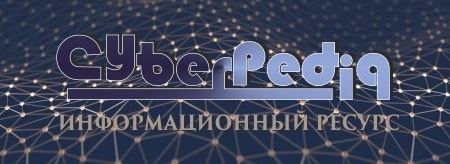
Организация стока поверхностных вод: Наибольшее количество влаги на земном шаре испаряется с поверхности морей и океанов (88‰)...
Таксономические единицы (категории) растений: Каждая система классификации состоит из определённых соподчиненных друг другу...
Топ:
Организация стока поверхностных вод: Наибольшее количество влаги на земном шаре испаряется с поверхности морей и океанов...
Оснащения врачебно-сестринской бригады.
Оценка эффективности инструментов коммуникационной политики: Внешние коммуникации - обмен информацией между организацией и её внешней средой...
Интересное:
Что нужно делать при лейкемии: Прежде всего, необходимо выяснить, не страдаете ли вы каким-либо душевным недугом...
Влияние предпринимательской среды на эффективное функционирование предприятия: Предпринимательская среда – это совокупность внешних и внутренних факторов, оказывающих влияние на функционирование фирмы...
Аура как энергетическое поле: многослойную ауру человека можно представить себе подобным...
Дисциплины:
![]() |
![]() |
5.00
из
|
Заказать работу |
|
|
Описание устройства узлов и агрегатов дизеля Д49 и компоновка его вспомогательного оборудования приводится на примере тепловозов ТЭМ7 и ТЭМ7А [З].
Рама дизель-генератора сварная, предназначена для установки на ней дизеля, генератора, размещения масла для смазки дизеля, охладителей масла и центробежных фильтров масла, а также крепления дизель-генератора к раме тепловоза. К боковым и торцевым листам приварен поддон, образующий емкость для масла. С правой стороны рамы имеется горловина для слива масла и щуп для замера его уровня. С левой стороны в раме находится полость со сливным краном для сбора отстоя из ресивера.
Блок цилиндров сварно-литой V-образной формы. Для размещения втулок цилиндров блок разделен на шесть секций. Нижняя картерная часть блока сварена из литых стоек, верхняя - из листов. Шпильки крепления крышек цилиндров установлены в нижнюю картерную часть блока. В развале блока находится ресивер для наддувочного воздуха, а ниже канал для подвода масла к подшипникам коленчатого вала. Подвод воды для охлаждения цилиндровых комплектов осуществляется водяными коллекторами, расположенными с левой и правой стороны блока. В нижней части боковых продольных листов блока против каждого цилиндра имеется отверстие для контроля герметичности полости охлаждения втулки цилиндра. В отверстиях, расположенных в стойках блока и подвесках, установлены вкладыши коренных подшипников. На седьмой стойке и подвеске установлены полукольца упорного подшипника, ограничивающего перемещение коленчатого вала в осевом направлении в пределах 0,1...0,35 мм. Доступ в картер дизеля обеспечивается через люки, закрытые крышками. С правой стороны блока крышки имеют предохранительные клапаны, открывающиеся в аварийных случаях при повышении давления в картере дизеля.
|
Коленчатый вал дизель-генератора 2-26ДГ [3] (рис. 3) отлит из высокопрочного чугуна. Шейки вала азотированы, что повышает усталостную прочность вала и износостойкость шеек. На первой, шестой, седьмой и двенадцатой щеках имеются противовесы е, отлитые за одно целое со щеками. У коренной шейки XIII имеются бурты ж, которые ограничивают осевое перемещение коленчатого вала. На фланец д устанавливается демпфер. Шлицевая втулка 4 через шлицевой вал передает вращение шестерням привода насосов. Между XIII и XIV коренными шейками вал имеет фланец, к которому крепится шестерня 9, привода распределительного вала. К фланцу и крепится соединительная муфта. Масло для смазки шатунных подшипников поступает из коренных подшипников по отверстиям в шейках коленчатого вала. На дизель-генераторах 11-26ДГ и 12-26ДГ применены стальные штампованные коленчатые валы с противовесами, закрепленными на всех щеках.
Коренной подшипник (рис. 4) состоит из верхнего 1 и нижнего 2 стальных тонкостенных вкладышей, залитых тонким слоем свинцовистой бронзы, на поверхности которых для лучшей приработки наносится тонкий слой сплава олова и свинца. Верхний вкладыш на рабочей поверхности имеет канавку в и отверстие с, через которые поступает масло из канала блока цилиндров в подшипник. Прилегание вкладышей к постели всей поверхностью обеспечивается установкой их с гарантированным натягом. Положение верхнего и нижнего вкладышей фиксируется штифтом 3, запрессованным в подвеску. Упорный подшипник состоит из бронзовых полуколец 4, прикрепленных винтами 5 к седьмой стойке и подвеске блока. Опорная поверхность полуколец покрыта тонким слоем сплава олова со свинцом [3].
