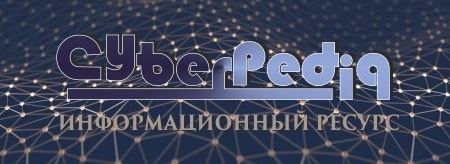
История развития пистолетов-пулеметов: Предпосылкой для возникновения пистолетов-пулеметов послужила давняя тенденция тяготения винтовок...
Биохимия спиртового брожения: Основу технологии получения пива составляет спиртовое брожение, - при котором сахар превращается...
Топ:
Эволюция кровеносной системы позвоночных животных: Биологическая эволюция – необратимый процесс исторического развития живой природы...
История развития методов оптимизации: теорема Куна-Таккера, метод Лагранжа, роль выпуклости в оптимизации...
Когда производится ограждение поезда, остановившегося на перегоне: Во всех случаях немедленно должно быть ограждено место препятствия для движения поездов на смежном пути двухпутного...
Интересное:
Финансовый рынок и его значение в управлении денежными потоками на современном этапе: любому предприятию для расширения производства и увеличения прибыли нужны...
Национальное богатство страны и его составляющие: для оценки элементов национального богатства используются...
Принципы управления денежными потоками: одним из методов контроля за состоянием денежной наличности является...
Дисциплины:
![]() |
![]() |
5.00
из
|
Заказать работу |
Содержание книги
Поиск на нашем сайте
|
|
ПАЙКА АЛЮМИНИЕВЫХ СПЛАВОВ
Алюминий сочетает весьма ценный комплекс свойств: малую плотность, высокие теплопроводность и электрическую проводимость, высокую пластичность и высокую коррозионную стойкость. Он легко поддается ковке, штамповке, прокатке, волочению.
Обладая большим сродством к кислороду, алюминий на воздухе покрывается тонкой, но очень прочной плёнкой оксида алюминия Al2O3, защищающей металл от дальнейшего окисления и обусловливающей его высокие антикоррозионные свойства. Прочность окисной плёнки и защитное действие её сильно убывают в присутствии примесей ртути, натрия, магния, меди и др.
Трудности пайки алюминиевых сплавов связаны прежде всего с физико-химическими свойствами алюминия и высокой стойкостью его оксида. Пайка алюминия имеет следующие особенности:
- поверхность алюминия всегда покрыта тугоплавким (Тпл=2045°С), химически и термически стойким оксидом, который препятствует контакту расплавленного жидкого припоя с поверхностью алюминия;
- алюминий имеет сравнительно низкий отрицательный электродный потенциал, что снижает коррозионную стойкость паяного соединения при воздействии окружающей среды;
- склонность алюминия и его сплавов к нежелательным металлургическим взаимодействиям при повышенных температурах (оплавление границ зерен, значительная химическая эрозия в расплавах припоев, образование хрупких интерметаллидов и т.д.);
- алюминий обладает высокой теплоемкостью – теплоемкость алюминия в интервале температур 0-300°С составляет 0,953 кДж/кг×°С, т. е. в 2,5 раза выше теплоемкости меди в этом интервале температур, поэтому при пайке изделий из алюминия требуются достаточно мощные источники теплоты для нагрева изделий, что приводит к образованию широкой зоны разогрева и значительным деформациям паяемых изделий;
|
- алюминий и его сплавы имеют большой относительный коэффициент линейного расширения, который в интервале температур 20-400°С равен 26,5×10-6°С-1 (для железа 13,9×10-6°С-1 ), это вызывает значительную деформации изделия при нагреве под пайку и накладывает дополнительные трудности при получении точных размеров, так как оснастку для пайки алюминиевых сплавов обычно выполняют из коррозионно-стойких аустенитных сталей или нихромовых сплавов, коэффициент линейного расширения которых существенно отличается от коэффициента линейного расширения алюминиевых сплавов;
- флюсы, применяемые при пайке алюминия и его сплавов, в большинстве своем вызывают активную коррозию паяемых материалов, поэтому остатки их должны быть тщательно удалены после пайки;
- многие припои, обеспечивающие высокую механическую прочность паяных соединений из алюминиевых сплавов и коррозионную стойкость, являются сплавами на основе алюминия, поэтому в отличие от пайки большинства других металлов разность между температурой пайки и температурой, при которой паяемый металл может разрушаться под действием собственного веса, сравнительно мала. Так, пайку эвтектическим силумином ведут при температуре 610°С, а температура начала плавления наиболее широко применяемых для пайки сплавов АМц и АМг составляет 640°С и 630°С соответственно, это накладывает жесткие требования к соблюдению температурного режима при пайке и технологическому процессу.
