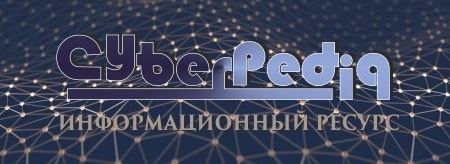
Эмиссия газов от очистных сооружений канализации: В последние годы внимание мирового сообщества сосредоточено на экологических проблемах...
История развития пистолетов-пулеметов: Предпосылкой для возникновения пистолетов-пулеметов послужила давняя тенденция тяготения винтовок...
Топ:
Оценка эффективности инструментов коммуникационной политики: Внешние коммуникации - обмен информацией между организацией и её внешней средой...
Интересное:
Финансовый рынок и его значение в управлении денежными потоками на современном этапе: любому предприятию для расширения производства и увеличения прибыли нужны...
Наиболее распространенные виды рака: Раковая опухоль — это самостоятельное новообразование, которое может возникнуть и от повышенного давления...
Принципы управления денежными потоками: одним из методов контроля за состоянием денежной наличности является...
Дисциплины:
![]() |
![]() |
5.00
из
|
Заказать работу |
Содержание книги
Поиск на нашем сайте
|
|
СОДЕРЖАНИЕ
I. Общие сведения.................................................................................. 4
II. Текст лекций...................................................................................... 5
Лекция 1. Введение.............................................................................. 5
Лекция 2. Основы проектирования технологических процессов
обработки деталей................................................................................ 9
Лекция 3. Основы базирования......................................................... 13
Лекция 4. Точность обработки деталей............................................... 16
Лекция 5. Качество поверхностей деталей машин.............................. 24
Лекция 6. Выбор заготовок................................................................. 31
Лекция 7. Определение припусков на механическую обработку... 33
Лекция 8. Расчет размерных цепей..................................................... 37
Лекция 9. Методы обработки основных поверхностей. Технологиче
ские основы типизации методов обработки......................................... 46
Лекция 10. Обработка наружных цилиндрических поверхностей.... 52
Лекция 11. Обработка внутренних цилиндрических поверхностей
(отверстий).......................................................................................... 67
Лекция 12. Методы обработки плоских поверхностей...................... 91
Лекция 13. Методы обработки резьбовых поверхностей................ 106
Лекция 14. Обработка зубчатых поверхностей................................ 116
Лекция 15. Обработка шлицевых поверхностей и шпоночных пазов.. 123
Литература 130
Процесс создания любого оборудования разделяют на два этапа: проектирование и изготовление. Первый этап завершается разработкой конструкции оборудования и представлением ее в чертежах, второй – реализацией разработанной конструкции с помощью технологического процесса, т.е. изготовлением оборудования.
Любое оборудование является сложной системой. Технология машиностроения изучает связи и закономерности в производственных процессах изготовления оборудования.
|
Под производственным процессом понимают совокупность всех этапов, которые проходят исходные продукты на пути их превращения в готовое оборудование. Этапы производственного процесса, на протяжении которых происходит качественное изменение объекта производства, называют технологическими процессами.
В зависимости от содержания, различают технологические процессы получения заготовок, изготовления деталей, сборки отдельных частей и оборудования в целом и др.
В курсе «Технологические основы машиностроения» (ТОМ) изучаются процессы механической обработки деталей машин и аппаратов, их сборки, вопросы выбора заготовок и методы их изготовления.
В курсе ТОМ рассматриваются вопросы взаимодействия станка, приспособления, режущего инструмента и обрабатываемой детали. Основным вопросом является построение наиболее рациональных технологических процессов обработки деталей или сборки изделий.
Возможность построения рационального технологического процесса обработки или сборки должна быть предусмотрена при проектировании детали или узла. Конструктор должен представлять процесс изготовления проектируемого изделия и стремиться к обеспечению технологичности как отдельных деталей, так и всего изделия в целом.
