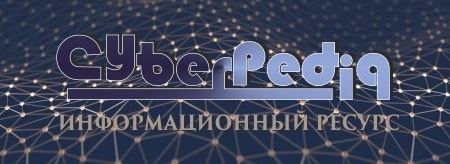
Механическое удерживание земляных масс: Механическое удерживание земляных масс на склоне обеспечивают контрфорсными сооружениями различных конструкций...
Биохимия спиртового брожения: Основу технологии получения пива составляет спиртовое брожение, - при котором сахар превращается...
Топ:
Методика измерений сопротивления растеканию тока анодного заземления: Анодный заземлитель (анод) – проводник, погруженный в электролитическую среду (грунт, раствор электролита) и подключенный к положительному...
Устройство и оснащение процедурного кабинета: Решающая роль в обеспечении правильного лечения пациентов отводится процедурной медсестре...
Проблема типологии научных революций: Глобальные научные революции и типы научной рациональности...
Интересное:
Национальное богатство страны и его составляющие: для оценки элементов национального богатства используются...
Финансовый рынок и его значение в управлении денежными потоками на современном этапе: любому предприятию для расширения производства и увеличения прибыли нужны...
Отражение на счетах бухгалтерского учета процесса приобретения: Процесс заготовления представляет систему экономических событий, включающих приобретение организацией у поставщиков сырья...
Дисциплины:
![]() |
![]() |
5.00
из
|
Заказать работу |
Содержание книги
Поиск на нашем сайте
|
|
Воздушная известь Ее получают умеренным обжигом известняков, мела, доломитизированных известняков и доломитов, содержащих не более 6 % глины. Технология получения воздушной извести состоит из добычи известняков в карьерах, их дробления, сортировки и обжига. Обжиг осуществляют, как правило, в шахтных печах при максимальной температуре в зоне обжига 1000...1200 °С. После обжига куски извести имеют пористую структуру вследствие удаления СОг из известняков. Такая известь называется комовой негашеной. Полученная после обжига комовая известь либо подвергается помолу для получения порошкообразной извести-кипелки (СаО), либо гасится водой для получения гашеной извести Са(ОНг).
При действии воды на комовую известь происходит гидратация оксида кальция:
СаО + НгО - Са(ОН)2 + 65,50 кДж
Процесс гашения извести чрезвычайно экзотермичен, поэтому осуществляется в специальных известигасильных установках и машинах.
Гидравлическая известь — продукт умеренного обжига мергелистых известняков, содержащих 6...20 % глинистых примесей. При обжиге (Т = 900...1000 °С) после разложения углекислого кальция (СаСОз) часть образующегося оксида кальция (СаО) соединяется с окислами SiO2, AI2O3 и БегОз, содержащимися в минералах глины, образуя силикаты, алюминаты и ферриты кальция по реакциям
Эти соединения кальция придают способность гидравлической извести твердеть как на воздухе, так и в воде.
Гидравлическая известь вследствие большого содержания в ее составе свободного оксида кальция при действии на него воды подвергается гашению. Чем больше в гидравлической извести свободных оксида кальция и магния, тем меньше ее способность к гидравлическому твердению.
|
Магнезиальные вяжущие вещества. К ним относятся каустический магнезит (MgO) и каустический доломит (Mgo • СаСОз). Это порошкообразные материалы, получаемые обжигом при 650...850 °С дробленых природных магнезитов и доломитов. Каустический магнезит и каустический доломит при зртворении водой твердеют медленно и имеют небольшую прочность, вследствие чего их затворяют растворами хлористого или сернокислого магния. В этом
случае процесс твердения протекает значительно быстрее, а полученный искусственный камень характеризуется большей прочностью. Каустический магнезит имеет марки 400, 500, 600, а каустический доломит — 100, 150, 200 и 300.
