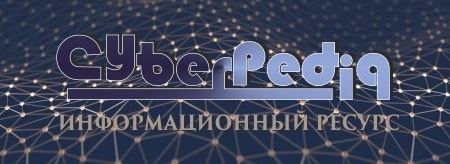
Архитектура электронного правительства: Единая архитектура – это методологический подход при создании системы управления государства, который строится...
Археология об основании Рима: Новые раскопки проясняют и такой острый дискуссионный вопрос, как дата самого возникновения Рима...
Топ:
История развития методов оптимизации: теорема Куна-Таккера, метод Лагранжа, роль выпуклости в оптимизации...
Устройство и оснащение процедурного кабинета: Решающая роль в обеспечении правильного лечения пациентов отводится процедурной медсестре...
Теоретическая значимость работы: Описание теоретической значимости (ценности) результатов исследования должно присутствовать во введении...
Интересное:
Национальное богатство страны и его составляющие: для оценки элементов национального богатства используются...
Аура как энергетическое поле: многослойную ауру человека можно представить себе подобным...
Инженерная защита территорий, зданий и сооружений от опасных геологических процессов: Изучение оползневых явлений, оценка устойчивости склонов и проектирование противооползневых сооружений — актуальнейшие задачи, стоящие перед отечественными...
Дисциплины:
![]() |
![]() |
5.00
из
|
Заказать работу |
|
|
Форма лотка | Эскизы поперечного сечения | Расчетные формулы |
V-образный Круглый внутренний Круглый наружный Коробчатый: открытый закрытый | ![]() ![]() ![]() ![]() | α=45°..60°;
h л = 0,5 d (ctg α + 0,4)
![]() ![]() ![]() ![]() ![]() ![]() ![]() ![]() ![]() ![]() ![]() ![]() ![]() ![]() ![]() ![]() ![]() ![]() ![]() |
_________
* Для исключения перекрытия деталей (без учета фасок) принимают х 1...2 мм.
Для принудительной подачи деталей в зону сборки применяют шибер с глубиной гнезда Н = 0,95 d. Бункерные загрузочные устройства используют для деталей простой геометрической формы массой менее 0,5 кг и длиной не более 100 мм, не склонных к слипанию и сцеплению, достаточно жестких и нехрупких. По объему деталей определяют конструкцию бункера: одноемкостную с одним бункером или многоемкостную с бункером для выдачи деталей и предбункером для их хранения (стационарным или перемещаемым) (рис. 2.56).
Рис. 2.56. Схемы одно- (а) и многоемкостного (б) бункеров
Объем бункера вычисляют по формуле
где - объем детали, см3;
- время непрерывной работы бункера (без досыпки), мин; t — такт сборки; q — коэффициент объемного заполнения (для простых деталей q = 0,4...0,6, причем чем сложнее и длиннее деталь, тем меньше q);
- средняя производительность устройства, шт./мин.
Наибольшее распространение в промышленности получили вибробункеры. При их применении рассчитывают диаметр чаши. Для чаши цилиндрической формы (рис. 2.57, а)
Рис. 2.57. Элементы конструкции вибробункера: а — вибробункер с цилиндрической чашей; б — коническая чаша вибробункера; 1 — чаша; 2 — лоток; 3 — пружинная подвеска; 4 — вибропривод
|
а для чаши конической формы (рис. 2.57, б)
где DBH ≥ (5...10) l дет — внутренний диаметр чаши бункера у днища, мм; b ст — толщина стенки, мм (для точеных чаш b ст = 2...3 мм, для сварных b ст = 1 1,5 мм); V дет — объем детали, мм3; П цил – цикловая производительность, мин; H расч – высота заполнения бункера, мм;
l дет — длина детали в преобладающем положении при перемещении по лотку, мм.
Полная высота чаши бункера Н = H расч+(1,0... 1,5)/ t, где
t = - шаг подъема спирального лотка, мм;
— средний диаметр лотка, мм;
= 0,5...3° — угол подъема лотка.
Рассчитанные диаметры чаш бункеров округляют в большую сторону до числа из стандартного ряда: 60, 100, 120, 160, 200, 250, 320, 400, 450, 500, 640, 800, 1000 мм. По обшей вибрирующей массе и необходимой производительности рассчитывают вибропривод.
Установочные приспособления
Установочные приспособления предназначены для базирования деталей и узлов на сборочной позиции с необходимой фиксацией. Количество и тип установочных элементов, реализующих выбранную схему базирования, определяют в зависимости от вида базовых поверхностей (плоские, цилиндрические, призматические и т.д.), их точности и шероховатости.
При автоматической сборке точность изготовления установочных элементов рассчитывают из условий собираемости сопрягаемых поверхностей. Например, для выполнения цилиндрических соединений с зазором или натягом (рис. 2.58) допустимое смещение ∆∑ осей сопрягаемых поверхностей определяют из следующих условий:
Рис. 2.58. Параметры выполняемого соединения
где — сумма катетов фасок на торцах деталей;
— минимальный зазор (со знаком «+») или максимальный натяг (со знаком «—»);
— размер выточки (расточки) на торцах деталей;
— угол перекоса деталей;
— допустимый угол перекоса, определяемый точностью соединения.