Основная трудность при пайке алюминия связана с наличием на его поверхности тонкой, самовосстанавливающейся пленки из тугоплавкого и химически инертного оксида, которая препятствует контакту расплавленного припоя с поверхностью паяемого металла.
Алюминий имеет высокое сродство к кислороду. Протекающая поверхностная реакция окисления фактически прекращается через 1 час, в результате образуется пленка окисла толщиной 2,5-5,0 нм, а в присутствии влаги она может составлять до 10 нм. Дальнейшее окисление алюминия тормозится, так как образовавшаяся пленка надежно изолирует металл от кислорода.
|
Температура плавления α-Al2O3 составляет 2045°С, температура кипения равна 2980°С. Давление паров α-Al2O3 при температуре его плавления равно 45,5∙10 Па; давление диссоциации α-Al2O3 при температуре 2000°С – 1.33∙10-3 Па, т. е. оксид Al2O3 практически не восстанавливается в используемых для этой цели газообразных средах и не испаряется при пайке.
Наличие окисной пленки на поверхности алюминия и его сплавов препятствует взаимодействию с ней расплавленного припоя и приводит к возникновению непропаев, окисных и газовых включений, что мешает получению качественных паяных соединений.
Другим затруднением при пайке алюминия и его сплавов является отрицательный электродный потенциал алюминия по отношению к большинству других металлов, что ограничивает выбор состава припоя для обеспечения коррозионной стойкости паяной конструкции.
Для повышения коррозионной стойкости в состав припоев вводят Zn. По мнению Дж.Д. Дауда положительное влияние Zn обусловлено улучшением соотношения потенциалов паяемого металла и шва. Однако при этом важную роль играют процессы пассивирования, т.е. образования оксидной пленки на контактирующих поверхностях металлов, тормозящие развитие коррозии.
Следующей трудностью при пайке алюминия является его склонность к нежелательным металлургическим взаимодействиям при повышенных температурах (оплавление границ зерен, значительная химическая эрозия в расплавах припоев, образование хрупких интерметаллидов и т. д.), поскольку с большинством легкоплавких элементов, составляющих основу легкоплавких припоев (Sn, Pb, Cd, Bi, In, Li, Na), он образует монотектические диаграммы состояния, с весьма слабой взаимной растворимостью компонентов (кроме цинка, образующего с алюминием эвтектику при температуре 382°С и широкую область твердых растворов со стороны алюминия и олова). Поэтому низкотемпературная пайка алюминия и его сплавов применяется весьма ограниченно.
Все перечисленные выше особенности обуславливают жесткие ограничения на выбор технологии пайки (выбор состава и способа введения припоя в паяемые зазоры, способы нагрева и активации паяемых поверхностей).
|
Постоянно присутствующая на поверхности алюминия и его сплавов прочная пленка оксида алюминия должна быть удалена непосредственно перед пайкой. Кроме того, на поверхностях соединяемых алюминиевых деталей, подлежащих пайке, всегда имеются частицы и вещества, оставшиеся после обработки давлением или резанием (стружка, технологические жидкости), а также пыль и грязь, осевшие при транспортировке и хранении.
Подготовка поверхностей соединяемых деталей имеет важное значение, поскольку от этого зависит результат всего процесса пайки.
