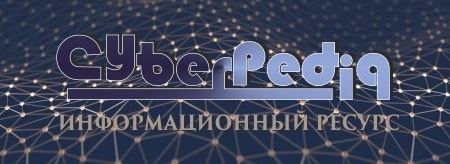
Эмиссия газов от очистных сооружений канализации: В последние годы внимание мирового сообщества сосредоточено на экологических проблемах...
Семя – орган полового размножения и расселения растений: наружи у семян имеется плотный покров – кожура...
Топ:
Характеристика АТП и сварочно-жестяницкого участка: Транспорт в настоящее время является одной из важнейших отраслей народного...
Оценка эффективности инструментов коммуникационной политики: Внешние коммуникации - обмен информацией между организацией и её внешней средой...
Теоретическая значимость работы: Описание теоретической значимости (ценности) результатов исследования должно присутствовать во введении...
Интересное:
Принципы управления денежными потоками: одним из методов контроля за состоянием денежной наличности является...
Наиболее распространенные виды рака: Раковая опухоль — это самостоятельное новообразование, которое может возникнуть и от повышенного давления...
Подходы к решению темы фильма: Существует три основных типа исторического фильма, имеющих между собой много общего...
Дисциплины:
![]() |
![]() |
5.00
из
|
Заказать работу |
|
|
Оборудование для литейного производства
20.12.2018
Источник: https://extxe.com/8910/oborudovanie-dlja-litejnogo-proizvodstva/
Содержание
1. Оборудование для подготовки формовочных и стержневых материалов и приготовления смесей
2. Машины для изготовления литейных форм и стержней
3. Оборудование для плавки металлов
4. Оборудование для заливки форм
5. Оборудование для выбивки литейных форм и стержней
6. Оборудование для обрубки литья
7. Оборудование для очистки литья
8. Оборудование для зачистки поверхностей отливок
9. Оборудование для литья в оболочковые формы
10. Оборудование для литья по выплавляемым и выжигаемым моделям
11. Оборудование для литья под давлением
12. Оборудование для литья в металлические формы, под низким давлением и для центробежного литья
1. Оборудование для подготовки формовочных и стержневых материалов и приготовления смесей
Щековые дробилки (рис. 1, а) рекомендуются для дробления отработанных жидко-стекольных смесей и других материалов. Дробление производится за счет сжатия между дробящими плитами неподвижной 1 и подвижной 2 щек. Качание подвижной щеки, являющейся одновременно шатуном, осуществляется при вращении эксцентрикового вала 3. Распорная плита 4 поддерживает низ щеки 2, сохраняя заданный зазор между дробящими плитами. Щековые дробилки имеют производительность 7,8–30 м3/ч. У молотковых дробилок (рис. 1, б) материал подается через воронку 1 и дробится молотками 5, закрепленными с помощью шарниров 4 на вращающемся роторе 3. Продукты дробления проваливаются сквозь колосниковую решетку 7. Корпус дробилки 2 облицован износостойкими плитами 6. Молотковые дробилки производительностью 10–27 т/ч рекомендуются для отработанных холодно-твердеющих смесей, угля и других материалов. Валковые дробилки (рис. 1, в) предназначены для отработанной смеси, стержней на жидком стекле и других материалов. Дробление в них производится затягиванием материалов в зазор между вращающимися в разные стороны валками 2 и 5, один из которых опирается на пружину 3, предохраняющую дробилку от поломки при попадании в бункер 1 недробящихся (например, металлических) кусков. Расстояние между валками регулируется прокладками 4.
В роторных дробилках (рис. 1, г) измельчение происходит в результате ударов кусков об отбойные плиты 3 (при их числе от 1 до 3), на которые куски отбрасываются вращающимся относительно горизонтальной оси ротором 1 с билами 2. Это оборудование рекомендуется применять для дробления отработанных песчаноглинистых, холодно-твердеющих, жидко-стекольных смесей и других материалов. Производительность известных роторных дробилок — до 125 м3/ч.
В вибрационных дробилках (рис. 1, д) куски истираются друг о друга и о стенки бункера 1 с шипами, ребрами, отверстиями в результате вибрации системы на пружинных опорах под действием вращающихся эксцентриков 2. Сетка 3 определяет размер частиц продукта. В некоторые вибрационные дробилки вместе с материалом помещают мелющие тела, например шары. Вибрационная дробилка имеет производительность 15 т/ч.
|
Рис. 1, а–к. О борудование для подготовки формовочных материалов
Рис. 1, л. Оборудование для подготовки формовочных материалов
Мельницы шаровые (дробилки) предназначены для тонкого измельчения глины, каменного угля, других материалов и представляют собой вращающийся около горизонтальной оси барабан, наполненный измельчаемым материалом и металлическими шарами (рис. 1, е). Шары за счет вращения барабана поднимаются на некоторую высоту и падают, дробя материал.
