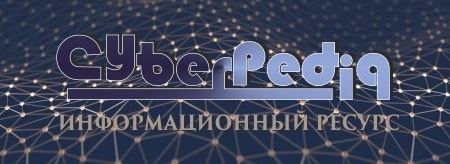
Археология об основании Рима: Новые раскопки проясняют и такой острый дискуссионный вопрос, как дата самого возникновения Рима...
Поперечные профили набережных и береговой полосы: На городских территориях берегоукрепление проектируют с учетом технических и экономических требований, но особое значение придают эстетическим...
Топ:
Эволюция кровеносной системы позвоночных животных: Биологическая эволюция – необратимый процесс исторического развития живой природы...
Особенности труда и отдыха в условиях низких температур: К работам при низких температурах на открытом воздухе и в не отапливаемых помещениях допускаются лица не моложе 18 лет, прошедшие...
Интересное:
Национальное богатство страны и его составляющие: для оценки элементов национального богатства используются...
Что нужно делать при лейкемии: Прежде всего, необходимо выяснить, не страдаете ли вы каким-либо душевным недугом...
Отражение на счетах бухгалтерского учета процесса приобретения: Процесс заготовления представляет систему экономических событий, включающих приобретение организацией у поставщиков сырья...
Дисциплины:
![]() |
![]() |
5.00
из
|
Заказать работу |
Содержание книги
Поиск на нашем сайте
|
|
5.7.1 Основные характеристики гибких производственных систем
Наивысшим уровнем автоматизации производства в настоящее время считаются гибкие производственные системы (ГПС).
Гибкая производственная система – это совокупность в разных сочетаниях оборудования с ЧПУ, роботизированных технологических комплексов, гибких производственных модулей, отдельных единиц технологического оборудования и систем обеспечения их функционирования в автоматическом режиме в течение заданного интервала времени, обладающая свойством автоматизированной переналадки.
Гибкий производственный модуль (ГПМ) – это единица технологического оборудования, оснащенная автоматизированным устройством программного управления и средствами автоматизации технологического процесса, среди которых может быть и промышленный робот. ГПМ – это автономно функционирующая система, осуществляющая многократные циклы и имеющая возможность встраивания в систему более высокого порядка.
Роботизированный технологический комплекс (РТК) – это совокупность единицы технологического оборудования с ЧПУ, промышленного робота и систем обеспечения, позволяющих комплексу автономно функционировать и осуществлять многократные рабочие циклы, и имеющая возможность встраиваться в систему более высокого порядка.
Создание ГПС по своим результатам сопоставимо с результатами изменений в организации промышленного производства, совершенных одним из «классиков менеджмента» Генри Фордом. В начале ХХ века Г. Форд революционизировал организацию промышленного производства, внедрив конвейерную технологию, согласно которой основные операции совершаются в определенной последовательности их этапов с использованием оборудования, специально предназначенного для одного стандартизированного продукта в исключительно больших количествах и в течение продолжительного времени. Хотя с окончанием производства модели «Т» заводы Форда из-за высокой специализации пришлось перепроектировать, тем не менее «конвейерный» или поточно-массовый подход оказал влияние не на одно поколение промышленников и изменил лицо индустриального производства.
|
До появления ГПС автоматизация производственных процессов шла в основном в массовом производстве на основе создания жестких автоматических линий, предназначенных для изготовления одной детали или одного узла. При этом значительно повышается производительность труда, но не обеспечивается высокая мобильность или гибкость производства, т.е. возможность в кратчайшие сроки переходить на выпуск новой продукции.
ГПС обеспечивает также значительное повышение производительности труда в сравнении с единичным производством, причем это повышение достигается за счет снижения времени на переналадку и повышение коэффициента использования основного оборудования, увеличение фонда времени его работы, сокращение численности работающих. И в то же время ГПС обеспечивает гибкость производства, т.е. обеспечивает возможность приспосабливать производство к изменениям производственных условий.
