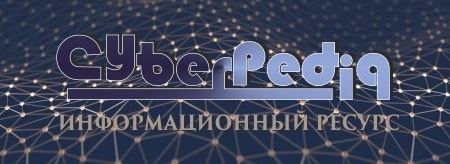
Наброски и зарисовки растений, плодов, цветов: Освоить конструктивное построение структуры дерева через зарисовки отдельных деревьев, группы деревьев...
Индивидуальные очистные сооружения: К классу индивидуальных очистных сооружений относят сооружения, пропускная способность которых...
Топ:
Организация стока поверхностных вод: Наибольшее количество влаги на земном шаре испаряется с поверхности морей и океанов...
Характеристика АТП и сварочно-жестяницкого участка: Транспорт в настоящее время является одной из важнейших отраслей народного хозяйства...
Теоретическая значимость работы: Описание теоретической значимости (ценности) результатов исследования должно присутствовать во введении...
Интересное:
Финансовый рынок и его значение в управлении денежными потоками на современном этапе: любому предприятию для расширения производства и увеличения прибыли нужны...
Уполаживание и террасирование склонов: Если глубина оврага более 5 м необходимо устройство берм. Варианты использования оврагов для градостроительных целей...
Средства для ингаляционного наркоза: Наркоз наступает в результате вдыхания (ингаляции) средств, которое осуществляют или с помощью маски...
Дисциплины:
![]() |
![]() |
5.00
из
|
Заказать работу |
|
|
Каталитические методы обезвреживания газов позволяют эффективно проводить очистку газов от оксидов азота. Каталитические методы дают возможность:перерабатывать многокомпонентные газы с малыми концентрациями вредных примесей;добиваться высоких степеней очистки;вести процесс непрерывно;избегать в большинстве случаев образования вторичных загрязнителей; переводить экологически опасные примеси в безвредные или даже в полезные.
Недостатки каталитических методов связаны чаще всего с проблемами поиска, и разработкой способов приготовления дешевых катализаторов и обеспечения их длительной эксплуатации.
Основным элементом технологической схемы гетерогенно-каталитического процесса является реактор, загруженный твердым катализатором в виде пористых гранул, колец, шариков или блоков со структурой, близкой к сотовой. Химические превращения происходят на развитой поверхности катализатора, доходящей до 1000 м2/г.
Промышленно освоенные каталитические методы восстановления NОХ условно можно разделить на два основных класса: высокотемпературное каталитическое восстановление, которое протекает только в безкислородной среде при использовании в качестве восстановителя горючих газов; и селективное каталитическое восстановление (СКВ), особенностью которого является взаимодействие используемого восстановителя с оксидами азота в присутствии кислорода.
Высокотемпературное каталитическое восстановление осуществляют в присутствии газов восстановителей водорода, оксида углерода, углеводородов (пары керосина, нефтяной и природный газ). До начала реакции газы должны быть нагреты в зависимости от природы катализатора и восстановителя до 200-480 °С. Нижний предел соответствует восстановлению NОX водородом при использовании в качестве катализатора платины на носителе. Температура 480 °С необходима при восстановлении природным газом. Оксиды азота восстанавливаются до N2 [5,6].
|
Проведено изучение процесса восстановления NO метаном в интервале 580--680 °С на оксидных катализаторах: MgO, Li/MgO. Установлено, что литий оказывает промотирующий эффект, но он мало зависит от концентрации лития в катализаторе [6].
Процесс восстановления оксидов азота горючими газами требует первоначального повышением температуры. В случае применения природного газа (метана) «выжигание» кислорода протекает по реакции:
СН4 + 2O2 = СО2 + 2Н2О + 804,58 кДж/моль СH4.
При недостатке кислорода из метана могут образоваться водород и оксид углерода:
СН4 + 0,5O2 = СО + 2Н2 + 35,13 кДж/моль СН4.
