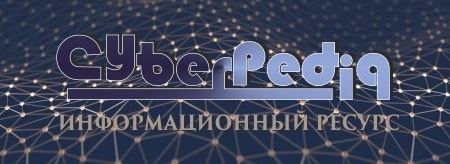
Биохимия спиртового брожения: Основу технологии получения пива составляет спиртовое брожение, - при котором сахар превращается...
Поперечные профили набережных и береговой полосы: На городских территориях берегоукрепление проектируют с учетом технических и экономических требований, но особое значение придают эстетическим...
Топ:
Выпускная квалификационная работа: Основная часть ВКР, как правило, состоит из двух-трех глав, каждая из которых, в свою очередь...
Установка замедленного коксования: Чем выше температура и ниже давление, тем место разрыва углеродной цепи всё больше смещается к её концу и значительно возрастает...
Методика измерений сопротивления растеканию тока анодного заземления: Анодный заземлитель (анод) – проводник, погруженный в электролитическую среду (грунт, раствор электролита) и подключенный к положительному...
Интересное:
Искусственное повышение поверхности территории: Варианты искусственного повышения поверхности территории необходимо выбирать на основе анализа следующих характеристик защищаемой территории...
Подходы к решению темы фильма: Существует три основных типа исторического фильма, имеющих между собой много общего...
Средства для ингаляционного наркоза: Наркоз наступает в результате вдыхания (ингаляции) средств, которое осуществляют или с помощью маски...
Дисциплины:
![]() |
![]() |
5.00
из
|
Заказать работу |
Содержание книги
Поиск на нашем сайте
|
|
Задачи и способы размерной обработки
Под точностью изготовления деталей понимают значения отклонения геометрической формы и размеров поверхности от предельных значений, указанных в конструкторской документации (рабочий чертеж, технические условия).
Качество поверхности характеризуется ее шероховатостью, величиной и знаком остаточных напряжений в поверхностном слое, структурой и химическим составом.
Технологический процесс изготовления деталей является ступенчатым. Он построен на последовательном выполнении операция изготовления заготовок с припуском (дополнительный слой материала) и последующим управляемым съемом материала припуска методами размерной обработки до получения заданных размеров и форм.
Задачей размерной обработки является получение деталей требуемой точности размеров и формы, а также качества поверхности с минимальной себестоимостью и высокой производительностью.
Способы размерной обработки,
Классифицируются по виду используемой энергии:
1. механические
2. физико-химические
3. комбинированные
По технологическому способу удаления припуска: точение, сверление, фрезерование и т.д.
Основы обработки металлов резанием.
1. Общие сведения
Обработка металлов резанием (ОМР) заключается в срезании с поверхности заготовки слоя материала (припуска) с помощью режущего инструмента, материал припуска при этом превращается в стружку, которая является характерным признаком всех видов ОМР.
Режущий инструмент:
- лезвийный
- абразивный
Процесс резания (стружкообразования) является сложным процессом, при котором имеют место упругие и пластичекие деформации (сжатия, растяжения, сдвига).
Количество тепла, которое нагревает заготовку, инструмент, стружку и приводит к изменению свойств материала режущего инструмента и поверхностного слоя заготовки. Поэтому режущий инструмент изготавливается из термостойких и износостойких материалов (быстрорежущие стали, металлокерамика).
ОМР осуществляется согласованным движением заготовки и режущего инструмента. При этом выделяют два типа движений: движение резания (ДР) и установочное движение (ДУ).
Движение резания складывается из элементарных движений, к которым относятся:
- главное движение (ДГ), происходящее с наибольшей скоростью (скорость резания)
- движение подачи (ДП), предназначенное для обеспечения заданной подачи (осуществляется с меньшей скоростью).
Оба вида движения могут быть вращательными либо прямолинейно-поступательными.
- движение формообразования (ДФ), обеспечивающее в совокупности с другими движениями заданную форму и размеры обработанной поверхности
- касательное движение (ДК), скорость которого направлена по касательной к режущей кромке и предназначенное для смены активного участка лезвия инструмента.
- вибрационное движение (ДВ) – это колебательное движение, составляющее движение резания, сообщаемое инструменту или обрабатываемой заготовке с целью улучшения характеристик процесса резания или дробления стружки.
Виды ОМР.
1) Точение.
Главным движением является вращательное движение заготовки.
Движение подачи – прямолинейно-поступательное движение резца.
