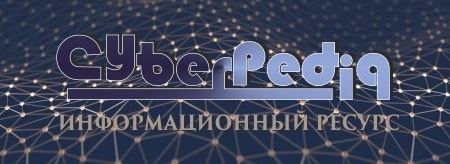
Таксономические единицы (категории) растений: Каждая система классификации состоит из определённых соподчиненных друг другу...
Архитектура электронного правительства: Единая архитектура – это методологический подход при создании системы управления государства, который строится...
Топ:
Оснащения врачебно-сестринской бригады.
Основы обеспечения единства измерений: Обеспечение единства измерений - деятельность метрологических служб, направленная на достижение...
Интересное:
Национальное богатство страны и его составляющие: для оценки элементов национального богатства используются...
Что нужно делать при лейкемии: Прежде всего, необходимо выяснить, не страдаете ли вы каким-либо душевным недугом...
Мероприятия для защиты от морозного пучения грунтов: Инженерная защита от морозного (криогенного) пучения грунтов необходима для легких малоэтажных зданий и других сооружений...
Дисциплины:
![]() |
![]() |
5.00
из
|
Заказать работу |
|
|
При использовании фильтра 6.46 в качестве основного фильтру- ющего элемента в масляной системе тепловозов с дизелями 5Д49 установлено, что фильтр очень устойчиво и надежно работает в ре- жиме самоочистки. Анализ опыта эксплуатации тепловозов с но- вой системой фильтрации дизельного масла, проведенный специ- алистами завода и компании «Болл и Кирх» на разных участках сети РЖД, показывает, что для наиболее полной реализации пре- имуществ новой системы очистки масла, оптимизации процесса обслуживания масляной системы, целесообразно в ремонтных ло- комотивных депо соблюдать следующиерекомендации:
а) производить промывку свечевых фильтрующих элементов и защитногосетчатогофильтрачерезкаждые200—250тыс.кмпробе- га тепловоза (ТР-2) или при достижении перепада давления масла доипослефильтраболее0,15МПа(1,5кгс/см2)приработедизе-
ля на номинальном режиме или появления видимой красной час- ти индикатора на корпусе фильтра (при отсутствии перепада дав- ления более 1,5 кгс/см2 видимая часть индикатора окрашена в зе- леныйцвет);
б) для повышения качества очистки фильтроэлементов рекомен- дуется следующая технологическая последовательность:
– обработка в ультразвуковой ванне (УЗВ) с использованием водныхрастворовтехническихмоющихсредств(ТМС);
– промывка струей горячей воды под давлением (3—4кгс/см2);
– продувка и осушкавоздухом.
в) в связи с использованием самоочищающего фильтра (СОФ) существенно повышается роль центробежных фильтров в систе- ме очистки масла в процессе работы дизеля. Поэтому на каждом ТО-3, а также при замене масла следует обращать внимание на техническое состояние ЦМФ, а также качественно производить очистку фильтров, в соответствии с требованиями Руководства по ТО и ТР тепловозов с дизелем 5Д49. Неудовлетворительная рабо- та ЦМФ приводит к уменьшению срока службы масла и к ускоре- нию загрязнения фильтроэлементовСОФ.
|
4.1.33.8.1. Указание мербезопасности
Не допускается работа дизеля с неисправными или неотрегули- рованными перепускными клапанами, установленными в фильтре.
Не допускается течь масла в местах соединения трубопроводов и в основных узлах фильтра. Устранение неисправностей филь- тра на работающем дизеле не допускается. Изменение направле- ния потока масла через фильтр на обратное не допускается. Фак- тический поток фильтруемого масла через фильтр, который опре- деляется проходными сечениями примененных соединительных трубопроводов, не должен превышать условную пропускную спо- собностьболее,чемна10%.
Недопустимые, резкие изменения нагрузочных режимов дизеля на холодном масле могут привести к деформации защитной сетки СОФ, а при сильном ее загрязнении — к разрушению сетки. Пуск дизеля, прогрев и дальнейший нагрузочный режим должен произ- водиться в строгом соответствии с РЭ дизеля, см. п. 3.2.4—3.2.6.
4.1.33.8.2. Подготовка кработе
Подготовка фильтра к работе заключается в визуальном его осмотре, проверке правильности подключения присоединитель- ных трубопроводов. Герметичность узлов, правильность установ- ки фильтрующих элементов в фильтре, регулировка перепускных клапанов, герметичность соединений основных узлов обеспечива- ются заводом-изготовителем. После монтажа фильтра необходимо проверить герметичность соединенийтрубопроводов.
