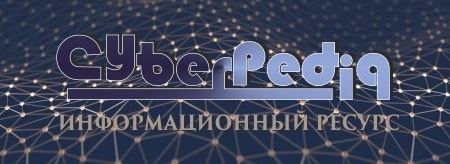
Индивидуальные и групповые автопоилки: для животных. Схемы и конструкции...
Состав сооружений: решетки и песколовки: Решетки – это первое устройство в схеме очистных сооружений. Они представляют...
Топ:
Определение места расположения распределительного центра: Фирма реализует продукцию на рынках сбыта и имеет постоянных поставщиков в разных регионах. Увеличение объема продаж...
Установка замедленного коксования: Чем выше температура и ниже давление, тем место разрыва углеродной цепи всё больше смещается к её концу и значительно возрастает...
Комплексной системы оценки состояния охраны труда на производственном объекте (КСОТ-П): Цели и задачи Комплексной системы оценки состояния охраны труда и определению факторов рисков по охране труда...
Интересное:
Распространение рака на другие отдаленные от желудка органы: Характерных симптомов рака желудка не существует. Выраженные симптомы появляются, когда опухоль...
Средства для ингаляционного наркоза: Наркоз наступает в результате вдыхания (ингаляции) средств, которое осуществляют или с помощью маски...
Финансовый рынок и его значение в управлении денежными потоками на современном этапе: любому предприятию для расширения производства и увеличения прибыли нужны...
Дисциплины:
![]() |
![]() |
5.00
из
|
Заказать работу |
Содержание книги
Поиск на нашем сайте
|
|
В гидрометаллургическом отделении осуществляется очистка никелевого электролита от примесей и ряд других операций, связанных с приготовлением католита. Технологические процессы включают в себя несколько операций:
- осаждение примесей с получением пульп,
- разделение пульп на жидкое (фильтрат) и твердое (кек),
- растворение металлов из твердых материалов (цементация, выщелачивание), а также ряд других операций.
На определенных стадиях процесса осуществляется транспортировка растворов, осадков, реагентов, сжатого воздуха, пара, отходящих газов и других материалов.
Оборудование для осуществления технологических процессов условно подразделяется на следующие виды:
1. Реакционное
2. Фильтровальное
3. Для транспортировки сред.
4. Теплообменное.
3.1. РЕАКЦИОННОЕ ОБОРУДОВАНИЕ.
3.1.1. ПАЧУК (пневматический агитатор).
Пачук - реакционная емкость с воздушным перемешиванием. Может использоваться в качестве сборников или сгустителей. В зависимости от назначения пачука изменяется и схема его обвязки.
Пачук (рис.1) представляет собой стальной цилиндрический бак с коническим днищем. Футеровка пачука производится следующим образом: наносится два слоя рубероида на горячем битуме, затем выкладывается диабазовая плитка и кислотоупорный кирпич в два слоя. Сверху пачук закрывают крышкой, имеющей штуцеры для подачи растворов и реагентов, пара, воздуха, удаления паро-воздушной смеси, установки приборов КИПиА. Пульпа и растворы подаются в пачук на зеркало раствора или на определенную глубину, через боковые трубопроводы или штуцеры. Отбор пульпы производится через желоба, боковые штуцеры или штуцеры в конусе пачука (самотеком, в корыто дисковых вакуум-фильтров эрлифтом или с помощью насоса).
Перемешивание пульпы осуществляется выносными эрлифтами, титановыми трубами, заглубленными в пачук, по которым подводится сжатый воздух с давлением 1,0-1,2 кгс/см2, а также рециркуляцией насосом.
Газо-воздушная смесь из пачука удаляется через специальный штуцер либо в атмосферу, либо с помощью вентилятора по титановому газоходу на пенный аппарат (с пачуков концентратного передела и кобальтоочистки).
Объём пачуков ГМО составляет от 60 до 125 м3.
Остановка пачука на ремонт при непрерывном процессе осуществляется следующим образом: прекращают подавать исходный раствор и реагенты и максимально выбирают пачук. Оставшуюся часть пульпы сливают в технологический процесс через коренную задвижку. На всех трубопроводах и линиях устанавливают заглушки, желоба перекладывают кислотоупорным кирпичом. Место установок заглушек записывается в журнале работ механиком ГМО.
|
3.1.2. ЦЕМЕНТАТОР.
