш поднимается и открывает заслонку 6. Начинается заполнение ковша снова.
Взвешенное зерно поступает в приемный бункер солодовой дробилки.
Солодовая дробилка. В пивоваренном производстве применяются вальцовые дробилки. В зависимости от числа вальцов дробилки бывают двух-, трех-, четырех-, пяти- и шестивальцовые. Вальцы могут быть гладкие и рифленые.
|
В настоящее время начинают применять так называемые ударные дробилки, работающие на принципе соударения зерен и ударов зерна о стенку центробежного барабана и отражательные поверхности корпуса мельницы.
Дробилка имеет приводной механизм и регулирующие помол приспособления.
Четырех- и шестивальцовые дробилки имеют сита для разделения помола на фракции.
Двухвальцовая дробилка. Эта дробилка самая простая по устройству. Она имеет два вальца одного диаметра (250- 350 мм), заключенные в кожух. Число оборотов вальцов 180- 240 в минуту. Качество помола регулируется изменением зазора между вальцами. На двухвальцовой дробилке нельзя получить дифференцированного помола - крупнодробленную мякинную оболочку и мелкодробленное мучнистое тело. Удовлетворительный помол получается только из очень хорошо растворенного солода.
Четырехвальцовая дробилка. Дробилка снабжена двумя парами основных вальцов одинакового диаметра. Над верхними вальцами в нижней части приемного ковша расположены рифленый распределительный валик и наклонный распределительный желобчатый щиток, по которому солод направляется на верхние вальцы.
С первой пары вальцов дробленый солод поступает в промежуточную камеру над второй парой вальцов. В ней имеются две пары быстро вращающихся крыльчатых валиков; солод, попадая на них, отбрасывается к стенкам. Под влиянием ударов из размятой шелухи выбиваются крупка и мука. Происходит некоторое отделение шелухи. Из промежуточной камеры солод попадает на вторую пару вальцов, где окончательно дробится до желаемой тонкости помола.
В четырехвальцовой дробилке верхние вальцы имеют число оборотов 200, а нижние - 300 в минуту. При одинаковом числе оборотов верхних и нижних вальцов возможна перегрузка нижних вальцов, и помол будет неравномерным.
Регулирование тонкости помола достигается изменением зазора между вальцами.
Верхние вальцы обычно дают помол следующего состава (в %): шелухи 30-36, крупки 50-58, муки 16-20. Состав помола на второй паре вальцов: шелухи 20, крупки 60 и муки 20%.
|
В корпусе дробилки имеются отверстия для отбора проб из под каждой пары вальцов.
Более совершенна четырехвальцовая дробилка с межвальцовыми ситами.
Солод после дробления на первой паре вальцов попадает на сотрясательные сита, расположенные между верхней и нижней парой вальцов. На ситах дробленый солод разделяется на две фракции:
1) шелуха и крупная крупка и
2) мелкая крупка и мука.
Шелуха и крупка сходом с сит направляются на вторые вальцы, а мука проходит через сита и направляется прямо в приемный бункер для дробленого солода.
Шестивальцовая дробилка (рис. 60). Дробилка имеет три пары вальцов и два постава сит 4 и 5.
На верхних вальцах 1 солод подвергается грубому дроблению, после чего попадает на постав с двумя сотрясательными ситами 4.
Мука проходит через оба сита и по дну подситовой коробки отводится в бункер готового дробленого солода. Шелуха и крупнодробленая часть солода сходом с первого сита попадают на вторую пару вальцов 2. Крупка задерживается вторым ситом и сходом с него отводится на третье сито второго постава 5. На третье сито поступает также весь дробленый солод со второй пары вальцов.
На третьем сите от помола отделяется шелуха и сходом поступает прямо в бункер дробленого солода, минуя третью пару вальцов 3.
Просеявшаяся через третье сито крупка попадает на четвертое сито. Здесь отсеивается мука, которая по дну ситовой коробки направляется в бункер готового солода, а оставшаяся на сите крупка сходом поступает на третью пару вальцов и дробится. Дробленая крупка с третьей пары вальцов присоединяется к остальным частям помола в бункере. Средний состав помола (в %), получаемый на шестивальцовой дробилке:
шелухи | |
грубой крупки | |
тонкой крупки | |
муки |
Дробильное отделение представляет опасность в пожарном отношении. Мучная солодовая пыль легко воспламеняется и при определенной критической концентрации ее в воздухе от искры может взрываться. Поэтому дробильное отделение изолируют от остальных и устанавливают в нем закрытые электровыключатели и рубильники, исключающие искрение.
