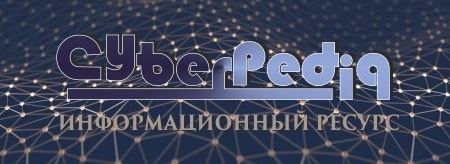
Своеобразие русской архитектуры: Основной материал – дерево – быстрота постройки, но недолговечность и необходимость деления...
Механическое удерживание земляных масс: Механическое удерживание земляных масс на склоне обеспечивают контрфорсными сооружениями различных конструкций...
Топ:
История развития методов оптимизации: теорема Куна-Таккера, метод Лагранжа, роль выпуклости в оптимизации...
Комплексной системы оценки состояния охраны труда на производственном объекте (КСОТ-П): Цели и задачи Комплексной системы оценки состояния охраны труда и определению факторов рисков по охране труда...
Интересное:
Что нужно делать при лейкемии: Прежде всего, необходимо выяснить, не страдаете ли вы каким-либо душевным недугом...
Распространение рака на другие отдаленные от желудка органы: Характерных симптомов рака желудка не существует. Выраженные симптомы появляются, когда опухоль...
Мероприятия для защиты от морозного пучения грунтов: Инженерная защита от морозного (криогенного) пучения грунтов необходима для легких малоэтажных зданий и других сооружений...
Дисциплины:
![]() |
![]() |
5.00
из
|
Заказать работу |
Этот способ основан на передаче давления прессования воздуха через эластичную диафрагму к заготовке, уложенной на жесткую матрицу-форму. Внутренняя поверхность изделия оформляется матрицей, а внешняя — резиновым мешком и цулагой (рис. 2.15). Укладку пакета из ПКМ на форму осуществляют вручную с помощью приемов, описанных выше.
Эластичный мешок закрепляют на основании формы, при этом образуется герметично замкнутый объем. Цулагу жестко скрепляют с формой накидными прижимами. Прессование
![]() |
Рис.2.15. Схема вакуумно-пресс-ка-мерного формования: 1 - форма; 2 — резиновый чехол; 3 — цулага; 4 - прессуемая заготовка; 5 — зажимы; 6 — основание формы |
осуществляется при подаче в мешок сжатого воздуха. Под давлением мешок растягивается в камере и плотно прижимается с одной стороны к уложенной на форме заготовке, а с другой стороны — к поверхности цулаги. После чего матрицу подвергают нагреву, и изделие отверждается. Режимы термообработки и прессования определяются свойствами компонентов ПКМ, конструкцией и габаритами изделия. Обычно давление прессования в камере не превышает 0,5 МПа. Во избежание изменения формы готовое изделие охлаждают под давлением, а затем снимают с формы.
Из-за разности давлений внутри эластичного мешка и окружающего воздуха форма испытывает значительные нагрузки. Поэтому формы для пневматического формования делают более прочными и жесткими, чем при вакуумном формовании.
Этим способом можно формовать практически любые волокнистые и слоистые материалы.
2.5. Особенности конструирования деталей с учетом
технологии контактного формования и формования
с эластичной диафрагмой
Может показаться, что изменить конфигурацию или толщину нового изделия достаточно просто. Однако при формовании деталей в открытой форме эти изменения необходимо осуществлять с учетом всех возможных последствий.
1. Перед формованием детали материал необходимо уложить в форму строго в соответствии с ее очертанием. При наличии острых углов (угол 90° без закруглений) маты не закрывают всю поверхность формы, и за наружным смоляным слоем около углов образуются пузырьки воздуха. При наличии
148
149
2.5. Особенности конструирования деталей
внутренних прямых углов, выполненных без закруглений, материал не будет прилегать к поверхности формы. Если же форма имеет наружные прямые углы, КМ также не сможет их плотно охватить.
Для предотвращения этих явлений рекомендуется закруглять внутренние и наружные углы по радиусу 3,00... 10,00 мм. В этом случае КМ будет полнее следовать очертанию формы, т.е. драпируемость будет лучше. Места резких переходов поверхности являются зонами концентрации высоких напряжений, где может происходить расслоение и растрескивание материала. Очевидно, что в конструкциях следует избегать таких мест и предусматривать самоупрочняющиеся переходные участки умеренного изгиба.
