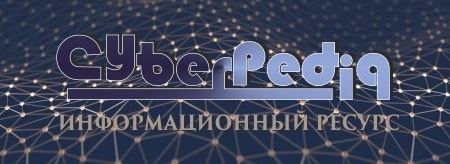
Состав сооружений: решетки и песколовки: Решетки – это первое устройство в схеме очистных сооружений. Они представляют...
Двойное оплодотворение у цветковых растений: Оплодотворение - это процесс слияния мужской и женской половых клеток с образованием зиготы...
Топ:
Проблема типологии научных революций: Глобальные научные революции и типы научной рациональности...
Оценка эффективности инструментов коммуникационной политики: Внешние коммуникации - обмен информацией между организацией и её внешней средой...
Интересное:
Аура как энергетическое поле: многослойную ауру человека можно представить себе подобным...
Финансовый рынок и его значение в управлении денежными потоками на современном этапе: любому предприятию для расширения производства и увеличения прибыли нужны...
Подходы к решению темы фильма: Существует три основных типа исторического фильма, имеющих между собой много общего...
Дисциплины:
![]() |
![]() |
5.00
из
|
Заказать работу |
|
|
ТЕРМИЧЕСКИЕ ТЕХНОЛОГИИ
Все термические технологии являются примерами физико-химических методов уничтожения отходов. Термические технологии применимы для обезвреживания многих видов твердых, растворимых, жидких и газообразных отходов. Их суть заключается в термической переработке отходов высокотемпературным носителем (контактным или бесконтактным методом), роль которого могут играть продукты сгорания топлива: плазменная струя, СВЧ-нагрев отходов. Продукты термического разложения подвергаются окислению, другим химическим взаимодействиям с образованием газообразных, жидких и твердых продуктов. Термический метод, как правило, состоит из следующих стадий: - предварительная, в том числе реагентная обработка;
- высокотемпературная обработка и обезвреживание;
- многоступенчатая очистка газов;
- теплоиспользование;
- получение побочных органических (синтез-газ, жидкое топливо) или минеральных продуктов (оксиды, цемент, минеральные соли и т.д.) [1].
Термические методы обладают определенной универсальностью, так как позволяют обезвреживать многие органические и неорганические соединения. На рисунке 3.1. представлены основные термические методы удаления отходов и токсичных веществ.
Рис.3.1.Термические методы удаления отходов
Инсинерация (сжигание) отходов
Инсинерация с выделением пара или энергии, является одним из наиболее распространенных методов устранения отходов в Европе [1-12]. Любой процесс, который использует горение для преобразования отходов в меньшие по объему, менее токсичные, менее ядовитые материалы, называется инсинерацией. Иногда его также называют «термическим окислением», «термическим уничтожением» или просто «сжиганием». Основным достоинством инсинерации является снижение количества материала, направляющегося на свалку, на 80-90%.
|
На рисунке 3.2. приведена схема современного завода по сжиганию мусора.
Схема иллюстрирует утилизацию золы и шлаков, очистку газовых выбросов, использование энергии пара.
Для окончательного уничтожения или использования золы, в зависимости от её количества, существует несколько приемов. В некоторых случаях остатки от сжигания (зола) непосредственно отправляют на свалку, в других - их используют в строительной индустрии или других областях.
Рисунок 3.2. Схема современного мусоросжигательного завода.
Содержание хлора в отходах требует особого внимания в связи с проблемами коррозии и загрязнения, образующимися хлорсодержащими соединениями. Технологии, предполагающие промывание золы, представляют собой эффективный способ удаления или растворения хлора или тяжелых металлов; это дает возможность снизить содержание хлора до уровня, ниже требуемого в случае использования золы в сельском хозяйстве [10]. Известно несколько технологий сжигания отходов.
Сжигание в решетчатых печах
Обычный метод огневого сжигания шлама в печах с подвижной решеткой предполагает его совместное горение с древесной корой. Инсинератор с подвижными решетками (Рис.3.2.) - самый простой и обычный способ сжигания шламов. Этот метод используют для удаления бытовых отходов.