Демпфер предназначен для уменьшения напряжений, возникающих вследствие крутильных колебаний в коленчатом вале и связанных с ним механизмах. Демпфер установлен на фланце коленчатого вала со стороны привода насосов.
|
Муфта соединительная обеспечивает соединение коленчатого вала дизеля с ротором генератора и состоит из ведущего и ведомого дисков, между которыми установлен пакет тонких стальных пластин. Ведущий диск имеет зубья для проворачивания коленчатого вала валоприводным механизмом.
Втулка цилиндра [3] (рис. 5) изготовлена из хромомолибденового чугуна, обладающего высокой износостойкостью и необходимыми антифрикционными свойствами. На втулку 1 напрессована рубашка 2, и между ними образована полость К для прохода охлаждаемой воды. К крышке цилиндра втулка крепится шпильками 4. Стык между крышкой и втулкой цилиндра уплотнен стальной омедненной прокладкой 8. В блоке втулка фиксируется верхним Ж и нижним Б опорными поясами. Охлаждающая вода по отверстию М в блоке цилиндров поступает в полость К и через втулки 9 перетекает в крышку цилиндра. При установке втулки в блок цилиндров скос Е на нижнем бурте должен находиться со стороны всасывания.
Крышка цилиндра (рис. 6) отлита из высокопрочного чугуна. В крышке установлены два впускных 2 и два выпускных клапана 6. Для обеспечения высокой износостойкости посадочных фасок для выпускных клапанов в крышке установлены плавающие вставные седла 5, удерживаемые в крышке пружинными кольцами 4. Уплотнительные фаски впускных клапанов опираются непосредственно на днище крышки цилиндра. Каждая пара клапанов открывается одним вильчатым рычагом 22 через гидротолкатели. Закрытие каждого клапана обеспечивается двумя пружинами 27 и 28, опирающимися торцами на нижнюю 12 и верхнюю 18 тарелки. Крышка 1 охлаждается водой, проходящей по полостям в ней. Вода поступает в крышку из втулки цилиндра по отверстию а и отводится через отверстие г в рубашку выхлопного коллектора. Рычажно-клапанный механизм смазывается разбрызгиваемым маслом, поступающим из лотка через патрубок 31. Оси рычагов смазываются маслом, поступающим по отверстиям в рычагах. Обратно масло стекает по отверстию к в крышке и по трубке в блоке цилиндров сливается в картер дизеля. В крышке предусмотрены места установки и крепления топливной форсунки 45 и индикаторного крана 46.
1 - втулка; 2 - рубашка; 3, 5, б, 7, 10 - кольца уплотнительные; 4 - шпилька; 8, 11 - прокладки;
|
9 - втулка перетока воды в крышку; В, Ж - нижний и верхний опорный пояса;
Г - отверстие для крепления приспособления; Д - отверстия для монтажного болта;
Е - скос; К - полость водяная; М - отверстие в блоке цилиндров для.подвода воды;
Н - теплоизолирующее покрытие втулки
Рисунок 5 – Втулка цилиндра
Шатунный механизм (рис. 7) состоит из главного 6 и прицепного 8 шатунов. Шатуны соединены между собой пальцем 14, который установлен во втулке 15, запрессованной в проушине главного шатуна. Прицепной шатун крепится к пальцу 14 двумя болтами 12 со шлицевыми головками. В верхние головки обоих шатунов запрессованы стальные втулки 7, залитые свинцовистой бронзой. Нижняя головка главного шатуна имеет съемную крышку 1, которая закреплена четырьмя шатунными болтами 2 с гайками 5. Стык нижней головки и крышки 1 имеет зубцы д треугольной формы, препятствующие поперечному смещению крышки. В нижнюю головку главного шатуна установлены верхний 16 и нижний 17 стальные тонкостенные вкладыши, залитые свинцовистой бронзой. Шатунный подшипник смазывается и охлаждается маслом, поступающим из коренных подшипников через каналы коленчатого вала. По отверстиям в нижнем вкладыше и по каналу з в крышке 1 масло перетекает в канал нижней головки шатуна и по втулке 3 поступает в канал стержня главного шатуна к втулке 7. Другая часть масла через отверстие в пальце поступает в канал стержня прицепного шатуна к втулке 7. Из втулок 7 через отверстия в заглушках 21, установленных в верхних головках шатунов, масло поступает на охлаждение поршней.
