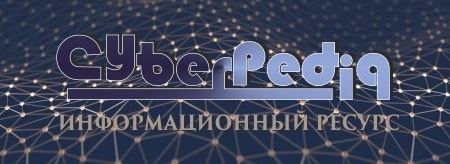
Семя – орган полового размножения и расселения растений: наружи у семян имеется плотный покров – кожура...
Кормораздатчик мобильный электрифицированный: схема и процесс работы устройства...
Топ:
Эволюция кровеносной системы позвоночных животных: Биологическая эволюция – необратимый процесс исторического развития живой природы...
Организация стока поверхностных вод: Наибольшее количество влаги на земном шаре испаряется с поверхности морей и океанов...
Характеристика АТП и сварочно-жестяницкого участка: Транспорт в настоящее время является одной из важнейших отраслей народного...
Интересное:
Уполаживание и террасирование склонов: Если глубина оврага более 5 м необходимо устройство берм. Варианты использования оврагов для градостроительных целей...
Принципы управления денежными потоками: одним из методов контроля за состоянием денежной наличности является...
Лечение прогрессирующих форм рака: Одним из наиболее важных достижений экспериментальной химиотерапии опухолей, начатой в 60-х и реализованной в 70-х годах, является...
Дисциплины:
![]() |
![]() |
5.00
из
|
Заказать работу |
|
|
Достижение заданной точности расположения обработанных на станке с ЧПУ поверхностей относительно баз заготовки, даже с допустимым отклонением +0,05 мм, связано с необходимостью точной выверки положения системы координат детали (СКД) (т. е. положения установочных элементов приспособления или баз заготовки) относительно системы координат станка (СКС). Осуществляют наладку нулевого положения. Комплекс приемов наладки учитывает способ установки заготовки для обработки, вид применяемого при наладке инструмента, конструктивные особенности станка, устройства ЧПУ (УЧПУ) и условия использования станка. Ориентацию заготовки на столе станка или в приспособлении проводят по трем плоскостям; по плоскости и двум установочным пальцам (один из которых срезанный); по цилиндрической поверхности и угловому упору.
Заготовка для обработки может непосредственно устанавливаться на стол станка (рис. 49, а), причем положение ее определяется направляющими и упорными планками. При использовании точных станков на стол станка
Рис. 49. Схемы установки заготовок для обработки на станке с ЧПУ: а — на столе станка; б - на переходной координатной плите; в — в специальном приспособлении; г — в универсальном трехкулачковом патроне; 1 — заготовка; 2 — прихваты; 3 — установочные планки; 4 — плита; 5 — приспособление |
1 3 |
~EtS----- Щ |
![]() |
J 4 |
Ф Ф -$ |
Рис. 51. Способы наладки нулевого положения: а — по боковой поверхности с помощью центра; б — по боковой поверхности с помощью контрольной оправки; в — по пальцу с помощью центро- искателя: / — заготовка; 2-центр; 3 — мерная плитка; ^ — контрольная оправка; 5 - установочный палец; 6 — центроискатель
|
устанавливают координатную плиту (рис. 49, б) или специальные призмы (рис. 50) с точными Т-образными пазами или отверстиями. Положение заготовки на плите (см. рис. 49, б) или в призме (рис. 50) определяется упорами или планками.
Применение унифицированных элементов позволяет установить для обработки одновременно несколько заготовок. Кроме унифицированных элементов используют специальные (см. рис. 49, в) и универсальные приспособления (например, трехкулачковый патрон, рис. 49,4
Наладку нулевого положения осуществляют по цилиндрической поверхности (пальцу или отверстию в плите, пальце) и по боковым поверхностям. При этом в зависимости от требуемой точности используют центр (рис. 51, я), оптическое устройство для установки по боковой поверхности (рис. 52, а), контрольную оправку (рис. 51,6 и 52,6), центроискатель (рис. 51,в и 52, в).
