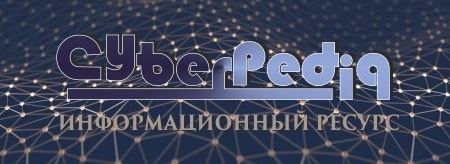
Общие условия выбора системы дренажа: Система дренажа выбирается в зависимости от характера защищаемого...
Своеобразие русской архитектуры: Основной материал – дерево – быстрота постройки, но недолговечность и необходимость деления...
Топ:
Техника безопасности при работе на пароконвектомате: К обслуживанию пароконвектомата допускаются лица, прошедшие технический минимум по эксплуатации оборудования...
Когда производится ограждение поезда, остановившегося на перегоне: Во всех случаях немедленно должно быть ограждено место препятствия для движения поездов на смежном пути двухпутного...
Устройство и оснащение процедурного кабинета: Решающая роль в обеспечении правильного лечения пациентов отводится процедурной медсестре...
Интересное:
Что нужно делать при лейкемии: Прежде всего, необходимо выяснить, не страдаете ли вы каким-либо душевным недугом...
Национальное богатство страны и его составляющие: для оценки элементов национального богатства используются...
Уполаживание и террасирование склонов: Если глубина оврага более 5 м необходимо устройство берм. Варианты использования оврагов для градостроительных целей...
Дисциплины:
![]() |
![]() |
5.00
из
|
Заказать работу |
Содержание книги
Поиск на нашем сайте
|
|
Анализ неисправностей при которых ДВС подлежит ремонту.
Описание видов операций выполняемых при ремонте двигателя …………..51
Раздел 2 Технология разборочно – сборочных работ ………..…………….....81
2.1. Разработка лабораторных и практических работ поста по ремонту ДВС, обучающихся учебной лаборатории………………………….…………………….81
Раздел 3 Техника безопасности при проведении работ……………………….90
3.1. Разработка мероприятий по технике безопасности на рабочих
местах поста по ремонту ДВС. Общие требования охраны труда…………..81
Раздел 4. Конструкторская часть………. ……………………………………...92
4.1. Анализ гаражных подъемных механизмов различных видов.
Назначение, описание конструкции, правила использования применяемого
подкатного крана………………………………………………………………...125
4.2. Анализ кантователей различных видов. Назначение, описание конструкции, правила использования кантователя, применяемого на учебном посту…….131
4.3. Оснащение поста учебной лаборатории приспособлениями, применяемыми при ремонте ДВС. Назначение, виды, описание используемых приспособле
иий……………………………………………………………………………......139
4.4. Оснащение поста учебной лаборатории инструментом, применяемым при ремонте ДВС. Назначение, виды, описание используемого инструмента….157
Раздел 5. Эконмическая часть………………………………………………..93
Заключение. …………………………………………………………..…….96
Список использованных источников………………………………………..99
Введение
Для эффективного функционирования современного производства, основанного на применении сложной техники, передовых технологий и характеризуемого большим количеством внутрипроизводственных связей, информационных потоков в сфере управления, необходимы четкая организация трудовых процессов, применение прогрессивных норм и нормативов, являющихся основой не только организации труда на рабочих местах, но и планирования, учета, анализа и регулирования производственных процессов.
|
Организация труда представляет собой систему рационального взаимодействия работников со средствами производства и друг с другом, основанную на определенных порядке построения и последовательности выполнения трудового процесса, направленную на получение высоких конечных социальных и экономических результатов.
Подчеркивая самостоятельность организации труда как части организации производства, необходимо отметить, что между всеми входящими в ее состав частями существует тесная взаимосвязь. Изменения в технике, происходящие под влиянием технического прогресса, влияют и на характер самого труда. Внедрение новых форм организации труда требует новых неординарных технических и технологических решений, внесения изменений в конструкции оборудования, оснастки и инструмента. Организация труда оказывает непосредственное влияние и на технологию производства, являясь средством установления трудоемкости работ, критерием оценки того или иного варианта технологического процесса. При распределении работы между работниками на основе ее разделения и кооперации организация труда рассматривается как одна из специальных функций управления.
