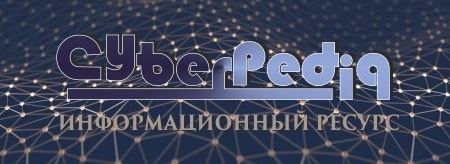
Автоматическое растормаживание колес: Тормозные устройства колес предназначены для уменьшения длины пробега и улучшения маневрирования ВС при...
Индивидуальные очистные сооружения: К классу индивидуальных очистных сооружений относят сооружения, пропускная способность которых...
Топ:
Эволюция кровеносной системы позвоночных животных: Биологическая эволюция – необратимый процесс исторического развития живой природы...
Техника безопасности при работе на пароконвектомате: К обслуживанию пароконвектомата допускаются лица, прошедшие технический минимум по эксплуатации оборудования...
Характеристика АТП и сварочно-жестяницкого участка: Транспорт в настоящее время является одной из важнейших отраслей народного...
Интересное:
Наиболее распространенные виды рака: Раковая опухоль — это самостоятельное новообразование, которое может возникнуть и от повышенного давления...
Уполаживание и террасирование склонов: Если глубина оврага более 5 м необходимо устройство берм. Варианты использования оврагов для градостроительных целей...
Искусственное повышение поверхности территории: Варианты искусственного повышения поверхности территории необходимо выбирать на основе анализа следующих характеристик защищаемой территории...
Дисциплины:
![]() |
![]() |
5.00
из
|
Заказать работу |
Содержание книги
Поиск на нашем сайте
|
|
Рассматриваемые вопросы: Понятие точности. Факторы, влияющие на точность обработки на металлорежущих станках. Связь погрешности обработки и допуска на размер.
Понятие точности
Точность - основная характеристика деталей и машин. Под точностью в машиностроении понимается степень соответствия производимых изделий заранее установленному прототипу или образцу. В качестве образца принимается деталь, заданная чертежом.
Точность детали, полученной в результате механической обработки, определяется:
- отклонениями действительных размеров детали от требуемых;
- отклонениями от геометрической формы детали или ее элементов (отклонения от прямолинейности, плоскостности, круглости, цилиндрич-ности и пр.);
- отклонениями поверхностей и осей детали от точного взаимного расположения (отклонения от параллельности, перпендикулярности, соосности, симметричности и пр.);
- шероховатостью поверхности.
Отклонения значений параметров реальной детали от детали, заданной чертежом, характеризует величину погрешности.
4.2. Факторы, влияющие на точность обработки на металлорежущих станках
Общая погрешность выполняемого размера складывается из нескольких составляющих. На точность обработки на металлорежущих станках влияют:
- неточность станка Аст;
- погрешность установки Ауст;
- неточность инструмента и его износ Аин;
- неточность установки инструмента Анастр;
- деформации деталей во время обработки, вызванные силами резания и закрепления Адеф;
- тепловые деформации Аг;
- деформации, вызванные внутренними напряжениями в материале детали Аа;
- погрешность измерения Аизм;
- ошибка исполнителя Аисп.
Рассмотрим подробнее каждую из перечисленных погрешностей, определим причины ее возникновения и степень влияния на окончательную точность детали.
|
Неточность станков
Точность станка в ненагруженном состоянии (геометрическая точность станка) зависит главным образом от точности изготовления деталей станка и точности их сборки. Нормы точности станка всегда выше норм точности деталей, получаемых на этом станке. Нормы точности и методы проверки точности станков регламентируются стандартами. Вследствие износа в процессе эксплуатации точность станка изменяется. Появляются такие отклонения как биение шпинделя (износ подшипников), непрямолинейность направляющих, по которым перемещается каретка суппорта, смещение центров передней и задней бабки, повышенные вибрации и т.п. Это приводит к несоосности поверхностей, смещению осей, искажению геометрической формы, ухудшению параметров шероховатости поверхностей детали.