Под технологичностью конструкции понимаются свойства конструкции, определяющие ее приспособленность к достижению оптимальных затрат при производстве, эксплуатации и ремонте. Другими словами, технологичная конструкция обеспечивает изготовление, ремонт и эксплуатацию изделия наиболее экономичными методами. Чем технологичней изделие, тем меньше трудоемкость и себестоимость его изготовления, тем удобней его ремонт и эксплуатация.
Изделие и его элементы
Изделием в машиностроении называют любой предмет производства, изготовляемый на предприятии. Изделием может быть сложная машина, ее элемент в сборе (сборочная единица) и отдельная деталь.
|
Деталь - это изделие, изготовленное из однородного материала без применения сборочных операций. Характерный признак детали - отсутствие разъемных и неразъемных соединений.
Сборочная единица - это изделие, составные части которого подлежат соединению (резьбовыми соединениями, сваркой, пайкой, склеиванием, крепежными изделиями, по посадкам и т.д.). Сборочная единица может состоять из отдельных деталей, может включать в себя более мелкие сборочные единицы.
Примером детали может быть зубчатое колесо, изготовленное из цельной заготовки (отливки или штамповки), но это же зубчатое колесо может быть сборочной единицей из нескольких деталей (ступицы, диска и венца), сваренных между собой.
Исходные данные для проектирования технологического процесса
Исходной информацией для проектирования технологического процесса служат рабочие чертежи деталей, сборочные чертежи и объем годового выпуска изделий.
Технологический процесс механической обработки проектируют на основе рабочего чертежа детали. В рабочих чертежах и технических требованиях содержатся сведения о точности, параметрах шероховатости и другие требования к изделию.
Для разработки технологического процесса обработки детали необходимо предварительно изучить ее конструкцию и функции, выполняемые в узле, механизме, машине, проанализировать технологичность конструкции и проконтролировать чертеж. Рабочий чертеж детали должен иметь все данные, необходимые для исчерпывающего и однозначного понимания конструкции и требований к детали при ее изготовлении и контроле, и соответствовать действующим стандартам.
Анализ технологичности проводят по двум признакам: с одной стороны, деталь должна быть технологична как объект изготовления; с другой стороны, должна обеспечивать технологичную и удобную сборку и демонтаж как составная часть сборочной единицы или изделия.
Контроль чертежа должен включать проверку соответствия точности размеров и параметров шероховатости, требований к взаимному расположению поверхностей, правильности простановки размеров и возможных ошибок конструктора.
Однако выбор оптимального варианта технологического процесса зависит в значительной степени от объема выпуска и производственных возможностей предприятия. При определении объема выпуска изделия необходимо учитывать процент запасных частей. Объем годового выпуска определяет тип производства.
|
Поверхности и базы
Базирование - придание заготовке требуемого положения в пространстве относительно станка и режущего инструмента.
Приложение сил к заготовке для обеспечения постоянства ее положения, достигнутого при базировании, называется закреплением.
Процесс базирования и закрепления заготовки называют установкой.
При установке деталей для обработки на станках различают следующие поверхности:
- обрабатываемые поверхности, с которых снимается слой металла;
- поверхности - базы, определяющие положение детали при обработке;
- поверхности, воспринимающие зажимные усилия;
- поверхности, от которых измеряют выдерживаемые размеры;
- необрабатываемые поверхности.
База - поверхность, сочетание поверхностей, ось или точка, принадлежа
щие заготовке и используемые для базирования.
Различают базы технологические, сборочные, конструктивные.
По ГОСТ 3.1109 - 82 технологической базой называется поверхность, сочетание поверхностей, ось или точка, используемая для определения положения заготовки в процессе изготовления.
Технологические базы разделяются на установочные и измерительные.
Установочной базой называют поверхности заготовки, которыми она устанавливается для обработки в определенном положении относительно станка и режущего инструмента.
Установочными базами могут быть плоские поверхности, наружные и внутренние цилиндрические поверхности, конические поверхности, поверхности центровых отверстий.
