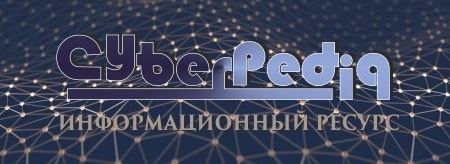
Механическое удерживание земляных масс: Механическое удерживание земляных масс на склоне обеспечивают контрфорсными сооружениями различных конструкций...
Эмиссия газов от очистных сооружений канализации: В последние годы внимание мирового сообщества сосредоточено на экологических проблемах...
Топ:
Оснащения врачебно-сестринской бригады.
Методика измерений сопротивления растеканию тока анодного заземления: Анодный заземлитель (анод) – проводник, погруженный в электролитическую среду (грунт, раствор электролита) и подключенный к положительному...
Определение места расположения распределительного центра: Фирма реализует продукцию на рынках сбыта и имеет постоянных поставщиков в разных регионах. Увеличение объема продаж...
Интересное:
Распространение рака на другие отдаленные от желудка органы: Характерных симптомов рака желудка не существует. Выраженные симптомы появляются, когда опухоль...
Что нужно делать при лейкемии: Прежде всего, необходимо выяснить, не страдаете ли вы каким-либо душевным недугом...
Принципы управления денежными потоками: одним из методов контроля за состоянием денежной наличности является...
Дисциплины:
![]() |
![]() |
5.00
из
|
Заказать работу |
|
|
1. Минимальная частота питающего тока:
, (4.4.1)
где м – удельное электросопротивление металла, Ом·м;
м – относительная магнитная проницаемость металла;
d ′м – диаметр металла, м (для жидкого металла dм = d0, для металлолома dм – средний размер куска металла).
2. Полезная вместимость тигля, т:
m = ( 1 +
2 +
3 +
4)∙П + mб, (4.4.2)
где 1 – время загрузки шихты впечь, ч;
2 – время плавки, ч;
3 – время доводки металла, ч;
4 – время слива металла из печи, ч;
П – производительность печи, т/ч;
mб – масса болота печи (при работе с болотом), т.
3. Объем жидкого металла в печи, м3:
, (4.4.3)
где м – плотность жидкого металла, т/м3.
4. Внутренний диаметр тигля, м:
. (4.4.4)
5. Высота тигля, м:
hм = B · d0. (4.4.5)
6. Толщина стенки S1 тигля, мм: (0,25…0,3)d0 до 0,5 т; (0,15 … 0,25)d0 для 0,5 – 3 т и (0,1…0,15)d0 свыше 15 т.
7. Толщина S2 изоляционного слоя между тиглем и индуктором, м: 0,005 до 3 т; 0,005…0,01 для 3…15 т; 0,01…0,015 свыше 15 т.
8. Внутренний диаметр индуктора, м:
dи= d0+2(S1 + S2). (4.4.6)
9. Полезная тепловая мощность печи, кВт:
Рпол= WтеорП′, (4.4.7)
где Wтеор – теоретический удельный расход энергии для расплавления металла, кВт.ч/т (см. прил. 5);
П′ – плавильная производительность печи, т/ч:
. (4.4.8)
10. Полезная активная мощность печи, кВт:
, (4.4.9)
|
где терм – термический КПД печи, равный 0,7…0,9.
11. Высота индуктора, м:
hи = (0,7…1,3)∙hм. (4.4.10)
Для печей, работающих на повышенной частоте, высота индуктора больше высоты металла в тигле; для печей, работающих на промышленной частоте, она меньше высоты металла в тигле, м.
12. Глубина проникновения тока в металл, м:
, (4.4.11)
где f – частота тока, питающего индуктор, Гц.
13. Напряженность магнитного поля в индукторе, А/м:
, (4.4.12)
где КS – коэффициент, учитывающий самоиндукцию и взаимоиндукцию между индуктором и металлом и равный 0,85…0,95;
Ам – поправочный коэффициент активной мощности, учитывающий кривизну металла в тигле и зависящий от отношения диаметра к глубине проникновения тока в него. Определяют по сплошной линии (прил. 6).
