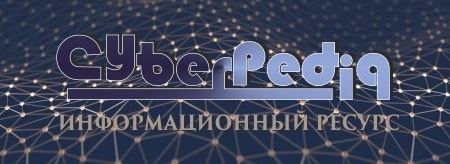
Механическое удерживание земляных масс: Механическое удерживание земляных масс на склоне обеспечивают контрфорсными сооружениями различных конструкций...
Общие условия выбора системы дренажа: Система дренажа выбирается в зависимости от характера защищаемого...
Топ:
Характеристика АТП и сварочно-жестяницкого участка: Транспорт в настоящее время является одной из важнейших отраслей народного...
Эволюция кровеносной системы позвоночных животных: Биологическая эволюция – необратимый процесс исторического развития живой природы...
Интересное:
Что нужно делать при лейкемии: Прежде всего, необходимо выяснить, не страдаете ли вы каким-либо душевным недугом...
Финансовый рынок и его значение в управлении денежными потоками на современном этапе: любому предприятию для расширения производства и увеличения прибыли нужны...
Аура как энергетическое поле: многослойную ауру человека можно представить себе подобным...
Дисциплины:
![]() |
![]() |
5.00
из
|
Заказать работу |
|
|
Ю.Н. Гондин, Б.В. Устинов
ПРОИЗВОДСТВЕННОЕ ОБОРУДОВАНИЕ
И ЕГО ЭКСПЛУАТАЦИЯ
КОМПЛЕКС УЧЕБНО-МЕТОДИЧЕСКИХ МАТЕРИАЛОВ
Рекомендовано Ученым советом Нижегородского государственного
технического университета в качестве учебно-методического пособия
для студентов очной, очно-заочной, заочной и дистанционной форм
обучения по специальностям
220301.65 «Автоматизация технологических процессов и производств»,
220402.65 «Роботы и робототехнические системы»
Часть 1
Нижний Новгород 2007
УДК 621.9.00
Гондин Ю.Н., Устинов Б.В. Производственное оборудование и его эксплуатация: комплекс учебно-методических материалов / Ю.Н. Гондин, Б.В. Устинов; Нижегород. гос. техн. ун-т. – Нижний Новгород, 2007. – 114 с.
Даются общие сведения о металлорежущих станках, включая назначение, технико-экономические показатели, методы формообразования обрабатываемых изделий, кинематические структуры станков, управление их рабочими органами, особенности конструкции различных технологических групп станков, а также сведения об эксплуатации этого оборудования.
Пособие предназначено для студентов очной, очно-заочной, заочной и дистанционной форм обучения технических специальностей.
Рецензент доктор технических наук, профессор А.А. Иванов
Редактор Н.Н. Максимова
Подписано в печать . Формат 60 х 84 1/16. Бумага офсетная.
Печать офсетная. Печ. л. 6,5. Уч.-изд. л. 6,0. Тираж 200. Заказ .
_______________________________________________________________________________________________________________________________________________________________________________________________
Нижегородский государственный технический университет.
Типография НГТУ. 603950, Н.Новгород, ул.Минина, 24.