Цементатор - ёмкость специальной конструкции, предназначенная для очистки растворов от меди при помощи активного никелевого порошка методом цементации, представляет собой круглый вертикальный сосуд, расширяющийся снизу вверх (рис.2). Футеровка цементатора осуществляется аналогично футеровке пачука.
Раствор подают насосами в нижнюю часть цементатора через тангенциально вваренный штуцер. Скорость подачи раствора должна обеспечить перемешивание всего никелевого порошка в аппарате. Зерна порошка имеют разную крупность, поэтому для равномерного распределения порошка по объему аппарата его сечение сделано коническим. Коническая часть полностью заполнена “кипящим” слоем никелевого порошка и цементной меди. Для уменьшения выноса цементной меди и порошка аппарат имеет в верхней части (чаше) отстойник. В верхней части чаши скорость вертикального потока снижается и частицы твердого продукта не поднимаются выше определенного уровня, образуя весьма четкую границу “кипящего” слоя. В отстойнике установлен сливной порог, переливаясь через который раствор вытекает из аппарата по трубопроводам и направляется на переработку. Выделившаяся из раствора цементная медь периодически выводится из цементатора. Выпуск меди осуществляется в основном с помощью аэролифта, а также еженедельно через нижний штуцер в корпусе цементатора (1,0-1,5 т в тару).
Аэролифт представляет собой титановый трубопровод диаметром 100 мм, в который нижней части врезана воздушная титановая трубка диаметром 20 мм. Аэролифт погружается в цементатор на 6-7 м. За счет высокого гидростатического давления плотной пульпы в нижней части цементатора и ускорения вертикального потока воздухом, цементная медь совместно с раствором поднимается по всей высоте аэролифта и в зависимости от положения запорной арматуры направляется на дальнейшую переработку (на шнек), либо обратно в цементатор (рециркуляция).
|
Цементатор сверху закрывается металлической крышкой, имеющей штуцеры для установки аэролифта, отбора проб, установки контрольно-измерительных приборов для измерения уровней в карманах и ОВП, вытяжки паро-воздушной смеси.
На напорном трубопроводе в цементатор устанавливается обратный клапан для избежания забивки трубопроводов при аварийной остановке насосов. Во всех цементаторах установлены решетки.
Все цементаторы оборудованы контрольным сливом, направленным в сборник № 1.
Объём цементатора-80 м3.
Порядок заполнения цементаторов:
1. Цементатор 1-й группы.
а) Заполнение цементной медью из цементатора 1-й группы: “подушка” до уровня 7 м-6 т.
б) Загрузка никелевого порошка -3 т.
в) Заполнение цементной медью из цементаторов 1-й или 2-й группы до уровня 2 м.
2. Цементатор 2-й группы.
а) Заполнение цементной медью из цементатора 1-й группы: “подушка” до уровня 7 м-6 т.
б) Заполнение цементной медью из цементатора 2-й группы до уровня 6 м-6 т.
в) Загрузка никелевого порошка -3 т.
г) Заполнение цементной медью из цементатора 2-й группы -20 т.
д) Загрузка никелевого порошка -3 т.
е) Заполнение цементной медью из цементатора 2-й группы -20 т.
ж) Загрузка никелевого порошка -3 т.
з) Заполнение цементной медью из цементатора 2-й группы до уровня 2 м.
3.1.3. ЕМКОСТЬ.
Емкости предназначены для сбора и усреднения никелевых растворов: анолита и католита (См. рис.3).
Емкость представляет собой цилиндрический металлический бак с плоским днищем, установленным на фундамент. Футеровка выполняется аналогично пачуку.
Диаметр емкости -9 м
Высота -8 м
Полный объем -400 м3
Сверху емкость закрывается титановой крышкой, в которой имеются штуцеры для подачи и рециркуляции растворов, вытяжки паро-воздушной смеси, подачи реагентов и установки приборов КИПиА.
В верхней части корпуса имеется штуцер для контрольного слива, а в нижней -для откачки растворов.
В отделении находятся 4 емкости.
№№ 1,2 -емкости католита.
№№ 3,4 -емкости анолита,
Емкости могут работать параллельно, либо по одной, заполняемые соответственно католитом или анолитом.
3.1.4. РЕПУЛЬПАТОР.
Репульпатор предназначен для распульповки твердых материалов, а также как емкость –наполнитель (рис.4).
В зависимости от назначения репульпатора изменяется схема его обвязки и оснащения.