В свою очередь,
где ,
-погрешности установки сопрягаемых поверхностей базовой и присоединяемой деталей; ∆н — погрешность настройки сборочной позиции (± 0,025...0,05 мм).
|
Погрешность приспособления определяют по формулам
где ,
соответственно погрешность базирования базовой и присоединяемой деталей;
,
— соответственно погрешность закрепления базовой и присоединяемой деталей; ∆поз, ∆пв.поз – соответственно погрешности позиционирования установочного приспособления и руки робота на сборочной позиции (повторного позиционирования).
При выполнении соединений с тепловым воздействием в расчетных формулах необходимо учесть возможные тепловые деформации элементов приспособлений (∆Т).
Рис. 2.59. Самоцентрирующее базирующее устройство
Для упрощенных расчетов можно принимать погрешность установки базовой и присоединяемой деталейε = 0,6...0,7∆∑.
Для повышения безотказности сборочного процесса в целях снижения погрешности установки сопрягаемых поверхностей часто используют самоцентрирующие приспособления: патроны, схваты (рис. 2.59) и т. п.
Ориентирующие устройства
При автоматизированной сборке ориентирующие устройства выполняют две функции: ориентируют присоединяемые детали в пространстве и определяют взаимное расположение сопрягаемых поверхностей перед выполнением соединения в зоне сборки.
Метод ориентации деталей в пространстве зависит от их конструкции, массы, материала и уровня автоматизации. Различают контактные и бесконтактные методы. При контактном методе ориентация детали происходит под воздействием твердого, жидкого или газообразного тела, при бесконтактном методе — под воздействием электрического, магнитного или электромагнитного поля.
По виду конструкции эти ориентирующие устройства бывают пассивные и активные. Используя гравитационные силы или конструктивные элементы деталей, пассивные ориентирующие устройства (рис. 2.60, а) сбрасывают неправильно сориентированные детали обратно в бункер, а правильно сориентированные — пропускают в лотке в зону сборки. Активные устройства всем неправильно сориентированным деталям придают нужное положение в пространстве. В качестве примера на рис. 2.60, б показано устройство, где присоединяемая деталь — керн 2 в магнитной катушке 1 — получает определенную полярность, что позволяет ей ориентироваться на лотке 4 под воздействием постоянного магнита 3. Переключатель 5 обеспечивает нужную полярность в катушке в зависимости от положения керна.
|
Механические ориентирующие устройства способны различать конструктивные элементы детали размером не менее 0,3 мм, оптические — не менее 0,01...0,05 мм, электромагнитные — не менее 0,01...0,1 мм (в зависимости от массы детали и чувствительности датчика), пневматические — не менее 0,02...0,03 мм.
Рис. 2.60. Пассивное (а) и активное (б) ориентирующие устройства
Ориентирующие устройства для взаимной ориентации сопрягаемых поверхностей в зоне сборки чаще всего выполняют механическими. Оптимальные параметры для взаимной ориентации (зазор 8 между ориентирующей поверхностью и присоединяемой деталью, жесткость упругих элементов, расстояние l т между торцами ориентируемых деталей) зависят от параметров соединения, погрешностей положения ∆∑ и α∑ сопрягаемых поверхностей и режимов сборочного процесса. Их определяют по математическим моделям, полученным на базе многофакторных экспериментальных исследований автоматического процесса выполнения соединения.
Рабочие приспособления
Рабочие приспособления — исполнительные механизмы — по виду выполняемого соединения подразделяют на прессовые
постоянного действия для раскатки, вальцовки, соединения с натягом и т. п.; ударные для заклепки, кернения и т. п.; адгезионные для сварки, пайки, склеивания и т. п.; резьбовые для затяжки резьбовых соединений; на устройства для выполнения соединений с зазором (досылатели, рабочие органы сборочных роботов и др.) и комбинированные (клеесварные, клеезаклепочные и т. д.).
Параметры исполнительных механизмов зависят от вида соединения (с зазором, с натягом и т.д.), способа его выполнения (с помощью досылателя, тепловым воздействием, запрессовкой) и от размеров сопрягаемых поверхностей. Например, при автоматической сборке при выполнении цилиндрических соединений (рис. 2.61) диаметр D досылателя 1 делают на 0,1...0,2 мм меньше диаметра d сопрягаемой детали 2, так как при этом досылатель выполняет функции отсекателя в лотке 4 и обеспечивает поштучную выдачу присоединяемой детали в ориентирующее устройство 3 зоны сборки.
|
При проектировании силовых исполнительных механизмов выбирают вид привода и выполняют силовой расчет для определения его параметров. В конструкциях используют ручные, электрические, пневматические, гидравлические, гидропневматические приводы, дополненные в ряде случаев рычажными или клиновыми усилителями. Для автоматизированной многопозиционной сборки проектируют устройства с несколькими рабочими органами, работающими параллельно.