Жидкое стекло. Жидким стеклом называют растворимые соли кремниевой кислоты — Na2O • пЪЮг и КгО • nSiO2. Величина п указывает отношение числа молекул кремнезема к числу молекул щелочного оксида и называется силикатным модулем стекла. Значения его колеблются от 2,31 до 3,5. В практике чаще используют силикат натрия. Получают его расплавлением в стекловаренных печах при температуре 1350...1400 °С тщательно перемешанной смеси размолотых кварцевого песка, кальцинированной соды, или поташа, или сульфата натрия с образованием силикат-глыбы, которую впоследствии подвергают помолу. Тонкомолотые порошки, получаемые помолом силикат-глыбы, могут медленно растворяться в воде. Однако чаще всего жидкое стекло как вяжущее получают обработкой дробленой силикат-глыбы паром в автоклавах при давлении 0,5...0,6 МПа. При твердении под действием углекислого газа силикаты разлагаются по реакции
Na2O
СОг + тЩО = Na2CO3
Однако на воздухе ЭТОТ процесс протекает медленно. Для ускорения твердения вводят добавки кремнефтористого натрия (Na2SiF6). Он вступает в химическую реакцию с жидким стеклом, быстро образуя гель кремниевой кислоты:
Na2SiF6 + Na2SiO3 + 6ЩО -* 6NaF +' 3Si(OH)4
Портландцемент представляет собой порошкообразное гидравлическое вяжущее вещество, твердеющее в воде и на воздухе, состоящее главным образом из силикатов кальция. Получают портландцемент тонким измельчением клинкера с гипсом (3...7 %), допускается введение в смесь активных минеральных добавок (10...15 %). Клинкер — продукт обжига (до полного спекания) искусственной сырьевой смеси, состоящей приблизительно из 75 % карбоната кальция (обычно известняка) и 25 % глины. Основные свойства портландцемента обусловливаются составом клинкера.
|
Химический состав портландцемента. Портландцемент характеризуется довольно постоянным химическим составом. Содержание основных составляющих окислов в нем колеблется в сравнительно небольших пределах, %: CaO (64...67), SiO2 (19...24), AI2O3 <4..,7), Fe2O3 (2...6), MgO (не более 5), SO3 (не менее 1,5 и не более 3,5).
Минералогический состав портландцемента. В процессе обжига сырьевой смеси перечисленные окислы вступают в химическое взаимодействие.
После распада каолинита AI2O3 • SiO2 • 2ЩО -> AI2O3 + 2S1O2 + + 2ЩО и термической диссоциации СаСОз по реакции СаСОз -* -* СаО + СОг в процессе обжига происходит химическое связывание СаО в твердом состоянии по следующим реакциям:
2СаО + S1O2 = 2СаО • SiO2 -- двухкальциевый силикат (Сг8);
ЗСаО + AI2O3 = ЗСаО • AI2O3 — трехкальциевый алюминат (СзА);
4СаО + АЬОз + РегОз = 4СаО • АкОз • РегОз — четырехкальциевый алюмоферрит (C4AF);
2СаО • SiO + СаО = ЗСаО • SiO2 — трехкальциевый силикат (C3S).
Относительное содержание минералов в портландцементом клинкере колеблется в следующих пределах, %: ЗСаО • SiO2 — 42...65; 2СаО • SiO2 - 15...50; ЗСаО • А12Оз - 2... 15; 4СаО • AI2O3 х х Fe2O3 — 10...25.
Для обжига извести применяют печи различных типов: шахтные, вращающиеся и др. Используют также установки для обжига извести во взвешенном состоянии, в кипящем слое, на специальных решетках и т. д.
Наибольшее распространение получили шахтные печи, представляющие собой полый цилиндр, имеющий наружный стальной кожух толщиной около 1 см и внутреннюю огнеупорную кладку, вертикально установленный на фундаменте. Эти печи характеризуются непрерывностью действия, пониженным расходом топлива и электроэнергии, а также простотой в эксплуатации. Строительство их требует относительно небольших капиталовложений.
По характеру процессов, протекающих в шахтной печи, в ней различают три зоны по высоте: подогрева, обжига и охлаждения.
В зоне подогрева, к которой относят верхнюю часть печи с температурой печного пространства не выше 850 °С, материал подсушивается и подогревается поднимающимися раскаленными дымовыми газами. Здесь выгорают также органические примеси. Поднимающиеся газы, в свою очередь, благодаря теплообмену между ними и загруженным материалом охлаждаются и далее отводятся в верх печи
|
Зона обжига размещается в средней части печи, где температура обжигаемого материала изменяется от 850 до 1200°С и затем до 900 °С; здесь известняк удаляется углекислый газ.
Зона охлаждения —нижняя часть печи, В этой зоне известь охлаждается от 900 до 50—100°С поступающим снизу воздухом, который далее поднимается в зону обжига.
