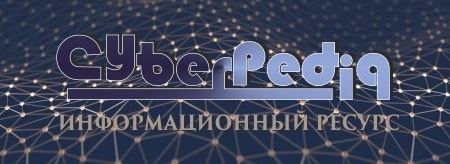
Папиллярные узоры пальцев рук - маркер спортивных способностей: дерматоглифические признаки формируются на 3-5 месяце беременности, не изменяются в течение жизни...
Двойное оплодотворение у цветковых растений: Оплодотворение - это процесс слияния мужской и женской половых клеток с образованием зиготы...
Топ:
Устройство и оснащение процедурного кабинета: Решающая роль в обеспечении правильного лечения пациентов отводится процедурной медсестре...
Процедура выполнения команд. Рабочий цикл процессора: Функционирование процессора в основном состоит из повторяющихся рабочих циклов, каждый из которых соответствует...
Характеристика АТП и сварочно-жестяницкого участка: Транспорт в настоящее время является одной из важнейших отраслей народного хозяйства...
Интересное:
Отражение на счетах бухгалтерского учета процесса приобретения: Процесс заготовления представляет систему экономических событий, включающих приобретение организацией у поставщиков сырья...
Уполаживание и террасирование склонов: Если глубина оврага более 5 м необходимо устройство берм. Варианты использования оврагов для градостроительных целей...
Берегоукрепление оползневых склонов: На прибрежных склонах основной причиной развития оползневых процессов является подмыв водами рек естественных склонов...
Дисциплины:
![]() |
![]() |
5.00
из
|
Заказать работу |
Содержание книги
Поиск на нашем сайте
|
|
Использование моделей управления запасами в японской промышленности нельзя воспринимать в отрыве от исторических фактов, национальных особенностей, комплексности различных мер по рационализации промышленности Японии.
Следует отметить следующие факты – очень низкое качество японских товаров в 50-ые годы; отсутствие собственных материальных ресурсов, что воспитывает весьма бережное отношение к ним; разразившийся в 70-ые годы нефтяной кризис поставил перед японской промышленностью казалось бы, неразрешимые задачи. Поэтому в японской промышленности успешно используются и развиваются совместно три направления:
1) всемерная экономия ресурсов;
2) борьба за качество;
3) рациональное управление запасами.
Отметим, что второе и третье направления являются следствием первого.
В ходе реализации третьего направления на предприятиях Японии внедрялась система «точно в срок» («точно вовремя», JIT, just in time). Согласно этой концепции закупки материальных ресурсов должны быть согласованы с производственными потребностями предприятия. В идеальном случае сырье и материалы должны быть доставлены в определенное подразделение, минуя склад, именно в тот момент, когда они там нужны (не раньше и не позже), что сводит запасы к нулю.
В качестве примера можно привести несколько инструментов управления системы «точно в срок»:
- ANDON (андон) – система управления, в которой путем световой сигнализации можно отслеживать ход выполнения производственного процесса и при необходимости вмешиваться в него (рис. 5.7);
Рис. 5.7. Примеры реализации системы управления (андон) на производственных
участках (а, б) и в составе технологического оборудования (в)
|
- JIDOHKA (дзидока, автономизация) – система автоматической остановки всей линии при обнаружении проблем (неполадок, брака и др.);
- KANBAN (канбан) – система организации производства и снабжения.
Система канбан была разработана и впервые в мире реализована японской фирмой «Тойота». Теоретической основой канбан являются идеи одного из основоположников научного менеджмента, американского ученого Ф. Тейлора (1856 – 1915) и основоположника массового производства в автомобильной промышленности Г. Форда (1863 – 1947).
Слово «канбан» означает «сигнал». Чаще всего это карточка или табличка, прикрепляемая к контейнеру с материалами, которая координирует подачу и отгрузку материалов на производственной линии. Может иметь форму разметки на полу, полках и столах. В 1959 г. фирма «Тойота» начала эксперименты с системой канбан; в 1962 г. начат процесс перевода всего производства на принципы канбан.
В основе организации производства фирмы «Тойота» лежит годовой план производства и сбыта автомобилей, на базе которого составляются месячные и оперативные планы среднесуточного выпуска на каждом участке. Суточные графики производства составляются только для главного сборочного конвейера. Для цехов и участков, обслуживающих главный конвейер, графики производства не составляются (им устанавливаются лишь ориентировочные месячные объемы производства). В этом – одно из важнейших отличий канбан. Другими словами, цехи и участки не имеют жесткого плана и графика, они организуют свою работу на основе заказа цеха-потребителя. Каждый по предыдущей технологической цепочке цех может знать, что он будет производить, только после того, как его готовая продукция фактически пошла в последующую обработку.