Все три восстановителя (СН4, СО и Н2) реагируют на катализаторе с оксидами азота, восстанавливая их до элементарного азота:
NО2 + Н2 = NО + Н2O;
2NО + 2Н2 = N2 + 2Н2О
Аналогично реагируют СН4 и СО.
Так как содержание оксидов азота в большинстве случаев не превышает 0,2%, расход горючего газа собственно на процесс восстановления невелик и определяется содержанием кислорода в очищаемых газах. В отходящих газах ТЭС концентрация кислорода составляет 3-8%. Для поддержания восстановительной среды отношение СH4/ NОх поддерживают на уровне 0,55-0,56. Бὸльший избыток метана приводит к появлению в газе после очистки токсичного оксида углерода. В реальных условиях в отходящих газах после восстановления оксидов азота содержание СО составляет 0,22-0,4% по объему.
В качестве катализаторов высокотемпературного восстановления используют различные металлы, чаще всего нанесенные на разнообразные носители. Основными активными компонентами служат Pt, Pd, Ro, Ni, Cr, а также ряд сплавов. В странах бывшего СССР наибольшее распространение получили палладиевые катализаторы марки АПК-2, представляющие собой таблетированный оксид алюминия, на который нанесен Рd в количестве 2% по массе. В качестве восстановителя используется природный газ. Температура газа на входе в реактор составляет 400-00, на выходе 700-750 °С. Остаточное содержание оксидов азота не более 0,005% по объему. Известен катализатор АЖМ-15 (на замену АПК-2), который представляет собой нанесенные на Al2O3 оксиды железа, марганца и меди. Процесс высокотемпературного каталитического восстановления оксидов азота применяется в основном на линиях по производству слабой азотной кислоты [1,5].
|
Неселективное высокотемпературное каталитическое восстановление применительно к газам ТЭС активно развиваются в Германии. Первоначально проводят восстановление оксидов азота за счет ввода в топливные газы метана. Процесс протекает при 450 °С на катализаторе из благородных металлов. Затем на втором слое катализатора при 400 °С осуществляется окисление SO2 в SO3 с последующим получением серной кислоты. Одним из вариантов этого процесса является каталитическое восстановление NОх и SO2 метаном при недостатке кислорода до N2 и Н2S с последующим получением из Н2S товарной серы. В рассматриваемых случаях отмечается явление коррозии металла и рост затрат на восстановитель - метан.
К недостаткам метода высокотемпературного каталитического восстановления следует отнести высокую начальную температуру реакции, значительный расход восстановителей на «выжигание» кислорода, затраты на утилизацию тепла отходящих газов и поддержание необходимого температурного режима процесса (Т < 850 °С), появление выбросов оксида углерода.
В последнее время появились разработки катализаторов, позволяющие осуществлять восстановление оксидов азота углеводородами (прежде всего пропан-бутаном) в присутствии кислорода. Пока эти разработки не вышли за уровень лабораторных испытаний. Катализаторы для такого процесса представляют собой цеолиты типа ZSМ-5, промотированные медью или перовскиты. Процесс осуществляется при температурах 450 –.800°С, времени контакта по катализатору 0,2-0,3 с. Эффективность удаления NОх достигает 95 % при отношении концентрации оксидов азота и восстановителя (пропан-бутан) - 1:2 и содержании кислорода в очищаемых газах - 3-5 % [6].
Селективное каталитическое восстановление (СКВ) получило в последние годы наибольшее распространение для очистки газов от NОX. Особенностью этого процесса является взаимодействие используемого восстановителя с оксидами азота в присутствии кислорода. Этот процесс выгодно отличается от высокотемпературного восстановления тем, что протекает в основном избирательно: используемый восстановитель (как правило, аммиак) реагирует преимущественно с NOx и почти не взаимодействует с находящимся в нитрозных газах кислородом. В связи с этим аммиак расходуют в количествах, эквивалентных содержанию в обезвреживаемых газах оксидов азота или превышающих стехиометрию на 10-50% с целью более полного протекания следующих экзотермических реакций: [5-7].
|
Ниже приведены основные реакции, протекающие при восстановлении оксидов азота в кислородсодержащей среде.
