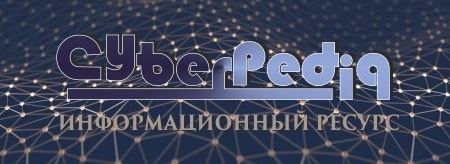
Типы сооружений для обработки осадков: Септиками называются сооружения, в которых одновременно происходят осветление сточной жидкости...
Кормораздатчик мобильный электрифицированный: схема и процесс работы устройства...
Топ:
Характеристика АТП и сварочно-жестяницкого участка: Транспорт в настоящее время является одной из важнейших отраслей народного хозяйства...
Методика измерений сопротивления растеканию тока анодного заземления: Анодный заземлитель (анод) – проводник, погруженный в электролитическую среду (грунт, раствор электролита) и подключенный к положительному...
Определение места расположения распределительного центра: Фирма реализует продукцию на рынках сбыта и имеет постоянных поставщиков в разных регионах. Увеличение объема продаж...
Интересное:
Что нужно делать при лейкемии: Прежде всего, необходимо выяснить, не страдаете ли вы каким-либо душевным недугом...
Как мы говорим и как мы слушаем: общение можно сравнить с огромным зонтиком, под которым скрыто все...
Уполаживание и террасирование склонов: Если глубина оврага более 5 м необходимо устройство берм. Варианты использования оврагов для градостроительных целей...
Дисциплины:
![]() |
![]() |
5.00
из
|
Заказать работу |
Содержание книги
Поиск на нашем сайте
|
|
Помол: грубый (1000—500 мкм), средний (500—100 мкм), тонкий (100-40 мкм) и сверхтонкий (< 40 мкм).
Цель помола — увеличение дисперсности твёрдого материала, придание ему определённого гранулометрического состава и формы частиц.
Оборудование для измельчения также делится на дробилки и мельницы.
Дроби́лка (камнедробилка) — оборудование для дробления, то есть механического воздействия на твердые материалы с целью их разрушения.
Пригодны для разрушения материала на куски меньшего размера. Разделяют в зависимости от крупности дробленного материала дробилки крупного, среднего и мелкого дробления.
По конструкции делятся на:
• Щековая дробилка
• Конусная дробилка
• Молотковая дробилка
• Валковая дробилка
Также к дробильным машинам относятся шаровые мельницы.
Ме́льница — механизм, предназначенный для измельчения, уменьшения размеров частиц сыпучих, а также пастообразных материалов.
По принципу измельчения мельницы подразделяются на:
• шаровые
• шнековые (дробилки)
• молотковые
• центробежно-ударные
• Стержневая мельница
Для помола клинкера с добавками применяют почти исключительно шаровые мельницы производительностью до 50—100 т/ч и более. Клинкер размалывают по открытому или замкнутому циклу с применением одностадийного, а иногда и двухстадийкого измельчения.
Длина шаровых мельниц, работающих по открытому циклу и называемых трубными, в несколько раз превышает их диаметр (в 4—5 раз). В многокамерные мельницы загружают шары нескольких размеров и цильпебс (цилиндрики) одного или двух размеров. При этом необходимо соответствие между удельной поверхностью мелющих тел и размалываемого материала во всех камерах. В первую камеру, где дробятся крупные зерна, помещают обычно более крупные стальные шары диаметром 60—120 мм (в зависимости от размера зерен поступающего клинкера). Вторую камеру заполняют шарами размером 40—60 мм, а третью — мелкими шарами 20—30 мм или цильпебсом размером 20—25 мм.
|
Большое влияние на производительность мельниц оказывает степень заполнения камер мелющими телами. Обычно камеру грубого измельчения заполняют на 26— 32, среднего — на 26—30 и тонкого — на 24—30 %. Однако правильность подбора мелющих тел и степень наполнения при помоле тех или иных материалов должны проверяться по эффективности работы мельницы (часовая производительность ее при заданной тонкости помола и удельный расход электроэнергии). Рациональность ассортимента мелющих тел и степени заполнения контролируют по диаграммам помола (32), которые строят по результатам просеивания проб, отобранных вдоль камер мельницы, через сита № 008, 021, 05, а также более крупные. Расход мелющих тел при помоле известняка и клинкера вращающихся печей составляет ориентировочно 0,8 кг на 1 т продукта.
При помоле материалов наблюдается значительное выделение теплоты, вызывающее нагревание мелющих тел и материала до 120—150 °С и более, что резко отрицательно сказывается на производительности помольных установок.
Положительно влияет на процесс измельчения введение в материал интенсификаторов помола в виде поверхностно-активных веществ (ПАВ): СДБ, мылонафта, петррлатума, триэтаноламина, контакта Петрова, угля и некоторых других веществ. Они повышают эффективность измельчения клинкера, так как понижают его сопротивляемость помолу, а также способствуют уменьшению агрегации частичек материала и их налипанию на мелющие тела. Это объясняется, по-видимому, тем, что указанные вещества адсорбируются активными участками частичек. Различные добавки вводят в количестве 0,02—0,5 % массы цемента.