Так, в 1988 году инженеры «Дженерал моторс» впервые в истории компании смогли использовать свои обычные производственные мощности для создания образцов моделей машин будущего года. Инженеры переналадили оборудование для производства моделей 1989 года во второй половине дня в одну из пятниц, после того, как с завода ушли рабочие. Они использовали оборудование в течение уик-энда, а затем переналадили его на выпуск машин моделей 1988 года, чтобы утром в понедельник обычное производство могло быть продолжено.
Следует заметить, что при использовании старого, менее гибкого оборудования, типичного ранее для обрабатывающей промышленности, переналадка оборудования для выпуска моделей будущего года требовала остановки производства на несколько недель.
|
Использование ГПС позволяет предприятию (фирме) эффективно вести производство разнообразной продукции очень маленькими партиями, особенно по сравнению с нормами, привычными для массового производства. Наиболее эффективной областью применения ГПС является многономенклатурное производство с размерами партии деталей от 30 до 2000 штук и числом типов деталей от 4 до 300.
ГПС в своем развитии прошли несколько этапов, которые определяются моментами появления отдельных компонентов, составляющих систему в целом (оборудование, микропроцессорная техника).
Первым этапом в развитии ГПС явилось появление станков с ЧПУ (1955 г.). Однако из-за несовершенства систем программирования и управления станками первое поколение станков с ЧПУ не нашло широкого применения.
Второй этап в развитии ГПС связан с появлением промышленных роботов (1962 г.).
Третий этап развития ГПС связан с появлением еще одного компонента гибкой автоматизации – микропроцессоров (универсальных и гибких средств обработки информации), которые резко снизили стоимость станков с ЧПУ и повысили надежность оборудования.
Четвертый этап развития ГПС – объединение технологического оборудования с ЧПУ, микропроцессоров и промышленных роботов в единую систему.
С появлением ГПС значительно изменились функции станочников. Так из всех функций станочника, таких как - установка и снятие детали; подбор, установка и замена инструмента; смена приспособления; контроль и измерение детали; включение и выключение станка – осталась одна функция: общее наблюдение за работой оборудования.
5.7.2 Структура и классификация ГПС
При формировании (при построении) ГПС используется модульный принцип. Различают два основных вида модулей: аппаратные (технологическое, транспортное оборудование и т.п.), из которых формируется техническая часть ЧПС и программное обеспечение систем управления ГПС. Именно модульность построения позволяет формировать состав технических и программных средств в соответствии с потребностями производства и представляет большие возможности для расширения состава технических средств.
|
В общем случае ГПС включает в себя две функциональные компоненты: технологическое оборудование обработки (ТО); систему обеспечения функционирования ГПС (рис.15).
К технологическому оборудованию относятся: основное технологическое оборудование (станки с ЧПУ, станки типа обрабатывающих центров), ПР и автооператоры, оснастка (накопители, спутники), устройства управления, инструмент, устройства смены и контроль качества инструмента, устройство удаления отходов, устройство автоматического контроля качества выполняемых операций, устройство технической диагностики, устройства транспортирования и складирования.
К системам обеспечения функционирования ГПС относятся:
АТСС (автоматизированная транспортно-складская система), состоящая из взаимосвязанных автоматизированных транспортных и складских устройств для укладки, хранения, временного накопления, разгрузки и доставки предметов труда, технической оснастки:
АСИО (автоматизированная система инструментального обеспечения), состоящая из накопителей, устройств смены и контроля качества инструмента, обеспечивающих хранение, автоматическую установку и замену инструмента;
САК (система автоматизированного контроля качества выполняемых операций) включая в себя различного рода датчики и устройства для автоматиче ского контроля качества выполняемых операций;
АСУО (автоматизированная система удаления отходов) включающая в себя комплекс устройств для накопления, доставки и разгрузки отходов.