Движение воздуха и газов в шахтных печах обеспечивается работой вентиляторов, нагнетающих в печь воздух и отсасывающих из нее дымовые газы. Прогнвоточное движение обжигаемого материала и горячих газов в шахтной печи позволяет хорошо использовать теплоту отходящих газов на подогрев сырья, а теплоту обожженного материала —на подогрев воздуха, идущего в зону обжига. Поэтому для шахтных печей характерен низкий расход топлива.
Вращающиеся печи для обжига извести позволяют получать мягкообожженную известь высокого качества из известняка и мягких карбонатных пород (мела, туфа, ракушечника) в виде мелких кусков. Вращающиеся печи допускают возможность полной механизации и автоматизации процесса обжига. Наконец, в них можно применять все виды топлива — пылевидное твердое, жидкое и газообразное..»
Расход условного топлива во вращающихся печах значителен и достигает 25—30 % массы извести, или 6700—8400 кДж на 1 кг. Недостатки вращающихся печей — большой расход металла на 1 т мощности, повышенные капиталовложения и значительный расход электроэнергии.
Различают длинные и короткие вращающиеся печи. Длинные печи имеют длину до 185 м и более, а короткие — от 40 до 85 м. Первые применяются для мокрого и сухого способов производства, а вторые — для сухого или комбинированного способов.
Длинные печи различаются не только по длине и диаметру, но и по внутреннему устройству барабана. В зависимости от конструкции длинные печи бывают с теплообменными устройствами и без них, виды теплообменных устройств и запечных установок в этих агрегатах также бывают разные.
Запечные установки применяют для предварительной подготовки сырья к обжигу в целях более полного использования тепла дымовых газов, образующихся при сгорании топлива, и снижения расхода последнего.
|
15. Привести технологические схемы получения гипсовых вяжущих на основе ɑ и β-полугидрата сульфата кальция
При тепловой обработке гипсовых пород различных месторождений в заводских условиях можно получать продукты, значительно различающиеся по содержанию отдельных модификаций. Это обусловливается неоднородностью исходного сырья, условиями тепловой обработки и, в частности, скоростью и длительностью нагревания, а также близостью и даже совпадением многих свойств а- и р-модификаций полугидратов, обезвоженных полугидратов и растворимых ангидритов. Характерно, например, что а- и -модификации сульфата кальция в, ряде случаев могут быть получены одновременно при тепловой обработке двуводного гипса в одном, и том же аппарате и даже в одном куске материала.
Улучшению качества полу водного гипса способствует некоторое увеличение продолжительности тепловой обработки, так как создаются более благоприятные условия. для дегидратации гипса и получения продукта с пониженной водоп отребностыо.
Интенсивное выделение воды из двуводного гипса в виде пара приводит к образованию частичек полугидрата с рыхлой губчатой структурой, характеризующейся большой внутренней поверхностью. Это обусловливает повышенную реакционную способность материала. Такая структура характерна для р-полугидрата, отличающегося повышенной водопотребностью при затворении водой в тесто нормальной густоты. Наоборот, при дегидратации двуводного гипса в среде насыщенного пара (особенно под давлением выше атмосферного), а также при его тепловой обработке в водных растворах солей при температуре около 110°С и выше полуводиый гипс получается в виде крупных хорошо оформленных плотных кристаллов «-модификации, характеризующихся пониженной водопотребностью.
Таким образом, регулируя процессы тепловой обработки, можно получать вяжущие с заданными свойствами.
Технологический процесс состоит из отдельных стадий производства (Бэта):
1. дробление исходного сырья
2. помол и сушка сырья
3. обжиг гипсовой мучки в котлах гипсоварочных
Первая стадия производства
Гипсовый камень фракции до 500 мм. поступает с помощью погрузчика и транспортной системы, состоящей из питателей и ленточного конвейера в щековую дробилку, где он дробится до фракции 20-60 мм. В щековой дробилке рабочими элементами являются две щеки: неподвижная и качающаяся, которая циклично приближается и ударяется от неподвижной щеки. При сближении щек кусок гипсового камня разрушается в результате приложения к нему концентрированных силовых воздействий в точках (на линии) соприкосновения с вершиной волны на броневых облицовочных плитах, установленных как на подвижной, так и на неподвижной щеках. Вершины волн на противоположных плитах смещены на ½ шага волны так, что в целом в куске возникает раскалывающе-разламывающие напряжения. Размер фракции регулируется размером выходной щели дробилки. Для регулирования производительности питателя используется шиберная заслонка, регулируемая приводом. Размеры ленточного конвейера подбирается исходя из габаритов участка дробления исходного материала, а также его производительности.