В качестве установочных баз могут использоваться обработанные и необработанные поверхности. Необработанные поверхности называются черновыми базами и используются только на начальных операциях обработки. Обработанные поверхности называют чистовыми базами и используют в качестве баз для последующих операций.
Установочные базы могут быть основными и вспомогательными.
|
Основной установочной базой называется поверхность детали, которая служит для установки детали при обработке и сопрягается с другой деталью при сборке.
Примером основной установочной базы может служить посадочное отверстие зубчатого колеса. При обработке колесо базируется отверстием на оправке, благодаря чему обеспечивается совпадение осей посадочного отверстия и делительной окружности зубьев. При сборке поверхность отверстия сопряга-13
ется с поверхностью вала. Совпадение установочных баз зубчатого колеса при обработке и сборке обеспечивает правильную работу его в собранном узле.
Вспомогательной установочной базой называют поверхность детали, которая служит только для установки ее при обработке.
Примером вспомогательной установочной базы являются центровые отверстия валов.
Измерительная база - поверхность, от которой при измерении производится отсчет размеров.
Сборочная база - поверхность, которая определяет положение данной детали относительно других деталей в узле или изделии.
Конструктивная база - совокупность поверхностей, линий, точек, от которых задаются размеры и положение других деталей при разработке конструкций.
Исходными данными для выбора баз являются: чертеж детали со всеми необходимыми требованиями, вид и точность заготовки, условия расположения и работы детали в машине.
При выборе технологических баз следует руководствоваться принципами постоянства базы и совмещения баз.
Принцип постоянства базы
Наибольшая точность обработки достигается при обработке детали с одной установки. Однако это не всегда возможно. Для достижения наибольшей точности необходимо все дальнейшие установки детали производить по той же базе. Каждая перемена базы увеличивает погрешность установки детали.
Принцип постоянства базы: для выполнения всех операций обработки детали следует использовать одну и ту же установочную базу.
Для выполнения этого принципа часто создают базы, не имеющие конструкторского назначения, например, центровые отверстия у валов.
Принцип совмещения баз
Для достижения наибольшей точности обработки необходимо стремиться использовать одну и ту же поверхность в качестве различных баз.
Целесообразно в качестве измерительной базы использовать установочную базу, если это возможно. Еще более высокой точности обработки можно достигнуть, если совместить установочную, измерительную и сборочную базы.
Принцип совмещения баз: сборочная база является одновременно установочной и измерительной.
Решение вопроса о возможности использования установочной базы в качестве измерительной зависит от того, какой размер детали должен быть точно выдержан и от какой поверхности при измерении может быть произведен отсчет размера.
|
На рисунке 3.1 а точно выдерживается размер х, и отсчет этого размера производится от поверхности А-А, которая в данном случае является одновременно измерительной и установочной базой.
Рис.3.1. Установочная и измерительная базы
На рисунке 3.1 б точно выдерживается размер у, и отсчет его производится от поверхности В-В, которая в этом случае является измерительной базой; установочной базой по-прежнему является поверхность А-А. В последнем случае точность размера у будет зависеть от точности размера, который связывает установочную и измерительную базы.
Основные правила выбора баз
1. Следует использовать принцип совмещения баз (при совмещении измерительной и установочной баз погрешность базирования равна нулю).
2. Следует соблюдать принцип постоянства базы, т.е. на всех основных операциях использовать в качестве технологических баз одни и те же поверхности.
3. Когда постоянство установочных баз обеспечить невозможно, в качестве новой базы принимают поверхности наиболее чисто и точно обработанные.
4. Если у заготовки есть необрабатываемые поверхности, установив по которым, можно с одной установки полностью обработать деталь, то их следует принимать за установочные базы.
5. За установочные базы следует принимать такие поверхности, которые не допускали бы деформации детали от сил закрепления и резания.
6. Базы должны обеспечивать хорошую устойчивость и надежность установки заготовки.
Понятие точности
Точность - основная характеристика деталей и машин. Под точностью в машиностроении понимается степень соответствия производимых изделий заранее установленному прототипу или образцу. В качестве образца принимается деталь, заданная чертежом.