Поршень (рис. 8) состоит из стальной головки 4 и алюминиевого тронка 9, скрепленных четырьмя шпильками 14 с гайками 15. Головка поршня охлаждается маслом, которое поступает из верхней головки шатуна в плотно прижатый к головке шатуна пружиной 2 стакан 3 и далее по отверстиям в полость охлаждения. Из полости охлаждения масло по трубкам б, запрессованным в тронк поршня, сливается в картер дизеля. Наружная боковая поверхность тронка покрыта антифрикционным приработочным покрытием из дисульфида молибдена. В отверстия бобышек тронка установлен поршневой палец 10 плавающего типа, осевое перемещение которого ограничивается стопорными кольцами 12. Поршень имеет три компрессионных кольца 5 трапециидального сечения, изготовленных из легированного высокопрочного чугуна и имеющих хромированную рабочую поверхность. Маслосъемные кольца 7 и 8 выполнены из легированного чугуна.
|
Лоток предназначен для размещения кулачкового распределительного вала с подшипниками, качающихся рычагов с роликами и топливных насосов высокого давления. Лоток установлен на блоке цилиндров и состоит из двух половин, скрепленных болтами и шпильками. В лотке установлены распределительный вал, вращающийся в разъемных алюминиевых подшипниках, и рычаги для привода клапанов. Роликами рычаги опираются на соответствующие кулачки распределительного вала. С переднего торца лоток закрыт крышкой, в которой размещен редукционный клапан, отрегулированный на давление 0,2 ± 0,02 МПа (2 ± 0,2 кгс/см2).
Вал распределительный предназначен для управления движением впускных и выпускных клапанов крышек цилиндров и работой топливных насосов высокого давления соответственно порядку работы цилиндров. Распределительный вал приводится во вращение коленчатым валом посредством шестерен привода и приводной втулки, напрессованной на вал. Кулачки для впускных и выпускных клапанов и кулачки для привода топливных насосов состоят из двух половин, закрепленных на валу гайками. Шпонки фиксируют кулачки в строго определенном положении согласно порядку работы цилиндров. Каждый кулачок служит приводом клапанов и топливных насосов правого и левого ряда цилиндров.
Привод распределительного вала предназначен для передачи вращения от коленчатого вала распределительному валу, приводному валу регулятора, шестерням привода механического тахометра, валу предельного выключателя. Привод представляет собой зубчатую передачу, состоящую из цилиндрических и конических шестерен, помещенных в корпусе. Шестерни привода вращаются в подшипниках, установленных в стальных обоймах, которые запрессованы в корпуса привода.
Привод насосов предназначен для передачи вращения рабочим колесам водяных насосов, шестерням масляного насоса и раздаточному редуктору вспомогательных механизмов. Привод представляет собой цилиндрическую прямозубую зубчатую передачу.
Коллекторы выпускные (рис. 9) предназначены для отвода отработанных газов от цилиндров дизеля и подвода их к турбокомпрессору. На каждый ряд цилиндров установлены выпускные двухтрубные, охлаждаемые водой трехстенные коллекторы и частично охлаждаемый выпускной трубопровод. Неохлаждаемая часть трубопровода закрыта термоизоляцией. Коллекторы 1 и 3 представляют собой сварные из листовой стали двухстенные трубы, внутри которых вставлены с зазором трубы 16 из жаропрочной стали. Между наружной 18 и промежуточной 17 трубами коллектора образуется полость для перетока воды, охлаждающей коллектор. Вода для охлаждения коллекторов поступает из крышек цилиндров по отверстиям в во фланцах коллекторов. Коллекторы к крышкам цилиндров крепятся болтами 47, а стыки уплотняются асбостальными прокладками. Для отвода воздуха и пара из водяных полостей коллекторов предусмотрены трубки 2. На газовыпускных трубах установлены съемные компенсаторы 20, которые покрыты термоизоляцией, а также кожухом из листовой стали.
|
Охладитель наддувочного воздуха (рис. 10) предназначен для охлаждения воздуха, поступающего из турбокомпрессора в цилиндры дизеля. Он установлен на кронштейне 8 и крепится к нему шпильками 7. Охладитель состоит из сварного корпуса 12, патрубка 13, верхней 2 и нижней 3 крышек и охлаждающей секции. Охлаждающая секция состоит из верхней 4 и нижней 11 трубных досок, в отверстиях которых закреплены оребренные трубы 5. Внутри трубок образуется водяная, а между труб -воздушная полость. Вода поступает в охладитель по патрубку в в нижнюю крышку, перегородка б, которая делит водяную полость секции пополам, проходит по трубкам одной, а затем второй половины секции и выходит через патрубок а. Наддувочный воздух поступает к охладителю по патрубку 13, охлаждается в межтрубном пространстве и по каналу s кронштейна поступает в ресивер блока цилиндров.