Сита барабанные полигональные (рис. 1, ж) для просеивания оборотных смесей и песков в механизированных смесеприготовительных отделениях представляют собой шестиили восьмигранную усеченную пирамиду, вращающуюся относительно оси, расположенной горизонтально. Смесь 1 подается внутрь пирамиды, образованной ситами со стороны меньшего основания, за счет вращения поднимается на угол 40–45°, соскальзывает, частично измельчаясь и просеиваясь (2 — просеянная смесь), одновременно перемещаясь вдоль оси под уклон. Непросеявшиеся комья 3 и инородные включения выпадают через окно в большем основании. Производительность самой крупной модели равна 160 м3/ч.
Для разминания и просеивания оборотной смеси и отделения посторонних металлических и неметаллических включений размерами более 20×20 мм в смесеприготовительных отделениях литейных цехов применяют плоские вибрационные сита производительностью до 250 м3/ч. Два плоских просеивающих полотна (деки) этих сит размещены одно над другим с наклоном к горизонту 15°. Вибрации создает эксцентриковый вибратор 1 (рис. 1, з). Для разминания комков над верхней декой имеются разминающие кольца 2, над нижней — башмаки 3. Посторонние неразрушаемые включения приподнимают кольца и башмаки и попадают в отходы.
|
Для просеивания отработанной смеси и свежих материалов преимущественно в составе автоматических смесеприготовительных систем применяют набор плоских вибрационных сит грубой очистки и тонкой очистки. Производительность самых крупных из этих сит достигает 240 чм.3/Сита грубой очистки оснащены пневмодробилками. Сита грубой очистки большой производительности (рис. 1, и) имеют двухмассный вибратор 1, направленные колебания которого заставляют материал двигаться по наклонному полотну вверх (Р — возмущающая сила, V — скорость перемещения материала).
Сита инерционные для грубой и тонкой очистки предназначены для очистки, просеивания и размельчения оборотной смеси и свежих материалов в автоматизированных цехах. Позволяют устанавливать одну деку для тонкого просева или для грубого либо одновременно две деки. Производительность сита 240 м3/ч.
Сита барабанные со встроенным аэратором предназначены для размельчения, аэрации (рыхления) и просеивания отработанной формовочной смеси и песка. Совмещенная конструкция позволяет увеличить производительность сита до 125 м3/ч. Смесь подается на зубья вращающегося гребенчатого вала. Ударяясь о них и об отражательный лист, комья дробятся и попадают в перфорированный вращающийся барабан, ось которого наклонена под углом 3–5° к горизонту, где перемещаются по винтовой линии (относительно поверхности барабана) к противоположному концу, где непросеянные комья переваливаются через край.
Для небольших литейных цехов установка высокопроизводительной дорогой техники экономически нецелесообразна. Там применяются средства малой механизации: передвижная сеялка и смесеприготовитель передвижной барабанный. Первая предназначена для просеивания свежего песка и отработанных смесей, второй — для просеивания и разрыхления наполнительной формовочной смеси, а также для извлечения из нее металлических ферромагнитных включений.
Песок часто сушат с помощью барабанных или трубных сушил и установок сушки в кипящем слое. Для глины применяются барабанные сушила (рис. 1, к) погрузка песка на перфорированную сушильную решетку 2 производится через воронку 4. Горячие газы подаются по трубам 1, через форсунки в решетке 2 продуваются через слой песка на ней, отбирая от него влагу, и удаляются через патрубок 3. Высушенный песок отводится через трубу 5. Барабанные сушила (рис. 1, л) представляют собой вращающийся относительно наклонной к горизонту оси барабан 3 с продольными полками 4, через который проходят горячие газы от горелок 1. Тягу создает вентилятор, присоединенный к патрубку 5. Материал загружается по лотку 2 и, пересыпаясь по полкам 4, омываемый горячими газами, постепенно перемещается под уклон, к разгрузочной камере 6. Барабан поддерживается роликами 7 и приводится во вращение приводом 8.
В трубных сушилах песок сушится в пневмопотоке горячего воздуха, что обеспечивает высокую скорость сушки, а также позволяет совместить сушку с транспортированием и обеспыливанием.
|
Основной компонент многих формовочных смесей — оборотная смесь (ранее уже использованная для получения литейных форм), подготовка которой к повторному применению включает извлечение из смеси металлических включений (сепарацию), размол комьев, просев, охлаждение и гомогенизацию (для однородности свойств смеси), а также регенерацию (избавление смеси от пыли). Кроме оборотной смеси формовочные смеси содержат свежие материалы.