Перед первым пуском дизеля с установленной системой филь- трации включить маслопрокачивающий насос и проверить рабо-
ту фильтра визуально по индикатору вращения рычага промывки, расположенному в крышке корпуса фильтра. Указательная втулка должна вращаться медленно с частотой вращения около 1 об/мин. При номинальной частоте вращения КВ дизеля частота вращения указательной втулки не менее 5 об/мин, т.е. один оборот за 12 с.Если вращение отсутствует или менее 5 об/мин, то необходимо про- извести проверку в соответствии с указаниями в п. 4.1.33.13. Ес- ли установлен новый фильтр и отсутствует вращение указательной втулки,тонеобходимовызватьпредставителейзавода-изготовителя.
|
4.1.33.8.3. Наблюдение заработой
Сразу после пуска двигателя проверить вращение вала устройства регенерации по индикатору вращения рычага промывки. По при- борам, установленным в дизельном помещении, проверить давле- ние масла до и после СОФ и перед ЦМФ. Давление масла в уста- новившемсярежимеработыдизеля(температурамасланавыходе— 60—80 °С и номинальной частоте вращения коленчатого вала) пос- ле фильтра и перед центробежными фильтрами должно быть не ме- нее 0,2 МПа (2,0 кгс/см2), у ДГУ 1А-9ДГ-3 давление масла перед ЦМФ не менее 0,8 МПа (8,0 кгс/см2). Убедиться в отсутствии те- чи масла по фланцевым соединениям и присоединительным тру- бопроводам. При необходимости после остановки дизеля подтя- нуть крепежсоединений.
При работе дизеля проверить перепад давления по индикато- ру дифференциального давления и зафиксировать эту величину. При нормальных условиях эта величина не должна превышать 0,08—0,1 МПа (0,8—1 кгс/см2), при этом видимая часть индика-тора зеленогоцвета.
Запрещается эксплуатация дизеля при отсутствии прокачки мас- ла через фильтр и давлении масла на входе в дизель менее допус- тимого. Даже кратковременное отсутствие или снижение давления масла приводит к повреждению двигателя. На неработающем ди- зеле выяснить и устранить причину, вызвавшую понижение дав- ления масла.
4.1.33.8.4. Техническоеобслуживание
Целесообразно,чтобысрокиТОсистемыфильтрациибылипри- уроченыксрокамТОиТРдизеляитепловоза,установленнымрас-
поряжением ОАО «РЖД» от 17.01.2005 г. № 3р «О системе техни- ческого обслуживания и ремонта ТПС».
Технические обслуживания фильтра являются периодически- ми и предназначены для контроля технического состояния узлов и систем фильтра с целью предупреждения отказов в эксплуата-ции. При проведении технического обслуживания демонтаж филь- тра непроизводится.
Необходимо помнить, что, несмотря на постоянную обратную промывку с учетом качества используемого масла, рано или позд- но может произойти засорение фильтрующих сеток элементов. За- сорение фильтрующих сеток наступает значительно быстрее при длительном использовании загрязненногомасла.
|
Значительное загрязнение защитного сетчатого фильтра может указывать на длительную работу при открытых перепускных кла- панах (при перепаде давления по индикатору 0,2 МПа (2 кгс/см2)
и более, а также загрязненных фильтрующих элементах, при рез- ких изменениях нагрузки ДГУ, особенно при низкой температуре масла (около 40 °С).
При проведении ТО фильтра необходимо обеспечить герметич- ность фильтра и всех мест соединения.
Рекомендуется при необходимости заменять фильтрующие эле- менты через каждые 400—500 тыс. км пробега тепловоза при бли- жайшем ТО дизеля. После тщательной проверки свечевых филь- троэлементов (проверки состояния фильтрующих сеток на отсут- ствие повреждений) возможно их более продолжительное исполь- зование. При наличии повреждений фильтрующей сетки элемента, его необходимо заменить.
Несоблюдение установленной периодичности и низкое качество технического обслуживания значительно уменьшают ресурс филь- тра, что приводит к увеличению отказов, росту трудовых и мате- риальных затрат на его эксплуатацию.
4.1.33.8.5. Порядок техническогообслуживания
При возникновении сомнений в правильности работы фильтра и для устранения неисправностей при эксплуатации СОФ необхо- димо до снятия и разборки фильтра уточнить характер неисправ- ности, проведя следующиепроверки:
– проверка по индикатору дифференциальногодавления;
– проверкапоиндикаторувращениярычагапромывки;
– проверка трубопровода обратной промывкифильтра.
Если при вращении КВ дизеля на 15 позиции КМ будет уста-новлено, что вращение указательной втулки блока фильтроэлемен- тов менее 5 об/мин, это свидетельствует об загрязнении фильтра (при этом индикатор дифференциального давления сигнализиру- ет красным цветом). Если вращение вала блока отсутствует сов-сем, в этом случае необходимо проверить легкость хода червячно- го редуктора, турбины с зубчатым колесом и рычагом промывки. Для этого необходимо при остановленном дизеле снять крышку, закрепленную четырьмя болтами. После этого проверить легкость хода с помощью торцового ключа (установив его на шестигранник червячногоредуктора).
|
Затрудненный ход вала редуктора может быть связан:
– с попаданием частицы между ведущим зубчатым колесом ва- ларедуктораизубчатымколесомваларычагапромывки;
– заклиниванием колесатурбины;
– рычаг промывки соприкасается с нижней плитой сетчатого фильтра(чащевсегоданныйслучайвстречаетсявпрактике);
– попадание посторонних частиц или загрязнений под рычаг промывки.
