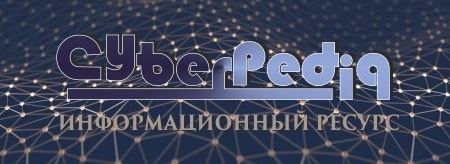
Типы сооружений для обработки осадков: Септиками называются сооружения, в которых одновременно происходят осветление сточной жидкости...
Таксономические единицы (категории) растений: Каждая система классификации состоит из определённых соподчиненных друг другу...
Топ:
Отражение на счетах бухгалтерского учета процесса приобретения: Процесс заготовления представляет систему экономических событий, включающих приобретение организацией у поставщиков сырья...
Методика измерений сопротивления растеканию тока анодного заземления: Анодный заземлитель (анод) – проводник, погруженный в электролитическую среду (грунт, раствор электролита) и подключенный к положительному...
Генеалогическое древо Султанов Османской империи: Османские правители, вначале, будучи еще бейлербеями Анатолии, женились на дочерях византийских императоров...
Интересное:
Отражение на счетах бухгалтерского учета процесса приобретения: Процесс заготовления представляет систему экономических событий, включающих приобретение организацией у поставщиков сырья...
Что нужно делать при лейкемии: Прежде всего, необходимо выяснить, не страдаете ли вы каким-либо душевным недугом...
Инженерная защита территорий, зданий и сооружений от опасных геологических процессов: Изучение оползневых явлений, оценка устойчивости склонов и проектирование противооползневых сооружений — актуальнейшие задачи, стоящие перед отечественными...
Дисциплины:
![]() |
![]() |
5.00
из
|
Заказать работу |
Содержание книги
Поиск на нашем сайте
|
|
Клинкер по сухому способу во вращающихся печах с циклонными теплообменниками, а в новейших системах в сочетании с реакторами (декарбонизаторами) получают по технологической схеме (при использовании известняка и глины), изображенной на 27.
Добывают известняк и глину с учетом их свойств теми же приемами, какие используются при мокром способе производства. Последующая их переработка (дробление, измельчение, смешение компонентов) определяется спецификой сухого способа производства. Добытый известняк вначале подвергают двухстадийному, а иногда одностадийному дроблению до кусков размером 1—3 см. Для этой цели на новых предприятиях часто используют передвижные механизмы, например молотковые дробилки соответствующей производительности. Полученную щебенку направляют на усредиительиый склад, где с помощью комплекса машин осуществляется первичная гомогенизация сырья. Добытую глину вначале также подвергают дроблению при одновременной сушке с последующей подачей полученного материала на усредиительиый склад для гомогенизации. С этих складов известняк и глину направляют через автоматические дозаторы в требуемом соотношении по массе в шаровые мельницы, где осуществляются сушка и тонкий помол •сырья. Для сушки в мельницы направляют дымовые газы, образующиеся во вращающихся печах при сжигании топлива. Шаровые мельницы часто работают в замкнутом цикле с сепараторами (проходными или центробежными). Из мельниц мука в виде пылегазовой смеси направляется в осадительные циклоны, а затем в горизонтальные электрофильтры, в которых выделяется твердая фаза. Иногда для оптимизации работы оборудования в линии устанавливаются охладители газов, в которые в необходимом количестве пульверизируется вода. При этом температура газов, поступающих в электрофильтры, должна держаться на уровне 120—140 °С. В этих условиях остаточное содержание пыли в газах, выбрасываемых в атмосферу, доводится до санитарных норм (75—90 мг/м3).
|
На крупных предприятиях с производительностью одной технологической линии 3000 т клинкера в сутки устанавливают две шаровые мельницы размером 4,2X10 м, дающие 120—130 т/ч муки с остатком 10—12 % на сите № 008.
В настоящее время все шире начинают применять каскадные мельницы без мелющих тел типа «Аэрофол», сырьевые материалы в которых измельчаются под действием падающих кусков самого материала. Эти мельницы применяют для измельчения сырья с влажностью до 20%, а по ряду данных и с большей влажностью. Выпускают их в разных странах в виде барабанов диаметром 5—9 и длиной до 1—2,4 м. Сырье загружают кусками размером до 30—50 см. В мельницу подают горячие газы, которые сушат материал до влажности 0,5— 1 %. Эти же газы выносят измельченный продукт, который затем выделяется из потока в проходных сепараторах и циклонах, причем более крупные частицы возвращаются на домол. Иногда после такой мельницы устанавливают обыкновенную шаровую для домола материала. Расход электроэнергии на помол материалов в бесшаровых мельницах уменьшается по сравнению с расходами на помол в трубных мельницах примерно на 25%- Производительность таких мельниц 250—300 т/ч и более.