Очистка должна быть проведена непосредственно перед сборкой и пайкой, поскольку на поверхности алюминия мгновенно образуется пленка его оксида в виде слоя толщиной < 0,5 нм. Поэтому, помимо предварительной подготовки, требуется разрушение Al2O3 в течение самого цикла пайки.
Загрязнения и жир удаляют обезжириванием паром и (или) с применением любого растворителя. Толстые слои окислов обычно удаляют механическим или химическим способом.
Механический способ наиболее простой, позволяет надежно удалить окислы различной толщины, особенно с контактных поверхностей небольшой площади и при ремонтных работах. Механическую очистку поверхности алюминиевых деталей и припоя проводят металлической щеткой или шлифовальной шкуркой, а также ультразвуком под слоем расплавленного припоя.
Химические способы применяют в тех случаях, когда нужно очистить от окислов большое количество деталей или когда форма и конфигурация очищаемых деталей исключают возможность применения механических средств. Химическая очистка (травление) сравнительно недорога, быстра и надежна.
Для травления алюминия его сплавов используют и щелочи, и кислоты. Щелочи более активны, поэтому их чаще применяют для удаления окислов. Однако при их использовании на поверхности материала остается шлам, образованный компонентами сплава, не взаимодействующими с травильным раствором. Поэтому для его удаления металл погружают в кислоту – эта операция называется осветление.
Очищенные детали следует подвергать пайке не позднее чем через 12 часов после обработки поверхности.
|
Основным недостатком химических способов очистки поверхности с использованием щелочей и кислот является низкая экологичность этого процесса. В настоящее время ведутся активные исследованиях области разработки новых, экологически чистых составов для удаления с поверхности алюминия оксидной пленки.
Припои
Припои, применяемые для пайки алюминия и его сплавов, можно разделить на три группы.
1. Легкоплавкие припои на основе олова, свинца, кадмия с температурой плавления ниже 300°С. Эти припои обладают низкой прочностью и образуют соединения с низкой коррозионной стойкостью, требующие специальных защитных покрытий от коррозии. Перед пайкой необходимо предварительное облуживание соединяемых поверхностей. Пайку в основном производит вручную электропаяльником или в ультразвуковых ваннах с расплавленным припоем.
2. Припои на основе цинка, обладающие достаточно высокой прочностью и являющиеся относительно коррозионностойкими, с температурой плавления в интервале 300-450° С. Пайка ими может применяться для любых алюминиевых сплавов. Способы пайки: абразивная, ультразвуковая, флюсовая с нагревом горелкой, в печах. Области применения: исправление брака алюминиевого литья, электромонтажные соединения, пайка листового алюминия, в том числе с другими металлами (оцинкованной сталью, медью).
К недостаткам данных припоев относится низкая пластичность, что обуславливает их применение в виде прутов, паст, расплавов для пайки окунанием, а также плохая способность к растеканию и затеканию в зазор, склонность к эрозии паяемого металла.
3. Припои на основе алюминия, обеспечивающие высокую прочность паяных соединений и высокую коррозионную стойкость, с температурой плавления в интервале 450-630°С.
Способы пайки алюминия.
Пайку алюминия можно осуществлять практически всеми известными способами, но не все они пригодны в условиях серийного и массового производства.
Низкотемпературная пайка применяется для алюминия и его сплавов достаточно широко. Полученные соединения, как правило, имеют невысокие прочностные характеристики. Такую пайку проводят обычно оловянно-цинковыми, кадмиево-цинковыми и цинковыми припоями.