Точность детали, полученной в результате механической обработки, определяется:
- отклонениями действительных размеров детали от требуемых;
- отклонениями от геометрической формы детали или ее элементов (отклонения от прямолинейности, плоскостности, круглости, цилиндрич-ности и пр.);
- отклонениями поверхностей и осей детали от точного взаимного расположения (отклонения от параллельности, перпендикулярности, соосности, симметричности и пр.);
- шероховатостью поверхности.
Отклонения значений параметров реальной детали от детали, заданной чертежом, характеризует величину погрешности.
4.2. Факторы, влияющие на точность обработки на металлорежущих станках
Общая погрешность выполняемого размера складывается из нескольких составляющих. На точность обработки на металлорежущих станках влияют:
- неточность станка Аст;
- погрешность установки Ауст;
- неточность инструмента и его износ Аин;
- неточность установки инструмента Анастр;
- деформации деталей во время обработки, вызванные силами резания и закрепления Адеф;
- тепловые деформации Аг;
- деформации, вызванные внутренними напряжениями в материале детали Аа;
- погрешность измерения Аизм;
- ошибка исполнителя Аисп.
Рассмотрим подробнее каждую из перечисленных погрешностей, определим причины ее возникновения и степень влияния на окончательную точность детали.
Неточность станков
Точность станка в ненагруженном состоянии (геометрическая точность станка) зависит главным образом от точности изготовления деталей станка и точности их сборки. Нормы точности станка всегда выше норм точности деталей, получаемых на этом станке. Нормы точности и методы проверки точности станков регламентируются стандартами. Вследствие износа в процессе эксплуатации точность станка изменяется. Появляются такие отклонения как биение шпинделя (износ подшипников), непрямолинейность направляющих, по которым перемещается каретка суппорта, смещение центров передней и задней бабки, повышенные вибрации и т.п. Это приводит к несоосности поверхностей, смещению осей, искажению геометрической формы, ухудшению параметров шероховатости поверхностей детали.
Погрешность установки
При установке детали на станке еѐ фактическое положение отличается от требуемого. Отклонение положения установленной заготовки от требуемого называется погрешностью установки.
s =fs-,s;б, (4.1)
уст J баз ' закр ' пр '
где ббаз - погрешность базирования;
£закр - погрешность закрепления;
епр - погрешность приспособления.
Погрешность базирования s баз возникает при несовпадении измерительной и установочной баз заготовки. При совпадении измерительной и установочной баз погрешность базирования равна нулю. Так, на рисунке 4.1 погрешность базирования размера L равна нулю, так как измерительная и установочная базы совпадают: ебазЬ = 0. Погрешность базирования размера К равна допуску на размер, связывающий измерительную и установочную базы: вбазК= δ.
Рис. 4.1. Схема установки детали на плоскую поверхность
При несовпадении измерительной и установочной баз погрешность базирования определяют путем расчета, исходя из геометрических элементов схемы установки (рисунок 4.2).
Погрешность базирования размера L при посадке детали на разжимную оправку без зазора
при посадке с зазором А:
£базЬ = ^ + А. (4.3)
Рис. 4.2. Схема установки детали на цилиндрическую оправку с зазором
Погрешность базирования для размеров, определяемых инструментом, равна нулю. К таким размерам относятся размеры, определяемые только размером инструмента: диаметром сверла, зенкера, развертки, шириной фрезы и т.п. Для размеров, определяющих взаимное положение поверхностей, обработанных с одной установки, погрешность базирования также равна нулю.
На погрешность базирования влияют погрешность формы и параметры шероховатости базовой поверхности, поэтому в качестве баз следует выбирать наиболее точно обработанные поверхности.
Погрешность закрепления вызвана смещение измерительной базы по направлению измеряемого размера под действием сил закрепления. На рисунке 4.1 погрешность закрепления размеров L и К £закр К Ф 0, s3aKp L Ф 0, так как измерительная база размеров перемещается под действием прижимной силы.