В комплекс приемов по наладке нулевого положения по боковым поверхностям входит: установка органов управления станком и УЧПУ в положение для осуществления наладки; установка центроискателя или контрольной оправки, оптического устройства в шпиндель станка; совмещение оси шпинделя с базой заготовки или приспособления или определение расстояния между боковой поверхностью и шпинделем или контрольной оправкой с помощью мерных плиток; набор с помощью переключателей установки нуля фактического положения исполнительных органов станка; снятие контрольных приспособлений. Наладку нулевого положения по отверстию осуществляют в такой же последовательности, только в этом случае с необходимой точностью ось шпинделя совмещают с осью отверстия.
Затраты времени на наладку нулевого по ложения учитывают в комплексе TD-31.
В качестве примера рассмотрим методику наладки пятикоординатного станка типа ОЦ с горизонтально расположенным шпинделем, оснащенного двумя поворотными столами. Проанализируем случай, когда база детали перпендикулярна установочной плоской поверхности вертикального поворотного стола (рис. 53). Заготовка установлена в приспособлении по двум пальцам и плоской поверхности. Все остальные случаи могут быть сведены к указанному с соответствующим исключением отдельных этапов наладки. Первоначально осуществляется угловая ориентация гори-
|
![]() |
зонтального поворотного стола (координата B), которую удобно проводить по одной из плоскостей приспособления (рис. 54, а). Поворотный стол устанавливают в такое положение, чтобы плоская поверхность приспособления была параллельна направлению перемещения рабочего органа вдоль оси X. Угловая
![]() |
Рис. 53. Схема расположения систем координат станка (СКС) и детали (СКД) на пятикоординатном станке типа L ОЦ |
ориентация вертикального поворотного стола (координата А) проводится по базе приспособления. Вертикальный поворотный стол устанавливают в такое положение, чтобы база приспособления была параллельна направлению перемещения рабочего органа вдоль оси
![]() |
![]() |
X (рис. 54, б). Необходимо совместить теоретическую (принятую при программировании) ось вращения приспособления и ось вращения вертикального поворотного стола. Для проверки смещения осей вращения по координате X не-
![]() |
обходимо коснуться щупом индикаторного устройства цилиндрического установочного элемента приспособления, после чего повернуть вертикальный поворотный стол на 180° и переместить рабочий орган вдоль оси X (рис. 55) на расстояние, равное удвоенному запрограммированному расстоянию от теоре-
![]() |
тической оси вращения приспособления до оси установочного элемента приспособления. Коснувшись щупом индикатора этого элемента (для чего его изготовляют сквозным), определяют смещение оси вращения приспособления относительно оси вращения вертикального поворотного стола по координате X. Для проверки смещения осей вращения по координате У необходимо коснуться щупом индикаторного устройства базы приспособления (рис. 56), повернуть вертикальный поворотный стол на 180° и переместить рабочий орган станка вдоль оси Y на расстояние, равное удвоенному запрограммированному расстоянию от оси вращения приспособления до его базы. Коснувшись щупом индикатора базы, определяют смещение оси вращения приспособления относительно оси вращения вертикального поворотного стола по координате У При наличии смещения регулируют положение приспособления на столе. После этого необходимо проверить размер, характеризующий положение оси эталонного элемента относительно оси вращения горизонтального поворотного стола. Для этой цели необходимо повернуть горизонтальный и вертикальный поворотные столы на 90° и совместить оси шпинделя и эталонного элемента с помощью индикаторного устройства. По показаниям отсчетной системы надо определить необходимый размер, а в случае необходимости отрегулировать положение приспособления.
|
Линейная ориентация приспособления по осям X, Y, Z проводится от эталонного элемента. Для определения исходного положения СКД относительно СКС по координате X с помощью индикаторного устройства определяют положение оси эталонного элемента и перемещают рабочий орган по оси X на расстояние, равное запрограммированному размеру Х0 от СКД до СКС; при этом фиксируют показания отсчетной системы.