Использование этого метода для удаления шламов ЦБП вызывает ряд проблем из-за его состава. Состав шлама по золе и кислороду существенно отличается от состава коры, поэтому он горит значительно хуже. Кроме того, существенную роль играет и содержание воды (СВ). Высокая зольность, низкое содержание кислорода и высокое содержание воды - все это снижает температуру сжигания. Установлено, что повышение СВ на 1 % требует повышение температуры на 10ºС. Рассмотрение различных способов поддержания температурного режима, связанных с изменением конструкционных и технологических параметров печи, а также составом топлива показало, что самым чувствительным фактором является СВ. Высокое содержание золы также снижает эффективность печи, особенно для шламов беленой целлюлозы. В приложении 2 приведена типичная решетчатая печь. Преимущества этого типа печей состоит в простоте технологии. Кроме того, имеется возможность варьировать количество сжигаемого шлама, что позволяет учесть как СВ, так и операционные параметры печи [11,13]. Описанный метод до сих пор применяется в России. Однако, недостаточная проработанность систем очистки отработанных газов и достижения европейских стандартов по нормативам выбросов дают основания считать эту технологию в будущем неперспективной. Даже при решении вопроса по очистке отработанных газов она может быть рекомендована только для достаточно узкого класса органических соединений [1].
|
Барабанные печи применяются для сжигания отходов с твердой, жидкой и пастообразной составляющими. Система сжигания состоит из вращающегося барабана с внутренними стенками из огнеупорных материалов, где производится сжигание твердых и пастообразных отходов, и камеры дожигания для окисления оставшейся в дымовом газе органики и сжигания жидких отходов при температуре 1200-1300ºС [14]. Данный тип печей предполагает хорошую очистку отработанных газов, однако к их недостаткам относят большие тепловые потери и высокую стоимость, так как они предусматривают использование второго, кроме отходов, источника топлива [1]. В работе [14] описан экономичный и безопасный для окружающей среды способ переработки шлама с бумажных фабрик при использовании печей барабанного типа. В качестве второго источника топлива предлагается природный газ. Отмечают, что влажность шлама в этом случае не должна превышать 20%.
Котлы с псевдоожиженным слоем (Fluidized bed boiler). В 1922 году фон Винклер разработал реактор, в котором впервые был проведен процесс газификации угля. С тех пор теоретические и экспериментальные исследования улучшили конструкцию котла кипящего слоя (КС). Эту технологию можно применить почти ко всем видам шламов, включая вторичный или биологический шлам [3,4,7]. Псевдоожиженный слой представляет собой совокупность полидисперсных частиц, через которые продувается ожижающий воздух с определённой скоростью, достаточной для ожижения и не превышающей скорость уноса частиц топлива из печи. Схема котла с псевдоожиженным слоем в варианте кипящего слоя (КС) приведена в Приложении 3.
|
При низких значениях содержания воды шлам может гореть без добавления дополнительного топлива. Температура слоя (760 - 900 град) - ниже, чем при обычном сжигании, что объясняется хорошим переносом энергии в слое [11,12]. Если отвод тепла отсутствует, температура внутри слоя может превысить требуемую величину. При определенном составе и соотношении кора/ шлам и при МС 58%-62% охлаждение поверхности слоя не требуется, так как при этих условиях тепло, полученное при горении, компенсирует количество тепла, необходимое для испарения и нагрева [12]. Точные цифры зависят от тепловой способности материала. Котлы КС являются эффективной, доступной и экономичной системой. Котлы КC менее чувствительны к составу топлива, что является проблемой для обычных печей. К их недостаткам следует отнести следующее. Так как продукты сгорания осаждаются на поверхности топки, требуется периодическая чистка и замена инертного материала, покрывающего её. Котлы КС применимы для переработки вторичного шлама, торфа, смешанного с бумагой картона и отходов переработки древесины (Таблица.3.1.)