|
© Нижегородский государственный
технический университет, 2007
© Гондин Ю.Н., Устинов Б.В. 2007
СОДЕРЖАНИЕ
1. Пояснительная записка....................................... | 5 |
2. Рабочая учебная программа по дисциплине...................... | 7 |
3. Опорный конспект лекций.................................... | 10 |
3.1. Общие сведения о станках.................................... | 10 |
3.1.1. Классификация станков.................................. | 10 |
3.1.2. Современная классификация металлорежущих станков и станочных систем......................................... | 12 |
3.1.3. Технико-экономические показатели станков................ | 21 |
3.2. Кинематические основы металлорежущих станков............... | 27 |
3.2.1. Методы образования поверхностей деталей при обработке на металлорежущих станках................................ | 27 |
3.2.2. Классификация движений................................ | 29 |
3.2.3. Основные понятия о приводе............................. | 30 |
3.2.4. Кинематические связи в станках.......................... | 31 |
3.2.5. Кинематическая структура станков........................ | 33 |
3.2.6. Кинематическая настройка станков........................ | 35 |
3.3. Станки для обработки тел вращения........................... | 37 |
3.3.1. Токарно-винторезные станки............................. | 38 |
3.3.2. Токарно-револьверные станки............................ | 40 |
3.3.3. Токарные многорезцовые станки.......................... | 43 |
3.3.4. Токарные лобовые станки................................ | 46 |
3.3.5. Токарные карусельные станки............................ | 47 |
3.3.6. Токарные автоматы и полуавтоматы....................... | 50 |
3.4. Станки для обработки призматических деталей.................. | 56 |
3.5. Сверлильные и расточные станки............................. | 63 |
3.5.1. Вертикально-сверлильные станки......................... | 64 |
3.5.2. Радиально-сверлильные станки........................... | 65 |
3.5.3. Расточные станки....................................... | 65 |
3.6. Шлифовальные станки....................................... | 68 |
3.6.1. Круглошлифовальные станки............................. | 70 |
3.6.2. Бесцентровые круглошлифовальные станки................. | 71 |
3.6.3. Внутришлифовальные станки............................. | 74 |
3.6.4. Плоскошлифовальные станки............................. | 75 |
3.7. Зубообрабатывающие станки................................. | 77 |
3.7.1. Зубодолбежные станки.................................. | 80 |
3.7.2. Зубофрезерные станки................................... | 82 |
3.8. Автоматические линии станков............................... | 85 |
3.8.1. Общие сведения........................................ | 85 |
3.8.2. Автоматизация на базе типового серийного оборудования....... | 87 |
3.8.3. Автоматизация на базе агрегатных станков................. | 89 |
3.8.4. Автоматизация на базе роторных машин................... | 92 |
3.8.5. Автоматизация на базе станков с ЧПУ..................... | 94 |
3.9. Станки с программным управлением........................... | 95 |
3.9.1. Числовая система программного управления................ | 95 |
3.9.2. Классификация и структура.............................. | 96 |
3.9.3. Исполнительные приводы металлорежущих систем с ЧПУ.... | 104 |
3.9.4. Многооперационные станки с ЧПУ........................ | 108 |
4. Список литературы........................................... | 114 |
|
ПОЯСНИТЕЛЬНАЯ ЗАПИСКА
Пособие предназначено для студентов очной, очно-заочной, заочной и дистанционной форм обучения специальностей 220301.65 «Автоматизация технологических процессов и производств» и 220402.65 «Роботы и робототехнические системы» и включает вопросы назначения, кинематики, устройства, расчета кинематических схем и основных узлов, а также эксплуатации основного технологического оборудования машиностроительного производства.
Известно, что основным оборудованием машиностроительных предприятий являются металлорежущие станки и станочные комплексы, с помощью которых ведется размерная обработка деталей. Многообразие конструктивного исполнения станков и комплексов вызвано не только большой номенклатурой обрабатываемых деталей, но и видом организации их производства.
Целью изучения дисциплины является обучение студентов основам методологии организации сложных структур комплексной автоматизации производства и эксплуатации технологического оборудования, а также системного подхода при анализе и синтезе сложных технологических процессов изготовления изделий на нем.
Для успешного освоения данной дисциплины необходимые базовые знания приобретаются в общеинженерных курсах: «Материаловедение», «Основы конструирования машин», «Теоретическая механика», «Электроприводы технологического оборудования» и др.
В результате освоения дисциплины студенты должны:
– иметь представление о станке как о рабочей машине, включающей в себя функциональные подсистемы, преобразующие материальные, информационные и энергетические потоки;
|
– знать структуру технологической машины, назначение и роль ее компонентов, методы формообразования;
– уметь настраивать оборудование на обработку деталей, производить кинематические расчеты его рабочих органов, подбирать необходимое оборудование при разработке техпроцесса на изготовление деталей.
