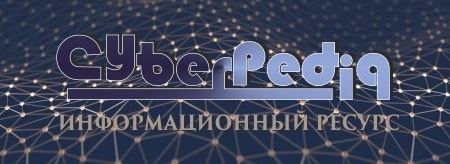
Археология об основании Рима: Новые раскопки проясняют и такой острый дискуссионный вопрос, как дата самого возникновения Рима...
Историки об Елизавете Петровне: Елизавета попала между двумя встречными культурными течениями, воспитывалась среди новых европейских веяний и преданий...
Топ:
Генеалогическое древо Султанов Османской империи: Османские правители, вначале, будучи еще бейлербеями Анатолии, женились на дочерях византийских императоров...
Определение места расположения распределительного центра: Фирма реализует продукцию на рынках сбыта и имеет постоянных поставщиков в разных регионах. Увеличение объема продаж...
Устройство и оснащение процедурного кабинета: Решающая роль в обеспечении правильного лечения пациентов отводится процедурной медсестре...
Интересное:
Финансовый рынок и его значение в управлении денежными потоками на современном этапе: любому предприятию для расширения производства и увеличения прибыли нужны...
Мероприятия для защиты от морозного пучения грунтов: Инженерная защита от морозного (криогенного) пучения грунтов необходима для легких малоэтажных зданий и других сооружений...
Что нужно делать при лейкемии: Прежде всего, необходимо выяснить, не страдаете ли вы каким-либо душевным недугом...
Дисциплины:
![]() |
![]() |
5.00
из
|
Заказать работу |
Содержание книги
Поиск на нашем сайте
|
|
Для повышения обрабатываемости резанием и стабилизации размеров литые заготовки подвергают термообработке. Характер термообработки зависит от вида литейного сплава, способа литья, размеров отливки и других факторов.
Термическая обработка чугуна применяется для изменения структуры металлической основы чугуна (матрицы), степени графитизации, снижения остаточных напряжений, стабилизации размеров. При этом форма графита в чугуне не изменяется.
Графитизирующий отжиг используют для разложения карбидов (устранения отбела) в отливках из всех видов чугуна и снижения твердости поверхностного слоя. Он производится при температуре 850...980°С. Продолжительность отжига зависит от размеров отливки, толщины стенок, химического состава чугуна и обычно принимается из расчета I ч на каждые 25 мм толщины стенки отливки.
Для снижения твердости по всему сечению отливки и получения ферритной структуры матрицы производят вторую стадию отжига при температуре 700...720°С. Переход с температуры 850...980 °С до 720 °С желательно проводить медленно. Это позволяет получить больше феррита и придает большую пластичность отливке. Окончательное охлаждение отливок в интервале температур 500...300°С стремятся производить быстро во избежание отпускной хрупкости.
Нормализация чугуна производится при температуре 850... 950 °С с целью получения отливок повышенной прочности и износостойкости, т. е. получения отливок со структурой перлита. Одновременно происходит измельчение перлита и частичное снятие остаточных напряжений. После полного прогрева отливки выдерживаются в печи еще 30... 120 мин с целью выравнивания структур по всему объему. Охлаждение производится на воздухе. Используя нормализацию, можно повысить марку чугуна примерно на два класса.
|
Отпуск как самостоятельный вид термообработки применяют только для снятия остаточных напряжений отливок из серого чугуна. При этом их нагревают до температуры 500...550°С, выдерживают 2...8 ч и охлаждают вместе с печью.
Стальные отливкиобычно имеют крупнозернистую неоднородную структуру и низкую пластичность. В зависимости от химического состава стальное литье отжигают при температуре 850... 900 °С с выдержкой в течение 2...4 ч и охлаждают с печью. В этом случае получают наибольшую пластичность и минимальный уровень внутренних напряжений.
При нормализации отливки нагревают до той же температуры, выдерживают 4...5 ч, а затем охлаждают на воздухе. Это приводит к выравниванию и измельчению структуры.
Для средне- и высокоуглеродистых сталей нормализация дает более высокую твердость и меньшую пластичность, чем отжиг. Для низкоуглеродистых сталей нормализация как более дешевый вид термообработки может полностью заменить отжиг.