2. Для изменения толщины изделия, формуемого в открытой форме, следует увеличить (или уменьшить) число слоев материала. При необходимости резких изменений слои следует тщательно укладывать точно в соответствии с очертанием формы, что, однако, увеличивает затраты на ручной труд. В местах утолщений происходит концентрация напряжений и, как следствие, расслоение материала. Поэтому надо избегать появления таких высоконапряженных зон. С этой целью рекомендуется толщину изделия изменять постепенно, укладывая слои материала ступенчато или как кровельную черепицу.
3. Наиболее удобным для формования следует считать круглое отверстие; самым неудобным — отверстие с острыми незакругленными углами. Для предотвращения роста напряжений рекомендуется увеличивать радиусы закруглений в углах, а толщину изделия в острых углах увеличивать постепенно или предусматривать фланцы вокруг отверстий.
4. Изделия из ПКМ часто получают соединением нескольких отдельных деталей. Поэтому в зависимости от прочности (от большей к меньшей) следует различать соединения: нахлес-точные, работающие на сдвиг; стыковые; косые нахлесточные, работающие на раздир (на расслаивание).
Нахлесточные соединения являются самыми легкими и широко используемыми при изготовлении деталей из ПКМ (рис. 2.16, а). Их форма и особенности нагружения (на сдвиг) предполагают применение клеев, что обеспечивает максимальную прочность соединения. Разрушение нахлесточного соеди-
2. ТЕХНОЛОГИЯ КОНСТРУКЦИЙ ИЗ ПОЛИМЕРНЫХ КОМПОЗИЦИЙ
нения под действием напряжений сдвига происходит тогда, когда при возрастании нагрузки оно начинает работать на раздир.
При увеличении нагрузки происходит поворот места соединения, при этом действующие силы располагаются на одной оси (см. рис. 2.16, а). Этот поворот приводит к изгибанию материала и расслаиванию его на концах нахлеста. Если нагрузки продолжают расти, расслаивающие напряжения могут превысить адгезионную прочность, и соединение быстро разрушится. Однако если края нахлеста скошены, жесткость конструкции уменьшается и в результате повышается прочность соединения без увеличения площади его поверхности. Более того, при надлежащей подготовке материалов можно получить еще более высокие значения прочности при той же поверхности сдвига, выполнив соединение деталей вскос ("в ус") (см. рис.2.16, б).
Рис. 2.16. Примеры технологических соединений при склеивании
материалов:
а — нахлестанное; б — вскос (в "ус"); в — стыковое: 1 — слой клея;
2, 3 — жесткие материалы; 4 - промежуточный слой
Стыковое соединение со слоем клея и промежуточными слоями используют при склеивании жестких материалов, оно работает только на растяжение (рис. 2.16, в). Прочность его обычно колеблется от низких до средних значений, и ее легко
150
151
2.6. Формообразование давлением
рассчитать. Однако в реальных конструкциях такие соединения встречаются редко.
Соединение, работающее на раздир, представляет собой конструкцию, в которой напряжения концентрируются вдоль линии, по которой один склеиваемый материал отгибается от другого, в результате чего в материалах возникают неуравновешенные растягивающие напряжения (см. рис. 2.16, в). В таком соединении под нагрузкой оказывается только тот участок клеевого шва, который находится в точке расслаивания, а остальные участки шва остаются ненагруженными до тех пор, пока до них не дойдет зона расслаивания.
5. Минимальный угол технологического уклона должен составлять 2° (нулевой уклон — только в разъемных формах). Поднутрения не желательны, допускаются только в разъемных и резиновых формах.
6. Минимальную реальную толщину изделий при формовании ручной укладкой слоев следует задавать 0,8 мм, при напылении — 1,5 мм. Максимальная реальная толщина, в принципе, не ограничивается, но с учетом отверждения должна составлять 8... 10 мм. Стандартная разнотолщинность: при формовании ручной укладкой слоев — от +0,8 до —0,4 мм и при напылении — от +0,64 до —0,64 мм. Максимальное увеличение толщины не ограничивается.
влением |
2.6. Формообразование да
1. ТЕХНОЛОГИЯ КОНСТРУКЦИЙ ИЗ ПОЛИМЕРНЫХ КОМПОЗИЦИЙ
Пропитка под давлением
Сущность этого метода формования заключается в том, что связующее подают под давлением к нижнему отверстию формы и постепенно оно заполняет пространство между матрицей и пуансоном, вытесняя воздух из материала, уложенного на матрицу (рис. 2.17).