Для определения исходного положения СКД относительно СКС по координате У используют специальный шаблон 1 (рис. 57), который устанавливают на базу приспособления 2. На шаблоне выгравирован фактический размер от его установочной плоскости до оси паза. При наладке с помощью индикаторного устройства 3 необходимо определить положение оси паза по координате У и затем переместить рабочий орган станка по оси У на расстояние, равное (у0 - /ф) мм, что соответствует расстоянию между СКД и СКС по координате У При этом необходимо зафиксировать показания отсчетной системы.
|
Q
Рис. 58. Оправка для определения исходного положения СКД по координате Z
Для определения исходного положения СКД относительно СКС по координате Z используют специальную индикаторную оправку (рис. 58). На оправку навернут съемный колпачок 1, который внутренним торцом нажимает на щуп индикатора с небольшим натягом. Перед установкой оправки в шпиндель станка на приборе для наладки инструмента измеряют его фактическую длину L, после чего колпачок свертывают с оправки. Для наладки исходного положения необходимо переместить рабочий орган станка по координате Z до соприкосновения щупа индикаторной оправки с эталонным элементом с заданным натягом. Рабочий орган станка перемещают по оси Z на расстояние (Z0 — L + 5) мм, и фиксируют показание отсчетной системы. Таким образом, как линейная, гак и угловая ориентация СКД завершена.
В процессе наладки при регулировании положения приспособления необходимо возвращаться к уже выполненным проверкам, так как при регулировании одного параметра может измениться другой. Например, после совмещения осей вращения приспособления и столов необходимо проверить угловую ориентацию приспособления и т. д. Это определяет высокую трудоемкость процесса наладки. Например, трудоемкость наладки для пя- тикоординатного станка составляет 3 — 5 ч в зависимости от способа установки детали и требований, предъявляемых к точности на ладки.
Для ГПС с несколькими налетами в памяти УЧПУ необходимо зафиксировать погрешности наладки нулевого положения всех применяемых палет.
![]() |
Кроме рассмотренных методов наладки на станках с ЧПУ начинают использовать метод наладки, используемый для координатно-изме- рительных машин. В этом случае в шпиндель станка устанавливают специальный измерительный щуп. По программе с помощью щупа определяют положение фиксированных точек на заготовке или приспособлении. ЭВМ си- схемы ЧПУ вычисляет фактическое положение заготовки или приспособления и вносит соответствующие коррективы в управляющую программу. Этот метод перспективен, так как позволяет автоматизировать процесс наладки. Кроме того, он менее трудоемок. Более подробно этот метод рассмотрен ниже.
ПОВЫШЕНИЕ ТОЧНОСТИ ОБРАБОТКИ ДЕТАЛЕЙ НА СТАНКАХ С ЧПУ И В ГИБКИХ ПРОИЗВОДСТВЕННЫХ СИСТЕМАХ
Основные требования к точности станков, применяемых в гибких производственных системах. В ГПС механической обработки деталей входят станки с ЧПУ токарной, сверлильной, расточной, фрезерной групп и станки типа «обрабатывающий центр» (сверлильно-фрезер- но-расточные и токарно-сверлильно-фрезерно- расточные станки). Все элементы технологической системы, входящие в ГПМ или ГАЗ, должны обеспечить высокое качество выпускаемых изделий при работе в автоматическом режиме с ограниченным участием обслуживающего персонала в течение 18 — 24 ч. В связи с этим к станкам, входящим в ГПС, предъявляют повышенные требования по точности. При этом необходимо учитывать возможность использования этих станков в ГПС более высокого уровня для обработки деталей с точностью выше планируемой на данном этапе.
|
Станки должны обеспечивать требуемую траекторию взаимного перемещения обрабатываемой заготовки и инструмента. Однако вследствие элементарных погрешностей реальная траектория отличается от требуемой. В некоторых случаях (при рассмотрении отклонений формы, расположения поверхностей детали) погрешности станка являются доминирующими. Необходимо уменьшить погрешности станка до величин, в 3 — 5 раз меньше по сравнению с наименьшими допустимыми погрешностями деталей, обрабатываемых на этом станке.