Теоретический материал дает общие сведения о станках и технологических роботах, включая назначение, технико-экономические показатели, методы формообразования, кинематические структуры, понятие об управлении их рабочими органами, особенности кинематики и основных движений в различных технологических группах, назначение и состав основных узлов и механизмов, а также сведения об их эксплуатации.
Закрепление теоретических знаний производится на лабораторных занятиях, где студенты изучают назначение технологического оборудования, кинематические схемы, конструкцию основных рабочих органов и механизмов, производят настройку на обработку заданной детали, а также выполняют некоторые элементы приемочных испытаний.
Учебное пособие состоит из двух частей. Часть 1 содержит общие сведения о станочном оборудовании: назначение, классификация, технико-экономические показатели, кинематические связи и структуры, а также основные узлы и наиболее распространенные группы. В часть 2 вошли основные сведения по кинематическим расчетам, конструкции шпиндельных узлов станков, назначению и структуре технических роботов, а также основные понятия по эксплуатации технологического оборудования. Кроме того, здесь же представлены лабораторные работы по дисциплине, контрольные вопросы по лекционному материалу и глоссарий.
РАБОЧАЯ УЧЕБНАЯ ПРОГРАММА ПО ДИСЦИПЛИНЕ
Ведомость числа часов по рабочим учебным планам
Направление подготовки, направление специальности, специальность (шифр и наименование) | Форма обучения | Объем работы студентов (час) | Распределение по семестрам | |||||||
Всего | аудиторной | внеаудиторной | ||||||||
лекции | лабораторные занятия | практи-ческие занятия | курсовой проект (работа) | самостоятельная работа | экзамен | зачет | курсовое проектирование | |||
220200.62 «Автоматизация и управление» 220300.65 Автоматизированные технологии и производства» 220301.65 «Автоматизация технологических процессов и производств» 220400.65 «Мехатроника и робототехника» 220402.65 «Роботы и робототехнические системы» | ![]() | 72 | 54 | 18 | – | – | 48 | – | 6 | – |
220300.65 Автоматизированные технологии и производства» 220301.65 «Автоматизация технологических процессов и производств» | Павлово, Заволжье очно-заочная | 51 | 34 | 17 | – | – | 79 | 8 | – | – |
220301.65 «Автоматизация технологических процессов и производств» | заочная | 28 | 12 | 16 | – | – | 102 | 8 | – | – |
|
Часть 1
1. Основные понятия «машина» и «металлорежущий станок». Представление о станке как о системе. Применение станков и автоматизированного оборудования в зависимости от типа производства.
2. Классификация станков: по назначению, точности, стационарности, массе, степени универсальности и степени автоматизации. Обозначение моделей станков.
3. Формообразование поверхностей на металлорежущих станках. Методы формообразования: копирование, обкатка, методы следа и касания. Связь метода обработки с видами режущего инструмента.
4. Кинематическая структура и связи движений в станках. Состав движений. Приводы движений. Кинематические связи. Соединение кинематических цепей. Настройка кинематических цепей.
5. Станки для обработки деталей типа тел вращения. Разновидности и технологические возможности. Классификация, основные движения и инструмент. Структурные кинематические схемы станков: токарно-винторезных, токарно-револьверных, токарно-карусельных, многорезцовых токарных. Токарные автоматы. Классификация. Характерные механизмы. Станки шлифовальной группы. Классификация. Основные движения.
6. Станки для обработки призматических деталей. Классификация, выполняемые технологические операции, инструмент, основные движения. Структурные кинематические схемы станков фрезерной группы, сверлильной и расточной групп. Агрегатные станки.
7. Станки зубообрабатывающей группы. Классификация, выполняемые технологические операции, режущий инструмент, основные движения. Структурные кинематические схемы и настройка долбежных и зубофрезерных станков.
8. Автоматические линии. Классификация. Область рационального применения. Линии для обработки деталей тип тел вращения. Линии для обработки корпусных деталей. Переналаживаемые автоматические линии.
