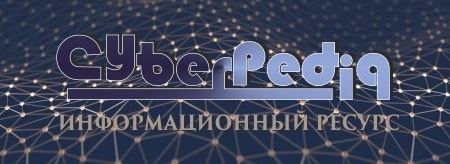
Кормораздатчик мобильный электрифицированный: схема и процесс работы устройства...
Адаптации растений и животных к жизни в горах: Большое значение для жизни организмов в горах имеют степень расчленения, крутизна и экспозиционные различия склонов...
Топ:
Комплексной системы оценки состояния охраны труда на производственном объекте (КСОТ-П): Цели и задачи Комплексной системы оценки состояния охраны труда и определению факторов рисков по охране труда...
Устройство и оснащение процедурного кабинета: Решающая роль в обеспечении правильного лечения пациентов отводится процедурной медсестре...
Основы обеспечения единства измерений: Обеспечение единства измерений - деятельность метрологических служб, направленная на достижение...
Интересное:
Лечение прогрессирующих форм рака: Одним из наиболее важных достижений экспериментальной химиотерапии опухолей, начатой в 60-х и реализованной в 70-х годах, является...
Аура как энергетическое поле: многослойную ауру человека можно представить себе подобным...
Финансовый рынок и его значение в управлении денежными потоками на современном этапе: любому предприятию для расширения производства и увеличения прибыли нужны...
Дисциплины:
![]() |
![]() |
5.00
из
|
Заказать работу |
Содержание книги
Поиск на нашем сайте
|
|
Специфическим случаем кристаллизации паяных швов является изотермическая кристаллизация, происходящая в процессе выдержки при температуре выше температуры солидуса припоя. Очевидно, что такая кристаллизация может быть результатом удаления из расплавленного припоя легкоплавких компонентов или компонентов-депрессантов (снижающих температуру его плавления), которое может происходить в результате следующих процессов: диффузии в паяемые металлы, испарения в окружающую среду или связывания в тугоплавкие интерметаллиды. В принципе возможно сочетание всех трех процессов, однако, на практике наиболее часто применяется и изучен первый. Осуществление диффузионного отвода легкоплавкого компонента или компонента-депрессанта из жидкого припоя в паяемый металл в объеме, приводящего к его изотермической кристаллизации на практике возможно благодаря тому, что припой в виде тонкой прослойки контактирует с относительно большими поверхностями паяемого металла. При этом необходимо наличие растворимости компонента-депрессанта в основном металле.
Движущей силой изотермической кристаллизации является развитие в системе основной металл – жидкий припой процессов и превращений, направленных к установлению такого фазового состава, при котором свободная энергия системы будет минимальной. Для простейшей системы, когда паяемый металл и припой являются чистыми металлами и взаимодействуют с образованием неограниченных растворов в твердом и жидком состоянии (рис. 4.19), при температуре Tп, будут развиваться следующие процессы и превращения. При контакте жидкого металла-припоя А с твердым металлом В будут происходить диффузионные процессы, приближающие жидкую и твердую фазы к равновесным для этой температуры концентрациям и
, определяемым точками пересечения каноды с линиями ликвидус и солидус.
Рис. 4.19. Равновесные составы жидкой и твердой
фаз в системе
металлов А-В для Т=Тп.
Так как скорость диффузии в жидких металлах на 2-3 порядка больше, чем в твердых, то на начальном этапе будет преобладать процесс растворения основного металла в припое. При этом толщина жидкой прослойки будет увеличиваться, а межфазная граница сместится в сторону основного металла. Этот процесс завершится, когда состав жидкой фазы станет близким к равновесному во всем ее объеме, и из-за малой толщины жидкой прослойки и больших значений скорости диффузии длится несколько секунд. В дальнейшем, при неизменном в среднем составе жидкой фазы, преобладающим процессом в рассматриваемой системе станет диффузия металла-припоя А в основной металл В. Из-за малой скорости диффузии в твердых металлах и сравнительно больших сечений паяемых деталей равновесная концентрация твердой фазы
достигается лишь на межфазной границе, при этом происходит постоянная диффузия металла припоя А от межфазной границы вглубь основного металла В. Это приводит к снижению его концентрации на межфазной границе ниже равновесного значения
, восстановление которого происходит за счет диффузии в поверхностный слой основного металла В дополнительного количества металла-припоя А. При этом пограничный слой жидкой фазы становится перенасыщенным основным металлом В, что приводит к его кристаллизации, причем состав кристаллизующейся фазы соответствует твердому раствору равновесного состава
, а межфазная граница смещается в сторону жидкой фазы. Поскольку диффузионный отвод металла-припоя А от межфазной границы вглубь металла В продолжается непрерывно, непрерывно протекают и последующие процессы, сопровождающиеся кристаллизацией приграничного слоя жидкой фазы и движением межфазной границы к центру паяного шва, которые заканчиваются полным исчезновением жидкой фазы. Распределение концентрации металла-припоя в зоне паяного соединения в различные моменты изотермической кристаллизации схематически показаны на рисунке 4.20. После завершения изотермической кристаллизации, если продолжать выдержку при Тп, будут происходить процессы выравнивающей диффузии сопровождающиеся снижением концентрации металла припоя в центре паяного шва и увеличением глубины диффузионной зоны в основном металле.
