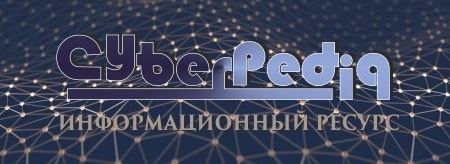
История развития хранилищ для нефти: Первые склады нефти появились в XVII веке. Они представляли собой землянные ямы-амбара глубиной 4…5 м...
Механическое удерживание земляных масс: Механическое удерживание земляных масс на склоне обеспечивают контрфорсными сооружениями различных конструкций...
Топ:
Когда производится ограждение поезда, остановившегося на перегоне: Во всех случаях немедленно должно быть ограждено место препятствия для движения поездов на смежном пути двухпутного...
Генеалогическое древо Султанов Османской империи: Османские правители, вначале, будучи еще бейлербеями Анатолии, женились на дочерях византийских императоров...
Комплексной системы оценки состояния охраны труда на производственном объекте (КСОТ-П): Цели и задачи Комплексной системы оценки состояния охраны труда и определению факторов рисков по охране труда...
Интересное:
Что нужно делать при лейкемии: Прежде всего, необходимо выяснить, не страдаете ли вы каким-либо душевным недугом...
Уполаживание и террасирование склонов: Если глубина оврага более 5 м необходимо устройство берм. Варианты использования оврагов для градостроительных целей...
Распространение рака на другие отдаленные от желудка органы: Характерных симптомов рака желудка не существует. Выраженные симптомы появляются, когда опухоль...
Дисциплины:
![]() |
![]() |
5.00
из
|
Заказать работу |
|
|
Надежная работа турбокомпрессора (ТК) — необходимое усло- вие нормальной эксплуатации дизеля Д49. В процессе работы ди- зеля необходимо постоянно следить за турбокомпрессором, обес- печивая выполнения ряда условий. Следует помнить, что ТК вклю- чает ряд сложных и точно изготовленных деталей, работающих при очень высоких тепловых и механических нагрузках. Поэтому при проверках и регулировках в первую очередь следует обращать вни- мание на исключение перегрузок от центробежных сил (увеличен- ный дисбаланс ротора) и от перегрева из-за превышения темпера- туры газов и ухудшения охлаждения корпусов. Особое и постоян- ное внимание должно уделяться созданию необходимых условий для работы подшипников. Необходимо, чтобы до пуска дизеля мас- ло успевало поступить к подшипникам (для этого в электрической схеме запуска дизеля предусмотрена предварительная прокачкамас- ла в течении 40—60 с маслопрокачивающим насосом). После оста- новки дизеля ротор ТК продолжает вращаться в течение 1—3 мин, поэтому электрическая схема тепловозов Коломенского и Луган- ского заводов и в этом случае включает маслопрокачивающий на- сос в автоматическом режиме. Подача масла на режиме выбега ро- тораисключаетперегревизадирподшипников.
Следует обращать внимание на стабильность параметров ТК в процессе эксплуатации: давления наддува, температуру выхлоп- ных газов в газоприемном корпусе, длительность выбега ротора после остановки дизеля (не менее 1 мин). При значительных от-клонениях этих величин от нормальных необходимо установить причину и устранить ее. Работоспособность ТК чаще всего нару- шается вследствие отложения нагара на поверхностях деталей га- зового тракта: на колесе турбины, сопловом аппарате и его кожу- хе, газоприемном корпусе, а также износа и повреждений лопаток газовой турбины и колесакомпрессора.