Основные параметры:
- скорость резания V – это наибольшая линейная скорость точки лезвия инструмента в главном движении (лежит на обрабатываемой поверхности) [м/мин, м/с]
- подача S – величина внедрения инструмента в тело срезаемого припуска за определенное время, измеренная в основной плоскости в заданном направлении (например, при точении перемещение резца за один оборот (подача на оборот) заготовки, обеспечивается движение подачи). В зависимости от времени измерения подачи различают подачу на зуб, подачу на оборот и минутную подачу.
- глубина резания t – расстояние между обрабатываемой и обработанной поверхностями [мм].
Точение проводится на станках токарной группы, режущим инструментом является резец.
Разновидности резцов:
- проходные и проходные упорные (для обработки цилиндрических и конических поверхностей)
- подрезные (для обтачивания торцевых поверхностей)
- отрезные (для отрезания заготовок)
- резьбовые (для нарезания резьбы)
- фасонные и т.п.
По форме режущей головки различают резцы прямые, отогнутые, изогнутые, оттянутые, по виду точения (черновые, чистовые), по направлению движения подачи (правые и левые), по материалу режущей головки (быстрорежущие, твердосплавные) и т.д
2) Строгание.
Заключается в обработке плоских горизонтальных поверхностей и различных канавок в условиях единичного и мелкосерийного производства.
Главное движение – возвратно-поступательное движение резца: рабочий ход, холостой ход.
Движение подачи – прерывистое, поступательное движение, перемещается заготовка, закрепленная на столе станка (резец тоже может перемещаться). Движение подачи направлено перпендикулярно главному движению.
Врезание резца в заготовку в начале каждого рабочего хода сопровождается ударом, за время холостого хода резец остывает, поэтому при строгании в большинстве случаев СОЖ не применяются.
Чистовое строгание обеспечивает точность обработки по 8…7 квалитету и шероховатость поверхности Ra=1,6, что не уступает поверхностям, полученным чистовым точением.
3) Долбление.
Обработка вертикальных плоских поверхностей, обработка несквозных пазов в мелкосерийном производстве.
Обработка производится на долбежных станках.
4) Сверление (зенкерование, развертывание, зенкование).
Процесс получения или обработки отверстий.
При сверлении режущим инструментом является сверло. Главное движение (движение резания) – вращение сверла, движение подачи – перемещение сверла или заготовки. Обеспечивается точность не выше 14…12-го квалитета и шероховатость поверхности Ra 20 мкм.
Зенкерование – это обработка отверстий уже получены литьем, обработкой металлов давлением или сверлением для придания им необходимой формы и размеров. Точность при зенкеровании отверстий после сверления – 11 квалитет, шероховатость поверхности Ra 6,3…2,5 мкм.
Режущий инструмент – зенкер. Различают цилиндрические, конические и торцовые зенкеры, по конструкции – цельные, насадные и с припаянными твердосплавными пластинками.
Зенкерованием обрабатывают отверстия диаметром до 120 мм.
Развертывание – обработка отверстий с целью получения необходимой точности и качества поверхности.
Предшествующие операции сверление, черновое, чистовое зенкерование или чистовое растачивание. Точность обработки до 6…7-го квалитета, шероховатость поверхности до Ra 0,63…0,32 мкм.
Зенкование – обработка отверстий под потайные или полупотайные головки крепежных изделий. Режущий инструмент – зенковки.
5) Фрезерование.
Проводится многолезвийным инструментом – фрезой. Главное движение – вращение фрезы. Движение подачи – поступательное перемещение заготовки или фрезы. Каждый режущий зуб при вращении фрезы находится в контакте с заготовкой и осуществляет резание только в пределах определенного угла поворота фрезы, затем вращается в холостую, т.е. особенностью процесса фрезерования является периодичность и непрерывность резания. Причем процесс врезания зуба сопровождается ударами.
Режущий инструмент – фрезы (цилиндрические, торцевые), соответственно фрезерование подразделяется на цилиндрическое и торцевое.
По методу обработки фрезерование делят на встречное и попутное.
Попутным называют фрезерование, когда направление главного движения резания и движения подачи совпадают.
При встречном фрезеровании (против подачи) направления главного движения резания и движения подачи не совпадают, зуб фрезы снимает стружку толщиной от нулевого до максимального значения, возрастает нагрузка на зуб. Действующая на заготовку сила стремится оторвать ее от стола, вырвать из зажимного приспособления. Вследствие этого в технологической системе возникают вибрации, отрицательно сказывающиеся на обработке. Возможное скольжение зуба по поверхности металла, упрочненного предыдущим зубом, приводит к повышенному износу фрезы.
