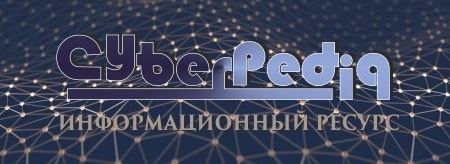
Особенности сооружения опор в сложных условиях: Сооружение ВЛ в районах с суровыми климатическими и тяжелыми геологическими условиями...
Типы оградительных сооружений в морском порту: По расположению оградительных сооружений в плане различают волноломы, обе оконечности...
Топ:
Техника безопасности при работе на пароконвектомате: К обслуживанию пароконвектомата допускаются лица, прошедшие технический минимум по эксплуатации оборудования...
Оценка эффективности инструментов коммуникационной политики: Внешние коммуникации - обмен информацией между организацией и её внешней средой...
Интересное:
Финансовый рынок и его значение в управлении денежными потоками на современном этапе: любому предприятию для расширения производства и увеличения прибыли нужны...
Как мы говорим и как мы слушаем: общение можно сравнить с огромным зонтиком, под которым скрыто все...
Инженерная защита территорий, зданий и сооружений от опасных геологических процессов: Изучение оползневых явлений, оценка устойчивости склонов и проектирование противооползневых сооружений — актуальнейшие задачи, стоящие перед отечественными...
Дисциплины:
![]() |
![]() |
5.00
из
|
Заказать работу |
Содержание книги
Поиск на нашем сайте
|
|
Для правильной оценки возможности применения литья по выплавляемым моделям необходимо сопоставить его преимущества и недостатки.
Этот способ литья позволяет максимально приблизить отливку по форме и размерам к готовой детали, а в ряде случаев получить литую деталь в окончательном виде, не требующую какой-либо дополнительной обработки перед сборкой. При этом достигается резкое снижение трудоемкости механической обработки, уменьшается расход металла и металлорежущего инструмента, сокращается потребность в металлорежущих станках. Создается также возможность для совершенствования конструкции деталей и объе-динения отдельных мелких деталей в цельнолитые узлы при уменьшении их габаритных размеров и массы.
Рисунок 4.12 - Заключительные операции изготовления оболочковой формы: а - удаление моделей выплавлением; б – прокаливание
Литье по выплавляемым моделям обладает следующими недостатками:
§ процесс изготовлении формы многооперационный, трудоемкий и длительный;
§ большое число технологических факторов, влияющих на качество формы отливки и соответственно сложность управлении качеством;
§ большая номенклатура технологических материалов;
§ повышенная температура заливки и применение предварительно нагретых форм приводят к снижению механических свойств;
§ повышенный расход металла на литники и поэтому невысокий технологический выход годного.
Масса отливок при литье по выплавляемым моделям ограничена. Отливки изготавливают массой от нескольких граммов до нескольких десятков килограммов, но преимущественно в пределах 50...500 г. Наибольшие размеры отливок достигают 1000 мм.
Данный способ оказывается наиболее рентабельным:
|
• при крупносерийном и массовом производстве мелких, но сложных и ответственных деталей, с высокими требованиями к точности размеров и шероховатости поверхности; особенно эффективно применение литья по выплавляемым моделям, если эти требования могут быть обеспечены влитом состоянии без последующей механической обработки;
• для деталей сложной конфигурации, которые нельзя изготовить как одно целое никакими иными способами;
• при изготовлении отливок со сложными внутренними очертаниями, когда достигается снижение себестоимости отливки за счет экономии металла;
• для деталей, изготавливаемых из металлов и сплавов, которые не поддаются обработке давлением, а также сплавов с низкими литейными свойствами.
Способ литья по выплавляемым моделям используют для получения отливок из литейных сплавов на основе железа, никеля, титана, меди и алюминия. Однако чаще всего этот способ литья применяют при производстве отливок из сталей, особенно из специальных, и сплавов, плохо поддающихся механической обработке.
Заливка форм, имеющих высокую температуру, позволяет получать отливки с малой толщиной стенок (0,5... 1,0 мм) при протяженности стенки до 50 мм. Тонкие стенки могут быть выполнены только при площади их поверхности не более 100×100 мм. Отдельные кромки отливок могут иметь толщину 0,7...0,8 мм и протяженность не более 10 мм. Оптимальная толщина стенок отливки составляет 6 мм, так как при большей толщине и недостаточном питании отливки жидким металлом могут появиться усадочные и газовые раковины и пористость.
