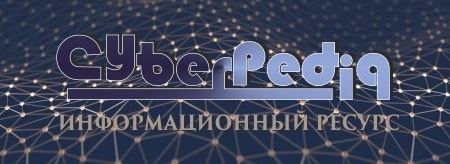
Организация стока поверхностных вод: Наибольшее количество влаги на земном шаре испаряется с поверхности морей и океанов (88‰)...
Кормораздатчик мобильный электрифицированный: схема и процесс работы устройства...
Топ:
Определение места расположения распределительного центра: Фирма реализует продукцию на рынках сбыта и имеет постоянных поставщиков в разных регионах. Увеличение объема продаж...
История развития методов оптимизации: теорема Куна-Таккера, метод Лагранжа, роль выпуклости в оптимизации...
Характеристика АТП и сварочно-жестяницкого участка: Транспорт в настоящее время является одной из важнейших отраслей народного хозяйства...
Интересное:
Аура как энергетическое поле: многослойную ауру человека можно представить себе подобным...
Наиболее распространенные виды рака: Раковая опухоль — это самостоятельное новообразование, которое может возникнуть и от повышенного давления...
Принципы управления денежными потоками: одним из методов контроля за состоянием денежной наличности является...
Дисциплины:
![]() |
![]() |
5.00
из
|
Заказать работу |
Содержание книги
Поиск на нашем сайте
|
|
Изготовление изделий из термопластов литьем под давлением.
Литьё под давлением — технологический процесс переработки пластмасс, цветных металлов и других материалов путем впрыска их расплава под давлением в пресс-форму с последующим охлаждением.
Этот способ позволяет получать изделия сравнительно сложной конфигурации по массе от десятых долей грамма до десятков килограмм с толщиной стенок от 1 до 20 мм (чаще 6-8 мм) при небольших затратах труда и электроэнергии.
Для осуществления литья под давлением применяют плунжерные (поршневые) или шнековые литьевые машины, рис.18
Литьевая машина состоит из трех узлов: инжекционного, прессового, привода и управления.
Инжекционный узел включает: бункер 9 для подачи материала, пластикационный (инжекционный) цилиндр 6, шнек 7 или плунжер 16, гидроцилиндр впрыска 13 с поршнем 12 для поступательного движения шнека при впрыске, привод вращательного движения шнека 10.
Рис. 18. Схема литьевой машины со шнековой (а) и плунжерной (б) пластикации расплава: 1 – гидроцилиндр механизма смыкания; 2 – поршень гидроцилиндра механизма смыкания; 3 – подвижная плита; 4 – полуформы; 5 – неподвижная плита; 6 – пластикационный цилиндр; 7 – шнек; 8 – загрузочное окно цилиндра пластикации; 9 – бункер; 10 – привод шнека; 11 – корпус гидроцилиндра механизма впрыска; 12 – поршень гидроцилиндра впрыска; 13 – гидроцилиндр шнека; 14 – торпеда - рассекатель потока расплава; 15 – дозатор; 16 – плунжер |
Прессовый узел включает плиту 5 с полуформой, подвижную плиту 3 с другой полуформой, гидроцилиндр механизма смыкания 1 с поршнем 2.
|
Назначение прессового узла: обеспечение возможности изготовления изделий различных размеров в пределах определенного ассортимента, перемещении подвижной плиты для смыкания полуформы, создавание усилия запирания формы для предотвращения ее раскрытия под действием давления, возникающего в форме при формовании, перемещение подвижной плиты назад для раскрытия полуформы.
Назначение узлов привода и управления: механизация основных технологических операций, обеспечение заданных параметров и режимов литья, обеспечение выполнения технологического процесса при заданных технологических условиях и режимах.
Технология литья под давлением
Технологическая схема процесса приведена на рис.19.
Технологический процесс литья состоит из следующих стадий: прием сырья, входной контроль сырья, хранение и подготовка сырья, нагревание пресс-материала, дозирование и смыкание пресс-формы; подвод узла впрыска к форме; формование изделия; раскрытие формы и извлечение изделия; контроль качества продукции.
Рис.19. Технологическая схема процесса литья под давлением: 1 – вагон (цистерна), 2 – подвесная кран-балка, 3 – склад материала, 4 – вакуумная сушилка, 5 – литьевая машина, 6 – транспортер, 7 – станок механической обработки, 8 – стол упаковки, 9 – дробилка, 10 – экструдер, 11 – охлаждающая ванна, 12 – гранулятор |
В операциях подготовки особое значение имеет сушка. Переработка невысушенных материалов приводит к получению бракованных изделий с разводами, серебристостью, пузырями. Некоторые термопласты, особенно полиамиды, склонны к деструкции при высоких температурах в присутствии кислорода. Поэтому сушку в атмосферных условиях осуществляют при низких температурах (70-80оС). Для этого используют воздушные сушильные шкафы различных конструкций, а для полиамидов – вакуумные сушильные шкафы.
|
При сушке инфракрасными лампами толщина слоя не должна превышать 30 мм.
Для мелкосерийных производств эффективна установка УСПЭ-301, в которой сушка осуществляется за счет циркуляции материала в потоке горячего воздуха. Циркуляция материала позволит уменьшить время сушки в 10-15 раз и повысить температуру до 150оС.
Время сушки зависит от исходной влажности материала и устанавливается в соответствии с ГОСТ 180361-78.
Подсушенный материал желательно загружать в бункер литьевой машины в горячем состоянии.
Контроль качества просушивания рекомендуется производить методом технологической пробы: на литьевой машине из открытого сопла выдавить расплав, который должен быть однородным, без включений и пузырей, а для прозрачных материалов еще и прозрачным.
Пенистый расплав, небольшие пузыри, «серебро» в деталях указывают на повышенное содержание влаги.
Вопросы для закрепления знаний
1. Литье под давлением-это?
2. Узлы литьевой машины?
3. Стадии процесса?
|
|
Автоматическое растормаживание колес: Тормозные устройства колес предназначены для уменьшения длины пробега и улучшения маневрирования ВС при...
Двойное оплодотворение у цветковых растений: Оплодотворение - это процесс слияния мужской и женской половых клеток с образованием зиготы...
Таксономические единицы (категории) растений: Каждая система классификации состоит из определённых соподчиненных друг другу...
Состав сооружений: решетки и песколовки: Решетки – это первое устройство в схеме очистных сооружений. Они представляют...
© cyberpedia.su 2017-2024 - Не является автором материалов. Исключительное право сохранено за автором текста.
Если вы не хотите, чтобы данный материал был у нас на сайте, перейдите по ссылке: Нарушение авторских прав. Мы поможем в написании вашей работы!