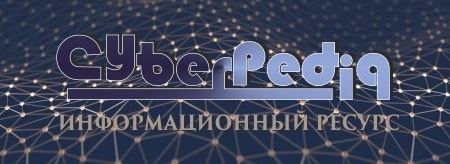
Организация стока поверхностных вод: Наибольшее количество влаги на земном шаре испаряется с поверхности морей и океанов (88‰)...
Типы сооружений для обработки осадков: Септиками называются сооружения, в которых одновременно происходят осветление сточной жидкости...
Топ:
Характеристика АТП и сварочно-жестяницкого участка: Транспорт в настоящее время является одной из важнейших отраслей народного хозяйства...
Проблема типологии научных революций: Глобальные научные революции и типы научной рациональности...
Интересное:
Финансовый рынок и его значение в управлении денежными потоками на современном этапе: любому предприятию для расширения производства и увеличения прибыли нужны...
Влияние предпринимательской среды на эффективное функционирование предприятия: Предпринимательская среда – это совокупность внешних и внутренних факторов, оказывающих влияние на функционирование фирмы...
Аура как энергетическое поле: многослойную ауру человека можно представить себе подобным...
Дисциплины:
![]() |
![]() |
5.00
из
|
Заказать работу |
Содержание книги
Поиск на нашем сайте
|
|
Флюсы классифицируют по назначению, химическому составу, структуре, степени легирования шва, способу изготовления, зависимости вязкости шлака от температуры.
По назначению флюсы делят на три группы:
1) для сварки углеродистых и легированных сталей;
2) для сварки высоколегированных сталей;
3) для сварки цветных металлов и сплавов.
По химическому составу различают флюсы оксидные, солевые и солеоксидные (смешанные). Оксидные флюсы состоят из оксидов металлов и могут содержать до 10% фтористых соединений. Их применяют для сварки углеродистых и низколегированных сталей. Солевые флюсы состоят из фтористых и хлористых солей металлов и других, не содержащих кислород химических соединений. Они используются для сварки активных металлов электрошлакового переплава. Солеоксидные флюсы состоят из фторидов и оксидов металлов, применяются для сварки легированных сталей.
По химическим свойствам оксидные флюсы подразделяют на кислые и основные, а также нейтральные. К кислым относят SiO2 и ТiO2; к основным — CaO, MgO, к химически нейтральным соединениям — фториды и хлориды.
В зависимости от содержания SiO2 различают высококремнистые, низкокремнистые и бескремнистые флюсы, а в зависимости от содержания MnO — марганцевые и безмарганцевые флюсы.
По степени легирования металла шва различают флюсы пассивные, т. е. не вступающие во взаимодействие с расплавленным металлом, активные — слабо легирующие металл шва и сильно легирующие, к которым относят большинство керамических флюсов.
По способу изготовления флюсы делят на плавленые и неплавленые (керамические).
По строению крупинок — стекловидные, пемзовидные и цементированные.
|
По характеру зависимости вязкости шлаков от температуры различают флюсы, образующие шлаки с различными физическими свойствами. Флюсы, у которых вязкость шлаков с понижением температуры возрастает медленно, называют длинными, а флюсы, у которых вязкость шлаков при аналогичных условиях возрастает быстро — короткими. Зависимость вязкости флюсов от температуры существенно влияет на качество формирования шва. Преимущественно находят применение флюсы с короткими шлаками (основные флюсы)
При сварке под флюсом состав флюса полностью определяет состав шлака и атмосферу дуги. Взаимодействие жидкого шлака с расплавленным металлом оказывает существенное влияние на химический состав, структуру и свойства наплавленного металла.
Применительно к углеродистым сталям качественный шов можно получить при следующем сочетании флюсов и сварочной проволоки:
1) плавленый марганцевый, высококремнистый флюс и низкоуглеродистая или марганцовистая сварочная проволока;
2) плавленый безмарганцевый, высококремнистый флюс и низкоутлеродистая марганцовистая сварочная проволока;
3) керамический флюс и низкоуглеродистая сварочная проволока.
Для сварки углеродистых и низколегированных конструкционных сталей чаще всего используют углеродистую проволоку марок Св-08 и Св-08А в сочетании с высококремнистым марганцевым флюсом марок ОСЦ-45, АН-348А, ОСЦ-45М, АН-348АМ (мелкий). Требования к этим флюсам регламентируются ГОСТ 9087 — 81.
Флюсы ОСЦ-45 и АН-348А с зерном 0,35-3,0 мм применяют для автоматической сварки сварочной проволокой диаметром 3 мм и более. Флюсы ОСЦ-45М и АН-348АМ с зерном 0,25 — 1,6 мм применяют для автоматической и механизированной сварки сварочной проволокой диаметром менее 3 мм.
Флюс ОСЦ-45 малочувствителен к ржавчине, дает весьма плотные швы, стойкие против образования горячих трещин. Существенным недостатком флюса является большое выделение вредных фтористых газов. Флюс АН-348А более чувствителен к коррозии, чем ОСЦ-45, но выделяет значительно меньше вредных фтористых газов.
|
Флюсы для высоколегированных сталей
Керамические флюсы.