|
На интенсивность и скорость отложения нагара очень вли- яет длительность работы дизеля в режиме холостого хода в хо- лодное время года (самопрогрев двигателя) в отстое тепловоза вожидании работы, когда топливо не полностью и некачественно сгорает, оседает в начальной стадии в виде рыхлого нагара и в даль- нейшем твердеет и закоксовывается. Поэтому в обязательном по- рядке необходимо в этом случае через 1—2 ч работы дизеля (дизе- лей) в режиме холостого хода увеличивать обороты КВ вплоть до номинальных на 5—7 мин для удаления рыхлой фракции нагара. В качестве предупредительной меры в отдельных ремонтных депо детали газового тракта турбины очищают от нагара без демонта- жа турбокомпрессора. Для этого используют установки различной конструкции «3, 4», с помощью которых при работающем дизеле прогоняется химический водный раствор между лопатками сопло- вого аппарата и турбинного колеса и через полости лабиринтных уплотнений, но при этом нагар лабиринтных уплотнений со сто-роны газовой турбины все равно не очищается, в большей степе- ни это относится кТК41В.
Снятие (демонтаж)турбокомпрессора
Перед снятием ТК автор советует произвести замер осевого раз- бега ротора. Снятие выполнить в следующей последовательности:
а) открепить и снять воздуховод и газоотвод (выхлоп);
б) слить охлаждающую жидкость из системы охлаждения дизеля; в) открепить и снять трубы, препятствующие снятию ТК;
г) открепить хомуты соединения воздушной улитки турбокомп- рессора с горловиной патрубка охладителя;
д) привести механизм воздушной захлопки в нерабочее поло- жение;
е) открепить ТК от дизеля (от кронштейна ТК), застопорить подъемным устройством за рым и снять ТК.
Разборка
Для производства разборочно-сборочных работ по турбокомп- рессору в арсенале ремонтного подразделения должен быть кан-тователь (кантователи), где турбокомпрессор надежно закреплен иеговозможновращатьвразличныхкомбинациях.
|
Разборку произвести в следующей последовательности:
а) открепить и снять с турбокомпрессора механизм воздушной захлопки;
б) открепить и снять входной патрубок и проставок
в) открепить болты крепления воздушной улитки к среднему корпусу, оставив не отвернутыми три-четыре болта, равномерно расположенных по окружности;
г) отвернуть болты и снять газовыпускной патрубок;
д) отвернуть болты и, используя резьбовые отверстия в корпусе турбины, отжать корпус и, не допуская перекоса, снять его;
е) отвернуть болты и снять газовые улитки и фланец;
ж) окончательно отвернуть оставшиеся болты и снять воздуш- ную улитку;
и) открепить болты, скрепляющие половины среднего корпуса, приспособлением 11Д45.181.24спч рассоединить половины кор- пуса и, не допуская перекоса, снять верхнюю половину корпуса;
к) открепить болты, снять верхние половины подшипников и, не допуская перекосов, вынутьротор;
л) открепить и снять с проставка диффузор компрессора. Разо- брать его, очистить лопатки и поверхности диффузора и простав- ка от нагароотложений, промыть дизельным топливом или керо- сином. После скрепления проставка с диффузором винты крепле- ния попарно застопоритьпроволокой.
Осмотр
После разборки очистить детали ТК от грязи и нагара, затем промыть их дизельным топливом или керосином, продуть сжатым воздухом и осмотреть. Для более производительного процесса ре- монта в этом случае лучше использовать физико-химический спо- соб очистки с помощью моечных машин. Особенно тщательно про-
дуть воздухом воздухоподпорный канал среднего корпуса и втул- ки. Установить деревянные или резиновые заглушки на воздуш- ныемасляныеиводяныеканалывкорпусахТК.
