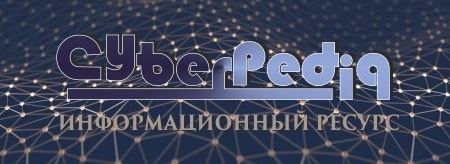
Автоматическое растормаживание колес: Тормозные устройства колес предназначены для уменьшения длины пробега и улучшения маневрирования ВС при...
История развития пистолетов-пулеметов: Предпосылкой для возникновения пистолетов-пулеметов послужила давняя тенденция тяготения винтовок...
Топ:
Характеристика АТП и сварочно-жестяницкого участка: Транспорт в настоящее время является одной из важнейших отраслей народного...
История развития методов оптимизации: теорема Куна-Таккера, метод Лагранжа, роль выпуклости в оптимизации...
Проблема типологии научных революций: Глобальные научные революции и типы научной рациональности...
Интересное:
Аура как энергетическое поле: многослойную ауру человека можно представить себе подобным...
Подходы к решению темы фильма: Существует три основных типа исторического фильма, имеющих между собой много общего...
Мероприятия для защиты от морозного пучения грунтов: Инженерная защита от морозного (криогенного) пучения грунтов необходима для легких малоэтажных зданий и других сооружений...
Дисциплины:
![]() |
![]() |
5.00
из
|
Заказать работу |
|
|
Давление газа на входе и выходе нагнетателя значительно отличается – 52кг/см2 и 76кг/см2. Для того чтобы конструктивно уплотнения нагнетателя были выполнены одинаково и работали в одинаковых условиях, также с целью уменьшения осевых нагрузок на ОУП, полость задумиса соединена уравнительной трубой с входным патрубком. Кроме того это способствует более эффективной работе уплотнений.
Газ под избыточным давлением из полости на входе и из полости задумиса поступает к втулкам уплотнения и пройдя первый лабиринт попадает в полость к втулкам уплотнения. Пройдя первый лабиринт попадает в полость, которые соединены между собой уравнительной трубой, где происходит окончательное выравнивание давления газа перед уплотнением. С другой стороны масло под давлением от насоса уплотнения подаётся к полости плавающих колец по трубопроводу с давлением превышающем на 1,5- 2,0 кг/см2 давление газа. За счёт ∆Р масла, газ и масло дренируется по полости м/г в маслоотводчики, а часть масла которое не участвовала в уплотнение поступает в слив масла. Масло от насосов смазки поступает на смазку подшипников и торсионного вала, после него смешивается с излишками масла от уплотнения и идёт в бак.
II вариант.
Из станционного трубопровода по линии 1, газ поступает в газо-приемную полость А нагнетателя. После сжатия он поступает в выходную полость Б, откуда по линии 2 подаётся в напорную линию станционного трубопровода. Давление газа на выходе значительно выше давления газа на входе, для того чтобы конструктивно уплотнения были одинаковыми (с целью уменьшения осевых нагрузок на опорно-упорных подшипник), в полость В за разгрузочным диском соединена с полостью А трубопроводом 8 ( задумисная линия).Данное мероприятие кроме того способствует повышению эффективности лабиринтного уплотнения между думисом и улиткой, т.к. уменьшает ∆ Р между полостями Б и В.
|
Газ находясь под избыточным давлением, из полости А и В, через зазоры между валом ротора и крышкой нагнетателя, поступает к втулкам уплотнений и пройдя первый лабиринт попадает через радиальные отверстия в полость Г. Эти полости (Г;Г)
соединены между собой уравнительной линией 7 благодаря чему в них происходит окончательное выравнивание давления газа.
С другой стороны масло под давлением от насоса уплотнения по линии 14 направляется к РПД-2М. К этому же агрегату подводится линия 4, связывающая его с полостями кольцевых проточек Д. Назначение РПД заключается в том что обеспечивает подачу масла по линии 3, в полости кольцевых проточек Е на 1,6-2,0 кг/см2 больше, чем в полость Д. Поэтому масло всегда будет перетекать из полостей Е через зазоры в полости Д навстречу движению газа. И таким образом обеспечивать надёжную герметизацию между вращающимся валом и неподвижным уплотнением.
Из кольцевых проточек Д масло-газовая смесь под давлением направляется по линии 5 к маслоотводчикам.
