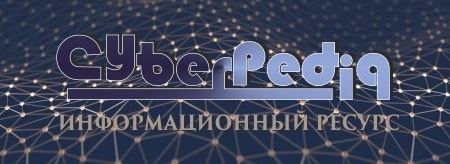
Индивидуальные и групповые автопоилки: для животных. Схемы и конструкции...
Типы сооружений для обработки осадков: Септиками называются сооружения, в которых одновременно происходят осветление сточной жидкости...
Топ:
Генеалогическое древо Султанов Османской империи: Османские правители, вначале, будучи еще бейлербеями Анатолии, женились на дочерях византийских императоров...
Проблема типологии научных революций: Глобальные научные революции и типы научной рациональности...
Характеристика АТП и сварочно-жестяницкого участка: Транспорт в настоящее время является одной из важнейших отраслей народного...
Интересное:
Финансовый рынок и его значение в управлении денежными потоками на современном этапе: любому предприятию для расширения производства и увеличения прибыли нужны...
Лечение прогрессирующих форм рака: Одним из наиболее важных достижений экспериментальной химиотерапии опухолей, начатой в 60-х и реализованной в 70-х годах, является...
Что нужно делать при лейкемии: Прежде всего, необходимо выяснить, не страдаете ли вы каким-либо душевным недугом...
Дисциплины:
![]() |
![]() |
5.00
из
|
Заказать работу |
Содержание книги
Поиск на нашем сайте
|
|
В зависимости от вида извести и условий, в которых происходит ее твердение, различают три типа твердения: карбонатное, гидратное и гидросиликатное.
Карбонатным твердением называют процесс постепенного затвердевания растворных или бетонных смесей, изготовленных на гашеной извести, при воздействии на них углекислоты. Твердение при этом обусловлено одновременным протеканием двух процессов: кристаллизации гидроксида кальция из насыщенного водного раствора и образования карбоната кальция по реакции: Са(ОН)2+; Н-С02+лН20 == СаС08+ (И-1) Н20.
При испарении воды из раствора гелевидная масса известкового теста уплотняется и упрочняется.
Кристаллики образующегося карбоната срастаются друг с другом, с частичками Са(ОН)2 и песка, обусловливая твердение. Объем твердой фазы увеличивается, что приводит к дополнительному уплотнению и упрочнению, твердеющего раствора. Наряду с карбонатом кальция возможно также образование соединений типа СаС03-пСа(ОНЬ-тН2.0.
Испарение влаги и карбонизация растворов протекают очень медленно. Последняя захватывает преимущественно поверхностные слои, что объясняется малой концентрацией С02 в воздухе (0,03 %) и большой плотностью пленки образующегося карбоната, сильно затрудняющей дальнейшее проникание углекислоты к внутренним слоям раствора.
Гидратным твердением называют процесс постепенного превращения в твердое камневидное тело известковых растворных и бетонных смесей на молотой негашеной извести в результате взаимодействия такой извести с водой и образования гидроксида кальция.
Эффект твердения обусловливается взаимным сцеплением и срастанием образующихся субмикроскопических частичек гидроксида кальция. От них зависит и физико-механическая прочность всей системы, состоящей из гидратирующегося вяжущего, воды, заполнителя и воздушных пор.
|
При длительном хранении растворов и бетонов, изготовленных на молотой негашеной извести, в сухих условиях на воздухе наблюдается их упрочнение за счет испарения воды и перехода гидроксида кальция в устойчивый карбонат кальция под действием углекислоты.
Гидросиликатным твердением называют процесс превращения известково-кремнеземистых смесей в твердое камневидное тело, обусловленный образованием гидросиликатов кальция при тепловлажностной обработке в автоклавах насыщенным паром под давлением 0,9— 1,6 МПа, что соответствует температуре 174,5—200 °С. Способ автоклавной обработки известково-пёсчаных камней был предложен В. Михаэлисом в 1880 г.
Высокая температура автоклавной обработки при наличии в обрабатываемом материале воды в жидком- состоянии способствует резкому ускорению химического взаимодействия гидроксида кальция с кварцевым песком или каким-либо другим кремнеземистым компонентом (суглинок, трепел, зола, шлак, керамзит и др.)- Извест-ковопесчаные (силикатные) мелкозернистые бетоны получают из смесей извести (8—12 %) и кварцевого песка (88-92 7о).
При автоклавной обработке в результате взаимодействия извести с кремнеземом образуются значительные количества гидросиликата кальция, обеспечивающие высокую прочность и долговечность изделий. Через 6—12 ч автоклавной обработки получают известково-песчаные изделия прочностью при сжатии 30—50 МПа и более.