Сырьевая мука, получаемая в результате помола в мельницах того или иного типа, направляется на гомогенизацию и корректирование в специальные железобетонные силосы вместимостью до 500—2000 м3 (в зависимости от масштабов производства и однородности сырья). Чем неоднороднее сырье, тем меньше обычно вместимость отдельных силосов. Муку в них перемешивают сжатым воздухом, вводимым через керамические пористые плитки, укладываемые на днище силосов. Иногда вместо керамических применяют специальные металлические плитки или даже перфорированные трубы, покрытые тканью. Воздушные струи, проникающие в муку, аэрируют ее, что сопровождается уменьшением насыпной плотности. Одновременно материал приобретает большую текучесть.
|
После гомогенизации проверяют состав сырьевой муки по содержанию оксида кальция (титр муки). Если оно соответствует требуемому, то смесь направляют на обжиг. Если же выявляется отклонение, то муку из двух силосов направляют в третий в таком соотношении, чтобы получить смесь требуемого состава. После заполнения общего силоса материалы в нем тщательно перемешивают до полной однородности.
При использовании способа непрерывной гомогенизации мука непрерывно подается на верх большого силоса, заполненного уже аэрированной и гомогенизированной смесью. Одновременно у днища силоса непрерывно отбирается готовый материал. Вместимость силоса принимается равной 8—10-кратной часовой производительности мельниц. Высота силосов в 1,5—2 раза больше их диаметра.
Для перемешивания применяют обычно воздух, очищенный от масла и паров воды, под давлением до 0,15— 0,2 МПа. Через 1 м2 пористых плиток подается в 1 мин около 2 м3 воздуха. Затраты электроэнергии на гомогенизацию составляют 0,4—0,6 кВт-ч на 1 т муки; общий расход энергии на всю установку (подача материала в. силосы, его выгрузка и перемешивание) 2,2—2,5 кВтХ Хч/т. В месте выхода готовой муки из силосов устанавливают пробоотборники, автоматически отбирающие пробы массой 10—15 г/т материала. Силосы снабжают также устройствами для обеспыливания отработанного воздуха и удаления воздуха из готовой муки.
В тех случаях, когда муку обжигают во вращающихся печах, снабженных циклонными теплообменниками, сухую смесь из силосов с помощью пневмонасосов того или иного типа направляют в приемный бункер 8 печной установки (28). Отсюда элеватором 7 материал подают на ленточный конвейер-дозатор 6, передающий его в газоход батарейного циклона 4. Здесь он подхватывается отходящими газами из циклона 5 и поступает в циклон 4. Далее таким же образом он проходит газоходы и циклоны 5, 3, 9 и поступает в печь 10. Во время перемещения по газоходам и циклонам сырьевая мука постепенно нагревается и поступает в циклон 9 с температурой 800—850 °С частично (на 30—40%) декарбонизированной. Нагревается мука в газовом потоке циклонных теплообменников очень интенсивно. Циклоны 3 и 9 изнутри футеруют огнеупорами. Газы через систему циклонов движутся под действием дымососа 1. Отработанные газы с температурой 200—300 °С очищаются от пыли в циклоне 2 и в электрофильтрах или же сначала используются для сушки муки.
|
Вращающиеся печи с циклонными теплообменниками имеют размеры 5X75 и 7X95 м, их суточная производительность 1600 и 3000 т. Расход топлива 3250— 3500 кДж на 1 кг клинкера. Мощные печи оснащают двумя ветвями четырехступенчатых теплообменников.
В материале, обжигаемом в рассматриваемых печах, идут те же процессы, что и при обжиге смеси в виде шлама. Полученный клинкер после охлаждения в холодильниках того или иного типа направляют на склад, а затем перерабатывают в цемент.
В последнее десятилетие печные агрегаты с циклонными теплообменниками получили дальнейшее существенное развитие [3]. Был предложен обжиг сырьевой муки по схеме циклонный теплообменник — декарбони-затор— вращающаяся печь. Известно, что около 60% общего количества теплоты, необходимой для получения клинкера, расходуется на декарбонизацию сырьевой муки. В соответствии с этим в новых конструкциях печных агрегатов материал после теплообменников в потоке газов с температурой 800—850 °С поступает з зону, где температура повышается до 1000—1050 °С благодаря сжиганию здесь дополнительного количества топлива. В этой зоне, называемой реактором, в среде раскаленных газов при вихреобразном движении пылевидные частички в течение 70—80 с подвергаются почти полной декарбонизации (85—90%). Отсюда материал с температурой 900—950 °С поступает во вращающуюся печь, где завершаются процессы клинкерообразования и последующего охлаждения продукта. Важно отметить, что почти полная декарбонизация материала и высокая его температура при поступлении в печь дают возможность устанавливать ее с уклоном 3,5—4° и в два-три раза увеличивать частоту ее вращения.
