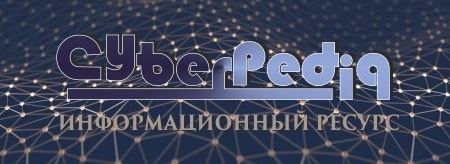
Общие условия выбора системы дренажа: Система дренажа выбирается в зависимости от характера защищаемого...
Особенности сооружения опор в сложных условиях: Сооружение ВЛ в районах с суровыми климатическими и тяжелыми геологическими условиями...
Топ:
Техника безопасности при работе на пароконвектомате: К обслуживанию пароконвектомата допускаются лица, прошедшие технический минимум по эксплуатации оборудования...
Генеалогическое древо Султанов Османской империи: Османские правители, вначале, будучи еще бейлербеями Анатолии, женились на дочерях византийских императоров...
Интересное:
Распространение рака на другие отдаленные от желудка органы: Характерных симптомов рака желудка не существует. Выраженные симптомы появляются, когда опухоль...
Как мы говорим и как мы слушаем: общение можно сравнить с огромным зонтиком, под которым скрыто все...
Финансовый рынок и его значение в управлении денежными потоками на современном этапе: любому предприятию для расширения производства и увеличения прибыли нужны...
Дисциплины:
![]() |
![]() |
5.00
из
|
Заказать работу |
|
|
Для направления мерного инструмента (сверла, зенкера, развертки и борштанги) на станках сверлильно-расточной группы применяют кондукторные втулки. Они позволяют повысить точность диаметральных размеров, формы и особенно расположения отверстий. Кондукторные втулки бывают постоянные без бурта (рис. 2.38, а) и с буртом (рис. 2.38, б) для работы одним инструментом. Сменные кондукторные втулки (рис. 2.38, в, г) применяют при обработке отверстий несколькими последовательно сменяемыми инструментами. Сменные втулки 1 устанавливают в постоянные втулки 2 по посадкам H7/g6 либо H6/g5. В корпус постоянные втулки устанавливают по посадке Н7/n6. Втулки диаметром до 25 мм изготовляют из стали У10А или У12А с закалкой до твердости 62...65 HRC. Для втулок с d > 25 мм
Рис. 2.38. Постоянные (а, б) и сменные (в, г) кондукторные втулки
применяют сталь 20 и 20Х с цементацией на глубину 0,8...1,2 мм и закалкой до той же твердости. Ориентировочный срок службы кондукторных втулок (1...1,5) 104 сверлений при
. Высота H =(1,5...2)
.
Для уменьшения изнашивания втулки между ее нижним торцем и поверхностью заготовки предусматривают зазор е (см. рис. 2.38, а) для отвода стружки. При сверлении чугуна е = (0,3...0,5) , при сверлении стали и других вязких материалов зазор увеличивают до
.
Специальные кондукторные втулки (рис. 2.39) имеют конструкции, отвечающие особенностям детали и операции. Так, на рис. 2.39, а представлена втулка для обработки отверстия в криволинейной поверхности. Удлиненная быстросменная втулка (рис. 2.39, б)
Рис. 2.39. Специальные кондукторные втулки
служит для направления оси отверстия, расположенного в углублении. При малом расстоянии между осями применяют конструкции, представленные на рис. 2.39, в и г.
|
Для направления борштанг расточных приспособлений используют неподвижные и вращающиеся направляющие втулки. Неподвижные втулки проще вращающихся по конструкции, но они быстрее нагреваются. Поэтому при больших скоростях резания следует применять вращающиеся втулки.
Вращающиеся втулки (рис. 2.40, а) располагают обычно по обе стороны растачиваемого отверстия; это предотвращает увод инструмента при расточке. Их монтируют на подшипниках скольжения или качения.