В отделении используются репульпаторы 2-х типов:
- репульпатор с плоским днищем,
- репульпатор с коническим днищем.
На рис.4 показан репульпатор с плоским днищем.
Репульпатор с коническим днищем выполняется аналогично.
Репульпатор представляет собой металлический сосуд, футерованный аналогично пачуку.
Для перемешивания пульпы применяют мешалки, рециркуляцию пульпы насосом, сжатый воздух. В крышке репульпатора смонтированы штуцеры, предназначенные для ввода пульпы (кека, раствора), подачи реагентов, пара, воздуха, установки приборов КИПиА, удаления паро-воздушной смеси, а также люк-лаз.
|
Штуцер для ввода пульпы монтируется в нижней части корпуса.
Пуск в работу репульпатора осуществляется следующим образом: репульпатор на 30 % заполняется водой (раствором) и ставится на рециркуляцию насосом, затем включается мешалка, открываются вентили подачи пара и сжатого воздуха. После загрузки (подачи) раствора или пульпы подаются реагенты, При снижении уровня раствора до 20 % отключается мешалка, закрывается пар и воздух.
Некоторые операции по пуску, работе и остановке репульпаторов могут быть опущены, изменены или дополнены в зависимости от требования технологического процесса.
В отделении используются репульпаторы различных геометрических форм и размеров, но принципиального отличия от вышеописанных они не имеют.
3.1.5. СГУСТИТЕЛЬ.
Сгуститель предназначен для сгущения пульпы карбоната никеля перед фильтрованием.(Рис.5)
Сгуститель одноярусный, с центральным приводом, представляет собой цилиндрический бак объемом 70 м3. В центре сгустителя подвешен вертикальный вал с прикрепленным к нему скребковым устройством, состоящим из 4-х радиально направленных граблин.
Механизм вращения граблин передает вращение привода вертикальному валу и связанным с ним граблинам. Механизм подъема граблин служит для регулирования положения скребкового устройства относительно днища чана и
подъема его для предупреждения заклинивания на время остановки сгустителя.
Загрузочная воронка служит для равномерного и спокойного поступления пульпы в чан сгустителя. Она представляет собой цилиндр, подвешенный к нижней части фермы.
Т е х н и ч е с к а я х а р а к т е р и с т и к а:
Диаметр чана внутренний -6000 мм;
Высота чана -2500 мм;
Объем пульпы в чане -70 м3;
Скорость вращения граблин -0,256 об/мин;
Поверхность осаждения -28,3 м2;
Производительность -14,62 т/сутки;
Передаточное число редуктора -39;
Высота подъема граблин -300мм.
3.1.6. ПАЧУК КАНАЛЬНОГО СГУЩЕНИЯ.
Пачук канального сгущения конструктивно аналогичен пачуку, показанному на рис.1
Пакеты (канальные сгустители) устанавливаются в специальную раму, заглубленную под зеркало раствора на расстояние 1455 мм от верхней крышки. В пачуках может находиться от 21 до 27 пакетов.(Рис.6)
Пакет состоит из корпуса, представляющего наклонную на 10 градусов четырехгранную призму с габаритными размерами 1200 х 600 х 250 мм. Пакет изготовлен из титанового сплава ВТ -1. Внутренняя полость разделена на пять продольных каналов, общей площадью 4,05 м2. В верхней части через трубки с отверстиями все пять таких плоских каналов объединяются в коллектор, снабженный штуцером диаметром 33 мм. На штуцер надевается резиновый шланг, который заканчивается специальной насадкой с выходным отверстием диаметром 7 мм. Сечение насадки может изменяться с помощью регулировочного винта
|
Резиновые шланги с коллекторов сгустителей через специальные штуцеры в корпусе пачука направлены в приемные коробки.
Пульпа с выгрузки свечевых фильтров железоочистки подается сверху в пачук через специальную воронку на глубину 6 м.
Частицы твердого седиментируют (оседают) в нижнюю часть пачука и самотеком направляются на дисковые вакуум-фильтры. Содержание твердого 40-100 г/л.
Осветленный слив с содержанием твердого до 5 г/л из приемных коробок самотеком поступает в емкость электроподогрева. В пачуках непрерывно автоматически поддерживается объем 110-115 м3.
В отделении имеется 4 пачука канального сгущения №№ 1,3,5 и 8.
3.1.7. КОЛОННА АВТОКЛАВА.