Термическая обработка отливок из цветных металловприменяется редко, в основном не для улучшения обрабатываемости резанием, а для улучшения механических свойств заготовки. Вид термической обработки указывается в технических условиях на отливку. Для снятия остаточных напряжений, возникающих в крупных отливках с неравномерным сечением стенок, применяют отпуск. Режим отпуска зависит от вида сплава, толщины стенок и конфигурации отливок.
Дефекты отливок, способы их предупреждения и исправления
Основными видами литейных дефектов являются искажения формы и размеров, разрывы сплошности металла, различные раковины и поверхностные дефекты. Искажения формы и размеров проявляются в виде коробления, недоливов, перекосов.
Коробление возникает в отливке в результате значительных остаточных напряжений при охлаждении из-за неравномерности охлаждения, торможения усадки. Недолив возникает при неправильной конструкции литниковой системы, недостаточной жидко-текучести сплава или утечке металла в разъем формы. Перекос может быть вызван неточной сборкой стержней или формы, плохим центрированием половинок стержневого ящика, случайным сдвигом полуформ, вызванным внешним воздействием.
|
Для предотвращения искажений формы отливок следует проработать более рациональную конструкцию отливки и технологию литья, увеличить податливость формы, повысить технологическую дисциплину и т. д.
Разрывы сплошности металла проявляются в виде горячих и холодных трещин, спаев.
Горячие и холодные трещины вызываются в основном недостатками конструкции отливки: наличием «термических узлов», завышенной температурой заливки, недостаточной податливостью формы и стержней, недостаточной пластичностью металла в интервале температур образования трещин. Спай - сквозная либо поверхностная с закругленными краями щель - получается из-за недостаточной скорости заливки формы, пониженной жидкотекучести, недостаточной эффективности вентиляции формы.
Для предупреждения возникновения горячих трещин в отливках необходимо создавать условия, способствующие формированию мелкозернистой структуры; обеспечивать одновременное охлаждение тонких и толстых частей отливок; увеличивать податливость литейных форм; по возможности снижать температуру заливки сплава. Для предупреждения образования в отливках холодных трещин необходимо обеспечивать равномерное охлаждение отливок во всех сечениях путем использования холодильников; применять сплавы для отливок с высокой пластичностью; проводить отжиг литейных отливок и т. п.
Усадочные раковины и рыхлоты возникают из-за нетехнологичности конструкции отливки, неправильной конструкции литниковой системы, недостаточной эффективности холодильников. Образование газовых раковин связано с повышенной газотворностью и низкой газопроницаемостью формы и стержней, пониженной температурой заливки, с механическим захватом газов в элементах литниковой системы во время заливки.
Шлаковые раковины образуются при пониженной вязкости шлака, недостаточной эффективности литниковой системы, неправильной или небрежной заливке. Для уменьшения газовых раковин и пористости в отливках плавку следует вести под слоем флюса, в среде защитных газов с использованием хорошо просушенных шихтовых материалов. Кроме того, перед заливкой расплавленный металл необходимо подвергать дегазации вакуумированием, продувкой инертными газами и другими способами, а также увеличивать газопроницаемость литейных форм и стержней, снижать влажность формовочной смеси, подсушивать формы и т. д.
|
Пригар - поверхностный дефект возникающий из-за слишком высокой температуры заливки, излишней длительности заливки, слабого уплотнения или низкого качества формовочной смеси.
Обнаруженные дефекты могут быть исправимыми и неисправимыми. Обычно возможность и способ исправления дефектов оговариваются в технических условиях.
Так, коробление стальных отливок может быть исправлено правкой. Наружные дефекты заваривают дуговой или газовой сваркой. При недоливе крупных отливок иногда допускается исправление дефекта заливкой жидкого металла. Раковины и пористость устраняют пропиткой или заделывают различными замазками, шпатлевкой или клеями. Неисправимый брак требует пересмотра конструкции отливки или технологии ее получения.
Контрольные вопросы
1. Что определяет универсальность использования песчано-глинистых форм при литье?
2. От чего зависит выбор материала модельных комплектов?