Таблица 3.1. Некоторые европейские предприятия сжигания отходов ЦБП [9]
Предприятие, страна | Топливо | Производственные мощности |
Cartiere Burgo Verzuolo, Италия | Бумажный шлам и древесные отходы | 27 MВт, 29 тонн/ч водяного пара, 86 бар. 490ºC |
Cartiere Burgo Mantova, Италия | Шлам производства бумаги и беленой целлюлозы и пере-работанные отходы, 43% золы, 55% воды | 13,5 MВт, перегретый водяной пар, до 3,2 MВт в турбинном генераторе |
Jamsannkosten Voima Oy, Финляндия | Торф, кора, древесная щепа, шлам, масло | 185 MВт, 252 тонн/ч водяного пара, 107 бар. 535 ͦC |
Katrinefors Kraftvärme, Швеция | Шлам, древесные остатки, отходы древесины | 36 MВт, 47 тонн/ч водяного пара, 80 бар. 480ͦ C |
Äänevoima Oy, Финляндия | Кора, древесная отходы, шлам, торф, масло | 157 MВт, 217 тонн/ч водяного пара, 105 бар. 535 º C |
Vamy Oy, Vattenfall Oy, Финляндия | Кора, вторичный шлам, природный газ, торф, древесные отходы, масло | 88 MВт, 130тонн/ч водяного пара, 115 бар. 525 ºC |
Modo Paper AB Husum, Швеция | Кора, шлам, масло | 87 MВт, 112 тонн/ч водяного пара, 60 бар. 450 ºC |
Sodra Cell AB Monsteras, Швеция | Кора, шлам, масло | 105 MВт, 133 тонн/ч водяного пара, 61 бар. 480 ºC |
Electrocieplowni Ostroleka, Польша | Кора, первичный и вторичный шлам | 35 MВт,47 тонн/ч водяного пара, 40 бар. 450 ºC |
Metsa-Serla Oy Simple, Финляндия | Торф, кора, шлам, масло | 113 MВт, 144 тонн/ч водяного пара, 115 бар. 525 ºC |
Oy Metsa - Botnia Kaskinen, Финляндия | Кора, шлам, масло | 96 MВт, 126 тонн/ч водяного пара, 85 бар. 500 ºC |
Из-за высокого содержания влаги и присутствия золы в большинстве шламов, процесс сжигания может стать энергетически невыгодным, и в этом случае может возникнуть необходимость использования дополнительного топлива.
|
Инсинерация в кипящем слое представляет собой метод эффективного термического окисления золы, отходов с высоким содержанием воды, методом проведения процессов с генерацией пара и (или) электроэнергии при одновременном снижении зависимости предприятий от затрат дорогого ископаемого топлива для выработки пара. Эти системы используются для утилизации не только шламов производств беленой целлюлозы или бумаги, но и для обработки твердых отходов на свалках. Сжигание в кипящем слое сейчас основной метод удаления отходов целлюлозо-бумажных производств [6-8,11]. Инсинерация отходов позволяет получить тепловую энергию. Так, например, на фабрике Katrinefors Kraftvärme (Швеция) проводится сжигание отходов производства бумаги в сочетании с древесными остатками. В технологии используется печь с кипящим слоем. Водяной пар, полученный сжиганием топлива с влажностью 45-55%, имеет температуру 480°C и давление 80 бар. Для поглощения окислов азота используют аммиак, а для поглощения диоксинов - активированный уголь. Энергия водяного пара используется для отопления жилых районов. [15]. На фабрике Äänevoima Oy Äänekoski используют котел КС фирмы (Foster Wheeler Energia Oy), Finland). Топливом являются кора, древесные отходы, шлам, торф, масло [16].
Диаграмма на рисунке 3.3 позволяет увидеть взаимосвязь между содержанием горючих органических соединений и содержанием золы и воды для отходов ЦБП (беленой целлюлозы, отходов после отбелки и сортировки, шлама после очистки сточных вод).
Содержание золы, вес. % |
Область самопроизвольной инсинерации |
Сухой шлам |
Содержание воды, вес.% |
Содержание органики, вес.% |
Рисунок. 3.3. Диаграмма состава шламов. [2]
На диаграмме указана область содержания органических веществ, золы и воды, для которой возможно горение без использования дополнительного топлива. [10].
|
Инсинерация этого вида отходов регулируется в Европе соответствующими нормативами, согласно которым все предприятия должны проводить сжигание при температуре не ниже 850º С в течение не менее 2 сек. В случае сжигания опасных отходов с содержанием хлора в органических галогенсодержащих соединениях более 1%, температура должна быть повышена до 1100º С хотя бы на 2 сек. Концентрации выбросов в атмосферу также регламентированы. Это касается тяжелых металлов, диоксинов и фуранов, окиси углерода, пыли, общего органического углерода (ТОС), хлористого водорода (HCl), SO2, NO, NO2. Например, предельно допустимая норма для диоксинов и фуранов составляет 0,1 нг/м3, для СО -50 мг/м3 в сутки.
Котлы с циркулирующим кипящим слоем (ЦКС) обладают рядом преимуществ по сравнению с котлами КС. К ним относятся тепло- и массоперенос и более длинное время пребывания, что позволяет достигнуть более высокую степень конверсии топлива. Конструкция этих печей позволяет провести переработку топлива с более широким диапазоном размеров частиц. Мощность этих котлов варьируется в широких пределах от (30 Мвт до 1000 МВт). В Приложении 3 описаны особенности печей с циркулирующим кипящим слоем [17]. Фирма Foster Wheeler Energia [18] разрабатывает котлы ЦКС. Топливом для них могут быть как уголь, так и смесь отходов ЦБП и угля. (Таблица 3.2.)
