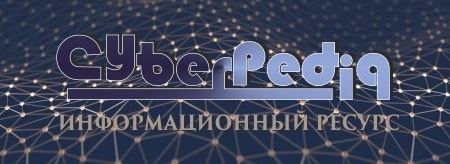
История развития хранилищ для нефти: Первые склады нефти появились в XVII веке. Они представляли собой землянные ямы-амбара глубиной 4…5 м...
Папиллярные узоры пальцев рук - маркер спортивных способностей: дерматоглифические признаки формируются на 3-5 месяце беременности, не изменяются в течение жизни...
Топ:
История развития методов оптимизации: теорема Куна-Таккера, метод Лагранжа, роль выпуклости в оптимизации...
Комплексной системы оценки состояния охраны труда на производственном объекте (КСОТ-П): Цели и задачи Комплексной системы оценки состояния охраны труда и определению факторов рисков по охране труда...
Проблема типологии научных революций: Глобальные научные революции и типы научной рациональности...
Интересное:
Распространение рака на другие отдаленные от желудка органы: Характерных симптомов рака желудка не существует. Выраженные симптомы появляются, когда опухоль...
Что нужно делать при лейкемии: Прежде всего, необходимо выяснить, не страдаете ли вы каким-либо душевным недугом...
Финансовый рынок и его значение в управлении денежными потоками на современном этапе: любому предприятию для расширения производства и увеличения прибыли нужны...
Дисциплины:
![]() |
![]() |
5.00
из
|
Заказать работу |
|
|
При высокой температуре (1500-1700ºС) в печи в результате интенсивного разложения горючих составляющих образуется коксовый остаток и газ, содержащий в основном водород и СО. Минеральная часть, состоящая, в основном, из силикатов и металлов, плавится и разделяется на металл и шлак. Оксид железа, содержащийся в шлаке, вступает в реакцию с коксовым остатком, восстанавливается до металла и образует оксид углерода. Восстановившийся металл непрерывно отделяется от шлака. Полученный расплав состоит в основном из железа, других металлов и кремния. Состав этой массы и количество электроэнергии, необходимое для ее получения, зависят от количества и состава исходных материалов [1].
Способ разложения отходов в электродуговой печи имеет ряд преимуществ по сравнению с распространенными способами обезвреживания: цикл процесса замкнут; процесс является безотходным; при переплавке отходов полностью разрушаются все органические соединения, уничтожается болезнетворная микрофлора; продукты, полученные после сжигания газа, содержат меньше вредных примесей, чем газы мусоросжигательных установок [1]. Стоимость данного метода довольно высока, но она частично компенсируется доходом от реализации полученных продуктов [41,46].
3.1.13. Достоинства и недостатки термических методов обезвреживания отходов.
Дан краткий обзор основных термических методов уничтожения отходов: сжигание, пиролиз, жидкофазное окисление, окисление в сверхкритическом водном флюиде, термоселект, высокотемпературное окисление на базе ракетного двигателя, плазменнохимический метод, паровой крекинг, термическое разложение в электродуговой печи, гидрирование, газификация, технология плавления. Достоинства и недостатки рассмотренных термических методов переработки твердых отходов и шламов представлены в Таблице 3.6.
|
Таблица 3.6.
