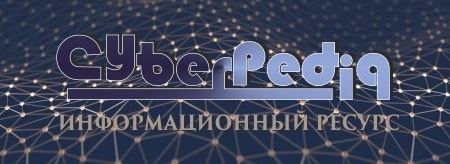
Историки об Елизавете Петровне: Елизавета попала между двумя встречными культурными течениями, воспитывалась среди новых европейских веяний и преданий...
Поперечные профили набережных и береговой полосы: На городских территориях берегоукрепление проектируют с учетом технических и экономических требований, но особое значение придают эстетическим...
Топ:
Определение места расположения распределительного центра: Фирма реализует продукцию на рынках сбыта и имеет постоянных поставщиков в разных регионах. Увеличение объема продаж...
Проблема типологии научных революций: Глобальные научные революции и типы научной рациональности...
Установка замедленного коксования: Чем выше температура и ниже давление, тем место разрыва углеродной цепи всё больше смещается к её концу и значительно возрастает...
Интересное:
Что нужно делать при лейкемии: Прежде всего, необходимо выяснить, не страдаете ли вы каким-либо душевным недугом...
Берегоукрепление оползневых склонов: На прибрежных склонах основной причиной развития оползневых процессов является подмыв водами рек естественных склонов...
Лечение прогрессирующих форм рака: Одним из наиболее важных достижений экспериментальной химиотерапии опухолей, начатой в 60-х и реализованной в 70-х годах, является...
Дисциплины:
![]() |
![]() |
5.00
из
|
Заказать работу |
Содержание книги
Поиск на нашем сайте
|
|
Точечная контактная сварка — сварочный процесс, при котором детали соединяются в одной или одновременно в нескольких точках. Прочность соединения определяется размером и структурой сварной точки, которые зависят от формы и размеров контактной поверхности электродов, силы сварочного тока, времени его протекания через заготовки, усилия сжатия и состояния поверхностей свариваемых деталей. С помощью точечной сварки можно создавать до 600 соединений за 1 минуту. Применяется для соединения тончайших деталей (до 0,02 мкм) электронных приборов, для сварки стальных конструкций из листов толщиной до 20 мм в автомобиле-, самолёто- и судостроении, в сельскохозяйственном машиностроении и других отраслях промышленности.
Различают мягкий и жесткий режимы точечной сварки. Мягкий режим характеризуется большей продолжительностью времени сварки и плавным нагревом заготовок умеренными силами тока, с плотностью тока на рабочей поверхности электрода обычно не превышающей 100 А/мм²[3]. Время протекания тока обычно 0,5—3 секунды[4]. Преимуществами мягких режимов являются меньшие потребляемые мощности, по сравнению с жесткими режимами; меньшие нагрузки сети; менее мощные и более дешевые сварочные машины, необходимые для производства точечной сварки; уменьшение закалки зоны сварки. Мягкие режимы применяют для сварки сталей, склонных к закалке.
Жесткий режим точечной сварки характеризуется малой продолжительностью времени сварки, бо́льшими, чем при мягком режиме, значениями силы тока и значительным сжимающим давлением электродов. Плотности тока достигают 120—300 А/мм² при сварке стали[3]. Время протекания тока обычно 0,1—1,5 секунды[4]. Давление электродов обычно принимают в пределах 3—8 кг/мм²[3]. К недостаткам жестких режимов относятся повышенная мощность, потребляемая при сварке; значительные нагрузки сети; мощные сварочные машины. Преимущества — уменьшение времени сварки и повышение производительности. Жесткие режимы применяют при сварке алюминиевых и медных сплавов, с высокой теплопроводностью, деталей неравной толщины и разноименных деталей, а также высоколегированных сталей с целью сохранения коррозионной стойкости[4].
|
Конструктивные элементы сварных соединений, выполненных контактной точечной сваркой: а — неплакированные металлы; б — плакированные металлы; в — детали неравной толщины; г — разноименные металлы;
s и s1 — толщина детали; d — расчетный диаметр литого ядра точки или ширина литой зоны шва; h и h1 — величина проплавления; g и g1 — глубина вмятины
8.4 Радиационные методы контроля, их классификация. Основные единицы измерения
Радиационный контроль – это вид неразрушающего контроля, основанный на регистрации и анализе ионизирующего излучения после его взаимодействия с объектом контроля.
Существуют два вида ионизирующих излучений:
1. корпускулярное, состоящее из частиц с массой покоя, отличной от нуля (альфа- и бета-излучение и нейтронное излучение);
2. электромагнитное (гамма-излучение и рентгеновское) с очень малой длиной волны.
Основными направлениями радиационной дефектоскопии являются рентгено- и гамма- дефектоскопия.
Различие между рентгеновской и гамма- дефектоскопией заключается в используемых источниках ионизирующих излучений, однако ввиду общности способов регистрации излучения и целей испытаний они имеют общую методику и технологию проведения контроля в производственных условиях.