Колонна автоклава предназначена для увеличения скорости реакции выщелачивания сульфидов никелевого концентрата в серной кислоте при высокой температуре и давлении воздуха.
Растворение производится в автоклаве, состоящем из 12 последовательно соединенных вертикальных колонн.
Головная колонна (рис.7) представляет собой цилиндрический вертикальный сосуд с нижним и верхним запорными узлами, присоединенными к корпусу при помощи накидных фланцев. Корпус колонны состоит из двух частей, соединенных фланцами. Внутри колонн установлена решетка.
Через нижний запорный узел по штуцерам вводится пульпа, пар и воздух соответственно.
Через верхний запорный узел по штуцеру вводится серная кислота и по штуцеру А пульпа выводится из колонны и через стояки поступает снизу во вторую и т.д., проходя последовательно еще 11 колонн.
На верхнем запорном узле головной колонны установлены также штуцеры Е,К для установки манометра и термометра
Последующие колонны (от 2-й до 12-й) принципиальных конструктивных отличий не имеют, за исключением корпуса колонн, который выполнен из нижнего и верхнего запорных узлов, имеющих по одному штуцеру для входа и выхода пульпы.
В отделении находится 4 нитки автоклава по 12 колонн каждая.
Пульпа из последней 12-й колонны направляется в сепаратор.
3.2. ПЕННЫЕ АППАРАТЫ.
Пенный аппарат (рис.8) представляет собой прямоугольный сосуд, выполненный из титана, с конусным днищем, высотой -5 м. В верхней части аппарата установлены две горизонтальные титановые решетки. Назначение решеток -создание развитой поверхности соприкосновения нейтрализующего раствора с хлоро-воздушной смесью, которая протягивается вентилятором через весь объем аппарата.
В ГМО-1,2 установлены по два пенных аппарата. В работе как правило один аппарат (второй-резерв).
По мере забивания отверстий на решетках снижается производительность аппарата -ему проводят регенерацию раствором сульфита натрия (Na2SO3) с серной кислотой -концентрация -50 г/л.
|
3.3.ФИЛЬТРОВАЛЬНАЯ АППАРАТУРА.
Оборудование, при помощи которого производится разделение пульп на твердое и жидкое, называется фильтровальным.
В зависимости от требований, предъявляемых к качеству осадка и качеству фильтрата в каждом конкретном случае, подбирается и используется различное фильтровальное оборудование.
3.3.1. СВЕЧЕВОЙ ФИЛЬТР.
ПКФ-80А-ТС; ПКФ-40А св.-Т
(Патронный керамический фильтр 80, 40-соответственно площадь фильтрации.)
Свечевой фильтр -аппарат периодического действия. Предназначен для получения фильтрата с минимальным количеством твердого.
Устройство его и техническая характеристика представлена на рис.9.
Фильтр состоит из цилиндрического сосуда с коническим или сферическим днищами, съемной сферической крышкой, цилиндрических свечей, собранных из керамических элементов, опирающихся на отводные трубы в нижней части фильтра и линейные боковые направляющие со стороны корпуса фильтра и общего коллектора для фильтрата. Пульпа поступает в фильтр через штуцеры на нижней или верхней крышке, жидкая фаза ее последовательно проходит, как показано на рис.6, слой уже образовавшегося осадка, пористую стенку керамического элемента, после чего по вертикальному каналу уходит из свечи в коллектор, где в виде фильтрата со всех свечей выходит из аппарата. Твердая фаза накапливается в виде слоя осадка на внешней поверхности свечей. Осадок с остатками пульпы периодически выгружается из фильтра в репульпатор или на всас центробежного насоса.
Свеча представляет собой металлическую трубу с радиальными отверстиями и продольными ребрами. На металлическую трубу надеваются керамические элементы, между которыми размещаются уплотнительные прокладки. Из свечей состоит пакет, в котором свечи расположены в один ряд и объединены одним коллектором по фильтрату. На свечи, собранные из керамических элементов, при необходимости одеваются рукава из ткани. Выбор ткани определяется составом фильтруемых пульп.
Керамические элементы в каждой свече стягиваются гайками через тарельчатые пружины, служащие для компенсации разности температурного расширения керамики и металлической трубы.
Верхние концы свечей одного пакета скреплены траверсой для придания жесткости всему пакету.
