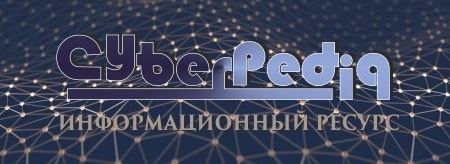
Типы сооружений для обработки осадков: Септиками называются сооружения, в которых одновременно происходят осветление сточной жидкости...
История развития пистолетов-пулеметов: Предпосылкой для возникновения пистолетов-пулеметов послужила давняя тенденция тяготения винтовок...
Топ:
Устройство и оснащение процедурного кабинета: Решающая роль в обеспечении правильного лечения пациентов отводится процедурной медсестре...
Характеристика АТП и сварочно-жестяницкого участка: Транспорт в настоящее время является одной из важнейших отраслей народного хозяйства...
Марксистская теория происхождения государства: По мнению Маркса и Энгельса, в основе развития общества, происходящих в нем изменений лежит...
Интересное:
Наиболее распространенные виды рака: Раковая опухоль — это самостоятельное новообразование, которое может возникнуть и от повышенного давления...
Мероприятия для защиты от морозного пучения грунтов: Инженерная защита от морозного (криогенного) пучения грунтов необходима для легких малоэтажных зданий и других сооружений...
Что нужно делать при лейкемии: Прежде всего, необходимо выяснить, не страдаете ли вы каким-либо душевным недугом...
Дисциплины:
![]() |
![]() |
5.00
из
|
Заказать работу |
Содержание книги
Поиск на нашем сайте
|
|
Под системой контроля качества продукции на АЛ понимается совокупность контрольных операций, измерительных средств и форм их эксплуатации, предназначенных для обеспечения и поддержания заданного и проверки фактического уровня качества продукции на всех этапах ее изготовления.
Система контроля должна решить две основные задачи. Во-первых, необходимо по возможности предупредить появление брака в процессе изготовления продукции; во-вторых, исключить возможность попадания бракованной продукции к потребителю. Для того чтобы решить эти задачи, требуется прежде всего достаточная информация о технологическом процессе, с которым система контроля неразрывно связана. Если технологический процесс не гарантирует получения заданного допуска, применяют сплошной контроль. Вопрос о применении ручного или автоматического контроля определяется экономической целесообразностью. Приемочный контроль может в основном решить лишь вторую задачу — гарантировать потребителя от негодных деталей. В ряде случаев, когда сплошной контроль оказывается экономически малоэффективным, применяют выборочный приемочный контроль, основанный на математико-статистических методах.
Правильно организованный приемочный контроль позволяет также систематически получать надежную информацию для изучения и корректирования рабочих процессов и наряду с выполнением основных функций способствует поддержанию технологической дисциплины и тем самым предупреждению брака.
Для предупреждения появления брака главным образом применяют операционный контроль, который базируется на использовании методов теории управления, математической статистики и теории вероятностей. В практике эксплуатации АЛ нашли применение как приемочный, так и операционный контроль, которые дополняют друг друга и образуют единую систему контроля.
|
По мере совершенствования системы контроля сокращаются потери производства, но при этом, как правило, возрастают затраты на контроль. Таким образом, при разработке системы контроля необходимо сопоставлять затраты на ее реализацию с потерями производства, вызываемыми ее несовершенством. Система контроля будет оптимальной при минимальной сумме затрат на реализацию и убытков от ее несовершенства.
Система контроля характеризуется рядом основных показателей, к которым относятся: а) объем и периодичность контроля; б) контролируемые параметры; в) точность измерения; г) производительность контроля; д) надежность средств измерения.
Для определения количественных значений многих из указанных показателей системы контроля необходимо прежде всего располагать данными о характере технологического процесса. Если систему контроля разрабатывают для вновь проектируемого производства, то характеристики технологического процесса в пределах установленных допусков и с учетом допускаемого брака выбирают априорно на основании общепринятых теоретических положений. При разработке системы контроля для действующего или аналогичного производства характеристики технологического процесса необходимо установить экспериментально.
При автоматической обработке на станках различают управляемые и неуправляемые параметры деталей. К управляемым относятся параметры соблюдение которых обеспечивается настройкой станка, регулируемой без нарушения цикла, обработки, т. е. без остановки станка. К управляемым параметрам в основном относятся размеры обрабатываемых поверхностей.