Минимальная толщина стенок приведена в табл. 4.7.
Таблица 4.7 - Минимальная толщина стенок, мм
Сплавы | Наибольшие габаритные размеры отливок | ||||
До 50 | 50-100 | 100-200 | 200-350 | 350-500 | |
Сталь: | |||||
углеродистая | 2,5-4 | 4-5 | 5-6 | 6-7 | 7-10 |
легированная | 3-4,8 | 4,8-6 | 6-7,2 | 7-8 | 8-12 |
Алюминиевые | 2,5-4 | 4-5 | 5-6 | 6-7 | 8-9 |
Магниевые | 2,5-4 | 4-5 | 4-6 | 5-7 | 7-8 |
Медные | 2-3 | 4-5 | 4-6 | 5-7 | 6-8 |
Цинковые | 1,5-2 | 3-4 | 3,5-5 | 4-6 | 5-7 |
Оловянно-свинцовые | 1,5-2 | 2-3 | 3-4 | 3,5-5 | 4-6 |
Чугун | 2-3 | 3,5-4 | 4-5 | 4,5-6 | 5-8 |
|
При конструировании деталей, ориентируемых на изготовление их способом литья по выплавляемым моделям, избегают местных утолщений и резких переходов от толстого сечения к тонкому. Отношение толщин сопряженных стенок не должно превышать 1:4. Для исключения коробления литых деталей с тонкими стенками протяженностью более 150 мм либо со стенками неравномерной толщины предусматривают технологические окна (отверстия) или ребра жесткости. Отверстия в отливках можно получить любой формы - как сквозные, гак и глухие, однако диаметром не менее 3 мм. Отверстия диаметром 3...5 мм рекомендуют выполнять только в отливках из сплавов, не поддающихся механической обработке. Сквозные отверстия рекомендуют выполнять в отливках при отношении их глубины к диаметру не более 2: 1, а глухие - при отношении 1:1; отверстия малого диаметра в стенках большой толщины выполняют при помощи трубок, залитых в отливке.
При необходимости выполнить отверстие в стенках отливок делают специальные выступы и бобышки (рис. 4.13). Высоту выступа устанавливают в зависимости от диаметра отверстия или толщины ступени Н =(4–6) D или Н ≥2,5 t (рис. 4.13, а, б). Толщину стенки выступа назначают в зависимости от толщины стенки отливок t 1 =(1–1,5) t. Если отверстия расположены на торцах стенки (рис. 4.13, в, г), то соотношения размеров следующие: Н =2,25 D, С =4,5 В, А =1,5 В.
Рисунок 4.13 - Формы выступов в отливках: а - на плоской стенке; б - в углу стенки; в, г - на торцах стенки
Прямые стенки большой протяженности рекомендуют заменять искривленными или предусматривать в них технологические окна для увеличения жесткости конструкции отливки; сопряжение стенок оформляют по радиусам или галтелью.
Следует избегать глубоких пазов и узких полостей, для оформления которых могут потребоваться стержни. Ширина паза или расстояние между выступами (рис. 4.14) могут быть выполнены при h <2b, если для сплавов цветных металлов b >1 мм, для стали b ≥2,5 мм.
Рисунок 4.14 - Размеры паза отливки
При данном способе литья наиболее качественными получаются сложные корпусные, компактные детали, поэтому желательно объединять несколько деталей в одну с последующим разделением их тем или иным способом. Крупные плоскостные детали, наоборот, целесообразно расчленять на более мелкие с последующей сборкой отдельных частей.
|
Экономическую целесообразность изготовления деталей литьем по выплавляемым моделям необходимо рассчитывать в каждом конкретном случае сравнением себестоимости детали, полученной этим способом, с себестоимостью деталей, полученных механической обработкой, штамповкой или литьем иным способом. Использование деталей, полученных литьем по выплавляемым моделям, вместо штампованных позволяет снизить расход металла на 55...75%, трудоемкость механической обработки - на 50...60% и себестоимость деталей - на 20 %.
Себестоимость 1 т литья, получаемого по выплавляемым моделям, при всех условиях значительно выше, чем при литье в песчаные или оболочковые формы. Например, в условиях массового производства на автомобильных заводах себестоимость 1 т отливок по выплавляемым моделям в 6 - 7 раз выше по сравнению с отливками, получаемыми в сырых песчано-глинистых формах, и в 5 -6 раз - по сравнению с отливками, получаемыми в оболочковых формах.