|
Вторая стадия производства
Измельчённый материал до фракции 20 – 60 мм, пройдя железоотделитель, подаётся мельницы тонкого помола. Тонкий помол гипсового камня может осуществляться в аэробильных, шахтовых, роликово-маятниковых, шаровых, молотковых и других мельницах. Основной помольной установкой для измельчения гипса является шахтная мельница, представляющая собой молотковую мельницу с гравитационным сепаратором. Эта мельница служит не только для помола, но и для сушки гипса. В отдельных случаях – и для обжига сыромолотой муки (например, при получении медицинского гипса). Можно применять серийно выпускаемые для угольной промышленности помольные установки, включающие молотковую мельницу и центробежный сепараторов. В таких установках материал измельчается, нагревается и подсушивается. Молотковые сепарируемые мельницы относятся к группе быстроходных молотковых размольных машин и состоят из корпуса, ротора с билами, привода и встроенного сепаратора. Подача материала в мельницу осуществляется по направлению вращения ротора. В результате ударов бил щебень измельчается в порошок. Тонкость помола материала и производительность мельниц зависят от скорости газового потока. В качестве теплоносителя используются отходящие дымовые газы гипсоварочных котлов. Температура дымовых газов при входе в мельницу, в зависимости от выбранного теплового режима обжига гипса в котлах, находится в пределах от 300 до 500 °С. Измельченный, высушенный и отсепарированный до остатка не более 2 - 5% на сите №02 гипсовый порошок выносится в пылевоздушном потоке в систему пылеосаждения. Газопылевая смесь после выхода из мельниц проходит через систему пылеулавливающих устройств (циклоны, батареи циклонов, рукавные фильтры и электрофильтры). Движение газов в системе принудительное и осуществляется за счет работы центробежных вентиляторов. Осажденный в системе пылеочистки гипсовый порошок поступает в расходные бункеры над варочными котлами. В зависимости от температуры газов при выходе из мельниц (85…105°С) температура порошка может колебаться от 70 до 95…10°С.
Третья стадия производства
Варка гипсового порошка происходит в гипсоварочном котле топочными газами с температурой 800-900 °С, подаваемыми по наружным каналам, созданным футеровкой котла и жаровым трубам. Теплоносителем в этих проходах служат продукты сгорания природного газа (жидкого светлого топлива) в специальной топке. Варка гипса производится при постоянном перемешивании и длится 1…2 часа и более. Гипс в варочном котле непосредственно не соприкасается с дымовыми газами, его температура составляет 100-180 °С. Сжигание газообразного (жидкого) топлива происходит в печи обогрева. Первый период - Рабочая температура до 110…120°С соответствует нагреву порошка от температуры при загрузке до температуры начала интенсивной дегидратации гипса. Далее наступает процесс обезвоживания испарения кристаллизационной (гидратной) воды. Этот период внешне характеризуется «кипением массы». Третий период характеризуется быстрым подъемом температуры и резким снижением интенсивности реакций дегидратации. По мере прекращения парообразования и увеличения плотности полученных продуктов дегидратации гипса масса уплотняется и снижается ее уровень в котле (первая «осадка» порошка). Вторая «осадка» порошка наблюдается в последний период варки и соответствует обезвоживанию полугидрата сульфата кальция до растворимого безводного сульфата кальция (ангидрита). Готовый продукт выгружается из котла в приемный бункер, откуда механическим или пневматическим транспортом передается в силосные склады для хранения и отгрузки потребителям.
Альфа
|
|
Индивидуальные и групповые автопоилки: для животных. Схемы и конструкции...
Своеобразие русской архитектуры: Основной материал – дерево – быстрота постройки, но недолговечность и необходимость деления...
Архитектура электронного правительства: Единая архитектура – это методологический подход при создании системы управления государства, который строится...
Археология об основании Рима: Новые раскопки проясняют и такой острый дискуссионный вопрос, как дата самого возникновения Рима...
© cyberpedia.su 2017-2024 - Не является автором материалов. Исключительное право сохранено за автором текста.
Если вы не хотите, чтобы данный материал был у нас на сайте, перейдите по ссылке: Нарушение авторских прав. Мы поможем в написании вашей работы!