3. Какие факторы учитывают при назначении поверхности разъема литейной формы?
4. В каких случаях целесообразно разместить всю отливку в одной (нижней) части формы?
5. В какой части отливки наблюдается более высокое качество металла, а в какой - менее высокое?
6. Каковы основные требования технологичности отливок?
7. Объясните назначение и расскажите виды термической обработки отливок из чугуна, стали, цветных сплавов.
8. Перечислите дефекты отливок и причины их возникновения.
9. Как осуществляется контроль качества на различных стадиях производства литых заготовок?
Лекция 4 СПЕЦИАЛЬНЫЕ МЕТОДЫ ЛИТЬЯ
Литье в металлический формы
Литье в металлические формы (кокиль) является одним из прогрессивных способов получения отливок из чугуна, стали и цветных сплавов массой от нескольких граммов до десятков тонн.
|
Сущность процесса заключается в многократном применении металлической формы, имеющей гораздо более высокую стойкость, чем обычная песчано-глинистая, поэтому их иногда называют постоянными. Полости в отливке выполняют при помощи металлических или песчаных стержней, которые извлекают из отливки после ее затвердевания и охлаждения до заданной температуры. Чаще всего металлические формы изготавливают из серого чугуна, реже из различных марок стали. В последнее время для изготовления металлических форм стали применять сплавы алюминия с анодированными рабочими поверхностями (при анодировании создается прочная и огнеупорная пленка оксидов алюминия).
Характерным свойством металлических форм является высокая теплопроводность. Вследствие этого процесс кристаллизации сплавов, залитых в металлические формы, и их дальнейшее охлаждение протекают с большой скоростью. Это приводит к образованию мелкозернистой структуры, что сказывается на повышении механических свойств металла отливок. Исключением является серый чугун, так как большая скорость охлаждения серого чугуна в металлической форме вызывает образование так называемого отбела, когда в поверхностных слоях отливки, а иногда даже во всем ее объеме возникает структура с высокой твердостью и хрупкостью. Поэтому приходится проводить тщательный подбор химического состава чугуна в зависимости от толщины сечений отливки, осуществлять покрытие рабочих поверхностей металлических форм огнеупорными, теплоизоляционными составами или красками и нагревание их перед работой до 300 °С.
Большим и основным недостатком металлических форм является отсутствие податливости. Это часто приводит к необходимости применения песчаных стержней, формирующих внутренние полости и отверстия, а также участки внешней поверхности отливки между выступающими элементами. В таких случаях форма становится комбинированной или полуметаллической.
Металлические формы в зависимости от величины, массы, материала и формы отливаемой заготовки изготавливают литьем или механической обработкой. Литые металлические формы могут иметь обработанные и необработанные рабочие поверхности. Формы с необработанными рабочими поверхностями, отлитые из чугуна и стали, имеют более высокую стойкость.
Конструкция металлических форм зависит от конфигурации и массы отливок, вида сплава и способа его заливки в форму, масштабов производства и других факторов. Они могут быть одногнездными и многогнездными, неразъемными (вытряхными) и разъемными (с вертикальной или горизонтальной плоскостью разъема), с одним или несколькими разъемами, с металлическими или песчаными стержнями. Число рабочих полостей в металлической литейной форме зависит от массы и размера литых деталей. Многогнездные металлические формы применяют только для получения небольших деталей. Неразъемные формы обычно отличают простота конструкции, легкость изготовления и обслуживания. Их применяют для получения деталей простой конфигурации, легко извлекаемых из металлической формы. К подобным деталям относятся грузы, вкладыши, крышки, колосники и др. На рис. 4.1, а представлена одногнездная неразъемная металлическая форма, а на рис. 4.1, 6 - полуметаллическая форма, в которой предусмотрено применение песчаного стержня.
|
Для небольших отливок простой конфигурации применяют также разъемные металлические формы. На рис. 4.1, в показана многогнездная металлическая форма с вертикальной плоскостью разъема. На рис. 4.1, г показана полуметаллическая форма с вертикальным разъемом для получения более сложных деталей - тройников из латуни. Часто применяют металлические формы с горизонтальной плоскостью разъема (рис. 4.1, д).