![]() |
Составные части ГПС Система обеспечения функционирования ГПС
ГПМ Основное технологическое оборудование РТК Автоматизированное транспортно-складская система
![]() | ![]() | ||
ПР и автооператоры Автоматизированная система инструментального
обеспечения
Оснастка (накопители, спутники, …) Система автоматизированного контроля качества операций
Устройства управления Автоматизированная система удаления отходов
Инструмент Автоматизированная система научных исследований
|
Устройство удаления отходов Система автоматизированного проектирования
![]() |
Устройство автоматического контроля качества Автоматизированная система технологической
подготовки производства
Устройство технической диагностики Автоматизированная система управления
Рис. 15 Структура ГПС
АСНИ (автоматизированная система научных исследований) позволяет проводить автоматизированную разработку научно-исследовательской тематики, в первую очередь, поисковой и прикладной, которая дает возможность получать выходной материал в формализованном виде, пригодном для дальнейшего использования на последующих автоматизированных стадиях гибкого автоматизированного производства;
САПР (система автоматизированного проектирования) позволяет выполнять трудоемкую работу конструирования изделий с использованием ЭВМ и выдавать в необходимой форме исходную информацию для следующей стадии;
АСТПП (автоматизированная система технологической подготовки производства) решает вопросы автоматизации проектирования технологических процессов обработки деталей, инструмента приспособлений, управляющих программ, а также их изготовление, накладки и контроля;
АСУ (автоматизированная система управления) в условиях функционирования ГПС решает вопросы планирования сменно-суточных зданий, их МТО (постановка заготовок, инструмента оснастки), выполнения операций вне ГПС.
Результаты, формируемые системами САПР, АСТПП и АСУ представляют собой программы производства, расчлененные до уровня технологических операций и очередности запуска партий детальной обработки, а также программы управляемые оборудованием. Используемые в САПР и АСТПП вычислительные комплексы способны передавать данные о конструкции и технологии изделий непосредственно в ЭВМ управляющие оборудованием. Таким образом разработка конструкции, технологии и управление технологическими процессами производства от начала до конца осуществляются с помощью ЭВМ на основе общего банка данных.
ГПС различают по многим классификационным признакам. Так по организационному признаку выделяют гибкую автоматизированную линию (ГАЛ), гибкий автоматизированный участок (ГАУ) и гибкий автоматизированный цех (ГАЦ).
ГАЛ состоит из нескольких ГПМ, объединенных автоматизированной СУ. Технологическое оборудование ГАЛ расположено в последовательности выполняемых над изделием технологических операций.
ГАУ - это ГПС функционирующая по технологическому маршруту, в котором предусмотрена возможность изменения последовательности использования технологического оборудования при смене изделия. Состоит также из нескольких ГПМ, объединенных автоматизированной СУ.
|
ГАЦ - это ГПС представляющая собой совокупность различных сочетаний ГАЛ и (или) ГАУ.
По уровню автоматизации выделяют:
· первый - автоматизированная переналадка при переходе на изготовление освоенных изделий;
· второй - автоматическая переналадка при переходе на изготовление освоенных изделий;
· третий - автоматизированная переналадка при переходе на изготовление новых изделий.
По виду обработки (литье, сварка, обработка, резанье и т.п.).
По разновидности обрабатываемых деталей (корпусные, плоскостные, детали тел вращения).
5.7.3 Факторы повышения эффективности производства и
проблемы создания ГПС
Среди факторов повышения эффективности производства при создании и внедрении ГПС можно отметить следующие:
1. Повышение производительности труда за счет замены ручного и машинно-ручного труда автоматизированным на основных и вспомогательных операциях;
2. Сокращение потерь рабочего времени основных и вспомогательных рабочих (АСД, АТСС, АСУ)
3. Уменьшение количества требуемого оборудования, а значит и производственных площадей;
4. Уменьшение потребности в станочниках и обслуживающем персонале (особенно во вторую и третью смены);
5. Уменьшение времени переналадки производственного процесса при переходе на изготовление другой продукции;
6. Сокращение длительности производственного цикла, а следовательно незавершенного производства и оборотных средств в незавершенном производстве;
7. Уменьшение потерь от брака за счет повышения стабильности технологических процессов (САК, АСД);
8. Снижение себестоимости продукции;
9. Повышение производительности труда за счет более полного использования технических возможностей оборудования, увеличения коэффициента машинного времени (коэффициента использования оборудования);
10. Увеличение сменности работы оборудования.
Последние два фактора являются преобладающими.
Покажем на примере замены автономного станка с ЧПУ гибким производственным модулем возможность многократного роста агрегатной производительности станка.