В зависимости от вида извести и условий, в которых происходит ее твердение, различают три типа твердения: карбонатное, гидратное и гидросиликатное.
Карбонатным твердением называют процесс постепенного затвердевания растворных или бетонных смесей, изготовленных на гашеной извести, при воздействии на них углекислоты. Твердение при этом обусловлено одновременным протеканием двух процессов: кристаллизации гидроксида кальция из насыщенного водного раствора и образования карбоната кальция по реакции: Са(ОН)2+; Н-С02+лН20 == СаС08+ (И-1) Н20.
|
При испарении воды из раствора гелевидная масса известкового теста уплотняется и упрочняется.
Кристаллики образующегося карбоната срастаются друг с другом, с частичками Са(ОН)2 и песка, обусловливая твердение. Объем твердой фазы увеличивается, что приводит к дополнительному уплотнению и упрочнению, твердеющего раствора. Наряду с карбонатом кальция возможно также образование соединений типа СаС03-пСа(ОНЬ-тН2.0.
Испарение влаги и карбонизация растворов протекают очень медленно. Последняя захватывает преимущественно поверхностные слои, что объясняется малой концентрацией С02 в воздухе (0,03 %) и большой плотностью пленки образующегося карбоната, сильно затрудняющей дальнейшее проникание углекислоты к внутренним слоям раствора.
Известь применяют в виде растворов и бетонов с соотношением известкового теста и заполнителя в пределах 1: 3—1: 5 по объему. Введение надлежащего количества заполнителей важно не только с экономической, но и с технической точки зрения, так как оно способствует улучшению процессов карбонизации и высыхания материала. Последнее особенно важно, поскольку при карбонизации выделяется влага, избыточное накопление которой сопровождается замедлением этого процесса. Обычно карбонизация наиболее интенсивна при влажности растворов и бетонов 5—8 %
Наличие жесткого каркаса из наполнителей в растворах и бетонах способствует также резкому уменьшению усадочных деформаций при их высыхании.
Прочность при сжатии растворов и бетонов на гашеной извести при твердении в обычных условиях в течение месяца достигает небольших значений порядка 0,5— 1 МПа. При длительном твердении в течение многих десятков (а иногда и сотен) лет прочность возрастает до 5—7 МПа. Это обусловливается иногда не только большой степенью карбонизации раствора или бетона, но и некоторым взаимодействием кремнеземистых (в частности, кварцевого песка) и карбонатных заполнителей с гидроксидом кальция.
При введении в известковые растворы или бетоны тоикоизмельчешюго кварцевого песка происходит заметное взаимодействие между известью и кремнеземом даже при обычных температурах 10—20 °С, что способствует ускорению твердения и достижению более высокой прочности. Г. С. Ходаков, Г. И. Логинов, П. А. Ребиндер и другие исследователи объясняют это аморфизацией поверхностных слоев кварцевых частичек при измельчении и возрастающей их активностью во взаимодействии с гидроксидом кальция с образованием гидросиликатов кальция.
|
Получить изделие с помощью искусственной карбонизации известковых растворов и бетонов пытались уже давно. Соответствующие исследования проводились А. А. Байковым еще в начале XX в. Процессы карбонизации изучали также П. А. Пшеницын, И. Н. Завьялов, Н. И. Ильина, К. С. Зацепин и др. Результаты исследований выявили возможность получения с помощью искусственной карбонизации бетонов с высокой прочностью (до 30—40 МПа). Особенно эффективными оказались бетоны на молотой негашеной извести, а также с добавкой мелассы (около 0,2 % по массе извести), способствующей ускорению процесса карбонизации и увеличению прочности.
В послевоенные годы работало несколько установок по изготовлению пустотелых стеновых камней методом карбонизации. Камни формовали из песчаных и шлако-песчаных бетонов на молотой негашеной извести и затем направляли на карбонизацию в специальные камеры, куда из известеобжигательных шахтных печей подавали отходящие газы, содержащие до 28—32 % С02. Получали камни прочностью при сжатии до 5—7 МПа и достаточной морозостойкостью.
Гидратным твердением называют процесс постепенного превращения в твердое камневидное тело известковых растворных и бетонных смесей на молотой негашеной извести в результате взаимодействия такой извести с водой и образования гидроксида кальция.
Эффект твердения обусловливается взаимным сцеплением и срастанием образующихся субмикроскопических частичек гидроксида кальция. От них зависит и физико-механическая прочность всей системы, состоящей из гидратирующегося вяжущего, воды, заполнителя и воздушных пор.