Рис. 2.17. Схема пропитки пакета материала под давлением:
/ — пуансон; 2 — пакет материала; 3 — матрица; 4 ~ бачок со связующим;
5 — установка для подогрева органического теплоносителя; 6 - компрессор
Способность смолы растекаться в замкнутом объеме формы под действием давления используют для изготовления изделий с простой симметричной формой. Этот способ формообразования позволяет получать конструкции с высокой точностью геометрических размеров, постоянной плотностью по объему материала стенки, при этом стенка драктически не будет иметь пустот или местных расслоений. Такие требования необходимо выполнять, например, при изготовлении различных типов обтекателей ЛА. В этой области метод и получил наиболее широкое применение.
Способ изготовления форм для пропитки отличается от способа изготовления форм для контактного формования, он более трудоемкий, поскольку требуется обеспечить с высокой точностью зазор между матрицей и пуансоном, равный толщине стенки изделия. Поэтому для изготовления металлических и неметаллических форм, применяют модель из того же материала и с такой же толщиной стенок, как и у изделия. Эту модель обычно формуют на гипсовой оправке, и она является точным объемным макетом поверхности изделия. Одновременно модель служит технологической оснасткой для изготовления нижней части формы (матрицы) и верхней части (пуансона).
152
153
2.6. Формообразование давлением
2. ТЕХНОЛОГИЯ КОНСТРУКЦИЙ ИЗ ПОЛИМЕРНЫХ КОМПОЗИЦИЙ
Толщины стенок матрицы и пуансона для конкретного изделия определяют экспериментальным путем.
Подготока поверхностей матрицы и пуансона заключается в нанесении антиадгезивных смазок или разделительных пленок так же, как и в случае контактного формования. Сухой армирующий материал выкладывают на матрицу до закрытия ее верхней частью формы и свинчивания.
Перед пропиткой материал, уложенный между позитивной и негативной формами, следует высушить. Для сушки через форму пропускают поток горячего воздуха, подаваемый от калорифера. В некоторых случаях для малогабаритных изделий осуществляют "промывку" армирующего материала той же смолой, которая входит в состав связующего. Таким образом удаляют пузырьки воздуха из материала и тем самым устраняют опасность образования в изделии незаполненных смолой участков. Однако для крупногабаритных изделий операция "промывки" экономически не выгодна.
Давление связующего в процессе пропитки, воздействуя на стенки матрицы и пуансона, расширяет зазор между ними и способствует равномерному заполнению связующим армирующего материала. Поэтому в данном случае небольшая неравномерность при укладке материала на матрицу не имеет существенного значения. Скорость подъема связующего по форме ограничена условиями качественной пропитки. Если эту скорость превысить, то связующее зальет воздушные пузырьки до того, как они отделятся от волокна. Тогда пузырьки можно удалить только путем "промывки" новой порцией чистой смолы; такая промывка настолька длительна, что полностью обесценивает все другие преимущества процесса.
Для качественной пропитки следует регулировать и контролировать температуру, вязкость и скорость, с которой поднимается связующее.
После того, как связующее появляется в выводных отверстиях в верхней части формы, подачу связующего прекращают, и с целью ускорения процесса отверждения форму начинают обогревать. В некоторых случаях пропитку материала осуществляют в уже разогретой форме, для чего используют соответствующие обогревательные устройства. Иногда в качестве нагревателя используют медную проволоку, обмотанную вокруг
формы. В ряде случаев отверждение изделий проводят в печах, в которые помещают форму. Параметры отверждения определяются типом применяемого связующего.
В том случае, когда требуется обеспечить высокую производительность процесса, применяют короткие рубленые волокна (50...70 мм), предварительно отформованные по форме изделия. Однако в этом случае невозможно получить высокопрочный материал.
Пропитка в вакууме
Процесс формования изделий пропиткой в вакууме (технология подготовки формы, укладки материала заготовки) аналогичен процессу формования пропиткой под давлением. Схема вакуумной пропитки показана на рис. 2.18.
-2
Рис. 2.18. Схема формования:
/ - связующее; 2 - запорное устройство; 3 - пуансон; 4 - смотровое стекло; 5 - вакуумная система; 6 - бачок для излишков связующего; 7 - заготовка; 8 - матрица; 9 - канал для прохождения связующего; 10 — эластичная прокладка
При использовании вакуума элементы формы должны быть достаточно жесткими для предотвращения сдавливания армирующего материала и нарушения свободного протекания смолы при возможном сплющивании матрицы или пуансона. Если
154
155
2.7. Формообразование прессованием в формах
материал *по форме расположен неравномерно, то через некоторые уплотненные участки смола проходить не будет, и эти участки останутся непропитанными. По мере приближения смолы к верхнему выводному отверстию необходимо для обеспечения дальнейшего ее движения увеличивать вакуум.