Вынос наиболее теплоемкого процесса декарбонизации из вращающейся печи в специальный реактор с подачей сюда большей части топлива дает высокий технический эффект. Так, по производственным данным, если печи с циклонными теплообменниками дают в сутки около 1,5 т клинкера с 1 м3 объема печи, то у печей, работающих с декарбоыизатором, удельная производительность увеличивается вдвое и более при практически одинаковом расходе топлива (3200—3300 кДж/кг клинкера).
|
В настоящее время печные агрегаты, работающие по схеме циклонные теплообменники — реакторы — печь, получили значительное применение в Японии. Здесь созданы, в частности, различные типы реакторов-декарбонизаторов, включенных в технологические линии производительностью до 3000—5000 т и более клинкера в сутки. В других странах известны обжиговые агрегаты системы «Дополь», в которых последняя ступень теплооб* менников имеет вид шахты, выполняющей роль декар-бонизатора.
На 29 представлена схема обжига клинкера с использованием теплообменников и декарбонизаторов, применяемая на некоторых заводах в Японии. Сырьевая мука, пройдя циклоны, поступает в декарбонизатор, куда также подается топливо и вторичный воздух из холодильника 7 по газоходу 4. Во вращающуюся печь 5 материал поступает с температурой около 1000 °С, почти полностью декарбонизированный и подготовленный к завершающим реакциям образования клинкера.
Как уже указывалось, сырьевую муку при сухом способе производства можно обжигать во вращающихся печах, работающих в сочетании с конвейерными кальцина-торами (печи «Леполь»), а также в шахтных. В том и в другом случаях муку до поступления на обжиг гранулируют и получают гранулы размером от 5—10 до 20— 30 мм. В настоящее время для этой цели используют тарельчатые грануляторы вместо ранее распространенных барабанных.
Вращающиеся печи в сочетании с кальцинаторами (печи «Леполь») характеризуются суточной производительностью 1000—3000 т. Установка, рассчитанная на выпуск 1800 т/сут, состоит из печи размером 5X85 м и кальцинатора с площадью решетки 200 м2. Расход теплоты в печах с кальцина торами примерно 3150— 3550 кДж/кг клинкера. Из вращающейся печи клинкер направляется в холодильник и далее на склад и помол.
Вращающиеся печи с кальцинаторами, часто работающие с пониженными коэффициентами использования по времени (не более 0,8—0,85) и плохо поддающиеся автоматизации, в последние годы реконструируются и переводятся на работу с теплообменниками, что способствует значительному сокращению удельных расходов труда, топлива и электроэнергии и повышению производительности печей.
Шахтные печи рассчитаны на производительность 150—250 т клинкера в сутки. Они работают на короткопламенных видах топлива (антрацит, кокс). Эти печи характеризуются пониженным расходом теплоты—3750—4600 кДж на 1 кг клинкера. Вместе с тем по качеству получаемого клинкера эти печи уступают вращающимся. В СССР в шахтных печах выпускается лишь около 3—4 % всего цемента.
|
Процесс обжига клинкера в современных шахтных печах полностью автоматизирован. Высота шахты 8 — 10, диаметр 2,5—2,8 м. Печь конструкции Гипроцемента имеет высоту 8 и внутренний диаметр 2,85 м. Мощность ее до 250 т клинкера в сутки при расходе теплоты 4200 кДж/кг. В печи обжигается сырьевая мука, смешаиная с топливной крупкой и подвергнутая грануляции. Сырьевая мука и топливная крупка из отдельных бункеров, размещенных над шахтой, с помощью ленточных весовых дозаторов направляются в строго установленном количестве в смесительный шнек, а далее в тарельчатый гранулятор. Отсюда гранулы вращающейся воронкой загружаются в печь, где распределяются ровным слоем. Топливо сгорает за счет воздуха, подаваемого под разгрузочную решетку в низ печи под давлением 25—30 кПа. Часть воздуха поступает непосредственно в зону горения. Предусмотрена также возможность введения некоторого количества воздуха, обогащенного кислородом, в зону интенсивного горения топлива.
Готовый клинкер разгружается с помощью решетки, которая может вращаться с разной скоростью в зависимости от протекания процесса обжига. Чтобы предотвратить выбивание воздуха из печи, при выгрузке продукта устанавливают двух- или трехшлюзовый затвор. Верхнюю часть печи футеруют огнеупором, а внизу устанавливают чугунные кольца, лучше выдерживающие абразивное действие клинкера.
При обжиге материала в шахтных печах сырьевые гранулы вначале подвергаются сушке отходящими дымовыми газами. Затем по мере перемещения их вниз в зону более высоких температур и нагревания до 400— 500 °С в них проходит дегидратация глинистых минералов. В это время начинается горение топлива (антрацита, кокса с содержанием летучих не более 3—5 %), находящегося в гранулах. Это резко повышает температуру материала, что сопровождается декарбонизацией известняка и выделением С02.