Извлечение из отработанных смесей и свежих материалов металлических магнитных включений производится с помощью электромагнитных сепараторов: шкивных и подвесных. Шкив заставляет магнитные включения пройти некоторое расстояние в обратном движении ленты, тогда как немагнитная смесь сходит с транспортера сразу за шкивом. Подвесные сепараторы представляют собой поперечные (к потоку смеси) магнитные транспортеры.
Параметры отработанной смеси после выбивки в зависимости от близости к отливке значительно различаются: влажность колеблется от 0 до 3%, а температура может достигать 80–120°С. Поэтому перед повторным использованием необходимо охладить смесь и усреднить влажность, для чего и предназначены различные охладители.
|
Охладители смешивающие имеют производительность 35–240 м3/ч и представляют собой чаши с двумя вертикальными валами, несущими перемешивающие скребки. Охлаждение происходит за счет парообразования при увлажнении смеси. Процесс интенсифицируется непрерывным перемешиванием и продувкой воздуха, удаляющего пар.
Вибрационные охладители (рис. 2, а) представляют собой двухмассные виброконвейеры с нижней и верхней воздушными камерами, разделенными перфорированным полотном 2 и слоем охлаждаемого материала. Рама охладителя опирается на фундамент через пружинные амортизаторы 4.
В процессе работы горячая отработанная формовочная смесь через загрузочную воронку 1 попадает на наклонную плоскость охладителя, затем на перфорированное полотно 2 и за счет направленной вибрации транспортируется в зону выгрузки. Воздух 3, проходя из нижней камеры в верхнюю, продувает транспортируемый слой горячей формовочной смеси и уносит часть теплоты, охлаждая смесь. Теплый воздух с частицами формовочной смеси попадает в установку пылеулавливания, в которой происходит сбор частиц и возвращение их в смесеприготовительную систему. Производительность достигает 240 м3/ч.
Установки охлаждения отработанной формовочной смеси предназначены для автоматического доведения влажности смеси до 2–3% с точностью ±0,2% и температуры до 30–40°С с точностью ±5° путем увлажнения и охлаждения. Установки могут применяться самостоятельно в линиях возврата отработанной смеси и в автоматизированных системах приготовления смесей. Смесь подается транспортером во вращающийся увлажнительный барабан, где через сопла разбрызгивается вода, откуда конвейером направляется в охладитель. Самая крупная модель имеет производительность до 250 м3/ч, длину 65 м и массу 80 т. Существуют установки с правым и левым исполнением.
Аэраторы рыхлят формовочные смеси для улучшения их пластичности и формуемости. Их производительность достигает 240 м3/ч. Аэраторы (рис. 2, б) рыхлят смесь при пересыпке с транспортера на транспортер. Смесь подается через горловину 3 на лопатки 2 вращающегося ротора 1, которыми отбрасывается на цепи 4 (или гребенку), разрыхляется и падает на транспортер под аэратором. Одни надленточные аэраторы служат для рыхления отработанной смеси, а другие — для рыхления готовой смеси; число зубьев гребенчатого вала у них в два раза больше.
|
Они рыхлят смесь, проходящую под ними на транспортерной ленте.
При многократном использовании формовочных и стержневых смесей происходит чередование нагрева и охлаждения. При этом в смесях протекают различные химические реакции и полиморфные превращения кварца, сопровождающиеся изменением объема, приводящим к растрескиванию. Кроме того, некоторые зерна сращиваются. Таким образом, средняя (основная) фракция песка сокращается, что приводит к изменению свойств смесей.
Регенерация (восстановление) отработанных смесей позволяет получать песок, годный для повторного изготовления смесей. Регенерация включает дробление комьев, магнитную сепарацию металлических включений, просеивание, очистку поверхности песчинок от пленок связующего, обеспыливание песка и классификацию — разделение регенерата по фракциям (размерам зерен).
При гидравлической регенерации зерна песка интенсивно промываются в потоке воды, который уносит пылевидные частицы, и оттираются от пленок. Системы гидрорегенерации производят сухой регенерированный песок с температурой 30 C, оборотную воду глубокого осветления, металлические отходы (все это для повторного использования), кусковые неметаллические отходы размером частиц более 5 мм и пылевидные отходы в виде шлама с влажностью до 50% (два последних свозят на свалку). Производительность самой крупной модели по загружаемой смеси — 60 т/ч; эта система способна обеспечить производство 100–240 тыс. т литья в год.