При выборе дробилок в первую очередь исходят из масштаба производства; при этом принимается, что весь солод на один затор должен дробиться в течение 1-2 ч.
На мелких предприятиях средней мощности обычно устанавливали двух- и четырехвальцовые дробилки. В настоящее время двухвальцовые дробилки не используются. Шестивальцовые дробилки устанавливают на крупных пивоваренных заводах.
Дробление солода - весьма важная технологическая операция, так как от качества дробления солода зависят скорость осахаривания затора, выход экстракта, а также продолжительность фильтрации сусла.
|
В зависимости от степени дробления солода помол может быть грубым или тонким. Распределение отдельных фракций помола и их экстрактивность приводятся в табл. 41.
Таблица 41
Фракции помола | Содержание | Экстрактивность фракций | |
в % | в % к общему выходу | ||
Шелуха | 4,35 | 6,05 | |
Крупная крупка | 8,02 | 11,25 | |
Мелкая крупка | 23,10 | 32,50 | |
Мука | 35,74 | 50,20 | |
71,21 | 100,0 |
Приведенные в табл. 41 данные далеко не предельные: при более тонком помоле можно добиться увеличения выхода экстракта на 0,5% и более.
Повышение выхода экстракта солода зависит также от способа затирания. При выборе степени помола следует учитывать, на каком оборудовании проводится фильтрация сусла - в фильтрационном чане или на фильтрпрессе.
Как правило, мелкое дробление солода ускоряет процесс осахаривания солода, значительно увеличивает выход экстракта, но вместе с тем может сильно затруднить фильтрацию сусла, особенно при работе на фильтрационных чанах. Более крупное дробление всегда уменьшает выход экстракта, но заторы, полученные из крупнодробленого солода, лучше и быстрее фильтруются.
Так как выход экстракта зависит от того, насколько мелко раздроблен эндосперм солода, а скорость фильтрации от того, сколько осталось крупной мякинной оболочки, то при дроблении солода стремятся мелко раздробить эндосперм и оставить, по возможности, нераздробленной мякинную оболочку.
Однако и слишком мелкое дробление эндосперма (до муки) также нежелательно, так как в этом случае нерастворимые остатки тканей эндосперма создают слишком мелкую муть в заторе (так называемое тесто), что засоряет фильтрующий слой в фильтрационном чане и затрудняет фильтрацию сусла.
При дроблении сухого неотлежавшегося солода мякинная оболочка сильно измельчается. Поэтому солод, идущий на дробление, должен иметь около 5-6% влаги. При большей влажности солод также неудобно дробить, так как эндосперм теряет хрупкость, плющится между вальцами дробилки и не дает достаточно мелкого помола.
За последнее время для увлажнения мякинной оболочки без заметного увлажнения эндосперма практикуют кратковременное увлажнение поверхности солода перед дроблением распыленной водой на специальных увлажнительных машинах. При этом мякинная оболочка становится мягкой и эластичной и при дроблении солода не рвется, эндосперм же не успевает увлажниться, остается сухим и хрупким и дробится в мелкую крупку.
Осахаренный затор, полученный из увлажненного перед дроблением солода, имеет более грубую и рыхлую структуру и благодаря этому сусло легче отфильтровывается.
Дробленый солод, выходящий из дробилки, собирается в бункер для солода, а из него поступает самотеком в заторные чаны или котлы для затирания с водой и других операций.
Варочное отделение
В варочном отделении проводится затирание солода с горячей или теплой водой, осахаривание затора, отварка определенных частей затора, фильтрация сусла и кипячение его с хмелем. Эти операции проводятся в специальной аппаратуре в строго последовательном порядке и по определенному регламенту.
Водогрейный бак. Бак для горячей воды устанавливают над варочным отделением. На затирание в варочном отделении потребляется горячая вода температурой не ниже 50°, а для фильтрации затора - не ниже 75°С.
Емкость бака и поверхность нагрева в нем рассчитывают по расходу воды на затор, который в среднем составляет около 8 м3, а съем воды температурой 80ºC - не менее 4 м3/т на 1 т затираемого солода.