Водяные насосы навешены на привод насосов при помощи фланцевых соединений, имеют привод через шлицевые валики и предназначены для обеспечения циркуляции воды в системах основного и дополнительного контура охлаждения.
Масляный насос (главный) установлен на приводе насосов и предназначен для создания циркуляции масла в системе смазки дизеля. Насос шестеренного типа, односекционный, нереверсивный. Для поддержания заданного рабочего давления насос снабжен перепускным клапаном, прифланцованным к наружной крышке насоса. Клапан отрегулирован на давление 0,96 МПа (9,6 кгс/см2), что соответствует давлению в насосе 0,9 МПа (9 кгс/см2).
Маслопрокачивающий насос предназначен для прокачки маслом дизеля перед запуском. Насос шестеренчатого типа установлен на фланце электродвигателя. Имеет предохранительно-перепускной клапан, обеспечивающий полный перепуск масла при повышении давления в нагнетательном трубопроводе. На напорном трубопроводе установлен невозвратный клапан, который не допускает переток масла из нагнетательной магистрали дизеля в период работы главного масляного насоса в магистраль маслопрокачивающего насоса.
Охладитель масла (рис. 11) предназначен для охлаждения масла, циркулирующего в системе дизеля. Охладитель состоит из корпуса б, передней 1 и задней 7 крышек, охлаждающей секции 9 и кронштейнов 17 и 22. Перегородка 3 крышки 1 разделяет водяную полость охладителя пополам. Охлаждающая секция 9 имеет переднюю 5 и заднюю 16 трубные доски, в отверстиях которых закреплены оребренные трубки 8 с сегментными перегородками 20, создающими поперечное смывание маслом трубного пучка, что способствует лучшему теплообмену. Вода в охладитель масла поступает по патрубку б передней крышки, проходит по трубам 8 одной половины секций, а затем по трубам другой половины секций и выходит из патрубка а. Масло в охладитель поступает по трубопроводу через отверстие в кронштейне 22, проходит в межтрубном пространстве и выходит через отверстие в кронштейне 17.
Фильтр масла центробежный (рис. 12) предназначен для тонкой очистки масла и состоит из ротора, вращающегося на неподвижной оси 2, колпака 8 и кронштейна 1. Принцип работы фильтра следующий: часть масла под давлением из масляной системы дизеля поступает во внутреннюю полость ротора и, проходя по каналам в крышке, поступает к соплам 15. Реактивная сила струй масла, вытекающих из сопел, приводит во вращение ротор, заполненный маслом. Центробежная сила отбрасывает к периферии ротора механические примеси и другие включения, имеющие большой удельный вес, которые оседают на прокладке 10. Выходящее из ротора очищенное масло втекает через окна в кронштейне в раму дизеля.
Фильтр масла грубой очистки (рис. 13) состоит из крышки 12, корпусов 9 и фильтрующих пакетов 7. Фильтрующий пакет состоит из стержня 6, сетчатых фильтрующих элементов 5 и опоры 3. Масло по каналу в крышке поступает к фильтрующим элементам, где на сетках оседают посторонние частицы, а очищенное масло по пазам в стержне и отверстию в крышке выходит из фильтра.
Маслоотделительный бачок и заслонка предназначены для обеспечения разрежения в картере дизеля в заданных пределах. Принцип действия заслонки основан на использовании давления воды после водяного насоса для управления заслонкой, изменяющей проходное сечение корпуса заслонки. Газы из картера по трубе через маслоотделительный бачок, где находятся маслоотделительные элементы, через корпус заслонки и по трубе попадают во всасывающую полость турбокомпрессора. Гидравлическое управление заслонкой, в зависимости от частоты вращения вала дизеля, а следовательно, и изменения давления воды, позволяет поддерживать необходимый диапазон разрежения в картере при работе дизеля на всех режимах. Дополнительно в маслоотделительном бачке находится шибер, предназначенный для регулировки разрежения вручную. На маслоотделительном бачке установлен жидкостный манометр для замера уровня разрежения в картере и подачи сигнала в электрическую схему тепловоза на остановку дизеля в случае повышения давления выше заданного предела.
Регулятор частоты вращения (рис. 14) позволяет осуществлять:
• ступенчатое 8-позиционное дистанционное электрогидравлическое управление частотой вращения коленчатого вала;
• дистанционную остановку дизеля с пульта управления тепловоза или при срабатывании защит;
• ограничение подачи топлива - в зависимости от давления наддува;
• аварийное ручное управление частотой вращения коленчатого вала дизеля.