Погрешность закрепления определяется в основном деформациями в месте контакта заготовки с установочными элементами. Контактные деформации зависят от величины прижимной силы Q:
y = C-Q", (4.4)
где С и п - коэффициенты, зависящие от вида контакта, материала, шероховатости поверхности.
![]() |
у
Y i
Qi
Q
Рис. 4.3. Зависимость контактных деформаций от прижимной силы
Необходимо отличать погрешность установки от неправильной схемы установки. Сила закрепления должна надежно прижимать базовую поверхность заготовки к установочным элементам приспособления. Поворот или смещение заготовки при закреплении указывает на неправильную схему установки.
Погрешность приспособления пр определяется:
- погрешностью изготовления и сборки самого приспособления;
- износом установочных элементов;
- погрешностью установки приспособления на станке. Способы устранения или уменьшения этих погрешностей:
- при использовании одного приспособления его погрешность постоянна и ее можно учесть при настройке. При использовании нескольких приспособлений-дублеров их погрешность будет входить в погрешность установки;
- износ установочных элементов приспособлений периодически контролируется и при достижении предельно допустимой величины их заменяют. Для уменьшения износа установочные элементы выполняют из закаленной стали, хромируют или наплавляют твердым сплавом.
- погрешность установки самого приспособления на станке (перекосы, смещения) уменьшают путем установки фиксаторов, направляющих элементов и т.п. на столе станка.
Погрешности £баз, £закр, пр - величины векторные. Погрешность установки определяют как векторную сумму
ч |
(4.5) |
„ 2, ~ 2, 2
£ + £ + £
уст |
баз закр пр
Погрешность приспособления обычно значительно меньше, чем погрешности базирования и закрепления. Поэтому с достаточной степенью точности погрешность установки можно определить, учитывая только погрешности базирования и закрепления.
Степень точности инструмента и его износ
Инструмент, как и всякое другое изделие, имеет свою точность изготовления. Погрешности инструмента переносятся на обрабатываемую деталь. Размеры и точность стандартных инструментов регламентированы стандартами. Выбранный инструмент должен обеспечивать заданную точность обработки.
На точность обработки существенно влияет износ инструмента. Износ инструмента характеризуется начальным износом и н (приработкой режущей
кромки) и размерным износом. Приработка режущей кромки - это износ на первой 1000 м пути резания. Во время приработки режущей кромки износ идет более интенсивно, чем при установившемся режиме резания. Размерный износ характеризуется удельным износом ио за время пути резания в 1000 м. Величина удельного износа для различных инструментов в зависимости от конкретных условий обработки приводится в справочных таблицах. Приняв по нормативным данным величину удельного износа и для обработки партии деталей од-
ним инструментом без переточки, можно определить его размерный износ А и в мкм:
А =и +-^—-и, (4.6)
" " 1000 °
где L - длина пути резания, м.
Длину пути резания можно определить по скорости резания V, м/мин, и стойкости инструмента Т, мин.:
L = V-T.
Неточность установки инструмента
Периодическая смена затупившегося инструмента вызывает необходимость настройки станка на выполняемый размер. Однако невозможно обеспечить совершенно одинаковое положение инструмента для обработки другой партии деталей. Задача настройки или установки инструмента на размер - обеспечить выполнение размеров детали в пределах поля допуска.
Установка инструмента, рабочих элементов станка и установочных элементов приспособления в положение, обеспечивающее получение размера в поле допуска, называется размерной наладкой станка.
Процесс наладки состоит в том, чтобы обеспечить совпадение середины поля мгновенного рассеяния с наладочным размером.
Наладка может производиться следующими методами:
- методом пробных стружек и промеров;
- методом пробных деталей;
- по калибрам наладчика (с меньшими полями допусков);
- статическая наладка (на неработающем станке) по эталону.