Углекислый газ способен взаимодействовать с углеродом по реакции: C-J-C02=F^2CO. Образование СО в массе материала сопровождается возникновением среды, которая может вызвать восстановление оксида железа до Fe304 или FeO, ухудшающих качество клинкера и облегчающих спекание материала в крупные куски и его привары к стенкам печи. Для предотвращения таких нежелательных явлений следует часть воздуха, необходимого для горения топлива, вводить в зону спекания материала. Все это осложняет управление процессами обжига и клинкерообразования в шахтных печах и приводит иногда к снижению качества продукта.
Образовавшийся клинкер в нижней части печи интенсивно охлаждается. Затем его выгружают и направляют, как обычно, на склад и помол.
Разрабатываются также новые способы обжига сырьевых смесей, в частности в «кипящем» слое. Сущность этого способа заключается в том, что через слой мелкозернистой или гранулированной сырьевой смеси просасываются снизу вверх горячие газы со скоростью 1,5— 3 м/с, при которой гранулы находятся в непрерывном возвратно-поступательном движении (в «кипящем» состоянии). При этом происходит интенсивный теплообмен между газами с температурой 1350—1450 °С и материалом.
Ряд исследований показал, что в этих условиях обжиг гранул размером 2—5 мм заканчивается в течение 30—40 мин, причем получаются цементы высоких марок.
По опытам П. Г. Романкова, А. Б. Рашковской, М. М. Сычева и других, при использовании реактора вихревого типа цикл клинкерообразования заканчивается в течение 5—6 мин. Изучается возможность обжига сырьевой муки во взвешенном состоянии в потоке горячих газов с использованием для этой цели топок циклонного типа. Проводятся исследования электротермической обработки сырьевых смесей.
Большой интерес в создании принципиально новой технологии цемента представляют опыты, проведенные сотрудниками Гипроцемента (Н. А. Олесов, И. Г. Абрам-сон, Б. В. Волконский, С. И. Данюшевский и др.) и Института электрофизической аппаратуры им Д. В. Ефремова (В. А. Глухих, Б. И. Альбертинский и др.). Они подвергли облучению ускоренными электронами образцы из сырьевой портлаидцементиои смеси и обнаружили практически полное завершение реакций синтеза клинкера в течение 5—15 с при энергопотреблении 3300± ±300 Дж/г. Клинкер через 28 сут твердения показал прочность 50 МПа. Авторы преимуществами радиацион-ио-химического способа изготовления цементного клинкера считают следующее: скорость протекания реакций клинкерообразования в 100 раз выше обычной, что создает предпосылки для коренного уменьшения габаритов и металлоемкости производственных агрегатов; отказ от применения природного топлива; резкое уменьшение вредных выбросов в атмосферу и повышение уровня технической культуры производства
Процессы помола портландцементного клинкера. Требования по зерновому составу и его влияние на свойства цемента.
Влияние дисперсности портландцемента на его свойства. Многие свойства портландцемента, в том числе активность, скорость твердения, определяются не только химическим и минеральным составом клинкера, формой и размерами кристаллов алита, белита и др., наличием тех или иных добавок, но и в большой степени тонкостью помола продукта, его гранулометрическим составом и формой частичек порошка.
Цементный порошок в основном состоит из зерен размером от 5—10 до 30—40 мкм. Тонкость помола портландцемента характеризуют обычно остатками на ситах с размером ячеек в свету 0,2, 0,08, а иногда и 0,06 мм, а также удельной поверхностью порошка, определяемой на приборах конструкции В. В. Товарова, ПСХ, Р. Блейна, Ф. Ли и Р. Нерса и др. На этих приборах при точно установленных условиях определяют воздухопроницаемость порошка, а затем по показателям проницаемости и пористости рассчитывают удельную поверхность (с использованием зависимости Козени — Кармана).
В настоящее время обычные портландцемента измельчают до остатка на сите № 008 5—8 % (по массе), цементы же быстротвердеющие — до остатка 2— 4 % и меньше. При этом удельная поверхность соответственно достигает 2500—3000 и 3500—4500 см2/г и более.
С увеличением тонкости помола цемента повышается его прочность и скорость твердения, но лишь до показателей удельной поверхности 7000—8000 см2/г. С этого предела наблюдается обычно ухудшение прочностных показателей затвердевшего цемента. Морозостойкость же его часто начинает ухудшаться и при более низких показателях удельной поверхности (4000— 5000 см2/г).