Осмотреть трубопровод слива масла обратной промывки из филь- тра на наличие возможной деформации сечения трубы. Дефектную трубу заменить. При замене необходимо обеспечить постоянный ук- лон трубопровода обратной промывки из фильтра в поддизельную раму без застойных зон. Труба должна быть изогнута плавно, без резких переходов, сужающих проходное сечение трубопровода. На- личие таковых приводит к дополнительному сопротивлению в про- цессе обратной промывки и более быстрому загрязнению фильтра.
4.1.33.8.6. Разборкафильтра
Разборку производить после остановки дизеля (при температу- ре масла 60—70 °С) через 20—30 мин. С целью слива максималь- ного количества масла в маслосборник поддизельной рамы из тру- бопроводов и корпусафильтра.
Разборку произвести в последовательности:
а) отвернуть пробку выпуска воздуха, находящуюся в верхней части крышки;
б) отвернуть пробку слива масла в нижней части корпуса фильтра; в) слить масло в специальную емкость;
г) отвернуть восемь гаек крепления крышки к корпусу филь- тра, если крышка не снимается, то отжать ее от корпуса с помо- щью двух отжимных болтовМ12;
д) вынуть блок фильтрации в сборе с рычагом промывки и ведо- мым зубчатым колесом из корпуса с помощью отверстий для про- хода масла в защитнойпластине.
Внимание! Выемка блока фильтрации за конец вала рычага про- мывки или за втулку указательную не допускается;
е) транспортировать блок фильтрации к месту разборки (цех фильтрокомплектации) и после ремонта только в отдельной ем- кости (корзине).
4.1.33.8.7. Разборка блокафильтрации
В цехе фильтрокомплектации установить блок фильтрации ведо- мым зубчатым колесом вниз на чистую ровную поверхность стола со столешницей из дерева или покрытую пластинами из меди или алюминия, чтобы избежать повреждения зубьев и нижней (уплот- нительной) поверхности зубчатого колеса.
При снятии, а также разборке и сборке деталей блока фильтра- ции и при установке блока в сборе в корпус фильтра необходимо соблюдатьследующее:
– не допускается использовать инструменты из твердого мате- риала (металла), например молоток (во избежание механического повреждениядеталей);
– не допускается прилагать усилие при установке блока филь- трациивсборевкорпусфильтра;
|
– ремонт блока фильтрации должен производиться в чистом месте;
– соблюдать особую чистоту при установке блока в корпус фильтра.
Разборку блока фильтрации произвести в следующей последо- вательности:
а) отвернуть винт крепления указательной втулки и снять втул- ку со встроенной пружиной;
б) отвернуть винты крепления пластины защитной и снять плас- тину;
в) установить блок фильтрации зубчатым колесом вниз на крайстола, удерживая его рукой для предотвращения его падения, и припомощи оправки диаметром 8—10 мм (оправка из дерева или ла-туни) вытолкнуть снизу вверх все 78 свечевых фильтроэлементов. Внимание! Для выталкивания фильтроэлементов запрещается ис-пользовать металлический Г-образный ключ с внутренним шести-гранником из комплекта ключей, используемых при ремонте СОФ;г) ключом с внутренним шестигранником отвернуть болты креп-
ления верхней плиты, снять верхнюю плиту;
д) поднять руками вверх и снять защитный сетчатый фильтр. Снятие рычага промывки производить только в следующих слу-
чаях:
– при общем загрязнении фильтра и засорении каналов в ры- чагепромывки;
– при сильном износе нижней плиты (при отсутствии зазора междунижнейплитойирычагомпромывки).
Для снятия рычага промывки необходимо отвернуть два болта крепления зубчатого колеса к фланцу рычага промывки и снять зубчатое колесо.
Затем ключом с внутренним шестигранником отвернуть болт крепления рычага к валу, снять рычаг промывки.
4.1.33.8.8. Очисткафильтра
Очистка фильтра (свечевых фильтрующих элементов и защит- ного сетчатого фильтра) производится в следующих случаях:
– через каждые 200—300 тыс. км пробега тепловоза при бли- жайшем ТО-3 или ТР или при достижении перепада давления до и после СОФ более 0,15 МПа (1,5 кгс/см2) при работе дизеля на номинальном режиме, когда индикатор дифференциального давле- ния показывает постоянный перепад давления более 1,5 кгс/см2) или дифференциальное давление постоянноповышается;
– при вводе в эксплуатацию ДГУ после длительного переры- ва. При слитом масле из масляной системы дизеля загрязнения на фильтрующих сетках элементов под воздействием атмосферных ус- ловий окисляются и уплотняются, что затрудняет обратную про- мывку фильтрующих элементов при последующей работе фильтра даже на прогретоммасле.