2.7. Формообразование прессованием в формах
В общем случае метод формования изделий прессованием -это процесс, при котором материал в пресс-форме принимает заданную конфигурацию, определяемую матрицей и пуансоном, причем отверждение его происходит в форме.
В настоящее время около 50 % всех изделий из армированных пластмасс получают этим методом. Его применяют в том случае, когда требуются высокая производительность, точность и воспроизводимость деталей. При этом достигается высокое качество изделий при минимальной стоимости. Но даже если объем производства невелик, например при получении деталей аэрокосмических аппаратов и других изделий с высокими эксплуатационными свойствами, требования к точности и воспроизводимости деталей заставляют использовать методы формования в пресс-формах.
Для всех случаев формования используют пресс-формы. Форма или комплект формующих деталей обычно состоит из двух основных частей: матрицы и пуансона, причем одна из них входит в другую при смыкании формы с соблюдением заданного зазора между ними, равного толщине формуемой детали.
В зависимости от применяемого армирующего материала, конструкции формы, способа загрузки материала в форму различают три основных метода формообразования изделий из ПКМ: прямое прессование; литьевое прессование; термокомпрессионное прессование. Особенности технологии изготовления деталей этими методами описаны ниже.
2. ТЕХНОЛОГИЯ КОНСТРУКЦИЙ ИЗ ПОЛИМЕРНЫХ КОМПОЗИЦИЙ
Прямое прессование
Этот метод прессования является одним из наиболее распространенных в производстве изделий прессованием. Метод прямого прессования армированных композиций несущественно отличается от формования пластмасс. Главное различие заключается в природе самого материала, из которого прессуется деталь. Вместо свободно текущих смол или порошков на формование поступает липкая волокнистая масса, таблетиро-ванные ПКМ, пропитанные маты, ткани или предварительно отформованные заготовки из ПКМ либо премиксы.
![]() |
Премикс — армированная волокном термореактивная композиция, которая после получения не нуждается в дальнейшем отверждении и может быть отформована при приложении давления, достаточного только для течения и уплотнения материала.
Для прессования изделий из ПКМ в большинстве случаев применяют гидравлические прессы, так как они обеспечивают постоянное давление на прессуемую деталь в течение всего времени прессования и, кроме того, они проще и надежней в эксплуатации, чем механические прессы. Гидравлические прессы приводятся в действие давлением жидкости (воды или масла), подаваемой насосом в цилиндр пресса.
Рис.2Л9. Схема устройства гидравлического пресса нижнего давления: / — верхняя неподвижная плита (траверса); 2 — пуансон; 3 — направляющая колонна; 4 — матрица; 5 - нижняя подвижная плита (стол); 6 — станина; 7 -рабочий плунжер; 8 — гидравлический цилиндр |
Обычно используют гидравлические прессы с одним рабочим цилиндром (с нижним или верхним расположением) или с двумя рабочими цилиндрами (вертикальные и угловые).
На рис. 2.19 показана схема устройства гидравлического пресса с нижним расположением рабочего цилиндра.
Верхняя плита и станина пресса, связанные между собой колон-
156
157
2.7. Формообразование прессованием в формах
2. ТЕХНОЛОГИЯ КОНСТРУКЦИЙ ИЗ ПОЛИМЕРНЫХ КОМПОЗИЦИЙ
нами, воспринимают усилие пресса, развиваемое плунжером рабочего цилиндра. Установленная на нижнюю подвижную плиту пресс-форма с загруженным в нее материалом при подъеме плунжера прижимается к верхней неподвижной плите, и материал в пресс-форме подвергается прессованию. При прекращении подачи воды в рабочий цилиндр и сообщении его со сливной магистралью плунжер пресса и подвижная плита силой своего веса вытесняют жидкость из рабочего цилиндра и опускаются.
Прессы с нижним давлением чаще всего используют для прессования изделий в съемных пресс-формах. Такие прессы иногда имеют промежуточные подвижные плиты, которые называют этажными.
Для нагревания съемных пресс-форм на нижней подвижной плите и верхней неподвижной плите пресса закрепляют обогревательные плиты, изолированные с опорной поверхности теплоизоляционными прокладками. Промежуточные подвижные плиты этажных прессов также имеют обогрев.
