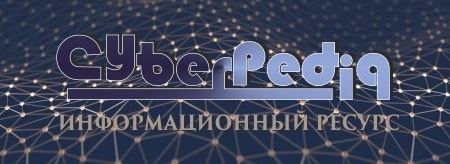
Поперечные профили набережных и береговой полосы: На городских территориях берегоукрепление проектируют с учетом технических и экономических требований, но особое значение придают эстетическим...
Адаптации растений и животных к жизни в горах: Большое значение для жизни организмов в горах имеют степень расчленения, крутизна и экспозиционные различия склонов...
Топ:
Оценка эффективности инструментов коммуникационной политики: Внешние коммуникации - обмен информацией между организацией и её внешней средой...
Организация стока поверхностных вод: Наибольшее количество влаги на земном шаре испаряется с поверхности морей и океанов...
Устройство и оснащение процедурного кабинета: Решающая роль в обеспечении правильного лечения пациентов отводится процедурной медсестре...
Интересное:
Отражение на счетах бухгалтерского учета процесса приобретения: Процесс заготовления представляет систему экономических событий, включающих приобретение организацией у поставщиков сырья...
Берегоукрепление оползневых склонов: На прибрежных склонах основной причиной развития оползневых процессов является подмыв водами рек естественных склонов...
Принципы управления денежными потоками: одним из методов контроля за состоянием денежной наличности является...
Дисциплины:
![]() |
![]() |
5.00
из
|
Заказать работу |
Содержание книги
Поиск на нашем сайте
|
|
Процесс резки заключается в проплавлении металла и удалении жидкого металла из полости реза плазменной струей. В качестве плазмообразующих газов могут быть использованы сжатый воздух, кислород, азотно-кислородная смесь, азот, аргоноводородная смесь. Выбор плазмообразующего газа определяется физико-химическими свойствами разрезаемого металла, необходимым качеством реза, стойкостью плазматрона, стоимостью самих газов. Например, дорогую аргоноводородную смесь применяют в случае повышенного требования к качеству резания алюминия, меди и сплавов на их основе.
Более подробно, чем в первом издании, рассмотрены металлургические особенности резки высоколегированных хромистых и хромоникелевых сталей. На основе дальнейшего изучения физико-химических процессов, протекающих в разрезе и в металле кромки, анализа образующихся во время резки шлаков и структурных превращений предложена принципиально новая классификация разрезаемости высоколегированных сталей и приведены технологические рекомендации по резке. Обобщены данные по исследованию кислородно-флюсовой резки стали большой толщины, биметалла и горячего металла в условиях непрерывного металлургического производства, по резке бронзы и порошково-копьевой резке железобетона большой толщины. Предложена методика расчета основных технологических
Техника кислородной резки.
Общие сведения. Кислородная резка является одним из наиболее распространённых процессов газопламенной обработки металлов. Она широко используется в металлообработке и металлургии при резке листов, заготовок профильного проката, труб и т.д.
Различают два вида кислородной резки: разделительную и поверхностную.
|
При разделительной резке образуются сквозные разрезы, а при поверхностной – канавки круглого очертания.
Разделительная резка производится без и со скосом кромок под сварку, а поверхностная бывает либо сплошной, когда обрабатывается вся поверхность заготовки за один проход, либо выборочной с удалением поверхностного слоя металла.
В отличие от сварки кислородная резка на вертикальной плоскости или в потолочном положении не представляет трудностей и может производиться в любом пространственном положении.
В процессе резки металл расплавляется и вытекает из полости реза. Однако железо легко окисляется, а в чистом кислороде горит и превращается в оксиды и шлаки.
К термическому и химическому действию может присоединяться механическое действие струи газа, выталкивающее жидкие и размягчённые продукты из полости реза.
При кислородной резке происходит химическая реакция сгорания железа в кислороде.
