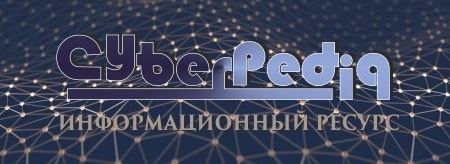
Биохимия спиртового брожения: Основу технологии получения пива составляет спиртовое брожение, - при котором сахар превращается...
Особенности сооружения опор в сложных условиях: Сооружение ВЛ в районах с суровыми климатическими и тяжелыми геологическими условиями...
Топ:
История развития методов оптимизации: теорема Куна-Таккера, метод Лагранжа, роль выпуклости в оптимизации...
Выпускная квалификационная работа: Основная часть ВКР, как правило, состоит из двух-трех глав, каждая из которых, в свою очередь...
Установка замедленного коксования: Чем выше температура и ниже давление, тем место разрыва углеродной цепи всё больше смещается к её концу и значительно возрастает...
Интересное:
Распространение рака на другие отдаленные от желудка органы: Характерных симптомов рака желудка не существует. Выраженные симптомы появляются, когда опухоль...
Влияние предпринимательской среды на эффективное функционирование предприятия: Предпринимательская среда – это совокупность внешних и внутренних факторов, оказывающих влияние на функционирование фирмы...
Берегоукрепление оползневых склонов: На прибрежных склонах основной причиной развития оползневых процессов является подмыв водами рек естественных склонов...
Дисциплины:
![]() |
![]() |
5.00
из
|
Заказать работу |
|
|
Рисунок 5.19 – Гидродемпфер буксовый
Поводок буксовый
Поводки буксовые (рис. 5.20) передают тяговые и тормозные усилия от колесной пары и удерживают ее в определенном положении относительно рамы тележки. За счет деформации резиновых амортизаторов поводки допускают упругие поперечные и вертикальные перемещения букс относительно рам тележек.
Буксовый поводок состоит из: амортизатора поводка длинного 1, амортизатора поводка короткого 2, амортизатора торцевого 3, корпуса поводка 6, штифтов 7 и проставочной втулки 8. Амортизаторы запрессованы в корпусе поводка, а торцевые амортизаторы на валики.
Буксовое рессорное подвешивание
Буксовое рессорное подвешивание предназначено для создания упругой связи между рамой тележки и колесной парой и обеспечения требуемых нормативных характеристик связи колесной пары с рамой тележки.
ТЕХНИЧЕСКАЯ ХАРАКТЕРИСТИКА
1. Высота в свободном состоянии, мм………………………………………… ;
2. Высота под статической нагрузкой, мм…………………………………….. ;
3. Прогиб пружины под статической
нагрузкой 4625 кгс, мм………………………………………………………. 93;
4. Наружный диаметр, мм……………………………………………………… 227;
5. Диаметр прутка, мм………………………………………………………….. 38;
6. Материал……………………………………………………………………… шлифованный
пруток из стали
60С2ХА;
7. Жесткость пружины продольная, кгс/мм…………………………………... 47,5;
|
8. Жесткость пружины поперечная, кгс/мм…………………………………... 25,2;
9. Напряжение в витках пружины, кгс/мм2…………………………………… 53;
10. Масса пружины, кгс…………………………………………………………. 42,4.
Буксовая ступень рессорного подвешивания (рис. 5.21) состоит из пружин 1, амортизаторов 2, нижних 3 и верхних 4 направляющих чаш, опоры 5. Верхние чаши имеют направляющие штыри для фиксирования амортизаторов и пружин на раме тележки и резьбовые отверстия для ввертывания технологических болтов, служащих для фиксации пружин в сжатом состоянии при их монтаже и демонтаже. Для регулирования нагрузок на колеса и оси электровоза при взвешивании между рамой тележки и резино-металлическими амортизаторами устанавливаются регулировочные шайбы 6 и 7.
![]() |
При переточке бандажей, а также переподкатке колесных пар необходимо заново отрегулировать распределение нагрузки по колесам и колесным парам установкой (снятием) шайб поз.6 и 7, при этом устанавливать (снимать) шайбы допускается только под обе пружины буксы одинаковой толщины. При отсутствии в депо весов допускается развеску регулировать ориентируясь на высоты пружин поз.1, которые замерены на электровозе после регулировки развески на заводе – изготовителе на прямом нивелированном пути и занесены в формуляр электровоза. Разность высот пружин указанных в формуляре электровоза и замеренных вновь при регулировке развески допускается не более 1 мм. Замеры высот пружин производить на полностью укомплектованном, собранном и экипированном электровозе на прямом, нивелированном пути удовлетворяющем требованиям инструкции ЭП2К.31.07.000И. Действительные высоты пружин определяются путем замера размера Е (рисунок 5.21) при этом величина Е-10 мм соответствует высоте пружины. Размеры Е замерять с точностью 0,1 мм. Замеры размера Е производить в плоскости перпендикулярной продольной оси тележки, проходящей через ось пружины. при регулировки развески необходимо иметь ввиду, что разность радиусов колеса до переточки и после должна быть примерно равна суммарной толщине шайб 6 и 7 устанавливаемых под каждую пружину букс колесной пары подвергнутой переточки. При установки шайб поз.6 и 7 необходимо иметь ввиду, что максимальная суммарная их толщина с учетом установленных ранее должна быть не более 16 мм. После регулировки развески необходимо проверить центровку полых валов относительно колесных пар и при необходимости отцентрировать.
