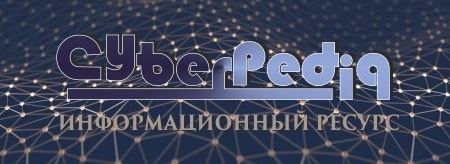
Археология об основании Рима: Новые раскопки проясняют и такой острый дискуссионный вопрос, как дата самого возникновения Рима...
Индивидуальные и групповые автопоилки: для животных. Схемы и конструкции...
Топ:
Когда производится ограждение поезда, остановившегося на перегоне: Во всех случаях немедленно должно быть ограждено место препятствия для движения поездов на смежном пути двухпутного...
Техника безопасности при работе на пароконвектомате: К обслуживанию пароконвектомата допускаются лица, прошедшие технический минимум по эксплуатации оборудования...
Марксистская теория происхождения государства: По мнению Маркса и Энгельса, в основе развития общества, происходящих в нем изменений лежит...
Интересное:
Средства для ингаляционного наркоза: Наркоз наступает в результате вдыхания (ингаляции) средств, которое осуществляют или с помощью маски...
Подходы к решению темы фильма: Существует три основных типа исторического фильма, имеющих между собой много общего...
Наиболее распространенные виды рака: Раковая опухоль — это самостоятельное новообразование, которое может возникнуть и от повышенного давления...
Дисциплины:
![]() |
![]() |
5.00
из
|
Заказать работу |
|
|
Этот метод основывается на результатах конверсии ракетно-космической техники в интересах экологии. Отработана высокотемпературная технология и создан промышленный модуль установки для обезвреживания супертоксичных веществ [1]. Метод базируется на термическом преобразовании обезвреживаемого вещества, включающий ряд последовательных стадий: высокотемпературное разложение (2000 -3500ºС), доокисление и химическое связывание элементов окисления, многоступенчатая система нейтрализации и улавливания конечных малотоксичных соединений (Рис.3.6.). По характеру физико-химических процессов предлагаемый режим занимает промежуточное положение между обычным сжиганием (Т<1500ºС) и плазменным обезвреживанием с характерным температурным уровнем в десятки тысяч градусов. Этот рабочий диапазон позволяет устранить принципиальный недостаток, присущий обычному сжиганию, выражающийся в образовании высокотоксичных промежуточных соединений типа диоксинов. С другой стороны, удается избежать основных недостатков плазменного метода, связанных с чрезвычайной сложностью и дороговизной технологического процесса [1].
Технический облик установки принципиально отличается от мусоросжигательных печей или камер плазменного обезвреживания., в которых основные процессы идут по условной
Окисление 2000 ºС |
Многоступенчатая очистка малотоксичных продуктов реакции T ~ 3500º C |
Окончательная очистка T ≤100º C |
Жидкость (утилизация) |
Твердое вещество (утилизация) |
Термохимическое разложение T ≤3500º C |
Газ (выхлоп) |
|
схеме «горение в объеме». В созданной установке основные исполнительные органы (камера сгорания РД, реакционная камера, абсорбер) расположены в последовательной цепи и работают по схеме организации процессов в высокоскоростном движущемся потоке. Обезвреживанию подвергались основные виды токсичных (фтор-, хлор-, серо-, фосфорсодержащих) соединений, пестициды, дихлофос, карбофос, дизенфецирующая жидкость на фенольной основе. Концентрации веществ в выхлопных газах соответствуют строгим экологическим нормам: HCl- 14 мг/м3 (при допустимой норме 30 мг/м3 ), HF - 0,14 мг/м3 (2 мг/м3 ), SO2 -30 мг/м3 (50 мг/м3). По результатам анализа проб поглощающего раствора и твердого осадка концентрация диоксинов укладывается в допустимые нормативы [1].
Термоселект
Термоселект (ТС) - метод, не требующий предварительной сортировки отходов; он позволяет перерабатывать многие виды особых отходов, твердые отходы любого размера (до 700 мм) сочетая эти достоинства с довольно доступной ценой [1,25,41,42]. Исходным сырьем для технологического процесса являются бытовые и промышленные отходы (в том числе токсические), как поступающие, так и накопленные на городском полигоне для складирования отходов. Единственный вид отходов, который не перерабатывется технологией ТС являются радиоактивные. Схема технологии Термоселект представлена на рисунке 3.7. [42].