Сущность процесса кислородной резки. Смесь кислорода с горючим газом выходит из подогревательного мундштука резака и сгорает, образуя пламя, которое называют подогревающим. Когда металл нагревается до температуры начала горения, пор осевому каналу режущего мундштука подаётся технически чистый кислород. Он попадает на нагретый металл и зажигает его. В процессе горения выделяется значительное количество кислоты. Нижележащие слои металла нагреваются, и горение быстро распространяется в глубину, прожигая сквозное отверстие, через которое режущая струя кислорода выходит, наружу пробивая металл. Если перемещать резак с определённой скоростью, то металл будет разрезаться.
Таким образом, кислородная резка состоит из нескольких процессов: подогрева металла, сжигания металла струёй кислорода, выдувания расплавленного шлака из полости реза. Подогревательное пламя обычно не тушат, и оно горит в течении всего процесса резки, так как теплоты, выделяющейся при сжигании железа в кислороде, недостаточно для возмещения всех потерь теплоты в зоне резки. Если подогревательное пламя потушить, то процесс резки быстро прекращается, металл охлаждается настолько, что кислород перестанет на него действовать, и реакция горения металла в кислороде останавливается.
|
Условия резки. Кислородной резке подвергаются только те металлы и сплавы, которые удовлетворяют определённым условиям.
• Температура воспламенения металла в кислороде должна быть ниже температуры его плавления. Этому требованию соответствуют низкоуглеродистые стали, температура воспламенения которых в кислороде около 1300оС, а температура плавления около 1500оС. Увеличение содержания углерода в стали сопровождается повышением температуры воспламенения в кислороде и понижением температуры плавления. Поэтому с ростом содержания углерода кислородная резка сталей ухудшается.
• Температура плавления оксидов металлов, образующихся при резке, должна быть ниже температуры плавления самого металла. В противном случае тугоплавкие оксиды не будут выдуваться струёй режущего кислорода, что нарушит нормальный процесс резки. Этому условию не удовлетворяют высокохромистые стали и алюминий. При резке высокохромистых сталей образуются тугоплавкие оксиды с температурой плавления 2000оС, а при резке алюминия – оксид, температура плавления которого около 2050оС. Кислородная резка их невозможна без применения специальных флюсов.
• Теплоты, которая выделяется при сгорании металла в кислороде, должно быть достаточно для поддержания непрерывного процесса резки. При резке стали около 70% теплоты выделяется в результате сгорания металла в кислороде и только 30% её поступает от подогревающего пламени резака.
• Образующиеся при резке шлаки должны быть жидкотекучими и легко выдуваться из места реза.
• Теплопроводность металлов и сплавов не должна быть слишком высокой, иначе теплота от подогревающего пламени и нагретого шлака интенсивно отводится от места реза, процесс резки становится неустойчивым и в любой момент может прерваться. При резке стали сгорание железа в кислороде происходит в соответствии со следующими реакциями:
Fe + 0,5O2 = FeO + 269 МДж/кмоль,
2Fe + 1,5O2 = Fe2O3 + 272 МДж/кмоль,
3Fe + 2O2 = Fe3O4 +276 МДж/кмоль.
Из уравнений следует, что на сгорание 1 кг железа расходуется 0,38 кг (0,27 л) кислорода, или на 1 см3 железа требуется 2,1 л кислорода. На практике же расход кислорода в процессе резки может быть выше или ниже теоретического значения, так как часть металла выдувается из полости реза в неокислённом виде и вытекающий шлак содержит не только оксиды, но и металлическое железо. Выделяемое при горении железа значительное количество теплоты оплавляет поверхность металла. Этот жидкий металл увлекается в шлак вместе с расплавленными оксидами. Количество теплоты, образующееся в результате сгорания железа при резке, в 6-8 раз превышает количество теплоты, выделяемой подогревающим пламенем резака.
|
Указанным условиям удовлетворяет лишь железо и его технические сплавы – стали. Большинство других металлов не поддаются кислородной резке.