Управляемые параметры могут контролироваться либо непосредственно в процессе обработки, либо по окончании ее. Результаты измерений используются в первом случае для подачи командных импульсов на изменение режимов и окончание обработки, а во втором — для текущей подналадки уровня настройки станка.
|
К неуправляемым относятся параметры деталей, заданная точность которых обеспечивается настройкой станка, не подвергающейся текущему корректированию; к ним относятся в основном отклонения формы и взаимного расположения поверхностей. При снижении точности станок останавливают для наладки или ремонта. Эта операция нарушает ритм автоматической работы и снижает производительность АЛ. Поэтому одно из главных требований к автоматическим процессам обработки заключается в том, чтобы настройка станка, обеспечивающая заданную точность, особенно неуправляемых параметров, сохранялась на протяжении достаточно длительного времени.
Объем и периодичность контроля. Объем и периодичность выборок, которые определяют возможность применения выборочного контроля, устанавливают на основании анализа технологического процесса. При этом для наладчиков технологического оборудования и контролеров ОТК объем и периодичность выборки устанавливают по-разному, исходя из поставленной цели контроля.
Разработаны стандарты, которые устанавливают порядок ведения выборочного контроля. Для определения объема и периодичности контроля рекомендуется использовать ГОСТ 15893—77 (метод средних значений и размахов) и ГОСТ 16490—70, ГОСТ 16491—80Е, ГОСТ 16492—70, ГОСТ 16493—70 (статистический приемочный контроль по альтернативному признаку).
Контролируемые параметры. Количество измеряемых параметров деталей и узлов зависит прежде всего от значимости контролируемого параметра и надежности его формирования в технологическом процессе. Существенное значение имеет связь различных параметров для данного технологического процесса. Наличие этих связей устанавливают на основании определения коэффициента корреляции.
Наряду с выборочным контролем по параметрам, определяемым техническими требованиями и чертежами, в объеме и с периодичностью, о которых было сказано выше, в некоторых случаях на АЛ создают специальные пункты сплошного приемочного контроля, расположенные по ходу технологического процесса. На этих пунктах контролируемые параметры выбирают с учетом следующих соображений: а) после операций, повторное проведение которых для устранения дефектов обработанных поверхностей становится невозможным в случае обработки детали на последующей операции (в связи с отсутствием имевшихся ранее технологических баз); б) перед операциями, требующими аварийной блокировки от попадания на них изделий, не соответствующих операционному чертежу; в) после операций окончательной обработки некоторых поверхностей детали (это ликвидирует непроизводительные затраты, связанные с дальнейшей обработкой заведомо бракованных деталей, и уменьшает объем приемочного контроля изделий в конце АЛ); г) после окончательной обработки деталей в конце АЛ по параметрам, служебное назначение которых требует высокой гарантии их качества.
|
Целесообразность применения автоматических средств приемочного контроля обусловливается трудоемкостью контроля изделия, ритмом работы АЛ, легкостью автоматизации и другими условиями, определяющими в целом технико-экономическую эффективность системы контроля.
Точность измерения. Регламентированный СТ СЭВ 303—76 предел допускаемой погрешности измерения является наибольшей допускаемой погрешностью измерения, включающей влияние погрешности средств измерения, установочных мер, температурных деформаций, базирования и т. д. Значения размеров, полученные при измерении с погрешностью, не превышающей пределы допускаемой погрешности измерения, принимают за действительные. Допускаемые погрешности устанавливают в зависимости от допуска на изготовление и номинальных измеряемых размеров.
Допускаемая погрешность измерения состоит из случайных и неучтенных систематических погрешностей измерения; при этом случайная погрешность не должна превышать 0,6 допускаемой погрешности измерения и принимается равной 2а, где а — среднее квадратическое отклонение погрешности.
Поскольку стандарт регламентирует погрешность измерения, которая включает суммарное влияние многих составляющих, то при назначении средств измерения необходимо выполнить расчет составляющих погрешности измерения и установить долю каждой из них. Установленное значение каждой составляющей погрешности измерения в значительной степени определит выбор необходимых средств измерения и условия их эксплуатации.
|
Для автоматических средств контроля важно, чтобы точность их работы (при использовании для этих целей ручных измерительных средств) оценивалась с применением тех же принципов. Во избежание различной оценки контролируемых величин схемы измерения размерных параметров для соответствующих деталей должны быть специально оговорены при разработке средств измерения.