![]() | Рис. 4.20. Распределение концентрации металла А (припоя) в зоне паяного шва: 1 – в начальный момент диффузионной пайки, t=0; 2 – в процессе диффузионной выдержки, 0<t<tи.к.; 3 – в момент завершения диффузионной пайки, t=tи.к.. h/2 – координата центра паяльного зазора, y(t) – положение межфазной границы в момент времени t. |
Способ пайки, при котором осуществляется изотермическая кристаллизация паяного шва, получил название диффузионного. Он позволяет получать паяные швы с более равновесной структурой, повышать температуру распайки и, соответственно, жаропрочность; за счет уменьшения химической неоднородности, в том числе за счет устранения интерметаллидных прослоек, повышать коррозионную стойкость, прочность и пластичность. На практике нужно уметь определять время, необходимое для завершения изотермической кристаллизации, влияющие на него факторы.
Процесс изотермической кристаллизации контролируется диффузией атомов металла-припоя (или компонента-депрессанта) в паяемый металл и может быть количественно описан с помощью известных уравнений диффузии. Для рассматриваемого выше простейшего случая взаимодействия паяемый металл – металл-припой при условии постоянства коэффициента диффузии, её объемного характера и плоского фронта кристаллизации распределение металла – припоя в зоне твердого раствора, образовавшегося при изотермической кристаллизации описывается системой уравнений:
(3)
где с(x,t) – концентрация диффундирующего элемента на расстоянии x от межфазной границы в момент времени t;
D – коэффициент диффузии;
Dс = –
в долях по массе;
y – расстояние межфазной границы от её исходного положения в момент времени t;
при начальных и граничных условиях:
– при x=0 и t=0, с(0,0) = ;
– на перемещающейся границе твердой и жидкой фаз в любой момент времени с[y(t),t] = .
Решением этой системы уравнений является уравнение
(4),
где b – безразмерный коэффициент, определяемый соотношением:
(5)
(6)
Ограничиваясь первым членом бесконечной суммы, получаем:
(7)
Авторами [2] приводится номограмма (рис. 21) для определения коэффициента b по данным диаграммы фазового равновесия системы: паяемый металл – металл-припой (депрессант).
![]() | Рис. 4.21. Номограмма для определения величины коэффициента b. |
Из уравнения (4) следует уравнение для времени изотермической кристаллизации tи.к.:
(8),
где h – исходная толщина жидкой прослойки.
Время изотермической кристаллизации зависит от толщины жидкой прослойки, коэффициента диффузии D и соотношения , которые, в свою очередь, зависят от температуры пайки.
Таким образом, основными параметрами процесса диффузионной пайки является ширина паяного шва, температура пайки и время выдержки. Ширина паяного шва регулируется величиной исходного зазора и может быть уменьшена путём приложения давления. Оптимальным вариантом является сочетание диффузионной пайки с контактно-реактивной, которая осуществляется в условиях сжимающего давления и при которой толщина жидкой фазы может быть выбрана минимальной, достаточной для заполнения зазора, определяемого в этом случае чистотой обработки паяемых поверхностей. Так, при пайке плоских трубок пластинчато-ребристых теплообменников из технического титана ВТ1-0 с гофрированным наполнителем, которые изготавливаются из фольги толщиной 0,2 и 0,1 мм соответственно, качественные паяные соединения обеспечиваются при толщине промежуточного покрытия из меди 8-11 мкм, температуре пайки 960 °С и времени изотермической выдержки 60 мин. Толщина жидкой прослойки при этом составляет 21-33 мкм [3]. Следует отметить, что такое время изотермической выдержки существенно больше времени изотермической кристаллизации капиллярной части шва и обусловлено временем изотермической кристаллизации галтельных участков. При этом в капиллярной части шва после завершения изотермической кристаллизации идет процесс выравнивающей диффузии, в результате которого максимальное содержание меди в центре шва снижается до 4–5 %,
В практике применения диффузионной пайки различных материалов редко процесс завершается окончанием кристаллизации жидкой фазы припоя. Количественная оценка времени изотермической кристаллизации, учитывая малые (0,05-0,2 мм) величины капиллярных зазоров и диффузионные процессы в жидкой фазе, выполненная по формуле (8), показывает, что порядок этих величин составляет единицы-десятки секунд. Дальнейшее изменение состава и структуры паяных швов контролируется диффузией в твердой фазе. Целью такой выдержки при температуре пайки является уменьшение химической неоднородности паяных соединений, повышение прочности, увеличение температуры распая и т.д. Расчетную оценку времени диффузионной обработки для получения заданной концентрации компонентов припоя в паяном шве можно сделать используя известные решения уравнений диффузии (рис. 4….).