Аппаратура варочного отделения на пивоваренном заводе состоит из двух,- четырех- и шестипосудных емкостей, рассчитанных на единовременную засыпку 0,5; 1,5; 3 или 5,5 т зерно- припасов.
Четырехпосудный порядок состоит из заторного чана с паровым обогревом или без него; заторного котла; фильтрационного чана или фильтрпресса; сусловарочного котла.
В новых варочных агрегатах вместо заторного чана и заторного котла предусматриваются два котла одинакового объема.
Простейшим оборудованием варочного отделения является порядок, состоящий из двух посуд - заторно-фильтрационного чана (рис. 61) и сусловарочного котла, используемых в процессе затирания дважды, но с разным назначением.
Новейшее оборудование варочного отделения - это варочный порядок, состоящий из шести посуд: двух заторных котлов, двух фильтрационных чанов и двух сусловарочных котлов.
Это оборудование должно по объему соответствовать друг другу. Емкость его (в м3) определяется, исходя из расчета на 1 т затираемого солода: заторный чан, заторный котел и фильтрационный чан по 7-8 и сусловарочный котел - 8,0.
Старые заторные котлы имели емкость от 3,5 до 2,5 м3 на 1 т зерна.
Заторный чан. Чан (рис. 62) служит для затирания солода с водой и осахаривания затора. Он представляет собой цилиндрический сосуд со сферическим днищем из железа или меди.
Во избежание теплопотерь боковую поверхность чана и его днище покрывают изоляцией. Сверху заторный чан закрывается сферической крышкой, в центре которой установлена вытяжная труба. В крыше имеются открывающиеся дверцы для обслуживания чана. В центре днища чана устанавливают пропеллерную мешалку, делающую 35-45 об/мин. Целесообразно устраивать пропеллерные мешалки с переменным числом оборотов.
В чане имеется труба для спуска затора в заторный котел, снабженная вентилем или задвижкой. Целесообразно оборудовать обогрев заторных чанов, так как это дает возможность поддерживать необходимый температурный режим затирания.
Характеристика заторных чанов, изготовляемых Ленинградским машиностроительным заводом, приведена в табл. 42.
Таблица 42
Количество затираемого солода в т | Размеры чана в м | Полезная емкость в м3 | Число оборотов мешалки в минуту | |
диаметр | высота цилиндрической части | |||
1,0 | 2,6 | 1,25 | 6,5 | |
1,5 | 3,15 | 1,35 | 10,5 | 30-45 |
3,4 | 0,5 | 1,35 | 30-45 |
Предзаторник. Заторные чаны оборудуются предзаторниками, которые служат для предварительного смешивания поступающего дробленого солода с водой во избежание распыла муки. Конструкция предзаторников различна. В большинстве случаев они представляют собой цилиндрические медные или железные сосуды. Внутри предзаторника установлены перфорированная труба или перфорированные конусообразные насадки, через отверстия которых разбрызгивается вода.
Дробленый солод, поступая по трубе предзаторника сверху, равномерно смачивается водой и вместе с ней поступает в заторный чан.
Заторный котел. Котел (рис. 63) используется для осахаривания и кипячения затора по частям.
Характеристика котлов, изготовляемых машиностроительным заводом, приведена в табл. 43.
Tаблица 43
Количество затираемого солода в т | Размеры котла в м | Число оборотов мешалки в минуту | Поверхность нагрева в м2 | Полный объем котла в м3 | ||
высота цилиндрической части | внутренний диаметр | высота сферического днища | ||||
1,0 | 1,126 | 2,5 | 0,98 | 7,2 | ||
1,5 | 1,326 | 2,5 | 0,98 | 7,2 | ||
3,0 | 1,378 | 3,7 | 1,88 | 12,5 | ||
5,5 | 1,400 | 4,8 | 0,90 | 20,8 |
Заторные котлы делают цилиндрической формы с двойным сферическим дном для парового обогрева и сферической крышкой. В крышке имеется дверца на роликах, а в центре сферы крышки - вытяжная труба с кольцевым желобом для отвода конденсата. Диаметр трубы равен 1/30-1/50 диаметра котла. Боковые стенки и сферическое дно котлов имеют теплоизолирующую обмуровку.
Котлы обогреваются паром. Избыточное давление пара в паровых рубашках не превышает 2,5 атм.
Для равномерного нагревания и перемешивания жидкости внутри котла монтируется пропеллерная мешалка с нижним приводом.
