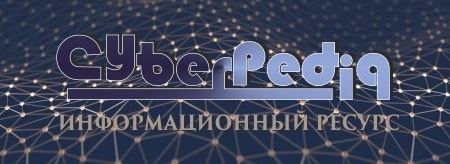
Архитектура электронного правительства: Единая архитектура – это методологический подход при создании системы управления государства, который строится...
Кормораздатчик мобильный электрифицированный: схема и процесс работы устройства...
Топ:
История развития методов оптимизации: теорема Куна-Таккера, метод Лагранжа, роль выпуклости в оптимизации...
Интересное:
Наиболее распространенные виды рака: Раковая опухоль — это самостоятельное новообразование, которое может возникнуть и от повышенного давления...
Отражение на счетах бухгалтерского учета процесса приобретения: Процесс заготовления представляет систему экономических событий, включающих приобретение организацией у поставщиков сырья...
Национальное богатство страны и его составляющие: для оценки элементов национального богатства используются...
Дисциплины:
![]() |
![]() |
5.00
из
|
Заказать работу |
Содержание книги
Поиск на нашем сайте
|
|
Сущность литья по выплавляемым моделям
Литье по выплавляемым моделям известно много столетий. Оно применялось в художественном литье, в котором использовались восковые выплавляемые модели. Современный способ литья по выплавляемым моделям основан на применении моделей, изготовленных из легкоплавких материалов и огнеупорных красок или покрытий, наносимых на поверхности моделей. Литейная форма при этом способе получается без разъема, благодаря чему появляется возможность получения отливок высокой точности. Применение огнеупорных красок при изготовлении форм позволяет получить у литых деталей поверхности с малой шероховатостью.
Этот способ литья можно охарактеризовать как прогрессивный способ получения точных и сложных по форме отливок из любых литейных сплавов, в связи с чем оно получило широкое распространение в машиностроении, приборостроении, в инструментальном производстве, при изготовлении художественного литья, в том числе и ювелирных изделий. Литейная форма для этого способа литья представляет собой неразъемную тонкостенную, прочную, негазотворную, высокоогнеупорную оболочку с очень гладкой внутренней (рабочей) поверхностью. Такую оболочку изготавливают из мелкозернистых формовочных материалов по разовым (выплавляемым, растворимым или выжигаемым) моделям.
Литье по выплавляемым моделям заключается в следующем. Вначале по чертежу отливки (рис. 4.11, а) изготавливают пресс-форму (рис. 4.11, б), которая в дальнейшем служит для получения моделей из легкоплавких материалов.
Пресс-форма может быть изготовлена различными методами и из различных материалов (стали, алюминиевых сплавов, легкоплавких металлов, гипса, цемента, эпоксидной смолы и др.). По своей конструкции пресс-формы могут быть одногнездными и многогнездными. Полость пресс-формы, в которой формируют модель, должна быть выполнена с учетом усадки материала моделей и литейного сплава. Она должна иметь минимальное число разъемов, обеспечивать требуемую точность размеров и чистоту поверхности модели. Для получения моделей в пресс-формах применяют различные легкоплавкие материалы или составы (парафин, стеарин, церезин, канифоль и др.). Наибольшее распространение в отечественной промышленности нашли двухкомпонентные легкоплавкие материалы, состоящие из парафина и стеарина, температура плавления которых 50...60°С.
|
После подготовки пресс-формы (очистки, нанесения смазки и сборки) ее полость заполняют легкоплавким модельным составом, который подают или свободной заливкой (при температуре 70...90°С), или запрессовкой в пастообразном состоянии (при температуре 42...45°С).
Рисунок 4.11 - Последовательность получения заготовки при литье по выплавляемым моделям: а - отливка; б - пресс-форма; в - литейная форма; г - блок литейных форм; 1 - до покрытия оболочкой; 2 - после покрытия оболочкой
В полости модельный состав охлаждается и затвердевает. Полученную модель извлекают из пресс-формы и охлаждают до нормальной температуры. Следует иметь в виду, что с помощью пресс-формы образуют как наружные, так и внутренние поверхности модели. Стержни для получения внутренних полостей или отверстий при литье по выплавляемым моделям, как правило, не применяют. Если получить отливку без стержней невозможно, то последние изготавливают с высокой точностью чаше всего из специальных керамических материалов и вставляют в пресс-форму при сборке, перед подачей в нес модельного состава. Это очень усложняет процесс, что учитывают при проектировании деталей.