При длительном хранении растворов и бетонов, изготовленных на молотой негашеной извести, в сухих условиях на воздухе наблюдается их упрочнение за счет испарения воды и перехода гидроксида кальция в устойчивый карбонат кальция под действием углекислоты.
|
Гидросиликатным твердением называют процесс превращения известково-кремнеземистых смесей в твердое камневидное тело, обусловленный образованием гидросиликатов кальция при тепловлажностной обработке в автоклавах насыщенным паром под давлением 0,9— 1,6 МПа, что соответствует температуре 174,5—200 °С. Способ автоклавной обработки известково-пёсчаных камней был предложен В. Михаэлисом в 1880 г.
Высокая температура автоклавной обработки при наличии в обрабатываемом материале воды в жидком- состоянии способствует резкому ускорению химического взаимодействия гидроксида кальция с кварцевым песком или каким-либо другим кремнеземистым компонентом (суглинок, трепел, зола, шлак, керамзит и др.)- Извест-ковопесчаные (силикатные) мелкозернистые бетоны получают из смесей извести (8—12 %) и кварцевого песка (88-92 7о).
При автоклавной обработке в результате взаимодействия извести с кремнеземом образуются значительные количества гидросиликата кальция, обеспечивающие высокую прочность и долговечность изделий. Через 6—12 ч автоклавной обработки получают известково-песчаные изделия прочностью при сжатии 30—50 МПа и более.
Твердение известково-кремнеземистых материалов в условиях обработки паром в автоклавах — следствие ряда сложных физических и физико-химических процессов. Изучением этих процессов интенсивно занимались и занимаются в нашей стране Н. Н. Смирнов, И. Ф. Пономарев, П. П. Будников, Ю. М. Бутт, П. И. Боженов, Т. М. Беркович, Л. С. Болквадзе, Б. Н. Виноградов, X. С. Воробьев, К. Э. Горяйнов, Г. И. Книгииа, С. А. Кржемин-ский, М. Я. Кривицкий, К. К. Куатбаев, К- Ф. Ломунов, Л. А. Малинина, С. А. Миронов, А. П. Меркни, А. В. Са-талкин, К. И. Саснаускас, Е. С. Силаенков, А. А. Федии, Л. М. Хавкин, М. С. Шварцзайд и другие исследователи.
Некоторые из основных положений теории автоклавной обработки нзвестково-кремнеземистых материалов разработаны А. В. Волженским в 1932—1935 гг. Согласно этой теории, автоклавная обработка состоит из трех стадий. Первая включает период с момента впуска пара в автоклав до достижения заданной температуры обрабатываемых изделий. Вторая характеризуется постоянством температуры и заданного давления пара в автоклаве. При этом максимальное развитие получают все те химические и физико-химические процессы, которые обусловливают возникновение цементирующих новообразований и твердение известково-песчаных или бетонных изделии. Третья начинается с момента прекращения доступа пара в автоклав и включает время остывания изделий в нем до их извлечения.
Пар, впускаемый в автоклав с отформованными изделиями, охлаждается и конденсируется от соприкосновения с ними и холодными стенками котла. До создания в автоклаве давления пара конденсат образуется преимущественно на гранях изделий, но при постепенном подъеме давления пар начинает проникать в мельчайшие поры материала и превращаться в воду. Таким образом, к воде, введенной при изготовлении изделия, присоединяется еще вода от конденсации пара. Вода в порах растворяет присутствующий здесь гидроксид кальция и другие растворимые вещества, входящие в состав изделия, что также способствует конденсации пара (закон Ф. Рауля), поэтому при обработке изделий паром низкого или высокого давления образование цементирующих веществ протекает в присутствии воды в жидком состоянии. Роль пара при запаривании сводится только к сохранению жидкой воды в материале в условиях повышенных и высоких температур. В отсутствие пара вода испарялась бы, материал высыхал и полностью бы прекращались реакции, связанные с образованием цементирующих веществ.
|
На первой стадии тепловлажностной обработки наблюдается разница температур пара и запариваемого изделия, обусловливающая в последнем значительные напряжения, как термические, так и вызываемые расширяющимися воздухом и водой в порах изделия. Чем больше изделие, чем меньше теплопроводность и выше пористость материалов (например, ячеистых бетонов), тем значительнее термические и иные напряжения при прочих равных условиях.
Как только достигаются наивысшие температуры запаривания, не превышающие обычно 174,5—200 °С (0,9— 1,6 МПа), наступает вторая стадия запаривания. В это время преобладают все те процессы, которые ведут к образованию монолита и начинаются еще во время нагревания изделия паром. К этому моменту его поры в достаточной степени заполнены раствором гидроксида кальция, непосредственно соприкасающимся с кремнеземистыми компонентами. Таким образом, в рассматриваемых условиях взаимодействие между гидроксидом кальция,и кремнеземом, а также гидратация каких-либо компонентов изделия протекают при наличии воды в жидкой фазе.