9. Станки с ЧПУ. Область рационального применения. Классификация систем ЧПУ. Структурная схема станка с ЧПУ. Точность станков с ЧПУ. Конструктивные особенности кинематики станков. Многооперационные станки с ЧПУ. Характерные механизмы.
|
Часть 2
1. Кинематические расчеты приводов станков. Структурные формулы. Структурные сетки. Графики частот вращения. Графо-аналитический метод кинематического расчета коробок скоростей с множительной структурой. Особые множительные структуры.
2. Особенности конструкций шпиндельных узлов металлорежущих станков. Схемы компоновок. Особенности конструкций шпинделей, материалы. Шпиндельные подшипники качения и скольжения. Расчеты шпиндельных узлов.
3. Промышленные роботы. Определение. Область применения. Структурная схема. Классификация.
4. Эксплуатация производственного оборудования. Понятие эксплуатации. Транспортирование. Требования к устройству помещений (цехов). Установка оборудования на фундамент. Испытание станков (разновидности). Ремонт оборудования.
ОПОРНЫЙ КОНСПЕКТ ЛЕКЦИЙ
Общие сведения о станках
Классификация станков
Основные определения
Металлорежущий станок (станок) – машина для размерной обработки заготовок в основном путем снятия стружки. В свою очередь «машина» представляет собой техническое устройство, работа которого основана на использовании механизмов и механического движения. Кроме металлических заготовок на станках обрабатывают также детали из других материалов. К станкам относят и технологическое оборудование, использующее для обработки электрофизические и электрохимические методы, сфокусированный электронный или лазерный лучи.
Помимо основной рабочей операции, связанной с изменением формы и размеров заготовки, на станке необходимо осуществлять вспомогательные операции для смены заготовок, их зажима, измерения, операции по смене режущего инструмента, контроля его состояния и состояния всего станка. В связи с большим разнообразием функций, выполняемых на станках, их целесообразно рассматривать как систему, состоящую из нескольких функциональных подсистем (рис.1).
Рис.1. Структурная схема станка:
I 0, I 1 – входная и выходная информация; М 0, М 1 – заготовки и изделия; Е – энергия;
1 – подсистема управления; 2 – подсистема контроля; 3 – подсистема манипулирования;
4 – подсистема обработки
Подсистема манипулирования обеспечивает доставку заготовок к месту обработки, их зажим в заданной позиции, перемещение к месту контроля и измерения и, наконец, вывод готовых изделий из рабочей зоны станка.
Таким образом, подсистема манипулирования обеспечивает поток материала, проходящего через рабочую зону станка в процессе его обработки. Дополнительные функции подсистемы манипулирования необходимы также для смены режущих инструментов и дополнительных приспособлений. Подсистема управления на основе входной внешней информации и дополнительной внутренней текущей информации от контрольных и измерительных устройств обеспечивает правильное функционирование всех остальных подсистем в соответствии с поставленной задачей. Входная информация поступает в виде чертежа, маршрутной технологии или заранее подготовленной управляющей программы.
Текущая информация о правильности состояния и поведения всей технологической системы (станка, инструмента, манипуляторов, вспомогательных устройств) поступает в подсистему управления при ручном управлении от органов чувств оператора, а при автоматизации контрольных функций – от соответствующих преобразователей (датчиков) подсистемы контроля. Выходная информация дает сведения о фактических размерах обработанной на станке детали по результатам ее измерения.
Собственно станок подразделяется на несколько важнейших частей, обычно называемых узлами. Главный привод станка сообщает движение инструменту или заготовке для осуществления процесса резания с соответствующей скоростью. У подавляющего большинства станков главный привод (рис.2) сообщает вращательное движение шпинделю, в котором закреплен режущий инструмент либо заготовка.
Рис.2. Основные узлы (сборочные единицы) станка:
1 – главный привод; 2 – базовые детали; 3 – приводы подачи
Привод подачи необходим для перемещения инструмента относительно заготовки при формировании обрабатываемой поверхности. У подавляющего большинства станков привод подачи сообщает узлу станка прямолинейное движение. Сочетанием нескольких прямолинейных, а иногда и вращательных движений, можно реализовать любую пространственную траекторию.
