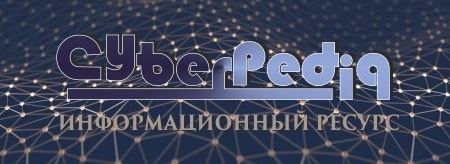
Археология об основании Рима: Новые раскопки проясняют и такой острый дискуссионный вопрос, как дата самого возникновения Рима...
История развития пистолетов-пулеметов: Предпосылкой для возникновения пистолетов-пулеметов послужила давняя тенденция тяготения винтовок...
Топ:
Установка замедленного коксования: Чем выше температура и ниже давление, тем место разрыва углеродной цепи всё больше смещается к её концу и значительно возрастает...
Организация стока поверхностных вод: Наибольшее количество влаги на земном шаре испаряется с поверхности морей и океанов...
История развития методов оптимизации: теорема Куна-Таккера, метод Лагранжа, роль выпуклости в оптимизации...
Интересное:
Лечение прогрессирующих форм рака: Одним из наиболее важных достижений экспериментальной химиотерапии опухолей, начатой в 60-х и реализованной в 70-х годах, является...
Инженерная защита территорий, зданий и сооружений от опасных геологических процессов: Изучение оползневых явлений, оценка устойчивости склонов и проектирование противооползневых сооружений — актуальнейшие задачи, стоящие перед отечественными...
Наиболее распространенные виды рака: Раковая опухоль — это самостоятельное новообразование, которое может возникнуть и от повышенного давления...
Дисциплины:
![]() |
![]() |
5.00
из
|
Заказать работу |
Содержание книги
Поиск на нашем сайте
|
|
Обработка металлов давлением – это такой процесс, при котором металлу придается нужная форма и размер под силовым воздействием. Пластические свойства металлов позволяют сохранить полученные форму и размер, даже после того, как воздействие давления прекращается.
При помощи методов обработки металлов давлением получают как заготовки, так и уже готовые изделия. При этом существует целый ряд различных методов, каждый из которых позволяет воздействовать на металл уникальным образом.
Прокатка — процесс, при котором заготовка под действием сил трения втягивается в зазор между вращающимися валками и пластически деформируется ими. Основными видами прокатки являются продольная, поперечная и поперечно-винтовая.
При продольной прокатке (рис. 1.1, а) валки 1 вращаются в разные стороны; заготовка 2, получая поступательное движение, обжимается ими с уменьшением площади поперечного сечения и увеличением длины. Этим способом изготовляют около 90% всей катаной продукции — заготовки, сортовой прокат, листы, полосы и ленты.
При поперечной прокатке (рис. 1.1, б) валки 1 вращаются в одну сторону. Прокатываемая между ними заготовка 2, получая вращательное движение, деформируется в поперечном направлении. Этим способом получают, например, цилиндрические шестерни с накатанными зубьями, фасонные профили и другие изделия.
При поперечно-винтовой прокатке (рис. 1.1, в) валки 1 расположены под углом друг к другу и вращаются в одну сторону. Прокатываемая между ними заготовка 2, получая одновременно вращательное и поступательное движения, втягивается в зазор между валками и деформируется ими. Этот способ применяют в производстве бесшовных труб, когда заготовка прошивается прошивнем 3 на неподвижной оправке, и периодических профилей, т. е. профилей с меняющимся по длине сечением.
|
Волочение (рис. 1.2, а-в) — процесс протягивания катаного или прессованного прутка (или трубы) через постепенно сужающееся отверстие в инструменте, называемом волочильной матрицей. Волочение обеспечивает точные размеры по сечению, высокую чистоту поверхности, увеличивает прочность материала. Этим способом получают проволоку, тонкостенные трубы, фасонные профили и т. п.
Схемы волочения прутка: (а), трубы на короткой неподвижной оправке (б) и трубы без оправки (в): 1 - волочильная матрица, 2 - оправка, 3 – изделие
Прессование — процесс выдавливания металла заготовки из замкнутой полости контейнера через матрицу, площадь отверстия которой меньше площади поперечного сечения исходной заготовки. Прессованием получают изделия с разнообразными формами поперечного сечения.
Рис. 1.3. Схемы прессования
При прессовании прутка (рис. 1.3, а) заготовку 3 укладывают в полость, контейнера 4. Давление пресса передается на заготовку пуансоном 5 через пресс-шайбу 6. При этом металл заготовки выдавливается в отверстие матрицы 1, укрепленной в матрицедержателе 2.
При прессовании трубы (рис. 1.3, б) пуансон 5 с пресс-шайбой 6 выдавливает металл заготовки 3 из контейнера 4 в зазор, образованный матрицей 1, укрепленной в матрицедержателе 2, и иглой 7, т. е. толщина стенки трубы соответствует величине зазора.
При прессовании металл подвергается всестороннему сжатию и поэтому имеет весьма высокую пластичность, что позволяет обрабатывать низко-пластичные металлы и сплавы.
Ковка - процесс горячей обработки металлов давлением с помощью бойков или универсального подкладного инструмента. При ковке заготовка постепенно меняет форму за счет неоднократных ударов молота (ходов пресса) при кантовке, подаче, повороте заготовки.