Рис. 2.40. Направляющие втулки для борштанг с подшипником скольжения (а) и качения (б)
Вращающуюся втулку 1, устанавливаемую в подшипник скольжения, изготовляют из чугуна или бронзы, а постоянную втулку 2 — из стали 20 или 20Х с цементацией и закалкой до твердости 56...62 HRC. Втулка удерживается от осевого перемещения в одну сторону буртом, а в другую — крышкой 3. На рис. 2.40, 6 показана вращающаяся втулка, смонтированная на роликовых подшипниках.
Вращающиеся втулки, смонтированные в игольчатых подшипниках, более точны (радиальный зазор ≤ 15 мкм) и допускают обработку на высоких скоростях резания.
Для размерной наладки фрезерных, токарных и строгальных станков применяют угловые 1 или высотные 2, 3 установы (рис. 2.41). Для установки фасонных фрез используют специальные установы (рис. 2.42).
Инструменты устанавливают по щупам, помещаемым между режущим лезвием инструмента и установочной плоскостью установа.
При настройке по щупу (см. рис. 2.41, в) размер установа Су определяют из геометрических связей:
где — наименьший выполняемый размер, мм;
— наименьшее упругое отжатие технологической системы;
— толщина щупа, мм.
Рис. 2.41. Угловые (а) и высотные (б) установы, а также расчетная схема для определения размера установа (в)
Плоские щупы выполняют в виде пластин толщиной 1, 3 и 5 мм, а цилиндрические — диаметром 3 и 5 мм. Толщину и диаметр щупов выдерживают с отклонениями по посадке h6.
Рис. 2.42. Специальные установы:
|
1 — установочный габарит; 2 — щупы для настройки инструментов; 3 — фреза
Щупы закаливают до твердости 56...62 HRC и шлифуют до Ra = 0,63 мкм. Установы выполняют из сталей 15 или 20, стали 20Х с цементацией на глубину 0,8... 1,2 мм и закалкой до твердости 55...60 HRC.
К вспомогательным относятся делительные устройства, применяемые в поворотных частях приспособления для установки заготовки в различные положения; фиксаторы; выталкиватели для удаления заготовок; прижимные устройства для плотного прижатия поворотной части к неподвижному основанию и некотсн рые другие.
Типовые конструкции фиксаторов приведены на рис. 2.43.
Шариковый фиксатор (см. рис. 2.43, а) наиболее прост, но не обеспечивает точное деление и не воспринимает момент сил обработки. Его поворотную часть переводят на следующее деление вручную до характерного щелчка при попадании шарика в новое углубление. Фиксатор с вытяжным цилиндрическим пальцем (см. рис. 2.43, 6) может воспринимать момент от сил обработки, но не обеспечивает высокую точность деления из-за наличия зазоров в подвижных соединениях. Несколько большую точность обеспечивает фиксатор с конической частью вытяжного пальца
Рис. 2.43. Типы фиксаторов: а — шариковый;
б — цилиндрический; в — конический; г — рычажный
(см. рис. 2.43, в). Угол α у него составляет 15°. Для уменьшения износа палец и обе втулки фиксатора выполняют из закаленной стали. Рычажный фиксатор 4 (см. рис. 2.43, г) с помощью рукоятки 5 поворачивается на оси 6 и поворотный диск 2, закрепленный на вращающейся части 1 приспособления, производит деление. Поворотный диск 2 вращается по неподвижной станине 3, к которой прикреплен кронштейн 9 с осью 6. Ввод фиксатора осуществляет пружина 8 через плунжер 7.
Примеры выталкивателей для ручного и автоматического удаления небольших деталей из приспособлений приведены на рис. 2.44. Применение выталкивателей повышает производительность и создает удобство в работе.
Для фиксации вала 3 поворотного устройства в корпусе 2 зажимного устройства (рис. 2.45) используют сухарь 4, установленный с зазором на стержне винта 1, и рукоятку 5, при повороте которой происходит совместное движение винта и сухаря
Рис. 2.44. Пружинный (а) и рычажный (б) выталкиватели
Рис. 2.45. Зажимное устройство: 1 — головка винта; 2 — корпус; 3 — вал поворотной части; 4 — сухарь; 5 — рукоятка
|
навстречу друг другу. Открепление вала 3 поворотного устройства происходит в обратной последовательности.