Деформации системы станок-приспособление-инструмент-деталь
Система станок-приспособление-инструмент-деталь (СПИД) - это замкнутая упругая система, в которой в процессе обработки действуют силы резания, закрепления и силы тяжести. Эти силы вызывают деформации, влияющие на точность обработки.
Точность обработки зависит от жесткости системы. Под жесткостью упругой системы понимают ее способность оказывать сопротивление действию сил, стремящихся ее деформировать. При отсутствии достаточной жесткости под действием сил резания и других сил система деформируется, что приводит к искажению формы детали и получению ее неправильных размеров. С жесткостью системы СПИД связано и явление вибрации. Системы, обладающие большой жесткостью, могут работать с более высокими режимами резания без появления вибраций, что обеспечивает большую производительность.
На рисунке 4.4 показана деформация вала под действием сил резания при обработке на токарном станке в центрах без люнета. На рисунке 4.5 показано
разложение силы резания на составляющие.
Рис. 4.4. Деформация вала при обработке на токарном станке в центрах без люнета
На точность обработки преимущественно влияют те деформации системы, которые изменяют расстояние между режущей кромкой инструмента и обрабатываемой поверхностью, т.е. деформации, направленные по нормали к обрабатываемой поверхности. Поэтому в технологии машиностроения жесткостью технологической системы принято называть отношение составляющей силы резания Ру, направленной по нормали к обрабатываемой поверхности, к смещению у режущей кромки инструмента в том же направлении:
Р
}= —. (4.7)
у
Рис. 4.5. Разложение силы резания на составляющие
Величина деформации прямо пропорциональна силе Ру и обратно пропорциональна жесткости системы:
Pv
У = —. (4.8)
j
Введя понятие податливости системы как величины, обратной жесткости со = 1 /у, получим:
у = Русо. (4.9)
Погрешность, вызванная деформациями всех звеньев системы СПИД
\ =у = Р а +а} +со +а}. (4.10)
деф J у cm np ин дет
Высокая жесткость системы СПИД является одним из основных условий обеспечения точности обработки.
Повышение жесткости технологической системы приводит к уменьшению вибраций ее звеньев и, следовательно, позволяет повышать режимы резания, не снижая точности обработки.
Тепловые деформации
На точность механической обработки деталей существенно влияют температурные деформации обрабатываемой детали, инструмента и деталей станка, вызываемые их нагревом.
Тепловые деформации возникают из-за нагрева детали и инструмента в зоне резания и нагрева станка теплом, образующимся при трении движущихся частей станка. Тепловые деформации особенно влияют на точность деталей при выполнении окончательных, чистовых операций.
При обработке с охлаждением детали и инструмента смазывающе-охлаждающей жидкостью тепловые деформации всей системы СПИД значительно уменьшаются.
Остаточные напряжения в материале заготовок
Внутренними или остаточными называют напряжения, существующие в заготовке при отсутствии внешних нагрузок. Они полностью уравновешиваются, и их действие в заготовках внешне не проявляется
Причиной появления внутренних остаточных напряжений является неравномерное охлаждение заготовки при литье, ковке, штамповке, сварке.
Особенно характерны внутренние напряжения для крупных, нежестких и толстостенных заготовок.
С течением времени внутренние напряжения в заготовке выравниваются. При снятии поверхностного слоя материала (особенно при черновых операциях, где снимается значительный слой) происходит нарушение равновесия внутренних напряжений и деталь деформируется из-за их перераспределения. Это особенно проявляется при обработке крупных литых заготовок.
Для снятия внутренних напряжений заготовок применяют медленное охлаждение (например, вместе с печью) и термообработку (отжиг, отпуск, старение естественное или искусственное). Термообработку применяют и после черновой обработки перед чистовыми операциями. На чистовых операциях уменьшаются деформации, полученные на черновых операциях. Чистовые операции, на которых снимается очень небольшой слой металла, исправляют форму детали и придают ей окончательные размеры.