Таблица 3.2. Мощность фабрик и характер используемого топлива.
Фабрика, страна | Год запуска | Топливо | Мощность |
Yuen Foong Yu Paper, Naturfacturing Co. Ltd. (Yangzhou). Китай | 2007 | Битумный уголь, суббитумный уголь, автопокрышки, шлам | 50 МВт |
United Pulp Paper Corp. Ltd. (UPPC) Pampanga, Филиппины | 2006 | Уголь, шлам, отходы бум пром. | 35 MВт |
Malarenergi AB, KVV Vȁster, Швеция | 2001 | Древ отходы, торф, уголь | 59 МВт |
Тальтакуано, Чили | 1998 | Нефтяной кокс, | 67 МВт |
Lomellina Energia, Парона, Италия | 2007 | ТБО | 17 МВт |
При горении шлама с высоким содержанием коры, угля или другого топлива с высокой теплотворной способностью выделяется тепла больше, чем необходимо для испарения и нагревания. Для поддержания температуры в слое тепло надо отводить либо за счет уменьшения поверхности теплопередачи, либо другим способом. Это позволяет избежать "перегрев" печи. Печи ЦКС не требуют уменьшения теплопередачи за счет удаления части материала из горячего слоя. По сравнению с КС печи ЦКС позволяютиспользовать топливо с более высокой теплотворной способностью. Так, для КС предельная теплотворная способность топлива - от 7000 до 10500 кДж/кг, а для ЦКС- более 10500 кДж/кг. Эти печи можно использовать для сжигания биомассы и отходов её переработки [17].
Содержание воды в шламах имеет принципиальное значение, поэтому предварительно проводят обезвоживание шламов. Обычно в котлах с многоярусными топками (см. Приложение 3) термической переработке подвергают мокрый шлам, прошедший механическое обезвоживание, а печах с псевдоожиженным слоем сжигают как мокрый, так и полусухой с содержанием воды 41-65% [4,7,15]. В [7] описан котел КС, скомбинированный с многоярусными топками. Эта установка предназначена для сжигания шлама (в смеси с природным газом) и одновременного осушения его отходящими газами.
Пиролиз
В процессе пиролиза, который также называют деструктивной дистилляцией, органические отходы нагреваются в отсутствие кислорода с образованием смеси газообразного и жидкого топлива и твердого остатка (состоящего, в основном, из углерода). Эта технология состоит в разрушении органического материала в интервале температур 400 - 800ºС, используется непрямое нагревание в анаэробной атмосфере; этот процесс предусматривает образование летучих соединений. При нагревании реактора под высоким давлением происходит деструкция шлама, образуются газообразные соединения, жидкая смола, тяжелые и легкие масла. Для образования угля требуется длительное нагревание [4, 9,19].
Реакцию пиролиза можно представить следующим образом:
Органич. вещество + энергия → (углеродсодерж. вещество) + смолы + СО + СО2 + Н2 + Н2О + СН4 + СnНm.
Первичными продуктами могут быть жидкость, твердое углеродсодержащее вещество и газы в зависимости от вида и параметров процесса пиролиза, вторичными - энергия, топливо и химические продукты [2,4,19].
Жидкие продукты пиролиза вызывают большой интерес вследствие их высокой энергетической плотности и потенциальной возможности использования в качестве жидкого топлива. Жидкость, образующуюся в процессе пиролиза, часто называют "масла", "пиротопливо", "биотопливо" или "смолы". По данным [19,21,22] она близка по своему составу к биомассе, имеет чуть большую теплоту сгорания (20-25 МДж/кг) и состоит из смеси высокоокисленных углеводородов с содержанием воды до 20 %.
Твердым продуктом процесса пиролиза является углеродсодержащее вещество с теплотой сгорания QHP = 30 МДж/кг, выход которого может достигать 30-35 % массы сухого сырья при карбонизации и медленном пиролизе. Оно может использоваться в качестве топлива для бытового применения, а также для технологических нужд промышленности [19].