Регулятор всережимный непрямого действия с центробежным измерителем скорости и автономной масляной системой, объединенный с регулятором мощности, состоит из нижнего корпуса 20, плиты 21, среднего корпуса 22,.верхнего корпуса 31, проставка 30, крышки 28 и гидроусилителя 27. В нижнем корпусе 20 размещен масляный шестеренчатый насос, его ведомая шестерня выполнена за одно целое с валом привода измерителя скорости. Плита 21 является крышкой масляного насоса. В ней размещены два всасывающих и два нагнетательных шариковых клапана, В среднем корпусе размещены золотниковая часть с измерителем скорости, аккумуляторы масла, силовой и дополнительный сервомоторы и рычажная передача обратной связи, В верхнем корпусе 31 размещены механизмы: управления оборотами, регулирования нагрузки, вывода индуктивного датчика в положение минимального возбуждения генератора, стопа и рычажная передача механизма ограничения топлива в зависимости от давления топлива.
Выключатель предельный предназначен для аварийной остановки дизеля в случае увеличения частоты вращения коленчатого вала свыше 1115 – 1155 об/мин и установлен с правой стороны дизеля на корпусе распределительного вала. Упор предельного выключателя г (рис. 18) воздействует на механизм управления топливными насосами, устанавливая рейки топливных насосов в нулевое положение. Для остановки дизеля предельным выключателем вручную необходимо нажать на кнопку, а для приведения предельного выключателя в рабочее состояние необходимо рукоятку переместить вверх. С пульта управления тепловозом дополнительно предусмотрена кнопка дистанционной аварийной остановки дизеля.
Топливный насос высокого давления (рис. 15) предназначен для подачи необходимого количества топлива в форсунку. Плунжер насоса 17 получает перемещение на подачу топлива через толкатель от кулачка распределительного вала. Возврат плунжера осуществляется под действием пружины 6. Топливный насос состоит из корпуса 4, в котором установлены втулка 16 с плунжером 17 и корпус 10 нагнетательного клапана с клапаном 11. На втулку плунжера установлен зубчатый венец 5, в пазы которого входит ведущий поводок плунжера. В зацеплении с зубчатым венцом находится рейка 31, установленная в корпусе насоса, которая проворачивает плунжер при своем перемещении. Максимальный выход рейки 31 насоса замеряется от торца рейки до болта 8. Начальная установка размера А производится при регулировании насоса по производительности на стенде изменением положения рейки и прокладок под болтом 8. При установке на дизель размер А выставляется при соединении механизма управления топливными насосами с регулятором дизеля. Обеспечение одинаковых углов начала подачи топлива по всем цилиндрам дизеля выполняется подбором регулировочных стальных прокладок 19 между опорными поверхностями фланца направляющей втулки 2 толкателя и лотком, что выполняется на стенде, и этот размер набора в миллиметрах выбивается на поверхности а корпуса насоса. Эта толщина является исходной при установке насоса на дизель, при регулировке давления сгорания допускается уменьшение или увеличение прокладок на 0,5 мм.
Форсунка (рис. 16) закрытого типа с гидравлическим управляемым подъемом иглы распылителя уплотняется в крышке цилиндра конусной поверхностью а и резиновым кольцом 9. К нижнему торцу корпуса 7 прикреплены колпаком 4 корпус 2 распылителя и сопло 1. На шаровой поверхности сопла равномерно по окружности расположены распыливающие отверстия. В корпусе 2 распылителя размещена игла 3, которая прижимается к корпусу распылителя пружиной 8 через штангу б, они точно пригнаны друг к другу. Топливо подводится в форсунку через щелевой фильтр, состоящий из корпуса 16 и стержня 17. Давление поступающего топлива - 31,4 + 0,5 МПа (320 + 5 кгс/см2) преодолевает усилие пружины 8, игла 3 поднимается, и топливо через отверстие в носке сопла 1 впрыскивается в камеру сгорания. Посадка иглы на седло производится под действием пружины 8 в момент окончания подачи топлива топливным насосом.