Разные фракции цементного порошка по-разному влияют на прочность цемента при твердении, а также на скорость твердения. В связи с этим ряд исследователей рекомендует характеризовать цементы не только по удельной поверхности порошка, но и по зерновому составу.
Однако некоторые исследователи считают, что чрезмерное измельчение продукта не всегда целесообразно, так как частички 1—3 и даже 5 мкм быстро гидратиру-ются влагой воздуха уже при кратковременном хранении цементов на складах, что значительно снижает активность материала. Некоторые предполагают, что эти высокодисперсные частички при затвореиии цемента водой гидратируются так быстро, что не участвуют в последующем его твердении.
Однако, говоря о влиянии тонких фракций на активность цементов, следует внимательно учитывать как минеральный состав, так и размеры, структуру кристаллов алита, белита и других компонентов клинкера.
Представление о зерновом составе современных портландцементов, а также о влиянии разных фракций на прочность и интенсивность твердения можно составить по данным опытов, которые Р. Я. Цернес, Л. Н. Шорох и А. В. Бугайчук провели на Здолбуновском цементно-шиферном комбинате. Они изучили до 80 партий цементов, полученных помолом в шаровой мельнице, работавшей в замкнутом цикле с двумя сепараторами. Клинкеры характеризовались следующим средним составом, %: C3S 57, C2S 20, С3А 7, C4AF 14; /(# = 0,9. При помоле получались продукты с удельной поверхностью 2000— 6200 см2/г- На основании опытов исследователи рекомендуют для получения цемента той или иной марки измельчать клинкер в порошок, зерновой состав и удельная поверхность которого приведены в табл. 12. Как видно, на показатели активности цементов (прочность в 28-суточ-ном возрасте) влияют фракции порошка с размером частиц до 20 мкм. Более же крупные частицы (до 30— 50 мкм) влияют на прочность в более отдаленные сроки твердения. Авторы исследования полагают, что фракция 0—5 мкм оказывает решающее влияние ча рост прочности цемента в первые сутки твердения, фракция 5—10 мкм влияет в основном на прочность в 3- и 7-су-точном возрасте, а фракция 10—20 мкм определяет прочность в возрасте 1 мес и более. В частности, измельчая один и тот же клинкер до содержания в порошке 45, 50, 65 и 80 % фракции 0—20 мкм, можно получать цементы марок соответственно 600, 700, 700 ОБТЦ (особо быстротвердеющий) и 800 (при испытании трамбованных образцов). Для получения цементов тех или иных марок исследователи рекомендуют и соответствующие схемы помола клинкеров в шаровых мельницах в замкнутом цикле с центробежными сепараторами.
Многочисленные исследования показывают, что характеристики дисперсности цемента по остаткам на ситах (даже на сите с размером ячейки 0,04 мм) и по удельной поверхности не дают надлежащего представления о содержании различных фракций в порошке и поэтому не позволяют исчерпывающе оценить результаты помола и свойства получаемого цемента.
Для определения содержания различных фракций в цементном порошке используют методы воздушной сепарации, а также седиментациоиный и микроскопический анализы.
Зерновой состав цемента представляют часто в виде кривых в системе координат, где по оси абсцисс наносят логарифмы диаметров зерен, исчисленных- в мкм (обычно от 0 до 200 мкм), а на ординате откладывается суммарное содержание в порошке частиц диаметром от принятого до минимального (в % по массе). Для оценки гранулометрического состава портландцементяого порошка применяют также кривые распределения по массе частиц по фракциям. В этом случае по оси абсцисс наносят значения диаметров зерен в мкм (или их логарифмы, а по оси ординат — процентное содержание (по массе) в цементе частиц той или иной отдельной фракции, лежащей между любыми двумя диаметрами, различающимися лишь очень немного (2—4 мкм). На 30 показаны кривые зернового состава портландцемента заводского.помола с удельной поверхностью 3200 и 4500 см2/г.
Некоторые исследователи показали, что при измельчении клинкера в мельницах получаются цементы с разным числом (1—3) максимумов на кривой содержания различных фракций в измельченном материале в зависимости от вида мельницы. Результаты этих опытов свидетельствуют о значительном влиянии вида помольного агрегата и свойств клинкера на зерновой состав цемента, а следовательно, и на его свойства.
Вопрос о том, как связан зерновой состав портландцемента и, в частности, содержание в нем тех или иных фракций с его активностью, водопотребкостыо, пластичностью теста, скоростью твердения и другими свойствами, изучен пока недостаточно. Мало исследованы н возможности регулирования содержания в цементном порошке зерен тех или иных фракций, а также их формы. Можно лишь отметить, что зерновой состав порошка и форма зерен в большой степени зависят от вида мельницы, применения открытого или замкнутого цикла измельчения, формы и размера мелющих тел, а также от бронеплит в шаровых мельницах, соотношения между длиной и диаметром мельниц, степени заполнения камер мелющими телами и др. Вместе с тем влияние этих факторов при измельчении разных материалов проявляется в разной степени в зависимости от их свойств (прочности, твердости, слоистости, степени хрупкости и т.п.).