Метод | Достоинства метода | Недостатки метода |
Инсинерация | -снижение количества отходов, направляемых на свалку; -почти полное удаление органических веществ; -возможность использование золы; | -процесс может быть энергетически невыгодным; -проблемы с загрязнениями (NOx, SOx); -остатки токсичных металлов в золе; -высокая стоимость из-за возрастающих расходов на очистку газов. |
Пиролиз | - неогневой термический процесс; - образование смеси газообразного и жидкого топлива; -возможность размещения на большинстве предприятий; -минимизация загрязнений воздуха, воды и земли; -превращение всех фракций биомассы в полезную энергию; -снижение объёма газов на 90% и образование стерильного горючего материла; | -необходимость использовать плотный поток перерабаты-ваемого шлама для получения требуемого продукта; -технология требует снижения содержания воды до <20%; -низкая технологическая надежность при утилизации шламов ЦБП; |
Паровой крекинг | -высокая скорость переноса энергии; -низкие выходы NOx; -низкие капитальные и эксплуатационные расходы; -ингибирование образования диоксинов и фуранов; -снижение содержания токсичных металлов в летучих отходах; | - применим к отдельным видам отходов; |
Окисление в жидкой фазе | -отсутствие выбросов в атмосферу; -образование потока водяных паров под высоким давлением; -отсутствие необходимости проводить осушение шлама; - пригодность для различных шламов; -экзотермичность процесса поддерживает его энергетически; | -высокая стоимость; |
Окисление в сверхкритическом водном флюиде | - полная деструкция органических соединений; -отсутствие NOx и диоксинов из-за низких температур; - удаление и повторное использование солей и осадков, образующихся вне зоны сверхкритической воды; - использование теплового эффекта реакции в качестве водяного пара или горячей воды; | - ограничения по составу шлама: -высокое содержание сухого вещества и малые размеры частиц; - образование следов уксусной кислоты и окислов азота; |
Газификация | - более высокая эффективность регенерации энергии; - снижение выбросов в окружающую среду; - способность переработать большее количество неорганических веществ, присутствующих в шламе; - образование золы не оказывает влияния на надежность процесса; - образование инертных твердых отходов; | - обезвоживание и осушка шлама; -сложность технологии; - характеристики шлама, лимитирующие эффективность газификации, неизвестны. |
Плазмо-химический метод | -деструкция жидких и пылевидных твердых отходов, содержащих стойкие органические загрязнители -ингибирование образования диоксинов и фуранов; -возможность использования для уничтожения диоксинов; | - высокая стоимость, связанная с капиталовложениями на начальной стадии; |
Гидрирование | - не требует рассортировки мусора - использует материальный потенциал отходов. - гидрирующее ожижение - позволяет получать высококачественный бензин и дизельное топливо; -безвреден для окружающей среды; | высокая стоимость; |
Термоселект | - не требует предварительной сортировки отходов; -получение синтез-газа; -предусмотрена очистка от диоксинов, -позволяет устранять многие виды особых отходов, -довольно доступная цена; -получение строительных материалов; | -не предусматривает очистку водной фракции |
Высоко-температурное окисление на базе ракетного двигателя | - обезвреживание токсичных (фтор-, хлор-, серо-, фосфорсодержащих) соединений, пестициды, дихлофос, карбофос; - концентрация диоксинов укладывается в допустимые нормативы | -отсутствие промышленных образцов; - высокая стоимость, связанная с капиталовложениями на начальной стадии; |
Метод термичес-кого разложе-ния в электроду-говой печи | - процесс является безотходным; - полностью разрушаются все органические соединения, - уничтожается болезнетворная микрофлора; -газовые выбросы содержат меньше вредных примесей, чем газы мусоросжигательных установок | -высокая стоимость; |
Технология плавления | - невысокая стоимость. - возможность получения из ТБО ценных компонентов, которые в нем содержатся, включая, драгоценные металлы. | -не предусматривает очистку водной фракции |
|
|
Из приведенного материала видно, что в настоящее время основным методом переработки отходов является сжигание. Другие термические методы столь широко не используются.
Наиболее экологически - чистыми методами обезвреживания твердых отходов являются следующие: окисление в сверхкритическом водном флюиде, а также плазменнохимический метод, пиролиз и окисление в жидкой фазе, так как эти современные высокотехнологичные методы позволяют провести наиболее глубокую очистку от хлорсодержащих органических соединений.
Среди достоинств некоторых методов отмечается их высокая экологическая чистота, возможность совместить процесс с другими технологиями – например, получения строительных материалов, использование энергии процесса для бытовых и технологических нужд; не последнюю роль играет и финансовая составляющая. Среди недостатков отмечены высокие капитальные затраты, ограничения по составу отходов и другие технологические сложности.
ЗАХОРОНЕНИЕ ОТХОДОВ
Захоронение – окончательный последний этап на пути переработки и утилизации отходов. Захоронению подлежат отходы 1 – 4 класса опасности, которые нельзя сжечь, невозможно переработать и использовать в дальнейшем. По примерным подсчётам называемый мировой запас утилизированного материала, достигает отметки в 1200 млрд. тонн, при этом больше трети от всего объёма, это твёрдые отходы.
Такая отрасль, как добывание горных пород, даёт огромные пространства, в которых можно осуществлять захоронение отходов. Горнодобывающие компании, ежегодно обрабатывают более 30 млрд. тонн твёрдых пород, из которых лишь 60%, после первичной переработки руды уходит в хвостохранилище. На заполнение пустот, в разработанных карьерах, провалах или образовавшихся трещинах, идёт около 45-65% ТБО. 1% уходит на закладку вырытого пространства. И более 5% ежегодного утиля, хоронят в морской бездне.