Рис. 2. Оборудование для регенерации смесей
Важнейший элемент системы гидравлической регенерации — оттирочная машина (рис. 2, в). В машине производительностью до 25 т/ч зерна песка очищаются за счет соударения в потоках пульпы, создаваемых лопатками вертикальных валов двух камер, имеющими разный угол наклона.
Чан агитационный для перемешивания пульпы производительностью 25 т/ч входит в состав комплекса гидравлической регенерации и предназначен для перемешивания и поддержания во взвешенном состоянии пульпы, поступающей из оттирочной машины для последующего ее транспортирования насосами. Чан пригоден также для растворения реагентов в системах очистки воды систем регенерации и в составе оборудования для обогащения полезных ископаемых. Представляет собой вертикальный цилиндр с мешалками, приводимыми в движение от электродвигателя через клиноременную передачу.
Системы гидрорегенерации содержат также железоотделители, дробилки, грохоты, классификаторы, сушилки и охладители.
Гидравлические системы наиболее универсальны и эффективны, позволяют перерабатывать смеси сложного состава, дают пески, близкие по зерновому составу к обогащенным, при работе образуют мало пыли, но требуют больших производственных площадей и затрат на энергию для сушки песка. Эти системы хорошо совмещаются с гидровыбивкой форм и стержней.
В системах сухой механической регенерации зерна песка очищаются от пленки связующего перетиранием отработанной смеси в дробилках. Образующаяся пыль удаляется из смеси вместе с отсасываемым воздухом. Производительность самой крупной модели составляет 60 т/ч, позволяет обслуживать цех с производством отливок в объеме 30–60 тыс. т/год. Эти системы рекомендуется применять для единых холоднотвердеющих смесей (ХТС) на синтетических смолах или жидком стекле. Их достоинствами являются компактность установок и сравнительно небольшие капитальные и энергетические затраты, но качество продукта уступает гидро- и терморегенерату. В состав таких систем входят классификаторы воздушные и вибрационно-каскадные, охладители, дробилки, магнитные сепараторы и грохоты.
Классификатор воздушный каскадный противоточный (рис. 2, г) предназначен для удаления из регенерированных или свежих песков частиц размером менее 0,1– 0,16 мм. Состоит из восьми секций-полок 2, установленных в корпусе 1 под углом 45° к горизонту и перекрывающих 50% поперечного сечения. Смесь пересыпается по полкам сверху вниз. Навстречу потоку смеси движется поток воздуха, уносящий пыль в циклон. После первичной очистки от пыли в циклоне воздух проходит фильтр, где вторично очищается от пыли, после чего выбрасывается в атмосферу. Производительность — 5 т/ч.
Охладитель бесконтактный трубчатый противоточный водяной (рис. 2.2, д) предназначен для снижения температуры отработанной смеси и охлаждения песка после сушки. Смесь охлаждается за счет контакта с трубчатыми решетками змеевиков 3, по которым течет вода. Смесь загружается через патрубок 2, а выгружается через патрубок 1. Производительность по песку — 5 т/ч.
Для удаления из регенерируемых песков частиц размером менее 0,1–0,16 мм применяют также вибрационно-каскадные классификаторы (рис. 2, е). Их корпус 5 установлен на пружинах (не показаны) и совершает вибрационное движение под действием вибраторов 8. Песок загружается через воронку 6. В корпусе установлена сетка 3 для удаления случайных крупных кусков и пересыпные полки 4 с отверстиями. Пылевидные отходы потоком продуваемого воздуха удаляются через патрубок 7, регенерат — через патрубок 1, а крупные куски — по лотку 2. Производительность — 10 т/ч.
Комплексы пневматической регенерации песчано-глинистых смесей имеют производительность по загрузке соответственно 6–72 т/ч. Их основу составляет пневморегенератор производительностью 6 т/ч. Сущность его работы (рис. 2, ж) состоит в том, что загружаемый песок потоком сжатого воздуха от сопла 1 разгоняется по трубе 2, при этом песчинки ударяются друг о друга и об экран 3, за счет чего происходит разрушение оболочек связующего вокруг песчинок. Пылевидные продукты разрушения уносятся потоком воздуха, а неполностью регенерированный песок из коллектора 4 частично снова поступает в трубу 2, а частично через патрубок 5 в следующую такую же камеру (возможно последовательное соединение от двух до восьми камер). Недостаток таких установок — неполное дробление песка. Стоимость пневморегенерации в 1,5–2 раза выше, чем механической.