После промывки масляной системы дизеля, при замене масла, промывочной жидкостью МПТ-2 ([1] Приложение Э, [2, 3] При-
ложение Н), которая проводится согласно руководству по эксплу- атации ДГУ, убедиться, что перепад давления до и после СОФ не превышает 0,15 МПа (1,5 кгс/см2) при работе дизеля на номиналь- ном режиме, в противном случае произвести промывку фильтру- ющих элементов.
Для сокращения времени технического обслуживания теплово- за на промывку фильтрующих элементов рекомендуется иметь для замены предварительно очищенный и промытый сменный комп- лект фильтрующих элементов или блок фильтрации в сборе и под- готовленный кустановке.
Снятые детали при разборке блока фильтрации: защитную плас- тину, плиту верхнюю, зубчатое колесо, рычаг промывки, соедини- тельную трубу с перепускными клапанами и нижней плитой про- мыть в ванне с чистым дизельным топливом или керосином про- тереть насухо, осмотреть. Каналы рычага промывки продуть сжа- тым воздухом.
Комплект фильтрующих элементов устанавливается в специ- альное приспособление (кассету), входящую в комплект постав- ки ультразвуковой ванны, которое обеспечивает омывание их мо- ющим раствором со всех сторон. Приспособление помещается в ванну, заполненную приготовленным моющим раствором. Раствор нагревается в ванне и поддерживается при определенной темпера- туре (рекомендованной изготовителем ТМС) в течение всего вре- мени, необходимого дляотмывания.
Технология промывки должна включать в себя следующие этапы:
– обработка загрязненных элементов раствором ТМС в уль- тразвуковой ванне (УЗВ). Рабочая температура моющего раствора 30—60 °С. Продолжительность промывки зависит от степени загряз- ненности фильтрующих элементов (для элементов, внешне оцени- ваемых как очень загрязненные, и для элементов, имеющих нара- ботку 360—450 тыс. км пробега тепловоза, продолжительность про- мывкидолжнасоставлять10—15ч).Промывкунадлежитпроводить до полной очистки фильтрующих элементов, когда на фильтрую- щих сетках элементов отсутствуют загрязнения. Контроль качест- ваочисткиосуществлятьвизуально(примерночерезкаждые2ч);
– промывка элементов мелко распыленной веерной струей го- рячей воды (температура 40—70 °С) с использованием моечной ма- шины высокого давления. Фильтроэлементы устанавливаютсявер-
тикально в приспособление, которое представляет собой две плиты, выполненные из дерева или пластика толщиной 20—30 мм, шири- ной 200—250 мм, в которых в шахматном порядке высверлены от- верстия для установки фильтрующих элементов. У нижней плиты отверстия не сквозные. Плиты закреплены по краям на стойках и отставлены одна от другой на высоту фильтроэлементов;
– обязательную продувку сжатым воздухом и сушку фильтро- элементов. Наличие влаги в фильтрующих элементах не допусти- мо, так как это приводит к ускорению засорения фильтра при его работе надизеле.
Технология промывки слабо загрязненных фильтроэлементов — это вариант упрощенного способа вышеописанной технологии:
– замачивание элементов в растворе ТМС в любой стойкой к щелочи емкости в течение 8—10 ч (в зависимости от степени за- грязненности) или обработка в ультразвуковой ванне в течение 4—8чприрабочейтемпературераствора;
– промывка проточной водой или с использованием моечной машины высокогодавления;
– продувка сжатым воздухом исушка.
При незначительной загрязненности фильтрующих элементов до- пускается использовать для промывки дизельное топливо, керосин или уайт-спирит. При этом очистка элемента производится волося- ной щеткой с продувкой сжатым воздухом. Запрещается использо- вание при очистке элементов металлической щетки, а также и дру- гих приспособлений, которые могут повредить фильтроэлемент.
Фирма «Болл и Кирх» и ОАО ХК «Коломенский завод» испы- тали и допускают к применению следующие технические моющие средства (ТМС).
Фирма-производитель | Название ТМС |
Производство Германии | |
Фирма «Болл и Кирх» (поставка че- рез представительство фирмы) | BollClean-2000, щелочное моющее средство (концентрат) |
Производство России | |
ООО «Барс» | ТМС «Барсик» (ТУ 24 5840-001-94686392-2003): концентрат щелочного раствора; концентрат поверхностно-активных веществ (ПАВ) |
ООО «Дексан» | ТМС «Синвал» (ТУ 2499-009-10408765-2003), концентрированное моющее средство |
НПОАО «СИНТЕЗПАН» | ТМС «Лабомид-203» (ТУ 38.307.47001-90), порошкообразное средство |
ОАО «Синтез» | ОП-7 ГОСТ8433-81, пастообразный препарат |
ОАО «Воскресенские минеральные удобрения» | Тринатрийфосфат (ГОСТ 201—76), порошкообразное средство (используется для водоподготовки дизельных двигателей) |
4.1.33.8.9. Очистка защитного сетчатогофильтра
Поместить загрязненный защитный сетчатый фильтр в ультра- звуковую ванну (УЗВ), заполненную раствором ТМС, на 4—8 ч или размягчить отложения в емкости со щелочным раствором в тече- ние 8—10 ч при рабочей температуре раствора.