14. Реактивная мощность, выделяемая в металле, квар:
, (4.4.13)
где Rм – поправочный коэффициент реактивной мощности.
15. Реактивная мощность, выделяющаяся в зазоре между металлом и индуктором, квар:
(4.4.14)
16. Толщина стенки трубки индуктора, мм. Из условий минимальных потерь активной мощности в индукторе:
Sm =103·1,3∆. (4.4.15)
17. Потери активной мощности в индукторе, кВт:
(4.4.16)
где и – удельное электросопротивление материала индуктора, Ом·м;
и – относительная магнитная проницаемость материала индуктора;
Аи – поправочный коэффициент активной мощности, учитывающий кривизну индуктора. Определяют по пунктирной линии для разных dв/∆u;
Кз.и – коэффициент заполнения индуктора, равный 0,7…0,9.
18. Реактивная мощность, выделяющаяся в индукторе, квар:
, (4.4.17)
где R и – поправочный коэффициент мощности, учитывающий кривизну индуктора, определяют по штриховой линии для разных dв/∆u (прил. 6).
|
19. Общая активная мощность, кВт:
Р = Рм+Ри. (4.4.18)
20. Общая реактивная (индуктивная) мощность, квар:
Q = Qм+ Qв+ Qн. (4.4.19)
21. Полная мощность системы индуктор-металл, кВ·А:
. (4.4.20)
22. Сила тока в индукторе, А:
, (4.4.21)
где Uи – напряжение в индукторе, В.
23. Число витков в индукторе, шт.:
. (4.4.22)
24. Шаг витка индуктора, м:
. (4.4.23)
25. Высота трубки индуктора, м:
. (4.4.24)
26. Толщина изоляции между витками, м:
. (4.4.25)
27. Напряжение тока между витками индуктора, В:
. (4.4.26)
28. Напряжение на 1 см изоляции между витками, В:
, (4.4.27)
допускается не более 200 В на 1 см.
30. Ширина трубки индуктора. Размер трубки в поперечном сечении определяют из условия, при котором плотность тока должна быть не более 20 А/мм2.
29. Коэффициент мощности печи:
. (4.4.28)
30. Емкость конденсаторной батареи, мкФ:
(4.4.29)
где – напряжение на конденсаторе, В.
Мощность конденсаторной батареи Uк, квар, должна быть равна общей реактивной (индуктивной) мощности, т. е. Qс = Q.
Тогда контур (индуктор – конденсаторная батарея) рассчитывают на полную мощность системы S, а подводящую электрическую линию – только на общую активную мощность Р.
31. Общая площадь поперечного сечения магнитопровода, м2:
(4.4.30)
где В – индукция в магнитопроводе, В/м2, при частоте 50 Гц (0,6…1).
32. Площадь поперечного сечения одного магнитопровода, см2:
(4.4.31)
где Nмг – число пакетов магнитопровода вокруг индуктора.
Расчет канальной печи
1. Полезная тепловая мощность, передаваемая жидкому металлу, кВт:
Рпол= Wтеор·∆ t ·П, (4.5.1)
где Wтеор – теоретический удельный расход энергии для перегрева металла на 1 ºС, кВт·ч/т (для чугуна 0,3 кВт·ч/т);
|
∆t – температура перегрева металла в печи, ºС;
П – производительность печи, т/ч.
2. Активная мощность печи, кВт:
(4.5.2)
где терм – термический КПД печи, равный 0,7…0,85.
3. Активная мощность индуктора, кВт:
(4.5.3)
где N – число индукторов на печи.
4. Площадь поперечного сечения стержня магнитопровода индуктора, см2:
, (4.5.4)
где – коэффициент, учитывающий отношение массы стали магнитопровода к массе меди катушки индуктора: при воздушном охлаждении катушки
= 5…25, при водяном
= 0,9… 1,3;
В – магнитная индукция в стержне магнитопровода, Тл;
j1 – допустимая плотность электрического тока в катушке: при водяном j1 ≤ 20 А/мм2;
сos – коэффициент мощности индуктора (для чугуна 0,5…0,7, для алюминия 0,35…0,5).