Газообразные продукты пиролиза представляют собой среднекалорийный газ с низшей теплотой сгорания (QHP = 15-22 МДж/нм3), (QHP -низшая теплота сгорания - теплота сгорания без учета теплоты конденсации водяных паров), а при частичной газификации низкокалорийный газ ((QHP = 4-8 МДж/нм3). Выход газообразного топлива может доходить до 70 % массы сухого сырья при высокотемпературном быстром пиролизе. Состав газа зависит от сырья и параметров процесса. Газообразные продукты характеризуются высоким содержанием углеводородов (в частности, метана) и его целесообразно использовать в самом процессе пиролиза для поддержания температуры процесса и сушки исходного сырья (Рис.3.4.).
Сжигание |
Пиролиз (550 ° С, без воздуха) |
Газы Н2,СО,СН4,С2Н2,С2Н4 |
Конденсация |
уголь |
жидкости |
пары |
Биомасса |
Каталитическая конверсия в водород |
нагревание |
Рис.3.3. Принципиальная схема процесса пиролиза
Рисунок 3.4. Схема пиролиза.
В составе продуктов пиролиза выявлено несколько сотен химических составляющих - полифенолов, левоглюкозан и гидроксиуксусный альдегид и др. Ряд соединений представляют высокую ценность, что может сделать выгодным извлечение отдельных химических продуктов по сравнению с топливом. Современные технологии пиролиза биомассы разделяют по характерным признакам: скорость нагрева (быстрый, медленный пиролиз); среда, в которой происходит пиролиз (вакуумный, гидропиролиз, метанопиролиз). Характеристики основных технологий пиролиза обобщены в таблице 3.3. [19,21].
При высоких скоростях нагрева (1000 -10000 °С/с) до 650 °С с последующим быстрым охлаждением достигается эффективная конденсация промежуточных жидких продуктов. Доля образующегося углеродсодержащего вещества минимальна, а при определенных обстоятельствах оно может вообще не образоваться. При высоких температурах процесса основным продуктом является газ. Пиролиз при высоких скоростях нагрева известен как быстрый, огневой или ультрапиролиз в соответствии со скоростью нагрева и временем пребывания процесса, хотя различия между этими видами пиролиза определены нечетко [19, 20] (Таблица 3.3.).
В настоящее время быстрый пиролиз утвердился как наиболее перспективная технология термохимической конверсии биомассы, особенно с точки зрения высокого выхода жидкого топлива и химических продуктов. Этот тип пиролиза используется для получения максимального количества либо газа, либо жидкости в соответствии с установленной температурой процесса. Низкотемпературный быстрый пиролиз позволяет максимизировать долю жидкого продукта.
Таблица 3.3. Характеристики быстрого и медленного пиролиза
Характеристики процесса | Быстрый пиролиз, низкие температуры | Быстрый пиролиз, высокие температуры | Медленный пиролиз | Карбонизация |
Время процесса | 1с | 1 с | 5-30 мин | часы, дни |
Размер сырья | малый | малый | средний | Большой |
Влажность сырья | очень низкая | очень низкая | низкая | Низкая |
Температура, °С | 450-600 | 650-900 | 500-700 | 400-600 |
Давление, кПа | 100 | 10-100 | 100 | 100 |
выход, % массы сухого сырья | до 30 | до 70 | до 40 | до 40 |
теплота сгорания, МДж/нм3 | 10-20 | 10-20 | 5-10 | 2-4 |
выход, % массы сухого сырья* | до 80 | ДО 20 | ДО 30 | до 20 |
теплота сгорания, МДж/кг | 23 | 23 | 23 | 10-20 |
Твердое вещество: | ||||
выход, % массы сухого сырья | до 15 | до 20 | 20-30 | 30-35 |
теплота сгорания, МДж/кг | 30 | 30 | 30 | 30 |
*Количество жидкости с учетом воды, образующейся в реакции, и влажности сырья.
Быстрый пиролиз является основным термохимическим способом прямого получения жидкости из биомассы и отходов. Технические проблемы, связанные с процессом быстрого пиролиза состоят в следующем: На процесс пиролиза влияет содержание воды в топливе. Считают, что содержание воды должно быть около
10% [21]. При более высоком СВ образуется много воды, а при более низких СВ есть риск образования пыли вместо масел, поэтому необходимо проводить предварительное осушение сырья. Для повышения выхода определенных химических продуктов и жидкого топлива применяется кислотная промывка [20-22]. Эффективность пиролиза зависит от размера частиц сырья. Большинство из технологий пиролиза предполагает переработку частиц размером около 2 мм, что связано с необходимостью быстрой теплопередачи через частицы. Это требование означает предварительное измельчение сырья [21]. Это дорогостоящее требование, поэтому реакторы, использующие частицы большего размера (как, ЦКС или абляционный), имеют значительные преимущества [19,20]. Типы реакторов приведены в Приложении 3. Исследование большого числа пиролизных реакторов различной конструкции показало, что многие из них отвечают основным требованиям технологии быстрого пиролиза. Лучшая конструкция пока не установлена [19].