Рабочее место является первичным звеном производственно-техноло-гической структуры предприятия (организации), той элементарной ячейкой, в которой осуществляются процесс производства, его обслуживание и управле
ние. Именно здесь происходит соединение трех основных элементов этого процесса (живого труда, предметов и средств труда) и достигаются его главные цели – производство материальных и духовных благ (предметов труда), оказание услуг либо технико-экономическое обеспечение и управление этими процессами.
|
Оно представляет собой закрепленную за отдельным рабочим или группой рабочих часть производственной площади, оснащенную необходимыми технологическим, вспомогательным, подъемно-транспортным оборудованием, технологической и организационной оснастками, а также предметами труда, предназначенными для выполнения определенной части производственного процесса.
Каждое рабочее место имеет свои специфические особенности, связанные с особенностями организации производственного процесса, многообразием форм конкретного труда. Вид рабочего места определяется такими факторами, как тип производства, уровень разделения и кооперации труда, место выполнения работы, содержание труда, степень механизации и автоматизации, число единиц оборудования на рабочем месте. Тип производства, в свою очередь, связан со специализацией рабочих мест и означает закрепление за каждым из них группы однородных работ (операций).
Целью данной работы является изучить, проанализировать, оборудование применяемое для ремонта двигателей, и на основе полученных результатов, оснастить рабочий пост учебной лаборатории минимальным, но основным, необходимым оборудованием для обучения студентов.
Стук коленчатого вала.
Причинами могут быть: ослабление болтов крепления маховика; увеличенный зазор между шейками и вкладышами коренных подшипников; работа двигателя на несоответствующем масле.
Для устранения причин неисправности необходимо:
Стук шатунных подшипников.
Резкий стук шатунных подшипников прослушивается на коренном ходу
двигателя при резком открытии дроссельной заслонки. Место стука определяют, отключая по очереди свечи зажигания. Причинами могут быть: недостаточное давление масла; увеличенный зазор между шатунными шейками коленчатого вала и вкладышами; не параллельность осей верхней и нижней головок шатуна; работа на масле несоответствующей марки.
|
Для устранения причин неисправности необходимо:
Перегрев двигателя.
Причинами могут быть: слабое натяжение ремня привода жидкостного насоса и генератора; недостаточное количество жидкости в системе охлаждения; неправильная установка начального момента зажигания; загрязнение наружного момента зажигания; неисправность термостата; неисправность электродвигателя вентилятора; неисправность жидкостного насоса; применение низкооктанового бензина.
Для устранения причин неисправности необходимо:
ЛАБОРАТОРНАЯ РАБОТА № 1
Порядок выполнения работы
1. Изучить методику диагностирования двигателя по величине утечки воздуха.
2. Выполнить практическую работу по диагностированию цилиндропоршневой группы по величине компрессии и сделать вывод по ее состоянию.
3. Составить таблицу, где в первой графе указать проверяемые характеристики, а во второй графе записать свои наблюдения и их числовые значения, на указанном преподавателем двигателе.
|
4. Составить отчет о работе в соответствии с пп.1 – 3, дать ответ на контрольные вопросы и сделать вывод о ЦПК в целом
Таблица – технологическая карта.
Технологическая карта проверки состояния двигателя с помощью прибора К-69М по утечке воздуха.