Прессы с верхним расположением рабочего цилиндра, т.е. прессы с верхним давлением (рис. 2.20), применяют главным образом для прямого прессования деталей из ПКМ в стационарных пресс-формах. Отличие этих прессов от прессов с нижним рабочим давлением состоит в том, что они имеют вспомогательные цилиндры обратного хода (ретурные цилиндры) и цилиндр выталкивателя, закрепленные на нижней неподвижной плите. Ретурные цилиндры служат для подъема подвижных рабочих частей пресса — верхней подвижной плиты и плунжера. Цилиндр выталкивателя обеспечивает извлечение отпрессованных деталей из пресс-формы. Прессы с верхним расположением рабочего цилиндра, как правило, бывают только одноэтажные.
Основным элементом технологического оснащения процесса прессования является пресс-форма, сложность и стоимость которой определяют качество и себестоимость изделий.
Пресс-формы в соответствии с методом прессования подразделяют на пресс-формы для обычного прессования (компрессионные) и литьевые для литьевого прессования; согласно характеру эксплуатации — на съемные, полусъемные и стационарные в зависимости от числа оформляющих гнезд (числа
одновременно прессуемых деталей) — на одногнездовые и многогнездовые.
В соответствии с принципом устройства оформляющего гнезда пресс-формы для прямого прессования подразделяют на открытые, полузакрытые и закрытые пресс-формы.
![]() |
Рис. 2.20. Схема устройства гидравлического пресса с верхним расположением рабочего цилиндра: 1 - станина (нижняя подвижная плита или рабочий стол); 2 - колонна; 3 — верхняя неподвижная плита (головка); 4 — рабочий цилиндр; 5-плунжер; 6 — верхняя подвижная плита; 7- упоры; 8 — пазы в верхней подвижной и нижней неподвижной плитах для закрепления пресс-формы; 9 — выталкиватель; 10 — цилиндры обратного хода (ретурные цилиндры); // —опорные рамы; 12- цилиндр выталкивателя
Пресс-формы открытого типа (рис. 2.21). Такие пресс-формы не имеют загрузочной камеры, уплотнение прессуемого в них материала достигается за счет трения, которое возникает при вытекании материала из оформляющего гнезда через зазор между пуансоном и матрицей. Поэтому для прессования в открытой пресс-форме необходим значительный избыток материала (до 10...15 %).
158
159
2.7. Формообразование прессованием в формах
2. ТЕХНОЛОГИЯ КОНСТРУКЦИЙ ИЗ ПОЛИМЕРНЫХ КОМПОЗИЦИЙ
![]() |
Так как сопротивление вытеканию материала постоянно
Рис. 2.21.Схема съемной пресс-формы открытого типа: / - пуансон; 2 - направляющая колонна; 3 — ручки; 4 — матрица; 5 — выталкиватель; 6 — заготовка |
изменяется по мере уменьшения зазора между пуансоном и матрицей и зависит от свойств материала, то применение открытых пресс-форм для прессования изделий из термореактивных пластических масс возможно только в случае прессования несложных изделий с небольшой высотой вертикальных стенок. Детали, отпрессованные в открытых пресс-формах, имеют низкую точность по высоте.
![]() |
Рис. 2.22.Схема пресс-формы полузакрытого типа: а ~ с горизонтальной плоскостью разъема; б — с вертикальной плоскостью разъема; / — пуансон; 2 — матрица; 3 — вкладыш; 4 — обойма |
Пресс-формы полузакрытого типа, или пресс-формы с перетеканием (рис. 2.22). В них, как и в пресс-формах открытого типа, необходимое уплотнение достигается за счет трения, возникающего при вытекании материала из оформляющего гнезда. Однако зазор, через который вытекает материал, регламентирован и остается практически постоянным в течение всего процесса формования. Такие пресс-формы обеспечивают большую степень уплотнения прессуемого материала, чем пресс-формы открытого типа, что позволяет оформлять в них сложные детали. В полузакрытых пресс-формах матрицы имеют
надпрессовочное пространство - загрузочную камеру, являющуюся продолжением оформляющего гнезда.
Загрузочная камера служит для того, чтобы поместить в нее навеску пресс-материала. Для прессования в полузакрытых пресс-формах необходим меньший избыток материала, чем при прессовании в открытых пресс-формах.
