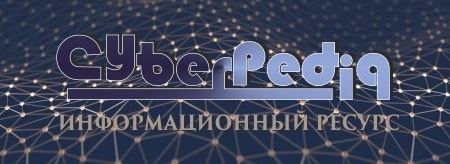
Таксономические единицы (категории) растений: Каждая система классификации состоит из определённых соподчиненных друг другу...
Организация стока поверхностных вод: Наибольшее количество влаги на земном шаре испаряется с поверхности морей и океанов (88‰)...
Топ:
Отражение на счетах бухгалтерского учета процесса приобретения: Процесс заготовления представляет систему экономических событий, включающих приобретение организацией у поставщиков сырья...
Организация стока поверхностных вод: Наибольшее количество влаги на земном шаре испаряется с поверхности морей и океанов...
Определение места расположения распределительного центра: Фирма реализует продукцию на рынках сбыта и имеет постоянных поставщиков в разных регионах. Увеличение объема продаж...
Интересное:
Инженерная защита территорий, зданий и сооружений от опасных геологических процессов: Изучение оползневых явлений, оценка устойчивости склонов и проектирование противооползневых сооружений — актуальнейшие задачи, стоящие перед отечественными...
Лечение прогрессирующих форм рака: Одним из наиболее важных достижений экспериментальной химиотерапии опухолей, начатой в 60-х и реализованной в 70-х годах, является...
Влияние предпринимательской среды на эффективное функционирование предприятия: Предпринимательская среда – это совокупность внешних и внутренних факторов, оказывающих влияние на функционирование фирмы...
Дисциплины:
![]() |
![]() |
5.00
из
|
Заказать работу |
Содержание книги
Поиск на нашем сайте
|
|
Назначение: для кратковременного разобщения двигателя от ведущих колёс. Требования: полное и плавное включение; полнота выключения; защита трансмиссии от динамических перегрузок (за счёт пробуксовки ведомых частей относительно ведущ и оценивается коэффициентом запаса); min момент инерции ведом частей; хороший отвод тепла; лёгкость управления.
МУФТЫ СЦЕПЛЕНИЯ ПОДРАЗДЕЛЯЮТСЯ:
1. гидравлические — передача крутящего момента осуществляется путем использования энергии потока жидкости;
2. электромагнитные - передача момента происходит в результате взаимодействия электромагнитных полей; Различают 2 типа эл. магнитных сцеплений: сухие и с наполнителем.
3. фрикционные – момент передается за счет сил трения между деталями.
Фрикционные муфты сцепления, получившие наибольшее распространение на современных тракторах, в свою очередь могут быть подразделены на группы:
1. по форме поверхностей трения – дисковые (с одним, двумя, и т.д.), конусные, колодочные
2. по конструкции нажимного механизма – на постоянно и не постоянно замкнутые
3. по роду трения – с сухим и работающем в масле
Выбор муфты того или иного типа определяется функциями, которые она должна выполнять, конструкцией механизма, в котором монтируется муфта, типом и назначением САТТОи, главным образом, условиями его эксплуатации.
Однодисковые фрикционные муфты сцепления отличаются высокой «чистотой» выключения по сравнению со всеми другими муфтами. Необходимый для выключений однодисковых муфт зазор между трущимися поверхностями невелик (0,8 – 1 мм ) и его легко обеспечить.
КОНСТРУКЦИЯ муфт сцепления.
1. Диски муфт сцепления
2. Валы муфт сцепления
3. Пружины
|
4. Рычаги выключения
5. Кожух сцепления
6. Картер
Конструкция: ведущая часть (маховик, нажим диск, соеденит эл-т м/д ними, кожух сцепления, нажимные пружины); ведомая часть (первичный вал КП, ведомый диск со ступицей, гаситель крутильных колебаний); механизм выкл сцепления (отжимные рычаги, муфта выкл с выжимным подшипником, направляющие муфты в крышке КП); привод механизма выкл. Используются виды пружин: нажимные пружины: цилиндр переферийная; мягкая пружина допускает большой износ антифрик накладок, но пружина занимает большие габариты; диафрагменная пружина (тарельчатая – лёгкое переключ, значит износ накладок, не треб большого усилия при включ); центральная коническая пружина (хар-ки хуже). При расчёте сначало определяют передаваемый момент исходя из max момента двигателя Temax, и требуемого коэффициента запаса сцепления β, затем определяют основные параметры ведом диска и ссумарные усилия пружин исходя из допустим уд давления на фрик накладки, далее производят расчёт пружин рычагов выкл ведом и нажим дисков, гасителя крут колебаний и шлиц соеденений. Также выполняют расчёт сцепления на нагрев где опред работа буксования и перепад температур, также определяют основные параметры привода сцепл (усилия на педаль, полный и раб ход педали, необход передат число привода).
ЗАДАЧЕЙ РАСЧЕТА ФРИКЦИОННЫХ МУФТ сцепления является определение числа и размеров поверхностей трения, потребной для передачи крутящего момента, силы нажатия на трущиеся поверхности, передаточного числа привода управления и прочих размеров деталей муфты.
Определение геометрических параметров фрикционного сцепления.