При этом предполагаем, что емкости накопителей приспособлений, деталей, заготовок, инструмента в ЧПМ достаточны для работы во вторую и третью смены без вмешательства человека. Полагаем также, что производительность труда адекватно соответствует производственной мощности станка с ЧПУ и ГПМ, выраженной в часах их работы в течение года. Исходные данные для расчета приведены в табл. 6, сам расчет в табл. 7.
Таблица 6
Исходные данные
Показатели | Автономный станок с ЧПУ | Станок с ЧПУ в ГПМ |
Коэффициент сменности работы Коэффициент загрузки (коэффициент использования) оборудования Простои по организационно-техническими причинами, ч/см Устранение отказов, ч/см Настройка и переналадка, ч/см | 1,4 0,5 0,5 0,4 0,8 | 3,0 0,8 0,25 0,2 0,15 |
Как следует из табл. 7, создание ГПС позволяет довести рабочее время основного технологического оборудования с 1083 ч до 4528 ч. А при работе без выходных и праздничных дней полезное используемое время приближается к своему теоретическому максимуму и составляет около 6700 ч.
Опыт эксплуатации действующих ГПС показывает, что непременным условием их эффективности является высокая загрузка оборудования в течение суток.
Следовательно, первой и одной из важнейших проблем создания ГПС становится обеспечение реальной загрузки производственной мощности ГПС на длительный период времени при ее 2-3-х сменной работе.
Вторая проблема связана с необходимостью коренной реконструкции и перевооружения (еще до начала эксплуатации ГПС) вспомогательных и обслуживающих производств непосредственно или даже косвенно связанных с обеспечением ГПС.
Таблица 7
Расчет агрегатной производительности станков
Показатели | Величина показателя | |
Станок с ЧПУ | Станок в ГПМ | |
Календарный фонд времени | 24*365=8760 ч | |
Потери календарного фонда из-за выходных и праздничных дней, ч | 24*110=2640 | |
Потери календарного фонда из-за неработы в 3-ю смену, ч | 8*(365-110)=2040 | - |
Потери фонда из-за неработы 0,6 станочного оборудования во 2-ю смену, ч | 8*(365-110)*0,6=1224 | - |
Потери из-за невыходов на работу, ч | 8*15=120 | - |
Потери из-за устранения отказов, ч | 0,4*(365-110-15)*1,4= =134 | 0,2*(365-10)*3,0= =153 |
Потери из-за простоев по организационно-техническим причинам, ч | 0,5*(365-110-15)*1,4= =168 | 0,25*(365-10)*3,0= =192 |
Потери из-за настройки и переналадки, ч | 0,8*(365-110-15)*1,4= =268 | 0,15*(365-110)*3,0 =115 |
Фонд времени работы станка, ч | 8760-6594=2196 | 8760-3100=5660 |
Отсутствие загрузки при Ки=0,5, ч | 2166*(1-0,5)=1083 | 5660*(1-0,8)=1132 |
Действительный (полезный) фонд, ч | 2166-1083=1083 | 5660-1132=4528 |
Создание ГПС требует кардинальных, четко координируемых изменений во всех аспектах деятельности фирмы и, в частности, в методах ведения бизнеса, начиная от разработки продукта, закупки комплектующих и кончая контролем качества продукции.
Так корпорация «Форд» внедрила параллельный, групповой, в противовес последовательному, подход к организации работы проектировщиков и инженеров, что в совокупности с применением технологии компьютерного проектирования и контроля за производственным процессом КАД/ КАМ (Computer aided design/computer aided manufacturing) привело к сокращению на одну треть времени на разработку новых моделей.
Многие производители ныне планируют производство совместно со своими поставщиками и поддерживают с ними постоянные связи. Это позволяет фирмам, находящимся ниже по технологической цепочке обновлять запасы компонентов и материалов на основе поставок точно в срок.