При термической регенерации пленки с зерен песка сжигают прокаливанием смеси при 550–800 С, после чего производят воздушную сепарацию. Способ дóрог (в 2– 3 раза дороже механического), требует много энергии на нагрев, охлаждение и обеспыливание смеси. Применяется для смесей со смоляным связующим (для стержней и оболочковых форм). Имеются установки термической регенерации.
Процесс приготовления смеси состоит из дозирования всех компонентов смеси (кварцевого песка, пылевидных добавок и жидких добавок), включая жидкие связующие и воду, загрузки их в смесители в определенной последовательности, перемешивания для обеспечения однородности и заданных свойств готовых смесей.
Смесители литейные чашечные периодического действия с вертикально вращающимися металлическими катками (их схема приведена на рис. 3, а) предназначены для приготовления единых, наполнительных, облицовочных и стержневых смесей из песчано-глинистых фракций с пылевидными и жидкими добавками.
При вращении вертикального вала 3 смесь размешивается (разминается) и растирается катками 2, вращающимися на горизонтальных осях 4 и устанавливаемыми с регулируемым зазором относительно дна неподвижной чаши 1 и перемешивается отвалами 5 и 6, направляющими смесь под катки. При этом песчинки обволакиваются оболочкой связующего. Последнее облегчается наличием проскальзывания большей части цилиндрической поверхности катка относительно смеси, благодаря чему песчинки перекатываются в глинистой суспензии. Запыленный воздух отсасывается из-под колпака. Выгружается смесь через люки 7. Производительность
(110–60 м3/ч) бегунов (второе название смесителей) зависит от длительности цикла.
Смесители (бегуны) литейные чашечные периодического действия центробежные с горизонтально-вращающимися катками (рис. 3, б) предназначены для приготовления формовочных и стержневых смесей с незначительным количеством освежающих добавок. Перемешивание здесь осуществляется за счет отбрасывания (центробежной силой) подаваемой на диск 5 смеси на обечайку 4 (вертикальную, цилиндрическую поверхность чаши, облицованную резиной), где прокатывающиеся по ней также обрезиненные катки 1 разминают комья. Верхние скребки отделяют смесь от обечайки, а нижние 2 — поднимают смесь с днища чаш 3 на обечайку под катки. Запыленный воздух отсасывается. Применяются эти смесители в основном для сырых песчано-глинистых смесей (ПГС).
Более производительны смесители (бегуны) литейные чашечные, непрерывного действия, сдвоенные, с вертикально вращающимися катками для приготовления формовочных смесей. Производительность достигает 240 м3/ч. По конструкции представляют собой сдвоенные смесители периодического действия с вертикальновращающимися катками, смежные чаши которых сообщаются через общий сегмент. Увеличение производительности достигается благодаря последовательному смешению двумя парами катков. Готовая смесь выдается непрерывно. Запыленный воздух отсасывается.
Агрегат для приготовления глинистой суспензии (рис. 3, в) представляет собой горизонтальный барабан 1, установленный вместе с приводом (5 — электродвигатель, 6 — ременная передача, 7 — редуктор, 8 — зубчатая передача) на раме 2. Внутри барабана расположен горизонтальный вал 3 с параллельными ему зубчатыми лопастями 4. Подача молотой глины и воды производится через воронку 9. Готовая суспензия сливается через вентиль 10 и подается для загрузки в смесители для приготовления формовочных смесей. Производительность — 13 т/ч. Известны также комплексы оборудования для приготовления глинистых суспензий производительностью от 1 до 16 м3/ч.
Имеются комплексы оборудования для автоматизированных смесеприготовительных систем массового и крупносерийного производства, включающие смесители периодического или непрерывного действия, охладители смеси, аэраторы, сита, железоотделители, ленточные конвейеры с весовыми устройствами и плужковыми сбрасывателями.
Лучшие песчано-смоляные смеси для производства оболочковых форм и стержней — плакированные смеси, где каждая песчинка покрыта тонким слоем связующего — термореактивной смолы.
Смеситель центробежный периодического действия для приготовления плакированных смесей горячим способом производительностью 1 т/ч имеет нагреватель песка — камеру с вращающимся барабаном внутри нее. Барабан несет ковши, поднимающие, а в верхнем положении высыпающие песок, при падении проходящий зону нагрева и поступающий в центробежный смеситель с двумя катками на диске. Затем смесь поступает через вибросито в охладитель. Установка имеет также емкости и дозаторы для смолы, уротропина и стеарата кальция.
Рис. 3. Оборудование для приготовления смесей
Установка непрерывного действия для приготовления плакированных смесей горячим способом применяется в серийном и массовом производстве. Песок нагревается до 120–180 °С газовыми горелками в псевдокипящем слое; смешивание его со смолой, уротропином и стеаратом кальция происходит в лопастном смесителе. Далее смесь попадает на вибросито, а затем в охладитель.
