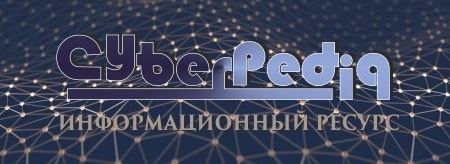
История развития хранилищ для нефти: Первые склады нефти появились в XVII веке. Они представляли собой землянные ямы-амбара глубиной 4…5 м...
Архитектура электронного правительства: Единая архитектура – это методологический подход при создании системы управления государства, который строится...
Топ:
История развития методов оптимизации: теорема Куна-Таккера, метод Лагранжа, роль выпуклости в оптимизации...
Характеристика АТП и сварочно-жестяницкого участка: Транспорт в настоящее время является одной из важнейших отраслей народного хозяйства...
Интересное:
Распространение рака на другие отдаленные от желудка органы: Характерных симптомов рака желудка не существует. Выраженные симптомы появляются, когда опухоль...
Национальное богатство страны и его составляющие: для оценки элементов национального богатства используются...
Финансовый рынок и его значение в управлении денежными потоками на современном этапе: любому предприятию для расширения производства и увеличения прибыли нужны...
Дисциплины:
![]() |
![]() |
5.00
из
|
Заказать работу |
Содержание книги
Поиск на нашем сайте
|
|
Воздушную известь получают путем обжига карбонатных пород при соответствующей температуре и последующей переработке комовой извести.
Комовую негашеную известь получают в специальных обжиговых печах различной конструкции. Молотую негашеную известь получают помолом комовой извести;
гашеную — гашением комовой или молотой негашеной извести; известковое тесто — гашением негашеной извести с большим расходом воды. Гашение (гидратация) извести заключается в затворении комовой или молотой извести (кипелки) водой.
Негашеная известь состоит в основном из оксидов кальция и магния, а гашеная и известковое тесто — из гидроксидов кальция и магния и свободно связанной воды.
В зависимости от качества карбонатных пород известь подразделяют на жирную и тощую. Жирная известь быстро гасится, выделяя при этом много теплоты, на ощупь дает жирное пластичное тесто. Тощая известь после гашения содержит непрогасившиеся зерна, тесто из нее менее пластично.
В соответствии с ГОСТ 9179—77 воздушную известь разделяют на кальциевую, магнезиальную и доломитовую в зависимости от содержания MgO. Для кальциевой извести содержание MgO не должно превышать 5 %, для магнезиальной — 5—20 %, доломитовой—20—40 %.
Технологический процесс производства извести состоит из следующих основных переделов: добыча сырья и его подготовка, обжиг, помол или гашение. Обжиг известняка производят в шахтных или вращающихся печах. При обжиге в шахтных печах известняк дробят до размеров 60—200 мм, а во вращающихся (сушильных барабанах) — до 5—40 мм.
Шахтную печь загружают послойно известняком и короткопламенным твердым топливом (антрацитом или коксом). По высоте печь условно подразделяют на три зоны: подогрева, обжига и охлаждения. В нижнюю часть печи — зону охлаждения ссыпается обожженная известь. Воздух, подаваемый снизу, нагревается за счет теплоты кусков извести, поднимается вверх и попадает в зону обжига. Температура в этой зоне достигает 1200°С. Здесь происходит выгорание топлива и разложение углекислого кальция с образованием оксида кальция и углекислого газа.
|
Горячие газы вентилятором (дымососом) просасываются вверх и подогревают вышележащие слои топлива и материала. В зоне подогрева известняк подсушивается и органические примеси в нем выгорают. Так как в зоне обжига слой топлива сгорает, то вышележащие слои опускаются и новые подогретые порции известняка поступают в зону обжига. Готовый продукт через выгрузочный механизм и барабанный затвор отправляется на склад готовой продукции.
Известь из вращающихся печей получается более высокого качества, но при этом затрачивается больше топлива, условный расход которого достигает 25—30 % по массе извести.
Комовую известь перед употреблением следует измельчить или загасить. Помол извести проводят в трубных мельницах по замкнутому циклу. Измельчают ее до удельной поверхности 3500—5500 см2/г совместно с активными минеральными добавками (доменные или топливные шлаки, золы, пуццоланические породы и т. д.). Если предполагается использование извести при производстве автоклавных изделий, то в качестве добавки вводят кварцевый песок. Для замедления скорости гашения можно добавлять двуводный гипс в количестве 3—5 % по массе извести.
Хранят комовую и молотую известь на крытых механизированных складах. Срок хранения не должен превышать 10—15 сут, так как иначе активность извести снижается. Транспортируют комовую известь в крытых вагонах или контейнерах, молотую — в битуминизиро- ванных мешках, вагонах или автоцементовозах.