1. Проверка износа поршневых колец. - установить поршень проверяемого цилиндра в положение, соответствующее началу такта сжатия (все клапаны закрыты) - затем через наконечник 6 в отверстие для форсунки или свечи зажигания подают сжатый воздух под давлением 0,4 МПа. |
2. Проверка утечки воздуха через клапаны при неплотной их посадке в седлах определяют на слух. - установить поршень проверяемого цилиндра в положение, соответствующее началу такта сжатия (все клапаны закрыты) - затем через наконечник 6 в отверстие для форсунки или свечи зажигания подают сжатый воздух под давлением 0,4 МПа. | |
3. Проверка герметичности прокладки головки блока цилиндров. - по появлению пузырьков воздуха в горловине радиатора или в стыке головки с блоком цилиндров, смоченного мыльным раствором | |
4. Проверка компрессии в цилинд. двигателя. - поршень цилиндра устанавливают в ВМТ такта сжатия (когда оба клапана закрыты), затормаживают коленчатый вал двигателя и автомобиль включением стояночной тормозной системы. - вворачивают вместо свечи зажигания штуцер, к которому подсоединяют шланг от компрессора, и подают в цилиндр сжатый воздух под давлением 200—300 Па, либо подают воздух от компрессора через компрессометр, если последний имеет соответствующий штуцер для подвода сжатого воздуха, либо используют для этого специальный пневмотестер К-272 или прибор К-69М (см. рис. 2.) |
Выводы: _________________________________________________________________________________________________________________________________________________________________________________________________________________________________________________________________________________________________________
Контрольные вопросы
1. В чем заключается принципиальная разница в диагностировании ЦПГ с помощью замера компрессии и величины утечки воздуха.
ПРАКТИЧЕСКАЯ РАБОТА № 1
ТЕМА: Расчёт толщины шайб для установки оптимальных зазоров в газораспределительном механизме двигателя ВАЗ-2109.
Цель работы: научиться выполнять расчёт толщины шайб для регулировки зазоров в ГРМ двигателя ВАЗ-2109.
Содержание работы: подготовка исходных данных, согласно индивидуального задания; расчёт ремонтных размеров шайб; оформление отчета о работе.
Оборудование и материалы: методическое пособие, справочная литература, компьютер.
Индивидуальное задание. Определить размеры и выполнить расчёт толщины шайб для ГРМ двигателя ВАЗ-2109.
Номинальный зазор А между кулачками распределительного вала и регулировочными шайбами на холодном двигателе должен быть 0,2 + 0,05 мм для впускных клапанов и 0,35 + 0,05 мм для выпускных клапанов. Зазор регулируется подбором толщины регулировочных шайб. В звпасные части поставляются регулировочные шайбы толщиной от 3 до 4,5 мм с интервалом через каждые 0,05 мм. Толщина шайбы маркируется на ее поверхности.
|
1. Определение толщины регулировочной шайбы:
Н = В + (А – С),
где А – замеренный зазор, мм; В – Толщина снятой шайбы, мм;
С – номинальный зазор, мм; Н – толщина новой шайбы, мм;
ПРИМЕР: Допустим А = 0,26 мм; В = 3,75 мм; С = 0,2 мм (для впускного экзамена), тогда: Н = 3,75 + (0,26 – 0,2) = 3,81 мм. В пределах допуска на зазор + 0,05 мм принимаем толщину новой шайбы равную 3,8 мм.
2. Решение:
Выводы: _________________________________________________________________________________________________________________________________________________________________________________________________________________________________________________________________________________________________________
ЛАБОРАТОРНАЯ РАБОТА № 2
Порядок выполнения работы
1. Изучить методику протяжки головки блока цилиндров, проверку зазоров в газораспределительном механизме.
2. Выполнить практическую работу по протяжке головки блока цилиндров, проверке зазоров в газораспределительном механизме.
3. Составить таблицу, где в первой графе указать методику протяжки головки блока цилиндров, а во второй графе порядок проверки зазоров в газораспределительном механизме, на указанном преподавателем двигателе.
4. Составить отчет о работе в соответствии с пп.1 – 3, дать ответ на контрольные вопросы и сделать вывод.