Масло от насоса смазки под давлением подаётся в линию 12 в масляную систему, откуда по линии 6 направляется в полость кольцевых проточек Ж, и через отверстие в крышке попадая на смазку опорного и опорно-упорного подшипника.
Часть масла из системы уплотнения, прошедшего через лабиринтное уплотнение из полостей Е в полость Ж смешивается там с маслом идущим на смазку подшипников. Масло отработавшее в системах смазки и уплотнения, поступает по линии 9 на слив.
СИСТЕМА СМАЗКИ.
Система смазки нагнетателя служит для смазки подшипников и зубчатой муфты, а также для отвода тепла которое выделяется в результате трения в опорах ротора.
Система смазки состоит:
|
1. Маслобак. 7. Фильтр низкого давления.
2. ПНС. 8. Зубчатая полумуфта.
3. Обратный клапан. 9. Опорный подшипник.
4. ГНС. 10. Опорно-упорный подшипник.
5. Маслоохладитель. 11. Картер.
6. Терморегулятор. 12. КР-2.
В сис-му смазки масло забирается насосами ПНС и ГНС и подаётся на маслоохладители (Р = 6 кг/см2, КР №3). Для выпуска воздуха из маслоохладителей при заполнении МОНов предусмотрены пробки и дроссели, находящиеся в верхней части теплообменника, которые обеспечивают также поступление воздуха при сливе масла с МОНов. Слив масла с МОНов производится по линии через вентиль в бак. Линия дренажа дросселей и линия слива соединены. Также по линии подачи. Проходя МОНы масло попадает в РТ, который поддерживает температуру масла путём частичного перепуска масла по байпасной линии (tо настройки 45о). При достижении 45о перепуск с байпасной линии прекращается и масло поступает через МОНы. Для повышения температуры масла регулировочный винт закручиваем (по часовой), а для снижения температуры выкручиваем (против часовой стрелки).
После РТ масло поступает на фильтр, где очищается REGOTMAS 631-1-0,6 (25мкм). Для определения ∆ Р на фильтрах служат отборы на входе и выходе фильтров (не более 2кг/см2). Охлаждённое и очищенное масло поступает в коллектор смазки. Регулирование давления масла в системе производится КР-1, КР-2 за счёт частичного сброса масла в МБН. КР-1 (1,6-2,0 кг/см2)-служит для ограничения Р в системе смазки. КР-2 (3,0-4,0 кг/см2) – предохраняет систему смазки от перегрузки при одновременном включении ПНС и ГНС. До КР-1, КР-2 устанавливается «САПФИР». КР-3, Р срабатывания = 6,0 кг/см2 и служит для ограничения выходного давления ГНС.
СИСТЕМА УПЛОТНЕНИЯ.
Служит для предотвращения перетока газа по ротору нагнетателя в отсек нагнетателя. Состоит:
1. Маслобак. 7. Гидроаккомулятор.
2. ПНУ. 8. Уплотнение.
3. Обратный клапан. 9. Маслоотводчик.
4. ГНУ. 10. Дегазатор.
|
5. РПД. 11. Запорная арматура.
6. Фильтр (10мкм). 12. Трубопроводы.
Часть масла циркулирующего в маслосистеме смазки отбирается насосами высокого давления и подаётся через систему вентилей в фильтра очистки масла высокого давления. (REGOTMAS 631-1-19. 10 мкм) На входном и выходном коллекторе есть система отбора, для определения ∆Р на фильтрах (6,0кг/см2). Из фильтров масло поступает в проточные гидроаккомуляторы. Предназначены для подачи масла в уплотнение при аварийном останове ГПА без включения насоса (5мин). В верхней части гидроаккумулятора расположены шариковые клапаны, служащие для выпуска воздуха или газа при заполнении гидроаккомулятора маслом. Для сообщения с газовой полостью при А.О. Гидроаккомуляторы снабжёны указателем уровня масла проточного типа, вентилем для слива масла с г-а. Гидроаккомулятор постоянно прокачивается на маслоотводчики, для стабилизации температурного режима масла в г-ре. Из гидроаккомулятора масло поступает на РПД-2М, который постоянно поддерживает Рм>Рг на 1,5-2,0 кг/см2 за счёт изменения слива части масла из системы уплотнения на всех режимах работы ГПА. Из РПД масло сливается в коллектор масла смазки нагнетателя. Вторая линия от гидроаккомуляторов идёт на уплотнения, где разделяется на два потока: часть сливается от подшипников в маслобак, часть под давлением направляется на маслоотводчики, где происходит частичное отделение масла и газа. Из маслоотводчиков масло поступает в дегозатор под давлением, где происходит полное отделение масла от газа и последующий его слив в м/б. Выделившийся в дегозаторе газ, через систему трубопроводов идёт в атмосферу. Выделившийся газ из маслоотводчиков через систему трубопроводов на РПД, на г-ры и в уравнительную линию уплотнений. При неисправности одного из маслоотводчиков, система позволяет работать на одном, через байпас. Слив масла из камеры м/г во время останова и пуска т/а, когда отсутствует давление газа, выполняется через маслоотводчики и клапаны (стояночные).