Соединения из алюминия и его сплавов, паяные легкоплавкими припоями на основе олова или олова со свинцом, имеют низкую коррозионную стойкость. Для снижения склонности к коррозии в легкоплавкие припои вводят цинк. Однако, соединения, паяные цинковыми припоями с повышенным содержанием примесей олова, свинца, сурьмы, кадмия склонны к развитию в паяных швах межкристаллитной коррозии. Кроме того, цинковые припои склонны к межзеренной и общей химической эрозии паяемых алюминиевых сплавов. Для устранения негативных явлений в состав таких припоев дополнительно вводят в небольших количествах алюминий, хром, галлий и т.п.
|
Для получения ответственных высокопрочных соединений наиболее широко применяется высокотемпературная пайка алюминия. Для этой цели применяют главным образом готовые припои на основе алюминия Al-Si, Al-Zn, Al-Cu-Si, Al-Mg-Si, а также контактно-реактивные флюсы.
Трудности, связанные с пайкой некоторых алюминиевых сплавов и удалением оксидной пленки, могу быть устранены предварительным нанесением на контактные поверхности металлических покрытий, обеспечивающих пайку труднопаяемых алюминиевых сплавов. Эти покрытия предотвращают межкристаллитное проникновение припоя в основной металл, возникновение высокого электродного потенциала припоя в паре с основным металлом или образование химических соединений. В качестве покрытий, обеспечивающих надежное смачивание и устранение указанных явлений, используют чистые металлы (Sn, Zn, Al, Cu, Ni, Ag и др.) и припои. В этом случае механическая прочность паяемого соединения лимитируется прочностью сцепления основного металла с металлом покрытия.
Предварительное нанесение металлических покрытий осуществляют лужением (абразивным или ультразвуковым), плакированием, напылением или гальваническим методом. Широко применяют алюминий, плакированный силуминовыми сплавами (АПС, АМцПС).
Флюсовая пайка.
Флюсовая высокотемпературная пайка алюминия и его сплавов готовым припоем может быть выполнена с локальным нагревом в пламени паяльных ламп, горелок, токами высокой частоты и общим нагревом в печах и погружением в флюсовые ванны.
Для пайки с локальным нагревом, как правило, используют флюсы типа 34А (NaF – 9…11%, ZnCl2 – 8…12%, LiCl – 29…30%, KCl – 54…56%).
Для пайки алюминия с общим нагревом используют печи с воздушной и защитной атмосферой. Пайка осуществляется путем нагрева деталей с заранее нанесенными на них припоем и флюсом.
При пайке в воздушных печах чаще всего используют флюсы Ф5 (KCl– 44-46%, LiCl– 37-39%, NaF– 9-11%, SnCl2– 3%, CdCl2– 4%), температура пайки – выше 500°С, Ф124 (KCl– 41,2%, LiCl– 22,8%, NaF– 6,1%, NaCl–21,9%, ZnCl– 8%), 34А, ТПИ-3. Флюсы можно наносить в виде спиртовой пасты, а последние два погружением в водный раствор флюса.
Более эффективен метод флюсовой печной пайки алюминиевых изделий в контролируемой атмосфере, состоящей из полностью обезвоженного «сухого» воздуха или очищенного инертного газа, что позволяет уменьшить количество используемого флюса в 6-10 раз.
Наиболее отработанным способом на сегодняшний день является процесс пайки алюминиевых изделий в соляных ваннах. При пайке в соляных ваннах припой чаще всего наносят в виде плакирующего слоя на поверхности паяемых деталей. При пайке теплообменников хорошо себя зарекомендовал флюс состава, %: NaCl – 18…22, KCl – 33…37, LiCl – 9…11, KF, CaCl2 – 23…27, температура пайки 600-610°С, припой – эвтектический силумин.
Основным недостатком всех способов флюсовой пайки является высокая коррозионная активность применяемых флюсов, что требует их тщательного удаления с поверхности изделия после пайки.
На сегодняшний день наиболее перспективным направлением развития флюсовой пайки является использование сложных флюсов на основе алюмокалиевых фтористых солей KAlF4 – K3AlF6. Температура плавления таких флюсов находится в интервале 835–875 К и ниже. В расплавленном состоянии они активны, а в твердом состоянии остатки негигроскопичны, малорастворимы в воде, коррозионнонеактивны, что позволяет исключить операцию отмывки флюса из технологического процесса.