Наиболее используемым методом радиационного контроля является рентгенографический контроль, при котором генерирование рентгеновского излучения происходит с помощью рентгеновской трубки, в которой излучение возникает при взаимодействии быстрых электронов с атомами вещества анода, а регистрация изображения осуществляется помощью детектора излучения — на пленке или пластине.
|
Рентгенографический контроль наиболее достоверный способ контроля сварных соединений и основного металла при контроле трубопроводов, оборудования при проведении экспертизы промышленной безопасности.
Рентгенографический контроль применяют для выявления грубых трещин, непроваров, пор, раковин, шлаковых, вольфрамовых, окисных и других включений в литых и сварных стальных изделиях толщиной до 80 мм и в изделиях из легких сплавов толщиной до 250 мм.
Также контроль применяют для выявления прожогов, подрезов, оценки величины выпуклости и вогнутости корня шва, недопустимых для внешнего осмотра. Наличие таких дефектов приводит к тому, что проходящие через материал лучи ослабляются в различной степени. Наиболее широко используется рентгеновское излучение (Х-лучи). Это фотонное излучение с длиной волны 6*10-13...1*10-9 м. Имея ту же природу, что и видимый свет, но меньшую длину волны (у видимого света 4...7 * 10-7 м), рентгеновское излучение обладает высокой проникающей способностью и может проходить через достаточно большие
— любые несплошности и включения с размером в направлении просвечивания менее удвоенной чувствительности контроля;
— непровары и трещины, плоскость раскрытия которых не совпадает с направлением просвечивания и (или) величина раскрытия менее значений, приведенных 0,1;
— любые несплошности и включения, если их изображения на снимках совпадают с изображениями посторонних деталей, острых углов или резких перепадов трещин просвечиваемого металла.
Рентгенографический метод контроля эффективен только в том случае, если выбраны оптимальные режимы контроля: определены геометрические параметры контроля, размер фокусного пятна трубки, фокусное расстояние, расстояние от контролируемого объекта до преобразователя излучения, напряжение и ток рентгеновской трубки.
8.5 Борьба со сварочными деформациями с помощью сварочных приспособлений. Крепление деталей и узлов с деформированием в сборочно-сварочной оснастке.
При сварке изделий невозможно полностью избежать остаточных деформаций и напряжений. Поэтому борьбу с ними необходимо осуществлять на разных стадиях изготовления сварной конструкции: до сварки (на стадии проектирования конструкции и технологии производства), во время и после сварки. Газовая сварка дает большую зону нагрева по сравнению с другими видами сварки, поэтому она вызывает и большие деформации свариваемых изделий. Для уменьшения деформаций при сварке необходимо стремиться к равномерному распределению объема наплавляемого металла, более равномерному нагреву детали при сварке, а также применять определенный порядок наложения швов. Важно правильно выбрать режим сварки. При сборке изделий под сварку зазор должен быть равномерным по всей длине шва. Прихватывать детали необходимо в меньшем числе точек. Для устранения деформаций при сварке встык применяют обратноступенчатый и комбинированный порядок наложения швов. В этом случае весь шов делят на участки длиной 100—250 мм. Сварку ведут отдельными участками в порядке, отмеченном цифрами, и направлении, указанном стрелками. При этих способах листы почти не будут коробиться, так как обеспечивается более равномерное распределение теплоты вдоль шва, чем при непрерывной сварке, а потому величина деформации уменьшается.
|
Способы уменьшения деформаций: а — уравновешивание деформаций, б — обратная деформация; 1—4 — швы
Для уменьшения деформаций применяют также способ уравновешивания деформаций, при котором имеет значение очередность наложения швов. Очередность наложения выбирают так, чтобы последующий шов вызывал деформации, обратные деформациям, полученным при наложении предыдущего шва. Для уменьшения деформаций применяют и способ обратных деформаций. Сущность этого способа заключается в том, что детали перед сваркой располагают так, чтобы после сварки они приняли требуемое взаимное расположение. В этом случае листы размещают под некоторым углом относительно друг друга. В процессе сварки вследствие усадки металла шва кромки сближаются, в результате чего уменьшается деформация.
Порядок наложения швов: а — обратноступенчатый, б, в — комбинированный
|
|
Поперечные профили набережных и береговой полосы: На городских территориях берегоукрепление проектируют с учетом технических и экономических требований, но особое значение придают эстетическим...
Типы сооружений для обработки осадков: Септиками называются сооружения, в которых одновременно происходят осветление сточной жидкости...
Семя – орган полового размножения и расселения растений: наружи у семян имеется плотный покров – кожура...
История развития хранилищ для нефти: Первые склады нефти появились в XVII веке. Они представляли собой землянные ямы-амбара глубиной 4…5 м...
© cyberpedia.su 2017-2024 - Не является автором материалов. Исключительное право сохранено за автором текста.
Если вы не хотите, чтобы данный материал был у нас на сайте, перейдите по ссылке: Нарушение авторских прав. Мы поможем в написании вашей работы!