ХТС очень быстро твердеют, поэтому приготовляются на формовочном участке в лопастных смесителях непрерывного действия, из которых сразу выгружаются в опоку или ящик. Эти смесители могут быть одноплечими, у которых окно для выдачи смеси в опоку или ящик перемещается по окружности, и двуплечими, у которых это окно может перекрывать значительную зону; первые применяются в поточных линиях, вторые — для формовки на плацу.
Основной элемент лопастных смесителей — горизонтальные валы (один или два) с лопастями, вращающимися в желобе. Лопасти захватывают материалы и перемещают их по окружности и вдоль желоба, постоянно вороша, перебрасывая и перетирая по стенкам желоба, за счет чего и происходит перемешивание.
У двухжелобных смесителей: одноплечего и двуплечих (рис. 3, г) предварительное смешивание компонентов, не реагирующих друг с другом, производится в двух разных желобах 1 с лопастными смесителями (в одном смешиваются песок со связующим, в другом — песок с отвердителем), а окончательное — в вихревой головке 2, конический корпус которой (рис. 3, д) имеет вертикальный вал 1 с лопатками 3, внизу — шибер 2 с пневмоприводом 4. Раздельное смешивание позволяет получать смеси с малым временем живучести (быстротвердеющие), исключать потери смеси при остановках смесителя и потери времени на очистку от застывшей смеси.
Смесители высокоскоростные с горизонтальной смесительной камерой для приготовления ХТС на органических (смолах) и неорганических (жидком стекле) связующих материалах одноплечие и двуплечие (производительность достигает 40 т/ч) имеют время перемешивания не более 5 с и могут применяться для приготовления смесей живучестью до 1 мин. Эти смесители имеют систему программирования шести вариантов смеси по составу, виду связующего и производительности, с возможностью быстрого перехода с одного варианта смеси на другой.
Установки для приготовления жидких самотвердеющих смесей (ЖСС) (рис. 3, е) содержат лопастной смеситель 1, выдающий смесь через затвор 8 в опоку или стержневой ящик; бункеры песка 4 и феррохромового шлака 5 с питателями 6, весовой дозатор 7; бак жидкой композиции 3 с мешалкой и дозатором 2. Установка для приготовления ЖСС периодического действия имеет производительность 6–8 т/ч, а установки непрерывного действия соответственно 5–10 и 20–30 т/ч.
Установка стационарная периодического действия для приготовления жидкой композиции для ЖСС содержит резервуары хранения компонентов жидкой композиции, дозаторы, смеситель, трубопроводы, пневмо- и электрооборудование и аппаратуру управления и сигнализации.
Стационарная установка непрерывного действия для приготовления пластичных самотвердеющих смесей (ПСС) производительностью 20 т/ч смешивает базовую смесь с феррохромовым шлаком в лопастном двухвальном смесителе и с помощью питателей раздает ее по опокам или ящикам. Базовая смесь песка с жидким стеклом приготовляется в обычных бегунах.
Оборудование для литейного производства
20.12.2018
Источник: https://extxe.com/8910/oborudovanie-dlja-litejnogo-proizvodstva/
Содержание
1. Оборудование для подготовки формовочных и стержневых материалов и приготовления смесей
2. Машины для изготовления литейных форм и стержней
3. Оборудование для плавки металлов
4. Оборудование для заливки форм
5. Оборудование для выбивки литейных форм и стержней
6. Оборудование для обрубки литья
7. Оборудование для очистки литья
8. Оборудование для зачистки поверхностей отливок
9. Оборудование для литья в оболочковые формы
10. Оборудование для литья по выплавляемым и выжигаемым моделям
11. Оборудование для литья под давлением
12. Оборудование для литья в металлические формы, под низким давлением и для центробежного литья
1. Оборудование для подготовки формовочных и стержневых материалов и приготовления смесей
Щековые дробилки (рис. 1, а) рекомендуются для дробления отработанных жидко-стекольных смесей и других материалов. Дробление производится за счет сжатия между дробящими плитами неподвижной 1 и подвижной 2 щек. Качание подвижной щеки, являющейся одновременно шатуном, осуществляется при вращении эксцентрикового вала 3. Распорная плита 4 поддерживает низ щеки 2, сохраняя заданный зазор между дробящими плитами. Щековые дробилки имеют производительность 7,8–30 м3/ч. У молотковых дробилок (рис. 1, б) материал подается через воронку 1 и дробится молотками 5, закрепленными с помощью шарниров 4 на вращающемся роторе 3. Продукты дробления проваливаются сквозь колосниковую решетку 7. Корпус дробилки 2 облицован износостойкими плитами 6. Молотковые дробилки производительностью 10–27 т/ч рекомендуются для отработанных холодно-твердеющих смесей, угля и других материалов. Валковые дробилки (рис. 1, в) предназначены для отработанной смеси, стержней на жидком стекле и других материалов. Дробление в них производится затягиванием материалов в зазор между вращающимися в разные стороны валками 2 и 5, один из которых опирается на пружину 3, предохраняющую дробилку от поломки при попадании в бункер 1 недробящихся (например, металлических) кусков. Расстояние между валками регулируется прокладками 4.