Отличительная особенность негашеной извести — ее тонкое измельчение химическим путем — гашением. Достигается это взаимодействием оксида кальция с водой и получением частиц гидроксида кальция размером до 0,01 мм: Ca0 + H20=Ca(0H)2 + Q. При гашении выделяется большое количество теплоты. При гашении извести резко поднимается температура и вода закипает. Если известь хорошего качества, то гашение начинается и проходит быстро. Скоростью гашения можно управлять. Хлористые соли NaCl, СаС12 и др., находящиеся в воде, в количестве до 1 % ускоряют гидратацию СаО. Гипс, Na2S04 и некоторые ПАВ замедляют гашение. Повышение температуры гашения ускоряет процесс гидратации СаО. Зависит скорость гашения и от величины кристаллов оксида кальция. Крупные кристаллы гидра- тируются медленнее. Переход оксида в гидроксид сопровождается не только выделением теплоты, но и резким увеличением объема, иногда более чем в 2 раза.
|
Полученная гидратная известь подразделяется на пушонку и известковое тесто. Пушонка—тонкодисперсный порошок с большой удельной поверхностью, характеризующийся большой водопотребностью. Известковое тесто — сметанообразная паста, состоящая в основном из Са(ОН)2. Для изготовления пушонки добавляют воды по массе в 2—3 раза больше, чем извести, так как происходит интенсивное испарение воды. При большем увеличении количества воды получим известковое тесто.
В промышленных условиях известь гасят в аппаратах периодического и непрерывного действия. В гасильном барабане периодического действия (2.16) гашение проводится паром под давлением 0,3—0,5 МПа. Вместимость барабана 15 м3. Куски извести размером 3—5 мм через загрузочный люк сверху загружают в барабан. Затем подают пар, и при вращении барабана в течение 15—20 мин происходит гашение извести. Частота вращения 3—5 об/мин. На загрузку и разгрузку барабана уходит тоже 15—20 мин. Весь цикл длится 30—40 мин.
Интенсивность гашения возрастает при использовании подогретой воды. На этом способе основана конструкция термомеханической известегасилки непрерывного действия. Подогрев воды осуществляется за счет теплоты гашения извести. Гасильный барабан состоит из двух цилиндров, вставленных один в другой с зазором 12 мм. Пространство между ними служит теплообменником. Поступающая сюда вода нагревается от поверхности внутреннего цилиндра, в котором гасится известь, а затем направляется на гашение
|
В Для производства строительной воздушной извести применяются известняки и мел.
ИЗВЕСТНЯКИ - мелкокристаллические плотные, прочностью 20 до 60 МПа, с содержанием
СаСО3 от 100 до 72-47%,
MgСО3 от 0 до 45%,
∑Al2O3+ Fe2O3 от 3 до 8%.
СЫРЬЕВЫЕ МАТЕРИАЛЫ. Для производства воздушной извести применяются все природные материалы, содержащие в основном углекислый кальций (мрамор, известняк, известковый туф мел, и т.д.). Карбонатные породы практически повсеместно распространены на территории России, что способствует широкому развитию производства из них вяжущих материалов. Основным химическим соединением, являющимся основой большинства разновидностей карбонатных пород, является углекислый кальций – CaCO3.
Теоретический состав химически чистого углекислого кальция: 56 % СаО и 44 % СО2. Углекислый кальций встречается в природе в виде трех минералов: кальцита, арагонита и ватерита. Кальцит или известковый шпат кристаллизуется в гексагональной системе, плотность его 2600 - 2800 кг/м3, твердость по шкале Мооса - 3.
Основными литологическими разновидностями известняков, выделяемыми по структурным признакам, являются известняки кристаллические, органогенные, обломочные и известняки смешанной структуры. Кристаллические известняки сложены кристаллами кальцита, которые могут быть различных размеров. Плотность кристаллических плотных известняков колеблется в пределах от 2400 до 2800 кг/м3, такие известняки имеют предел прочности при сжатии до 120 МПа. Органогенные известняки - это скелетные остатки животных (зоогенных) или растительных (фитогенных) организмов, состоящие из кальцита или арагонита и цементирующей их массы — микрокристаллического кальцита. Обломочные известняки представляют собой обломки ранее сформировавшихся известняков и кальцитового цемента. Известняки со смешанной структурой являются переходными разновидностями между кристаллическими, органогенными и обломочными известняками.