|
В случае выкатки и разборки тележки необходимо вновь оттарировать пружины буксового рессорного подвешивания с занесением новых данных тарировки на бирки
прикрепленные к пружинам и в формуляр электровоза. В этом случае при отсутствии в депо весов развеску электровоза допускается регулировать руководствуясь данными тарировки. При этом при сборке тележки количество шайб 6 и 7 под каждую пружину подбирать так, чтобы фактическая высота пружины, указанная на бирке вновь и суммарная толщина шайб 6 и 7 устанавливаемых на одну пружину составляла величину 350 мм, а при замере высоты буксовых пружин на укомплектованном, собранном и экипированном электровозе на прямом нивелированном пути их разность с обозначенной на бирке вновь не должна превышать 3 мм. Кроме того необходимо отрегулировать зазоры между ограничителями вертикальных перемещений букс и рамой тележки (размеры В и Г) прокладками 9 на прямом нивелированном пути, которые должны быть 32-1 мм для крайних колесных пар и 30 ± 1 мм для средних, и занести эти новые данные по зазорам в формуляр электровоза.
5.1.14.Система смазки гребней колес
Система смазки гребней колес предназначена для автоматической подачи смазки на гребни колес первой по ходу движения колесной пары электровоза с целью уменьшения их износа. Принципиальная схема системы смазки гребней колес показана на рис.5.22.
Электронный блок управления; 2,3– Насосы; 4,5– Резервуары; SP13– Сигнализатор отпуска тормозов; КН1,КН2– Разобщительные краны; ФР1–ФР4– Форсунки; Y18, Y19– Электропневматические вентили ВВ–1415;.
Рисунок 5.22- Система смазки гребней колес. Схема принципиальная
В качестве смазки используется осевое масло летнее или зимнее по ГОСТ 610-72, которое заливается в два резервуара 4,5 объемом по 15,5л расположенных в переднем и заднем тамбурах.
|
При движении электровоза электронный блок управления 1 (в зависимости от направления движения) подает питание через определенный промежуток времени на электропневматический вентиль Y18 или Y19. При этом электропневматический вентиль открывается и воздух из питательной магистрали поступает к пневматическому приводу насоса 2 или 3 и форсункам ФР1, ФР2 или ФР3,Фр4.
Насосы подают порцию масла к форсункам. Под действием давления масла форсунка открывается и распыляемое потоком воздуха масло подается на гребни первой по ходу движения колесной пары. Форсунки устанавливаются на кронштейнах рамы тележки. Электропневматический вентиль и насос установлены на корпусе резервуара.
Для приведения в действие системы гребнесмазывателя необходимо открыть разобщительные краны КН1 или КН2 (рисунок 5.22) на подводящем воздухопроводе и включить тумблер “Гребнесмазыватель” на пульте управления в кабине машиниста.
Система приходит в действие при достижении электровозом скорости 20 км/час. На стоянке проверить работоспособность пневматической и гидравлической части системы гребнесмазывания и правильности регулировки положения форсунок можно нажатием на кнопку электропневматического вентиля Y18 или Y19.
При пневматическом торможении воздух поступает к сигнализатору отпуска тормозов SP13, что приводит к замыканию его контактов и блокированию системы подачи смазки.
Система смазки гребней колес конструктивно состоит из электронной системы управления, блока подачи смазки, форсунок и трубопроводов масла и воздуха.
Блок подачи смазки (рис.5.23) представляет собой резервуар 1 с закрепленным на нем насосом 2 и электропневматическим вентилем 3. В корпусе резервуара установлен фильтр 4, поджатый пружиной 5 к упору 6 и клапан 7, который при снятии насоса под действием пружины 8 перекрывает отверстия В и Г. Масло заливается через крышку 9 и его уровень контролируется щупом 10. Масло из резервуара через отверстия Б, В, Г самотеком поступает в насос.
1– Резервуар; 2–Насос; 3– Электропневматический вентиль ВВ–1415; 4– Фильтр;
|
|
Поперечные профили набережных и береговой полосы: На городских территориях берегоукрепление проектируют с учетом технических и экономических требований, но особое значение придают эстетическим...
Типы оградительных сооружений в морском порту: По расположению оградительных сооружений в плане различают волноломы, обе оконечности...
Биохимия спиртового брожения: Основу технологии получения пива составляет спиртовое брожение, - при котором сахар превращается...
Организация стока поверхностных вод: Наибольшее количество влаги на земном шаре испаряется с поверхности морей и океанов (88‰)...
© cyberpedia.su 2017-2024 - Не является автором материалов. Исключительное право сохранено за автором текста.
Если вы не хотите, чтобы данный материал был у нас на сайте, перейдите по ссылке: Нарушение авторских прав. Мы поможем в написании вашей работы!