Отчет о работе
Схема протяжки головки блока цилиндров двигателя ВАЗ-2109
Методика протяжки головки блока цилиндров. | |
Поверните коленчатый вал так, чтобы поршни находились в средней части цилиндров | |
1 прием — затяните болты моментом 20 Н·м (2 кгс·м); | |
2 прием — затяните болты моментом 69,4–85,7 Н·м (7,1–8,7 кгс·м); | |
3 прием — доверните болты на 90°; | |
4 прием — снова доверните все болты на 90°. | |
Порядок проверки зазоров в газораспределительном механизме. | |
— снимите крышку головки цилиндров и переднюю защитную крышку зубчатого ремня; | |
— выверните свечи зажигания ключом 67.7812.9515 и удалите масло из верхней части головки цилиндров; | |
— осмотрите поверхность кулачков распределительного вала: на них не должно быть задиров, раковин, износа и глубоких рисок; | |
— установите на шпильки крепления крышки головки цилиндров приспособление 67.7800.9503 для утапливания толкателей клапанов; | |
— поверните коленчатый вал до совмещения установочных меток на шкиве и задней крышке зубчатого ремня, а затем доверните его еще на 40–50° (2,5–3 зуба на шкиве распределительного вала). При этом в первом цилиндре будет фаза сгорания; | |
— проверьте набором щупов зазоры у 1-го и 3-го кулачков распределительного вала | |
— если зазор отличается от нормы, то приспособлением 67.7800.9503 утопите толкатель и зафиксируйте его в нижнем положении, установив между краем толкателя и распределительным валом фиксатор 67.7800.9504; | |
— приспособлением 67.7800.9505 удалите регулировочную шайбу и микрометром измерьте ее толщину; | |
— определите толщину новой шайбы |
Порядок регулировки зазоров в механизме привода клапанов
Выводы: __________________________________________________________________
____________________________________________________________________________
_________________________________________________________________________
ЛАБОРАТОРНАЯ РАБОТА № 3
Порядок выполнения работы
1. Изучить методику разборки двигателя.
2. Выполнить практическую работу по разборке двигателя.
3. Составить таблицу, где в первой графе указать последовательность разборки, а во второй графе записать свои наблюдения при выполнении разборочных работ на двигателе.
4. Составить отчет о работе в соответствии с пп.1 – 3, дать ответ на контрольные вопросы и сделать вывод.
2. Порядок разборки двигателя.
Выводы: ____________________________________________________________________________________________________________________________________________________________________________________________________________________________
Контрольные вопросы
1.В чем заключается особенности разборки двигателя ВАЗ-2109.
ЛАБОРАТОРНАЯ РАБОТА № 4
Задание
Описать параметры расположения поясов обмера гильзы цилиндров.
_______________________________________________________________________________________________________________________________________________________________________________________________________________________________________
ЛАБОРАТОРНАЯ РАБОТА № 5
ЛАБОРАТОРНАЯ РАБОТА № 6
Таблица 3 - Результаты замеров кулачков распределительного вала
Схема замеров | Наименование кулачка | Пояс замеров | Номер кулачка | |||
1, 2 | 3, 4 | 5, 6 | 7, 8 | |||
Впускной 2, 3, 6, 7 | ||||||
Высота кулачка | ||||||
Выпускной 1, 4, 5, 8 | ||||||
Высота кулачка |
Выводы: _____________________________________________________________________________________________________________________________________________________________________________________________________________________________________________________________________________________________________________________
ЛАБОРАТОРНАЯ РАБОТА № 7
ТЕМА: Дефектация шатуна
Цель работы: научиться выполнять дефектацию шатуна.
Содержание работы: подготовка исходных данных для дефектации; определение технического состояния дефектуемых конструктивных элементов; сортировка деталей по результатам контроля; назначение способов ремонта и содержания операций по дефектной технологии; оформление отчета о работе.
Оборудование и материалы: верстак слесарный с тисками, динамометрический ключ, штангенциркуль ШЦ 2-250-0,1 ГОСТ 166-89, микрометры МК-25 и МК-75 ГОСТ 6507-90, нутромеры индикаторные с пределами измерений 18-50 и 50-100 ГОСТ 868-82, дефектуемые шатуны, компьютер.