Фильтрационный чан. Чан (рис. 64) служит для фильтрации затора, т. е. отделения солодового сусла от твердых нерастворившихся частиц - дробины.
Фильтрационный чан представляет собой железный цилиндрический с плоским дном сосуд. Над плоским дном чана, на расстоянии 10-12 мм от него, устанавливается второе съемное фильтрационное дно, опирающееся на ножки и борт по окружности чана. Оно составляется из отдельных сит, имеющих форму сегментов. Отверстия в ситах бывают круглые, диаметром 0,8 мм, но большей частью щелевидные, трапециевидные размером 20÷30X0,4÷0,7 мм с расширением книзу до 3-4 мм. Щели в сите располагаются в шахматном порядке. Расстояние между рядами щелей 6 мм. На 1 м2 поверхности сита приходится около 2,5 тыс. щелей, или около 80 тыс. круглых отверстий. Площадь живого сечения щелей в ситах составляет 4-8%, а при круглых отверстиях - 4% от общей площади сит.
Фильтрационные сита изготовляют из фосфористой бронзы толщиной 3,5-4,5 мм.
Для отвода сусла из фильтрационного чана служат сусловые трубы, отверстия которых равномерно распределены по всему дну фильтрационного чана. По трубам сусло отводится; в фильтрационную батарею. Количество отводных труб определяется размером фильтрационного чана: на каждые 1,25-1,50 м2 фильтрующей поверхности устанавливается одна труба внутренним диаметром от 25 до 45 мм.
На 1 м2 дна чана приходится 400-800 см2 живого сечения фильтрующей поверхности чана, а живое сечение отводных труб составляет всего 5-14 см2.
Все отводные трубы соединяются в фильтрационную батарею с общим приемником для сусла. Каждая отводная труба имеет кран с сифоном, обеспечивающим более равномерную фильтрацию сусла и предотвращающим засасывание воздуха под фильтрационное дно во время фильтрации.
Фильтрационные краны различны по конструкции. Основное требование, предъявляемое к кранам, заключается в возможности регулирования стока сусла и промывных вод. Краны с сифонами (гидравлическими затворами) позволяют регулировать скорость фильтрации в широких пределах.
Максимально допустимое число кранов 25, при большем числе кранов затрудняется обслуживание фильтрационной батареи. Размеры фильтрационного чана ограничиваются еще и потому, что при большем количестве затираемого солода получается огромная поверхность, с трудом обрабатываемая разрыхлителем и оросителем.
Приемник для сусла (корыто) соединен трубой с сусловарочным котлом, куда спускается отфильтрованное сусло, и с насосом для перекачивания обратно в фильтрационный чан мутного сусла, получаемого в начале фильтрации.
В дне чана устраивают люк для удаления дробины.
Фильтрационный чан устанавливают строго горизонтально; его боковые стенки должны иметь хорошую теплоизоляцию, чтобы затор во время фильтрации не остывал. Стенки фильтрационного чана имеют деревянную, а чаще железную обшивку, под которой кладут слой теплоизолирующего материала.
Сверху фильтрационный чан закрыт железным или медным колпаком с вытяжной трубой.
Емкость фильтрационного чана определяется количеством затираемого солода и высотой слоя дробины. На 1 т солода объем фильтрационного чана принимается 6-7 м3.
Для нормальной работы чана имеет большое значение удельная нагрузка его, определяемая количеством солода, приходящегося на 1 м2 площади чана.
Допустимые колебания удельной нагрузки чана приводятся в табл.44.
Таблица 44
Высота слоя дробины в см | Поверхность сит на 100 кг солода в м2 | Удельная нагрузка на 1 м2 фильтрующей поверхности в кг | Необходимая фильтрующая поверхность в м2 для затора в т | |||
1,5 | ||||||
0,6 | 6,0 | 9,0 | 12,0 | 18,0 | ||
0,5 | 5,0 | 7,5 | 10,0 | 15,0 | ||
0,45 | 4,5 | 6,75 | 9,0 | 13,5 |
Для лучшей фильтрации и полного выщелачивания дробинка фильтрационные чаны оборудуются промывным аппаратом (сегнеровым колесом) и механическим разрыхлителем.
Промывной аппарат представляет собой цилиндрический сосуд небольшой емкости с двумя горизонтальными трубами, расположенными по обе стороны сосуда; сосуд установлен на вертикальной оси внутри фильтрационного чана. В трубах по всей, длине с противоположных сторон просверлено по одному ряду отверстий; концы труб наглухо закрыты.
