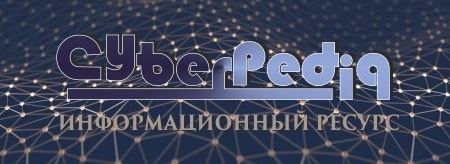
Двойное оплодотворение у цветковых растений: Оплодотворение - это процесс слияния мужской и женской половых клеток с образованием зиготы...
Наброски и зарисовки растений, плодов, цветов: Освоить конструктивное построение структуры дерева через зарисовки отдельных деревьев, группы деревьев...
Топ:
Эволюция кровеносной системы позвоночных животных: Биологическая эволюция – необратимый процесс исторического развития живой природы...
Организация стока поверхностных вод: Наибольшее количество влаги на земном шаре испаряется с поверхности морей и океанов...
Генеалогическое древо Султанов Османской империи: Османские правители, вначале, будучи еще бейлербеями Анатолии, женились на дочерях византийских императоров...
Интересное:
Искусственное повышение поверхности территории: Варианты искусственного повышения поверхности территории необходимо выбирать на основе анализа следующих характеристик защищаемой территории...
Принципы управления денежными потоками: одним из методов контроля за состоянием денежной наличности является...
Средства для ингаляционного наркоза: Наркоз наступает в результате вдыхания (ингаляции) средств, которое осуществляют или с помощью маски...
Дисциплины:
![]() |
![]() |
5.00
из
|
Заказать работу |
Содержание книги
Поиск на нашем сайте
|
|
Припуском на обработку называется слой металла, подлежащий удалению с поверхности заготовки в процессе обработки для получения готовой детали.
Размер припуска определяют разностью между размером заготовки и размером детали по рабочему чертежу; припуск задается на сторону
В качестве полуфабрикатов для изготовления сварных конструкций в абсолютном большинстве случаев используется листовой и фасонный прокат широкой номенклатуры типоразмеров. Неравномерный нагрев металла при сварке, усадочные явления, вызванные пластической деформацией при нагреве и кристаллизацией неизбежно вызывают деформации и перемещения в сварных конструкциях, наличие которых не обеспечивает заданную чертежом точность размеров и поверхностей изделий. Для обеспечения заданной точности в технологическом процессе изготовления изделий предусматривают операции механической обработки. Количество операций, виды и объем обработки определяются конструкцией изделия и ее назначением.
В изделиях машиностроения требования точности часто достаточно жесткие, что предопределяет необходимость механической обработки.
При изготовлении сложных изделий они как правило расчленяются на узлы и подузлы. Механическая обработка назначается при изготовлении сварных деталей этих сборочных единиц, собираемых из них подузлов и после сварки всего узла.
Для проведения механической обработки в деталях предусматривают соответствующие технологические припуски. Величина припусков зависит от размеров изделия и толщины свариваемых деталей, величины возникающих деформаций, способа получения неразъемных соединений и может составлять от долей миллиметра до нескольких миллиметров.
|
Минимальные деформации возникают при пайке, диффузионной сварке, контактной точечной и шовной сварке, наибольшие – при сварке плавлением и контактной стыковой
Легирование наплавленного металла сварных швов при сварке плавлением и наплавке. Методы легирования и области их применения. Понятие о коэффициенте перехода и усвоения легирующих элементов из сварочных материалов в металле сварного шва (наплавки)
Нужные свойства наплавленного слоя обычно получают легированием, т. е. введением в его состав легирующих примесей. Существует много методов легирования. Методы легирования и способы наплавки взаимосвязаны — выбранный способ наплавки, как правило, диктует рациональный метод легирования, и, наоборот, эффективный метод легирования требует применения соответствующего способа наплавки. С другой стороны, основными признаками, по которым следует оценивать метод легирования, являются: точность (надежность) получения заданного химического состава наплавленного металла при возможных колебаниях режимов наплавки, однородность состава по объему наплавленного слоя, экономичность и удобство применения метода легирования. Что касается экономичности метода легирования, то здесь необходимо учитывать целесообразность применения тех или иных легирующих элементов для данного объекта наплавки и потери этих легирующих элементов при выборе метода легирования.
Легировать сварочную ванну можно за счет обменных реакций между металлом и шлаком (окислами), через газовую среду и путем введения металлических добавок. Примером легирования за счет обменных реакций являются известные кремние- и марган-цевовосстановительные процессы при сварке и наплавке под флюсами АН-348-А, ОСЦ-45, АН-60 и др. Легирование посредством газовой фазы имеет место при дуговой наплавке плавящимся электродом в атмосфере воздуха или азота, когда наплавленный металл содержит заметные количества азота. Благодаря этому повышается износостойкость хромистых сплавов или регулируется количество аустенитной фазы.
|
Однако эти два процесса легирования для износостойкой наплавки применяют редко, так как они не могут обеспечить необходимый уровень содержания легирующих элементов. Поэтому наибольшее распространение получило легирование путем введения в сварочную ванну металлических сплавов, чистых металлов и металлоподобных соединений. Кинетика растворения металлических добавок и металлоподобных соединений в жидких металлах изучена еще недостаточно.
При ручной наплавке штучными электродами легирование осуществляется введением легирующих элементов в покрытие электрода или в электродный стержень. Применяют и комбинированный метод легирования, когда легирующие примеси вводят и в стержень, и в покрытие.
Процессы легирования протекают на стадии капли и в сварочной ванне. Концентрация легирующего элемента в наплавленном металле пропорциональна толщине легирующего покрытия (коэффициенту массы покрытия). возрастание концентрации легирующего элемента при увеличении толщины покрытия больше эффективной происходит за счет процессов в сварочной ванне. Эффективная толщина покрытия зависит главным образом от его температуры плавления. Чем больше толщина покрытия отличается (в большую сторону) от эффективной толщины, тем больше вклад ванны в процесс легирования
|
|
Типы оградительных сооружений в морском порту: По расположению оградительных сооружений в плане различают волноломы, обе оконечности...
Наброски и зарисовки растений, плодов, цветов: Освоить конструктивное построение структуры дерева через зарисовки отдельных деревьев, группы деревьев...
Археология об основании Рима: Новые раскопки проясняют и такой острый дискуссионный вопрос, как дата самого возникновения Рима...
Эмиссия газов от очистных сооружений канализации: В последние годы внимание мирового сообщества сосредоточено на экологических проблемах...
© cyberpedia.su 2017-2024 - Не является автором материалов. Исключительное право сохранено за автором текста.
Если вы не хотите, чтобы данный материал был у нас на сайте, перейдите по ссылке: Нарушение авторских прав. Мы поможем в написании вашей работы!