В роторных дробилках (рис. 1, г) измельчение происходит в результате ударов кусков об отбойные плиты 3 (при их числе от 1 до 3), на которые куски отбрасываются вращающимся относительно горизонтальной оси ротором 1 с билами 2. Это оборудование рекомендуется применять для дробления отработанных песчаноглинистых, холодно-твердеющих, жидко-стекольных смесей и других материалов. Производительность известных роторных дробилок — до 125 м3/ч.
В вибрационных дробилках (рис. 1, д) куски истираются друг о друга и о стенки бункера 1 с шипами, ребрами, отверстиями в результате вибрации системы на пружинных опорах под действием вращающихся эксцентриков 2. Сетка 3 определяет размер частиц продукта. В некоторые вибрационные дробилки вместе с материалом помещают мелющие тела, например шары. Вибрационная дробилка имеет производительность 15 т/ч.
Рис. 1, а–к. О борудование для подготовки формовочных материалов
Рис. 1, л. Оборудование для подготовки формовочных материалов
Мельницы шаровые (дробилки) предназначены для тонкого измельчения глины, каменного угля, других материалов и представляют собой вращающийся около горизонтальной оси барабан, наполненный измельчаемым материалом и металлическими шарами (рис. 1, е). Шары за счет вращения барабана поднимаются на некоторую высоту и падают, дробя материал.
Сита барабанные полигональные (рис. 1, ж) для просеивания оборотных смесей и песков в механизированных смесеприготовительных отделениях представляют собой шестиили восьмигранную усеченную пирамиду, вращающуюся относительно оси, расположенной горизонтально. Смесь 1 подается внутрь пирамиды, образованной ситами со стороны меньшего основания, за счет вращения поднимается на угол 40–45°, соскальзывает, частично измельчаясь и просеиваясь (2 — просеянная смесь), одновременно перемещаясь вдоль оси под уклон. Непросеявшиеся комья 3 и инородные включения выпадают через окно в большем основании. Производительность самой крупной модели равна 160 м3/ч.
Для разминания и просеивания оборотной смеси и отделения посторонних металлических и неметаллических включений размерами более 20×20 мм в смесеприготовительных отделениях литейных цехов применяют плоские вибрационные сита производительностью до 250 м3/ч. Два плоских просеивающих полотна (деки) этих сит размещены одно над другим с наклоном к горизонту 15°. Вибрации создает эксцентриковый вибратор 1 (рис. 1, з). Для разминания комков над верхней декой имеются разминающие кольца 2, над нижней — башмаки 3. Посторонние неразрушаемые включения приподнимают кольца и башмаки и попадают в отходы.
Для просеивания отработанной смеси и свежих материалов преимущественно в составе автоматических смесеприготовительных систем применяют набор плоских вибрационных сит грубой очистки и тонкой очистки. Производительность самых крупных из этих сит достигает 240 чм.3/Сита грубой очистки оснащены пневмодробилками. Сита грубой очистки большой производительности (рис. 1, и) имеют двухмассный вибратор 1, направленные колебания которого заставляют материал двигаться по наклонному полотну вверх (Р — возмущающая сила, V — скорость перемещения материала).
Сита инерционные для грубой и тонкой очистки предназначены для очистки, просеивания и размельчения оборотной смеси и свежих материалов в автоматизированных цехах. Позволяют устанавливать одну деку для тонкого просева или для грубого либо одновременно две деки. Производительность сита 240 м3/ч.
Сита барабанные со встроенным аэратором предназначены для размельчения, аэрации (рыхления) и просеивания отработанной формовочной смеси и песка. Совмещенная конструкция позволяет увеличить производительность сита до 125 м3/ч. Смесь подается на зубья вращающегося гребенчатого вала. Ударяясь о них и об отражательный лист, комья дробятся и попадают в перфорированный вращающийся барабан, ось которого наклонена под углом 3–5° к горизонту, где перемещаются по винтовой линии (относительно поверхности барабана) к противоположному концу, где непросеянные комья переваливаются через край.