Известняковые горные породы обычно содержат различные примеси, главным образом глинистых веществ, доломита, кварца, оксида железа. Количество примесей колеблется в довольно значительных пределах. Даже сравнительно чистые известняки содержат 2 - 3 % примесей.
|
Самостоятельной разновидностью известняков является мел, который представляет собой рыхлую слабоцементированную тонкозернистую породу с землистым изломом, состоящую из тонкого органогенного кальцита. Существуют и другие разновидности известняков химического происхождения: оолитовые известняки, состоящие из округлых зерен карбоната кальция, с диаметром зерен от 1 – 2 мм и более. Оолитовые известняки, известковые туфы, мел и известняки- ракушечники имеют предел прочности при сжатии 0,5 - 50 МПа при плотности 100 - 1800 кг/м3 (мел имеет плотность от 1400 да 2400 кг/м3). Мел представляет собой мягкую, легко растирающуюся карбонатную породу. Рыхлая структура мела облегчает его добычу, но затрудняет обжиг в шахтных печах, так как куски мела легко крошатся, а образующаяся мелочь заполняет пространство между обжигаемыми кусками, ухудшая тягу и аэродинамический режим работы печи. При обжиге мела во вращающихся печах затруднений не встречается.
Прочность некоторых видов мрамора достигает 300 МПа, при плотности 2900 - 3100 кг/м3. Влажность мрамора составляет до 3 %, известняков 3 - 10 %, а мела – 15 - 25 %.
ПО ВЕЩЕСТВЕННОМУ СОСТАВУ КАРБОНАТНЫЕ ПОРОДЫ ДЛЯ ПРОИЗВОДСТВА ИЗВЕСТИ ДЕЛЯТСЯ НА ПЯТЬ КЛАССОВ.
Из карбонатных пород класса А получают кальциевую жирную известь. Из пород классов Б и В производят маломагнезиальную известь, в первом случае более жирную, а во втором — более тощую. Породы класса Г применяются для производства доломитовой, а класса Д — гидравлической извести.
Влияние качества известняка проявится на качество извести следующим образом:
- Если СаСО3 – 100-96%; MgСО3 до 3%; ∑Al2O3+ Fe2O3 до 2.5% (А)
Известь кальциевая, «жирная», дающая высоко пластичное тесто.
- Если СаСО3 –95 - 85%; MgСО3 до 5%; ∑Al2O3+ Fe2O3 до 3-8%
Известь кальциевая, «тощая».
Наличие MgСО3 в сырье проблематично по следующим причинам: процесс обжига известняка протекает в интервале 800-1100 град, а разложение карбоната магния начинается при температурах 600-700 град. в результате разложения получают MgО, частицы которого начинают оплавляться.
Примеси глины особенно учитываются при высоких температурах обжига, т.к. минералы глины участвуют в процессах синтеза новых минеральных фаз, при низких температурах обжига являются балластом в готовом продукте, но если после обжига произведен помол и выпускаемый продукт молотая негашеная известь, то примеси глины, прошедшие дегидратацию, являются добавкой пуццоланического действия.
Примеси железистых соединений (особенно пирит) вредны, при высоких температурах обжига ~ 1200٥ вызывают образование легкоплавких эвтевтик, способствующих интенсивному росту кристаллов окиси кальция, полученная известь медленно реагирует с водой при гашении, кроме этого в составе продукта увеличивается количество «пережога».
|
Технология производства извести включает: операции по добыче, транспортировке и хранению сырья; процессы дробления и сортировки известняка; обжиг известняка и охлаждение готового продукта – комовая негашеная известь; хранение и отгрузку. В технологическую схему может быть включено оборудование по помолу продукта обжига – молотая негашеная известь; гасильное оборудование – гидратная известь.
ОСНОВНАЯ ТЕХНОЛОГИЧЕСКАЯ ОПЕРАЦИЯ – ОБЖИГ, ДИССОЦИАЦИЯ КАРБОНАТА КАЛЬЦИЯ С ОБРАЗОВАНИЕМ СаО И СО2
СаСО3 ←→ СаО + СО2↑
ЗАТРАТЫ ТЕПЛА – 1780 КДЖ НА 1 КГ СаСО3, НА 1 КГ СаО 3200 КДЖ.
Процесс топохимический, обратимый (направление процесса зависит от температуры и давления углекислого газа). Для обеспечения процесса необходим отвод углекислого газа из печного пространства.
Температурный интервал процесса 800-1100٥. В процессе обжига необходимо обеспечить полноту протекания процесса и получить вяжущее с высокой реакционной способностью.
Факторы, определяющие полноту процесса:
Качество сырья;
Крупность обжигаемого сырья – размер кусков;
Назначение температуры обжига
Режим обжига
Вид печного агрегата.