В общем случае при создании ГПС стре мятся полностью обрабатывать детали на одном станке (в результе чего исключаются точные станки для окончательной обработки); иметь в составе ГПС однотипное оборудование, желательно с малым разнообразием систем управления. В то же время ГПС не должна быть очень дорогой, иначе трудно обеспечить ее высокую экономическую эффектив-
![]() |
/---------- | |||
с с | З4 | ] 3 |
1» (Г^ | ] 3 |
б)
■?h | X | " ШЦ0Ш—| | ||
ъ С5 | с | X | Щг | |
! | [ | -L | 1 Ч v |
v
Рис. 59. Схемы управления приводами подач станков с ЧПУ: а — разомкнутого типа; б — замкнутого типа с круговым ИП на ходовом винте; «— с круговым ИП с реечной передачей; г — с линейным ИП
ность. Поэтому ГПС, состоящая из нескольких модулей, должна включать по экономическим соображениям различные по точности и стоимости станки.
Необходимая точность станков обусловлена совершенством их конструкции, погрешностями, возникающими при изготовлении деталей и сборке станка, и погрешностями, допустимыми при наладке и регулировании технологической системы. В наибольшей степени на точность обработки влияют погрешности станка (включая кинематическую-точность механизмов, погрешность позиционирования рабочих органов станка и т. п.). Кроме этого, важным является уменьшение чувствительности станка к внешним и внутренним воздействиям (силовым, тепловым и т. п.). По мере изнашивания начальная точность станка меняется. Поэтому следует осуществлять контроль, осмотры, проверку точности и периодическое регулирование узлов станка, обеспечивающие длительное сохранение требуемой точности.
Кинематическая точность механизмов приводов подач имеет особое значение при применении разомкнутой схемы управления приводом подач, в качестве которого применяется шаговый электродвигатель (рис. 59, а). Меньшее значение кинематическая точность имеет в приводах подач с замкнутой схемой управления (рис. 59,6 и в) при применении линейных измерительных преобразователей (ИП). В этом случае большое влияние имеет погрешность позиционирования рабочих органов станка. При применении схемы с круговыми ИП погрешности передачи винт — гайка могут различно влиять на точность обработки.
Точность позиционирования рабочих органов определяется не только точностью самого станка, но и зависит от типа системы ЧПУ (конструкции, места установки ИП, точностных параметров ИП и т. д.). Так, при применении шагового привода погрешность перемещения рабочих органов станка 1 (рис. 59, а определяется погрешностью отработки шаговым двигателем командных импульсов, погрешностями гидроусилителя, зубчатой передачи 2 и передачи винт — гайка 3, а также погрешностями рабочего органа станка.
При применении следящего привода подачи с замкнутой схемой управления наблюдается два вида погрешностей, снижающих точность перемещений рабочих органов: 1) погрешности элементов привода подачи и рабочего органа, не охватываемые системой обратной связи; 2) погрешности результатов измерения перемещения или угла поворота рабочего органа станка измерительным преобразователем. Первая группа погрешностей появляется в основном при применении систем обратной связи с круговым ИП. Преобразователе устанавливают на ходовом винте (рис. 59, б или измеряют перемещение рабочего органа через реечную передачу (рис. 59, в). В первом случае система обратной связи не учитывая погрешности передачи винт — гайка (накопленную погрешность по шагу ходового винта; зазоры в соединении винт — гайка и в опорам винта; упругие деформации ходового винта его опор и соединения винт - гайка; тепловые деформации ходового винта и др.), а также погрешности рабочего органа (отклонения oт прямолинейности и параллельности перемещений; зазоры в направляющих; упругие дефор
мации рабочего органа и др.). Во втором случае на точность измерений влияют погрешности реечной передачи (накопленная погрешность по шагу рейки, ее тепловые деформации, зазоры в зацеплении и др.).