Отходы подаются на гидравлический пресс. Далее спресованные отходы и отжатая из них вода попадают в горизонтальный канал. Объем спресованных отходов очень мал, за счет чего достигается высокая теплопроводность массы отходов и имеется полный контакт со стенками канала, который снаружи обогревается синтез - газом до достижения температуры стенок около 600ºС. Органическая составляющая отходов разлагается на CO, CO2, H2, смесь простейших углеводородов и твердый углерод. Неорганическая часть мусора нагревается до 600ºС. Брикеты, содержащие из органики, только углерод, а также образовавшиеся в канале газообразные продукты реакций разложения, подаются в высокотемпературный реактор, где в присутствии кислорода (в этом принципиальное отличие от пиролиза) углерод и продукты дальнейшего разложения превращаются в богатый энергией синтез - газ.
|
нагревание |
пресс |
р еактор Т 1200 ° С |
Реактор-гомогенизатор |
Выход гранулята |
Шоковое охлаждение синтез газа |
Спрессованное сырье 600 ° С |
Рис. 3.7. Схема процесса «Термоселект» [42].
При температуре 1200 ºC (время пребывания 2 сек) происходит деструкция хлорпроизводных углеводородов диоксинов и фуранов и других органических соединений. Последующее резкое охлаждение синтез - газа и содержащихся в нем примесей от 1200 ºC до 90 ºC в присутствии воды предотвращает повторное образование диоксинов и фуранов. Синтез - газ подвергается многостадийной очистке, предусматривающей адсорбционную очистку или конденсацию. Чистый синтез-газ используется или как источник энергии или для производства метанола. Тяжелые металлы, входящие в состав мусора, выносятся вместе с реакционным газом, поэтому его подвергают сложной газоочистке. [ 25,42-45]
Неиспарившиеся неорганические соединения либо расплавляются, либо окисляются кислородом. Таким образом, в реакторе образуется расплав оксидов металлов со слоем шлака наверху (минеральный расплав). Металлический расплав выносится в реактор-гомогенизатор, а затем удаляется из зоны реакции отдельно от него. Стекловидный гранулят минерального расплава со свойствами, идентичными свойствам естественного минерала базальта, может найти применение, например, при строительстве дорог. Металлический гранулят можно использовать в тех отраслях, где невысоки требования к качеству металла [41].
Технология Термоселект включает уникальный процесс высокоскоростного охлаждения, исключающий повторное образование диоксинов, обеспечивает процесс обработки отходов и дополнительную выработку энергии и ресурсов, используя пиролизную газификацию и систему плавления (система газификации и преобразования газа) исключающие обычное сжигание. ТС неагрессивен к окружающей среде. Система ТС вырабатывает очищенный синтетический газ из отходов, который может быть использован как источник энергии, а также производит металлы и шлаки, т.е. ресурсы, пригодные для использования. Швейцарская компания TERMOSELEKT S.A - разработчик этой технологии. 7 заводов, построенных по этой технологии, лицензированы и работают в Японии (таблица 3.5.) [45].
|
Таблица 3.5.
Фабрика, год запуска | Характер отходов | Мощность, т/ч |
Chiba: 1999 | бытовые отходы, шламы, пульпа | 300 |
Mutsu: 2003 | бытовые отходы | 140 |
Osaka: 2004 | пластик, промышленные отходы | 95 |
Kurashiki: 2004 | бытовые отходы, промышленные отходы, пластик, крупногабаритные отходы, пыль, отходы химической промышленности | 555 |
Nagasaki. 2005 | бытовые отходы, крупногабаритные отходы | 300 |
Tokushima: 2005 | бытовые отходы, промышленные отходы | 120 |
Yorii: 2006 | бытовые отходы, промышленные отходы | 450 |
В 2007 г. между ООО «НПП Эко-Синтез Текноледжи» (г. Комсомольск, Полтавской области, Украина) и компанией TERMOSELEKT S.A., Швейцария (Локарно) заключен контракт на поставку технологического оборудования TERMOSELEKT для строительства завода мощностью 100 тыс. тонн в год по переработке бытовых и промышленных отходов в г. Комсомольск, Полтавской области, Украина. [43 ]. Предполагается использовать бурый уголь в качестве дополнительного топлива [43].
