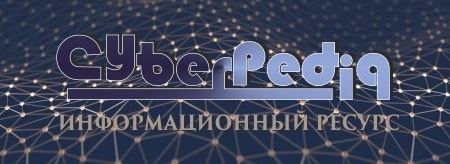
Архитектура электронного правительства: Единая архитектура – это методологический подход при создании системы управления государства, который строится...
Биохимия спиртового брожения: Основу технологии получения пива составляет спиртовое брожение, - при котором сахар превращается...
Топ:
История развития методов оптимизации: теорема Куна-Таккера, метод Лагранжа, роль выпуклости в оптимизации...
Когда производится ограждение поезда, остановившегося на перегоне: Во всех случаях немедленно должно быть ограждено место препятствия для движения поездов на смежном пути двухпутного...
Установка замедленного коксования: Чем выше температура и ниже давление, тем место разрыва углеродной цепи всё больше смещается к её концу и значительно возрастает...
Интересное:
Влияние предпринимательской среды на эффективное функционирование предприятия: Предпринимательская среда – это совокупность внешних и внутренних факторов, оказывающих влияние на функционирование фирмы...
Берегоукрепление оползневых склонов: На прибрежных склонах основной причиной развития оползневых процессов является подмыв водами рек естественных склонов...
Мероприятия для защиты от морозного пучения грунтов: Инженерная защита от морозного (криогенного) пучения грунтов необходима для легких малоэтажных зданий и других сооружений...
Дисциплины:
![]() |
![]() |
5.00
из
|
Заказать работу |
|
|
![]() |
радиальная сила частично уравновешена, что обеспечивает большую точность.
При обработке точных отверстий применяют оправки с регулированием положения резца (рис. 40). Они позволяют также отвести резец от обрабатываемой поверхности при выводе оправки из отверстия.
Особенно эффективно применять комбинированные (ступенчатые) сверла (рис. 41) для одновременного сверления и снятия фаски в отверстии под резьбу (рис. 42,а); обработки ступенчатых отверстий с конической зенковкой под винты с потайной и полупотайной головками (рис. 42,6) и с цилиндрической зенковкой под винты с цилиндрической головкой. Выпускают сверла под нарезание резьбы Мб, М8, М10, М12, М14, М16.
Сверла выпускают для станков с ЧПУ двух классов точности: А (повышенной) и В (нормальной). Обработка указанных отверстий обеспечивает позиционное отклонение не более +/- (0,1-0,2) мм.
При обработке деталей из чугуна и конструкционных сталей средней прочности увеличение диаметра отверстия при сверлении сверлами с меньшим диаметром ступени составляет 0,1-0,15 мм, а при сверлении сверлами с большим диаметром ступени - 0,04-0,1 мм. Точность обрабатываемого отверстия соответствует 10-12-му квалитету. Параметр шероховатости поверхности Ra = 1,25 мкм. Стойкость сверл без покрытия 20 — 40 мин при диаметре меньшей ступени 5 — 18 мм (работа
![]() |
![]() |
по стали) и 50-70 мин (по чугуну). Стойкость сверл с покрытием выше при работе по стали в 2 раза, по чугуну - в 1,5-2 раза.
Широкое применение на станках типа ОЦ начинают находить различные головки для обработки группы отверстий, плоских поверхностей, расположенных под углом, и т. д. На рис. 43 показан цикл работы специальной головки для подрезания торца с обратной стороны отверстия.
|
ТОЧНОСТЬ ОБРАБОТКИ ДЕТАЛЕЙ НА СТАНКАХ С ЧПУ И В ГИБКИХ ПРОИЗВОДСТВЕННЫХ СИСТЕМАХ
Основные положения
Рис. 42. Отверстия под нарезание резьбы и головки винтов, обрабатываемые ступенчатыми сверлами |
N | |||
К | |||
Общая методика анализа точности обработки детали приведена в т. 1, гл. 1 справочника. В отличие от обработки на универсальных
станках с ручным управлением при обработке на станках с ЧПУ и в ГПС процессы обработки происходят в более сложной технологической системе. ГПС механической обработки включает взаимосвязанные и функционирующие как единое целое оборудование, технологическую оснастку (режущий инструмент, приспособления, контрольно-измерительные приборы, диагностическое оборудование), заготовку и процесс резания. По сложности даже ГПМ в несколько раз превышает обычное оборудование. Точность и надежность функционирования каждого элемента ГПС должны быть повышенными. Поэтому задача обеспечения заданной точности обрабатываемых деталей в этом случае решается как обычными методами, так и с помощью специальных контрольных и диагностических систем. На свер- лильно-фрезерно-расточных, токарно-фрезер- ных станках типа «обрабатывающий центр» и других станках с ЧПУ концентрация переходов обработки и режимы обработки существенно выше.