5. Диаметр стержня магнитопровода, мм:
, (4.5.5)
где Кd – коэффициент заполнения окружности стержнем, Кd = 0,78… 0,88.
6. Наружный диаметр катушки, мм:
dкат = dмг+ 2(Sз + Sкат), (4.5.6)
где Sз – толщина зазора между стержнем магнитопровода и катушки,
Sз = 10…20 мм;
Sкат – толщина катушки, Sкат = 20…50 мм.
6. Внутренний диаметр канала, мм:
dк.в = dкат+ 2(S1 + S2), (4.5.7)
где S1 – толщина футеровки между каналом и катушкой, S1 = 65…150 мм;
S2 – толщина зазора между катушкой и футеровкой, S2 = 10…30 мм.
8. Ширина канала вк, мм; для чугуна ширина канала 60…120 мм, для алюминия – до 150 мм.
9. Длина канала lк, мм: построив по полученным данным эскиз индуктора, находим длину канала (по средней линии), представляющего собой часть замкнутого контура, расположенного в индукторе.
10. Площадь поперечного сечения канала, м2:
, (4.5.8)
где j2 – плотность тока в канале, А/м2, для меди j2 ≤ 13·106, для латуни j2 ≤ 9·106, для чугуна j2 ≤ 6·106;
м – удельное электросопротивление металла, Ом·м.
11. Форма поперечного сечения канала. В поперечном сечении канал может иметь форму окружности, эллипса, овала или другой фигуры, не имеющей углов. Размеры поперечного сечения канала определяют с учетом уже найденных площади поперечного сечения и ширины канала.
|
12. Активное сопротивление канала, Ом:
(4.5.9)
13. Индуктивность канала:
L = Lвнеш+ Lвн, (4.5.10)
где Lвнеш и Lвн – внешняя и внутренняя индуктивность канала, Гн; Lвнеш = 2·10-7lp·lк·ln(R1/R2), Lвн = 10-7lк/2,
R1 – расстояние от оси канала до катушки плюс глубина проникновения тока в катушку;
R2 – расстояние от оси канала до поверхности канала, т. е. R2 = bк/2;
lp – коэффициент, учитывающий рассеяние энергии индуктором в зависимости от индукции в стержне. При В до 1 Тл lр = 1; при В = 1,5 Тл lр = 1,2; при В = 1,85 Тл lр = 1,55.
14. Индуктивное сопротивление канала, Ом:
Х L =2 fL. (4.5.11)
15. Полное сопротивление канала, Ом:
. (4.5.12)
16. Коэффициент индуктивной мощности канала:
. (4.5.13)
17. Активное напряжение в канале, В:
. (4.5.14)
18. Полное напряжение в канале, В:
. (4.5.15)
19. Полная мощность индуктора:
. (4.5.16)
20. Реактивная (индуктивная) мощность, выделяющаяся в индукторе:
. (4.5.17)
21. Полная мощность печи, кВ·А:
S = N · Sинд. (4.5.18)
22. Реактивная (индуктивная) мощность печи, квар:
Q = N · Qинд, (4.5.19)
23. Число витков катушки индуктора:
(4.5.20)
где U1 – напряжение, подаваемое на катушку и зависящее от лица выбранного трансформатора, В.
24. Сила тока в катушке, А:
. (4.5.21)
25. Площадь поперечного сечения витка катушки, мм2:
(4.5.22)
26. Ширина bвит и высота витка hвит катушки, мм. Размеры витка катушки определяют с учетом размеров сечения провода, из которого изготовлена катушка. В основном применяют медный провод прямоугольного сечения.
27. Длина катушки, мм:
, (4.5.23)
где Ксл – число слоев витков в катушке.