Производительность контроля. Производительность контроля определяют исходя из такта работы АЛ, обусловленного производственной программой, с учетом выбранного объема контроля. При определении производительности контроля приходится также учитывать необходимость повторной проверки деталей, забракованных контрольными автоматами.
Расчет производительности автоматических контрольно-измерительных средств следует вести с учетом их технического обслуживания. Производительность контроля лимитируется точностью измерения, которая в значительной степени зависит от скорости вращения измеряемой детали. Для нахождения оптимальной производительности контроля необходимо также располагать данными о связи точности и производительности различных методов измерения.
Надежность средств измерения. Надежность АЛ является важнейшей характеристикой, определяющей эффективность автоматизации производственных процессов. Существенное значение при этом имеет надежность средств измерения.
При работе АЛ возникают как функциональные, так и параметрические (точностные) отказы. Следствием функциональных отказов являются остановки АЛ, вызванные поломками ее отдельных узлов и механизмов и другими причинами, а точностных отказов — выход значений размерных параметров обрабатываемых деталей за допустимую границу.
Основными средствами контроля размеров изделий для использования в АЛ являются: приборы ручного контроля, устройства операционного контроля и контрольно-измерительные автоматы.
Приборы ручного контроля применяют для выборочного и сплошного контроля различных размерных параметров изделия. При правильно организованной эксплуатации они обеспечивают высокое качество контроля и практически не влияют на надежность АЛ.
Устройства операционного контроля влияют на функциональную и технологическую надежности АЛ. Поломки устройств операционного контроля вызывают остановку АЛ. Различные неисправности устройств операционного контроля и системы станок—прибор могут вызвать точностные отказы, при которых размеры х обрабатываемых деталей выходят за границу поля допуска на величину Условие точностного отказа выражается неравенством
где
— предел допустимой погрешности средства измерения;
— допуск.
|
К числу таких неисправностей относятся поломки отдельных элементов измерительного тракта и сбои настройки устройств управляющего контроля. Последние могут иметь устойчивый или самоустраняющийся характер. Поломки и устойчивые сбои должны своевременно обнаруживать и устранять наладчики АЛ. Самоустраняющиеся отказы (к их числу следует отнести и сбои релейных элементов устройств управляющего контроля) имеют неявный характер и создают в основном технологические отказы АЛ по данному параметру.
Различают следующие количественные показатели надежности устройств операционного контроля: 1) наработка на функциональный отказ (среднее время между отказами); 2) интенсивность самоустраняющихся точностных отказов (доля или процент отказов); 3) у %-ный ресурс до ремонта или замены устройства (время, в течение которого 7 % устройств работает до ремонта или замены).
Контрольные автоматы влияют на функциональную и точностную надежность АЛ. Поломки (функциональные отказы контрольных автоматов) приводят к потерям времени на ремонт и снижают коэффициент технического использования АЛ и ее производительность.
При точностных отказах контрольных автоматов (контроль деталей с недопустимыми погрешностями) ухудшается качество разбраковки или сортировки изделий. Основной характер точностных отказов контрольных автоматов — грубые самоустраняющиеся погрешности контроля. При этом под погрешностью контроля ΔК понимается находимая экспериментально (при повторной проверке проконтролированных деталей на ручных приборах или другими способами) разность между действительным размером х детали и размером х0 ближайшей сортировочной группы, к которой она была отнесена в результате неправильного контроля:
В качестве количественных показателей надежности контрольных автоматов рекомендуются:
1) наработка на функциональный отказ;
2) интенсивность сбоев или процент неправильно проконтролированных деталей (с погрешностью контроля ΔК )
По интенсивности сбоев (надежности) автоматы делят на пять классов:
Табл. 1
|
|
Архитектура электронного правительства: Единая архитектура – это методологический подход при создании системы управления государства, который строится...
Папиллярные узоры пальцев рук - маркер спортивных способностей: дерматоглифические признаки формируются на 3-5 месяце беременности, не изменяются в течение жизни...
Кормораздатчик мобильный электрифицированный: схема и процесс работы устройства...
Поперечные профили набережных и береговой полосы: На городских территориях берегоукрепление проектируют с учетом технических и экономических требований, но особое значение придают эстетическим...
© cyberpedia.su 2017-2024 - Не является автором материалов. Исключительное право сохранено за автором текста.
Если вы не хотите, чтобы данный материал был у нас на сайте, перейдите по ссылке: Нарушение авторских прав. Мы поможем в написании вашей работы!