Для небольших литейных цехов установка высокопроизводительной дорогой техники экономически нецелесообразна. Там применяются средства малой механизации: передвижная сеялка и смесеприготовитель передвижной барабанный. Первая предназначена для просеивания свежего песка и отработанных смесей, второй — для просеивания и разрыхления наполнительной формовочной смеси, а также для извлечения из нее металлических ферромагнитных включений.
Песок часто сушат с помощью барабанных или трубных сушил и установок сушки в кипящем слое. Для глины применяются барабанные сушила (рис. 1, к) погрузка песка на перфорированную сушильную решетку 2 производится через воронку 4. Горячие газы подаются по трубам 1, через форсунки в решетке 2 продуваются через слой песка на ней, отбирая от него влагу, и удаляются через патрубок 3. Высушенный песок отводится через трубу 5. Барабанные сушила (рис. 1, л) представляют собой вращающийся относительно наклонной к горизонту оси барабан 3 с продольными полками 4, через который проходят горячие газы от горелок 1. Тягу создает вентилятор, присоединенный к патрубку 5. Материал загружается по лотку 2 и, пересыпаясь по полкам 4, омываемый горячими газами, постепенно перемещается под уклон, к разгрузочной камере 6. Барабан поддерживается роликами 7 и приводится во вращение приводом 8.
В трубных сушилах песок сушится в пневмопотоке горячего воздуха, что обеспечивает высокую скорость сушки, а также позволяет совместить сушку с транспортированием и обеспыливанием.
Основной компонент многих формовочных смесей — оборотная смесь (ранее уже использованная для получения литейных форм), подготовка которой к повторному применению включает извлечение из смеси металлических включений (сепарацию), размол комьев, просев, охлаждение и гомогенизацию (для однородности свойств смеси), а также регенерацию (избавление смеси от пыли). Кроме оборотной смеси формовочные смеси содержат свежие материалы.
Извлечение из отработанных смесей и свежих материалов металлических магнитных включений производится с помощью электромагнитных сепараторов: шкивных и подвесных. Шкив заставляет магнитные включения пройти некоторое расстояние в обратном движении ленты, тогда как немагнитная смесь сходит с транспортера сразу за шкивом. Подвесные сепараторы представляют собой поперечные (к потоку смеси) магнитные транспортеры.
Параметры отработанной смеси после выбивки в зависимости от близости к отливке значительно различаются: влажность колеблется от 0 до 3%, а температура может достигать 80–120°С. Поэтому перед повторным использованием необходимо охладить смесь и усреднить влажность, для чего и предназначены различные охладители.
Охладители смешивающие имеют производительность 35–240 м3/ч и представляют собой чаши с двумя вертикальными валами, несущими перемешивающие скребки. Охлаждение происходит за счет парообразования при увлажнении смеси. Процесс интенсифицируется непрерывным перемешиванием и продувкой воздуха, удаляющего пар.
Вибрационные охладители (рис. 2, а) представляют собой двухмассные виброконвейеры с нижней и верхней воздушными камерами, разделенными перфорированным полотном 2 и слоем охлаждаемого материала. Рама охладителя опирается на фундамент через пружинные амортизаторы 4.
В процессе работы горячая отработанная формовочная смесь через загрузочную воронку 1 попадает на наклонную плоскость охладителя, затем на перфорированное полотно 2 и за счет направленной вибрации транспортируется в зону выгрузки. Воздух 3, проходя из нижней камеры в верхнюю, продувает транспортируемый слой горячей формовочной смеси и уносит часть теплоты, охлаждая смесь. Теплый воздух с частицами формовочной смеси попадает в установку пылеулавливания, в которой происходит сбор частиц и возвращ<
|
|
Поперечные профили набережных и береговой полосы: На городских территориях берегоукрепление проектируют с учетом технических и экономических требований, но особое значение придают эстетическим...
Общие условия выбора системы дренажа: Система дренажа выбирается в зависимости от характера защищаемого...
Организация стока поверхностных вод: Наибольшее количество влаги на земном шаре испаряется с поверхности морей и океанов (88‰)...
Типы сооружений для обработки осадков: Септиками называются сооружения, в которых одновременно происходят осветление сточной жидкости...
© cyberpedia.su 2017-2024 - Не является автором материалов. Исключительное право сохранено за автором текста.
Если вы не хотите, чтобы данный материал был у нас на сайте, перейдите по ссылке: Нарушение авторских прав. Мы поможем в написании вашей работы!