Погрешность установки
При установке детали на станке еѐ фактическое положение отличается от требуемого. Отклонение положения установленной заготовки от требуемого называется погрешностью установки.
s =fs-,s;б, (4.1)
уст J баз ' закр ' пр '
где ббаз - погрешность базирования;
£закр - погрешность закрепления;
епр - погрешность приспособления.
Погрешность базирования s баз возникает при несовпадении измерительной и установочной баз заготовки. При совпадении измерительной и установочной баз погрешность базирования равна нулю. Так, на рисунке 4.1 погрешность базирования размера L равна нулю, так как измерительная и установочная базы совпадают: ебазЬ = 0. Погрешность базирования размера К равна допуску на размер, связывающий измерительную и установочную базы: вбазК= δ.
Рис. 4.1. Схема установки детали на плоскую поверхность
При несовпадении измерительной и установочной баз погрешность базирования определяют путем расчета, исходя из геометрических элементов схемы установки (рисунок 4.2).
|
Погрешность базирования размера L при посадке детали на разжимную оправку без зазора
при посадке с зазором А:
£базЬ = ^ + А. (4.3)
Рис. 4.2. Схема установки детали на цилиндрическую оправку с зазором
Погрешность базирования для размеров, определяемых инструментом, равна нулю. К таким размерам относятся размеры, определяемые только размером инструмента: диаметром сверла, зенкера, развертки, шириной фрезы и т.п. Для размеров, определяющих взаимное положение поверхностей, обработанных с одной установки, погрешность базирования также равна нулю.
На погрешность базирования влияют погрешность формы и параметры шероховатости базовой поверхности, поэтому в качестве баз следует выбирать наиболее точно обработанные поверхности.
Погрешность закрепления вызвана смещение измерительной базы по направлению измеряемого размера под действием сил закрепления. На рисунке 4.1 погрешность закрепления размеров L и К £закр К Ф 0, s3aKp L Ф 0, так как измерительная база размеров перемещается под действием прижимной силы.
Погрешность закрепления определяется в основном деформациями в месте контакта заготовки с установочными элементами. Контактные деформации зависят от величины прижимной силы Q:
y = C-Q", (4.4)
где С и п - коэффициенты, зависящие от вида контакта, материала, шероховатости поверхности.
![]() |
у
Y i
Qi
Q
Рис. 4.3. Зависимость контактных деформаций от прижимной силы
Необходимо отличать погрешность установки от неправильной схемы установки. Сила закрепления должна надежно прижимать базовую поверхность заготовки к установочным элементам приспособления. Поворот или смещение заготовки при закреплении указывает на неправильную схему установки.
Погрешность приспособления пр определяется:
- погрешностью изготовления и сборки самого приспособления;
- износом установочных элементов;
- погрешностью установки приспособления на станке. Способы устранения или уменьшения этих погрешностей:
- при использовании одного приспособления его погрешность постоянна и ее можно учесть при настройке. При использовании нескольких приспособлений-дублеров их погрешность будет входить в погрешность установки;
- износ установочных элементов приспособлений периодически контролируется и при достижении предельно допустимой величины их заменяют. Для уменьшения износа установочные элементы выполняют из закаленной стали, хромируют или наплавляют твердым сплавом.
|
- погрешность установки самого приспособления на станке (перекосы, смещения) уменьшают путем установки фиксаторов, направляющих элементов и т.п. на столе станка.
Погрешности £баз, £закр, пр - величины векторные. Погрешность установки определяют как векторную сумму
ч |
(4.5) |
„ 2, ~ 2, 2
£ + £ + £
уст |
баз закр пр
Погрешность приспособления обычно значительно меньше, чем погрешности базирования и закрепления. Поэтому с достаточной степенью точности погрешность установки можно определить, учитывая только погрешности базирования и закрепления.
Степень точности инструмента и его износ
Инструмент, как и всякое другое изделие, имеет свою точность изготовления. Погрешности инструмента переносятся на обрабатываемую деталь. Размеры и точность стандартных инструментов регламентированы стандартами. Выбранный инструмент должен обеспечивать заданную точность обработки.