Погрешность измерения
На погрешность измерения влияют точность мерительного инструмента и качество поверхности детали. Если поверхность детали имеет большую шероховатость, то при контроле размера детали измерение производят по вершинам или впадинам микронеровностей, что может существенно повлиять на показания при измерении. Чтобы достичь заданной точности размеров детали и установить при контроле, действительно ли получен заданный размер, необходимо обеспечить при обработке надлежащий класс шероховатости поверхности. Степень точности размера и параметры шероховатости поверхности связаны между собой. Параметр шероховатости Rz для размеров 5 - 10 квалитетов точности не должен превышать 25 % величины поля допуска на обрабатываемый размер. Для размеров, выполняемых по 11 и более грубым квалитетам, параметр шероховатости не должен превышать 12,5 % от величины поля допуска. Суммарную погрешность обработки трудно определить теоретически из-за различного характера и направленности перечисленных погрешностей. Одни погрешности дают увеличение размеров, другие - уменьшение; некоторые погрешности компенсируют друг друга, другие, наоборот, накладываются и увеличивают общую погрешность. Путем расчета определить влияние каждого из перечисленных факторов при их совместном действии затруднительно. Поэтому, общую погрешность обработки представляют как алгебраическую сумму погрешностей, учитывая те погрешности, которые действуют в направлении обрабатываемого размера
Аобщ = ^Аг. (4.11)
В справочной литературе приводятся таблицы достижения определенной точности различными методами обработки и инструментами, т.е. приводится величина технологического допуска 5 на выполняемый размер. Общая погрешность обработки должна находиться в пределах поля допуска на выполняемый размер
Ao6m=T;A i -S. (4.12)
Таблицы составляются на основании опытных данных для различных методов обработки. Этими таблицами пользуются при проектировании технологических процессов.
Лекция 6. ВЫБОР ЗАГОТОВОК
Рассматриваемые вопросы: Виды и способы получения заготовок. Заготовки для типовых деталей.
Заготовка – это предмет производства, из которого изменением формы и размеров, свойств материала и шероховатости поверхности изготавливают деталь.
Выбрать заготовку – значит определить ее рациональный вид, определяющий конфигурацию заготовки, метод ее получения, размеры, припуски на обработку.
При выборе заготовки учитывают форму, размеры и массу детали, материал, масштаб производства, периодичность повторения, размеры припусков на обработку и точность размеров.
Конфигурация заготовки вытекает из конструкции детали и определяется ее размерами и материалом, а также условиями работы детали.
Метод получения заготовки определяется назначением и конструкцией детали, материалом и объемом выпуска.
Материал заготовки обычно задается конструктором на рабочем чертеже. Конструктор назначает технические требования, предъявляемые к детали, и может задавать метод изготовления заготовки. Технолог при разработке технологического процесса обработки детали обязан проверить обоснованность принятых конструктором решений. От правильности выбора заготовки зависят трудоемкость и себестоимость обработки. При изготовлении заготовки, максимально приближающейся по форме и размерам к готовой детали, значительная часть трудоемкости относится на долю изготовления заготовки и меньшая часть – на механическую обработку. И, наоборот, при изготовлении заготовок простой формы с большими припусками основная доля трудоемкости приходится на механическую обработку.
Уравнение размерной цепи
Для достижения требуемой точности машины и ее отдельных деталей необходимо правильно установить размеры и допускаемые отклонения размеров для отдельных деталей и их взаимного расположения. Эта задача требует расчета размерных цепей.
Размерной цепью называется замкнутая цепь взаимно связанных размеров, определяющих взаимное положение поверхностей и осей детали или деталей.
Различают следующие виды размерных цепей:
– размерные цепи с линейными размерами и параллельными звеньями;
– размерные цепи с линейными размерами и непараллельными звеньями;
– размерные цепи с угловыми размерами;
– пространственные размерные цепи.
Элементы детали или узла, образующие размерную цепь, называют звеньями размерной цепи.
Звено размерной цепи - это размер, определяющий расстояние между поверхностями или осями.