Полученные из легкоплавкого материала модели (рис. 4.11, в) позволяют перейти к изготовлению литейных форм. Однако при небольших габаритных размерах и массе отливок, получаемых при литье по выплавляемым моделям, изготовление форм для получения только одной отливки бывает нецелесообразно. Поэтому полученные модели чаще всего предварительно собирают в блок (рис. 4.11, г) с единой литниковой системой. Модель литниковой системы изготавливают отдельно в специальной пресс-форме. Блок объединяет от нескольких единиц до нескольких десятков моделей.
|
Основным материалом для получения формы при литье по выплавляемым моделям служит огнеупорная краска или покрытие. Огнеупорная краска представляет собой жидкую сметанообразную суспензию, состоящую из 55...60% тонкозернистого пылевидного кварца и 40...45 % связующего раствора. В качестве связующего раствора применяют гидролизованный этилсиликат или жидкое стекло. Литейную форму получают нанесением огнеупорной краски на поверхность моделей, собранных в блок. Эту операцию чаще всего осуществляют погружением блока в бак с огнеупорной краской. Тонкую пленку, прилипающую к поверхности моделей и точно воспроизводящую форму, обсыпают мелким кварцевым песком. Песок внедряется в слой краски, задерживает ее на поверхности модели, формирует скелет оболочки-формы и увеличивает ее толщину. Создаваемая песком шероховатая наружная поверхность оболочки способствует хорошему сцеплению последующего слоя краски с предыдущим. Полученная таким образом оболочка из краски практически не обладает прочностью. Оболочка приобретает прочность в процессе сушки (2...4 ч) без повышения температуры. Толщина одного слоя оболочки составляет всего 1,0... 1,5 мм. В результате нанесения нескольких (3 - 5) слоев огнеупорной краски на блоке моделей образуется неразъемная оболочка - форма с достаточной прочностью (рис. 4.11, д). Далее выполняют технологическую операцию освобождения оболочки от моделей. Чаще всего модель в течение 10... 15 мин расплавляют в горячей воде (температура примерно 90 °С). Модельный состав, вытекающий через каналы литниковой системы, собирают и вновь используют для изготовления моделей, а пустую оболочку-форму просушивают.
Оболочку после удаления из нее моделей (рис. 4.12, а) прокаливают, помещая ее в неразъемную опоку (рис. 4.12, б). В зависимости от выбранного варианта технологического процесса пространство между стенками опоки и оболочки-формы заполняют наполнителем (крупнозернистый песок, чугунная дробь или другой материал) до обжига или сразу после него. Температура обжига форм составляет 900... I 000°С.
|
Прокаленную и заформованную оболочку заливают жидким литейным сплавом. При производстве сложных и тонкостенных отливок из стали полученную после обжига форму, не охлаждая, заливают металлом при температуре 900...950 °С, отливок из сплавов на основе меди - при температуре 600... 800 °С, отливок из сплавов на основе алюминия - при температуре 200...300 °С.
Толстостенные отливки из любых сплавов получают в охлажденных формах.
После заливки металла формы охлаждают и разрушают. При этом керамическая оболочка формы отслаивается от внешних поверхностей отливок, однако прочно удерживается во внутренних полостях, углублениях и отверстиях. Поэтому отливки, отделенные от литниковой системы, подвергают механической очистке (дробеструйной и гидроструйной, в галтовочных барабанах) или химико-термической очистке (в растворах или расплавах щелочей). Затем производят зачистку остатков от литников, прибылей и выпоров, термическую обработку (в случае необходимости) и контроль отливок.
Таким образом, но сравнению с другими способами литья процесс получения отливок по выплавляемым моделям имеет характерные особенности.
Первая особенность касается модели: модель отливки не имеет разъема и знаковых частей, ее контуры полностью и точно повторяют форму детали; модель всегда является одноразовой, т.е. служит для изготовления только одной литейной формы и в процессе изготовления формы уничтожается.
Вторая особенность связана с литейной формой: керамическая оболочка толщиной 2...8 мм не имеет поверхности разъема, формирующая отливку поверхность формы обеспечивает получение отливки с малой шероховатостью и требуемой точностью.
Наконец, третья особенность состоит в том, что металл заливают в горячие формы, что создает благоприятные условия для заполнения формы и питания отливки и позволяет получать тонкостенные отливки массой в несколько граммов.
|
|
Индивидуальные очистные сооружения: К классу индивидуальных очистных сооружений относят сооружения, пропускная способность которых...
Типы сооружений для обработки осадков: Септиками называются сооружения, в которых одновременно происходят осветление сточной жидкости...
Автоматическое растормаживание колес: Тормозные устройства колес предназначены для уменьшения длины пробега и улучшения маневрирования ВС при...
Историки об Елизавете Петровне: Елизавета попала между двумя встречными культурными течениями, воспитывалась среди новых европейских веяний и преданий...
© cyberpedia.su 2017-2024 - Не является автором материалов. Исключительное право сохранено за автором текста.
Если вы не хотите, чтобы данный материал был у нас на сайте, перейдите по ссылке: Нарушение авторских прав. Мы поможем в написании вашей работы!