Показатели режима резки. Основными показателями режима резки являются: мощность пламени, давление режущего кислорода и скорость резки. От их выбора во многом зависят производительность и качество резки.
Мощность пламени определяется толщиной разрезаемого металла, составом и состоянием стали (прокат или поковка). При ручной резке из-за неравномерности перемещения резака обычно приходится в 1,2-2 раза увеличивать мощность пламени по сравнению с машинной. При резке литья следует повышать мощность пламени в 3-4 раза, так как поверхность отливок, как правило, покрыта песком и пригаром.
Для резки стали толщиной до 300 мм применяют нормальное пламя, а толщиной свыше 400 мм – подогревающее пламя с избытком ацетилена (науглероживающее) для увеличения длины факела и прогрева нижней части реза.
Давление режущего кислорода зависит от толщины разрезаемого металла, формы режущего сопла и чистоты кислорода. При повышении давления сверх нормативного скорость резки уменьшается, и качество поверхности реза ухудшается. Соответственно увеличивается расход кислорода.
Скорость резки должна соответствовать скорости окисления металла по толщине разрезаемого листа. Судить о правильном выборе скорости резки можно по следующим признакам. При замедленной скорости происходит оплавление верхних кромок разрезаемого листа и расплавленные шлаки (оксиды) вылетают из разреза в виде потока искр в направлении резки.
|
Слишком большая скорость характеризуется слабым вылетом пучка искр из разреза в сторону, обратную направлению резки, и значительным «отставанием» линий реза от вертикали. Возможно непрорезаение металла. При нормальной скорости резки поток искр и шлака с обратной стороны разрезаемого листа сравнительно небольшой и направлен почти параллельно кислородной струе.
Подготовка поверхности. Перед резкой поверхность разрезаемого металла должна быть тщательно очищена от окалины, ржавчины, краски и грязи. Для ручной резки достаточно очистить пламенем резака место реза в виде узкой полосы (30-50 мм) с последующей зачисткой металлической щеткой. Перед механизированной резкой на стационарных машинах листы обычно правят на листоправильных вальцах и очищают всю поверхность либо химическим, либо механическим (дробеструйной обработкой) путем.
Листы укладываются горизонтально на опоры. Свободное пространство под листом должно составлять половину толщины разрезаемого металла плюс 100мм.
Ручная разделительная кислородная резка.
Резка листов. Ручная разделительная резка применяется для резки листов, поковок профильного проката и скрапа. При резке в качестве горючего газа используется как ацетилен, так и газы-заменители ацетилена (пропан-бутан, природный газ и др.). В последнем случае увеличивается время предварительного подогрева металла до начала процесса резки, поэтому предпочтительнее использовать ацетилен (где это возможно). Резка скрапа преимущественно производится с применением жидкого горючего (керосин, бензин и их смеси).
Для резки листов толщиной от 3 до 300 мм используются универсальные ручные резаки Р2А-01,РЗП-01, а до 800 мм – специализированные резаки типа РЗР-2.
Резка стали малой толщины сопровождается значительным перегревом, оплавлением кромок и короблением разрезаемого металла. При этом на резаках устанавливается внутренний мундштук №0 с минимальным отверстием для режущего кислорода и наружный мундштук №1. Лучшие результаты даёт резка с последовательным расположением подогревающего пламени и режущего кислорода. Резку ведут с максимальной скоростью и минимальной мощностью подогревающего пламени. Мундштук резака наклоняют под углом 15-40о к поверхности реза в сторону, обратную направлению резки.