Пакеты свечей устанавливаются в корпус фильтра по линейным направляющим, размещенным внутри корпуса фильтра, на посадочные гнезда отводных труб (отвод фильтрата от пакета к коллектору фильтрата) через уплотнительную (ромбическую в сечении) прокладку из резины. Отводные трубы соединены с коллектором фильтрата посредством вентилей, и, в случае повреждения одного керамического элемента на одном из пакетов, последний может быть отключен.
Для контроля чистоты фильтрата каждого пакета на отводных трубах установлены вентили с пробоотборниками. Свечевые фильтры являются аппаратами периодического действия. Цикл их работы состоит из следующих операций:
-наполнение фильтра;
-фильтрование пульпы;
-барботаж пульпы в межсвечевом пространстве;
-выгрузка осадка,
после чего цикл повторяется.
Для заполнения свечевого фильтра (рис.10) открываются задвижки № 4 (по линии выпуска воздуха со свечевого фильтра), №№ 3,1 на линии подачи пульпы
для фильтрования на аппарате.
На рис.11 показаны линии подвода и отвода пульпы, фильтрата, воздуха и т.д. Пульпа под давлением подается в фильтр через задвижку №1, воздух вытесняется пульпой через задвижку №4. После заполнения фильтра пульпой задвижка №4 закрывается и одновременно открывается задвижка №3 на линии (трубопроводе) чистого фильтрата.
По мере фильтрования пульпы на керамических элементах увеличивается толщина осадка и уменьшается производительность фильтра. По окончании фильтрования (по циклограмме работы фильтра для определенного передела) производится барботаж пульпы. Для этого открывается задвижка №4, задвижки №1 и №3 закрываются и открывается задвижка №9, и в течении 15-30 мин. происходит отдувка пульпы при давлении 1,5-2,0 кгс/см2. После этого происходит выгрузка осадка, для чего закрывается задвижка №9 и открывается задвижка №10, и пульпа выгружается либо самотеком в репульпатор, либо на всас насоса.
По мере фильтрования пульпы на свечевом фильтре керамика забивается мельчайшими частицами осадка, в результате чего производительность фильтра снижается. Для очистки пор керамических элементов производится их регенерация -растворение осадка кислым раствором (водный раствор серной кислоты с концентрацией 50-120 г/л), который по трубопроводу закачивается через штуцер верхней крышки, и последующим барботажем регенерат выгружается по трубопроводу через задвижку №10 согласно технологии выгрузки регенерата для данных переделов.
У п р а в л е н и е запорной арматурой свечевых фильтров.
Система управления запорной арматурой свечевых фильтров состоит из пульта управления, шкафа мембранных блоков, блоков воздухораспределителей (золотников) и манометров.
Управление запорной арматурой производится с пульта управления. При включении определенного тумблера командный электрический сигнал поступает в блок пневмораспределителей, где преобразуется в пневматический для управления соответствующей запорной арматурой (задвижкой) с пневмоприводом, при этом задвижка открывается или закрывается в зависимости от положения тумблера, о чем сигнализирует соответствующая лампа. При нахождении задвижки в открытом положении лампа горит в полный накал, в промежуточном не горит, в конечном горит в полнакала.
Во избежание ошибочного включения фильтра, находящегося в ремонте (переборка, замена трубопроводов, задвижек), с него должно быть снято напряжение. Производство подключений и отключений производится цеховой службой КИПиА.
3.3.2. ДИСКОВЫЙ ВАКУУМ-ФИЛЬТР.
ДТ-68-2,5 ДТ-34-2,5
(Дисковый титановый, 68 и 34 соответственно -площадь фильтрования; 2,5-диаметр (м)).
Дисковый вакуум-фильтр является фильтром непрерывного действия и предназначен для обезвоживания сгущенных пульп. Устройство и техническая характеристика дискового вакуум-фильтра представлены на рис.11.
Дисковый вакуум-фильтр состоит из горизонтально расположенного полого двенадцати канального вращающегося вала с установленными на нем дисками, частично погруженными в корыто с пульпой.
Каждый диск состоит из двенадцати разобщенных один от другого секторов с перфорированными стенками, обтянутыми фильтровальной тканью. Внутренние полости секторов соединены с каналами вала, выходящими на его торцевую стенку, к которой прижата своими рабочими (внутренними) поверхностями распределительная головка. Распределительная головка вала имеет кольцевой ряд камер, разобщенных одна от другой перегородками. Камеры связаны через трубопроводы с вакуум-насосом и воздухонагнетателем. На корыте имеются сливные штуцеры в верхней части (для слива избыточной пульпы) и нижней части (для полной очистки корыта).