Вытекающая через эти отверстия вода приводит во вращение промывной аппарат и вода разбрызгивается по всей поверхности затора в фильтрационном чане.
Медленное вращение промывного аппарата (5-10 об/мин) обеспечивает равномерное орошение всей поверхности дробины. При более быстром вращении орошается главным образом дробина, расположенная у краев фильтрационного чана.
Разрыхлитель. Для рыхления дробины с целью ускорения- фильтрации и лучшего вымывания экстракта применяется специальная рыхлительная машина, устанавливаемая в фильтрационном чане. Она состоит из горизонтальной станины, укрепленной по центру на вертикальном валу и вращающейся вместе с ним. Один конец вертикального вала проходит через дно чана и соединяется с редуктором и электродвигателем, установленными внизу на прочном основании.
На горизонтальной станине установлены вертикальные плоские ножи длиной по 75 см, которые специальным устройством одновременно поворачиваются вокруг своей оси и могут быть поставлены под любым углом в пределах 90°.
В некоторых разрыхлителях на вертикальных ножах дополнительно приварены короткие горизонтальные или слегка наклонные пластинки для рыхления слоев дробины по высоте.
Ножи на станине расположены по обе стороны вала так, что с одной стороны первый нож находится на расстоянии 10 см от вала, а с другой - на расстоянии 20 см. Расстояние между остальными ножами 20 см. Благодаря такому расположению- при вращении рыхлителя дробина в заторе разрезается ножами на концентрические цилиндры с толщиной стенки 10 см.
При помощи масляного насоса (подъемника) разрыхлительный механизм может плавно и медленно перемещаться по вертикальному валу вверх и вниз. Это позволяет рыхлить дробину на любой высоте.
Поворотом ножей вокруг своей оси можно регулировать степень рыхления и перемещения дробины во время вращения рыхлителя.
При установке ножей в плоскость горизонтальной станины рыхлителя широкие плоскости ножей создают большое сопротивление, и дробина уже не разрезается на концентрические цилиндры, а сдвигается общей массой. При таком положении ножей разрыхлитель служит механизмом для подачи дробины к разгрузочному люку во время выгрузки ее из фильтрационного чана.
Число оборотов рыхлителя 0,4 в минуту.
Фильтрпресс. Фильтрпресс используется вместо фильтрационного чана для фильтрации сусла (рис. 65). Он состоит из станины, прямоугольных рам и рифленых промежуточных плит, зажимаемых между крышками в станине.
Каждая рама имеет три прилива с круглыми каналами: один прилив вверху посередине рамы и два сбоку - слева внизу и справа вверху. На боках рамы находятся плечики для установки в станине.
Канал верхнего прилива сообщается широкой прорезью с полостью рамы. Боковые каналы с полостью рамы не сообщаются. Плиты фильтрпресса имеют только два боковых прилива, два плечика и один кран. Расположение боковых приливов и плечиков плит такое же, как и в рамах.
На плоскости плит сделаны бороздки глубиной 6-7 мм; у верхнего и нижнего края плиты они расположены горизонтально, а посередине плиты - вертикально.
В приливах плит имеются круглые каналы, по размеру и расположению точно соответствующие боковым каналам рам. У половины всех плит пресса каналы в приливах широкой прорезью сообщаются с бороздками на плоскостях плит. Кран в плиту ввернут сбоку внизу так, что он тоже сообщается с бороздками плиты.
Крышки фильтрпресса представляют собой массивные плиты. Внутренние плоскости их рифленые, сбоку крышки, как и плиты, имеют краны. Передняя крышка неподвижно соединена со станиной и составляет с ней одно целое, задняя крышка подвижная.
В передней крышке сверху имеется канал, по размеру и расположению точно соответствующий каналам в верхних приливах рам.
Собирают фильтрпресс следующим образом. На плоскость передней неподвижной крышки надевается салфетка и к ней придвигается первая рама. К этой раме ставится первая плита с салфеткой, к ней придвигается вторая рама, затем вторая плита и т. д. На все плиты надеваются салфетки. К последней раме пододвигается задняя крышка с салфеткой, и все это соединяется затяжным винтом, упирающимся в середину задней крышки. В собранном виде в прессе образуются три канала: один верхний для подачи затора и два боковых для промывания дробины водой.