28. Емкость конденсаторной батареи индуктора (для компенсации сos ), мкФ:
. (4.5.24)
Расчет нагревательных печей
С помощью теплового баланса определяем расход топлива для проектируемых печей, а также анализ тепловой работы действующих печей. При этом определяем расход топлива или электроэнергии за единицу времени. Для печей непрерывного действия определяем часовой расход топлива или электроэнергии, а для печей периодического действия – период работы печи. В связи с тем, что большинство печей литейного производства – непрерывного действия, рассмотрим методику составления теплового баланса для пламенной печи.
|
Тепловой баланс состоит из количественно одинаковых частей: прихода и расхода.
I . Приход за 1 ч
1. Химическая теплота горения топлива в кДж:
Qхим= ·В, (4.6.1)
где В – искомая величина – расход топлива, м3/ч или кг/ч.
2. Физическая теплота подогретого воздуха (эта статья учитывает теплоту, вносимую подогретым воздухом, который идет на горение топлива) в кДж:
Qв.ф=св·tв·Lв·В, (4.6.2)
где св – удельная теплоемкость подогретого воздуха при температуре tв, кДж/(м3·ºС);
tв – температура подогретого воздуха, ºС;
Lв – количество воздуха, необходимое для горения единицы топлива при коэффициенте расхода воздуха, равном n, м3/м3.
4.Физическая теплота подогретого топлива (имеется в виду количество теплоты на подогрев газового топлива перед сжиганием) в кДж:
Qт.ф =ст·tг·В, (4.6.3)
где ст – удельная теплоемкость газового топлива при температуре tг, кДж/(м3·°С);
tг – температура подогретого газового топлива, ºС.
4. Теплота, выделяемая при окислении металла (процесс окисления протекает с положительным тепловым эффектом), Вт:
Qэкз=1570· Gм.т , (4.6.4)
где Gм.т – количество металла, включая тару, проходящее через печь в течение одного часа, кг;
– угар металла, % (для нагревательных печей
= 2%, для термических
= 1%).
При нагреве металла до 600…700 ºС этой статьей можно пренебречь.
II . Расход за 1 ч
1. Теплота в кДж, идущая на нагрев металла:
Qм = cм( –
)Gм, (4.6.5)
где см – средняя удельная теплоемкость металла в интервале температур …
tмн, кДж/(кг·ºС);
Gм – количество металла, нагреваемого в течение 1 ч, кг;
и
– начальная и конечная температура металла, ºС.
2. Теплота в кДж, идущая на нагрев тары (в этой статье учитывают потери теплоты на нагрев поддонов, конвейерной ленты и т. п):
Qтар = cтар( –
)Gтар, (4.6.6)
где стар – удельная теплоемкость тары в интервале температур …
, кДж/(кг·ºС);
Gтар – масса тары, нагреваемой в течение одного часа, кг;
,
– начальная и конечная температура тары, ºС.
3. Потери теплоты с уходящими продуктами горения топлива в кДж:
Qух= cухtухVух, (4.6.7)
где сух – удельная теплоемкость продуктов горения при tух, кДж/(м3·ºС);
tух – температура уходящих из печи продуктов горения, ºС;
Vух – количество продуктов горения, получающихся при сжигании единицы топлива, при коэффициенте расхода воздуха, равном n, м3/м3.
4. Потери теплоты в кДж через стены, под и заслонки печи за счет теплопроводности. Эти потери Qкл определяют отдельно для каждого элемента футеровки печи:
Qкл= K(tп – tокр.в)Fср, (4.6.8)
где tп и tокр.в – температура печного пространства и окружающего воздуха, ºС;
Fср – средняя площадь теплопередающей поверхности, м2.
5. Потери теплоты в кДж излучением через окна и отверстия (в момент открывания заслонок печи часть теплоты теряется за счет лучеиспускания печного пространства в окружающую среду, также имеются потери за счет лучеиспускания через технические отверстия в печи):
, (4.6.9)
где С0 – коэффициент излучения абсолютно черного тела;
Тпечи – средняя температура печи, К;
F – площадь окна или отверстия, м2;
Ф – коэффициент диафрагмирования (прил. 7);
– доля времени, в течение которого отверстие открыто (при постоянно открытом отверстии
= 1).