В процессе решения этой задачи осваивается методика расчета фрикционных муфт сцепления и определения геометрических параметров сцепления. Для этого определяется значения расчетного момента, передаваемого сцеплением. Изучается влияние конструктивных параметров сцепления на величину передаваемого крутящего момента. Последовательность решения задачи: Задачей расчета фрикционных муфт сцепления является определение числа и размеров поверхностей трения, потребной для передачи крутящего момента силы нажатия на трущиеся поверхности, передаточного числа привода управления и прочих размеров деталей муфты сцепления. На основании данных из справочной литературы определяется модель двигателя, установленная на САТТО, что определяет расчетные значения передаваемого сцеплением крутящего момента. Размеры муфты сцепления определяются исходя из возможности передачи ею крутящего момента, несколько превышающего момент двигателя. Расчет по увеличенному моменту необходим для обеспечения надежной передачи момента двигателя на трансмиссию даже в случае замасливания дисков, небольшого износа поверхностей трения или некоторой потери упругости нажимных пружин. Расчетный момент трения муфты сцепления определяется по формуле:
|
Мр = β * Me, где Мр - расчетный момент трения муфты сцепления, н*м;
Me - максимальный крутящий момент двигателя, н*м; β - коэффициент запаса муфты сцепления. При выборе численного значения коэффициента запаса β руководствуются следующими соображениями. Небольшой коэффициент запаса не может гарантировать надежной передачи крутящего момента. Значение коэффициента запаса β может быть принято из следующих соображений:
Специальная автомобильная техника обычной (нормальной) проходимости (1,3 - 1,4*); Специальная автомобильная техника повышенной проходимости (полноприводные автомобили) (1,5-1,6*); Специальная автомобильная техника высокой проходимости (с числом ведущих осей 4 и более) (1,7 - 2,0); Специальная автотракторная техника (2,0 - 2,5), * - меньшие значения принимаются для двухосных автомобилей, большие для трехосных.
Далее определяется значение момента трения муфты сцепления, который может быть передан рассчитываемой муфтой: Мсц=2π(Rcp)2bμqi, где Мсц - значение момента трения муфты сцепления, который может быть передан рассчитываемой муфтой, н*м; Rcp - радиус приложения равнодействующей сил трения, м; b - ширина трущегося элемента, м; - коэффициент трения; q -допустимое для данного материала удельное давление на поверхность, Па; i- число пар поверхностей трения. Радиус приложения равнодействующей сил трения определяется по следующей формуле: Rcp = 2[(R2)3-(R1)3]/3[(R2)2-(R1)2] где R2 - наружный радиус поверхности трения, м; R1 - внутренний радиус поверхности трения, м. Ширина трущегося элемента определяется по формуле: b = R2 - R1. В свою очередь наружный радиус поверхности трения R2 ограничивается размерами маховика и может быть определен из соотношения: R2 = (0,8....0,85) Rмахов где Rмахов - радиус маховика, м. Радиус маховика задается преподавателем по вариантам в задании на курсовой проект. Внутренний радиус поверхности трения R1 определяется конструктивными соображениями ведомого диска сцепления и связывается следующим соотношением:R1 = (0,5.... 0,7) R2 Число пар поверхностей трения i может быть определено по следующей формуле: i = m + n - 1 где m - число ведущих дисков; n - число ведомых дисков. Если Мр / Мсц > 1, то необходимо провести перерасчет сцепления с увеличением геометрических параметров. Если Мр / Мсц < 0,75, так же требуется перерасчет сцепления в сторону уменьшения геометрических параметров.
|
Если Мр / Мсц = 0,75... 1,0, то расчет принимается и считается законченным. Рассчитывают наружный диаметр ведом диска (если наруж D=300мм, то внутр d=164мм, а толщина накладки = 4,0 мм). Момент передав сцепл Тсц=PссумRсрiμ. Ссумарное усилие пружины Pссум=βTemax/(D+d)iμ. Затем проверяют уд давление на фрик накладки q=Pссум/π(R2-r2). Рассчитывают также нажимное усилие – определяется исходя из момента трения с учётом того что каждый ведомый диск имеет 2 поверхности трения PН=βTemax/f2ZдискаRср. Толщина нажим диска h=0,05D. Задача расчёта пружин – выбор её размеров, начальное нажимное усилие, хар-ка, прочность. Ход сжатия = длина пружины – длина сжатой пружины. Нагрузка на пружину Pmax=Pвык=Pвк+СПΔlвык (СП – жёскость пружины). Число раб витков nраб=GdП4/8DП3СП. Жёскость пружины СП=GdП4/8DП3 nр. Напряжение в пружине τ=8KD/πd3. Рассчитывают ведомый затем ведущий диск.
|
|
История развития пистолетов-пулеметов: Предпосылкой для возникновения пистолетов-пулеметов послужила давняя тенденция тяготения винтовок...
Архитектура электронного правительства: Единая архитектура – это методологический подход при создании системы управления государства, который строится...
Организация стока поверхностных вод: Наибольшее количество влаги на земном шаре испаряется с поверхности морей и океанов (88‰)...
Общие условия выбора системы дренажа: Система дренажа выбирается в зависимости от характера защищаемого...
© cyberpedia.su 2017-2024 - Не является автором материалов. Исключительное право сохранено за автором текста.
Если вы не хотите, чтобы данный материал был у нас на сайте, перейдите по ссылке: Нарушение авторских прав. Мы поможем в написании вашей работы!