Осмотреть ротор. На шейках ротора и упорных поверхностяхвтулки и вала ротора количество отдельных кольцевых рисок недолжно превышать 3—4 шт. на каждую поверхность при глуби- не выработки до 0,05 мм и ширине до 0,3 мм. Острые края коль-цевых рисок притупить полировкой. При износе шеек вала бо- лее 0,06 мм допускается их перешлифовка в ремонтный размер
Æ54,7 — 0,03 мм. В этом случае при сборке установить ремонт-ные подшипники 6ТК.03.068-01 и 6ТК9.03.005-01. Обмерами оп- ределить зазор на масло в подшипниках. Разность между разме-ром внутреннего отверстия подшипника при сомкнутых половин- ках вкладышей и в перпендикулярном направлении к их стыку и размером соответствующей шейки вала равна зазору на масло. За- зор должен быть в пределах 0,11—0,20 мм, браковочный — более 0,22 мм. Острые края отдельных рисок на рабочих поверхностяхподшипников зачистить шабером. Восстановить скосы на упорных торцах опорно-упорного подшипника. Проверить суммарное про- ходноесечениесопловогоаппарата,котороедолжнобытьвпреде-
|
лах148—150см2.Величинасечениярегулируетсяподгибкойвыход- ных кромок лопаток по шаблону с помощьюклинаД49.181.165-01.Удалить слой старого герметика со стыков половинсреднегокорпуса, удалить резиновые кольца из проточекнижнейполови-ны корпуса и стянуть четырьмя болтами обеполовинысреднего корпуса.Проверитьприлеганиеполовинкорпуса.Щуптолщиной0,03ммнедолженпроходитьвстык.Врайонелабиринтовустано-витьвнихуплотнительныелабиринтныекольцаротора,дляпро-веркизазороввзамкахколец(неболее0,45мм).Незначительные
следы выработки от колец глубиной 0,03—0,04 мм заполировать. Приобнаружениизабоинналопаткахтурбиныиколесакомп-
рессора размером до 2 мм допускается острые края в районе забоин зачистить полировкой и проверить отсутствие трещин в этих местах методом цветной дефектоскопии. Если размеры забоин превыша- ют допустимые или при контроле обнаружены трещины, дефект- ные детали заменить. При этом разновес, сменяемых рабочих ло- паток турбины и устанавливаемых в диаметрально-противополож- ныхместахдопускаетсянеболее1°.СостояниешеекротораТКи
вал вне зависимости от механических повреждений обязательно проверить магнитной дефектоскопией. При замене упорной втулки (износе гребешков) допускается спрессовка колеса и ВНА с пос- ледующей установкой их на ротор, при этом необходимо обеспе- чить натяг по шлицам 0,06—0,109 мм. Проверить боковые зазоры между уплотнительными кольцами и ручьями вала и упорной втул- ки, которые должны быть в пределах 0,35 мм (браковочный более 0,4 мм). При необходимости кольца заменить. После устранения любых дефектов на роторе или замены деталей на нем ротор в обя- зательном порядке подвергнуть динамической балансировке. Ос- таточный дисбаланс с газовой и компрессорной стороны допуска- ется не более 3 град·см.
|
Сборка
ПродутьсжатымвоздухомканалыСиХсреднегокорпуса,про-веряя проход воздуха через них к опорномуиопорно-упорномуподшипникам. Для сборки среднего корпусанеобходимоизгото-вить и использовать специальный кантователь.Установитьниж-нююполовинусреднегокорпусанакантователь,установитьновыерезиновые кольца на водоперепускные отверстиясреднегокорпусаикорпусатурбины,стянутьихболтамииопрессоватьводойдав-лением0,6МПа(6кгс/см2)притемпературе60—80°С.Течьвсо-единенияхнедопускается.Послеопрессовкиоткрепитькорпусга-зовойтурбиныотсреднегокорпуса,разъединитьполовинысред-него корпуса. Поставить нижние половиныкорпусовподшипни-ков с половинами вкладышей в постели нижнегосреднегокорпуса.До установки нижних половин подшипниковпроверитьуто-паниеконцовшпилекотносительноповерхностиосевогоразъема среднегокорпуса.Утопаниедолжнобыть29+0,2ммиобеспечи-ваетсявывертываниемиливвертываниемшпилекврезьбовыеот-верстия.Длянадежнойфиксациишпилекврезьбовыхотверстиях, резьбу шпилек обезжирить и покрытьклеем-герметикомсилико-новым«Полисил».Порядокпримененияклеяизложенвприложе-нииГРуководства1А-9ДГ.62РЭ,2А-9ДГ-02.94РЭ,вприложенииЛРуководства1А-9ДГ-2.99РЭ.Обмерамиопределитьбоковойза-зор на масло в опорно-упорном подшипнике. Зазорравенразно-стимеждуразмером,определяющимрасстояниемеждуупорнымиторцамивтулки,валаиразмероммеждуупорнымиторцамивкла-
дыша подшипника. Зазор должен быть в пределах 0,2—0,4 мм, не более 0,48 мм. В случае превышения зазора заменить опорно- упорный подшипник или еговкладыш.