В этих условиях на результаты обработки влияют не только финишные, но и все предшествующие переходы изготовления заготовки и детали. Увеличивается внимание к явлениям преемственности свойств, т. е. наследованию, копированию свойств и погрешностей.
При изготовлении деталей в соответствии с принятым технологическим процессом осуществляется ряд последовательных преобразований свойств и параметров качества заготовки (физико-механических свойств, геометрических параметров формы). Выявление физической сущности процессов преобразования свойств, технологических связей между этапами этого преобразования позволяет разработать модели технологического перехода, операции, процесса. Зная модели процессов, можно оптимизировать условия обработки деталей, решить проблему интенсификации машиностроительного производства.
|
При механической обработке преемственность свойств непрерывна. Поэтому уровень выходных параметров f(t), например отклонений размеров, формы и расположения в произвольный период времени t выполнения технологического перехода, определяется всей предысторией изменений воздействий X (т), физико-механических свойств заготовки $(т), параметров геометрической формы, расположения поверхностей и размеров заготовки й (т), а также режима обработки Л (т), параметров технологической системы £(т) и других неучтенных факторов Й(х):
<J(t); Л(х); 0(т); Я(т)].
Символ функционала F'0 означает задание способа определения f(t) при известных значениях указанных выше параметров (факторов). Таким образом, образование поверхностей при механической обработке деталей на станках с ЧПУ, в том числе включенных в ГПС, следует рассматривать как случайный процесс, учитывающий все изменения в объекте производства и в технологической системе за весь период те (0,f), причем необходимо учитывать изменения не только за период обработки, но и за весь период нахождения детали в производстве (при транспортировании, на складе и т. п.).
Точность обработки в ГПС зависит от большого числа факторов, степень воздействия которых на выходные параметры качества неодинакова. При анализе конкретного процесса действием ряда факторов и некоторыми связями можно пренебречь без существенного изменения физической модели процесса.
Все процессы формообразования при механической обработке можно условно разделить на две группы. К первой группе следует отнести процессы обработки, характеризующиеся тем, что положение формообразующего элемента режущей кромки инструмента во время этих процессов, а следовательно, траектория ее и точность обработки зависят не только от силовых, но и от кинематических воздействий. Например, люнет и направляющие инструментов для обработки глубоких отверстий при работе находятся в контакте с ранее обработанным участком поверхности; поэтому все погрешности формы и расположения этого участка отражаются на положении режущей кромки и, следовательно, на точности обработки. В общем случае при точении, растачивании и выполнении других переходов обработки, относящихся к первой группе, смещение реальной траектории режущей кромки относительно номинальной определяется соотношением
|
j
где Uj — элементарное несиловое воздействие, например смещение или поворот элемента, вызванное геометрическими погрешностями станка; Pq — элементарное силовое воздействие, зависящее (сила резания) или независящее (сила закрепления) от параметров режима резания; А — оператор системы, обозначающий задание способа, с помощью которого при известных воздействиях определяется составляющая смещения Аг£.
Процессы обработки второй группы характеризуются тем, что во время этих процессов не наблюдается взаимосвязи между результатами обработки поверхности в рассматриваемый и предшествующий моменты времени обработки одной поверхности. Примером процессов второй группы является растачивание отверстий, точение наружных поверхностей без применения люнетов или направляющих, которые контактируют с обработанной ранее (при выполнении этого или предшествующего перехода) поверхностью детали. В этом случае при анализе точности на рассматриваемом переходе обработки кинематические воздействия не учитываются, что упрощает расчеты точности обработки.
Формулы для расчета суммарной погрешности размера с учетом элементарных факторов, определяющих точность обработки, приведены в т. 1 гл. 1.
Рассмотрим методику определения суммарного отклонения формы и расположения обработанной поверхности. Будем считать, что образующееся в результате обработки суммарное отклонение расположения (формы) поверхностей является результатом двух первичных отклонений:
ух = Д! = ск1 cos (/сср + \|гк1) и у2 = &2= ск 2 cos (/с\|/ 4- \|/к2),
|
где Aj - собственная погрешность данного перехода обработки; А2 — погрешность, полученная в результате преобразований технологической системой на данном переходе обработки исходного отклонения предшествующего перехода обработки; Д2 = Л (А2(1_ 1}) (здесь А — оператор преобразований исходного отклонения; А 2 (._1} — исходное отклонение); с — амплитуды отклонений; \|/ — фазы отклонений; к — номер гармоники (отклонения); при к = 1 рассматривается отклонение расположения поверхностей; при к = 2, к = = 3,... — элементарные отклонения формы: овальность (к = 2), трехгранная форма (к = 3) и т. д.