Привод позиционирования необходим во многих станках для перемещения того или иного узла станка из некоторой исходной позиции в другую заданную позицию, например, при последовательной обработке нескольких отверстий или нескольких параллельных плоскостей на одной и той же заготовке. Во многих современных станках с числовым программным управлением (ЧПУ) функции приводов подачи и позиционирования выполняет один общий привод.
Несущая система станка состоит из последовательного набора соединенных между собой базовых деталей. Соединения могут быть неподвижными (стыки) или подвижными (направляющие). Несущая система обеспечивает правильность взаимного расположения режущего инструмента и заготовки под воздействием силовых и температурных факторов.
Манипулирующие устройства необходимы для автоматизации различных вспомогательных движений в станке при смене заготовок, их зажиме, перемещении или повороте, смене режущих инструментов, удалении стружки и т.п. Современный многооперационный станок имеет набор манипуляторов, транспортеров, поворотных устройств, а в некоторых случаях обслуживается универсальным манипулятором с программным управлением (промышленным роботом).
Контрольные и измерительные устройства необходимы в станке для автоматизации наблюдения за правильностью его работы. С их помощью контролируют состояние наиболее ответственных частей станка, работоспособность режущего инструмента, измеряют заготовки и изделие. При достаточно высоком уровне автоматизации результаты контроля измерения поступают в управляющее устройство, а оттуда в виде управляющих сигналов корректируют положение узлов станка.
Устройство управления может быть с ручным обслуживанием оператором, с механической системой управления или с ЧПУ. В настоящее время происходит широкое внедрение микропроцессорных устройств ЧПУ для управления всеми видами станочного оборудования.
И станочных систем
Выбор основных направлений при создании новых типов станков и станочных систем (ССт), оценка их технического уровня и технико-экономических показателей, планирование выпуска и развитие систем автоматизированного проектирования металлорежущего оборудования в значительной степени зависят от того, насколько обоснованно установлены существенные признаки станков и ССт, объединенных многопараметрической классификацией, отражающей иерархию основных понятий.
В связи с указанным в ЭНИМСе разработана современная классификация металлорежущих станков и ССт (рис.3 и рис.4). В качестве определяющих параметров в классификации приняты подетальная и целевая специализация, а также степень автоматизации оборудования. На базе указанной классификации представлена система терминов и определений, в основу которой положен ряд исходных понятий; остальные формируются с их помощью. Определения указывают основное служебное назначение станка или ССт любого типа, обобщенные технические характеристики и, при необходимости, основные принципы конструктивного исполнения.
Рис.3. Классификация металлорежущих станков:
1 – станки-автоматы; 2 – станки-полуавтоматы; 3 – автоматизированные станки с ручным управлением; а – обеспечивается полностью автоматическая работа без участия оператора или при его минимальном участии; б – предполагается участие оператора в производственном процессе
Рис.4. Классификация станочных систем:
1 – автоматическая станочная линия, система автоматических станочных линий;
2 – полуавтоматическая станочная линия; 3 – поточная линия; 4 – участок специализированных станков; 5 – участок универсальных станков; а – обеспечивается полностью автоматическая работа без участия оператора или при его минимальном участии;
б – предполагается участие оператора в производственном процессе
(человеко-машинные системы)
Как видно из рис.4, специализированному и универсальному оборудованию свойственна гибкость, под которой понимается способность переходить от изготовления одного изделия к изготовлению другого с большей или меньшей степенью автоматизации и универсальности.
Таким образом, гибкость зависит от степени автоматизации и универсальности, причем последняя определяется номенклатурой изделий, производство которых по различной технологии возможно на станке или в ССт.
Применительно к гибким автоматизированным производственным системам (ГПС) в настоящее время принята система терминов и определений (табл.1), имеющая общепромышленный характер.