Площадь земель, отведённых под захоронение отходов, давно уже приблизилась к 1 млн. га. Поэтому применение для таких целей, выработанного горного пространства, представляется перспективным способом захоронения.
|
При создании могильников используются резервуары геологических формаций – гранит, базальт, гипс, но в таком случае учитывать, что пласты должны быть водонепроницаемыми, а под ними должна располагаться водоносная толща. Обязательным является отсутствие деформации, которая может быть вызвана сдвигом под воздействием различных факторов. Если используется подземное захоронение отходов, то делается это с применением специальных емкостей. Отходы размещаются в тарах, которые смогут выдержать разные нагрузки – механические удары, токи. Размещение веществ целесообразно вдали от ЛЭП. Обязательным является соблюдение низкой температуры хранения и флегматизации (флегматизация - насыщение атмосферы резервуара инертными газами, аэрозолями, подавляющими процесс горения, чтобы защитить отходы от химических взаимосвязей с остальными компонентами) [48].
В Российской Федерации, действуют определённые нормативы [49], согласно которым, захоронение отходов, должно проводиться на полигонах, которые располагают на своей территории следующими объектами:
Полигон з ахоронения ТБО - это комплекс природоохранных сооружений, предназначенных для складирования, изоляции и обезвреживания твердых бытовых отходов, обеспечивающий защиту от загрязнения атмосферы, почвы, поверхностных и грунтовых вод, препятствующий распространению грызунов, насекомых и болезнетворных микроорганизмов. Полигон для захоронения ТБО – по существу это «ванна» с дном и бортами из глины и полиэтиленовой пленки, в которой уплотнены слои ТБО, пересыпанные слоями почвы. Принципиальная схема полигона приведена ни рисунке 3.8.
Конструкция предусматривает сток вод, образовавшихся вследствие попадания в слои с отходами осадков, сбора фильтрата и его последующую очистку. Образующиеся газы (метан, СО и др.) частично собираются и подвергаются очистке и утилизации.
Строительство полигона предполагает использование геосинтетической прокладки (геомембраны), которая надежно защищает почву от попадания в неё вредных веществ, невосприимчива к влиянию большинства активных химических элементов и нечувствительна к процессу гниения.
|
Рис.3.8. Схема полигона.
Используют геомембраны из полиэтилена высокого давления (ПВД) и низкого давления (ПНД), так как они обладают отличными механическими показателями прочности и пластичности, что делает их невосприимчивыми к прорастанию корней деревьев. Срок жизни среднего полигона ТБО – 50-60 лет, в течение этого времени геомембрана и геотекстиль могут обеспечить надежную защиту почвы и грунтовых вод от попадания вредных химических элементов [50].
Опасные отходы, прошедшие все возможные виды обработки, подлежат захоронению в резервуарах на дне котлованов. Полигоны с такими захоронениями отмечаются знаками и огораживаются с помощью колючей проволоки. Существует ряд правил по устройству захоронений. В частности, нельзя устраивать места для захоронения ТБО и промышленных отходов:
Преимущества и недостатки полигонов
Преимущества:
· Низкие капитальные расходы по сравнению с другими методами
· Возможность размещения различных видов отходов (при соответствующем оборудовании полигона)
· Полигон обеспечивает полное конечное размещение отходов
· После закрытия участок рекультивируют, он может быть использован для других целей (лесопосадки, складские помещения, автостоянки и т.п.)
Недостатки:
· Потребность в больших площадях
· Значительные эксплуатационные
· расходы при удалении объекта от города
· Возможность образования газообразных продуктов разложения
· Образование фильтратов
· Необходимость обслуживания участка после закрытия (фильтрат, биогаз) с целью обеспечения безопасности окружающей среды
· Экологическая опасность, сохраняющаяся длительное время.
При захоронении опасных и чрезвычайно опасных отработок обязательно проводится фиксация и капсулирование. Резервуар с опасным веществом покрывается обволакивающим составом для исключения контактов со всем, что может его разрушить.