Влияние размера. Разложение СаСО3 начинается с поверхности и постепенно распространяется к внутренней части куска
Продвижение фронта диссоциации зависит от температуры в печи, так при температуре 800° продвижение 2 мм/час, 1100° – 14 мм/час. По мере продвижения фронта диссоциации скорость разложения снижается, т.к. образовавшийся на поверхности куска продукт обеспечивает сопротивление теплопередаче и замедляет диффузию СО2 через слой уже обожженного материала. Следовательно, когда обжигаются куски крупного известняка для полного протекания процесса необходимо повысить температуру, но! Возникает опасность пережога. Под пережогом понимают получение при обжиге оплавленных зерен, которые при охлаждении остекловываются, и как следствие реакционная способность резко падает. В течение длительного промежутка времени происходит постепенное разрушение остеклованной «оболочки» и возникают условия для гидратации внутренней части зерна. Однако процесс гидратации протекает когда камень уже затвердел, поэтому продукты гидратации занимающие объем больше, чем исходные приводят к появлению внутренних растягивающих напряжений, способных не только привести к образованию микродефектов, но и к разрушению камня. Чем больше образовано пережога, тем вероятнее разрушение камня. Особенно опасен подъем температуры, если в сырье присутствует карбонат магния. При температурах порядка 1100°-1200° происходит плавление, а при охлаждении образуется остеклованый продукт, называемый периклазом, гидратация которого может произойти в длительные сроки (через год).
Поэтому дробление и сортировка известняка перед обжигом обязательны и размер зерен должен строго отвечать условиям обжига.
В Л И Я Н И Е
Температура обжига.
• В зависимости от температуры обжига получают известь различной: микроструктуры,
• величины и формы кристаллов СаО и MgО,
• размеру пор и их распределение по массе куска обожженного продукта.
Так при низкой температуре обжига 800-850٥, известь будет представлена мелкокристаллической фазой с размером зерен ~ 0.3 мкм (микрон), решетка неупорядочена, в продукте присутствует неразложившийся СаСО3. Поры микро капиллярные с радиусом около 80 А٥, удельная поверхность 50 м²/г. Полученная известь будет малоактивной.
Повышение температуры обжига до 900٥ способствует перестройке структуры, упорядочению кристаллической решетки с одновременным ростом кристаллов до 0.5-0.6 мкм. Поры крупные, величина удельной поверхности – 4-5 м²/г. Известь обладает наибольшей реакционной способностью.
Температура 1000٥ происходит частичное спекание, размер кристаллов увеличивается до 1-2 мкм. Реакционная способность падает.
Температура 1300٥. За счет наличия в исходном сырье железистых примесей происходит укрупнение кристаллов, их оплавление, возникает опасность подваров к футеровке печи, может произойти зависание материала в шахте.
Температура 1400٥ размер кристаллов извести 10-20 мкм, протекает реакция между СаО и примесями (глиной) с образованием силикатов, ферритов, алюминатов кальция и магния. Состав продуктов β 2СаОSiO2, CaOAl 2O3, 2CaOFe2O3 реакционная способность данных соединений иная, чем у СаО.
Режим обжига. Характеризуется не только максимальной температурой в зоне обжига, но и скоростью подъема температуры, скоростью охлаждения продукта обжига.
Быстрый подъем температуры и интенсивный спад обеспечивают получение извести с высокой реакционной способностью и минимальным количеством пережога.
Равномерный замедленный подъем температуры и такой же спад – известь среднегасящаяся, в состав будет входить пережог в виде периклаза, кроме этого низкоосновные силикаты, ферриты и алюминаты кальция.лияние параметров процесса обжига известняка на свойства готового продукта.
|
|
Типы оградительных сооружений в морском порту: По расположению оградительных сооружений в плане различают волноломы, обе оконечности...
Своеобразие русской архитектуры: Основной материал – дерево – быстрота постройки, но недолговечность и необходимость деления...
Опора деревянной одностоечной и способы укрепление угловых опор: Опоры ВЛ - конструкции, предназначенные для поддерживания проводов на необходимой высоте над землей, водой...
Адаптации растений и животных к жизни в горах: Большое значение для жизни организмов в горах имеют степень расчленения, крутизна и экспозиционные различия склонов...
© cyberpedia.su 2017-2024 - Не является автором материалов. Исключительное право сохранено за автором текста.
Если вы не хотите, чтобы данный материал был у нас на сайте, перейдите по ссылке: Нарушение авторских прав. Мы поможем в написании вашей работы!