Для иллюстрации сказанного можно привести результаты опытов Б. В. Волконского, Л. Г. Судакаса, А. Ф. Краюль и др. по определению повышенной активности цементов, получаемых помолом клинкеров монадо-бластической микроструктуры. По их данным, в этом случае цементные частички получаются «щебеночной» формы с острыми углами и сильно развитой конфигурацией, благоприятствующей интенсивному взаимодействию их с водой. Такая форма частичек, образующихся при измельчении клинкера монадобластической структуры, является следствием кристаллохимических особенностей исходного клинкера. При измельчении клинкера с гломеробластической структурой получаются округленные, галькообразные частички, что при прочих.равных условиях (одинаковые химические состав и тонкость помола) обусловливает пониженную активность получаемого цемента (примерно на ЮМПа).
Размалываемость клинкера и способы ее определения. Все твердые материалы характеризуются присущим им сопротивлением измельчению, причем на разных ступенях тонкого измельчения оно может быть различным, что зависит в основном от макроструктуры и физических свойств материала.
В производстве вяжущих веществ тонкому измельчению подвергаются лишь хрупкие материалы, т. е. такие, у которых предел прочности при сжатии в четыре раза и более превосходит предел прочности при растяжении.
Разные твердые материалы в зависимости от их физических свойств при измельчении в одинаковых условиях с затратой одинакового количества энергии дают продукты, характеризующиеся различной степенью дисперсности. Следовательно, они обладают различно выраженной способностью размалываться. В настоящее время нет методов определения размалываемости материалов, позволяющих оценивать ее в абсолютных единицах применительно к различным способам измельчения. Размалываемость материалов приходится оценивать в значительной мере условно применительно к тем или иным способам помола (сухой или мокрый, в открытом или закрытом цикле) и к различным аппаратам измельчения. Так, размалываемость клинкера и других материалов можно оценивать по кварцу, размалываемость которого принята за единицу.
В производстве цемента материалы измельчают преимущественно в шаровых мельницах. В связи с этим и показатели размалываемости материалов изучались, главным образом, применительно к этим аппаратам.
При измельчении цементов в шаровых мельницах до удельной поверхности 3000—3500 см2/г ее прирост практически пропорционален затраченной работе (по закону Риттингера). Лишь при более высоких степенях, когда наступает агломерация тончайших частичек, прирост удельной поверхности сопровождается повышенным расходом энергии. В соответствии с этим предложено оценивать размалываемость материалов по отношению достигнутой степени дисперсности, устанавливаемой по удельной поверхности полученного порошка, к затраченной работе. Пападакис исчисляет удельную поверхность в см2/г, а работу —в Дж, получая таким образом показатели размалываемости в см2/Дж. Для этого он 20— 40 г материала в виде зерен размером 2,5—5 мм разрушал под давлением в цилиндре, а затем измерял удельную поверхность порошка и затраченную работу. Для разных материалов и при разных затратах работы на измельчение, исчисленной в Дж/г, Пападакис получил показатели удельной поверхности порошков, представленные в виде прямых и ломаных линий на 31. Эти данные свидетельствуют о том, что на разных ступенях измельчения некоторые материалы характеризуются разной размалываемостью, которая оценивается по значению удельной поверхности, полученной при измельчении на 1 Дж работы. Так, клинкер, измельченный до удельной поверхности 3000 см2/г, определенной по методу Ф. Ли и Р. Нерса, имел показатель размалываемости 109 см2/Дж, а при более тонком измельчении —лишь 39см2/Дж.
Размалываемость неоднородных тел зависит от природы, количественного соотношения и размера зерен, слагающих тело. Это видно и на примере одного из доменных шлаков, который, как и клинкер, характеризовался конгломератным строением.
ак уже отмечалось, для помола клинкера с добавками применяют почти исключительно шаровые мельницы производительностью до 50—100 т/ч и более. Клинкер размалывают по открытому или замкнутому циклу с применением одностадийного, а иногда и двухстадийкого измельчения.
Длина шаровых мельниц, работающих по открытому циклу и называемых трубными, в несколько раз превышает их диаметр (в 4—5 раз). На заводах применяют мельницы размерами 4X13,5, 3,2X15, 2,6X13 м и др. Их производительность при помоле клинкера до остатка 8—10% на сите № 008 достигает соответственно 90, 50, 25 т/ч. Первые две мельницы могут переключаться также на работу в замкнутом цикле с сепаратором. Приводятся они во вращение двигателями мощностью соответственно 3200, 2000 и 1000 кВт. Трубные мельницы разделяют по длине дырчатыми перегородками на две, три и более камер.