4NН3 + 4NО + О2 ® 4N2 + 6Н2O;
8NН3 + 6NО2 ® 7N2 + 12Н2O;
4NН3 + 5O2 ® 4NO + 6Н2О;
4NН3 + ЗО2 ® 2N2 + 6Н2O;
2 N Н3 + 2 O 2 ® N 2 O + ЗН2 O.
Селективное каталитическое восстановление происходит при низких температурах (180-360 °С) с выделением небольшого количества тепла. Температура очищаемых газов увеличивается в зоне катализа на 10-20 °С. При избытке аммиака его основное количество окисляется присутствующим в нитрозных газах кислородом по экзотермической реакции:
4NН3 + ЗО2 ® 2N2 + 6Н2O
Процесс достаточно прост по аппаратурному оформлению и внедрен в производствах азотной кислоты под давлением 0,35 МПа. Отходящие нитрозные газы таких производств содержат до 0,2 % (об.) NO + NO2. Технологическая схема процесса представлена на рисунке 4.1.
Нитрозные газы при 20-30 °С подают в подогреватель, где их нагревают до 240-280 °С и направляют в смеситель. Подаваемый в установку жидкий аммиак испаряют нагретым конденсатом. Образующиеся пары аммиака при давлении 3,5-10,0 Па очищают в фильтре, нагревают до 120 °С и смешивают с нагретыми нитрозными газами, регулируя соотношение NH3/NOx на уровне (1,2-1,3):1.
Рис. 4.1. – Схема установки каталитической очистки отходящих нитрозных газов производств азотной кислоты под давлением 0,35 Мпа [5].
1 – реактор; 2 – смеситель; 3 – рекуперационная турбина; 4 – испаритель; 5, 7, 8 – подогреватели; 6 – фильтр.
Активная масса катализатора обычно выполняется на основе диоксида титана ТiO2, пентаоксида ванадия V2О5 с добавками WO3 или оксидов молибдена и других металлов [5].
|
Обезвреженные нитрозные газы при 300 °С из реактора подают на рекуперационную турбину, откуда их направляют в подогреватель, после которого при 150-170 °С выбрасывают в атмосферу. При возможном образовании в системе аммонийных солей предусматривают периодическую остановку и пропаривание турбины насыщенным паром низкого давления. Процесс обеспечивает обезвреживание нитрозных газов на 96 %. Содержание NO и NO2 в обеззараженных газах не превышает 0,01 % (об.), NH3 – до 0,015 % (об.).
В качестве эффективных катализаторов при восстановлении нитрозных газов (содержащих 1-30 % NOх) аммиаком могут быть использованы цеолиты. Адсорбция на них NH3 и NOx ускоряет их взаимодействие, обеспечивая при 330 - 480 °С высокую эффективность процесса обезвреживания оксидов азота.
Процесс очистки газов, при котором NOx превращается в элементарный азот посредством введения аммиака, получил широкое распространение. [7,8].
Как пример, можно привести технологию DENOX датской фирмы «HALDORTOPSOEA/S». Процесс используется для очистки отходящих нитрозных газов тепловых электростанций и котельных, химических предприятий, мусоросжигательных заводов, газовых турбин, дизельных моторов и генераторов.
Наилучшим образом процесс DENOX зарекомендовал себя для очистки дымовых газов тепловых (мазутных) электростанций, где, как известно, имеют место значительные выбросы сажи.
Катализатор- сотовый, используемый в процессе, не забивается пылью, имеет низкое аэродинамическое сопротивление, срок службы катализатора до дезактивации – 4-5 лет, верхний слой катализатора меняется через 10 лет. Катализатор обеспечивает восстановление 90 % NOx в диапазоне температур 320-340 °С при объеме газа от 10 до 800 тыс.нм3/ч, концентрации оксидов азота в газе 0,04-0,09 %.