Смазать моторным маслом шейки ротора и рабочие поверхнос- ти подшипников. Установить в ручьи вала и втулки уплотнитель- ные кольца, замки рядом стоящих колец развернуть относитель- но друг друга на 120°. Осторожно без перекосов установить ротор на нижние половины подшипников. Проверить наличие фикса- торов в обоих подшипниках, предотвращающих проворот вкла- дышей. Поставить верхние половины подшипников и закрепить их болтами. Затяжку болтов произвести моментом 20—25 Н·м (2—2,5 кгс·м) и застопорить их проволокой. После установки но- вых резиновых колец на переливные отверстия нижней половины среднего корпуса покрыть стыки половин среднего корпуса герме- тиком, соединить и скрепить половины корпуса болтами и шпиль- ками, гайки застопорить новыми шплинтами. С помощью индика- тора определить осевое перемещение ротора в упорном подшип- нике. При необходимости еще раз опрессовать водяную полость среднего корпусаводой.
|
Прикрепить к среднему корпусу воздушную улитку, установив на стыке паронитовую прокладку толщиной 0,5 мм. Повернуть кантователь в удобное положение для установки фланца и поло-винок газовой улитки на средний корпус, перед завинчиванием болтов, резьбовую часть болтов покрыть графитной смазкой УСсА для облегчения отвинчивания болтов при последующей разбор- ке. Болты закрепить усилием 100—120 Н·м (10—12 кгс·м) и обвя- зать проволокой. Поставить в кольцевые проточки переливных от- верстий и корпуса турбины новые резиновые прокладки. Смазать стыкуемую торцовую поверхность среднего корпуса герметиком и, не допуская перекосов, опустить корпус турбины на средний кор- пус и закрепить его болтами, предварительно смазав резьбу болтов графитной смазкой УСсА. Болты закрепить усилием 100—120 Н·м (10—12 кгс·м). Повернуть кантователь на 180°, прикрепить шпиль- ками к проставку диффузор компрессора, установив между ними регулировочнуюпрокладку.
На стык проставка в сборе с диффузором и воздушной улиткой установить паронитовую прокладку, скрепить их тремя-четырьмя болтами, равномерно распределенными по окружности. При помо-
щи индикатора проверить правильность установки зазора на сты- ке между торцами лопаток колеса компрессора и проставком диф- фузора. Зазор должен быть в пределах 0,9—1,2 мм (см. приложе- ние А). При необходимости требуемый зазор можно установить за счет изменения толщины регулировочной прокладки. Окончатель- но закрепить всеми болтами проставок с диффузором и воздушной улиткой междусобой.
Установить и закрепить входной патрубок, дренажнуютрубу.В горизонтальном положении турбокомпрессора,закрепленном наглавном кантователе, прикрепить болтами к корпусу турбины газо-выпускной патрубок, установив на стыке асбостальную прокладку. Резьбу болтов смазать графитной смазкой УСсА. Проверить про-ход масла к подшипникам. При подаче моторного масла давлени-ем 0,1—0,15 МПа (1—1,5 кгс/см2) в каналы масло должно стекатьс обоих подшипников в полость среднего корпуса и далее на слив.Проверить вращение ротора. Ротор должен вращаться легко ибеззаеданий. Проверить на плотность охлаждающие полости тур- бокомпрессора и стыки между корпусами охлаждающей жидкос-тью давлением 0,6 ± 0,05 МПа (6 ± 0,5 кгс/см2) при температуре
60—80 °С. Течь воды в соединениях не допускается.