Кроме того, в настоящее время происходит активная замена флюсовой пайки на более экологически чистую бесфлюсовую пайку.
Бесфлюсовая пайка.
Низкотемпературная бесфлюсовая пайки алюминия и его сплавов основана механическом удалении оксидной пленки с поверхности изделия. Основными способами низкотемпературной бесфлюсовой пайки являются абразивная, ультразвуковая и абразивно-кавитационная пайка.
Пайка алюминия без применения флюсов возможна при нагреве паяемого металла в безокислительной среде (вакуум, инертные газы), что позволяет сохранить малую толщину слоя окисла, возникшего после предварительного травления, и способность к нарушению его сплошности при нагреве.
В случае использования защитных газов (азот, аргон, гелий и др.) бесфлюсовая пайка возможна при точке росы не выше –60°С и содержании кислорода не более 0,002 %. В этом случае в припои системы Al-Si (в виде плакировки) рекомендуется вводить в микроколичествах специальные присадки, например Li, Ca, Mg, Bi, Sb, Ba и др. Эти поверхостно-активные элементы снижают поверхностное натяжение некоторых припоев на основе алюминия, уменьшает его вязкость, улучшает смачиваемость и затекание припоя в зазор, обеспечивая проведение бесфлюсовой пайки в атмосфере аргона чистотой 99,95%. Известна технология пайки крупногабаритных теплообменников в среде аргона, при которой нагрев собранной под пайку конструкции производится в камере потоком циркулирующего газа. В процессе нагрева производится дополнительная очистка газа с помощью нераспыляемого геттера.
Недостатки технологии пайки в среде инертных газов – использование оборудования для их осушки и дополнительные затраты на газ.
Более широко применяется технология высокотемпературной пайки в вакууме. Первоначально пайку проводили в условиях высокого вакуума (10-3–10-4 Па) при одновременном приложении определенного усилия осадки в месте контакта. Обеспечение минимального зазора и приложение сжимающего усилия в месте контакта паяемых деталей является необходимым условием для качественного формирования паяного соединения при вакуумной пайке. Современная технология предусматривает использование высокого вакуума с остаточным давлением 10-2 – 10-3 Па и введение паров магния в рабочий объем камеры.
Положительное влияние магния на паяемость алюминия была обнаружена К. Дж. Миллером в начале 60-х годов. Существует два мнения по поводу действия магния:
– роль магния сводится главным образом к очистке вакуумированного пространства печи (2MgO + O2 = 2MgO и Mg + H2O = MgO + H2) и частичному восстановлению алюминия из окисной пленки (Al2O3 + 3Mg = 3MgO + 2Al);
– известно, что в системе Al-Si-Mg образуются две эвтектики: богатая кремнием с температурой плавления 550°С и богатая магнием с температурой плавления 450°С. Возможность ведения процесса пайки алюминия силумином в парах магния при 560°С доказывает наличие при этом контактного твердо-газового плавления.
Магний наиболее часто вводят в зону пайки в компактных заготовок, или путем использования плакированных алюминиевых листов, содержащих 0,2-2,0% Mg.
При бесфлюсовой вакуумной пайке алюминия повышается коррозионная стойкость изделий, снижается себестоимость производства и расширяются возможности изготовления паяных конструкций сложной формы, имеющих замкнутые каналы, которые довольно трудно очистить при флюсовой пайке.
Повысить производительность вакуумной пайки можно применением многокамерных проходных печей непрерывного действия. Такие печи могут иметь от трех до семи камер: для подсушивания изделия, создания вакуума, предварительного нагрева, пайки, напуска инертного газа и охлаждения.