Вынуть сетчатый фильтр из моечной ванны и смыть отложе- ния с помощью устройства для очистки горячей водой под вы- соким давлением (моечной машиной) без добавления моющего средства. При очистке сетчатого фильтра струей высокого давления струя воды должна быть обязательно направлена изнутри наружу. При этом расстояние от наконечника устройства до сетки должно быть от 100 до 200 мм, а угол подачи воды должен быть около 90° относительно поверхностисетки.
Если при очистке сетки струей высокого давления струя водыбудет направлена снаружи вовнутрь, может произойти разрыв сетки.После очистки сетчатого фильтра высушить его сжатым возду-
хом и считать его готовым для установки в блок фильтрации.
Внимание! При обнаружении разрывов сетки сетчатый фильтр за- менить. Пайка и другие способы скрепления разрывов недопустимы.
4.1.33.8.10. Сборкафильтра
Сборку фильтра произвести в последовательности, обратной последовательности разборки. И при этом обратить внимание на указания, приведенные ниже:
– опорное кольцо, предусмотренное в качестве монтажного средства при установке блока в сборе в корпус фильтра, должнобытьрасположеноврайоненижнейплиты;
– уплотнительное кольцо и защитный сетчатый фильтр долж- ныбытьплотноустановленывканавкенижнейиверхнейплит;
– установить рычаг промывки на вал со стороны нижней плиты, при этом обратить внимание на положение паза в рычаге и штиф- та на валу рычагапромывки;
– для крепления рычага установить (завинтить) болт с шайбой илиболтсбуртикомврезьбовоеотверстиевала;
– проверить наличие зазора между нижней плитой и рычагом промывки, который должен быть в пределах 0,1—0,3 мм. Приотсут- ствии указанного зазора регулировать зазор можно укладкой в паз рычагапромывкилентыпоширинепазаизмаслостойкойрезины;
– установитьнаместоизакрепитьзубчатоеколесо.
4.1.33.8.11. Установка свечевых фильтрующихэлементов
Установить блок фильтрации зубчатым колесом вниз. Свечевые фильтроэлементы вставлять в отверстия верхней плиты, коничес- ким концом элемента в отверстия нижней плиты, при этом необ- ходимо убедиться в том, что они установлены в соответствующие отверстия без перекоса.
Чтобы избежать перекоса свечевых фильтрующих элементов при установке, необходимо сначала вставить свечевые элементы, но не вдавливать их в отверстия. После установки всех элементов, лег- ко нажимая пальцем на каждый из них, зафиксировать элементы в отверстиях верхнейплиты.
Убедиться в том, что установлены все свечевые фильтрующие элементы (78 шт.). Установить на место и закрепить пластину за- щитную и указательную втулку со встроенной пружиной.
4.1.33.8.12. Установкаблокафильтрациивкорпусфильтра
Перед установкой блока необходимо:
а) проверить рукой вращение ведущего зубчатого колеса вала червячного редуктора. Вращение должно быть легким без прихва- тывания;
б) металлическим прутом диаметром 6—7 мм и длиной 700 мм, на конце которого закреплен волосяной ершик, проверить чис- тотусливногодроссельногоотверстия(диаметрдросселя8,5мм);
в) вставить в дроссель металлический конический наконечник воздушного рукава и продуть дроссель и весь сливной трубопровод сжатым воздухом в сторону маслосборника поддизельной рамы;
г) проверить положение втулки распорной, втулки промывоч- ной и наличие между ними пружины нажимной (пружина нажим- ная служит для центрирования зубьев зубчатых колес червячного редуктора и блока фильтрации по контуру зацепления).
Установить блок фильтрации в корпус фильтра и при этом убе- диться в том, что ведущее и ведомое зубчатые колеса находятся в зацеплении. Турбинка должна вращаться легко. Порядок контро- ляуказанвп.4.1.33.5и4.1.33.13.
Устанавливать уплотнительное кольцо верхней плиты толь- ко после установки блока фильтрации в сборе в корпус фильтра. В противном случае можно повредить уплотнительное кольцо. Пе- ред установкой крышки чистой салфеткой протереть смотровое стекло с обеих сторон и при этом убедиться, что вращение указа- тельной втулки будет хорошо просматриваться. Крышку закрепить равномерноперекрестносусилием12кгс·м.