Чем выше температура, мельче частички кремнеземистого материала и, следовательно, больше их реагирующая поверхность, чем теснее они соприкасаются и легче разлагается данная модификация кремнеземистого материала, тем скорее протекают процессы взаимодействия гидроксида кальция с кремнеземистым материалом и водой при одной и той же концентрации гидроксильных ионов,
При взаимодействии кварца с известью в реакцию в первую очередь вступают гндроксильные ионы, образующиеся при растворении Са(ОН)2 в воде. Они гидрати-руют молекулы SiC>2 и делают их способными к последующим реакциям с ионом кальция. Можно полагать, что под влиянием попов ОН~ происходит разрыв связей — —SiO—SiO— в тетраэдрах кремнезема и образование групп H==SiOH, которые в последующем взаимодействуют с ионами кальция с образованием гидросиликатов кальция.
Сначала при наличии насыщенного раствора гидроксида кальция в известково-песчаных смесях, подвергаемых тепловой обработке при 174,5—200 °С, образуется двухосновный гидросиликат кальция состава (1,8—2,4) CaO'Si02-(l—1,25) Н20. Этот гидросиликат, по системе X. Тейлора, можно обозначить С25а-гидрат. По системе Р. Богга, он имеет формулу C2SH(A). Кристаллизуется в форме призматических пластинок размером до 10— 20 мкм и более. Кроме того, образуется гидросиликат кальция состава (1,5—2)CaO-Si02-/zH20, кратко обозначаемый, по X. Тейлору, С—S—Н (II), а по Р. Боггу, C2SH2 (см. главу 5). В дальнейшем с увеличением температуры и длительности тепловлажностной обработки, сопровождающимся снижением концентрации гидроксида кальция в растворе и увеличением растворимости кремнезема, возникают условия для образования менее основных гидросиликатов кальция. Преимущественно возникают гидроснликаты группы С—S—Н (I), по X. Тейлору, или, по Р. Боггу, CSH (В), химического состава, меняющегося в пределах (0,8—1,5) CaO-Si02- (0,5—2)Н20. Они кристаллизуются в виде тончайших слоистых пластинок, которые при повышенном значении отношения CaO-Si02 свертываются в удлиненные трубки, имеющие вид волокон или игл длиной' до 0,5—1 мкм.
Длительная тепловая обработка способствует образованию хорошо выраженных кристаллов тоберморита, имеющего состав 5CaO-6Si02-5H20(C5S6H5). Новообразования такого состава получаются при изготовлении строительных изделий. из известково-песчаных бетонов в промышленных условиях при продолжительности изотермической выдержки под давлением пара 0,9—1,6 МПа от 4 до 8 ч.
По данным Ю. М. Бутта и Л. Н. Рашковича, Г. Ка-лоусека и др., гидросиликаты группы CSH (В), образующиеся в известково-песчаных смесях при автоклавной обработке, обеспечивают получение бетонов высокой прочности. Тоберморит, а особенно C2SH(A) характеризуются менее выраженными вяжущими свойствами. Надо полагать, что это связано с увеличенным размером частиц таких новообразований. С другой стороны, известково-песчаные бетоны, связанные CSH (В) и отчасти C5S6H5, отличаются пониженной морозостойкостью и повышенной склонностью к усадке при высыхании. Наличие же в бетонах C2SH (А) способствует повышению морозостойкости и стойкости против действия углекислоты воздуха,
Образующиеся малорастворимые низкоосновные гидросиликаты кальция выпадают в виде исключительно-дисперсных субмикроскопических коллоидальных осадков. Последние возникают преимущественно на поверхностях песчинок, окаймляя их по контуру. В процессе запаривания каемки на песчинках утолщаются за счет образования все новых и. новых слоев гидросиликатов кальция. При этом новообразования соединяются в одну общую своеобразную сетку, связывающую все частички песка. В связи с этим целесообразно уплотнение при формовании изделий с помощью вибрации, прессования и др.
Не надо забывать о том, что в условиях кратковременной обработки материалов в автоклавах необходимо быстрое образование значительного количества цементирующих веществ для сцепления всех частичек в единый монолит. Чем компактнее будут уложены все частички в сформованном изделии, тем скорее будет достигнут заданный эффект твердения при минимальном количестве новообразований.
Кристаллы гидросиликатов кальция вначале образуются в коллоидном состоянии и неразличимы даже в оптическом микроскопе, но при наличии водной среды и в условиях высокой температуры с течением времени переходят в более крупные кристаллические образования. К концу запаривания гидросиликаты кальция, а также другие возникшие цементирующие вещества в зависимости от возраста будут иметь различную структуру: образовавшиеся в начале запаривания успеют в какой-то степени перекристаллизоваться, возникшие же на последней стадии запаривания будут еще находиться в виде тонкодисперсных субмикроскопических частичек.