Механизм управления топливными насосами (рис. 17) установлен на лотке и предназначен для перемещения реек топливных насосов регулятором. Механизм приводится в движение от вала сервомотора регулятора, который через рычаг 7, тяги 5 и 2, пружину 3 и рычаг 1 поворачивает вал 34. Вал 34 посредством рычага 39, тяг 38 и рычагов 36 поворачивает валы 12, на которых неподвижно установлены рычаги 16, 18 и 22, 23. Рычаги 18 и 22 пружинами 17 прижаты к рычагам 16 и 23. На валиках установлены упоры 9 и рычаги 30. Упор 9 зафиксирован на валике штифтом 10 и закреплен болтом. Пружина 11 прижимает к упору 9 рычаг 30 с винтом 29, которым регулируют выдвижение рейки топливного насоса 6. В рычаге 30 имеется втулка 8 и ось 32 с сухарем 31, входящим в паз рейки топливного насоса. Конструкция механизма обеспечивает отключение любого из насосов, а также перевод механизма управления в положение нулевой подачи в случае заклинивания плунжера или рейки какого-либо топливного насоса. Для отключения топливного насоса рычаг 30 нужно переместить в осевом направлении, чтобы сухарь 31 вышел из зацепления с рейкой, переместить рычаг 30 вверх, а затем в осевом направлении назад и положить его на торец рейки топливного насоса. При этом рычаг 30 усилием пружины 11 переместит рейку в нулевое положение. Для ограничения выхода реек топливных насосов на рычаге 41 установлен болт 42 упора мощности. На нулевой позиции контроллера предусмотрено отключение части топливных насосов каждого ряда цилиндров (4, 5, 6 цилиндры с левой и правой стороны - отсчет цилиндров со стороны генератора). Механизм отключения состоит из корпуса 14, поршней 15 с упорами 19, пружин 21, прижимающих поршни к корпусу 14, крышек 20 с уплотнительными манжетами и прокладками. Сжатый воздух от магистрали тепловоза подводится к электропневматическому вентилю 37 и далее по трубке к штуцеру 28 и по каналам е - к поршням 15.
Фильтр тонкой очистки топлива (рис. 18) с бумажными фильтрующими элементами предохраняет детали топливной аппаратуры дизеля от попадания твердых частиц примесей свыше 3...5 мкм. Фильтр имеет по два фильтрующих элемента 6, расположенных в отдельных корпусах 7, объединенных общей крышкой. В нижней части корпуса расположен болт 1, который шариком 3 закрывает сливное отверстие. В крышке 8 имеются два болта 11 для выпуска воздуха из каждой секции отдельно и кран 14 для распределения подачи топлива в обе секции. Топливо через топливоподводящий штуцер 13 и отверстия в крышке и кране попадает в оба корпуса фильтра, проходит через фильтрующие бумажные элементы 6, по стягивающей трубе 5, отверстиям в крышке и поступает к топливоотводящему штуцеру 12.
Системы дизеля
Система воздухоподачи предназначена для очистки и подачи воздуха в дизель. Забор воздуха осуществляется через боковые жалюзи, расположенные на боковых стенках кузова, проходит через воздухозаборники, воздухоочистители, очищается от пыли и поступает в патрубок турбокомпрессора.
Воздухоочистители дизеля предназначены для очистки воздуха, поступающего в дизель, от содержащихся в нем частиц пыли. Для очистки воздуха использован принцип контактного улавливания частиц пыли, взвешенных в воздушном потоке и осаждающихся на нитях фильтрующей набивки, смоченной маслом. Воздухоочиститель имеет четыре кассеты с фильтрующей набивкой, размещенные в корпусе. Нижняя часть корпуса служит масляной ванной. В ней размещены поддон с маслоподающими циклонами. Воздух поступает в воздухоочиститель и разделяется на два потока. Первый поток поступает в кассеты, второй поток - в поддон и в полости поддона, закручивается специальными перегородками спиральной формы, увлекая капли масла. Капли масла разбрызгиваются перед фронтом кассет, смачивая набивку. Уровень масла в воздухоочистителе должен поддерживаться между рисками на щупе, являющимся также крышкой заливочной горловины. В процессе эксплуатации необходимо удалять осадок пыли из корпуса воздухоочистителя, производить промывку всех его деталей и фильтрующей набивки, а также заменять масло.
Турбокомпрессор ТК-35 (рис. 19) предназначен для подачи воздуха в дизель под избыточным давлением для увеличения мощности и экономичности дизеля. Остов турбокомпрессора состоит из входника 37, корпуса компрессора 3, корпуса выпускного 9, корпуса газоприемного 17. Воздух в компрессор поступает через входник 37, к фланцу которого подсоединяется патрубок воздухоочистителя. Во входнике установлены опорный 49 и упорный 45 подшипники ротора. Корпус компрессора 3 литой из чугуна, выполнен в виде спиральной улитки. В корпусе установлена вставка профильная 5, к которой прижимаются лопатки диффузора 7, образующие вместе колесом 4 компрессора и обтекателем 2 проточную часть компрессора. Корпус выпускной 9 литой из чугуна, имеет водяную рубашку, в которой циркулирует вода из системы охлаждения дизеля. Через корпус 9 отработавшие в турбокомпрессоре газы отводятся в глушитель дизеля. Корпус газоприемный 17 литой из чугуна имеет водяную рубашку в нем установлены сопловой венец 14 и кожух 30 соплового аппарата. Сопловой венец 14, кожух 30 и лопатки 13 турбины образуют проточную часть турбины. В газоприемном корпусе установлен опорный подшипник 22 ротора. Ротор 21 имеет вал сварной конструкции, состоящий из двух полувалов и диска турбины, Колесо 4 компрессора цельнолитое, фиксируется на валу гайкой. Лопатки 13 турбины установлены в диске турбины на ёлочных замках и зафиксированы стопорными пластинами.