Характеристика шатуна
Вид заготовки __________________________________
Материал детали __________________________________
Номинальный диаметр отверстия верхней головки шатуна, мм, D = ____
Номинальный диаметр отверстия нижней головки шатуна, мм, d = ____
Расстояние между осями отверстий верхней и нижней головок, мм, L = _____
Результаты замеров шатунов
Таблица
№ шатуна | Диаметр верхней головки, мм | Диаметр нижней головки, мм | Расстояние между осями отверстий головок, мм |
Выводы: ________________________________________________________________________________________________________________________________________________________________________________________________________________________________________________________________________________________________________________________________________________________________________________________________________________________________________________________________________________________________________________________________________________
Контрольные вопросы и задания
1. Перечислите конструктивные элементы шатуна, подлежащие дефектации, и технологические параметры их характеризующие.
2. Как определить состояние отверстия нижней головки?
3. Как определить изгиб шатуна? Причины деформации шатуна.
4. Как определить скручивание шатуна?
ЛАБОРАТОРНАЯ РАБОТА № 8
ТЕМА: Дефектация пружин
Цель работы: научиться выполнять дефектацию пружин.
Содержание работы: изучение конструкций пружин клапанов двигателя, условий их работы и возможных дефектов; изучение способов и средств дефектации пружин; изучение устройства прибора для проверки упругости пружин; дефектация пружин; оформление отчета.
Оборудование и материалы: пресс винтовой; приспособление для контроля пружин; пружина эталонная; пружины, подлежащие дефектации; компьютер.
1. Характеристика пружины
Вид пружины:
Длина пружины в свободном состоянии, L _______ мм
Длина пружины под нагрузкой _______Н, L1 ______ мм
Длина пружины под нагрузкой _______Н, L2 ______ мм
2. Результаты дефектации пружин внешним осмотром
Пружина № 1 ______________________________________________________
__________________________________________________________________
Пружина № 2 ______________________________________________________
__________________________________________________________________
Пружина № 3______________________________________________________
__________________________________________________________________
Пружина № 4______________________________________________________
__________________________________________________________________
1. Результаты замеров при испытании пружин под нагрузкой
№ пружины | Длина пружины L, мм без нагрузки | Длина L1, мм при нагрузке _____ Н | Длина L2, мм при нагрузке ___ Н | |
Выводы: ____________________________________________________________________________________________________________________________________________________________________________________________________________________________
Контрольные вопросы и задания
1. К каким последствиям в работе механизмов двигателя, сцепления, тормозов могут привести дефекты пружин?
2. Перечислить технические требования чертежа к элементам пружин.
3. Назовите возможные дефекты пружин и способы дефектации.
ПРАКТИЧЕСКАЯ РАБОТА № 2
ТЕМА: Расчёт размерных групп при комплектовании поршней с гильзами цилиндров
Цель работы: научиться выполнять расчёт размерных групп поршней и гильз цилиндров при комплектовании.
Содержание работы: подготовка исходных данных, согласно индивидуального задания; расчёт ремонтных размеров и классов деталей; оформление отчета о работе.
Оборудование и материалы: методическое пособие, справочная литература, компьютер.
Индивидуальное задание. Определить ремонтные размеры и выполнить расчёт размерных групп сопрягаемых деталей (поршень-цилиндр) для двигателя _______________. Номинальный диаметр поршня dн __________ мм, номинальный диаметр цилиндра Dн _______ мм. Имеются ___ ремонтных размеров с межремонтным интервалом (γ) через ____мм, каждый ремонтный размер имеет ____ групп (А, В, С, D, Е), с интервалом через б = ___ мм.
1. Расчёт ремонтных размеров гильз цилиндров двигателя
1.1. Определяем первый ремонтный размер гильз цилиндра Dp1, мм.
Dp1 = Dн + γ = (1)
1.2. Определяем классы первого ремонтного размера.
А = Dp1 + б = (2)
В = Dp1 + 2×б = (3)
С = Dp1 + 3×б = (4)
D = Dp1 + 4×б = (5)
Е = Dp1 + 5×б = (6)
1.3. Определяем второй ремонтный размер гильз цилиндра Dp2, мм.
Dp2 = Dн + 2×γ = (7)
1.4. Определяем классы второго ремонтного размера.