При описании подетальной специализации ССт используются термины, установленные применительно к станкам: специальным, специализированным и универсальным. Так, автоматические линии представляют собой специальные автоматические ССт, ГП линии – специализированные автоматические и автоматизированные ССт, ГП участки – универсальные автоматические и автоматизированные ССт.
Таблица 1
Таблица 2
Таблица 3
Системы станочные
Термин | Определение |
1 | 2 |
Система станочная | Управляемая совокупность металлорежущего и вспомогательного оборудования, предназначенная для обработки изделия (изделий) |
Оборудование вспомогательное | Совокупность транспортно-накопительных и загрузочно-разгрузочных устройств, предназначенных для хранения и перемещения предметов и орудий труда, а также отходов производства (заготовок, полуфабрикатов, деталей, инструментов, оснастки, стружки) |
Подсистема транспортно-накопительная | Автоматизированная или автоматическая совокупность устройств вспомогательного оборудования |
Подсистема управления | Автоматизированная или автоматическая совокупность технических средств (в частном случае вычислительной техники и программно-математического обеспечения), включающая также аппаратно и программно совместимые устройства управления оборудованием и предназначенная для организационно-технического управления, в том числе для преобразования и переработки информации о производственном процессе |
Окончание табл.3
1 | 2 |
Система станочная специальная | Система станочная, предназначенная для обработки одного изделия на основе одного маршрутного технологического процесса |
Система станочная специализированная | Система станочная, предназначенная для обработки конструктивно и технологически подобных изделий различных типоразмеров или наименований из определенной номенклатуры в определенном диапазоне геометрических параметров на основе одного или нескольких маршрутных технологических процессов |
Система станочная универсальная | Система станочная, предназначенная для обработки изделий различных типоразмеров или наименований из широкой номенклатуры в определенном диапазоне геометрических параметров на основе различных маршрутных технологических процессов с организацией свободного потока обрабатываемых изделий по схеме «станок – склад – станок» |
Система станочная неавтоматизированная | Система станочная с ручным управлением металлорежущим и вспомогательным оборудованием |
Система станочная автоматизированная | Система станочная, оснащенная автоматизированными подсистемами транспортно-накопительной и управления, обеспечивающими взаимосвязь станков и вспомогательного оборудования |
Система станочная автоматическая | Система станочная, состоящая из автоматических станочных модулей, оснащенная автоматическими подсистемами транспортно-накопительной и управления, обеспечивающими взаимосвязь и взаимодействие станков и вспомогательного оборудования |
Для обозначения моделей станков, выпускаемых серийно, в свое время в нашей стране была принята система, основанная на классификации, разработанной в экспериментальном научно-исследовательским институте металлорежущих станков (ЭНИМС). Согласно этой классификации, все станки в зависимости от вида технологических операций, выполняемых на них, или применяемого инструмента подразделяются на девять групп (табл.4). Каждая группа, в свою очередь, подразделяется на девять подгрупп (типов станков), характеризующих назначение станка, его компоновку, степень автоматизации работы или вид применяемого инструмента.
Обозначение модели станка состоит из сочетания трех или четырех цифр и букв. Первая цифра всегда обозначает номер группы по классификационной таблице ЭНИМС, вторая – номер подгруппы. Последние одна или две цифры характеризуют один из важнейших параметров станка. В различных группах станков одни и те же последние цифры обозначают различные наиболее характерные технологические параметры станка. Например, мод.1136 обозначает токарный одношпиндельный автомат с наибольшим диаметром обрабатываемого прутка 36 мм, мод.2135 – вертикально-сверлильный станок с наибольшим диаметром сверления 35 мм и т.д.