Использование цемента для фиксации отходов (омоноличивание) является в настоящее время наиболее распространенным методом. Технология применяется для отходов, содержащих воду, которая необходима для реакции цементирования. Недостаток метода - увеличение объема отходов и возможная деградация цемента при низких значениях рН. Применяется для неорганических отходов, особенно тяжелых металлов, а также радиоактивных отходов, не подлежащего переплавке металлического мусора, отстоя сточных вод некоторых производств. Если в резервуаре содержатся неорганические отходы, то может быть проведено капсулирование известью. Также применяется инкапсулирование - заливание измельченных отработок с термопластом. При затвердевании пластик покрывает и фиксирует частицы. Самый редкий (по причине больших затрат) и надежный способ – капсулирование в стекле [6,7]. Эти методы применительно к жидким отходам и шламам подробно описаны в Главе 2, раздел 2.1.9.
Стабилизация и рекультивация полигонов
Стабилизация мест утилизации и захоронения твердых бытовых отходов – обязательная процедура перед началом рекультивации свалки. Стабилизация представляет собой комплекс мер по упрочнению грунта на свалках. С этой целью создают газоны из долгоживущих трав. На местах захоронения твердых бытовых отходов сажают мелкие кустарники или крупные деревья. В этом случае места хранения твердых бытовых отходов стабилизируются, в зависимости от зоны климата, от одного года до трех лет.
Рис.3.9. Пример рекультивации полигона твердых отходов
Относительно новый и самый перспективный вариант – создание огородов или садов, однако срок стабилизации в этом случае составляет от 10 до 15 лет, из - за чего крайне редко применяется на практике.
Метод стабилизации почвы выбирается владельцами полигона на этапе его проектирования. Стоимость процедуры закладывается в общие расходы при создании места захоронения твердых бытовых отходов [54].
Современные технологические средства не позволяют полноценно восстановить закрытые места захоронения твердых бытовых отходов. По этой причине возникает необходимость в определении направления рекультивации полигонов ТБО. Выделяют три способа: создание сельскохозяйственных и лесохозяйственных зон, создание рекреационных мест и площадок для строительства.
Направление, связанное с сельским хозяйством, используется в случае, когда закрытый полигон расположен в зоне предприятия, ведущего сельскохозяйственную деятельность. Главная цель такого подхода – создать на непригодной земле сенокосные пастбища и площади для выращивания сельскохозяйственных культур. При выборе такого пути восстановления через 10 — 15 лет появится возможность выращивать фрукты и овощи. Лесохозяйственное направление подразумевает создание на бывших местах утилизации и захоронения твердых бытовых отходов зеленых насаждений различных типов. Цель этих мероприятий – привести территорию места бывшего захоронения к приемлемому состоянию для промышленного или гражданского строительства [54].
УТИЛИЗАЦИЯ ОТХОДОВ
Утилизация золы и шлаков
В результате сжигания твердого топлива содержащаяся в нем зола частично остается в топке в виде шлака, а частично уносится продуктами сгорания. Шлак - остаток после сжигания в топках твердого топлива [55]. Золовой унос частично оседает в газоходах котла и улавливается в золоуловителе, частично удаляется вместе с дымовыми газами в атмосферу. В шлаке и уносе имеются частицы несгоревшего топлива. Шлак, удаляемый из топки, обычно представляет собой крупные куски сплавленной стекловидной или хрупкой губчатой массы, а унос, осаждающийся в газоходах и золоуловителе,— сыпучую подвижную смесь частиц золы и несгоревшего топлива. Зола и шлак — ценное сырье для производства строительных материалов [55,56].
Золы и шлаки ТЭС являются эффективным сырьем для изготовления силикатного кирпича, зольной керамики, минеральной ваты, стекла. Применение топливных зол и шлаков в производстве рассматриваемых материалов обеспечивается совокупностью их свойств: химическим взаимодействием с известью, дисперсностью, спекаемостью, теплотворной способностью, способностью давать силикатный расплав. В зависимости от целевого назначения золошлакового сырья и применяемых технологий ведущее значение приобретают те или иные из указанных свойств [56].
Силикатный кирпич.
На долю силикатного кирпича приходится значительная часть всего объема стеновых материалов. Его производство значительно дешевле производства керамического кирпича [56]. В производстве его золы и шлаки ТЭС используются как компонент вяжущего или заполнителя. Оптимальное соотношение извести и золы в составе вяжущего зависит от активности золы, содержания в извести CaO, крупности и гранулометрического состава песка и других технологических факторов и может колебаться в широком диапазоне. При введении угольной золы расход извести снижается на 10-50%,, а сланцевые золы с содержанием (СаО + MgO) до 40—50% могут полностью заменить известь в силикатной массе. Зола в известково-зольном вяжущем является не только активной кремнеземистой добавкой, но также способствует пластификации смеси и повышению в 1,3-1,5 раза прочности сырца. Эффективность введения золы повышается с ростом удельной поверхности известково-зольного вяжущего.