На точность обработки существенно влияет износ инструмента. Износ инструмента характеризуется начальным износом и н (приработкой режущей
кромки) и размерным износом. Приработка режущей кромки - это износ на первой 1000 м пути резания. Во время приработки режущей кромки износ идет более интенсивно, чем при установившемся режиме резания. Размерный износ характеризуется удельным износом ио за время пути резания в 1000 м. Величина удельного износа для различных инструментов в зависимости от конкретных условий обработки приводится в справочных таблицах. Приняв по нормативным данным величину удельного износа и для обработки партии деталей од-
ним инструментом без переточки, можно определить его размерный износ А и в мкм:
А =и +-^—-и, (4.6)
" " 1000 °
где L - длина пути резания, м.
Длину пути резания можно определить по скорости резания V, м/мин, и стойкости инструмента Т, мин.:
L = V-T.
Неточность установки инструмента
Периодическая смена затупившегося инструмента вызывает необходимость настройки станка на выполняемый размер. Однако невозможно обеспечить совершенно одинаковое положение инструмента для обработки другой партии деталей. Задача настройки или установки инструмента на размер - обеспечить выполнение размеров детали в пределах поля допуска.
|
Установка инструмента, рабочих элементов станка и установочных элементов приспособления в положение, обеспечивающее получение размера в поле допуска, называется размерной наладкой станка.
Процесс наладки состоит в том, чтобы обеспечить совпадение середины поля мгновенного рассеяния с наладочным размером.
Наладка может производиться следующими методами:
- методом пробных стружек и промеров;
- методом пробных деталей;
- по калибрам наладчика (с меньшими полями допусков);
- статическая наладка (на неработающем станке) по эталону.
Деформации системы станок-приспособление-инструмент-деталь
Система станок-приспособление-инструмент-деталь (СПИД) - это замкнутая упругая система, в которой в процессе обработки действуют силы резания, закрепления и силы тяжести. Эти силы вызывают деформации, влияющие на точность обработки.
Точность обработки зависит от жесткости системы. Под жесткостью упругой системы понимают ее способность оказывать сопротивление действию сил, стремящихся ее деформировать. При отсутствии достаточной жесткости под действием сил резания и других сил система деформируется, что приводит к искажению формы детали и получению ее неправильных размеров. С жесткостью системы СПИД связано и явление вибрации. Системы, обладающие большой жесткостью, могут работать с более высокими режимами резания без появления вибраций, что обеспечивает большую производительность.
На рисунке 4.4 показана деформация вала под действием сил резания при обработке на токарном станке в центрах без люнета. На рисунке 4.5 показано
разложение силы резания на составляющие.
Рис. 4.4. Деформация вала при обработке на токарном станке в центрах без люнета
На точность обработки преимущественно влияют те деформации системы, которые изменяют расстояние между режущей кромкой инструмента и обрабатываемой поверхностью, т.е. деформации, направленные по нормали к обрабатываемой поверхности. Поэтому в технологии машиностроения жесткостью технологической системы принято называть отношение составляющей силы резания Ру, направленной по нормали к обрабатываемой поверхности, к смещению у режущей кромки инструмента в том же направлении:
Р
}= —. (4.7)
у
Рис. 4.5. Разложение силы резания на составляющие
Величина деформации прямо пропорциональна силе Ру и обратно пропорциональна жесткости системы:
Pv
У = —. (4.8)
j
Введя понятие податливости системы как величины, обратной жесткости со = 1 /у, получим:
|
у = Русо. (4.9)
Погрешность, вызванная деформациями всех звеньев системы СПИД
\ =у = Р а +а} +со +а}. (4.10)
деф J у cm np ин дет
Высокая жесткость системы СПИД является одним из основных условий обеспечения точности обработки.
Повышение жесткости технологической системы приводит к уменьшению вибраций ее звеньев и, следовательно, позволяет повышать режимы резания, не снижая точности обработки.
Тепловые деформации
На точность механической обработки деталей существенно влияют температурные деформации обрабатываемой детали, инструмента и деталей станка, вызываемые их нагревом.