Буква, стоящая после первой цифры, указывает на модернизацию основной базовой модели станка. Так, токарный автомат мод.1А136 – это модернизированный станок мод.1136; ступенчатый привод шпинделя заменен в модернизированной модели бесступенчатым. Наличие буквы в конце цифровой части обозначает модификацию (видоизменение) основной базовой модели. Так, на базе универсального токарно-винторезного станка мод.1К62 выпускают его модификации: мод.1К62А – с копировальным устройством, мод.1К62Б – тот же станок, но повышенной точности, мод.1К62Т – особо высокой точности, мод.1К62ПУ – с программным управлением, мод.1К62М – с возможностью переключения скоростей и подач в процессе обработки, с автоматическим рабочим циклом и копировальным и загрузочным устройствами.
Для обозначения станков специальных и специализированных каждому заводу присвоен индекс из одной или двух букв, после которого ставится порядковый номер модели станка. Например, шифром ЕЗ-9 обозначен специализированный станок для нарезания зубчатых реек, выпускаемый Егорьевским заводом зуборезных станков.
По степени специализации станки могут быть отнесены к одной из следующих групп:
– универсальные, предназначенные для выполнения разнообразных операций на деталях широкой номенклатуры; используются главным образом в индивидуальном и мелкосерийном производствах и на ремонтных работах (станки, предназначенные для особенно большого диапазона работ, называют широкоуниверсальными);
– широкого назначения, выполняющие ограниченный круг операций на деталях широкой номенклатуры (такие станки используются чаще всего в мелкосерийном производстве);
– специализированные, предназначенные для обработки однотипных деталей различных размеров;
– специальные, на которых может обрабатываться лишь одна деталь (деталь одного типоразмера).
Специализированные и специальные станки используются в крупносерийном производстве.
По весу различают станки легкие – весом до 1 т, средние – до 10 т и тяжелые – свыше 10 т. Последние подразделяются на три подгруппы: крупные – от 10 до 30 т, собственно тяжелые – от 30 т до 100т и особо тяжелые (уникальные) – весом более 100 т.
По точности все станки подразделяются на пять классов. Класс Н – станки нормальной точности. К нему относится большинство универсальных станков. Класс П – станки повышенной степени точности, изготовляемые на базе станков нормального класса точности, но при повышенных требованиях к точности изготовления ответственных деталей станка и качеству сборки и регулировки. Класс В – станки высокой точности, достигаемой за счет специальной конструкции отдельных узлов, высоких требований к точности изготовления деталей, к качеству сборки и регулировки узлов и станка в целом. Класс А – станки особо высокой точности. При их изготовлении предъявляются еще более жесткие требования, чем при изготовлении станков класса В. Класс С – станки особо точные или мастер-станки, предназначенные для изготовления деталей, определяющих точность станков классов А и В. Для обеспечения требуемой точности работы станков классов А и С их устанавливают в специальных термоконстантных (с автоматически регулируемой постоянной температурой и влажностью) помещениях.
Таблица 4
Рис.6. Примерные области использования станочного оборудования различной
Универсальности:
1 – автоматические линии; 2 – переналаживаемые автоматические линии;
3 – гибкие станочные системы; 4 – станочные модули и станки с ЧПУ;
5 – станки с ручным управлением
Переналаживаемость определяется потерями времени и средств на переоснащение станочного оборудования при переходе от одной партии заготовок к другой.
Таким образом, переналаживаемость является показателем гибкости оборудования и зависит от количества партий деталей, обрабатываемых на данном оборудовании в течение года. При этом средний размер партии связан с характером производства и переналаживаемостью оборудования.
Для каждого вида станочного оборудования существуют вполне определенные затраты на каждую переналадку (рис.7). С увеличением числа деталей в партии общие затраты на переналадку снижаются, нопри этом увеличиваются затраты на хранение деталей, которые не сразу идут в дальнейшую работу, например, на сборку, а создают незавершенное производство.
Таким образом, для каждого вида станочного оборудования с его переналаживаемостью существует оптимальный размер партии обрабатываемых деталей. Чем меньше оптимальный размер партии, тем большей гибкостью обладает станочное оборудование. Применение средств вычислительной техники для управления станками, оснащение их манипуляторами и устройствами ЧПУ позволили существенно повысить гибкость при высокой степени автоматизации.