А = Dp2 + б = (8)
В = Dp2 + 2×б = (9)
С = Dp2 + 3×б = (10)
D = Dp2 + 4×б = (11)
Е = Dp2 + 5×б = (12)
2. Расчёт ремонтных размеров поршней двигателя
2.1. Определяем первый ремонтный размер поршней dр1, мм.
dр1 = dн - γ = (13)
2.2. Определяем классы первого ремонтного размера.
А = dр1 + б = (14)
В = dр1 + 2×б = (15)
С = dр1 + 3×б = (16)
D = dр1 + 4×б = (17)
Е = dр1 + 5×б = (18)
2.3. Определяем второй ремонтный размер поршня dр2, мм.
dр2 = dн - 2×γ = (19)
2.4. Определяем классы второго ремонтного размера.
А = dр2 + б = (20)
В = dр2 + 2×б = (21)
С = dр2 + 3×б = (22)
D = dр2 + 4×б = (23)
Е = dр2 + 5×б = (24)
Выводы: ____________________________________________________________________________________________________________________________________________________________________________________________________________________________
__________________________________________________________________________________________________________________________________________________________
ПРАКТИЧЕСКАЯ РАБОТА № 3
ЛАБОРАТОРНАЯ РАБОТА № 9
ЛАБОРАТОРНАЯ РАБОТА № 10
ЛАБОРАТОРНАЯ РАБОТА № 11
Тема: Ремонт седел клапанов
Цель работы: формирование знаний и умений по разработке и оформлению слесарной ремонтной операции, приобретение практических навыков по ремонту седла клапана двигателя.
Содержание работы: подготовка исходных данных и материалов; определение технического состояния восстанавливаемых конструктивных элементов; изучение способов ремонта и содержания переходов операционной технологии; изучение и оформление технологической карты слесарных операций на ремонт фаски седла клапана; оформление отчета о работе.
Оборудование и материалы: приспособление для установки головки блока цилиндров; головка блока цилиндров; клапаны; приспособление для притирки клапанов; притирочная паста; методическое пособие; компьютер.
1.Технологическая карта слесарной операции на ремонт фаски седла клапана
Таблица
№ перехода | Содержание перехода | Технологический режим | Приспособление | Инструмент |
Установить головку цилиндров на приспособление | Вручную, плоскостью разъёма головки блока вверх | Подставка с опорными площадками с уклоном ![]() | ||
Зенковать рабочую поверхность (фаску) седла «как чисто» | Вручную, усилие 2-3 кгС, направляющий хвостовик смазать | Оправка, вороток | Зенковка с ![]() | |
Зенковать технологичес-кую фаску
под ![]() | Вручную, усилие 2-3 кгС, направляющий хвостовик смазать | Оправка, вороток | Зенковка под ![]() | |
Зенковать технологичес-кую фаску
под ![]() | Вручную, усилие 2-3 кгС, выдержать ширину ____ мм | Оправка, вороток | Зенковка под ![]() | |
Чистовое зенкование рабочей фаски под ![]() | Вручную, усилие 0,8 кгС. Выдержать ширину ___ мм. Хвостовик смазать. | Оправка, вороток | Зенковка чистовая под ![]() |
Окончание таблицы
№ перехода | Содержание перехода | Технологический режим | Приспособление | Инструмент |
Притереть рабочую фаску | Вручную, выдерживая ширину фаски ___ мм. Усилие 0,8 кгС, хвостовик смазать | Приспособление для притирки седла клапана | Притирочная паста, клапан, головка блока | |
Контрольная | Вручную | Приспособления для контроля биения и испытания на герметичность | Индикатор рычажный. |
ЛАБОРАТОРНАЯ РАБОТА № 12
Исходные данные
Материал обрабатываемой поверхности детали _________________
Твёрдость обрабатываемой поверхности детали ________ HRC.