Фильтрование начинается в тот момент, когда сектора, находящиеся в пульпе, соединяются через вал и распределительную головку с вакуумной системой. Фильтрат отсасывается через фильтровальную ткань и перфорированные стенки сектора и по каналам вала и камерам распределительной головки отводится в ресивер, а на секторах образуется слой осадка. Сектора, вышедшие из пульпы, по-прежнему соединены с вакуум-насосом. Раствор, находящийся в слое осадка секторов, также отсасывается в ресивер. После просушки слоя на секторах, последние попадают в зону отдувки, т.е. соединяются с воздухонагнетателем, и при помощи сжатого воздуха освобождаются от слоя осадка. Осадок секторов попадает в разгрузочные карманы бункера, оставшийся осадок снимается ножами, когда сектора проходят между разгрузочными карманами.
Ресивер -емкость на вакуумной линии (трубопроводе), предназначенная для разделения фильтрата и воздуха. Принципиальная схема работы дисковых вакуум-фильтров показана на рис.12.
Пуск и остановка вакуум-фильтра осуществляется в следующем порядке:
- включается вращение вала с дисками;
- ванна (корыто) фильтра до верхнего сливного штуцера заполняется пульпой;
- открывается задвижка на трубопроводе вакуум-насоса;
- после набора осадка секторами открывается вентиль на трубопроводе воздухонагнетателя.
Для остановки вакуум-фильтра сначала необходимо перекрыть поступление пульпы в корыто фильтра, выбрать находящуюся в нем пульпу. Затем перекрыть вакуумную и воздушную магистрали и отключить привод фильтра. При длительной остановке фильтра оставшуюся в корыте пульпу необходимо слить через нижний штуцер или отсифонить.
3.3.3. ФИЛЬТР ПАТРОННЫЙ.
ПАР-80-2 48 Т-2
Фильтр предназначен для фильтрования пульп, когда не требуется получения сухого остатка.
Фильтр (рис.13) представляет собой вертикальный сварной цилиндрический корпус с коническим днищем. Внутри корпуса в верхней его части имеются гнезда для установки в них секций фильтровальных элементов. Каждое гнездо с помощью трубы, опущенной внутри корпуса вниз аппарата, сообщается с коллектором отвода фильтрата, расположенным снаружи корпуса в нижней его части.
На каждой трубе, отводящей фильтрат от секции, предусмотрен пробоотборник для контроля качества фильтрата.
Фильтрующий элемент (патрон) представляет собой витой в виде пружины каркас, поверх которого одевается тканевый рукав (бельтинг), один конец которого зашит, а второй обматывается титановой проволокой.
Герметичность соединения фланцев корпуса и крышки обеспечивается байонетным затвором с клиновидными зубьями. В качестве уплотнения применяется резинотканевый шланг, внутрь которого подается сжатый воздух.
Поворот байонетного кольца и подъем крышки осуществляется с помощью пневмоцилиндров.
Работа фильтра заключается в следующем: пульпа центробежным насосом подается через задвижку 1 в штуцер А на корпусе фильтра, расположенный в его нижней части. Воздух вытесняется через штуцер В и задвижку 4, расположенные на крышке. После заполнения фильтра закрывается задвижка 4 и открывается задвижка 3; начинается фильтрование, раствор продавливается через поры ткани и выводится через коллектор из фильтра, а осадок накапливается на рукавах. Через 5-5,5 часов фильтр останавливается, закрываются задвижки №№ 1 и 3, открывается задвижка №4 и оставшаяся в фильтре пульпа через штуцер и задвижку №10 самотеком сливается в репульпаторы. После опорожнения фильтра производится поворот байонетного кольца и подъем крышки. Оставшийся на рукавах осадок смывается водой. После чего цикл повторяется.
В процессе работы поры ткани забиваются мельчайшими частицами пульпы (засульфачиваются). В таком случае ткани делается регенерация раствором, содержащим 10-15 г/л кислоты. Режим регенерации отрабатывается ЦЗЛ и персоналом цеха. При механическом повреждении ткань заменяется новой.
Управление запорной арматурой ПАР -80-248 Т -2 происходит аналогично управлению запорной арматурой свечевых фильтров.
Т е х н и ч е с к а я х а р а к т е р и с т и к а ПАР.