Перед началом резки нужно положить лист на опоры, очистить место реза и установить на резаке мундштуки в зависимости от толщины разрезаемой стали. Мощность пламени и давления газов (кислорода и горючего) регулируют при открытом вентиле режущего кислорода. Подогрев листа начинается с кромки и длится обычно 3-10 с. Если резку начинают с середины листа, продолжительность подогрева увеличивается в 3-4 раза.
|
Точность и качество ручной резки зависят от правильного выбора режимов и квалификации резчика. Чтобы повысить точность, резку выполняют по разметке и направляющим (при прямолинейной резке). Качество резки в значительной степени зависит от своевременного пуска режущего кислорода, равномерного перемещения резака и поддержания постоянного расстояния между резаком и поверхностью листа. Для этого используют простейшие приспособления: циркуль для вырезки фланцев и отверстий, тележку для поддержания постоянного расстояния между резаком и поверхностью листа; направляющую линейку или уголок для прямолинейных резов и т. д.
Существуют особые технологические приемы повышения качества ручной резки. К ним относятся, например, безгратовая и пакетная резка.
Безгратовая резка применяется для получения поверхности реза без грата на нижних кромках. При этом используют кислород чистотой не ниже 99.5 и сопло режущего кислорода с расширением на выходе (для резки металла толщиной более 12 мм).
Пакетная резка позволяет получать качественный рез тонких листов (толщиной 1,5-2 мм). Листы складываются в пакет и стягиваются струбцинами. Максимальная толщина каждого листа 8-10 мм, а общая толщина пакета – не более 100 мм. Режимы резки устанавливаются по суммарной толщине пакета, однако скорость ей должна быть несколько ниже, чем для однослойной стали той же толщины.
Пакетную резку можно производить без плотного прилегания листов (с зазорами между ними до 3-4 мм). В этом случае пакет закрепляют с одной стороны и выполняют резку кислородом низкого давления (0,3-0,5 МПа) с рассверливанием горлового канала мундштука на 0,3-04 мм. Облегчает начало процесса резки сборка листов с небольшим сдвигом. Пакетную резку используют и при машинной резке.
Резка поковок и отливов. Производится ручным резаком типа РЗР-2, работающим на пропан-бутане в смеси с кислородом. Этот резак режет поковки и отливки толщиной от 300 до 800 мм. Для обеспечения качественной резки заготовок такой толщины важное значение имеют положение резака и скорость его перемещения. В начале резки резак располагают под прямым углом к разрезаемой поверхности или под углом 5о в сторону, обратную движению. После предварительного подогрева места начала резки и пуска режущего кислорода необходимо убедиться в полном прорезании металла по всей толщине и затем начать перемещение резака. К концу реза следует немного снизить скорость резки и увеличить угол наклона резака в сторону, обратную движению, до 10-15о для обеспечения полного прорезания конечного участка и уменьшения отставания линий реза.
Резка труб. Ручная кислородная резка используется для обрезки торцов труб под сварку, вырезки дефектных участков и отверстий в трубопроводах и т.д. Резка выполняется с использованием в качестве горючего газа ацетилена или газов-заменителей. Трубы можно резать в любых пространственных положениях. Резка труб небольшого диаметра выполняется без их поворота. При резке неповоротных труб большого диаметра резак перемещается по направляющему угольнику, а при резке поворотных труб используются специальные каретки и роликовые стенды.
Скорость резки труб с толщиной стенок 6-12 мм не превышает 800мм/мин. Для повышения скорости резки резак устанавливают под углом 15-25о к касательной в точке пересечения оси резака с поверхностью трубы. При этом увеличивается зона взаимодействия кислорода с металлом и образующийся в процессе резки шлак нагревает лежащий впереди участок трубы, благодаря чему улучшается окисление металла. Однако время предварительного подогрева поверхности трубы до температуры воспламенения увеличивается до 60-70с. Чтобы избежать этого, необходимо ввести в зону реакции стальной пруток (или железный порошок). В этом случае средняя скорость резки труб диаметром 300-1020 мм с толщиной стенки до 12 мм составляет 1,5-2,5 м/мин, т.е. повышается в 2-3 раза по сравнению с резкой при перпендикулярном расположении резака.
Резка производится универсальными или вставными резаками. Режимы её устанавливаются в зависимости от толщины металла согласно паспортным характеристикам резаков.