Рисунок 4.1. Конструкции металлических форм:
а - одногнездная неразъемная форма; 6 - полуметаллическая форма с песчаным стержнем; в - многогнездная форма с вертикальной плоскостью разъема; г - полуметаллическая форма; д - форма с горизонтальной плоскостью разъема; е - форма с двумя разъемами и металлическими стержнями; 1, 5 - вертикальные половины формы; 2, 3, 4 - отдельные части стержня, формирующие внутреннюю полость; 6 - поддон
Для отливок сложной формы приходится применять несколько разъемов. Пример такой металлической формы с двумя разъемами и металлическими стержнями для получения отливки поршня из алюминиевого сплава показан на рис. 4.1, е. Форма состоит из двух частей (1 и 5) с вертикальной плоскостью разъема, которые устанавливаются на поддон 6 с образованием горизонтальной плоскости разъема. Центральный стержень, выполняющий внутреннюю полость поршня, имеет сложную разъемную конструкцию, состоящую из трех отдельных частей 2, 3 и 4. После заливки формы сплавом и его затвердевания неподатливые металлические стержни необходимо своевременно удалять из отливки, чтобы предотвратить образование трещин в отливках из-за развития больших усадочных напряжений.
По сравнению с литьем в песчано-глинистые формы литье в металлические формы обладает рядом технических и технологических преимуществ:
• многократное использование форм;
• повышение точности размеров отливок, уменьшение шероховатости поверхности, что позволяет снизить припуск на механическую обработку в два-три раза, а иногда и полностью ее устранить; увеличение выхода годного до 75-95 %;
• повышение плотности отливок, улучшение структуры отливок и повышение их механических свойств на 15-30 %;
• сокращение, а в некоторых случаях полное исключение формовочных материалов и стержневых смесей;
• исключение трудоемких операций формовки, сборки и выбивки форм;
• наличие возможности комплексной механизации и автоматизации технологического процесса, что приводит к росту производительности труда и снижению трудоемкости почти в три раза;
• увеличение съема с 1 кв. м производственной площади и снижение себестоимости отливок.
Вместе с тем изготовление отливок в металлические формы имеет и свои сложности:
• трудность получения отливок с поднутрениями, для выполнения которых необходимо применять стержни и вставки;
• снижение жидкотекучести сплавов, усложняющее получение тонкостенных, большой протяженности отливок;
• неподатливая, газонепроницаемая форма вызывает появление в отливках литейных дефектов (коробления, трещин, газовой пористости);
• высокая стоимость литейных форм, сложность и длительность их изготовления.
Металлические формы с металлическими стержнями применяют преимущественно для получения небольших по размерам деталей из алюминиевых, магниевых и цинковых сплавов и значительно реже - при отливке деталей из чугуна и сплавов на основе меди. Детали значительных размеров и сложной конфигурации, как правило, отливают в полуметаллических формах.
Процесс получения отливок в металлических формах легко поддается механизации. Сборку металлических форм перед заливкой металлом и разборку для извлечения отливок осуществляют как с помощью отдельных механизмов, так и с помощью разнообразных машин (однопозиционных и многопозиционных). В зависимости от массы металла, заливаемого в форму, производительность существующих машин колеблется в пределах 4-200 отливок в час.
|
|
Механическое удерживание земляных масс: Механическое удерживание земляных масс на склоне обеспечивают контрфорсными сооружениями различных конструкций...
Папиллярные узоры пальцев рук - маркер спортивных способностей: дерматоглифические признаки формируются на 3-5 месяце беременности, не изменяются в течение жизни...
Архитектура электронного правительства: Единая архитектура – это методологический подход при создании системы управления государства, который строится...
Индивидуальные очистные сооружения: К классу индивидуальных очистных сооружений относят сооружения, пропускная способность которых...
© cyberpedia.su 2017-2024 - Не является автором материалов. Исключительное право сохранено за автором текста.
Если вы не хотите, чтобы данный материал был у нас на сайте, перейдите по ссылке: Нарушение авторских прав. Мы поможем в написании вашей работы!