Целесообразно использовать золы и шлаки антрацитовых углей, в которых содержание несгоревшего топлива составляет 15-20%. Основная масса несгоревшего топлива содержится внутри частичек аморфизованного глинистого вещества, оплавленного снаружи. Суммарное содержание активных СаО и MgO в силикатной массе должно составлять 6-8%, содержание золы 50%, влажность 6-10%. Высококальциевые и кислые золы, содержащие значительное количество свободного оксида кальция, должны предварительно гаситься паром под давлением. Золы, не содержащие свободный оксид кальция, в гашении не нуждаются, но при смешивании с известью должны подвергаться обычному силосованию. Силикатный кирпич с добавками зол и топливных шлаков характеризуется: плотностью 1250-1400 кг/м3; прочностью 10-17,5 МПа, пористостью 27—28%, морозостойкостью 15-35 циклов. Применение его позволяет уменьшить толщину наружных стен на 20%, а массу на 40% и существенно сократить расход тепла на отопление зданий [56].
Исследуется возможность утилизации отходов ЦБП при изготовлении кирпича [57-59]. Показано, что добавка отходов производства беленой целлюлозы, содержащих короткие целлюлозные остатки, позволяет увеличить пористость кирпича, стабилизировать процесс высушивания, увеличивает прочность на изгиб [58]. Одновременно это позволяет сэкономить электроэнергию при изготовлении [59].
Керамические и плавленые изделия.
Золошлаковые отходы ТЭС могут служить в качестве отощающих или топливосодержащих добавок в производстве керамических изделий на основе глинистых пород, а также основного сырья для изготовления зольной керамики [56]. В золах, используемых как добавки при производстве стеновых керамических изделий, количество S03 не должно превышать 2% от общей массы, а шлаковых включений размером более 3-5 мм. Недопустимы включения размером более I мм в виде плотных каменистых зерен. Оптимальное содержание золы в шихте зависит от ее теплотворной способности и пластичности применяемого глинистого сырья. В зависимости от пластичности глин вводят золу по объему 10 до 40 %. Эффективность золошлаковых добавок зависит от их дисперсности и зернового состава.
Разработан ряд технологических способов получения зольной керамики, где золошлаковые отходы ТЭС являются уже не добавочным материалом, а основным сырьевым компонентом. Так, при обычном оборудовании кирпичных заводов может быть изготовлен зольный кирпич из массы, включающей золу, шлак и натриевое жидкое стекло в количестве 3% по объему. Последнее выполняет роль пластификатора, обеспечивая с минимальную влажность изделий, что исключает необходимость сушки сырца. Зольную керамику выпускают также в виде прессованных изделий из массы, включающей 60-80% золы уноса, 10-20% глины и другие добавки. Изделия поступают на сушку и обжиг. Установлено, что на основе зол с в содержанием оксидов алюминия и кремния (75-95%) можно получить керамические стеновые материалы, характеризующиеся достаточно высоким пределом прочности при сжатии (10-60 МПа). Существенное влияние на процессы структурообразования золокерамических материалов оказывают значительные колебания содержания СаО, обеспечиваемого карбонатными включениями и свободным оксидом кальция. Установлено, что золы, содержащие до 4,5% СаО, могут быть использованы в качестве исходного сырья без предварительного измельчения. Золы, содержащие 30-50% СаО, непригодны для получения золокерамических материалов. Процессы увлажнения и обработки смесей на основе зол с высоким содержанием оксида кальция сопровождаются экзотермической реакцией гидратации, тепло которой вызывает высушивание массы и, как следствие, ее рассыпание.
Показано, что по пределу прочности при сжатии и изгибе, сравнительно низкой средней плотности, теплопроводности и высокой морозостойкости (25-120 циклов) зольная керамика может служить не только стеновым материалом, обладающим прочностью и высокой морозостойкостью. Она характеризуется высокой кислотостойкостью и низкой истираемостью, что позволяет изготавливать из нее тротуарные и дорожные плиты, а также другие изделия, обладающие высокой химической и термической стойкостью [56].