Оборудование ______________________________________________
Режущий инструмент ________________________________________
Диаметр обрабатываемой поверхности, мм ________
Длина обрабатываемой поверхности, мм ________
Шероховатость рабочей поверхности фаски клапана, мкм _________
Квалитет точности диаметра фаски клапана _____________________
Угол рабочей фаски головки клапана к оси стержня, град __________
Биение рабочей поверхности фаски головки клапана относительно стержня не более, мм_____
ЛАБОРАТОРНАЯ РАБОТА № 13
Исходные данные
Материал обрабатываемой поверхности детали ________________________
Твёрдость обрабатываемой поверхности детали _______________________
Оборудование ____________________________________________________
Режущий инструмент ______________________________________________
Диаметр обрабатываемой поверхности, мм ________
Длина обрабатываемой поверхности, мм ________
Шероховатость рабочей поверхности отверстия гильзы, мкм __________
Квалитет точности диаметра отверстия гильзы _____________
Нецилиндричность отверстия не более, мм ________
Радиальное биение посадочных поясков относительно оси отверстия не более, мм _______
Практическая часть работы
Контроль рабочей поверхности отверстия гильзы цилиндра двигателя на соответствие рабочему чертежу и техническим требованиям.
Результаты контроля цилиндра двигателя после хонингования
диаметр отверстия гильзы:
- нецилиндричность отверстия, мм _______;
-радиальное биение посадочных поясков относительно оси отверстия не более, мм ______;
-шероховатость рабочей поверхности Rа = _______ мкм.
Выводы: __________________________________________________________________
__________________________________________________________________
Контрольные вопросы и задания
1. В какой последовательности назначается режим резания при растачивании цилиндра двигателя?
2. Как отцентровать растачиваемый цилиндр по расточному резцу?
3. Как выставить резец на заданную глубину резания?
4. Как произвести технический контроль расточенного цилиндра?
ЛАБОРАТОРНАЯ РАБОТА № 14
Исходные данные
Материал обрабатываемой поверхности детали ________________________
Твёрдость обрабатываемой поверхности детали _______________________
Оборудование ____________________________________________________
Режущий инструмент ______________________________________________
Диаметр обрабатываемой поверхности, мм ________
Длина обрабатываемой поверхности, мм ________
Шероховатость рабочей поверхности отверстия гильзы, мкм __________
Квалитет точности диаметра отверстия гильзы_____________
Нецилиндричность отверстия не более, мм ________
Радиальное биение посадочных поясков относительно оси отверстия не более, мм _______
Расчётная часть работы
Расчёты по определению размеров поверхностей, режимов обработки и норм времени.
2.1. Определяем припуск под хонингование Zхон, мм;
Zхон = Dрр - D = (37)
где Dрр – диаметр отверстия ремонтного размера под поршень по нижнему предельному отклонению,Dрр = ______ мм;
D - диаметр расточенного отверстия под поршень, D = ______ мм.
2.2. Определяем длину бруска, мм
l бр = = (0,2…0,4) l отв = (38)
где: l отв – длина хонингуемого отверстия, l отв = ______ мм.
2.3. Выбираем тип, размеры и характеристику хонинговальных брусков [2, с.102]. l бр = _____ мм.
2.4. Выбираем по нормативу режимов резания рекомендуемые:
- скорость возвратно-поступательное движение хонинговальной головки (Vвп), м/мин: предварительная 17…22, окончательная 10…15;
- вращательное движение хонинговальной головки (окружная скорость Vок), м/мин: предварительная 40…80; окончательная 30…50.
2.5. Определяем частоту вращения шпинделя, об/мин
n = = (39)
где Vок - окружная скорость хонинговальной головки, принимаем Vок = 40 м/мин;
D – диаметр хонингуемого отверстия, мм.
Принимаем по паспорту станка nф = _________ об/мин.
2.6. Определяем величину перебега брусков за пределы отверстия при возвратно-поступательном движении, мм
l пер = = (40)
Принимаем l пер = 15 мм в каждую сторону [4,с. 217].