Полузакрытые пресс-формы применяют главным образом для прессования изделий из пластических масс.
![]() |
Рис. 2.23. Схема пресс-формы закрытого типа; 1 — пуансон; 2 - матрица |
Закрытые (поршневые) пресс-формы (рис. 2.23). Характерно, что во время прессования материал практически не вытекает из оформляющего гнезда. Очертания пуансона таких пресс-форм в плане точно соответствуют очертаниям изделия. Это усложняет изготовление пресс-форм и обусловливает их сравнительно низкую эксплуатационную стойкость. Однако в таких пресс-формах достигается большее уплотнение материала при постоянном давлении на него со стороны пуансона в течение всего времени прессования. При прессовании в закрытых пресс-формах необходимо точно выбрать навеску прессуемого материала. Для промышленного производства в основном применяют металлические пресс-формы, изготовленные из износостойкой закаленной стали типа 4X13, У8А, ХВГ, 12ХНЗА, У10А и других.
Качество поверхности пресс-форм для изготовления армированных композиций необязательно должно быть высоким. Наличие наполнителей накладывает определенные ограничения на шероховатость и глянец прессованного изделия независимо от качества полированной поверхности формы. Тем не менее для защиты формы от коррозии, лучшего отделения готовых изделий, удаления следов инструментов от механической обработки ее поверхность желательно хромировать (толщина покрытия 10...25 мкм).
Для проведения опытных запрессовок или для прессования нескольких изделий возможно использование деревянных, пластмассовых или гипсовых форм. При небольших давлениях прессования формы можно изготавливать из цветных сплавов
160
11-243
161
2.7. Формообразование прессованием в формах
методом литья, но они имеют короткий срок службы, хотя и более дешевы, чем стальные.
Стадия извлечения изделий из формы является самой критической в процессе формования. Для облегчения этой операции, во-первых, необходимо на этапе разработки конструкции учитывать технологию ее изготовления, а во-вторых, применять антиадгезионные смазки или разделительные материалы, которые препятствуют прилипанию изделия к поверхности формы.
Материалы, употребляемые в качестве антиадгезивов, можно подразделить на два типа:
пленочные материалы или растворы, образующие защитную пленку;
жидкие или твердые вещества, размягчающиеся при температуре прессования и не образующие непрерывной пленки.
К первой группе относятся растворы поливинилового спирта в воде, растворы альгината натрия, целлофан, лавсан, фторопласт и другие материалы. Во всех случаях пленка оказывает влияние на образование дефектов поверхности отформованного изделия.
Вторую группу составляют смазывающие пленки, более удобные для нанесения на оснастку: воск, парафин, кремний-органические смазки (типа К-21), нефтяные остатки и т.п.
При выборе антиадгезивов необходимо учитывать температуру формования и воздействие их на связующее формуемого изделия.
Основными параметрами процессов прессования являются температура, давление, время.
Полуфабрикат в процессе формования необходимо нагревать до определенной температуры, чтобы придать ему требуемую пластичность, т.е. способность к формообразованию. Для термореактивных ПКМ нагревание необходимо также и для отверждения. Однако возможность повышения температуры формования всегда ограничена температурой деструкции и разложением связующих. Нагрев и охлаждение крупногабаритных изделий осуществляется нагревателями, расположенными в пресс-формах. В других случаях нагревательные устройства могут быть расположены как в самих пресс-формах, так и вне — в верхней и нижней плитах пресса. Время отверждения изделий
162
2. ТЕХНОЛОГИЯ КОНСТРУКЦИЙ ИЗ ПОЛИМЕРНЫХ КОМПОЗИЦИЙ
должно быть всегда больше времени, необходимого для заполнения материалом данной пресс-формы.
В процессе формования давление необходимо для уплотнения разогретого пластичного материала и придания ему конфигурации изделия. Давление на материал должно оказываться в течение всего времени, пока отформованное изделие не потеряет пластичность и не станет твердым в результате нагрева (для термореактивных композиций) или в результате охлаждения (для композиций на основе термопластов).
Время процесса определяется скоростью разогрева материала до пластического состояния и, главным образом, скоростью отверждения или скоростью охлаждения.
![]() |
Указанные три основные параметра процесса формования - температура, давление, время - взаимосвязаны. Изменение одного параметра влечет за собой изменение других. Например, повышение температуры формования термопластов улучшает их пластичность и, следовательно, уменьшает необходимое давление и длительность формования.