6. Потери теплоты в кДж на нагрев контролируемой атмосферы (часть теплоты теряется на нагрев ее до температуры печного пространства):
Qатм = cатм(tпечи – )А, (4.6.10)
где сатм – удельная теплоемкость контролируемой атмосферы в интервале температур tпечи … , кДж/(м3·ºС);
tпечи и tнатм – температура печного пространства и начальная температура контролируемой атмосферы, ºС;
А – расход контролируемой атмосферы, м3/ч.
7. Потери теплоты с охлаждающей водой Qвод определяют либо на основе опытных данных, либо расчетом для каждого конкретного случая.
8. Неучтенные потери Qнеучт обычно равны 15…20 % от всех статей расхода (за исключением потерь теплоты на нагрев металла). Приравнивая сумму статей прихода сумме статей расхода, находим расход топлива, В:
Qхим+ Qв.ф+ Qт.ф= Qм+ Qтар+ Q ух + Qкл+ Qизл+ Qатм+ Qвод+ Qнеуч, (4.6.11)
Данные теплового баланса сводим в следующую таблицу (см. форму)
Форма
Таблица баланса газовой печи
Статьи прихода | Единица измерения | Статьи расхода | Единица измерения | ||
кДж/ч | % | кДж/ч | % | ||
Химическая теплота горения топлива Qхим. Физическая теплота подогретого воздуха Qв.ф. Физическая теплота подогретого топлива Qт.ф. | Нагрев металла Qм. Нагрев тары Qтары Теплота с уходящими продуктами горения Qух. Потери теплоты через кладку Qкл. Излучение через окна Qизл. Нагрев контролирумой атмосферы Qатм. Потери теплоты сохлаждающей водой Qвод. Неучтенные потери Qнеучт. | ||||
Всего: | Qпр | 100 | Всего: | Qрасх | 100 |
С помощью теплового баланса определяют расход топлива для проектируемых печей, а также можно осуществить анализ тепловой работы действующих печей. Один из основных показателей работы печи – коэффициент полезного действия – определяют из теплового баланса:
(4.6.12)
Характерным показателем тепловой работы печи является удельный расход теплоты на единицу нагреваемого металла в кДж/кг:
(4.6.13)
Расход топлива В определяли ранее из теплового баланса, реальный расход топлива обычно принимают равным (1,3…1,4)В, с учетом форсированной работы печи.
Тепловой баланс для электрических печей составляем по аналогам с тепловым балансом для газовых печей.
Расходная часть баланса электрической печи состоит из тех же статей, что и расходная часть газовой печи, исключение составляет статья расхода теплоты с уходящими газами.
Статьи теплового баланса рассчитывают в кВт.
Из составленного баланса определяют расход электроэнергии Р. Установленную мощность печи Руст принимают завышенной, учитывая форсированный тепловой режим:
Руст = К·Р, (4.6.14)
где К – коэффициент запаса, учитывающий условия работы печи (1,2…1,3 – для непрерывно работающих и 1,4…1,5 – для периодически работающих печей).
Для определения габаритных размеров нагревателя необходимо знать его допустимую удельную поверхностную мощность , Вт/см2. Эта величина зависит от отдельных факторов, определяющих условия теплообмена нагревателя в печи: температуры и степени черноты нагреваемого материала и нагревателя, расположения последнего и т. д.
Так, для нихромовых нагревателей рекомендуют следующие величины удельной поверхностной мощности:
при температуре печи до 900 ºС – 1,5 Вт/см2;
при температуре печи 1000 ºС – 1,0 Вт/см2;
при температуре печи 1100 ºС – 0,7 Вт/см2.
Размеры круглых нагревателей определяют по формулам:
, (4.6.15)
, (4.6.16)
где d – диаметр проволоки, м;
– удельное сопротивление нагревателя, 10-6Ом·м;
Р – мощность фазы, кВт;
V – фазовое напряжение, В;
L – длина нагревателя для одной фазы, м.
Для ленточных нагревателей при отношении сторон ленты b / a = m:
. (4.6.17)
Длина ленточного нагревателя:
, (4.6.18)
где а и L измеряются в м.