4.1.33.8.13. Проверка работы приводного механизма фильтра иконтрольработыфильтрапривводевэксплуатацию
Приводной механизм фильтра, состоящий из турбинки, редук- тора и вала рычага промывки, должен вращаться легко усилием руки при помощи торцового ключа при снятой технологической крышке. Если это невозможно, то причиной может быть закли- нивание колеса турбины в корпусе или неправильная сборка бло- кафильтрации.
В этом случае произвести проверку указанных узлов.
При вводе в эксплуатацию фильтра после технического обслу- живания проконтролировать, чтобы:
– при прокачке масла маслопрокачивающим насосом происхо- диловращениеуказательнойвтулки(примерно1об/мин);
– при работе ДГУ на номинальном режиме(15-япозицияКМ)вращениеуказательнойвтулкипроисходилосчастотойболее5об/мин(1оборотза12илименеесекунд),атакжеиндикатор-ныйфлажокуказывалнаперепаддавлениядо0,1МПа(1кгс/см2).При текущих ремонтах, соответствующих пробегутепловоза
400—500 тыс. км, рекомендуется при необходимости заменить фильтрующие элементы и уплотнительные кольца фильтра.
Насосводяной
Снятиенасоса
Снятие насоса произвести в следующей последовательности: а)отсоединитьводянойтрубопроводотнасоса;
б) замаркировать положение насоса на приводе, отвернуть гай- ки крепления насоса к приводу и снять его, предварительно зача- лив корпус насоса подъемным механизмом. Далее насос транспор- тироватьвдизель-агрегатныйцехдляегопоследующейразборки.
Разборка
Разборку производят в следующей последовательности:
а) подметить взаимное положение крышки и кронштейна с улиткой;
б) отвернуть гайки и снять крышку, пружины тарельчатые со- хранить для повторной установки;
в) отогнуть замочную пластину. Застопорить приспособлением Д49.181.177спч (стопор вала) вал и отвернуть болт.
Внимание! Резьба на болте левая;
г) снять рабочее колесо, после чего снять пружину;
д) с помощью приспособления Д49.181.164-02 (скоба) снять кольцо;
е) отвернуть болты и отсоединить улитку от кронштейна; ж) отвернуть болты и снять фланец;
и) снять кольцо;
к) снять стопорные кольца и выпрессовать вал вместе с под- шипниками в сторону крепления кронштейна к приводу насосов, одновременно снимая детали.
Ремонт
Ремонт деталей насоса произвести в следующей последователь- ности:
а) промыть и очистить детали от отложений в дизельном топли- ве. Осмотреть резиновые кольца. При деформации колец (потере круглой формы) или появления растрескиваний кольца заменить;
б) замочную пластину заменить;
в) осмотреть уплотнительные кольца. Детали, у которых повер- хности трения со следами непрерывного кольцевого контакта ши-
риной не менее 3 мм, дополнительной проверки или дообработки не требуют. При нарушении следов непрерывного кольцевого кон- такта, кольцо исправить притиркой. Указания по доводке (притир- ке) и контролю за поверхностями трения из силицированного гра- фита помещены приложении П [2, 3] и в приложении Х [1]. Приобнаружении поперечных трещин или сколов, доходящих до поло- вины ширины детали и прерывающих следы непрерывного коль- цевого контакта, детальзаменить;
г) проверить прилегание по краске поверхностей улитки и флан- ца, которое должно быть равномерным на площади не менее 70 % стыкующихся поверхностей. При необходимости указанные требо- вания обеспечиваются шабровкой;
д) проверить свободное перемещение по окружности фланца в улитке. Для обеспечения этого требования допускается опиловка наружного диаметра фланца;
е) осмотреть посадочные поверхности колец подшипников и мест в кронштейне под подшипники. Обнаруженные забоины, за- усенцы, глубокие рискизаполировать;
ж) проверить, нет ли повреждения сепараторов и шелушения рабочих поверхностей шариков в подшипниках. При обнаружении указанных дефектов подшипники (подшипник)заменить;
и) на валу проверить чистоту резьбы под болт и свободное ввертывание болта в отверстие вала. При необходимости резьбу (М18х1,5-6Н, левая) (см. в п. 4.1.2) прокалибровать. Проверить так- же состояние шлицев. Износ более 0,20 мм, сколы, поломка шли- цев не допускаются. Износ шлицев определять с помощью слеп- ковспоследующейпроверкойнамикроскопе;
к) на поверхности кронштейна не должно быть забоин, обмятини острых кромок. При необходимости дефект устранить шабровкой;л) при наличии выработки и острых кромок на поводках коле-
са устранить их опиловкой;
м) допускается односторонняя выработка пазов обойм кольца до2мм.Прибольшейвыработкекольцозаменить;
н) проверить отсутствие проворачивания силицированного коль- ца в обойме, а также отсутствие свободного (от слабого усилия пальцев руки) выпадения этих колец из обоймы. При обнаруже-нии указанных дефектов кольцабракуются.