В многокамерные мельницы загружают шары нескольких размеров и цильпебс (цилиндрики) одного или двух размеров. При этом необходимо соответствие между удельной поверхностью мелющих тел и размалываемого материала во всех камерах. В первую камеру, где дробятся крупные зерна, помещают обычно более крупные стальные шары диаметром 60—120 мм (в зависимости от размера зерен поступающего клинкера). Вторую камеру заполняют шарами размером 40—60 мм, а третью — мелкими шарами 20—30 мм или цильпебсом размером 20—25 мм.
Большое влияние на производительность мельниц оказывает степень заполнения камер мелющими телами. Обычно камеру грубого измельчения заполняют на 26— 32, среднего — на 26—30 и тонкого — на 24—30 %. Однако правильность подбора мелющих тел и степень наполнения при помоле тех или иных материалов должны проверяться по эффективности работы мельницы (часовая производительность ее при заданной тонкости помола и удельный расход электроэнергии). Рациональность ассортимента мелющих тел и степени заполнения контролируют по диаграммам помола (32), которые строят по результатам просеивания проб, отобранных вдоль камер мельницы, через сита № 008, 021, 05, а также более крупные. Расход мелющих тел при помоле известняка и клинкера вращающихся печей составляет ориентировочно 0,8 кг на 1 т продукта.
В шаровых мельницах с гладкими бронеплитами, загруженных шарами различного диаметра, мелющие тела во время работы расслаиваются тем больше, чем больше разница диаметров шаров. При этом более крупные шары скапливаются обычно у выходного конца той или иной камеры. Чтобы предотвратить это, мельницы футеруют сортирующими броневыми плитами. В этом случае барабан делят обычно на две камеры, причем камеры грубого и среднего измельчения объединяют в одну и загружают ее шарами различного диаметра. Сортирующие броневые плиты имеют ступенчатый профиль, благодаря чему внутри мельницы образуются конические кольца с углом подъема в сторону разгрузки материала, зависящим от диаметра шаров. Сортирующая конусно-ступенчатая футеровка обеспечивает непрерывную классификацию мелющих тел по длине мельницы, а также необходимую пропорциональность между размером мелющих тел и частицами измельчаемого материала. Для этой же цели используют бронефутеровку так называемого спирального типа.
В СССР применяют преимущественно конусно-ступенчатую кулачковую футеровку из специальной хромо-марганцевой стали. Расход такого металла составляет около 13 г на 1 т цемента при сроке службы более 4 лет.
Расход же обычной марганцовистой стали при гладкой футеровке достигает 100 г/т при сроке службы до 8—9 мес. Применение рациональных видов бронефуте-ровки позволяет увеличить производительность мельниц на 15—20%.
Значительное распространение получает резиновая футеровка мельниц. Ее стойкость против истирания в 3—4 раза выше по сравнению с футеровкой из марганцевой стали. При этом значительно уменьшается шум
При помоле материалов наблюдается значительное выделение теплоты, вызывающее нагревание мелющих тел и материала до 120—150 °С и более, что резко отрицательно сказывается на производительности помольных установок. По данным С. М. Рояка и В. 3. Пироцкого, на измельчение клинкера -до удельной поверхности 2500 см2/г при температуре 40 °С затрачивается около 24, при 120°С —34 и при 150°—39 кВт-ч/т. При тонкости помола до 3300 см2/г с увеличением температуры материала расход электроэнергии еще более повышается (до 130 кВт-ч/т при 150°С). Это объясняется значительной агрегацией наиболее тонких частиц при повышенных температурах вследствие испарения воды, адсорбированной частицами и препятствовавшей их слипанию. В связи с этим размалывать следует только холодный клинкер. Кроме того, большое значение приобретают приемы, способствующие уменьшению температуры материала при его измельчении. Для этого применяют вентиляцию мельниц, а также впрыскивают в них воду. Иногда используют и орошение водой корпуса мельницы снаружи.
Вентиляция достигается просасьтванием через барабан воздуха со скоростью 0,5—0,7 м/с с помощью аспирационной установки, в состав которой входят вентилятор, циклоны, а также рукавные фильтры или электрофильтр. В последних улавливаются тонкие частички, присоединяемые обычно к общей массе продукта.
Большой эффект дает и впрыскивание воды в последнюю камеру мельницы в количестве 1—2 % массы цемента. Это позволяет повысить производительность мельницы на 10%, снизить температуру со 150—200 до 120 °С и повысить степень очистки аспирационного воздуха.