Расчетные данный относятся к одной фазе. Нагревательные элементы могут быть соединены последовательно, параллельно, звездой и треугольником.
Другой метод расчета нагревателей заключается в том, что, задаваясь размером поперечного сечения нагревателя, определяют его длину и проверяют величину щ для этого сечения. Если при этом величина щ значительно отличается от допустимой (особенно в сторону увеличения), то нагреватель еще раз рассчитывают, изменяя его поперечное или расчетное напряжение.
Расчет сушил
Интенсивность процесса испарения влаги с поверхности зависит от разности парциальных давлений пара на поверхности материала и окружающей среды. Чем больше эта разность, тем интенсивнее испарение. Количество влаги, испаряющейся с поверхности, в кг/(м2·с):
т = (Р n – Ргаз), (4.7.1)
где – коэффициент испарения, кг/(кН·с);
Рп – парциальное давление водяных паров на поверхности испарения, кН/м2;
Ргаз – парциальное давление водяных паров окружающей среды (сушильного агента-газа), кН/м2.
Тепловой расчет процесса сушки при заданном температурном режиме сводится к определению расхода сушильного агента и расхода теплоты на сушку данного материала. Различают абсолютную влажность, относительную влажность и влагосодержание воздуха.
Влагосодержание влажного воздуха характеризуется массой водяного пара mпар (кг), содержащегося в 1 м3 влажного воздуха (смеси сухого воздуха и пара), отнесенной к массе 1 м3 сухого воздуха mв.с (кг). Влагосодержание обозначается буквой d ,кг/кг:
. (4.7.2)
Влагосодержание влажного воздуха зависит от парциального давления водяного пара mпар (кг), содержащегося в нем, и не зависит о температуры:
(4.7.3)
где В – барометрическое давление, кПа. В расчетах принимают В = 98,1 кПа.
Из формулы
Рпар=0,01· нас, (4.7.4)
тогда
. (4.7.5)
Зная количество влаги, которое нужно испарить из материала за 1 с (mвл, кг), а также начальное и конечное влагосодержание воздуха (dн и dк), можно определить количество воздуха, необходимое для сушки (кг вс/с):
. (4.7.6)
Количество влаги, которое необходимо удалить из материала в процессе сушки, зависит от начальной и конечной влажности материала. Количество влаги, удаляемое из материала, определяется по одной из двух приведенных ниже формул, применяемых в зависимости от наличия исходных данных, кг/с:
, (4.7.7)
, (4.7.8)
где и
– масса материала до и после сушки, кг/с;
Uн и Uк – относительная влажность материала до и после сушки.
Относительная влажность материала, %, представляет собой отношение массы влаги mвл, содержащейся в материале, к массе влажного материала :
. (4.7.9)
Отношение массы влаги, содержащейся в материале, к массе абсолютно сухого материала mм абс с означает абсолютную влажность материала, %:
. (4.7.10)
Пересчитать одну влажность материала на другую можно по формуле
(4.7.11)
В тепловых расчетах сушил в качестве одного из основных параметров используют количество теплоты влажного воздуха, отнесенное к 1 кг абсолютно сухого воздуха (кДж/кг в с):
iвл=1,005· t + d(2490+1,97t). (4.7.12)
Первый член выражения представляет собой удельное количество теплоты сухого воздуха, а второй – водяного пара, содержащегося во влажном воздухе.
Расчет процесса сушки аналитическим путем труден и громоздок, поэтому широко используют графический метод расчета с помощью i - d-диаграммы (прил. 4). Диаграмма, построенная для влажного воздуха, может быть использована для расчета сушки продуктами горения, разбавленными воздухом.
Различают теоретический (идеальный) и действительный процесс сушки.
Расход воздуха при теоретическом процессе (кг в·с/с):
. (4.7.13)
При действительном процессе сушки часть теплоты, вносимой воздухом, необратимо теряется, вследствие чего процесс идет с уменьшением удельного количества теплоты воздуха. Для определения изменения удельного количества теплоты воздуха необходимо вычислить количество теплоты Qпот, затраченное на нагрев металла, тары и т. д.