Выпускная система - эжекционная, предназначена для выпуска отработанных газов в атмосферу, осуществления искрогашения и вентиляции дизельного помещения. Выпускная система состоит из выхлопного патрубка коробчатого сечения, прикрепленного к проточной части турбокомпрессора, и глушителя. Корпуса глушителя цилиндрической формы установлены вертикально, параллельно друг другу и смонтированы на люке крыши тепловоза. Внутри каждого корпуса расположен завихритель для сообщения направления потоку выхлопных газов, В закрученном потоке газов искры истираются о стенки корпуса и гаснут, а выхлопные газы дальше попадают в сепарационную камеру, состоящую из обечайки и сетки, расположенных концентрично. В нижнем фланце камеры вварены дренажные трубки для отделения от газов жидкой фазы в дренажную систему. Система дренажа состоит из труб и сепарационных бачков, расположенных с левой и правой стороны дизель-генератора.
Топливная система (рис. 20) предназначена для подачи топлива из подвесного бака к топливным насосам высокого давления. Топливо топливоподкачивающим насосом 9 засасывается из бака 33 через фильтр грубой очистки 7, топливоподогреватель 11 и фильтр тонкой очистки 14 поступает к насосам высокого давления, а от них к форсункам. Топливный бак представляет собой сварную емкость объемом 7050 л. Топливоподкачивающий насос имеет привод от электродвигателя. Избыточное топливо при давлении выше 0,11...0,13 МПа (1,1...1,3 кгс/см2) через подпорный клапан 17 сливается обратно в бак. Предохранительный клапан 8 служит для ограничения давления топлива в трубопроводе системы и предохранения топливоподкачивающего насоса от перегрузок.
Фильтр грубой очистки топлива (рис. 21) предназначен для очистки топлива. Он состоит из корпуса 9, в котором размещен набор фильтрующих элементов 11, собранных в пакет на трехгранном стержне 5. Стержень ввернут в крышку 7, которая уплотняется кольцом 8. Снизу в корпусе имеется резьбовая пробка 1 для слива отстоя. Топливо поступает в фильтр через отверстие в нижнем фланце 10 и далее через сетки фильтрующих элементов 11 внутрь пакета. Очищенное топливо по каналам трехгранного стержня 5 перетекает в канал крышки 7 и через отверстие в верхнем фланце 10 выходит из фильтра. Посторонние частицы размером более 45 мкм задерживаются сетками, оседая на их поверхности, а также накапливаются в нижней части корпуса фильтра и периодически удаляются через отверстие, закрытое пробкой 1.
1 - пробка сливная; 2, 24, 31 - краны; 3, 30 - стекла топливомерные; 4, 29 - заливные горловины;
5, 28 - трубы вентиляционные; 6, 27 - щупы; 7 - фильтр грубой очистки;
8 - клапан предохранительный; 9 - топливоподкачивающий агрегат;
10, 13, 21 - присоединения к трубопроводу дизеля; 11 - топливоподогреватель;
12 - грибок под манометр; 14 - фильтр тонкой очистки; 15 - манометр дистанционный;
16 - демпфер; 17 - клапан подпорный; 18 - дизель; 19 - кран выпуска воздуха; 20 - топливомер;
22 - отвод топлива, просочившегося через форсунки;
23 - подвод воздуха от питательной воздушной магистрали; 25 - фильтр воздушный;
26 - дроссель; 32 - клапан слива топлива; 33 - бак топливный
Рисунок 20 – Схема топливной системы
Топливоподогреватель (рис. 22) представляет собой трубчатый теплообменник. В цилиндрическом сварном корпусе 9 размещен нагревательный трубный элемент, состоящий из гладких стальных трубок 4, вваренных в трубные доски 5 и закрытых двумя крышками 7. Топливоподогреватель устанавливается на кузов дизельного помещения на кронштейнах 2.