Внимание! После всех технологических операций по осмотру, дефектации деталей, сборке, турбокомпрессор обязательно обка- тать на испытательном стенде в соответствии с технологической картой стенда.
Закрыть все полости и каналы ТК от попадания в них грязи ипосторонних предметов. Установить воздушную захлопку на улит- ку ТК вместе с новыми регулировочными прокладками.
Установка надизель
Установить турбокомпрессор на дизель, закрепить его на крон- штейне. Удалить заглушки из входных и выходных отверстий для газов, воздуха, воды и масла. Проверить плавность вращения ро- тора от руки через выхлопное отверстие. При монтаже ТК необ-ходимо помнить следующее.
Надежная работа турбокомпрессора зависит от правильности его монтажа на дизеле. Монтаж должен быть произведен таким обра- зом, чтобы во время работы ТК не испытывал усилий со стороны трубопроводов, связывающих его с дизелем и другими агрегатами
силовой установки. Обязательно должна быть обеспечена свобода тепловых расширений деталей. Для обеспечения центровки турбо- компрессора с наддувочным коллектором дизеля необходимо ис- пользовать набор прокладок между ТК и кронштейном. Для уплот- нения стыков фланцев выхлопного корпуса и выхлопного трубоп- ровода силовой установки, а также фланцев газоприемного кор- пуса и выхлопных коллекторов дизеля применять уплотнительные прокладки из асбостального полотна. Соединение газоприемно- го корпуса с выхлопными коллекторами дизеля должно произво- диться через компенсаторы в виде сильфонов или телескопичес-ких соединений. Выхлопной трубопровод не должен передавать усилия свыше 50 кг на ТК, он должен быть снабжен компенсато- ром, обеспечивающим свободу тепловых расширений. Соедине- ние корпуса компрессора с воздухоочистителем силовой установки не должно превышать усилия свыше 30 кг, должно производить- ся с помощью эластичного компенсатора (рекомендуется из рези- ны или плотнойткани).
Трубопровод, отводящий масло из турбокомпрессора, должен обеспечивать свободный слив масла, т.е. иметь достаточный внут- ренний диаметр и не иметь горизонтальных участков и подъемов, которые могли бы сыграть роль гидравлического затвора. Поступ- ление масла от масляной системы дизеля к подшипникам ТК долж- но быть бесперебойным, в том числе во время выбега ротора пос- ле остановкидизеля.
Перед окончательным креплением турбокомпрессора подсоеди- нить его к горловине патрубка охладителя наддувочного воздуха. Поставить на места и закрепить трубы подвода и слива охлажда- ющей жидкости и масла, трубопроводы подвода воздуха, газопод- водящие и газоотводящие системы вентиляции картера. Закрепить ТК моментом 180—200 Н·м (18—20 кгс·м). Проверить на плотность турбокомпрессор охлаждающей жидкостью и маслом совместно сдизелем.Течижидкостиимаславсоединенияхнедопускаются.