Попутное фрезерование снижает износ фрезы и шероховатость обработанной поверхности, поэтому оно более предпочтительнее. При попутном фрезеровании зуб фрезы сначала снимает слой металла наибольшей толщины, таким образом нагрузка на зуб изменяется от максимального до нулевого значений. Возникающая сила прижимает заготовку к столу, вибрации минимальны, проскальзывания зубьев нет. Все это приводит к получению лучшей шероховатости поверхности и меньшему износу инструмента, не смотря на то, что он начинает обработку с загрязненной корки заготовки.
При фрезерной обработке заготовок точность поверхностей соответствует 11-му квалитету, шероховатость при чистовом фрезеровании составляет Ra5…2,5 мкм.
Процесс фрезерования выполняется на станках фрезерной группы.
6) Шлифование.
Производится абразивным инструментом (шлифовальные абразивные круги). Качество обработки поверхностей зависит от размера зерен круга.
Главным движением является вращательное движение шлифовального круга, движение подачи – перемещение заготовки или круга параллельно оси вращения.
Процесс ведется с обильной подачей СОЖ. Различают плоское и круглое шлифование (обрабатываются как наружные, так и внутренние поверхности).
Плоское шлифование:
- периферией шлифовального круга
- торцом шлифовального круга
Скорость резания (окружная скорость шлифовального круга) – 20…80 м/с.
Глубина шлифования – 0,05…0,005
Шлифование обеспечивает размеры по 8…5 квалитету и следующие значения шероховатости поверхности: при внутреннем шлифовании – до Ra 0,1 мкм, при наружном – до Ra 0,4 мкм.
Оборудование:
- круглошлифовальные станки
- плоскошлифовальные станки
- безцентровошлифовальные станки
- специальные станки (торцешлифовальные, лентошлифовальные).
7) Протягивание.
Способ формообразования наружных и внутренних поверхностей деталей многолезвийными инструментами-протяжками, при этом производится копирование с большой точностью формы и размеров режущих кромок инструмента на обрабатываемой заготовке.
Главное движение – поступательное движение инструмента или заготовки.
Движение подачи заложено в конструкцию протяжки – высота каждого последующего зуба увеличена на определенную величину, называемую подачей на зуб, .
Обработка осуществляется на горизонтально- или вертикально – протяжных станках.
Точность обрабатываемых поверхностей соответствует 8-6-му квалитету, а шероховатость поверхности Ra 1.25…0,63 мкм.
Устройство проходного токарного резца.
Эффективность обработки резанием во многом определяется геометрической формой инструмента. Любой инструмент может рассматриваться как композицию на основе резца. Поэтому элементы последнего присущи любому режущему инструменту.
Резец состоит из присоединительной части (державки) и режущей части.
Режущая часть ограничена передней поверхностью, по которой сходит стружка, и задними поверхностями. Главная задняя поверхность обращена к обрабатываемой поверхности и поверхности резания, а вспомогательная задняя – к обработанной поверхности.
Линии пересечения передней и задней поверхностей является режущими кромками.
Под геометрией инструмента понимают совокупность углов, определяющих форму рабочих поверхностей, режущих кромок и их расположение в заданной системе координат.
Для измерения углов, составляющих геометрию в данной точке режущей кромки, принята пространственная прямоугольная система, состоящая из трех пересекающихся в этой точке плоскостей: плоскости резания, основной плоскости и секущей плоскости.
Плоскость резания образована вектором скорости движения резания и линией, касательной к режущей кромке. Основная плоскость – плоскость, перпендикулярная вектору скорости резания, секущая плоскость, проходящая через рассматриваемую точку режущей кромки перпендикулярно плоскости резания и основной плоскости.
Геометрия определяется четырьмя плоскими углами, лежащими в координатных плоскостях.
В главной секущей плоскости измеряются п6ередний угол (угол между передней поверхностью и основной плоскостью) и главный задний угол
(угол между главной задней поверхностью и плоскостью резания).
|
|
Поперечные профили набережных и береговой полосы: На городских территориях берегоукрепление проектируют с учетом технических и экономических требований, но особое значение придают эстетическим...
Типы оградительных сооружений в морском порту: По расположению оградительных сооружений в плане различают волноломы, обе оконечности...
Индивидуальные и групповые автопоилки: для животных. Схемы и конструкции...
История развития пистолетов-пулеметов: Предпосылкой для возникновения пистолетов-пулеметов послужила давняя тенденция тяготения винтовок...
© cyberpedia.su 2017-2025 - Не является автором материалов. Исключительное право сохранено за автором текста.
Если вы не хотите, чтобы данный материал был у нас на сайте, перейдите по ссылке: Нарушение авторских прав. Мы поможем в написании вашей работы!