Принципиальная технологическая схема процесса DENOX представлена на рисунке 4.2.
![]() |
Рис. 4.2. – Схема установки каталитической очистки топочных газов в процессе ДЕНОКС [8]. 1 – реактор; 2 – смеситель; 3 – емкость аммиака; 4 – испаритель аммиака; 5 – пароструйные воздуходувки. |
Жидкий аммиак из резервуара (3) подается в испаритель (4), откуда пары аммиака, смешиваясь с воздухом высокого (3-5 бар) давления, поступают в поток очищаемого газа через сопловый смеситель (2), обеспечивающий равномерное распределение аммиака в сечении газового потока, и далее – в реактор. Реактор имеет прямоугольное сечение, содержит 2 или более слоев катализатора, между которыми при необходимости располагают пароструйные воздуходувки (5) для улавливания пыли и летучей золы с поверхности катализатора. Внешний вид установки DENOX-процесса датской фирмы «HALDORTOPSOEA/S» представлен на рисунке 4.2.
|
Таким образом, процессы селективного каталитического восстановления оксидов азота используют для обработки нитрозных газов, содержащих пыль, сажу, диоксид серы и могут применять для очистки газовых выбросов в черной металлургии.
Оптимальной для протекания реакций восстановления в зависимости от катализатора и носителя считается температура 200-400 °С. Так, максимум конверсии NО на V2O5/ТiO2 наблюдается при 300 °С; при использовании V2О5/Аl2О3 оптимальные температуры для восстановления NОX составляют 400 °С. Максимальная активность в реакции восстановления NО аммиаком на катализаторе Сг2О3/Аl2О3 наблюдается при 310 °С. Каталитическая активность в реакциях восстановления убывает в ряду: Рt > МnO2 > V2О5 > СuО > Fе2О3 > Сг2О3 > СоО3.
Введение Cr2O3 в каталитическую систему V2O5/TiO2 также увеличивает активность селективного каталитического восстановления. Наиболее активен катализатор состава (2Cr2O3+6V2O5) /TiO2 [6].
В процессе восстановления NO аммиаком наблюдается образование N2O. Добавление воды при высоких температурах положительно влияет на активность и селективность при высоких температурах, поскольку тормозит окисление аммиака кислородом.
Аммиак по токсичности сопоставим с NOx: ПДКNH3 = 20 мг/м3, ПДКNOx = 5 мг/м3. При очистке горячих дымовых газов аммиак вводят в значительном избытке по отношению к NОX, чтобы одновременно связать присутствующий в газах диоксид серы в сульфат и (или) сульфит аммония.
Поэтому восстановление NOx аммиаком требует точной дозировки восстановителя. Кроме того, в избытке аммиака образуется сульфат аммония, который отрицательно влияет на производительность очистительных установок. Поэтому, для удобства применения вместо газообразного NH3 используют аммиачную воду или другой N-содержащий восстановитель, например, водный раствор карбамида. Предлагается AdBlue высококачественный реагент, представляющий собой раствор мочевины высокой чистоты (32,5%) в деминерализованной воде (67,5%) предлагается для удаления окислов азота из выхлопных газов. AdBlue является торговой маркой, зарегистрированной Ассоциацией Автомобильной Промышленности Германии (Verband der Automobilindustrie (VDA)). Установлено, что скорость восстановления NОX зависит от соотношения NО/NO2. Восстановление лучше всего осуществлять в потоке очищаемого газа испарением азотной кислоты до установления соотношения NО2/NО на уровне 0,9-1,1. С другой стороны, предлагается для очистки газов, богатых NО2, использовать первоначальное восстановление диоксида азота метанолом, пока отношение NO2/NO не достигнет оптимального значения, после чего в газ вводят аммиак и проводят селективное восстановление. При осуществлении процессов СКВ возможно протекание побочных реакций образования в газовой фазе нитритов и нитратов аммония по реакции
2NО2 + 2NН3 + Н2О = NН4NO2 + NН4NО3.