Рис. 2.61. Устройство с упругими компенсаторами для сборки цилиндрических соединений с зазором
При проектировании оборудования для нанесения клеев и других адгезивных материалов необходимо учитывать ряд особенностей. Во избежание выхода из строя дозаторов, подающих жидкие клеи, вследствие возникновения клеевых пробок на пути транспортировки клея не следует применять элементы из материалов, вызывающих адгезию или стимулирующих отверждение данного клея. Использование клеев, чувствительных к температурным перепадам, требует изоляции нагревающихся элементов конструкции, контактирующих с зонами транспортировки клея.
Для подачи термопластичных клеев, которые в нормальных условиях представляют собой пластичное твердое тело без клеящих свойств и становятся жидкими при нагреве, используют термопистолет (рис. 2.62). Нагревательные устройства пистолета имеют три зоны нагрева. В зоне I (см. рис. 2.62) температура должна быть достаточной лишь для размягчения расплава, в зоне II поддерживают его рабочую температуру, а в зоне III — на 5... 15 %
ниже рабочей. В противном случае расширяющийся при нагреве клей самопроизвольно будет поступать в зону сборки. Для поддержания температуры используют устройства обратной связи.
Для сборки резьбовых соединений в качестве исполнительных органов применяют различного типа гайковерты (электрические, пневматические) с тарированной муфтой или без нее. Выбор той или иной конструкции гайковерта зависит от типа производства, качества соединения, оснащенности производства, требуемого момента затяжки и параметров деталей соединения. Пример комбинированного загрузочно-исполнительного устройства представлен на рис. 2.63, где в одной конструкции объединены вибробункер 1, лоток 4 и винтоверт 3 с приводом 2.
Рис. 2.62. Ручной термопистолет для подачи гермопластичного клея: 1 — клей в виде стержня; 2 — нагреватель; 3 — сменное сопло
Рис. 2.63. Пример комбинированного устройства для автоматизированной подачи и завинчивания винтов
Контрольные приспособления
Контрольные приспособления служат для контроля качества выполнения соединения (момента затяжки, силы запрессовки), а также контроля выходных геометрических параметров соединения (параллельности, перпендикулярности поверхностей). На рис. 2.64 показано приспособление для контроля взаимного положения гильзы цилиндра 1 и корпусной детали 2. Погрешность положения (проседание) торца гильзы определяют по различию показаний индикаторов 3, предварительно настроенных на ноль по эталону. По конструкции контрольные устройства могут быть механическими, электронными, пневматическими, оптическими и др.
|
Рис. 2.64. Приспособление для контроля положения гильзы цилиндра: а — главный вид; б — вид сверху без деталей 1 и 2
Наиболее эффективными являются средства активного контроля, позволяющие управлять качеством сборки в процессе выполнения соединения. На рис. 2.65 представлена схема устройства для комбинированного контроля силы затяжки Р зат ответственных резьбовых соединений по моменту затяжки М зат и углу поворота φ. В микропроцессорную систему управления поступают сигналы от датчиков 2, 3, замеряющих реактивный момент на корпусе гайковерта (датчик момента) и угол поворота болта (гайки). Управляющая система определяет пороговый момент, приращения ∆ M, ∆φ и их отношение и рассчитывает требуемый момент затяжки М з ат = φзат ∆ М / ∆φ. Как только момент затяжки достигает требуемого значения, устройство контроля и управления 6, содержащее отключающее устройство, через электромагнитную порошковую муфту отключает двигатель привода гайковерта.
Рис. 2.65. Схема резьбозавертывающего устройства с активным контролем силы затяжки резьбового соединения комбинированным методом:
1 — торцевая насадка под ключ; 2 — датчик угла поворота ∆φ; 3 — датчик момента затяжки ∆ M; 4 — датчик обратной связи; 5 — привод; 6 — блок контроля и управления
|
|
Архитектура электронного правительства: Единая архитектура – это методологический подход при создании системы управления государства, который строится...
Особенности сооружения опор в сложных условиях: Сооружение ВЛ в районах с суровыми климатическими и тяжелыми геологическими условиями...
Своеобразие русской архитектуры: Основной материал – дерево – быстрота постройки, но недолговечность и необходимость деления...
Папиллярные узоры пальцев рук - маркер спортивных способностей: дерматоглифические признаки формируются на 3-5 месяце беременности, не изменяются в течение жизни...
© cyberpedia.su 2017-2024 - Не является автором материалов. Исключительное право сохранено за автором текста.
Если вы не хотите, чтобы данный материал был у нас на сайте, перейдите по ссылке: Нарушение авторских прав. Мы поможем в написании вашей работы!