Трубные мельницы с открытым циклом измельчения применяют для помола сырьевых материалов, а также клинкера. При помоле до удельной поверхности 2800— 3000 см2/г расход электроэнергии достигает 25—30 кВтХ Хч/Т продукта. На 33 показана схема помольной установки с двухкамерной шаровой мельницей, работающей по открытому циклу при помоле клинкера вместе с опокой и гипсом.
|
Для получения цемента с удельной поверхностью 3000—3500 см2/г и выше применяют обычно более экономичные мельницы, работающие в замкнутом цикле с воздушными сепараторами, одно- и двухкамерные. Чаще используют помольные установки с двухкамерными мельницами.
Измельченный в мельнице материал поступает в сепаратор, где из него выделяются фракции тех размеров, какие требуются для готового продукта, а более крупные частицы направляются снова в мельницу на дополнительное измельчение. Таким образом, из материала непрерывно извлекаются наиболее дисперсные частички, которым особенно присуще свойство агрегироваться и прилипать к мелющим телам и стенкам мельницы.
Благодаря этому производительность помольных установок возрастает на 10—20 %.
На помольных установках с сепараторами создается возможность получать высокопрочные быстротвердеющие цементы с удельной поверхностью до 3500—> 4000 см2/г и более при пониженном содержании в них тончайших частиц, быстро теряющих активность. Кроме того, в мельничных установках с сепараторами создаются предпосылки к лучшему охлаждению материала (на 25—35 °С), что положительно сказывается на его измельчении. Эти установки характеризуются большой маневренностью в работе и позволяют выпускать цементы с различной тонкостью помола при постоянных загрузках и размерах мелющих тел. Это недостижимо в мельницах с однократным прохождением материала. Требуемую тонкость помола устанавливают соответствующим регулированием работы сепаратора (скорость воздушных потоков и др.). Недостаток этих установок — их большая сложность и стоимость по сравнению с мельницами, работающими по открытому циклу.
Измельченный материал из мельницы в сепаратор подают элеваторами (ковшовыми и др.) или пневматическим транспортом. В первом случае применяют так называемые сепараторы с замкнутой циркуляцией воздуха, а во втором — сепараторы с проточной вентиляцией воздуха. В них воздух с измельченным материалом просасывается вентилятором из мельницы в сепаратор, где из потока выделяются крупные частицы, направляемые на дополнительный помол в мельницу. Мелкие же фракции выносятся воздушным потоком из сепаратора и осаждаются в циклонах и фильтрах того или иного вида (матерчатых или электрофильтрах) в виде готового продукта.
|
При помоле цемента применяют в основном установки, работающие по схеме мельница — ковшовый элеватор— сепаратор с замкнутой циркуляцией воздуха. Характеризуются они относительной простотой конструкции и пониженным расходом электроэнергии.
Влияние зернового состава вяжущего на его основные свойсва.Требование к зерновому составу.
сновным требованием к сырью в части зернового состава является обеспечение возможности получения скелета требуемой плотности. Для конструкционных материалов сырьё подбирают по максимальной плотности, для теплоизоляционных, напротив - возможно большей пористости. Во всех случаях крайне важно владеть соответствующим аппаратом, позволяющим быстро и надежно подбирать соотношения и расходы различных фракций.
Заполнитель называют однофракционным, в случае если наименьшая и наибольшая крупность его зерен близки и представляют из себяразмеры отверстий смежных сит стандартного набора: 5..10, 10..20, 20..40 мм и т д. Заполнитель крупностью, к примеру, 5...20 мм представляет собой смесь двух фракций: 5..10 и 10..20 мм.
Насыпная плотность, пустотность и другие характеристики заполнителя в значительной степени определяются размерами и формой зерен.
ᴀᴋᴎᴍ ᴏϬᴩᴀᴈᴏᴍ, при подборе оптимальных зерновых составов смеси следует руководствоваться следующими соображениями:
1. Реальные смеси по своему составу должны приближаться к теоретически рассчитанным; при этом исходя из исходного зернового состава сырья крайне важно руководствоваться общими принципами получения непрерывных, прерывистых или комбинированных плотнейших упаковок;
2. Состав смеси должен назначаться с учетом технологических требований, предъявляемых к ним в процессе дальнейшей переработки, – формуемости, спекаемости, нерасслаиваемости и т.д.;
3. Зерновой состав исходной смеси должен обеспечивать получение материала с заданными эксплуатационными свойствами, определяемыми пористостью готового изделия – морозостойкость, газопроницаемость, теплопроводность и т.п.;
4. При назначении состава смеси крайне важно учитывать экономический фактор, включающий энергетические затраты и трудоемкость процессов измельчения и фракционирования исходного сырья, транспортные расходы, объёмы неиспользуемых по прямому назначению отходов и т.п.
|
|
Археология об основании Рима: Новые раскопки проясняют и такой острый дискуссионный вопрос, как дата самого возникновения Рима...
Автоматическое растормаживание колес: Тормозные устройства колес предназначены для уменьшения длины пробега и улучшения маневрирования ВС при...
Адаптации растений и животных к жизни в горах: Большое значение для жизни организмов в горах имеют степень расчленения, крутизна и экспозиционные различия склонов...
Папиллярные узоры пальцев рук - маркер спортивных способностей: дерматоглифические признаки формируются на 3-5 месяце беременности, не изменяются в течение жизни...
© cyberpedia.su 2017-2024 - Не является автором материалов. Исключительное право сохранено за автором текста.
Если вы не хотите, чтобы данный материал был у нас на сайте, перейдите по ссылке: Нарушение авторских прав. Мы поможем в написании вашей работы!