При тепловлажностной обработке в автоклавах прочность известково-песчаных изделий вначале возрастает, достигает некоторого максимума, а затем при длительном запаривании снижается. Это явление характерно для изделий и и а других вяжущих веществах. Причиной прекращения роста прочности и ее падения следует считать затухание процессов возникновения новообразований и структурные изменения, происходящие в пленках новообразований.
В первые часы запаривания рост прочности известково-кремнеземистых изделий обусловливается интенсивным образованием частичек гидросиликатов кальция тончайшей дисперсности, обладающих высокими клеящими (вяжущими) свойствами. С течением времени процесс возникновения гидросиликатов затухает вследствие образования пленок на песчинках, затрудняющих взаимодействие кремнезема и гидроксида кальция. Естественно, что это обстоятельство приводит и к постепенному снижению интенсивности роста прочности системы во времени. Но наряду с образованием высокодисперсных частичек гидросиликатов кальция с самого начала запаривания изделия идет параллельный процесс — увеличиваются размеры ранее образовавшихся частичек, которые превращаются в более крупные кристаллы. Укрупнение частичек гидросиликатов, обусловливающее уменьшение площади контактов между ними, вызывает снижение механических показателей твердеющей системы. С того момента, когда процесс укрупнения частичек вследствие перекристаллизации начинает преобладать над процессом образования новых частичек высокой дисперсности, уже создаются предпосылки не к росту, а к падению прочности изделия. Это подтверждается сопоставлением прочности изделий и удельной поверхности новообразований в образцах из известково-песчаных, цементно-песчаных и шлакопесчаных смесей. При запаривании прочность при сжатии образцов, а также удельная поверхность новообразований вначале возрастают до определенного максимума, зависящего от свойств исходных материалов и температуры тепловой обработки. Дальнейшее запаривание приводит к снижению механической прочности с уменьшением удельной поверхности частичек новообразований вследствие перекристаллизации. Тем самым подтверждается справедливость гипотезы, по которой наибольшая прочность цементного камня, а следовательно, и изделия достигается при максимальной удельной поверхности новообразований.
Третья стадия запаривания начинается с момента прекращения доступа пара в автоклав и кончается в момент извлечения изделия из него. При охлаждении автоклава в теле изделий возникает интенсивное парообразование, что при чрезмерно быстром сбросе давления может нарушить структуру цементирующих веществ и понизить прочность изделия. Это обстоятельство надо учитывать при изготовлении изделий методом автоклавной обработки. Кроме механического воздействия пара на изделия в период его нагревания и охлаждения в автоклаве большое влияние оказывают термические напряжения.
Таким образом, на первой и на последней стадии запаривания изделия подвергаются значительным механическим воздействиям, сопротивляемость же материала их разрушающему влиянию определяется комплексом физико-механических свойств изделия. Отсюда вытекает важный для практики вывод о том, что для каждого изделия, подвергаемого тепловлажностной обработке паром, существуют, определенные критические скорости его нагревания и охлаждения.
При изготовлении известково-кремнеземистых автоклавных материалов успешно применяется молотая негашеная известь, обеспечивающая получение более прочных и долговечных изделий по сравнению с изготовляемыми на гашеной извести. В качестве кремнеземистого компонента используют преимущественно кварцевый песок. Однако целесообразно применение и различных отходов промышленности (золы, шлаки, горелые породы и т.п.). На их основе получают шлакосиликатные, золо-силикатные и тому подобные автоклавные изделия.
Твердение известково-кремиеземистых (в частности, известково-песчаных) изделий в автоклавах интенсифицируют следующими методами:
увеличивают реагирующую поверхность извести и кремнеземистого компонента (песка). Для этого негашеную известь размалывают совместно с песком в соотношении 1:1 —1:2 по массе до удельной поверхности 3000—5000 см2/г; далее эту смесь, рассматриваемую как вяжущее, вводят в немолотый песок в количестве 15— 30 % массы смеси;
подвергают изделия тепловлажностной обработке в автоклавах при давлении пара 1,2—1,5 МПа (оти.), а следовательно, и при повышенных температурах (190— 200°С). Однако применение пара повышенного давления связано с увеличением стоимости автоклавов и котельных установок и в каждом конкретном случае должно быть экономически обосновано. Вместе с тем ряд исследований показал возможность изготовления автоклавных материалов при пониженных давлениях пара (0,2— 0,6 МПа) с использованием в качестве добавок к основному сырью молотых металлургических и электротермо-фосфорных шлаков, зол, горелых пород, кирпичного боя и т. п.;
добавляют в известково-песчаные смеси материалы, более интенсивно реагирующие с известью, чем кварцевый песок, например трепел, диатомит, некоторые вулканические породы, керамзит и др.