Гидрирование
Гидрированием (гидрогенизацией) твердого топлива называется процесс превращения органической части топлива в жидкие продукты, обогащенные водородом и используемые как жидкое топливо. Гидрирование твердого топлива представляет собой деструктивный каталитический процесс, протекающий при высокой температуре и повышенном давлении. В этих условиях происходит разрыв межмолекулярных и валентных связей в органической массе топлива, и протекают реакции деструкции и деполимеризации высокомолекулярных структур. Одновременно с гидрированием углеродных соединений протекают реакции гидрирования соединений, содержащих серу, кислород и азот. В качестве катализаторов применяют различные контактные массы на основе соединений Ni, Pt, Co, Fe, Pd, Cu, V и др.[42] на основе соединений молибдена, никеля или железа. Изменением параметров процесса (температура, давление, время контактирования) и состава катализатора процесс гидрогенизации может быть направлен в сторону получения продуктов заданного состава. Выход жидких и газообразных продуктов гидрирования твердого топлива существенно зависит от содержания в нем летучих веществ.
|
Этот метод не требует рассортировки мусора и более полно, чем пиролиз и термоселект, использует материальный потенциал отходов. Кроме того, разновидность гидрирования - гидрирующее ожижение, - позволяет получать из несортируемых смесей полимеров высококачественный бензин и дизельное топливо. Метод гидрирования безвреден для окружающей среды, поскольку гетероатомы, входящие в состав молекул полимеров, образуют в ходе реакции гидрирования соединения с водородом, которые технически легко выделяются из смеси. Обычно гидрирование - многоступенчатый процесс при температуре 300 - 500ºС и давлении 200 - 400 бар. Время превращения - от 15 мин до нескольких часов в зависимости от состава исходного сырья. В результате образуется газовая фаза, масляная фракция и твердый осадок, включающий неорганические примеси, содержащиеся в отходах даже в случае, когда эта фаза не может быть подвергнута утилизации, требуемый объем на захоронение сокращается на 90% по сравнению с необработанными отходами.
Технология плавки
Специалистами Московского института стали и сплавов разработана принципиально новая технология плавки, которую предложено применять для утилизации твердых бытовых отходов. Мусор в этом случае будет не сжигаться, а плавиться — при температуре до тысячи пятисот градусов и при постоянной подаче технического кислорода. Более высокая, чем при сжигании, температура способствует полному разложению вредных соединений в отходящих газах. Анализ этих газов показал отсутствие в них хлорорганических и органических соединений и весьма малую запыленность. Большое достоинство такого метода — возможность получения из бытового мусора тех ценных компонентов, которые в нем содержатся, включая, например, драгоценные металлы. Подаваемый в ванну кислород интенсивно перемешивает расплав, помогая быстрому растворению и образованию крупных капель металла. Более тяжелые, нежели шлак, эти капли опускаются на самое дно — в наиболее спокойную зону ванны, концентрируясь там в виде донного слоя. Оттуда их время от времени изымают, направляя на дальнейшую переработку. Выпускают из ванны и более легкую — шлаковую — часть расплава, которая идет на производство строительных материалов. Содержащиеся в отходах углерод и углеводороды тоже находят свое применение — их можно использовать как низкокалорийное топливо. Предлагаемая технология, таким образом, не только экологически безвредна, но и позволяет извлекать из мусора реальную экономическую выгоду.
Первые предприятия, утилизирующие бытовые отходы этим полезным и экологически чистым способом, будут построены в подмосковных городах Ногинске и Подольске [47].
|
|
Состав сооружений: решетки и песколовки: Решетки – это первое устройство в схеме очистных сооружений. Они представляют...
Автоматическое растормаживание колес: Тормозные устройства колес предназначены для уменьшения длины пробега и улучшения маневрирования ВС при...
Эмиссия газов от очистных сооружений канализации: В последние годы внимание мирового сообщества сосредоточено на экологических проблемах...
Папиллярные узоры пальцев рук - маркер спортивных способностей: дерматоглифические признаки формируются на 3-5 месяце беременности, не изменяются в течение жизни...
© cyberpedia.su 2017-2024 - Не является автором материалов. Исключительное право сохранено за автором текста.
Если вы не хотите, чтобы данный материал был у нас на сайте, перейдите по ссылке: Нарушение авторских прав. Мы поможем в написании вашей работы!