Вода, вводимая в распыленном состоянии, способствует не только значительному снижению температуры материала, но и резко уменьшает агрегацию его частичек и их налипание на мелющие тела. Поэтому целесообразно направлять на помол материал с влажностью около 1—1,5 %. Более высокое содержание влаги уменьшает подвижность цемента, замедляет процесс измельчения, а иногда приводит к замазыванию решеток. Повышение температуры материала в мельнице до 100°С и более способствует испарению из него воды и увеличению склонности сухих частичек к агрегации.
Положительно влияет на процесс измельчения введение в материал интенсификаторов помола в виде поверхностно-активных веществ (ПАВ): СДБ, мылонафта, петррлатума, триэтаноламина, контакта Петрова, угля и некоторых других веществ. Они повышают эффективность измельчения клинкера, так как понижают его сопротивляемость помолу, а также способствуют уменьшению агрегации частичек материала и их налипанию на мелющие тела. Это объясняется, по-видимому, тем, что указанные вещества адсорбируются активными участками частичек. Различные добавки вводят в количестве 0,02—0,5 % массы цемента.
По данным С. М. Рояка и других, наиболее сильно действующими интенсификаторами являются триэтаноламин и его смесь с ССБ (1:1 по массе). Их вводят в первую камеру мельницы в количестве 0,01—0,03 % в виде тонкораспыленного водного раствора, что способствует увеличению производительности мельницы в среднем на 15 %.
По данным кафедры химической технологии Киевского ПТИ, добавка при помоле адипината натрия (отхода капролактамового производства) в количестве 0,1— 0,2 % дает прирост удельной поверхности на 25—30 % и повышает морозостойкость цемента. По ГОСТ 10178—76 (с изм.), для интенсификации процесса помола допускается введение специальных добавок, не ухудшающих качество цемента, в количестве не более 1 % его массы.
Оптимальное количество вводимого в мельницу интенсификатора зависит от свойств его и измельчаемого материала, а также от условий введения его в камеру, Устанавливают его опытным путем.
Трубные мельницы с открытым циклом измельчения применяют для помола сырьевых материалов, а также клинкера. При помоле до удельной поверхности 2800— 3000 см2/г расход электроэнергии достигает 25—30 кВтХ Хч/Т продукта. На 33 показана схема помольной установки с двухкамерной шаровой мельницей, работающей по открытому циклу при помоле клинкера вместе с опокой и гипсом.
Для получения цемента с удельной поверхностью 3000—3500 см2/г и выше применяют обычно более экономичные мельницы, работающие в замкнутом цикле с воздушными сепараторами, одно- и двухкамерные. Чаще используют помольные установки с двухкамерными мельницами.
Измельченный в мельнице материал поступает в сепаратор, где из него выделяются фракции тех размеров, какие требуются для готового продукта, а более крупные частицы направляются снова в мельницу на дополнительное измельчение. Таким образом, из материала непрерывно извлекаются наиболее дисперсные частички, которым особенно присуще свойство агрегироваться и прилипать к мелющим телам и стенкам мельницы.
Благодаря этому производительность помольных установок возрастает на 10—20 %.
На помольных установках с сепараторами создается возможность получать высокопрочные быстротвердеющие цементы с удельной поверхностью до 3500—> 4000 см2/г и более при пониженном содержании в них тончайших частиц, быстро теряющих активность. Кроме того, в мельничных установках с сепараторами создаются предпосылки к лучшему охлаждению материала (на 25—35 °С), что положительно сказывается на его измельчении. Эти установки характеризуются большой маневренностью в работе и позволяют выпускать цементы с различной тонкостью помола при постоянных загрузках и размерах мелющих тел. Это недостижимо в мельницах с однократным прохождением материала. Требуемую тонкость помола устанавливают соответствующим регулированием работы сепаратора (скорость воздушных потоков и др.). Недостаток этих установок — их большая сложность и стоимость по сравнению с мельницами, работающими по открытому циклу.
Измельченный материал из мельницы в сепаратор подают элеваторами (ковшовыми и др.) или пневматическим транспортом. В первом случае применяют так называемые сепараторы с замкнут<
|
|
Папиллярные узоры пальцев рук - маркер спортивных способностей: дерматоглифические признаки формируются на 3-5 месяце беременности, не изменяются в течение жизни...
Археология об основании Рима: Новые раскопки проясняют и такой острый дискуссионный вопрос, как дата самого возникновения Рима...
Архитектура электронного правительства: Единая архитектура – это методологический подход при создании системы управления государства, который строится...
Организация стока поверхностных вод: Наибольшее количество влаги на земном шаре испаряется с поверхности морей и океанов (88‰)...
© cyberpedia.su 2017-2024 - Не является автором материалов. Исключительное право сохранено за автором текста.
Если вы не хотите, чтобы данный материал был у нас на сайте, перейдите по ссылке: Нарушение авторских прав. Мы поможем в написании вашей работы!