ТурбокомпрессорТК41В
Турбокомпрессоры 6ТК и ТК41В взаимозаменяемые (отличи- тельные особенности конструкции указаны в п. 2.17) и поэтому снятие (демонтаж) ТК41В выполнить в той же последовательнос- ти,чтоидемонтаж6ТК,изложенныйвп.4.1.26.1.РазборкаТК
должна производиться также на кантователе. Разборку произвести вследующейпоследовательности(см.рис.27,28):
а) повернуть кантователь с турбокомпрессором в положение кор- пусом компрессора вверх;
б) отогнуть замочную пластину из паза гайки ротора;
в) отвернуть гайку ротора с помощью торцового ключа и воротка; г) снять шайбу;
д) отвернуть гайки крепления опорно-упорного подшипника и, пользуясь съемником, вынуть подшипник. Под фланцем подшипни- ка установлен компенсатор в виде кольца определенной толщины. Толщина компенсатора подогнана по месту и обеспечивает осевой зазор между колесом компрессора и вставкой, равный 0,9—1,2 мм;
е) вынуть пяту съемником;
ж) отвернуть гайки крепления корпуса компрессора к газопри- емному корпусу;
и) отсоединить корпус компрессора отжимными болтами, ввер- тывая их в резьбовые отверстия фланца газоприемного корпуса, и, используя подъемный механизм, снять корпус компрессора, пере- мещая его без перекосов;
к) вынуть диффузор, отвернуть гайку колеса компрессора, снять ВНА и колесо компрессора;
л) привернуть приспособление для фиксации ротора к газопри- емному корпусу;
м) перевернуть ТК выхлопным корпусом вверх;
н) отвернуть гайки крепления выхлопного корпуса;
п) отсоединить выхлопной корпус отжимными болтами, ввер- тывая их в резьбовые отверстия фланца газоприемного корпуса и с помощью подъемного механизма снять выхлопной корпус, пере- мещая его безперекосов;
р) ввернуть в торцовую часть вала ротора рым-болт, поднять ро- тор за рым-болт и аккуратно установить его на деревянный стел- лаж или специальную подставку;
с) удалить вязальную проволоку и отвернуть болты крепления кожуха соплового аппарата, пользуясь отжимными болтами, снять кожух;
т) удалить вязальную проволоку и отвернуть болты крепления со-плового венца, с помощью отжимных болтов снять сопловой венец;ф) вынуть втулку из газоприемного корпуса, пользуясь отжим-ными болтами. Если втулка закоксована и не вынимается, залить
под втулку керосин через отверстие в корпусе, заглушив отверс- тие вовтулке;
х) отвернуть гайки крепления втулки опорного подшипника, вынуть втулку и опорный подшипник;
ц) снять упругие уплотнительные кольца с ротора, заметить в каких канавках, какие стояли для того, чтобы при сборке устано- вить их на прежнее место, не перепутав.
Очистку корпусов турбокомпрессора, деталей их дальнейший осмотр, дефектацию произвести по аналогии с турбокомпрессо- ром6ТК,изложеннойвп.4.1.26.3.
Сборку турбокомпрессора произвести в порядке, обратном пос- ледовательности разборки. При установке уплотнительных колец за- мки их расположить диаметрально противоположно, смазать коль- ца консистентной смазкой так, чтобы они прилипли к валу и заня- ли центральное положение. Для уплотнения разъемов на предвари- тельно очищенные привалочные плоскости корпусов нанести пасту
«Герметик» и уложить капроновую нитку. При установке опорно-упорного подшипника не позабыть установить компенсатор, под-шипник установить так, чтобы сливные каналырасположены быливнизу. Не забыть установить и отогнуть новую замочную пластину.
Установку турбокомпрессора произвести в том же порядке и с соблюдением тех же условий, указанных в п. 4.1.26.5.
|
|
Кормораздатчик мобильный электрифицированный: схема и процесс работы устройства...
Типы оградительных сооружений в морском порту: По расположению оградительных сооружений в плане различают волноломы, обе оконечности...
Эмиссия газов от очистных сооружений канализации: В последние годы внимание мирового сообщества сосредоточено на экологических проблемах...
Семя – орган полового размножения и расселения растений: наружи у семян имеется плотный покров – кожура...
© cyberpedia.su 2017-2024 - Не является автором материалов. Исключительное право сохранено за автором текста.
Если вы не хотите, чтобы данный материал был у нас на сайте, перейдите по ссылке: Нарушение авторских прав. Мы поможем в написании вашей работы!