Основное ограничение на конструкцию реактора накладывает требование высокого уровня теплопередачи. В реакторах КС тепло привносится в реактор с горячими твердыми частицами. Для абляционного реактора передача тепла в реактор осуществляется через стенку и является основным ограничением производительности. Теплопередача осуществляется либо при контакте газ - твердое тело, либо твердое тело - твердое тело. Последний вариант более эффективен и встречается в большинстве реакторов.
· Температура, при которой выход жидких продуктов максимальный, составляет 500 - 520 °С для большинства видов древесной биомассы.
· - Время пребывания продуктов пиролиза в паровой фазе играет важную роль при получении некоторых химических продуктов, но он менее важен при получении жидких топлив;
· - вторичный крекинг. Присутствие пара в течение длительного времени и высокие температуры вызывают, вторичный крекинг, первичных продуктов пиролиза, при этом снижается выход жидких топлив;
· - отделение углесодержащего вещества. Некоторое количество его неизбежно уносится из циклонов и накапливается в жидкости. Произвести отделение достаточно трудно;
· - В течение длительного времени главной трудностью был сбор жидкостей. Необходима тщательно продуманная конструкция установки, чтобы избежать забивания элементов оборудования тяжелыми конденсирующимися продуктами.
Технологии быстрого пиролиза классифицируются по типу реактора - пиролиз в кипящем слое; абляционный пиролиз; пиролиз в ЦКС; пиролиз в двух реакторах КС; пиролиз в потоке [38].
В таблице 3.4 отражено состояние современных технологий пиролиза, которые используются для получения пиротоплива.
В настоящее время во многих странах имеются пилотные установки небольшой мощности [19,22]. Cреди полномасштабных следует отметить следующие: канадская компания Resource Transforms International (RTI) разработала и запустила пиролизную установку с кипящим слоем производительностью 10 кг/ч. Производятся пиротопливо и химические продукты.
Таблица 3. 4. Технологии пиролиза [19,21].
Организация, страна | Технология | Производительность по исходному сырью, кг/ч |
Pasquali-ENEL, Италия GRES, Греция | ЦКС ЦКС | 25 10 |
Red Arrow-Ensvn. США | 2 реактора с КС | 1500 |
ENEL-Ensyn, Италия Ensyn, Канада | 2 реактора с КС КС | 1700 100 |
VTT, Финляндия | 2 реактора с КС | 20 1 |
Union Fenosa-университет Ватерлоо, Испания | КС | 200 |
Dynamotive-RTI, Канада | КС | 20 |
RTI, Канада | КС | 10 |
Университет Ватерлоо, Канада | КС | 3 |
Schelde-BTG-Twente, Нидерланды | абляционный конусный | 50 |
NREL, США | вихревой | 20 |
Астонский университет, Великобритания | абляционный пластинчатый КС | 5 2 |
Pyrovac, Канада | вакуумный пиролиз | 75 3500 |
В Испании под руководством Union Fenosa с 1993 г. действует пиролизная установка КС производительностью 200 кг/ч, использующая технологию, разработанную в университете Waterloo (Канада).
Исследованные виды сырья содержали древесину дуба, сосны, эвкалипта. Достигнутый выход пиротоплива - более 55 % [35]. Компания VTT (Финляндия) имеет действующую установку производительностью 20 кг/ч, состоящую из двух реакторов с КС [23]. В 1997 г. на установках компании Ensyn (Канада, Великобритания, США) было переработано 14.7 тыс. т сухой древесины и выработано 11 тыс. т пиротоплива, которое использовалось как котельное топливо для выработки тепла и электроэнергии, а также для производства химических продуктов.
Фирма BTG (Нидерланды) занимается разработкой технологии быстрого пиролиза биомассы в абляционном конусном реакторе. Создан реактор производительностью 50 кг/ч, и ведутся работы по созданию реактора производительностью 200 кг/ч. Организация NREL (США) с 1980 г. разрабатывает технологию абляционного вихревого пиролизного реактора, созданы реакторы производительностью 20 кг/ч и 30 кг/ч [19,22].