2.7. Определяем длину рабочего хода шпиндельной бабки, мм
Lрх = l отв + 2· l пер - l бр (41)
2.8. Определяем машинное время хонингования, мин
tм = , (42)
где n1 – число двойных ходов, необходимое для снятия всего припуска; n2 – число двойных ходов шпиндельной бабки в минуту.
n1 = = (43)
где: припуск на хонингование на сторону;
b – слой металла, снимаемый за один двойной ход; для чугуна b = 0,002 мм.
2.9. Определяем число двойных ходов хонинговальной головки в минуту:
n2 = = (44)
где Vвп – скорость возвратно-поступательного движения хонинговальной головки, Vвп = 18 м/мин.
Принимаем число двойных ходов шпиндельной бабки по паспорту станка
n2 =_______ дв. ход /мин.
tм =
Практическая часть работы
Контроль рабочей поверхности отверстия гильзы цилиндра двигателя на соответствие рабочему чертежу и техническим требованиям.
Результаты контроля цилиндра двигателя после хонингования
диаметр отверстия гильзы:
- нецилиндричность отверстия, мм _______;
- радиальное биение посадочных поясков относительно оси отверстия не более, мм ______;
- шероховатость рабочей поверхности Rа = _______ мкм.
Выводы: __________________________________________________________________
_____________________________________________________________________________
__________________________________________________________________
Контрольные вопросы и задания
1. В какой последовательности выполняется хонинговальная операция?
2. Как проверить качество доводки цилиндра двигателя?
3. Отчего зависит величина перебега брусков за пределы отверстия при возвратно-поступательном движении?
Балочные траверсы
Балочные траверсы выполняют в виде металлических балок из двух швеллеров, обращенных полками друг к другу, соединенных накладами и имеющих по концам блоки с перекинутыми через них стропами. Такая система подвески стропов обеспечивает равномерное их натяжение и равномерную передачу нагрузки на все четыре точки захвата.
Решетчаты траверсы представляют собой металлические треугольные сварные фермы. Траверсами поднимают длинномерные конструкции.
Тяжелые большеразмерные элементы (например, плиты покрытий промышленных зданий размером 3x12 м) поднимают пространственными траверсами.
Для подъема тяжелых элементов со смещенным центром тяжести (например, объемных элементов размером на комнату) применяют траверсы с системой балансировки. В качестве сменного оборудования к траверсе могут быть подвешены облегченные стропы, клещевые захваты, вакуумные присоски, кантователи для колонн и др.
Захваты (рис.) предназначены для беспетельного подъема конструкций. По характеру удерживания конструкции различают захваты:
1. механические, в которых конструкция удерживается на весу за счет подхвата за выступающие части, зажима или фрикционного зацепления;
2. электромагнитные, используемые для подъема металлических листовых конструкций;
3. вакуумные, в которых конструкция удерживается за счет разрежения, создаваемого в вакуум-камере или вакуум-присосках.
Вакуумными захватами поднимают тонкостенные конструкции. Они состоят из вакуум-камер, рукавов и вакуум-насоса. Наиболее эффективно вакуумные захваты могут использоваться в стационарных условиях на предприятиях строительной индустрии. На строительной площадке захват подвешивают к грузовому крюку монтажного крана, а пульт управления устанавливают в кабине крановщика.
В зависимости от назначения захваты имеют различные устройства для кантования изделий в процессе подъема, а также могут быть оборудован
|
|
Кормораздатчик мобильный электрифицированный: схема и процесс работы устройства...
Археология об основании Рима: Новые раскопки проясняют и такой острый дискуссионный вопрос, как дата самого возникновения Рима...
Типы оградительных сооружений в морском порту: По расположению оградительных сооружений в плане различают волноломы, обе оконечности...
Двойное оплодотворение у цветковых растений: Оплодотворение - это процесс слияния мужской и женской половых клеток с образованием зиготы...
© cyberpedia.su 2017-2024 - Не является автором материалов. Исключительное право сохранено за автором текста.
Если вы не хотите, чтобы данный материал был у нас на сайте, перейдите по ссылке: Нарушение авторских прав. Мы поможем в написании вашей работы!