Рис.1.7. Оптимизация размера партии в зависимости от гибкости:
1 – затраты на незавершенную продукцию; 2 – затраты на переналадку;
3, 4 – суммарные затраты
Точность станка в основном предопределяет точность обработанных на нем изделий. По характеру и источникам возникновения все ошибки станка, влияющие на погрешности обработанной детали, условно разделяют на несколько групп:
1. Геометрическая точность зависит от ошибок соединений и влияет на точность взаимного расположения узлов станка при отсутствии внешних воздействий. Она зависит,главным образом, от точности изготовления стыковых соединений базовых деталей и от качества сборки станка.
2. Кинематическая точность необходима для станков, в которых сложные движения требуют согласования скоростей нескольких простых движений. Нарушение согласованных движений приводит к изменению заданной траектории движения инструмента относительно заготовки и искажает тем самым форму обрабатываемой поверхности. Особое значение кинематическая точность имеет для зубообрабатывающих, резьбонарезных и других станков, предназначенных для сложной контурной обработки.
Жесткость станков характеризует их свойство противостоять появлению упругих перемещений под действием постоянных или медленно изменяющихся во времени силовых воздействий. Жесткость – отношение силы к соответствующей упругой деформации в том же направлении.
.
Величину, обратную жесткости, называют податливостью. Податливость сложной системы, состоящей из набора упругих элементов, работающих последовательно, равна сумме податливостей этих элементов.
Жесткость станка, его несущей системы должна обеспечить упругое перемещение между инструментом и заготовкой в заданных пределах, зависящих от требуемой точности обработки.
На металлорежущих станках
Тела деталей машин ограничены геометрическими поверхностями, образованными при обработке. Это в основном плоскости, круговые и некруговые цилиндры и конусы, линейчатые и сферические поверхности. Все они имеют определенные протяженность и относительное положение. Реальные поверхности детали, полученные в результате обработки на станках, отличаются от идеальных геометрических поверхностей.
Поверхности обрабатываемых деталей можно рассматривать как непрерывное множество последовательных положений (следов) движущейся производящей линии, называемой образующей, по другой производящей линии, называемой направляющей. Например, для получения плоскости необходимо образующую прямую 1 перемещать по направляющей прямой 2 (рис.8, а). Цилиндрическая поверхность может быть получена при перемещении образующей прямой 1 по направляющей – окружности 3 (рис.8, б) или при движении образующей окружности 3 вдоль направляющей прямой 1 (рис.8, в). Рабочую поверхность зуба цилиндрического колеса можно получить, если образующую – эвольвенту 4 передвигать вдоль направляющей 1 (рис.8, г) или, наоборот, образующую прямую 1 передвигать по направляющей – эвольвенте 4 (рис.8, д).
Рис.8. Схемы образования поверхностей деталей
Большинство поверхностей деталей машин может быть образовано при использовании в качестве производящих линий прямой, окружности, эвольвенты, винтовой и ряда других линий. В реальных условиях обработки производящие линии воспроизводятся комбинацией согласованных между собой вращательных и прямолинейных перемещений инструмента и заготовки. Существуют четыре метода обр
|
|
Поперечные профили набережных и береговой полосы: На городских территориях берегоукрепление проектируют с учетом технических и экономических требований, но особое значение придают эстетическим...
Папиллярные узоры пальцев рук - маркер спортивных способностей: дерматоглифические признаки формируются на 3-5 месяце беременности, не изменяются в течение жизни...
Индивидуальные очистные сооружения: К классу индивидуальных очистных сооружений относят сооружения, пропускная способность которых...
Биохимия спиртового брожения: Основу технологии получения пива составляет спиртовое брожение, - при котором сахар превращается...
© cyberpedia.su 2017-2024 - Не является автором материалов. Исключительное право сохранено за автором текста.
Если вы не хотите, чтобы данный материал был у нас на сайте, перейдите по ссылке: Нарушение авторских прав. Мы поможем в написании вашей работы!