Тепловые деформации возникают из-за нагрева детали и инструмента в зоне резания и нагрева станка теплом, образующимся при трении движущихся частей станка. Тепловые деформации особенно влияют на точность деталей при выполнении окончательных, чистовых операций.
При обработке с охлаждением детали и инструмента смазывающе-охлаждающей жидкостью тепловые деформации всей системы СПИД значительно уменьшаются.
Остаточные напряжения в материале заготовок
Внутренними или остаточными называют напряжения, существующие в заготовке при отсутствии внешних нагрузок. Они полностью уравновешиваются, и их действие в заготовках внешне не проявляется
Причиной появления внутренних остаточных напряжений является неравномерное охлаждение заготовки при литье, ковке, штамповке, сварке.
Особенно характерны внутренние напряжения для крупных, нежестких и толстостенных заготовок.
С течением времени внутренние напряжения в заготовке выравниваются. При снятии поверхностного слоя материала (особенно при черновых операциях, где снимается значительный слой) происходит нарушение равновесия внутренних напряжений и деталь деформируется из-за их перераспределения. Это особенно проявляется при обработке крупных литых заготовок.
Для снятия внутренних напряжений заготовок применяют медленное охлаждение (например, вместе с печью) и термообработку (отжиг, отпуск, старение естественное или искусственное). Термообработку применяют и после черновой обработки перед чистовыми операциями. На чистовых операциях уменьшаются деформации, полученные на черновых операциях. Чистовые операции, на которых снимается очень небольшой слой металла, исправляют форму детали и придают ей окончательные размеры.
Погрешность измерения
На погрешность измерения влияют точность мерительного инструмента и качество поверхности детали. Если поверхность детали имеет большую шероховатость, то при контроле размера детали измерение производят по вершинам или впадинам микронеровностей, что может существенно повлиять на показания при измерении. Чтобы достичь заданной точности размеров детали и установить при контроле, действительно ли получен заданный размер, необходимо обеспечить при обработке надлежащий класс шероховатости поверхности. Степень точности размера и параметры шероховатости поверхности связаны между собой. Параметр шероховатости Rz для размеров 5 - 10 квалитетов точности не должен превышать 25 % величины поля допуска на обрабатываемый размер. Для размеров, выполняемых по 11 и более грубым квалитетам, параметр шероховатости не должен превышать 12,5 % от величины поля допуска. Суммарную погрешность обработки трудно определить теоретически из-за различного характера и направленности перечисленных погрешностей. Одни погрешности дают увеличение размеров, другие - уменьшение; некоторые погрешности компенсируют друг друга, другие, наоборот, накладываются и увеличивают общую погрешность. Путем расчета определить влияние каждого из перечисленных факторов при их совместном действии затруднительно. Поэтому, общую погрешность обработки представляют как алгебраическую сумму погрешностей, учитывая те погрешности, которые действуют в направлении обрабатываемого размера
Аобщ = ^Аг. (4.11)
В справочной литературе приводятся таблицы достижения определенной точности различными методами обработки и инструментами, т.е. приводится величина технологического допуска 5 на выполняемый размер. Общая погрешность обработки должна находиться в пределах поля допуска на выполняемый размер
Ao6m=T;A i -S. (4.12)
Таблицы составляются на основании опытных данных для различных методов обработки. Этими таблицами пользуются при проектировании технологических процессов.
|
|
Автоматическое растормаживание колес: Тормозные устройства колес предназначены для уменьшения длины пробега и улучшения маневрирования ВС при...
Кормораздатчик мобильный электрифицированный: схема и процесс работы устройства...
Историки об Елизавете Петровне: Елизавета попала между двумя встречными культурными течениями, воспитывалась среди новых европейских веяний и преданий...
История развития пистолетов-пулеметов: Предпосылкой для возникновения пистолетов-пулеметов послужила давняя тенденция тяготения винтовок...
© cyberpedia.su 2017-2024 - Не является автором материалов. Исключительное право сохранено за автором текста.
Если вы не хотите, чтобы данный материал был у нас на сайте, перейдите по ссылке: Нарушение авторских прав. Мы поможем в написании вашей работы!