Масляная система (рис. 23) предназначена для подачи масла к трущимся поверхностям дизеля с целью их смазки и охлаждения поршней. В дизеле применена принудительная система смазки под давлением, масло охлаждается водой холодного контура дизеля. Масляный насос дизеля 11 засасывает масло из масляной ванны через маслозаборник 34 и по трубопроводу нагнетает его к двум полнопоточным фильтрам тонкой очистки 1 и 3, соединенным параллельно. Затем масло поступает в охладители масла 19 и 33, фильтр грубой очистки 40 и далее в дизель. Часть масла поступает в центробежные фильтры 24 и 27, из которых сливается в картер дизеля. Прокачка масла через дизель перед запуском осуществляется маслопрокачивающим насосом с приводом от электродвигателя. Для автоматического контроля за давлением масла в системе и своевременным снятием нагрузки или остановки дизеля предназначены реле давления 1 - 4ДДМ.
Полнопоточный фильтр тонкой очистки масла (рис. 24) состоит из основания корпуса 5, корпусов 7 и фильтрующих элементов 4, 6 типа «Нарва-6». К основанию корпуса 5 шпильками крепятся корпуса 7 с уплотнением резиновыми кольцами. В корпусах 7 ввернуты клапаны перепускные тарельчатого типа, предохраняющие фильтрующие элементы от разрушения при повышении перепада давления. Начало открытия клапана наступает при перепаде давления масла 0,16...0,18 МПа (1,6...1,8 кгс/см2). Подвод и отвод масла осуществляется через отверстия в основании корпуса.
Водяная система дизеля (рис. 25) закрытого типа с принудительной циркуляцией воды имеет два самостоятельных контура охлаждения (горячий и холодный), каждый из которых имеет свои трубопроводы, водяные насосы, секции холодильника и общий вентилятор охлаждения. Система предназначена для отвода тепла, выделяющегося при работе дизеля.
Основной (горячий) контур предназначен для охлаждения цилиндровых втулок и крышек, корпуса турбокомпрессора, выхлопных коллекторов. Водяным насосом 46, левым по ходу тепловоза, вода нагнетается в охлаждающие полости дизеля 42 и турбокомпрессор. Нагретая вода отводится от дизеля в секции 53 холодильника тепловоза и далее во всасывающую полость водяного насоса. В холодное время часть воды из водяной полости левого выхлопного коллектора дизеля отводится на обогрев в топливоподогреватель 29, калорифер 32, обогреватели пола кабины машиниста 34 и 65.
Дополнительный (холодный) контур предназначен для отвода тепла от охладителя наддувочного воздуха и охладителей масла. Водяным насосом 63, правым по ходу тепловоза, вода нагнетается в маслоохладитель 22 дизеля, секции 3 холодильника. Охлажденная вода далее прокачивается через маслоохладитель 59, охладитель наддувочного воздуха 64 и поступает во всасывающий патрубок водяного насоса 63.
Положение вентилей, краников и соединительных головок при работе дизеля, включении обогрева, прогреве топлива, прогреве дизеля от внешнего источника, при заполнении системы водой и сливе воды из системы указано в таблице (рис. 25).
На тепловозе применена система автоматического регулирования температуры воды (САРТ) основного и дополнительного контура (рис. 26). При нагреве воды основного контура до 348 К (75 °С) открываются левые жалюзи пневмоцилиндром 27, в который по сигналу термодатчика 15 поступает воздух от электропневматического вентиля 19. Правые жалюзи открываются по сигналу термодатчика 17 при нагреве воды дополнительного контура до 328 К (55 °С). Верхние жалюзи открываются при открытии боковых жалюзи. При повышении температуры воды основного контура 360 К (87 °С) или дополнительного контура 333 К (60 °С) начинает вращаться вентилятор. При необходимости работой жалюзи и вентилятора можно управлять дистанционно вручную, пользуясь тумблерами в кабине машиниста. Для этого нужно установить переключатель ПЖ на режим «Ручное». При отказе систем автоматического и ручного дистанционного управления жалюзи можно открывать вручную рычагом у соответствующего пневмоцилиндра. В системе автоматического управления жалюзи применены термодатчики типа Т-35 и преобразователи температуры ДТПМ.
ПРИЧИНЫ НЕИСПРАВНОСТЕЙ
|
|
Двойное оплодотворение у цветковых растений: Оплодотворение - это процесс слияния мужской и женской половых клеток с образованием зиготы...
Археология об основании Рима: Новые раскопки проясняют и такой острый дискуссионный вопрос, как дата самого возникновения Рима...
Типы оградительных сооружений в морском порту: По расположению оградительных сооружений в плане различают волноломы, обе оконечности...
Типы сооружений для обработки осадков: Септиками называются сооружения, в которых одновременно происходят осветление сточной жидкости...
© cyberpedia.su 2017-2024 - Не является автором материалов. Исключительное право сохранено за автором текста.
Если вы не хотите, чтобы данный материал был у нас на сайте, перейдите по ссылке: Нарушение авторских прав. Мы поможем в написании вашей работы!