В наиболее простом случае, когда рассматривается суммирование двух элементарных отклонений с равными значениями /с, суммарное отклонение
У = Уг + У г = ci cos Ф + с2 cos (ф + Ф) = = ccos(cp -I- Р).
Здесь с = | /(сt + с 2 cos i|/)2 + (с2 sin \|/)2; sin (3 =
с2 1
= —sin \|/; cos Р =—+ с2 cos \|/); р =
с с
с2 sin y\f
= arctg-----------------, где сир — соответствен-
сх + c2cosv|/
но амплитуда и начальная фаза результирующего воздействия.
Если два отклонения являются случайными векторами, то результирующее отклонение
У = I Ух + У2 I = ]/у\ + У\ +2У1У2 cosY>
или
4 = Cfci + cl 2 + 2cklck2cos у,
где у — угол между векторами ух и у2.
В случае, когда 0 ^ у ^ 2л, причем все значения р в этом диапазоне равновероятны, M[cosy]=0; примем, что корреляционный момент также равен нулю; тогда для математических ожиданий амплитуд отклонений
ми-ми + ми,
где М — математическое ожидание соответствующей величины.
В ряде случаев можно принять, что случайные величины — амплитуды отклонений расположения и формы поверхностей подчинены закону однопараметрического распределения Релея, в котором математические ожидания и дисперсии взаимосвязаны. Тогда можно написать
t>[ck]=D[ckl]+Dlck2l
где D — дисперсия соответствующих величин.
Таким образом, при анализе точности по параметрам отклонения формы и расположения следует учитывать, что отклонения являются векторами, и, в общем случае, суммирование их более сложно, чем суммирование элементарных погрешностей размеров.
Часто можно перейти к более простому определению суммарной погрешности размера, формы и расположения поверхности, учитывая критерий ничтожности. Согласно этому критерию при определении суммарной дисперсии пренебрегают слагаемым (или суммой слагаемых), которое на порядок меньше наибольшей дисперсии. Таким образом, если ^ За2, то принимают ст «с^ (а — среднее квадратическое отклонение суммарной по- 1
грешности); при — а1<а2<3а1 расчет суммарной погрешности ведут с учетом двух элементарных погрешностей; при За! ^ а2 принимают g ~ о2. Пренебрежение в указанных случаях меньшим о1 (или а2) приведет к появлению относительной погрешности в определении а, не превышающей 5,5 %, что при вероятностных расчетах вполне допустимо.
|
Пусть Зст1 ^ ст2; тогда между дисперсиями, средними квадратическими отклонениями, средними арифметическими отклонениями амплитуды погрешностей расположения и формы поверхности справедливо равенство
D [с] «D [с2]; о [с] = а [с2] \ с — с2
или D [с] = AdD I ~с2 (i - 1)]; с = Асс2а- 1>,_ где A d, Ас — операторы преобразований; с и с2и--и — средние значения суммарного и исходного отклонений.
В общем случае при обработке может изменяться не только значение отклонения (амплитуды), но и направление (начальная фаза). Если не учитывать инерционность воздействий, то
2 С Скб а
Ad — /суТ; Ас -- куТ = — — —,
С2(/-1) Снб(г-1) 1
где /сух - коэффициент уточнения; снб — наибольшее значение амплитуды рассматриваемого отклонения расположения или формы.
Следует еще раз подчеркнуть, что полученные простые соотношения и возможность применения коэффициента уточнения существуют лишь тогда, когда учитывается только одно доминирующее отклонение, например отклонение, связанное с погрешностью предшествующего перехода обработки.
Анализ соотношения c = kyTc2(i_1) показывает, что возможны три пути повышения точности обработки: 1) снижением чувствительности системы к входным воздействиям, т. е. путем уменьшения коэффициента уточнения; 2) уменьшением уровня входных воздействий, т. е. путем повышения точности обработки на предшествующем переходе; 3) применением систем с обратной связью — управляющее воздействие компенсирует смещение формообразующей вершины инструмента вследствие силовых и кинематических воздействий. Первый путь повышения точности обработки может быть реализован подбором оптимального режима обработки.
|
|
Эмиссия газов от очистных сооружений канализации: В последние годы внимание мирового сообщества сосредоточено на экологических проблемах...
Своеобразие русской архитектуры: Основной материал – дерево – быстрота постройки, но недолговечность и необходимость деления...
Особенности сооружения опор в сложных условиях: Сооружение ВЛ в районах с суровыми климатическими и тяжелыми геологическими условиями...
Археология об основании Рима: Новые раскопки проясняют и такой острый дискуссионный вопрос, как дата самого возникновения Рима...
© cyberpedia.su 2017-2024 - Не является автором материалов. Исключительное право сохранено за автором текста.
Если вы не хотите, чтобы данный материал был у нас на сайте, перейдите по ссылке: Нарушение авторских прав. Мы поможем в написании вашей работы!