Погрешность результатов измерения угла поворота или перемещения рабочего органа станка обусловливается погрешностью ИП, вызванной погрешностями его изготовления и установки на станке, погрешностями, которые появляются в процессе эксплуатации ИП и станка. Так, при эксплуатации линейных ИП (рис. 59, г) может изменяться зазор между его подвижными и неподвижными элементами.
В общем балансе погрешностей обработки на станках с ЧПУ значительную долю занимают погрешности, обусловленные тепловыми деформациями механизмов станка, приводящими к изменению относительного положения инструмента и заготовки в направлениях осей координат X, У, Z и угловых поворотов вокруг этих осей. Их значение и направление действия в значительной степени определяется компоновкой и конструкцией базовых деталей и механизмов станка и размещением тепловыделяющих элементов относительно базовых деталей и механизмов станка, а также зависят от качества изготовления и сборки станка и условий его эксплуатации.
Наибольшее влияние на температурные деформации оказывают собственные источники тепла станка и устройства ЧПУ, выделяющие тепло вследствие: а) превращения электрической энергии; б) превращения механической энергии (потери на трение в подшипниках шпинделя, в зубчатых и червячных передачах, в передаче винт - гайка, в фрикционных муфтах и тормозах, в направляющих, в местах уплотнения валов и др.); в) потери энергии в гидроустройствах станка.
Электрические и механические потери в станке могут достигать 50% мощности, подводимой к станку. Значительными внутренними источниками тепла в станке являются опоры шпинделя. Температурные деформации подшипников шпинделей изменяют предварительный натяг в них и могут привести к повышенному изнашиванию подшипников.
При работе станка с ЧПУ происходит неравномерный нагрев его механизмов и деталей, вызывающий изменение их размеров, формы и относительного положения в пространстве, что приводит к изменению положения оси шпинделя относительно стола и координат нулевой точки; отклонению от прямолинейности перемещения подвижных органов станка; нарушению стабильности работы систем обратной связи и др.
![]() |
![]() |
![]() |
Точность станков с ЧПУ повышается путем рациональной компоновки и конструирования основных базовых деталей и механизмов, применения в приводах подач высокомо- ментных электродвигателей постоянного тока, беззазорных механизмов и механизмов, имеющих высокий КПД, направляющих с малыми потерями на трение, стабилизации или компенсации отдельных погрешностей станка предыскажением программы управления, введением корректирующей программы в память системы ЧПУ при применении дополнительных обратных связей. На рис. 60 приведен пример повышения точности при использовании более рациональной компоновки станка.
![]() |
Применение арочной конструкции колонны, в центральном проеме которой перемещается шпиндельная бабка с горизонтальным шпинделем (рис. 61,6), предотвращает скручивание колонны силой, действующей вдоль оси шпинделя, что наблюдается при консольном расположении шпиндельной бабки (рис. 61, а). Кроме того, такая термосимметричная компоновка позволяет снизить влияние температурных деформаций колонны путем равномерного нагрева ее левой и правой сторон (рис. 61,6). При консольном расположении шпиндельной бабки неравномерные температурные деформации могут привести к значительным отклонениям оси шпинделя по координате X (см. рис. 61, а).
На схеме (см. рис. 60, а) ходовой винт привода салазок занимает центральное положение среди направляющих. Его ось находится в одной плоскости с осью шпинделя, что позволяет исключить поворот стола с деталью под действием сил резания. При другой компоновке, когда ось ходового винта стола и ось шпинделя находятся в разных плоскостях (рис. 60,6), деформации весьма большие.
Перемещения шпиндельной бабки могут быть уменьшены путем увеличения ее высоты Я (см. рис. 60, а) по сравнению с шириной В.
Жесткость станков с ЧПУ увеличивают в результате того, что основные несущие базовые детали станка с ЧПУ (колонну, станину и др.) делают литыми, а в последнее время чаще сварными, с большим числом ребер, коробчатой формы.