В последние годы зольные отхода пополнились новым видом — золами от сжигания осадков очистных сооружений канализации населенных пунктов. Отходы этого вида существенно отличаются от отходов ТЭС. По химическому составу такая зола представляет кислое сырье с содержанием органики до 3,25%. Она включает повышенное количество красящих оксидов (Fe203 + Ti02 = 12,27%), легкоплавкая и относится к четвертому классу опасности (малоопасные вещества). В процессе контакта с водой зола не выделяет высокотоксичных соединений. Установлена возможность проиодства на основе шихты с добавкой золы от сжигания осадков сточных вод кирпича с достаточно высокими качественными показателями.
Из большинства разновидностей зол ТЭС как сухого, так и гидроудаления можно получать минеральную вату с плотностью, с широким диапазоном содержания Si02 и А1203 (40—75%). Разработана технология производства термически стойкой минеральной ваты из золы ТЭС методом плавки в электродуговой печи. Такая вата может применяться для изоляции поверхностей с температурой до 900 °С или при использовании керамической связки для изоляции поверхностей с температурой до 1150 °С. По своим характеристикам золовата подобна высокотемпературной каолиновой вате, но ее себестоимость в 2 раза меньше [56].
Возможно получение стекол типа марблит с содержанием в шихте 60—70% по массе отходов ТЭС. Кристаллизационные и вязкостные свойства таких стекол обеспечивают получение из них архитектурно-строительных изделий и облицовочных плиток.
В последние годы все более важное значение приобретает изготовление на основе топливных зол и шлаков эффективных стеклокристаллических материалов — золоситаллов и шлакоситаллов. Например, на основе зол Назаровской ГРЭС синтезированы золоситаллы, фазовый состав которых представлен пироксеновым твердым раствором.
Золошлаковое сырье может применяться для изготовления заполнителей как тяжелых, так и легких бетонов. Пористыми заполнителями для легких бетонов служат: шлаки от сжигания антрацита, каменного и бурого углей, торфа и сланцев; золы, щебень и песок из топливных шлаков, аглопорит на основе золы ТЭС, зольный обжиговый и безобжиговый гравий, глинозольный керамзит.
Золошлаковые заполнители.
Шлаки ТЭС целесообразно применять в легких и тяжелых бетонах в качестве основного заполнителя, для частичной замены щебня (20-50%), а также для улучшения гранулометрического состава песков. Все топливные шлаки можно классифицировать на основные, кислые и нейтральные. Шлаки каменных углей в основном кислые. Шлаки некоторых бурых углей и сланцев, содержащие до 40% СаО и повышенное количество оксидов железа, относятся к основным. Наименее кислыми являются антрацитовые шлаки.
Вредными компонентами шлаков, вызывающими при повышенном количестве разрушение бетона, являются сульфаты и сульфиды. Общее содержание сернокислых и сернистых соединений в пересчете на S03 в топливных шлаках не должно превышать 3% массы, в том числе не более 1% водорастворимых сульфатов и 1% сульфидов. Недопустимо также присутствие в шлаках ТЭС свободного оксида кальция, гашение которого в затвердевшем бетоне может послужить причиной его разрушения. Так же, как и металлургические, шлаки ТЭС должны быть устойчивы против силикатного и железистого распада. Стойкость против силикатного распада определяют пропариванием и автоклавной обработкой пористого щебня, а железистого - 30-дневным выдерживанием в дистиллированной воде. [57]
Для предотвращения распада топливные шлаки рекомендуется применять после длительного (3—6 месяцев) вылеживания в отвалах, в результате чего в них гасится свободный оксид кальция, частично выщелачиваются растворимые соли и окисляются топливные остатки. При применении шлаков в бетонах целесообразно их обогащать, отсеивая мелкие фракции, содержащие наибольшее количество несгоревшего угля и других вредных примесей.
В отличие от щебня из природного камня шлаковый щебень практически не содержит лещадных и игловатых зерен, глинистых и других вредных примесей, и при использовании в качестве заполнителя в бетонах такой щебень, как свидетельствуют результаты исследований, обеспечивает прочностные характеристики до 30 МПа.
Мелкий заполнитель в тяжелых и легких бетонах частично или полностью может быть заменен золой. Установлено, что на долговечность бетона при использовании зол оказывает влияние, главным образом, состав топливных остатков, стойкость которых к окислению и воздействию влаги зависит в свою очередь от минералогического состава исходного угля.