Рис. 4…. Распределение компонентов припоя при диффузионной обработке в твердом состоянии,
h – ширина паяного шва после завершения процесса кристаллизации.
Для малых значений толщины слоя припоя после его кристаллизации – h и постоянном значении коэффициента диффузии во всем интервале концентраций, распределение концентрации описывается уравнением:
где С0 – концентрация компонента припоя в паяном шве в момент
времени t=0;
х – координата точки с концентрацией С;
Концентрация в центре паяного шва при x=0 и ее изменение во времени, представляющее наибольший интерес, определяется выражением:
Приведенная методика может быть использована для приближенных расчетов нестационарных диффузионных процессов при капиллярной и диффузионной пайке металлических материалов.
Для сокращения времени выдержки при диффузионной пайке можно использовать обработку паяемых поверхностей с целью создания в поверхностном слое микродефектов, ускоряющих диффузию, или термоциклирование в процессе выдержки, также ускоряющее диффузионные процессы. Эти способы предложены для контактно-реактивной диффузионной паки изделий из магниевых сплавов с использованием промежуточной прослойки из серебра, которая наносится на паяемую поверхность ионным напылением [4].
4.4. Особенности формирования структуры при кристаллизации
паяных швов разнородных металлов
Одним из преимуществ пайки, как способа создания неразъемных соединений, является возможность создания конструкций из разнородных материалов. В таких конструкциях наиболее полном используются физико-химические и механические свойства материалов. В практике паяльного производства могут соединяться пайкой разнородные материалы (Ti-Al, Fe-Al, Cu-W и другие) или материалы одной металлической основы различающиеся легирующими компонентами или их концентрацией.
Так как после заполнения соединительного зазора жидким припоем в контакте с ним находятся материалы различного состава, взаимодействие их через жидкую фазу имеет свои особенности.
В результате различной растворимости соединяемых металлов или в случае растворимости одного и нерастворимости второго, в жидком припое образуется градиент концентрации , при котором у поверхности соединяемых металлов А и С она достигает равновесных для температуры пайки значений
и
соответственно. В результате процесса выравнивающей диффузии атомы металла с большей растворимостью переносятся и осаждаются на межфазной поверхности металла с меньшим значением растворимости, взаимодействуя с ним в соответствии с диаграммой фазового равновесия А-С. При этом обе межфазные границы смещаются в сторону металла с большим значением растворимости: одна – за счет растворения, другая – за счет осаждения.
Рис. 4… Линии ликвидуса разнородных материалов А и С при взаимодействии
с припоем В при температуре пайки ТП.
В – основа припоя,
А(В) – кривая растворимости паяемого металла А в припое В,
С(В) – кривая растворимости паяемого металла С в припое В,
Примером могут служить соединения Fe с Mo и W при использовании в качестве припоя меди (рис. 4.24, 4.25). На поверхности Mo и W, которые при температуре пайки 1225 °С в меди не растворяются, осаждается слой Fe,причем на границе Fe-Mo и Fe-W образуются тонкие слои интермметаллидов Fe7Mo6 и Fe7W6 соответственно, а в образовавшемся слое Fe содержится 10-15% Mo и около 3% Cu для сочетания Fe-Mo, а для сочетания Fe-W кроме интерметаллида Fe7W6 наблюдаются два слоя – наружный с 10-14% Cu, 1-2% W и внутренний с 9% Cu, 3-9% W.
Рис. 4.24. Массоперенос в микроструктуре паяного шва Fe с W, припой – медь, Тп=1125ºС, время выдержки 30 мин. | Рис. 4.25. Массоперенос в микроструктуре паяного шва Fe с Mo, припой – медь, Тп=1120ºС, время выдержки 5 мин. |
![]() |
|
|
Индивидуальные очистные сооружения: К классу индивидуальных очистных сооружений относят сооружения, пропускная способность которых...
Биохимия спиртового брожения: Основу технологии получения пива составляет спиртовое брожение, - при котором сахар превращается...
Общие условия выбора системы дренажа: Система дренажа выбирается в зависимости от характера защищаемого...
Поперечные профили набережных и береговой полосы: На городских территориях берегоукрепление проектируют с учетом технических и экономических требований, но особое значение придают эстетическим...
© cyberpedia.su 2017-2025 - Не является автором материалов. Исключительное право сохранено за автором текста.
Если вы не хотите, чтобы данный материал был у нас на сайте, перейдите по ссылке: Нарушение авторских прав. Мы поможем в написании вашей работы!