Накопление этих соединений нежелательно с точки зрения безопасности процесса. Независимо от концентрации NО2 и O2, для каждой температуры имеется значение парциального давления NН3, ниже которого соли аммония не образуются [10].
Основные области применения методов СКВ - это очистка отходящих газов от NОХ в производстве азотной кислоты и дымовых газов при сжигании топлива. Применение метода СКВ для очистки газов ТЭС имеет ряд особенностей, связанных с запыленностью отходящих газов, их сравнительно высокой температурой, а также содержанием в них диоксида серы. Процессы СКВ запыленных газов ТЭС могут быть реализованы лишь на катализаторах с керамической сотовой структурой (блоках) при высоких линейных скоростях, доходящих до 60 м/с, что исключает забивание каналов пылью [7,8].
В качестве восстановителя использоваться также аммиак - образующие реагенты. Это растворы аммиака: аммиачная вода, распыляемая в потоке горючего газа, после чего капли находятся в контакте с газом 2-10 с до попадания на слой катализатора или просто жидкий аммиак.
Аммиак может быть получен также непосредственно перед слоем катализатора за счет конверсии метана. Для селективного восстановления NОX предложено применять также сероводород. Количество восстановителя зависит от концентрации оксидов азота и необходимой степени очистки.
Существующие катализаторы позволяют проводить процессы восстановления при низких температурах (150-180 °С) в том случае, если будут обеспечены условия, исключающие накопление аммонийных солей (например, нитрата аммония). Разработаны методы разложения накопившихся аммонийных солей и восстановления активности катализатора.
Основные требования, предъявляемые к катализаторам СКВ промышленностью [7]:
· высокая активность и селективность в реакциях восстановления NОX при возможно низких температурах;
· низкая активность в реакциях окисления SO2 в SO3;
· медленная дезактивация;
· коррозийная устойчивость;
· механическая прочность и устойчивость к температурным колебаниям;
· низкое гидравлическое сопротивление.
В последнее время много внимания уделяется разработке новых каталитических систем для селективного восстановления NOx углеводородами и, прежде всего, метаном [2]. При проведении процесса восстановления оксидов азота метаном на Со-, Мn-, Ni-цеолитных катализаторах при температуре 400-450° С и соотношении СH4: О2= 0,05 конверсия NOX составила 50% [6], что считается хорошим результатом, так как реакция в этом случае протекает в условиях значительного избытка кислорода. Зависимость конверсии NOx от концентрации метана имеет вид «кривой насыщения» [2]. Показано, что с повышением температуры более 450 °С вклад реакции окисления СН4 на цеолитном катализаторе Ga-H-ZSM-5 не велик (конверсия метана составляет около 32%). Напротив, на катализаторах Co-H-ZSM-5 и Cu-H-ZSM-5 при температуре выше 500 °С протекает в основном реакция окисления метана до диоксида углерода и воды (конверсия метана составляет более 99%).
|
|
Таксономические единицы (категории) растений: Каждая система классификации состоит из определённых соподчиненных друг другу...
Своеобразие русской архитектуры: Основной материал – дерево – быстрота постройки, но недолговечность и необходимость деления...
Автоматическое растормаживание колес: Тормозные устройства колес предназначены для уменьшения длины пробега и улучшения маневрирования ВС при...
Биохимия спиртового брожения: Основу технологии получения пива составляет спиртовое брожение, - при котором сахар превращается...
© cyberpedia.su 2017-2024 - Не является автором материалов. Исключительное право сохранено за автором текста.
Если вы не хотите, чтобы данный материал был у нас на сайте, перейдите по ссылке: Нарушение авторских прав. Мы поможем в написании вашей работы!