Основные параметры процесса определяют в каждом конкретном случае в зависимости от компонентов ПКМ, схемы армирования композита, геометрии и формы изделия и отрабатывают опытным путем.
Рис. 2.24.Схема прямого прессования: / - плиты обогрева; 2 - прессуемая деталь; 3 — матрица; 4 — выталкиватель; 5 — навеска полуфабриката; 6 — пуансон |
Прямое прессование (рис. 2.24) заключается в том, что тот или иной прессовочный материал помещают в матрицу, нагретую до температуры формования, на который действует давление Р верхней половины пресс-формы — пуансона, нагретой до такой же температуры. Под воздействием температуры материал приобретает необходимую пластичность и под давлением распределяется по оформляющей
163 |
2.7. Формообразование прессованием в формах
полости, заполняя ее. Полное закрытие формы (замыкание) происходит в момент окончательного оформления детали. Замыкание пресс-формы осуществляется с малой скоростью, чтобы воздушные включения были вытеснены из полости. Отформованное изделие выдерживают в пресс-форме под давлением в течение некоторого времени, необходимого для охлаждения термопластичного композита или нагрева термореактивного материала, после чего пресс-форму открывают, и изделие извлекают с помощью выталкивателя с усилием рв.
При неправильном выборе режимов прессования или некачественных материалах в изделиях могут появиться следующие дефекты: пузырьки воздуха вокруг выступающих участков на поверхности детали; места, содержащие недостаточное количество связующего из-за избытка армирующего наполнителя; растрескивание связующего и места, содержащие его избыток; матовая поверхность и пятна на изделии.
Каждый дефект имеет свои причины возникновения; рекомендации по их устранению обычно отражают в таком документе, как технологический регламент.
Рассмотрим особенности прямого прессования.
а. При оформлении детали можно запрессовать в нее раз
нообразную арматуру (винты, гайки, стержни и т.п.), которая
будет прочно удерживаться в детали.
б. Прогревание материала происходит постепенно от сте
нок нагретой пресс-формы вглубь, и, следовательно, в про
цессе формования изделия различные слои материала могут
иметь разную температуру.
в. Разность температуры по толщине изделия приводит к
образованию внутренних напряжений и дефектов в результате
неравномерного протекания процесса отверждения или вулка
низации.
г. Имеется опасность повреждения тонких и малопроч
ных оформляющих элементов пресс-формы или впрессо
вываемой в деталь арматуры, так как материал под давле
нием начинает заполнять оформляющую полость еще до
того момента, когда он весь прогреется и приобретет до
статочную пластичность. Для устранения этой опасности в
большинстве случаев программируют режим давления и
применяют несколько предварительных подпрессовок.
2. ТЕХНОЛОГИЯ КОНСТРУКЦИЙ ИЗ ПОЛИМЕРНЫХ КОМПОЗИЦИЙ
Кроме того, с помощью подпрессовки удаляют летучие и пары Влаги за короткий промежуток времени начальной стадии от-перждения материала.
д. На отформованных изделиях всегда образуются заусенцы (грат) в плоскости разъема пресс-формы.
Методом прямого прессования можно изготавливать изделия из любых материалов, как термопластичных, так и термореактивных. Практически этот метод применяют главным образом для изготовления деталей из термореактивных КМ. Использование его для формования деталей из термопластов нецелесообразно, так как в этом случае необходимо попеременно нагревать и охлаждать пресс-форму в течение каждого цикла формования, а это в значительной степени увеличивает длительность процесса.
Примерные режимы прямого прессования деталей, на которые ориентируются при отработке процесса формования, приведены в табл. 2.5.
Таблица 2.5 Примерные режимы прямого прессования
Наименование материала | Температура, К | Удельное давление min/max, МПа | Время вьщержки, мин | Усадка, % |
Термопластичные КМ Эластомеры Термореактивные КМ Премиксы | 393-523 343-473 393-473 393-473 | 2/15 0,4/25 3,0/75 3,5-7,0 | 5-15 3-60 3-15 1-3 | 1-3 1-2 0,2-1,2 0,5-1,0 |
Различные методы пропитки армирующего материала и режимы прессования позволяют получить содержание наполнителя в композите от 20 до 50 %.