Жесткость и нагрузочную способность шпинделей увеличивают, создавая не только более рациональные конструкции, но и применяя в качестве опор шпинделей новые типы подшипников качения. Например, для восприятия осевых сил, действующих на шпиндель в станках с ЧПУ, применяют прецизионные двухрядные упорно-радиальные шариковые подшипники взамен упорных и ра- диально-упорных шариковых подшипников, которые обладают достаточной осевой жесткостью и имеют пониженную быстроходность, либо, наоборот, при высокой быстроходности имеют недостаточную осевую и радиальную жесткости.
Применение в приводах подач новых высокомерных малоинерционных электродвигателей постоянного тока, устанавливаемых непосредственно на ходовом винте, позволяет значительно упростить и сократить длину кинематической цепи привода подачи, увеличить ее крутильную жесткость и уменьшить число зазоров, влияющих на точность передачи движения.
Большое внимание уделяется повышению осевой жесткости передачи винт — гайка и опор ходового винта. В качестве опор ходового винта применяют роликовые упорные и комбинированные подшипники вместо ранее применяемых шариковых упорных подшипников, что позволяет значительно увеличить их осевую жесткость.
Для повышения жесткости рабочих органов станка с ЧПУ в рабочем состоянии их зажимают после позиционирования в заданную позицию (рис. 62).
На рис. 63 приведены схемы устранения упругих деформаций в тяжелых станках с ЧПУ. В первом случае (рис. 63, а) с помощью гидроцилиндра с поршнем 3 и тяги 4 устраняются упругие деформации опор шпиндельной бабки 1 при выдвижении вперед ползуна со шпинделем 2. Во втором случае (рис. 63,6) также с помощью гидроцилиндра с поршнем 3 и тяги 2 устраняются упругие деформации консольной части ползуна 1.
1 2
![]() |
Точность передачи движений достигается сокращением длины кинематической цепи привода подачи и более точным изготовлением ее элементов, применением беззазорных зубчатых передач и редукторов, беззазорных шариковых винтовых пар. В последнем случае обеспечивается также динамическая устойчивость следящего привода подачи станка, его надежная и стабильная работа.
Принцип построения большинства беззазорных зубчатых и червячных редукторов (или отдельных передач) заключается в том, что редуктор (передача) составляют из двух кинематически идентичных цепей, образующих замкнутый кинематический контур (рис. 64). В единичной зубчатой или червячной передаче одно зубчатое (червячное) колесо делают разрезным. Зазор устраняется взаимным разворотом половинок пружинами (рис. 64, а) или последующим жестким закреплением половинок болтами. Устранение зазоров и создание предварительного натяга в редукторе достигается взаимным разворотом его кинематических цепей специальным нагружающим устройством. В результате в каждой кинематической цепи получается однопрофильное зацепление, которое не нарушается и при реверсе движения (рис. 64. б). Нагрузка замкнутого контура часто осуществляется осевым смещением вала с ко- созубыми колесами пружиной или поршнем гидроцилиндра.
В шариковых винтовых парах (ШВП) (рис. 65) в отличие от обычных винтовых пар с тре- нИем скольжения коэффициент трения почти не зависит от скорости перемещения. Поэтому их применение обеспечивает снижение пускового момента, легкость хода и высокую плавность движения на малых скоростях. Малые потери на трение уменьшают износ деталей ШВП, а закалка рабочих поверхностей гайки,
![]() |
![]() |
S)
Рис. 64. Схемы беззазорных зубчатых передач:
а — цилиндрическая передача с пружинами растяжения; 6 — зубчатый редуктор
ходового винта и шариков до твердости HRC 58 — 60 с последующим шлифованием обеспечивает повышенную долговечность этих передач. Малые потери на трение позволили создать беззазорные ШВП с двумя полугайками, собранными с предварительным натягом, что устраняет зазоры в передаче, увеличивает жесткость и тем самым значительно повышает точность передаваемого движения при наличии реверсирования. На фланцах полугаек нарезаны зубья zt и z2, причем z2 + 1 =zt. При выводе полугаек 1 и 3 из зацепления с корпусом 2 и повороте каждой полугайки в одну сторону на один зуб происходит условное минимальное относительное смещение полугаек
( 1 1 \
на величину Дос =-------------- Рх в. При регули-
VZ2 /
ровании натяга необходимо учитывать, что его чрезмерная величина снижает долговечность ШВП, а малый натяг снижает жесткость ШВП.