Сборка
Внимание! При монтаже необходимо предохранять торцевое уп- лотнение (трущуюся пару) от ударов и падения.
Сборку насоса произвести в следующей последовательности: а) продуть сжатым воздухом масляный канал вала насоса;
б) смазать моторным маслом посадочные диаметры подшипни- ков и шарики подшипников. Этим же маслом смазать посадочные поверхности под подшипники вала насоса;
в) установить на вал подшипник. Для этого противоположный торец вала через медную прокладку установить вертикально на пли- ту, на внутреннее кольцо подшипника также установить медную или латунную трубу-выколотку, чтобы предохранить от прямого удара торец подшипника и вал насоса (сторона шлицев). Ударами молоткаподшипникустановитьдоупоравбуртвала;
г) установить на вал стопорное кольцо;
д) установить вал конусным концом вверх. Противоположныйторец установить на медное кольцо на плиту и ударами молотка помедной трубе установить на вал подшипник до упора в бурт вала; е) проверить легкость вращения наружных колец подшипни-ков, подклинивания и значительный шум при вращении не до-
пускаются;
ж) осмотреть места кронштейна под подшипники, смазать эти места моторным маслом;
з) установить отражатель;
и) установить вал с подшипниками в кронштейн. Легкими уда- рами молотка по наружному кольцу подшипника через медную или латунную трубу или кольцо передвинуть вал с подшипника- ми до упора в бурт кронштейна. Проверить легкость вращения ва- ланасоса;
к) установить стопорное кольцо, торцевой зазор между этим кольцом и кольцом подшипника должен быть не менее 0,2 мм;
л) проверить установку стопорных колец. Кольца по всей ок-ружности должны входить в соответствующие канавки вала и крон- штейна;
м) установить кронштейн с валом так, чтобы конусная часть ва- ла была вверху. Проверить, будет ли натяг 0,01—0,03 мм при посад- ке втулки-лабиринта на вал насоса. Нагреть в масле втулку-лаби-
ринт до температуры 90—120 °С и надеть ее на вал до упора в от- ражатель и поставить стопорное кольцо. Проверить легкость вра- щения вала насоса;
н) смазать резиновое кольцо и фланец мыльным раствором. Ус- тановить кольцо и кольцо уплотнительное во фланец. Усилием рук (через мягкую деревянную пластину) плотно прижать уплотнитель- ное кольцо к бурту фланца. Скручивание и выдавливание кольца недопускается;
о) в улитку установить прокладку и фланец. Проверить свобод- ное перемещение прокладки в улитке. Болтами закрепить их к улит- ке, болты обвязать проволокой, проволоку обвязывать так, чтобы она затягивала болты и не ослабляла затяжку. Установить улитку на кронштейн по меткам и соединить их болтами и пружинами та- рельчатыми, при этом проверить, правильно ли установлен нагне- тательныйпатрубокулиткипоотношениюкпазамкронштейна;
п) для обезжиривания мягкой кисточкой, смоченной в раство- рителе или ацетоне, промыть рабочие торцы колец, высушить их на воздухе. Установить подвижное кольцо на вал, используя оп-равкуД49.181.178спч;
р) смазать мыльным раствором резиновое кольцо и сопрягаемые с ним поверхности. Надеть кольцо на вал (одевание должно быть тугим). Усилием рук через оправку Д49.181.178спч плотно прижать кольцо. Скручивание и выдавливание кольца не допускается. Ус- тановить проставочное кольцо. Очистить пружину от отложений. Проверить состояние витков пружины и в случае обнаружения их повреждений или поломок пружину заменить. Пружину устано- вить на вал насоса;
с) осмотреть посадочную (конусную) поверхность колеса. За- чистить острые кромки и риски, промыть поверхность дизельным топливом. Если колесо заменили новым, то необходимо проверить прилегание колеса по конусу вала, которое должно быть равномер- ным, не менее 75 % поверхности. Для удобства выполнения этой работы использовать стопор Д49.181.177спч. Установить колесо на конус вала, обеспечив соединение поводков (выступов) колеса по подметке с пазами кольца. Зазор между торцами колеса и вала до затяжки болтом должен быть не менее 1,0 мм;
т) проверить свободное ввертывание болта в резьбовое отвер- стие вала (резьба левая), вал при этом удерживается стопором
Д49.181.177спч со стороны привода вала. Смазать резьбу болта и резьбовое отверстие вала пастой (смазкой) ВНИИ НП-232 или тех- ническим вазелином. Установить новую замочную пластину и за- стопорить ею болт (после его затяжки) на колесе. Ввернуть болт в резьбовое отверстие вала от руки и затем затянуть его динамомет- рическим ключом Д42.181.128спч с надставком Д42.181.06 усили- ем затяжки 200 ± 10 Н·м (20 ± 1 кгс·м). Проверить легкость вра- щения вала насоса усилием руки;
у) установить прокладку и крышку к улитке (по меткам) и скре-пить. Вновь проверить легкость вращения вала насоса усилием руки (вал вращать шлицевым приводным валиком). Вращение с заедани-ем или подклиниванием не допускается. Завернуть до упора пробки;ф) проверить, правильно ли собраны детали уплотнения, для че-
го вместо фланца установить стальную заглушку и закрепить ее на прокладке к крышке. Установить насос нагнетательным патрубком вверх, залить в насос воду до середины патрубка. Провернуть на не- сколько оборотов вал насоса по часовой стрелке и в обратном на- правлении (вращать вал усилием руки через приводной шлицевой валик). Подтекание охлаждающей жидкости более 5 капель в тече- ние 5 мин не допускается, контролировать через окна кронштейна;
х)установитьгайкуипружинытарельчатые.