Известково-песчаные изделия, полученные обработкой паром в автоклавах, при длительном нахождении в воздушной среде подвергаются воздействию углекислоты воздуха. При этом вначале карбонизируется несвязанный гидроксид кальция (если он остается после автоклавной обработки), а затем и оксид кальция, входящий в состав гидросиликатов. Одновременно происходит разложение гидросиликатов с выделением кремнезема. Прочность изделий при этом либо не меняется, либо даже повышается
Следует отметить, что гидросиликаты, приближающиеся по составу к двухосновным, обеспечивают повышенную долговечность известково-песчаных автоклавных изделий (при их службе в воздушной среде).
Известково-кремнеземистые материалы автоклавного твердения повсеместно применяются в СССР при производстве разнообразных строительных изделий — от силикатного кирпича до крупных блоков и панелей. По производству силикатного кирпича СССР стоит на первом месте в мире (около 15 млрд. шт. в год). В больших количествах выпускаются также силикатобетонные, в том числе армированные сталью, блоки и панели из извест-ково-песчаных мелкозернистых бетонов, что особенно важно для районов, бедных крупным заполнителем. Широко развито и изготовление теплоизоляционных и теплоизоляционно-конструктивных крупных изделий из ячеистых бетонов средней плотностью 300—800 кг/м3.
Распространение исходного сырья, низкая стоимость, а также высокомеханизированные процессы производства с автоклавной обработкой и циклом изготовления изделий 8—12 ч (что пока недостижимо при других методах производства) обусловливают пониженную стоимость получаемой продукции. Стоимость силикатобетонных изделий, в том числе крупных армированных, обычно на 15—20 % меньше стоимости бетонных на основе цемента, Строительные же их качества равноценны. Капиталовложения на "организацию производства силикатобетонных изделий примерно на 10 % меньше капиталовложений в производство железобетонных изделий. В ближайшие годы предстоит дальнейшее увеличение производства крупноразмерных изделий и конструкций, технология которых впервые разработана в СССР.
29. Вяжущие автоклавного твердения. Роль кремнеземистого компонента.
Гидросиликатным твердением называют процесс превращения известково-кремнеземистых смесей в твердое камневидное тело, обусловленный образованием гидросиликатов кальция при тепловлажностной обработке в автоклавах насыщенным паром под давлением 0,9— 1,6 МПа, что соответствует температуре 174,5—200 °С.
Высокая температура автоклавной обработки при наличии в обрабатываемом материале воды в жидком- состоянии способствует резкому ускорению химического взаимодействия гидроксида кальция с кварцевым песком или каким-либо другим кремнеземистым компонентом (суглинок, трепел, зола, шлак, керамзит и др.)- Извест-ковопесчаные (силикатные) мелкозернистые бетоны получают из смесей извести (8—12 %) и кварцевого песка (88-92 7о).
При автоклавной обработке в результате взаимодействия извести с кремнеземом образуются значительные количества гидросиликата кальция, обеспечивающие высокую прочность и долговечность изделий. Через 6—12 ч автоклавной обработки получают известково-песчаные изделия прочностью при сжатии 30—50 МПа и более.
Твердение известково-кремнеземистых материалов в условиях обработки паром в автоклавах — следствие ряда сложных физических и физико-химических процессов. Автоклавная обработка состоит из трех стадий. Первая включает период с момента впуска пара в автоклав до достижения заданной температуры обрабатываемых изделий. Вторая характеризуется постоянством температуры и заданного давления пара в автоклаве. При этом максимальное развитие получают все те химические и физико-химические процессы, которые обусловливают возникновение цементирующих новообразований и твердение известково-песчаных или бетонных изделии. Третья начинается с момента прекращения доступа пара в автоклав и включает время остывания изделий в нем до их извлечения.
Пар, впускаемый в автоклав с отформованными изделиями, охлаждается и конденсируется от соприкосновения с ними и холодными стенками котла. До создания в автоклаве давления пара конденсат образуется преимущественно на гранях изделий, но при постепенном подъеме давления пар начинает проникать в мельчайшие поры материала и превращаться в воду. Таким образом, к воде, введенной при изготовлении изделия, присоединяется еще вода от конденсации пара. Вода в порах растворяет присутствующий здесь гидроксид кальция и другие растворимые вещества, входящие в состав изделия, что также способствует конденсации пара (закон Ф. Рауля), поэтому при обработке изделий паром низкого или высокого давления образование цементирующих веществ протекает в присутствии воды в жидком состоянии. Роль пара при запаривании сводится только к сохранению жидкой воды в материале в условиях повышенных и высоких температур. В отсутствие пара вода испарялась бы, материал высыхал и полностью бы прекращались реакции, связанные с образованием цементирующих веществ.