Уменьшения вибрации на станках с ЧПУ достигают повышением жесткости, применением различных демпфирующих средств, снижением уровня возмущающих воздействий
![]() |
Рис. 65. Конструкция беззазорной шариковой винтовой пары |
1 2 |
![]() |
«3
£ £? * ^ ^
is
Ю
Рис. 66. Система охлаждения узла шпинделя (а) и схема ее управления (б)
динамической балансировкой быстровращаю- щихся частей, применением электродвигателей с малой амплитудой колебаний или вынесением их за пределы несущей системы станка, стабилизацией силы резания и др.
Точность перемещения и стабильность положения рабочих органов повышаются снижением сил трения в направляющих, устранением в них зазоров и увеличением их жесткости. Уменьшение сил трения в направляющих достигается применением специальных синтетических материалов, антифрикционных металлов, сплавов и мастик.
Задатчик температуры |
Указатель отклонения |
I i* Is г |
В * i! |
Сз ^ * £ Ч |
Коэффициент трения покоя в чугунных направляющих смешанного трения в случае, когда не принято специальных мер для снижения трения, составляет в среднем 0,25. Применение специальных антискачковых масел позволяет снизить коэффициент трения покоя в чугунных направляющих до 0,075-0,09. Коэффициент трения покоя направляющих, армированных специальными антискачковыми пластмассами на основе фторопласта, составляет 0,04 - 0,06, у направляющих качения - 0,002-0,003, а у гидростатических и аэростатических направляющих он еще меньше.
Влияние температурных деформаций на точность станков с ЧПУ снижается путем их компенсации (предварительным нагревом до стабилизации теплового поля и температурных деформаций); уменьшением количества тепла, выделяющегося при работе станка; снижением чувствительности станка к изменению температуры деталей и узлов станка.
Количество тепла, выделяемое в станке, можно уменьшить двумя путями: 1) выносом тепловыделяющих механизмов (насосных установок, приводных двигателей, масляных баков, гидроаппаратуры и др.) из станины или других базовых деталей станка; 2) использованием конструкций с небольшим тепловыделением, что достигается применением шпиндельных подшипников с меньшим тепловыделением, использованием соответствующего смазочного материала, сокращением длины кинематических цепей. Зубчатые и клино- ременные передачи рекомендуется размещать так, чтобы потоки воздуха уносили часть выделяемого тепла.
Уменьшение «чувствительности» станка к изменению его тепловых полей достигается изготовлением деталей станка из материалов с малым коэффициентом линейного расширения, теплоизоляцией источников тепла, созданием термосимметричной конструкции станка и его механизмов. Влияние температурных деформаций может быть уменьшено соответствующим взаимным расположением фиксирующих элементов, например упорных подшипников в шпинделе (в передней или задней опоре), места крепления шпиндельной бабки на станине и др.
Эффективным методом снижения температурных деформаций является охлаждение станка, включая его активные элементы (подшипники шпинделя, муфты, тормоза, электродвигатели и др.), и пассивные элементы, переносящие тепло (масла и охлаждающие жидкости), путем создания естественного или искусственного потока воздуха, отвода тепла с помощью охлаждающих устройств и др.
На рис. 66, а показана система охлаждения узла шпинделя 1 станка с ЧПУ путем принудительной прокачки охлаждаемого в резервуаре 2 масла. В случае превышения заданной температуры масла от термопары поступает команда на включение системы охлаждения масла в резервуаре 2.