При деформировании между бойками молота или пресса металл заготовки течет свободно в направлениях, не ограниченных рабочими плоскостями инструмента. Пластическое формоизменение (течение металла) определяется главным образом силами контактного трения, возникающими в месте контакта поковки с инструментом, и в редких случаях — формой инструмента.
|
Рис. 1.4. Операции ковки: а - протяжка, б - осадка; 1, 2 - нижний и верхний бойки молота или пресса, 3, 4- заготовка до и после осадки; Н и h - высота заготовки до и после деформации, τ тр - силы контактного трения
Основными операциями ковки являются протяжка (рис. 1.4, a) -удлинение заготовки или ее части за счет уменьшения плошади поперечного сечения — и осадка (рис. 1.4, б) — уменьшение высоты заготовки при увеличении площади её поперечного сечения.
Наличие на контактных поверхностях сил трения τ тр приводит при осадке цилиндрической заготовки к бочкообразности поковки, т.е. появлению максимального D max и минимального D min диаметров. Ковка является рациональной и экономически выгодной в условиях единичного и мелкосерийного производства. Поковки небольшой массы получают на ковочных молотах, крупные — на гидравлических ковочных прессах. В отличие от крупных заготовок, полученных литьем и сваркой, кованые заготовки обладают более высокими механическими свойствами и предназначаются поэтому для изготовления деталей ответственного назначения.
Объемная штамповка — придание заготовке заданной формы и размеров путем принудительного заполнения материалом рабочей полости штампа, называемой ручьем. Различают горячую и холодную объемную штамповку.
Горячая объемная штамповка, применяющаяся в машиностроении шире, чем холодная, по сравнению с ковкой обладает рядом преимуществ: позволяет получать более сложные по форме и более точные, с меньшими припусками и допусками поковки с лучшим качеством поверхности; ее производительность значительно превышает производительность ковки; уменьшаются объем последующей обработки резанием и соответственно расход металла
Рис. 1.5. Схемы горячей объемной штамповки
Различают горячую объемную штамповку с облоем в открытых (рис. 1.5, а) и безоблойную штамповку — в закрытых (рис. 1.5, б) штампах. Открытым называют состоящий из половин 1 и 5 штамп, у которого вдоль внешнего контура штамповочного ручья имеется облойная канавка 4, выполненная в виде углубления небольшой высоты. При штамповке в магазин облойной канавки 4 вытекает избыточный металл заготовки, который образует на поковке облой, компенсирующий неточность объема исходной заготовки.
|
Большое сопротивление течению металла, создающегося в конце штамповки мостиком 2 облойной канавки, имеющим вид узкой шели, и быстрое охлаждение относительно тонкого облоя способствуют лучшему заполнению ручья 3 штампа. Облой после штамповки удаляют на кривошипных, а с крупных поковок — на гидравлических прессах в обрезных штампах.
Закрытым называют состояший из двух половин 1 и 5 штамп, в котором металл деформируется в замкнутом пространстве ручья 3 без образования облоя (следовательно, затраты, связанные с его обрезкой, отcутствуют, а расход металла меньше). При безоблойной штамповке поковки получаются с более благоприятной структурой, так как в процессе образования поковки в полости штампа волокна заготовки "обтекают" ее контур. Однако для такой штамповки требуются точные по массе заготовки.
При холодной объемной штамповке (ХОШ) металл пластически деформируется в штампе в холодном состоянии. В качестве заготовок для ХОШ обычно применяют прутковый материал из углеродистых и легированных сталей с низким, средним и высоким сопротивлением деформированию, а также из цветных металлов и их сплавов.
В связи с тем что при холодной объемной штамповке металл не нагревается, она имеет перед горячей ряд преимуществ: из-за отсутствия на поверхности деталей окалины и обезуглероженного слоя повышается точность их размеров и снижается шероховатость поверхности. Это позволяет свести к минимуму последующую обработку деталей резанием и соответственно расход металла. ХОШ в зависимости формы деталей может осуществляться осадкой, высадкой, выдавливанием, калибровкой, чеканкой и применяется для изготовления болтов, винтов, заклепок, гаек, шариков, роликов, поршневых пальцев, мелких цилиндрических и конических зубчатых колес и т. д.
Рабочие части инструмента-штампа для ХОШ работают в тяжелых условиях повышенного трения, высоких удельных давлений, достигающих 2000—2500 МПа, и высоких температур, развиваемых в процессе деформирования. В связи с этим для изготовления штампов применяют стали повышенной и высокой износостойкости
|
|
Историки об Елизавете Петровне: Елизавета попала между двумя встречными культурными течениями, воспитывалась среди новых европейских веяний и преданий...
Типы сооружений для обработки осадков: Септиками называются сооружения, в которых одновременно происходят осветление сточной жидкости...
Папиллярные узоры пальцев рук - маркер спортивных способностей: дерматоглифические признаки формируются на 3-5 месяце беременности, не изменяются в течение жизни...
Биохимия спиртового брожения: Основу технологии получения пива составляет спиртовое брожение, - при котором сахар превращается...
© cyberpedia.su 2017-2024 - Не является автором материалов. Исключительное право сохранено за автором текста.
Если вы не хотите, чтобы данный материал был у нас на сайте, перейдите по ссылке: Нарушение авторских прав. Мы поможем в написании вашей работы!