Как только достигаются наивысшие температуры запаривания, не превышающие обычно 174,5—200 °С (0,9— 1,6 МПа), наступает вторая стадия запаривания. В это время преобладают все те процессы, которые ведут к образованию монолита и начинаются еще во время нагревания изделия паром. К этому моменту его поры в достаточной степени заполнены раствором гидроксида кальция, непосредственно соприкасающимся с кремнеземистыми компонентами. Таким образом, в рассматриваемых условиях взаимодействие между гидроксидом кальция,и кремнеземом, а также гидратация каких-либо компонентов изделия протекают при наличии воды в жидкой фазе.
Чем выше температура, мельче частички кремнеземистого материала и, следовательно, больше их реагирующая поверхность, чем теснее они соприкасаются и легче разлагается данная модификация кремнеземистого материала, тем скорее протекают процессы взаимодействия гидроксида кальция с кремнеземистым материалом и водой при одной и той же концентрации гидроксильных ионов,
Таким образом, на первой и на последней стадии запаривания изделия подвергаются значительным механическим воздействиям, сопротивляемость же материала их разрушающему влиянию определяется комплексом физико-механических свойств изделия. Отсюда вытекает важный для практики вывод о том, что для каждого изделия, подвергаемого тепловлажностной обработке паром, существуют, определенные критические скорости его нагревания и охлаждения.
Твердение известково-кремиеземистых (в частности, известково-песчаных) изделий в автоклавах интенсифицируют следующими методами:
увеличивают реагирующую поверхность извести и кремнеземистого компонента (песка). Для этого негашеную известь размалывают совместно с песком в соотношении 1:1 —1:2 по массе до удельной поверхности 3000—5000 см2/г; далее эту смесь, рассматриваемую как вяжущее, вводят в немолотый песок в количестве 15— 30 % массы смеси;
подвергают изделия тепловлажностной обработке в автоклавах при давлении пара 1,2—1,5 МПа (оти.), а следовательно, и при повышенных температурах (190— 200°С). Однако применение пара повышенного давления связано с увеличением стоимости автоклавов и котельных установок и в каждом конкретном случае должно быть экономически обосновано. Вместе с тем ряд исследований показал возможность изготовления автоклавных материалов при пониженных давлениях пара (0,2— 0,6 МПа) с использованием в качестве добавок к основному сырью молотых металлургических и электротермо-фосфорных шлаков, зол, горелых пород, кирпичного боя и т. п.;
добавляют в известково-песчаные смеси материалы, более интенсивно реагирующие с известью, чем кварцевый песок, например трепел, диатомит, некоторые вулканические породы, керамзит и др.
30. Особенности магнезиальных вяжущих.
Магнезиальные вяжущие вещества характеризуются хорошим сцеплением с органическими материалами (древесными опилками, стружкой и т. п.) и предохраняют их от загнивания. На этом основано применение этих вяжущих для устройства ксилолитовых полов (заполнителем в которых служат древесные опилки), изготовления некоторых материалов (фибролита). Применение. Магнезиальные вяжущие хорошо сцепляются с органическими волокнистыми материалами. Поэтому для их наполнения и армирования используют древесные материалы (опилки, стружки, рейки) На основе магнезиальных вяжущих и древесных стружек получают теплоизоляционный материал — фибролит и легкий и прочный материал для полов с наполнителем из опилок — ксилолит. На заводах изготовляют ксилолитовые плитки, а на стройках делают бесшовные ксилолитовые покрытия полов.
Каустический магнезит используют для устройства особо плотных штукатурок, в том числе искусственного мрамора, и изготовления строительных деталей (подоконных плит, ступеней, скульптурных изделий). Каустический доломит используют для устройства оснований под покрытия пола и изготовления теплоизоляционных изделий.
Все изделия из магнезиальных вяжущих не следует применять в помещениях с повышенной влажностью, так как водостойкость их невысока.
Каустический магнезит — порошок, состоящий в основном из оксида магния и получаемый помолом магнезита, обожженного при 700—800 °С.
В отличие от других вяжущих каустический магнезит затворяют не водой, а растворами хлористого или сернокислого магния. В таком виде его называют магнезиальным цементом. Иногда для затворения применяют ZnCl2, FeS04 и другие соли.