Основными элементами делительного устройства приспособления для сверлильного станка являются делительный диск 2 (рис. 2.46), установленный на валу 4, и фиксатор 8, расположенный в корпусе 1. Заготовку устанавливают по торцу делительного диска и закрепляют с помощью шайбы 5 и винта 6. Направление сверла осуществляется кондукторными втулками 3, установленными на делительном диске. При обработке следующего отверстия необходимо вывести фиксатор 8 из делительного диска и повернуть его на одно деление.
Пример делительного устройства для токарного станка приведен на рис. 2.47. Здесь поворотная планшайба 6 установлена на цилиндрический выступ корпуса 1 и удерживается кольцом 5.
Рис. 2.46. Делительное устройство приспособления для сверлильного станка: 1 — корпус; 2 — делительный диск; 3 -кондукторные втулки; 4 — вал; 5 — шайба; 6 — винт; 7 — заготовка; 8 — фиксатор
Фиксатор 9 выводят из втулки 7, затем поворачивают планшайбу 6 с поводком 4 до ввода фиксатора 9 пружиной 8 в очередную втулку 7.
Корпус приспособления объединяет в единое целое его
элементы; им воспринимаются силы, возникающие в процессе обработки, а также сила закрепления заготовки. Корпус должен быть достаточно прочным и жестким, удобным для установки и снятия заготовок, доступным для очистки от стружки, простым и дешевым в изготовлении. В конструкции корпуса должны быть направляющие элементы (шпонки, центрирующие буртики и т. п.) для быстрой фиксации приспособления на столе станка.
Рис. 2.47. Делительное устройство приспособления для токарного станка: 1 — корпус; 2 — винт; 3 — гайка; 4 — поводок; 5 — кольцо; 6 — поворотная шайба; 7 — втулка; 8 — пружина; 9 — фиксатор
Заготовки корпусов получают отливкой, ковкой и сваркой из отдельных частей. Материалом служит серый чугун СЧ12 и сталь СтЗ. Литые корпуса подвергают старению, а сварные — отжигу.
Корпусы передвижных или кантуемых приспособлений должны быть устойчивыми при разных положениях на столе станка: на всех позициях обработки центр тяжести приспособления не должен выходить за пределы опорных элементов корпуса. На столе станка корпус крепят с помощью болтов, заводимых в Т-образные пазы стола. В серийном производстве, когда на одном и том же станке периодически выполняют различные операции, крепление корпуса должно быть удобным и быстрым. Корпусы тяжелых приспособлений снабжают рым-болтами для удобства захвата при установке и снятии со станка. Сваркой можно получать корпусы сложных конфигураций; сроки и стоимость их изготовления при этом могут быть значительно снижены, а их масса уменьшена на 40% по сравнению с литыми.
|
Корпусы приспособлений простейших конструкций выполняют в виде единой базовой детали. Корпусы сложных приспособлений представляют собой сборную конструкцию.
|
|
Опора деревянной одностоечной и способы укрепление угловых опор: Опоры ВЛ - конструкции, предназначенные для поддерживания проводов на необходимой высоте над землей, водой...
Механическое удерживание земляных масс: Механическое удерживание земляных масс на склоне обеспечивают контрфорсными сооружениями различных конструкций...
Биохимия спиртового брожения: Основу технологии получения пива составляет спиртовое брожение, - при котором сахар превращается...
Состав сооружений: решетки и песколовки: Решетки – это первое устройство в схеме очистных сооружений. Они представляют...
© cyberpedia.su 2017-2024 - Не является автором материалов. Исключительное право сохранено за автором текста.
Если вы не хотите, чтобы данный материал был у нас на сайте, перейдите по ссылке: Нарушение авторских прав. Мы поможем в написании вашей работы!