Поэтому способ литья по выплавляемым моделям применяют, прежде всего, в тех случаях, когда необходимо осуществить получение точных по конструкции и размерам отливок из сплавов со специальными свойствами, которые с очень большим трудом обрабатываются режущим инструментом, а также не могут подвергаться обработке давлением (штамповке). К таким отливкам относят лопатки газовых турбин, работающие при высоких температурах газа (900...950 °С), изготавливаемые из специальных жаростой-ких сверхтвердых сплавов. Другим примером может служить турбинное колесо турбокомпрессора, имеющее 18 лопаток сложного профиля, минимальная толщина которых равна (0,8 ±0,2) мм, а отклонение по шагу допускается не более ±0,3 мм. Изготовить подобную деталь методом механической обработки сложно. Похожими на рассмотренную деталь являются насосные крыльчатки или роторы. Для получения подобных деталей способ литья по выплавляемым моделям может оказаться единственно возможным или наиболее оптимальным.
Отливки, выполняемые литьем по выплавляемым моделям, применяют для изготовления разнообразных деталей авиационной и автотракторной промышленности, тяжелого, транспортного и нефтяного машиностроения, приборостроения, а также для деталей подшипников, весов, пресс-форм и штампов, бурового, режущего и измерительного инструмента.
|
Применение литья по выплавляемым моделям может оказаться рентабельным в условиях мелкосерийного производства, а также для получения опытных образцов деталей, которые при крупносерийном производстве должны изготавливаться другими способами точного литья, требующими дорогостоящей оснастки (литье под давлением, литье в оболочковые формы). В таких случаях рекомендуют снижать затраты на специальную оснастку путем применения гипсовых пресс-форм и разовых полистироловых моделей.
Контрольные вопросы
1. Металлическая форма является одноразовой или многоразовой?
2. В чем заключается основной недостаток металлических форм?
3. Из каких материалов изготавливают стержни для литья в металлические формы?
4. В каких случаях целесообразно применение металлических форм без разъема?
5. Почему при литье в металлические формы толщина стенок отливок должна быть больше, чем при литье в песчано-глинистые формы?
6. При каком типе производства экономически целесообразно применять литье в металлические формы?
7. Из какого материала изготавливают литейные формы для литья под давлением?
8. Каким образом при литье под давлением извлекают из формы готовую отливку?
9. Приведите примеры решения конструкторских задач применением литья под давлением.
10. Заготовки какой массы целесообразно получать литьем под давлением?
11. За счет чего происходит заполнение жидким сплавом литейной формы при центробежном литье?
12. Как распределяется прочность отливки, полученной центробежным литьем, по направлению от центра заготовки к периферии?
13. В каких местах отливок, полученных центробежным литьем, будет повышенная точность, а в каких - пониженная?
14. Какие заготовки, полученные центробежным литьем, не могут быть получены никаким иным способом литья?
15. Какую толщину имеет оболочка при литье в оболочковые формы?
16. Из какого материала изготавливают модели при литье в оболочковые формы?
17. Какова максимальная масса отливки, получаемой литьем в оболочковые формы?
18. Какие факторы определяют эффективность способа литья в оболочковые формы?
19. При каком типе производства экономически целесообразно применение литья в оболочковые формы?
20. За счет чего отливки при литье по выплавляемым моделям имеют высокую точность?
21. Из каких материалов изготавливают выплавляемые модели?
22. Применяют ли стержни для получения отверстий в отливках, получаемых литьем по выплавляемым моделям?
23. За счет чего обеспечивается прочность оболочки формы для литья по выплавляемым моделям?
24. Для каких изделий экономически целесообразно применять литье по выплавляемым моделям
|
|
Механическое удерживание земляных масс: Механическое удерживание земляных масс на склоне обеспечивают контрфорсными сооружениями различных конструкций...
Адаптации растений и животных к жизни в горах: Большое значение для жизни организмов в горах имеют степень расчленения, крутизна и экспозиционные различия склонов...
История развития хранилищ для нефти: Первые склады нефти появились в XVII веке. Они представляли собой землянные ямы-амбара глубиной 4…5 м...
Семя – орган полового размножения и расселения растений: наружи у семян имеется плотный покров – кожура...
© cyberpedia.su 2017-2024 - Не является автором материалов. Исключительное право сохранено за автором текста.
Если вы не хотите, чтобы данный материал был у нас на сайте, перейдите по ссылке: Нарушение авторских прав. Мы поможем в написании вашей работы!