Кроме рассмотренных методов снижения погрешностей механизмов станка с ЧПУ, для повышения точности его работы широко применяют методы, основанные на измерении по-
грешностей и их компенсации или стабилизации.
Первый метод заключается в компенсации систематической составляющей погрешностей на основе информации, полученной аналитическими расчетами или экспериментальными исследованиями. Управляющая программа пред- искажается на этапе программирования или в процессе эксплуатации при редактировании программы вводом коррекций с пульта устройства ЧПУ
Применение микропроцессоров и ми- кроЭВМ в системах ЧПУ станка позволило реализовать функции управления приводами подач станка программными средствами, компенсировать погрешности станка путем использования постоянно действующих программ коррекции, заложенных в памяти системы управления (рис. 67). Система компенсирует упругие деформации, вызываемые не только силами резания, но и массами траверсы и шпиндельной головки. Система содержит блоки i, закрепленные на колонне и основании, трос 2 и устройство управления 3. Компенсирующее входное воздействие Ер задается от устройства ЧПУ станка. Оно вычисляет это воздействие в зависимости от положения рабочих органов по координатам X, W, Z и действующих сил резания. Получая сигнал о величине компенсации, устройство компенсации формирует на выходе соответствующее механическое воздействие (силу или момент) на упругую систему станка.
При компенсации температурных деформаций на основе применения специальных обратных связей в качестве контролируемых параметров можно использовать: частоту вращения шпинделя; темп генерирования тепла в станке; изменение температурных характерных точек станка; смещение шпинделя станка; погрешность обработки детали.
Наиболее удобным является способ измерения температуры характерных точек станка. В этом случае достигается полное соответствие измеренной температуры и смещения шпинделя станка. Эти точки определяют путем анализа температурных полей станка, измеренных при различных режимах его работы. Термопары, установленные в характерных точках, посылают сигналы через устройство компенсации (рис. 68) в сравнивающее устройство для коррекции перемещения рабочего стола станка.
гт | fn | |
а |
/2 |
и |
хт |
![]() |
![]() |
а) |
Л, мкм
![]() |
На рис. 69, а показано устройство компенсации температурных деформаций шпиндельной бабки станка с ЧПУ, а на рис. 69, б - гра-
Рис. 67. Схема компенсации упругих деформаций тяжелого фрезерного станка с ЧПУ
![]() |
фики смещения шпинделя этого станка по координате У без устройства компенсации (кривая 1) и с устройством (кривая 2) при частоте вращения шпинделя 2780 об/мин.
Примерно на уровне оси шпинделя в кронштейне 1 (рис. 69, а) шпиндельной бабки закреплен инваровый стержень 2, упирающийся в рычаг 3, поджимаемый к стержню 2 пружиной через струну 4, накрученную на вал датчика 5. При работе станка и смещении передней части шпиндельной бабки со шпинделем вправо при нагреве инваровый стержень (имеющий очень малый коэффициент линейного расширения) смещается также вправо, рычаг 3 отклоняется, и датчик 5 выдает в систему управления сигнал для коррекции управляющей программы.
Описанные методы компенсации позволяют
Состав сооружений: решетки и песколовки: Решетки – это первое устройство в схеме очистных сооружений. Они представляют...
Адаптации растений и животных к жизни в горах: Большое значение для жизни организмов в горах имеют степень расчленения, крутизна и экспозиционные различия склонов...
Наброски и зарисовки растений, плодов, цветов: Освоить конструктивное построение структуры дерева через зарисовки отдельных деревьев, группы деревьев...
Археология об основании Рима: Новые раскопки проясняют и такой острый дискуссионный вопрос, как дата самого возникновения Рима...
© cyberpedia.su 2017-2024 - Не является автором материалов. Исключительное право сохранено за автором текста.
Если вы не хотите, чтобы данный материал был у нас на сайте, перейдите по ссылке: Нарушение авторских прав. Мы поможем в написании вашей работы!