Фильтруемый затор нагнетается в верхний канал и из него через прорези поступает в полости рам. Сусло проходит через полотно и по рифленой поверхности плит стекает к кранам. Дробина остается в раме между салфетками. Промывание и выщелачивание дробины горячей водой, а также продувание сжатым воздухом проводятся через боковые каналы.
Во время фильтрации затора открывают краны у всех плит без исключения, а при продувании фильтра и промывании дробины, заключенной в фильтрпрессе, краны у всех четных плит должны быть закрыты. В этом случае вода входит через боковые каналы на рифленую поверхность плиты, проходит через салфетку в дробину, находящуюся в раме, вытесняет из нее сусло и через ткань на соседней плите выходит в краны нечетных плит (схему действия фильтрпресса см. на стр. 268).
Сусловарочный котел. Котел используется для кипячения сусла с хмелем, а в некоторых случаях (при двухпосудных варочных порядках) он служит одновременно и заторным котлом.
Существуют три системы котлов: котлы с паровой рубашкой (рис. 66), котлы с неподвижными обогревающими кольцами или змеевиками и котлы с подвижными вращающимися обогревающими механизмами.
В сусловарочном котле сусло должно не только кипеть, но и выпариваться с такой интенсивностью, чтобы за 1 ч выпаривалось от 8 до 12% общего объема сусла в котле. Для ускорения выпаривания сусловарочные котлы делают с большой поверхностью испарения (обычно отношение высоты сусла в котле к диаметру котла бывает 1:2) и снабжают соответствующими поверхностями нагрева.
В больших варочных агрегатах емкостью 3 и 5,5 т сусловарочные котлы оборудованы трубчатыми подогревателями (перколяторами) или дополнительными поверхностями нагрева. Это позволяет увеличить интенсивность выпаривания и улучшить циркуляцию сусла. Поверхность нагрева в сусловарочном котле со стальным дном должна быть около 1 м2 на 1 м3 полезной емкости и около 0,7 м2 на 1 м3 емкости сусловарочного котла с медным дном.
Снаружи поверхность котла теплоизолирована. Сусловарочный котел должен быть измерен и иметь устройство для вертикального направления измерительной рейки, которой проводится замер количества сусла в котле. Рейка делается не на всю высоту котла, а только для верхней цилиндрической части его. Полезно изготовлять одновременно две рейки: одна из них служит рабочей, другая - контрольной.
Эксплуатация сусловарочных и заторных котлов, имеющих паровую рубашку, разрешается только с ведома инспектора Котлонадзора. Характеристика котлов различной емкости приводится в табл. 45.
Таблица 45
Количество затираемого солода в т | Размеры котла в м | Число оборотов мешалки в минуту | Полный объем котла в м3 | ||
высота цилиндрической части | внутренний диаметр | высота сферического днища | |||
1,3 | 2,5 | 0,98 | |||
1,5 | 1,3 | 2,92 | 0,912 | 12,5 | |
3,0 | 1,163 | 4,2 | 1,437 | 25,2 | |
5,0 | 1,100 | 5,2 | 1,87 | 45,6 |
Хмелецедильник. Хмелецедильник служит для отделения сусла от хмеля. Сусло в нем процеживается через сито, а хмель задерживается на сите. Хмелецедильники простейшей конструкции представляют собой четырехугольные или цилиндрические сосуды, в которые вставляется второе ложное ситчатое дно или ситчатый сосуд меньших размеров. Хмелецедильник снабжен мешалкой для перемешивания хмеля при промывании его водой. Процеженное сусло передается насосом для отстаивания в отстойные чаны или на тарелки.
|
|
Археология об основании Рима: Новые раскопки проясняют и такой острый дискуссионный вопрос, как дата самого возникновения Рима...
Индивидуальные и групповые автопоилки: для животных. Схемы и конструкции...
Поперечные профили набережных и береговой полосы: На городских территориях берегоукрепление проектируют с учетом технических и экономических требований, но особое значение придают эстетическим...
Историки об Елизавете Петровне: Елизавета попала между двумя встречными культурными течениями, воспитывалась среди новых европейских веяний и преданий...
© cyberpedia.su 2017-2024 - Не является автором материалов. Исключительное право сохранено за автором текста.
Если вы не хотите, чтобы данный материал был у нас на сайте, перейдите по ссылке: Нарушение авторских прав. Мы поможем в написании вашей работы!