БЛОК МАСЛОНАСОСОВ.
|
Предназначен для обеспечения маслом системы смазки и уплотнения нагнетателя. Представляет собой шестеренчатый насос смазки и трехвинтовой насос уплотнения, работающих совместно.
Состоит из чугунного корпуса, в котором расположен редуктор и шестеренчатый насос.
Крутящий момент от ротора нагнетателя через полумуфту и торсионный вал передаётся на ведущую валшестерню. Валшестерня передаёт вращение на ведомую валшестерню винтового насоса и ведомую шестерню шестеренчатого насоса. Шестерня редуктора и ГНС установлены в подшипниках скольжения, смазка шестерен и шлицевых соединений редуктора производится через сверления в корпусе насоса и через трубопроводы соединённые с нагнетательным патрубком ГНС и ПНС.
ГНС – представляет собой шестеренчатый насос с наружным зациклением, с двумя одинаковыми шестернями. Шестерни находящиеся в зацеплении помещены в корпус. Стенки корпуса охватывают шестерни по внешним поверхностям шестерён с минимальным зазором. Вращение происходит в подшипниках скольжения. При выходе шестерён из зацепления происходит увеличение объёма между зубьями. И за счёт разряжения засасывает масло. Поступившее масло захватывается зубьями и переносится в виде дискретных объемов в полость отвода масла. Обратному перетоку масла с полости высокого давления, в полость низкого давления препятствует сопротивление зазоров между зубьями шестерён. Развитые поверхности трения вызывают значительные механические потери, поэтому КПД таких насосов не высок.
ГНУ – имеет один ведущий и два ведомых вала винта. Винты образованы тремя двузубыми шестернями с циклоидальным, а периферийные – цилиндрами, скользящими по поверхности корпуса находясь во вращении, винты образуют изолированные объёмы.
При вращении винтов эти объёмы передвигаются поступательно. В начале рабочего цикла каждый из них соединяется с полостью подвода масла. В конце - с полостью отвода масла, куда перенесённое масло вытесняется боковыми поверхностями винтов. Осевые силы действующие на винты (образованные в результате разности давления вх. и вых.) уравновешиваются за счёт подвода масла высокого давления по полостям внутри валов во внутреннюю полость подпятников. Тем самым обеспечивается смазка подшипников и уравнивание сил действующих на валы. Радиальные усилия действующие на валы воспринимаются корпусом.
Одно из преимуществ винтовых насосов заключается в том, что зацепление ведущего и ведомого винтов не является силовым. Силы давления масла действующие на боковые поверхности зубьев ведомых винтов со стороны полости отвода, стремятся вращать их в том же направлении, что и ведущий винт.
Благодаря удобному подводу и минимальным потерям, насосы обладают хорошей всасывающей способностью. Преимуществом является то, что вытеснение масла происходит непрерывным потоком.
|
|
Индивидуальные и групповые автопоилки: для животных. Схемы и конструкции...
Археология об основании Рима: Новые раскопки проясняют и такой острый дискуссионный вопрос, как дата самого возникновения Рима...
Архитектура электронного правительства: Единая архитектура – это методологический подход при создании системы управления государства, который строится...
История создания датчика движения: Первый прибор для обнаружения движения был изобретен немецким физиком Генрихом Герцем...
© cyberpedia.su 2017-2024 - Не является автором материалов. Исключительное право сохранено за автором текста.
Если вы не хотите, чтобы данный материал был у нас на сайте, перейдите по ссылке: Нарушение авторских прав. Мы поможем в написании вашей работы!