Определение качественного состава остатков несгоревшего топлива дает возможность оценить целесообразность применения золы как мелкого заполнителя бетона. В немалой степени свойства бетона зависят от влажности зол и содержания в них сернистых и сернокислых соединений. Количество последних в перерасчете на S03 не должно превышать 3% по массе (в том числе сульфидной серы в перерасчете на S03 не более 1%). Влажность не должна превышать 35% по массе. Для получения долговечного золобетона для армированных легкобетонных конструкций золы ТЭС должны также содержать пониженное количество глинистых частиц при повышенном содержании стеклофазы (не менее 50—60%). Свойства бетона зависят от гранулометрического состава заполнителей. Применение в бетонах золы-уноса позволяет заменять как часть песка, так и часть цемента. Количество вводимой в состав бетона золы может достигать 150—250 кг/м3 и более. При выборе возможного содержания золы в бетоне следует учитывать воздействие золы на свойства бетонной смеси. Так, в зависимости от содержания золы влияние ее на водопотребность может быть несущественным или значительным.
Золобетоны можно получать с широким диапазоном свойств: по прочности на сжатие, средней плотности. Недостатками плотных золобетонов являются значительное водопоглощение, а также усадка, которая при твердении образцов на воздухе составляет до 2-3 мм/м. Для уменьшения водопоглощения рекомендуется вводить в смесь тонкомолотые добавки, снижающие пористость золобетона, например гранулированный шлак.
Более широкое применение находит зола как мелкий заполнитель в производстве керамзитобетонов. Для обеспечения плотной структуры этих материалов в песчаной фракции должно содержаться 40—50% по массе частиц размером менее 0,15 мм. Применение золы в керамзитобетонах в количестве 180—200 кг/м 3, а для однофракционного керамзита и в больших количествах, улучшает технологические свойства легкобетонных смесей и способствует получению плотной структуры бетона. Полная замена мелкого заполнителя золой наиболее целесообразна в конструктивно-теплоизоляционных легких бетонах. Оптимальное содержание золы в конструктивно-теплоизоляционном керамзитобетоне составляет 300—450 кг/м3. Увеличение ее содержания повышает среднюю плотность легкого бетона. При изготовлении легких конструктивных бетонов добавка золы в количестве до 100 кг на 1 м3 бетона может служить микронаполнителем.
Возможно применение в бетонах рядовых классов, наряду с золой и шлаками и золошлаковой смеси отвалов ТЭС. Золошлаковую смесь целесообразно использовать в качестве основного заполнителя бетонов, для частичной замены щебня (20-50%) и песка (40-100%), а также для улучшения гранулометрии мелких песков. При введении золошлаковых смесей в бетоны применяются смеси с довольно широкими границами изменения гранулометрии. Однако оптимальными являются смеси, в состав которых входит 16—30% пылевидной золы- уноса. Общее содержание золошлаковой смеси должно быть в пределах 230—330 кг на 1 м3 бетона. При прочих равных условиях средняя плотность бетона на золошлаковой смеси на 130—150 кг/м3 меньше, чем на гранитном щебне. Для бетона, например, на золошлаковой смеси, полученной при сжигании донецких углей, характерны следующие физико-механические свойства: прочность при сжатии -до 35 МПа; растяжении - 2,3 МПа; модуль упругости — 24,1 МПа; морозостойкость - 150 циклов; усадка - 0,6-0,7 мм/м.
Гранулированный топливный шлак.
Химический состав гранулированных шлаков, полученных из одного и того же топлива, но с применением различных способов удаления, отличается. В топках топливо сжигают в условиях избытка воздуха, т. е. в слабо окислительной среде, в результате чего в кусковых шлаках образуются соединения трехвалентного железа. При жидком шлакоудалении ион Fe3+ восстанавливается до Fe2+ при непосредственном взаимодействии Fe2O3 с углеродом. Гранулированные шлаки устойчивы к силикатному и железистому распаду, не вступают в реакцию с оксидами щелочных металлов в цементе, несмотря на наличие в них значительного количества аморфного SiO2. Гидравлическая активность топливных гранулированных шлаков, выраженная количеством поглощенной извести, составляет 20-30 мг/г. Непосредственное влияние на гидравлическую активность шлаков имеет их фазовый состав.