Кроме этого повысить производительность процесса можно путем перехода на более низкий вакуум. Величина остаточного давления при вакуумной пайке характеризует количество остаточного кислорода и влаги. Поэтому при увеличении остаточного давления для сохранения низких значений парциальных давлений кислорода (Ро2) и воды (Рн2о) необходимо использовать геттеры, активно поглощающие О2 и H2O при температуре пайки. Применение только паров магния в условиях форвакуума не дает положительного эффекта из-за окисления источников паров, вследствие чего процесс испарения нарушается и может прекратиться. В качестве неиспаряющегося геттера могут применяться титан или цирконий. Например, разработана технология пайки высокоактивных металлов, при которой пайка ведется в специальном вспомогательном контейнере с затвором, уплотняемым неиспаряющимся геттером – измельченной титановой губкой, которая при температурах 500-550°С начинает активно поглощать в основном кислород, частично азот и другие газы, снижая парциальное давление О2 и H2O и создавая внутри контейнера безокислительную атмосферу, обеспечивающую качественную пайку Al-сплавов и Ti-сплавов при Рост ≈0,1-10 Па
МАГНИИ И ЕГО СПЛАВЫ
Трудности пайки магниевых сплавов обусловлены прежде всего образованием на их поверхности пленки оксида MgO, обладающего высокой химической стойкостью и практически не диссоциирующего в аргоне или вакууме или в известных в настоящее время активных газовых средах. Для удаления пленки применяют активные флюсы, содержащие хлористые и фтористые соли лития, калия и натрия, а пайку легкоплавкими припоями выполняют с предварительным абразивным лужением.
Перед пайкой деталей из магния и его сплавов с их поверхности должны быть тщательно удалены все загрязнения, оксиды и слой, образующийся при оксидировании. От жиров и грязи поверхности очищают ветошью, смоченной в бензине, этиловом спирте. Консервирующий смазочный материал удаляют кипячением в (0,5—1) %-ном водном растворе соды в течение 20—30 мин, последующей промывкой в теплой воде и сушкой при 60—80 °С.
Для пайки магниевых сплавов нашел применение флюс ДАУ-452 —аналог флюса 380Мг состава (%): 42,5 KCI, 10 NaCI, 37 LiCI, 10 NaF, 0,5 Na2AIF; температура плавления 380 °С. Остатки флюсов способствуют интенсивной коррозии паяного соединения и должны быть тщательно удалены не позже чем через 30 мин после пайки. Флюсы имеют большую плотность, чем припой на основе магния, и поэтому даже при быстром ведении процесса в паяном шве присутствуют флюсовые включения. При механической обработке паяного шва резанием и удалении с галтель-ных участков верхнего слоя могут вскрыться поры, поэтому паяные швы снова тщательно промывают.
Нашел применение также флюс состава (%): 89 плавленого карналита, 8 криолита, 3 оксида цинка: температура плавления 425—620 °С. При пайке сплавов Mg—AI—Zn при температурах выше их солидуса существует опасность образования легкоплавких эвтектик, плавления основного металла по границам зерен, что приводит к его охрупчиванию и разупрочнению.
Из-за сравнительно невысокой температуры плавления магния и его сплавов (640—655 °С) для пайки непригодны припои на основе меди, серебра, золота. Алюминиевые припои также непригодны из-за способности к активному химическому взаимодействию с магнием и образованию хрупких интерметаллидов в паяемом шве. Поэтому в качестве припоев для пайки магниевых сплавов применяют припои на магниевой основе.
|
|
Адаптации растений и животных к жизни в горах: Большое значение для жизни организмов в горах имеют степень расчленения, крутизна и экспозиционные различия склонов...
История создания датчика движения: Первый прибор для обнаружения движения был изобретен немецким физиком Генрихом Герцем...
Архитектура электронного правительства: Единая архитектура – это методологический подход при создании системы управления государства, который строится...
История развития пистолетов-пулеметов: Предпосылкой для возникновения пистолетов-пулеметов послужила давняя тенденция тяготения винтовок...
© cyberpedia.su 2017-2024 - Не является автором материалов. Исключительное право сохранено за автором текста.
Если вы не хотите, чтобы данный материал был у нас на сайте, перейдите по ссылке: Нарушение авторских прав. Мы поможем в написании вашей работы!