Изготавливают так же, как и электродное покрытие.
Сухие компоненты шихты замешиваются в жидком стекле. Полученную массу измельчают путем продавливания. Потом прокаливают, просеивают для получения частиц определенного размера.
Частицы сухой смеси могут быть скреплены за счет спекания. Происходит это при повышенных температурах без расплавления. Затем гранулируют до необходимого размера.
Не плавильные флюсы приготавливаются в виде механической смеси. Наиболее распространенны керамические флюсы. По составу близки к составу основного покрытия.
Легирование металла флюсом достигается путем введения в их состав ферросплавов.
Сочетание легирующих элементов может быть различно, а это позволяет получать практически любой состав металла шва.
Это наиболее характерная особенность керамических флюсов.
Химический состав шва также зависит от параметров сварки.
Чтобы определить, как изменились свойства шва, надо замерить твердость в различных местах.
Наиболее критичная зона – зона сплавления и околошовная зона. Керамические флюсы имеют и свои недостатки: малая прочность, вследствие чего в процессе транспортировки или эксплуатации меняют свою грануляцию.
Часто применяют для сварки высоколегированных и специальных сталей, а также для наплавочных работ.
Плавильные флюсы.
Сплавы оксидов и солей металлов. Процесс их изготовления включает следующие стадии:
1. Расчет и подготовка шихты.
2. Выплавка флюса.
3. Грануляция.
4. Сушка, если использовалась мокрая грануляция.
5. Просеивание.
Предварительно измельченные части флюса загружают в дуговые или плавильные печи. После расплавления и выдержки до окончания реакции при температуре 1400 C флюс выпускают из печи.
При сухой грануляции флюс выливается в металлические формы. После остывания отливка дробится, при этом используются валки. Размер частиц 0,1-3 мм. Затем флюсы просеивают.
Сухая грануляция применяется для гигроскопических флюсов, содержащих большое количество фтористых и хромистых солей.
Преимущество этих флюсов в том, что они могут быть использованы несколько раз.
Используют для сварки алюминиевых и титановых сплавов.
|
Мокрый способ грануляции: расплавленный флюс выпускается из печи достаточно тонкой струей и попадает в емкость с проточной водой. В ряде случаев используют дополнительную струю воды.
Далее идет просеивание.
Получают различную грануляцию. Флюс сушат при температуре 250-300 C, а после дробят, если возникает необходимость. После этого просеивают.
Флюс представляет из себя неровные зерна светло-серого, красно-бурого и коричневого цвета.
Транспортируют в герметичной таре, полиэтиленовых мешках, бочках.
Плавильный флюс не может содержать легирующих элементов в чистом виде, так как они окисляются в процессе изготовления. Поэтому легирование происходит путем восстановления окислов флюсов.
В основу классификации флюсов по химическому составу положено содержание в нем оксидов и солей.
Различают окислительные флюсы, имеющие оксид марганца и кремния в составе.
Для получения определенных свойств флюса, в его состав вводят другие компоненты – плавиковый шпат, более прочные оксиды.
Чем больше во флюсе оксида марганца и кремния, тем сильнее он может легировать металл данными элементами, но тем больше он будет окислять этот металл.
Плавильные флюсы применяются для сварки углеродистых и низколегированных сталей.
Безокислительные флюсы практически не содержат оксидов марганца и кремния, в их состав входят фториды, используются для сварки высоколегированных сталей.
Также безокислительные флюсы могут состоять из фтористых и хлоридных солей и элементов, не содержащих кислород.
Используют для сварки высокоактивных металлов – алюминия и титана.
В связи с широким применением флюсов, есть ГОСТ на основные марки: ГОСТ 9087-81 «Флюсы сварочные плавильные».
Регламентирует химический состав.
Различают стекловидный и пемзовидный характер зерна.
Строение зерна зависит от состава расплава флюса, степени его перегрева.
В зависимости от этого, флюс может получаться плотным, прозрачным, пористым, рыхлым.
Следует учитывать, что пемзовидный флюс при том же химическом составе, имеет в полтора-два раза меньший вес, чем стекловидный.
Данные флюсы хуже защищают металл от воздействия воздуха, но обеспечивают хорошее формирование шва при больших плотностях тока и скоростях сварки.
Буквы в обозначениях флюсов:
М – мелкий
С – стекловидный
П – пемзовидный
СП – смешанный
|
|
Особенности сооружения опор в сложных условиях: Сооружение ВЛ в районах с суровыми климатическими и тяжелыми геологическими условиями...
Индивидуальные очистные сооружения: К классу индивидуальных очистных сооружений относят сооружения, пропускная способность которых...
Типы сооружений для обработки осадков: Септиками называются сооружения, в которых одновременно происходят осветление сточной жидкости...
Автоматическое растормаживание колес: Тормозные устройства колес предназначены для уменьшения длины пробега и улучшения маневрирования ВС при...
© cyberpedia.su 2017-2024 - Не является автором материалов. Исключительное право сохранено за автором текста.
Если вы не хотите, чтобы данный материал был у нас на сайте, перейдите по ссылке: Нарушение авторских прав. Мы поможем в написании вашей работы!