Сырьем для получения каустического магнезита служит магнезит — горная порода, состоящая преимущественно из углекислой соли магния MgC03 в кристаллическом или аморфном состоянии. Кристаллический магнезит— минерал с истинной плотностью 3,1—3,3 г/см3,, Аморфный магнезит представляет фарфоровидную массу с истинной плотностью 2,9—3 г/см3. СССР богат крупными месторождениями высококачественного магнезита, который широко используется в металлургической, химической и строительной промышленности.
Производство каустического магнезита заключается в добыче сырья, его дроблении, обжиге и помоле. При обжиге магнезита он разлагается по реакции MgCC>3 = =MgO-f-C02. Реакция разложения карбоната магния эндотермическая с затратой 1440 кДж теплоты на 1 кг MgC03 или 3030 кДж на 1 кг MgO. Разложение MgC03 начинается примерно при 400 °С, но протекает достаточно полно лишь при 600—650 °С..
При увеличении температуры обжига сверх 800 °С оксид магния постепенно уплотняется и приобретает крупнокристаллическое строение. В таком виде MgO называется периклазом, с водой он почти не взаимодействует.
Нормально обожженный каустический магнезит имеет истинную плотность 3,1—3,4 г/см3. При недожоге истинная плотность каустического магнезита ниже 3,1, а при пережоге — выше 3,4 г/см3 вследствие наличия в нем периклаза с истинной плотностью 3,7 г/см3.
Обжигают магнезит в шахтных с выносными топками, а также во вращающихся печах. Обожженный каустический магнезит измельчают до остатка на сите № 02 не более 5 %, а на сите № 008— не более 25 %
Готовое вяжущее обычно упаковывают в металлические барабаны, чтобы предотвратить его гидратацию. При производстве каустических магнезита и доломита необходимо соблюдать правила техники безопасности и охраны труда.
Доломит — двойная углекислая соль магния и кальция (М^СОз-СаСОз)—слагает горные породы осадочного происхождения. Истинная плотность доломита 2,85— 1,95 г/см3. Обычно доломиты содержат около 20 % MgO, 30 % СаО и 45 % С02. В природе доломит встречается значительно чаще, чем магнезит.
Обжигая доломиты при разных температурах, можно изготовлять каустический доломит, состоящий из MgO и СаСОз и получаемый при 650—750 °С с последующим измельчением; доломитовый цемент, состоящий из MgO, СаО и СаСОз и получаемый при 750—850 °С с последующим измельчением в тонкий порошок, он затворяется водой, а по показателям прочности при сжатии трамбованных образцов из раствора 1:3 через 28 сут твердения на воздухе характеризуется марками 25—50, а также доломитовую известь, состоящую из оксидов магния и кальция и получаемую при 900—950 °С.
Доломит, обжигаемый до спекания при 1400—1500 °С, применяют в качестве огнеупорного материала. Он не взаимодействует с водой и поэтому не обладает вяжущими свойствами.
Каустический доломит должен содержать не менее 15 % MgO и не более 2,5 % СаОСВоб, а значение п. п. п. должно быть в пределах 30—35 %• Его качество определяется содержанием MgO и температурой обжига.
Производство каустического доломита принципиально не отличается от производства каустического магнезита. Доломит в заводских условиях обжигают при 650— 750 °С в шахтных печах с выносными топками и во вращающихся печах.
При затворении каустического доломита растворами солей магния СаО реагирует с ними, образуя хлористый или сернокислый кальций, что отрицательно отражается на качестве затвердевшего каустического доломита.
Каустический доломит должен измельчаться до остатка на сите № 02 не более 5 %, а на сите № 008 не более 25 %. Его вяжущие свойства значительно улучшаются при более тонком помоле. Каустический доломит затворяют водными растворами солей хлористого и сернокислого магния обычно той же концентрации, что и каустический магнезит. Схватывание и твердение каустических доломита и магнезита обусловлены в основном гидратацией MgO и образованием оксихлорида магния или других основных солей.
Истинная плотность каустическ<
|
|
Типы сооружений для обработки осадков: Септиками называются сооружения, в которых одновременно происходят осветление сточной жидкости...
Семя – орган полового размножения и расселения растений: наружи у семян имеется плотный покров – кожура...
Состав сооружений: решетки и песколовки: Решетки – это первое устройство в схеме очистных сооружений. Они представляют...
Механическое удерживание земляных масс: Механическое удерживание земляных масс на склоне обеспечивают контрфорсными сооружениями различных конструкций...
© cyberpedia.su 2017-2024 - Не является автором материалов. Исключительное право сохранено за автором текста.
Если вы не хотите, чтобы данный материал был у нас на сайте, перейдите по ссылке: Нарушение авторских прав. Мы поможем в написании вашей работы!