Фирма Pyrovac International Inc. предлагает технологию вакуумного пиролиза в реакторе с горизонтальным движущимся слоем. Процесс предназначен для получения пиротоплива и химических продуктов в результате переработки биомассы и отходов. Создана демонстрационная установка производительностью около 3 т/ч [22].
Наиболее совершенным является RTP-npouecc (Rapid Thermal Processing) быстрого пиролиза биомассы (собственность компании Ensyn Technologies Inc. (Канада)); он представляет собой технологию термохимической конверсии биомассы с высоким выходом легких несмолянистых жидкостей. В качестве сырья могут использоваться древесина, древесные отходы, лигнин, целлюлоза, отходы сельского хозяйства, сырая нефть, тяжелые мазуты, тяжелые продукты перегонки нефти, асфальт, битум, изношенные автомобильные шины, бумажные отходы, отстой сточных вод [19]. RTP-технология с реактором ЦКС установлена в Висконсине (США) для обеспечения пиротопливом коммунальных предприятий города. В 1993 г. компанией Red Arrow была запущена вторая RTP-установка, перерабатывающая до 60 т сырья в день. На установке производится пиротопливо для котлов, химически чистый уголь и пищевые химические продукты. В настоящее время компания Ensyn Technologies Inc. является ведущей в области разработки реакторов быстрого пиролиза для получения жидкого топлива и химических продуктов с производительностью от 1 до 110 т сырья в сутки. В Европе первая RTP-установка введена в действие в Umbria (Италия) при сотрудничестве с компанией ENEL [24]. В промышленном масштабе типичный выход пиротоплива при переработке твердой древесины влажностью 10 % составляет около 74 % (мас.).
С экологической точки зрения процесс пиролиза обладает лучшими показателями по сравнению с инсинерацией. Количество отработанных газов, подвергаемых очистке, намного меньше, чем при сжигании отходов. Объем твердого остатка, получаемого после пиролиза, может быть значительно уменьшен. Его можно использовать в промышленности (сажа, активированный уголь, и др.). Таким образом, некоторые схемы пиролиза могут быть безотходными [4,5,12,24].
Высокотемпературный пиролиз по сравнению с другими методами имеет ряд преимуществ: при нем происходит более интенсивное преобразование исходного продукта; скорость реакций возрастает с экспоненциальным увеличением температуры, в то время, как тепловые потери возрастают линейно; увеличивается время теплового воздействия на отходы; происходит более полный выход летучих веществ; сокращается количество остатка после окончания процесса [21].
Безокислительный пиролиз - новое направление в развитии термических технологий. Преимущества этого метода заключаются в возможности получения технологического газа, а в ряде случаев - минерального продукта (сорбента). Он позволяет резко сократить затраты на систему очистки газов за счет снижения в 3-4 раза объема очищенного газа, а также снизить количество твердого остатка. Полученный газ можно использовать для технологических и бытовых целей. Метод экологически безопасен.
Использование мощного СВЧ - нагрева для этой технологии может снизить энергопотребление на единицу объема перерабатываемого вещества, что дает возможность вместе с плазменной технологией разрабатывать передвижные комплексы для переработки токсичных отходов. Считают, что пиролиз - один из наименее требовательных к исходному сырью и один из наиболее доступных в финансовом отношении методов [21].
Паровой крекинг
Паровой крекинг (Steam reforming) или метод паротермической деструкции основывается на инновационной технологии импульсного возгорания, который осуществляется в реакторе парового крекинга. В системе с импульсным возгоранием и непрямым нагреванием псевдоожиженного слоя используется реактор с трубчатым нагревателем, находящимся непосредственно в слое, который является частью импульсной камеры сгорания. Образующиеся газы играют роль топлива. Импульсная камера сгорания позволяет достигнуть высокой скорости теплообмена, что способствует эффективному протеканию реакций в газовой фазе. Контактируя с паром и дисперсным материалом, отходы нагреваются и расплавляются. Под действием тепла происходит разложение отходов с образованием газообразных продуктов, которые смешиваются с потоком пара и увлекаются им на выход из реактора. Смесь газообразных продуктов и водяного пара подается в холодильник. В результате охлаждения смеси образуется конденсат и несконденсировавшийся газ. В этих системах удается высвободить высокие количества энергии и таким образом достигнуть более полного сгорания. Эта технология предполагает не только высокую скорость переноса энергии, но и низкие концентрации NOx. Кроме того, паротермическая деструкция протекает при низких температурах (500-600ºС), что снижает концентрацию образующихся летучих соединений и испарение токсичных металлов, остающихся в горючем остатке [25-27].