После определения Qпот находим потери удельного количества теплоты воздуха, кДж/кг в·с:
. (4.7.14)
Затем, пользуясь i-d -диаграммой (прил. 4), определим расход воздуха на действительный процесс, кг в∙с/с:
(4.7.15)
Для перевода массы воздуха в объемное количество Vв можно воспользоваться отношением, м3/с:
Vв = V м.в, (4.7.16)
где Vм.в – объем влажного воздуха, приходящегося на 1 кг сухого воздуха (прил. 1).
Потери теплоты в сушиле Qпот определяют так же, как и для расчета теплового баланса печей:
Qпот.= Qм+ Qтр+ Qокр+ Qух+ Qнепл, (4.7.17)
где Qм – расход теплоты на нагрев материала;
Qтр – расход теплоты на нагрев транспортных устройств;
Qокр – потери теплоты в окружающую среду;
Qух – потери теплоты с уходящими газами;
Qнепл – потери теплоты через неплотности сушила.
БИБЛИОГРАФИЧЕСКИЙ СПИСОК
1. Долотов, Г. П. Печи и сушила литейного производства / Г. П. Долотов, Е. А. Кондаков. – М. : Машиностроение, 1990.
2. Долотов, Г. П. Конструкция и расчет заводских печей и сушил / Г. П. Долотов, Е. А. Кондаков. – М. : Машиностроение, 1973.
3. Кривандин, В. А. Металлургические печи / В. А. Кривандин, Б. Л. Марков. – М. : Металлургия, 1977.
4. Мариенбах, Л. М. Печи в литейном производстве / Л. М. Мариенбах. – М. : Машиностроение, 1964.
5. Теплотехнические расчеты металлургических печей / под ред. А. С. Телегина. – М. : Металлургия, 1970.
6. Сушильные печи литейных цехов / под ред. Б. Ф. Забника.– Свердловск : ЧПН, 1977.
7. Благонравов, Б. П. Печи в литейном производстве. Атлас конструкций / Б. П. Благонравов. – М. : Машиностроение, 1989.
8. Расчеты нагревательных печей / под ред. Н. Ю. Тайца. – Киев : Техника, 1969.
9. Бигеев, А. М. Металлургия стали. Теория и технология плавки стали / А. М. Бигеев. – Челябинск : Металлургия. Челябинское отд-ние. – 1988.
10. Аксенов, П. Н. Оборудование литейных цехов / П. Н. Аксенов. – М. : Машиностроение, 1977.
11. Сухорчук, Ю. С. Плавка чугуна в вагранках / Ю. С. Сухорчук, А. К. Юдкин. – М. : Машиностроение, 1989.
12. Курдюмов, А. В. Литейное производство цветных и редких металлов / А. В Курдюмов, и др. – М. : Машиностроение, 1972.
13. Чурсин, В. М. Технология цветного литья / В. М. Чурсин, П. Н. Бидуля. – М. : Машиностроение, 1981.
14. Новое в технологии получения материалов / под. ред. Ю. А. Осиньяна. – М. : Машиностроение, 1990.
ПРИЛОЖЕНИЕ 1
|
|
Эмиссия газов от очистных сооружений канализации: В последние годы внимание мирового сообщества сосредоточено на экологических проблемах...
Историки об Елизавете Петровне: Елизавета попала между двумя встречными культурными течениями, воспитывалась среди новых европейских веяний и преданий...
Археология об основании Рима: Новые раскопки проясняют и такой острый дискуссионный вопрос, как дата самого возникновения Рима...
Механическое удерживание земляных масс: Механическое удерживание земляных масс на склоне обеспечивают контрфорсными сооружениями различных конструкций...
© cyberpedia.su 2017-2024 - Не является автором материалов. Исключительное право сохранено за автором текста.
Если вы не хотите, чтобы данный материал был у нас на сайте, перейдите по ссылке: Нарушение авторских прав. Мы поможем в написании вашей работы!