Установка надизель
Установку на дизель произвести в следующей последовательности: а) с помощью подъемного устройства установить насос на дизель; б) закрепить его согласно схеме (рис. 40) и табл. 30;
в) подсоединить трубопровод к насосу.
Таблица 30
№ этапа | Момент затяжки,Н·м (кгс·м) | Последовательность затяжки |
1 | 30+10(3+1) | 2, 5, 1, 4, 3, 6 |
2 | 70+10(7+1) | 6, 3, 4, 1, 5, 2 |
3 | 70+10(7+1) | 1, 2, 3, 4, 5, 6 |
6 1
5
2
4 3
Рис. 40. Схема крепления насоса
Маслоотделитель
Осмотр
В случае невозможности создания разрежения в картере дизе- ля шибером и управляемой заслонкой необходимо разобрать мас- лоотделитель, промыть все детали в дизельном топливе и продуть маслоотделительные элементы сжатым воздухом. Убедиться, что управляемая заслонка настроенаправильно.
Снятие
Для снятия с дизеля открепить и снять трубы, снять жидкост-ный манометр, открепить маслоотделитель и снять его.
Разборка
Разборку произвести в следующей последовательности:
а)отвернутьболтыкреплениякорпусаккаркасуиснятькорпус; б) отвернуть гайку, снять шайбу и нажимнойдиск;
в) снять маслоотделительные элементы;
г) снять опорный диск и резиновое кольцо.
Сборка
Сборку произвести в следующей последовательности:
а) промыть все детали в дизельном топливе и продуть сжатым воздухом маслоотделительные элементы;
б) установить уплотнительное резиновое кольцо и опорный диск; в) поставить маслоотделительные элементы;
г) поставить нажимной диск, шайбу и завернуть гайку; д)поставитьпрокладку,корпусизакрепитьихболтами.
Установка надизель
Установку произвести в следующей последовательности: а) поставить маслоотделитель и закрепить его;
б) подсоединить трубы;
в) поставить и закрепить на маслоотделителе жидкостный ма-нометр, подсоединить к нему и датчику разрежения трубопровод.
Примечания. 1. Перед установкой паронитовые прокладки смазать с двух сторон герметиком.
2. Резьбы болтов и гаек перед завертыванием смазать дизельным маслом и затянуть ихмоментами:
– для М10 — 20 + 3 Н·м (2 + 0,3 кгс·м);
– для М12 — 35 + 5 Н·м (3,5 + 0,5 кгс·м);
– для М16 — 85 + 10 Н·м (8,5 + 1,0 кгс·м).
4.1.36. Датчик разрежения (см. рис. 16)
Снятие сдизеля
Снятие с дизеля произвести в следующей последовательности: а)отсоединитьотдатчикатрубыподводаиотводамаслаитру-
бу от штуцера;
б) открепить и снять с прилива на заднем корпусе привода на- сосов датчик разрежения, очистить от остатков прокладки прива- лочный фланец под датчик, а отверстие в приливе закрыть.
Разборка
Разборку произвести в следующей последовательности: а) открепить и снять корпус 1 с прокладками;
б) вывернуть дроссель 2, про
|
|
История создания датчика движения: Первый прибор для обнаружения движения был изобретен немецким физиком Генрихом Герцем...
Индивидуальные очистные сооружения: К классу индивидуальных очистных сооружений относят сооружения, пропускная способность которых...
Археология об основании Рима: Новые раскопки проясняют и такой острый дискуссионный вопрос, как дата самого возникновения Рима...
Состав сооружений: решетки и песколовки: Решетки – это первое устройство в схеме очистных сооружений. Они представляют...
© cyberpedia.su 2017-2024 - Не является автором материалов. Исключительное право сохранено за автором текста.
Если вы не хотите, чтобы данный материал был у нас на сайте, перейдите по ссылке: Нарушение авторских прав. Мы поможем в написании вашей работы!