Исходное или замыкающее звено - это размер, связывающий поверхности или оси, расстояние между которыми необходимо обеспечить. Исходным это звено называется тогда, когда с него начинается построение размерной цепи, замыкающим - когда оно при построении размерной цепи получается последним. Все остальные звенья в размерной цепи называются составляющими.
Изменение величины составляющего звена оказывает влияние на величину замыкающего звена. Составляющее звено называется увеличивающим, если с его увеличением увеличивается замыкающее звено. Составляющее звено называется уменьшающим, если с его увеличением замыкающее звено уменьшается.
А 1
-*-
А 2
а
![]() |
А 1
А,
б
Рис.8.1. Размерная цепь с параллельными звеньями
1 – уменьшающее звено, замыкающее звено |
а
ось; б – схема размерной цепи: А 1
А
увеличивающее звено,
А
Каждое из составляющих звеньев размерной цепи может изменяться в пределах своего допуска. Эти изменения составляющих размеров влекут за собой изменение величины замыкающего звена. Для определения величины замыкающего звена используют уравнение размерной цепи:
k -i
A = Е i -4
(8.1)
i =1
где к- Q' А-Аt |
общее число звеньев в размерной цепи;
передаточное отношение;
замыкающее звено;
составляющее звено. Для линейных цепей с параллельными звеньями передаточное отношение для увеличивающих составляющих звеньев равно 1, для уменьшающих составляющих звеньев – равно минус 1, т.е. уравнение (8.1) для линейной размерной цепи с параллельными звеньями можно представить в виде
А = ЕД-ЁД, (8.2)
i =\ i =\
где Д. - увеличивающее составляющее звено;
т - число увеличивающих составляющих звеньев; Д. - уменьшающее составляющее звено; п - число уменьшающих составляющих звеньев. Определим предельные размеры замыкающего звена А А для размерной
цепи на рисунке 8.1. Наибольший предельный размер А Атах и наименьший предельный размер Аmin будут соответственно равны:
А maX = Amax-Ami„, (8.3)
А т1„= А т1„-Лтах. (8.4)
При вычитании уравнения (8.4) из уравнения (8.5) получим:
А тах - А n*, = (А тах - А т1„) + (Лтах - Лт1„) (8.5)
или
SA = S 2 + S. (8.6)
Мы получили уравнение допусков для размерной цепи. Таким образом, допуск замыкающего звена равен сумме допусков составляющих звеньев:
A = Z, (8.7)
2= 1
где SA - допуск замыкающего звена; 5t - допуск составляющего звена. Приведенное уравнение допусков (8.7) является основным уравнением размерного анализа, из которого вытекают два основных правила.
1. В качестве замыкающего звена в размерной цепи надо выбирать са
мое грубое (с точки зрения эксплуатации) по точности звено, чтобы
для него можно было назначить суммарный допуск всей размерной
цепи.
Это правило основано на том, что на замыкающем звене, как на последнем по процессу изготовления, накапливаются погрешности предшествующей обработки всех составляющих звеньев.
2. Для облегчения решения размерной цепинеобходимо проектировать
размерные цепи с наименьшим числом звеньев.
Это правило называют правилом короткой размерной цепи. Это объясняется тем, что при большом количе
|
|
Эмиссия газов от очистных сооружений канализации: В последние годы внимание мирового сообщества сосредоточено на экологических проблемах...
Папиллярные узоры пальцев рук - маркер спортивных способностей: дерматоглифические признаки формируются на 3-5 месяце беременности, не изменяются в течение жизни...
Состав сооружений: решетки и песколовки: Решетки – это первое устройство в схеме очистных сооружений. Они представляют...
История создания датчика движения: Первый прибор для обнаружения движения был изобретен немецким физиком Генрихом Герцем...
© cyberpedia.su 2017-2024 - Не является автором материалов. Исключительное право сохранено за автором текста.
Если вы не хотите, чтобы данный материал был у нас на сайте, перейдите по ссылке: Нарушение авторских прав. Мы поможем в написании вашей работы!