Наличие гибкого производства, малых запасов конечной продукции и средств электронной связи в совокупности позволяет фирме «Бenetton», постоянно имея запасы неокрашенной одежды (рубашки, шарфов, пуловеров) и исходя из информации о вечерних продажах, собранной в его автоматизированном центре управления сбытом от терминалов в магазине, на следующий день отгружать продукцию определенных цветов и в определенные места. Вершиной развития данного направления является производство продукции (ранее создававшейся в массовых количествах) на основе прямых заказов: в рамках проекта «Сатурн» автомашины «Дженерал Моторс» производятся по заказам клиентов в течение нескольких дней после получения по сетям компьютерных связей индивидуальных заказов.
Промышленные фирмы, которые применяют ГПС, отличаются от обычных фирм и стратегий управления продуктом. Многие из них расширяют ассортимент изделий и при этом повсеместно усиливают акцент на качество. Фирма «Моторола» при оплате труда рабочих больше учитывает квалификацию, чем характер работы и наделяет рабочих многими полномочиями, включая право осуществлять контроль качества.
Методы оценки эффективности инвестиций в любой проект, в том числе в создание ГПС, можно разделить на две группы: простые или статические (срок окупаемости и рентабельность инвестиций) и методы дисконтирования (расчет чистой текущей стоимости и внутренней нормы доходности).
Период окупаемости один из самых простых методов оценки инвестиций. Определяется как время, требуемое для того, чтобы доходы от проекта стали равны первоначальному вложению в проект. Если ожидается, что денежный поток от проекта будет одинаковым в течение ряда лет, то период окупаемости можно найти делением суммы капиталовложений на ожидаемую сумму ежегодной прибыли:
Ток=К/ПР, (5.32)
где Ток – период окупаемости;
К – инвестиции в проект;
ПР – сумма ежегодной прибыли.
Промышленные предприятия в развитых странах часто используют максимальный период окупаемости 4-5 лет и отклоняют все инвестиционные предложения, период окупаемости которых больше этого максимума, хотя от некоторых видов инвестиций редко может быть срок окупаемости в 5 лет.
Рентабельность инвестиций R есть величина обратная сроку окупаемости
R=ПР/К=ТП/К (5.33)
Ток и R не учитывают весь период функционирования проекта, а, следовательно, на них не влияют доходы, которые лежат за пределами Ток..
Дисконтированные методы основываются на расчете временной ценности денег. Чистая текущая стоимость характеризует общий абсолютный результат инвестиционного проекта. Ее определяют как разницу между текущей приведенной стоимостью потока будущих доходов и текущей приведенной стоимостью потока будущих затрат на реализацию и функционирование проекта во времени всего цикла его жизни:
(5.34)
где NPV – чистая текущая стоимость;
Bt, Zt -доходы, затраты в t-ом году;
r - ставка дисконта;
tн - год, принимаемый за расчетный;
n- срок жизни проекта.
Ставка дисконта для собственного капитала определяется исходя из депозитного процента по вкладам. Для заемного капитала ставка дисконта определяется условиями выплаты погашений по займам (усредненная ставка по долгосрочным банковским кредитам).
Внутренняя норма доходности (IRR)- это расчетная ставка процента, при которой получаемые доходы от проекта становятся равными затратам на проект, т.е. ставка процента при которой NPV =0.
(5.35)
Выбор того или иного варианта автоматизации производства основывается на сопоставлении показателей экономической эффективности инвестиций: срока окупаемости, рентабельности инвестиций, внутренней нормы доходности, чистой текущей стоимости.
6. Организация работ в основных и вспомогательных цехах
|
|
История развития пистолетов-пулеметов: Предпосылкой для возникновения пистолетов-пулеметов послужила давняя тенденция тяготения винтовок...
Индивидуальные очистные сооружения: К классу индивидуальных очистных сооружений относят сооружения, пропускная способность которых...
Организация стока поверхностных вод: Наибольшее количество влаги на земном шаре испаряется с поверхности морей и океанов (88‰)...
История создания датчика движения: Первый прибор для обнаружения движения был изобретен немецким физиком Генрихом Герцем...
© cyberpedia.su 2017-2024 - Не является автором материалов. Исключительное право сохранено за автором текста.
Если вы не хотите, чтобы данный материал был у нас на сайте, перейдите по ссылке: Нарушение авторских прав. Мы поможем в написании вашей работы!