Преимуществом этой системы является деструкция диоксинов и наличие препятствий для их образования. Отмечена высокая эффективность деструкции диоксинов (до 97,5%). Это объясняют присутствием соединений кальция в псевдоожиженном слое. Адсорбция НCl, образующегося при газификации, а также отсутствие кислорода в образовавшейся восстановительной среде позволяет избежать процессов образования диоксинов при сжигании отходов, содержащих хлорорганические соединения [11,26].
Высокая экономичность этого процесса достигается за счет рециркуляции теплоносителя, а также за счет получения ценного химического сырья. Характерное для процесса отсутствие вредных выбросов в окружающую среду обусловлено растворением вредных веществ в конденсате, что позволяет обезвредить их в растворе. Использование водяного пара обеспечивает высокую взрыво- и пожаробезопасность процесса [1,28] Эта технология используется для обработки старого шлама, и в настоящее время рассматривается как вариант технологии для переработки отходов ЦБП.
О кисление в жидкой фазе
Окисление в жидкой фазе (Wet oxidation (WO)) - процесс, при котором органические загрязнители, находящиеся в жидком или твердом состоянии, экстрагируются в водную фазу. Процесс протекает в водной фазе при температуре 150-330º С и давлении от 1 до 22 МРа с использованием чистого или атмосферного кислорода [29-31]. По своему смыслу этот метод относится к термическому варианту АОР [30]. В нем сочетаются основные принципы физических, химических, термических и биологических методов очистки.
Метод известен более 60 лет. В обычной коммерческой установке имеется барботажный реактор, воздух поступает в вертикальную колонну, заполненную горячей жидкостью, находящейся под давлением. Сточные воды поступают снизу реактора, вверху собираются обработанные стоки. Разделение жидкости и газа проводится в сепараторе. Тепло, выделяющееся при окислении, используется для поддержания температуры процесса [30].
Так как процесс представляет собой прямое окисление, проблема токсичности для него не существует. Вода играет роль среды для растворенного кислорода, реагирующего с органическими соединениями и другими окисляемыми компонентами. Вода является неотъемлемой частью процесса, действующей одновременно как катализатор, и как гидролизующий реагент. Предполагается, что свободные радикалы, образовавшиеся в системе, ответственны за протекающие процессы окисления. Для ускорения реакции могут быть использованы перекись водорода, гомогенные или гетерогенные катализаторы, содержащие железо или медь [29,30,32]. Использование катализаторов позволяет проводить процесс при более низкой температуре.
Рис. 3.5. Химические превращения в процессе окисления
в жидкой фазе.
Жидкофазное окисление сопровождается образованием карбоновых кислот, главным образом, уксусной, муравьиной и щавелевой. Эти кислоты - биологически легко деградируют и могут быть удалены с помощью последующей недорогой биологической обработки. Конечные продукты - СО2 и вода. Схема, приведенная на рисунке 3.5., иллюстрирует это.
В газовой фазе обьразуются окислы азота и серы (NOx и SOx) газе могут также содержаться альдегиды, кетоны и спирты, которые легко удаляются при термической обработке. По данным [33] использование этой технологии обеспечивает снижение ХПК; оно составляет 80-85%.
Жидкофазное окисление сопровождается образованием карбоновых кислот, главным образом, уксусной, муравьиной и щавелевой. Эти кислоты - биологически легко деградируют и могут быть удалены с помощью последующей недорогой биологической обработки. Конечные продукты - СО2 и вода. Схема, приведенная н
|
|
Автоматическое растормаживание колес: Тормозные устройства колес предназначены для уменьшения длины пробега и улучшения маневрирования ВС при...
История развития хранилищ для нефти: Первые склады нефти появились в XVII веке. Они представляли собой землянные ямы-амбара глубиной 4…5 м...
Биохимия спиртового брожения: Основу технологии получения пива составляет спиртовое брожение, - при котором сахар превращается...
Индивидуальные и групповые автопоилки: для животных. Схемы и конструкции...
© cyberpedia.su 2017-2024 - Не является автором материалов. Исключительное право сохранено за автором текста.
Если вы не хотите, чтобы данный материал был у нас на сайте, перейдите по ссылке: Нарушение авторских прав. Мы поможем в написании вашей работы!