Резка профильного проката. Последовательность операций резки зависит от профиля разрезаемого металла. Резку уголка начинают с кромки полки. Резку двутавровых балок начинают с резки полок, а затем прорезают стойку.
Поверхностная кислородная резка.
Поверхностной кислородной резкой называют процесс снятия слоя металла кислородной струёй. Эта резка отличается от разделительной тем, что вместо сквозного разреза на поверхности обрабатываемого металла образуется канавка. Профиль её зависит от формы и размеров выходного канала мундштука для режущего кислорода, а также режимов резки и расположения (угол наклона) резака относительно листа.
Суть процессов разделительной и поверхностной резки одинакова. Однако в последнем случае струя кислорода направляется под острым углом к поверхности металла и быстро перемещается. Источником нагрева металла является не только подогревающее пламя резака, но и расплавленный шлак, который, растекаясь по поверхности листа вдоль линии реза, подогревает нижележащие слои металла. Следовательно, при поверхностной резке эффективнее используется теплота, выделяемая в результате окисления железа, чем при разделительной. В результате этого скорость поверхностной резки достигает 2-4 м/мин, соответственно повышается и производительность труда. Ручным резаком удаляется до 40 кг/ч металла, в то время как при пневматической вырубке – не более 2-3 кг/ч.
Поверхностная резка широко применяется в металлургической промышленности и сварочном производстве. В сварочном производстве поверхностная резка используется для вырезки дефектных участков швов и при ремонтных работах.
Ручная резка выполняется резаками типов РПК и РПА, а машинная с помощью машин огневой зачистки (МОЗ). Они удаляют слои металла толщиной от 0,5 до 3,5 мм одновременно с четырех сторон сляба или блюма. Производительность сплошной зачистки проката велика и составляет 600-1000 кг/ч в зависимости от сортамента обрабатываемой стали. Скорость движения металла при зачистке достигает 45-50 м/мин.
Ручная зачистка начинается с прогрева начального участка до температуры воспламенения металла. При включении режущего кислорода образуется очаг горения металла и обеспечивается устойчивый процесс зачистки за счет равномерного перемещения резака вдоль линии реза. При нагреве резак обычно располагается под углом 70-80о к поверхности. В момент подачи режущего кислорода его наклоняют на 15-45о.
При прочих равных условиях глубина и ширина канавки зависят от скорости резки и с её увеличением уменьшаются. Глубина канавки увеличивается с возрастанием угла наклона мундштука резака, повышением давления режущего кислорода и уменьшением скорости резки. Ширина канавки определяется диаметром канала режущей струи кислорода. Чтобы избежать появления закатов на поверхности заготовки, ширина канавки должна быть в 5-7 раз больше её глубины.
При необходимости зачистки дефектов на значительной поверхности обычно производят резку «ёлочкой» за один или несколько проходов, придавая резаку колебательные движения. Расстояние между мундштуком и зачищаемым металлом должно быть постоянным.
Поверхностная кислородная резка может быть использована для зачистки дефектов на поверхности высоколегированных сталей. В этом случае следует применять кислородно-флюсовую резку в сочетании с поверхностной, используя резаки типа РПА или другие с кислородно-флюсовой оснасткой и установку типа УГПР
|
|
Папиллярные узоры пальцев рук - маркер спортивных способностей: дерматоглифические признаки формируются на 3-5 месяце беременности, не изменяются в течение жизни...
Общие условия выбора системы дренажа: Система дренажа выбирается в зависимости от характера защищаемого...
Индивидуальные очистные сооружения: К классу индивидуальных очистных сооружений относят сооружения, пропускная способность которых...
Типы оградительных сооружений в морском порту: По расположению оградительных сооружений в плане различают волноломы, обе оконечности...
© cyberpedia.su 2017-2024 - Не является автором материалов. Исключительное право сохранено за автором текста.
Если вы не хотите, чтобы данный материал был у нас на сайте, перейдите по ссылке: Нарушение авторских прав. Мы поможем в написании вашей работы!