Литьевое прессование
Литьевое прессование заключается в том, что прессуемый материал загружают в загрузочную камеру предварительно замкнутой пресс-формы (рис. 2.25). Нагреваясь от стенок загрузочной камеры и приобретая при этом необходимую пластичность, материал под давлением литьевого пуансона поступает через литниковый канал в оформляющую полость пресс-формы
164
165
2.7. Формообразование прессованием в формах
и заполняет ее. После выдержки, необходимой для затвердевания, пресс-форму раскрывают и извлекают готовое изделие вместе с литниковым остатком.
Рис. 2.25. Схема пресс-формы для литьевого прессования на прессах с одним рабочим цилиндром:
1 - коническая обойма матрицы; 2 - клиновая матрица; 3 - загрузочная камера; 4- литьевой пуансон; 5 - отформованное изделие; 6- выталкиватель; 7 - литниковый канал
Особенности литьевого прессования состоят в следующем:
а) можно изготавливать детали с малопрочной или сквозной
арматурой и детали с глубокими отверстиями малого диаметра,
так как материал поступает в оформляющую полость пресс-
формы уже в пластичном состоянии и не в состоянии оказать
на оформляющие элементы пресс-формы и впрессовываемую
арматуру значительных сил деформации;
б) процесс формования материала протекает быстрее, чем
при обычном прессовании;
в) в деталях, полученных литьевым прессованием, не воз
никают большие внутренние напряжения вследствие меньшего
перепада температур по толщине стенок детали;
г) на деталях, изготовленных литьевым прессованием, прак
тически не остается фата, так как оформляющая полость
пресс-формы, образуемая пуансоном и матрицей, плотно за
мыкается еще до заполнения ее материалом. Точность соблю
дения размеров деталей при этом методе высокая, а механи-
2. ТЕХНОЛОГИЯ КОНСТРУКЦИЙ ИЗ ПОЛИМЕРНЫХ КОМПОЗИЦИЙ
ческая доработка деталей сводится только к отрезке литников и зачистке мест сраза;
д) при литьевом прессовании расходуется больше материа
ла, чем при прямом прессовании, так как материал заполняет
литниковые каналы и в зафузочной камере запрессовывается
его остаток;
е) пресс-формы для литьевого прессования сложнее и до
роже пресс-форм для прямого прессования.
Методом литьевого прессования можно изготавливать изделия из резиновых смесей и порошкообразных пластических масс. Пластмассы с волокнистыми наполнителями теряют до 50 % своей прочности. Слоистые пластики перерабатывать литьевым методом нельзя, так как материал не в состоянии пройти из загрузочной камеры пресс-формы в ее оформляющую полость через узкие литниковые каналы.
Пресс-формы для литьевого прессования отличаются от пресс-форм прямого прессования тем, что они имеют зафу-зочную камеру для прессуемого материала, отделенную от оформляющего гнезда и связанную с ним литниковыми каналами. Оформляющее гнездо литьевой пресс-формы перед прессованием закрывают, а материал в него поступает уже в пластичном состоянии из зафузочной камеры по литникам.
Существует два принципиально различных конструктивных варианта литьевых пресс-форм — литьевые пресс-формы для прессования на специальных прессах с двумя рабочими цилиндрами (рис. 2.26) и литьевые пресс-формы для прессования на обычных прессах с одним рабочим цилиндром (см. рис. 2.25).
Для прессования детали в пресс-форме материал зафужают в загрузочную камеру, затем верхнюю половину пресс-формы опускают на нижнюю и удерживают под давлением плунжера верхнего рабочего цилиндра пресса, чтобы пресс-форма не раскрылась при заполнении материалом. Под действием давления нижнего рабочего плунжера пресса поднимается литьевой пуансон и выдавливает материал из загрузочной камеры по литникам в оформляющую полость. После окончания прессования пресс-форму открывают и изделия выталкивают дополнительным ходом литьевого пуансона.
Общие условия выбора системы дренажа: Система дренажа выбирается в зависимости от характера защищаемого...
Наброски и зарисовки растений, плодов, цветов: Освоить конструктивное построение структуры дерева через зарисовки отдельных деревьев, группы деревьев...
Опора деревянной одностоечной и способы укрепление угловых опор: Опоры ВЛ - конструкции, предназначенные для поддерживания проводов на необходимой высоте над землей, водой...
Индивидуальные и групповые автопоилки: для животных. Схемы и конструкции...
© cyberpedia.su 2017-2024 - Не является автором материалов. Исключительное право сохранено за автором текста.
Если вы не хотите, чтобы данный материал был у нас на сайте, перейдите по ссылке: Нарушение авторских прав. Мы поможем в написании вашей работы!