Физико-механические характеристики шлака, его структура зависят от вида сжигаемого топлива и способа его удаления. Среди общей массы шлака можно выделить плотные и пористые зерна с различным количеством открытых и закрытых пор. Средняя плотность таких зерен может колебаться от 2,6 до 1,5 г/см3, в редких случаях встречаются зерна со средней плотностью до 1 г/см3. Истинная плотность шлака в основном 2,3-2,7 г/см3, насыпная находится в пределах 1100-1700 кг/м3. Морозостойкость стекловидных шлаков довольна высока и допускает изготовление разнообразных бетонов для высокодолговечных строительных конструкций. Шлаки практически не содержат компонентов, которые могут снижать защитные свойства бетона или придавать ему агрессивность по отношению к арматуре. Предлагается применять топливный гранулированный шлак для литых бетонных смесей.
Физико-химическими исследованиями установлено, что прочность сцепления шлака с цементным камнем обусловлена не только адгезией за счет рельефа поверхности зерен, но и в значительной степени химическим взаимодействием цементного камня и заполнителя. Образуемая в зоне контакта пленка новоообразований (гидросиликаты кальция) является оболочкой, которая обволакивает зерна заполнителя, улучшает сопротивление бетона внешним воздействиям. При проведении испытаний бетона со шлаковым и гранитным заполнителями на прочность при растяжении методом раскалывания были получены практически одинаковые результаты.
Топливные шлаки и золы являются лучшим сырьем для производства аглопорита - искусственного пористого заполнителя. Это обусловлено способностью золошлакового сырья так же как глинистых пород и других алюмосиликатных материалов спекаться на решетках агломерационных машин; во-вторых, содержанием в нем остатков топлива, достаточных для процесса агломерации. При использовании обычной технологии аглопорит получают в виде щебня и песка. Из зол ТЭС можно получать также аглопоритовый гравий, имеющий высокие технико-экономические показатели [60].
Разработана и применяется технология производства аглопоритового гравия из золы ТЭС, особенность которой состоит в том, что в результате агломерации сырья образуется не спекшийся корж, а обожженные гранулы. Разработанная технология предусматривает возможность использования сухой золы-уноса, золы из отвалов ТЭС, а также водозольной суспензии, образующейся при гидротранспорте золы в отвалы.
Аглопоритовый щебень
В зависимости от состава золы и режима тепловой обработки зольных гранул получают аглопоритовый щебень с насыпной плотностью 500—700 кг/м3 и прочностью (в цилиндре) 1,5— 5,5 МПа. Он используется для получения легких бетонов: классов В3,5—В5 с плотностью около 1000 кг/м3 при расходе цемента 200 кг/м3, классов В7,5—В15 с плотностью 1200 кг/м3 при расходе цемента 260 кг/м3, классов В22,5—В30 с плотностью 1600 кг/м3 при расходе цемента от 385 до 500 кг/м3. Для производства аглопоритового гравия используют золы с интервалом плавкости не менее 50—100 °С и содержанием оксидов железа не менее 4%. Производство аглопоритового гравия, по сравнению с обычным производством аглопорита, характеризуется снижением расхода технологического топлива на 20—30%, низким разрежением воздуха в вакуум-камерах, а также увеличением удельной производительности в 1,5—2 раза. Аглопоритовый гравий имеет плотную поверхность и поэтому при практически равной средней плотности со щебнем отличается от него более высокой прочностью и меньшим водопоглощением.
Золы ТЭС могут применяться не только как основное сырье, но и как топливные добавки при производстве аглопорита из глинистых пород. В состав шихты для производства аглопорита требуется до 8% высококалорийного топлива. Применение добавки золы позволяет сократить расход топлива и снизить себестоимость аглопорита.<
|
|
Автоматическое растормаживание колес: Тормозные устройства колес предназначены для уменьшения длины пробега и улучшения маневрирования ВС при...
История развития хранилищ для нефти: Первые склады нефти появились в XVII веке. Они представляли собой землянные ямы-амбара глубиной 4…5 м...
Общие условия выбора системы дренажа: Система дренажа выбирается в зависимости от характера защищаемого...
Типы сооружений для обработки осадков: Септиками называются сооружения, в которых одновременно происходят осветление сточной жидкости...
© cyberpedia.su 2017-2024 - Не является автором материалов. Исключительное право сохранено за автором текста.
Если вы не хотите, чтобы данный материал был у нас на сайте, перейдите по ссылке: Нарушение авторских прав. Мы поможем в написании вашей работы!