Система канбан предполагает специфический подход к выбору и оцениванию поставщиков, основанный на работе с узким кругом поставщиков, отбираемых по их способности гарантировать поставку «точно вовремя» комплектующих изделий высокого качества. При этом количество поставщиков сокращается в два и более раз, а с оставшимися поставщиками устанавливаются длительные хозяйственные связи. Головная фирма оказывает поставщикам различную помощь, направленную в первую очередь на повышение качества поставляемой ими продукции.
|
Практическое применение системы канбан дает японским машиностроительным фирмам значительный эффект. Многие российские и западные специалисты считают, что высокая конкурентоспособность японской промышленной продукции в первую очередь обусловлена применением идей и методов системы канбан. Система канбан используется такими известными фирмами, как «Дженерал моторс» (США), «Рено» (Франция) и многими др. Анализ опыта ряда фирм Западной Европы, внедривших систему канбан, показывает, что она дает возможность уменьшить запасы производственные на 50 %, запасы товарные – на 8 % при значительном ускорении оборачиваемости оборотных средств и повышении качества продукции. Однако применение этого метода дает наилучшие результаты в тех странах, где сравнительно небольшие расстояния и хорошие дороги (Япония, Западная Европа).
Таким образом, введение системы «точно в срок» позволило на первых этапах уменьшить складские и финансовые потери. Развитие этой системы в дальнейшем позволило перейти к уменьшению размеров партии товаров, запускаемых изделий. Это даёт ряд преимуществ:
1) уменьшаются затраты на хранение;
2) уменьшаются стоимость брака;
3) постоянно улучшается качество и надежность процессов;
4) растёт качество, т. к. уменьшается вероятность появления бракованной продукции в меньших партиях. Растёт ответственность за передачу на очередное рабочее место (не на склад) качественной продукции;
5) растёт производительность из-за уменьшения количества бракованной продукции, из-за соревновательности и расширения узких мест (кружки качества), из-за разработок быстропереналаживаемой оснастки. Японским инженером Сигео Синго была разработана концепция быстрой переналадки SMED («Single Minute Exchange of Die», т. е. «Смена инструмента за время менее 10 минут»). Эта концепция произвела революцию в подходах к переналадке и переоснастке. Утверждается и доказывается на практике, что смена любого инструмента и переналадка могут быть произведены всего за несколько минут или даже секунд, «в одно касание».
|
6) из-за роста заинтересованности в конечных результатах труда большинство проблем решаются на рабочих местах, участках; проще становится планирование, документация; уменьшается объем контроля;
7) растет гибкость производства, что является одной из главных положительных характеристик рыночной экономики.
Опыт использования японской системы организации производства в других странах показывает, что не только национальные особенности играют роль в этой системе. Повсеместно указывается на рост заинтересованности персонала, выпуск более качественной продукции, снижение издержек.
Теория принятия решений
Теория принятия оптимальных решений представляет собой совокупность математических и численных методов, ориентированных на нахождение наилучших вариантов из множества альтернатив и позволяющих избежать их полного перебора. Ввиду того, что размерность практических задач, как правило, достаточно велика, а расчеты в соответствии с алгоритмами оптимизации требуют значительных затрат времени, то методы принятия оптимальных решений главным образом ориентированы на реализацию их с помощью ЭВМ.
Можно выделить следующие научно-технические предпосылки становления «Теории принятия решений»:
- удорожание «цены ошибки». Чем сложнее, дороже, масштабнее планируемое мероприятие, тем менее допустимы в нем «волевые» решения и тем важнее становятся научные методы, позволяющие заранее оценить последствия каждого решения, заранее исключить недопустимые варианты и рекомендовать наиболее удачные;
- ускорение научно-технической революции техники и технологии. Жизненный цикл технического изделия сократился настолько, что «опыт» не успевал накапливаться и требовалось применение более развитого математического аппарата в проектировании;
- развитие ЭВМ. Размерность и сложность реальных инженерных задач не позволяли использовать аналитические методы.
|
|
Археология об основании Рима: Новые раскопки проясняют и такой острый дискуссионный вопрос, как дата самого возникновения Рима...
История развития хранилищ для нефти: Первые склады нефти появились в XVII веке. Они представляли собой землянные ямы-амбара глубиной 4…5 м...
Семя – орган полового размножения и расселения растений: наружи у семян имеется плотный покров – кожура...
Папиллярные узоры пальцев рук - маркер спортивных способностей: дерматоглифические признаки формируются на 3-5 месяце беременности, не изменяются в течение жизни...
© cyberpedia.su 2017-2024 - Не является автором материалов. Исключительное право сохранено за автором текста.
Если вы не хотите, чтобы данный материал был у нас на сайте, перейдите по ссылке: Нарушение авторских прав. Мы поможем в написании вашей работы!