Поверхность фильтрования, м2 -80
Рабочее давление, кгс/см2 -3
Объем корпуса фильтра,м3
общий -11,5
заполненный пульпой -11,0
Состояние рабочей пульпы - жидкость, пульпа
Характеристика среды - агрессивная,
- невзрывоопасная,
- нетоксичная
Максимальная температура среды - 900 С
Допустимая скорость коррозии, мм/год - 0,1
Количество фильтровальных секций, шт. - 19
Количество фильтровальных патронов, шт. - 246
Диаметр фильтровального патрона, мм - 60
Материал частей, соприкасающихся с пульпой - сплав ВТ I -0.
3.3.4. РАМНЫЙ ФИЛЬТР-ПРЕСС.
Рамный фильтр-пресс - аппарат периодического действия, предназначен для фильтрации пульп.
Рамный фильтр-пресс состоит из головной неподвижной плиты со штуцером и зажимом подвижной плиты, перемещающейся по несущим тягам с помощью электропривода.
На несущих тягах помещается набор деревянных или металлических плит и рам с полотнами, являющимися фильтрующими элементами. Плиты и рамы (до 50 комплектов) плотно прижимаются друг к другу, образуя камеры фильтр-пресса. Плиты представляют собой плоские пластины с рифленой поверхностью. Рифление плит имеет целью создание каналов для стока фильтрата и выполняется в виде вертикальных борозд, соединенных внизу плиты в общий коллектор. Принцип работы рамного фильтр-пресса показан на рис.13. Отверстия в верхней части плит и рам, совпадающие по оси, образуют один общий канал для подачи пульпы в камеры между плитами, соединенный с вводным штуцером головной плиты. Пульпа нагнетается насосом в канал и через отверстия в верхних стенках рам поступает во внутреннее пространство камер, образованных плитами и рамами. Жидкость проходит через фильтровальную ткань, выбираемую в зависимости от состава пульп, и по канавкам в плитах стекает в нижний сборный канал и через направляющие каналы вытекает в желоб. Осадок остается на ткани. По окончании фильтрования осадок промывают и продувают. По окончании продувки отодвигают зажимную плиту и счищают осадок в поддон, откуда перегружают в кюбели.
Площадь фильтрования - 40-50 м2
Рабочее давление - до 4 кгс/см2
3.4. СЕПАРАТОР.
Сепаратор предназначен для отделения пульпы от паро-воздушной смеси при автоклавном выщелачивании никелевого концентрата.
Сепаратор (рис.14) представляет собой цилиндрический вертикальный аппарат с коническим днищем и плоской крышкой, присоединенной к корпусу при помощи накладных фланцев.
В верхней части сепаратора имеется штуцер для ввода продукта, а в нижней, конической, для вывода пульпы. В крышке имеются штуцеры для отвода паро-воздушной смеси и установки приборов КИПиА.
Из последней колонны нитки автоклавной установки пульпа и газ (воздух, насыщенный парами воды и обедненный кислородом) под давлением через тангенциально вваренный штуцер А поступает в корпус сепаратора и приобретают интенсивное вращательное движение.
Под воздействием центробежных сил пульпа прижимается к стенкам аппарата и движется по спиральной траектории вниз к штуцеру Б. Паро-воздушная смесь движется во внутреннем спиральном потоке вверх вдоль оси аппарата и удаляется через штуцер В.
Для более глубокого разделения пульпы и газо-воздушной смеси на каждой нитке автоклавной установки установлено 2 аппарата последовательно.
3.5. ОБОРУДОВАНИЕ ДЛЯ ТРАНСПОРТИРОВКИ РАЗЛИЧНЫХ СРЕД.
В гидрометаллургии никеля важное значение имеет транспортирование жидких и газообразных продуктов по трубопроводам внутри цеха между отдельными аппаратами и установками, а также между отделениями.
Движение жидкостей по трубопроводам и через аппарат связано с затратами энергии. В некоторых случаях, например, при движении с более высокого уровня на более низкий, жидкость перемещается самотеком, т.е. без затрат внешней энергии, вследствие преобразования собственной потенциальной энергии в кинетическую.
При перемещении жидкости по горизонтальным трубопроводам, с низшего уровня на высший применяют насосы.
3.5.1. ЦЕНТРОБЕЖНЫЙ НАСОС.
Насос -гидравлическая машина, которая преобразует механическую энергию перемещаемой жидкости, повышая ее давление. Разность давления жидкости в насосе и трубопроводе обуславливают ее перемещение.
Центробежные насосы -основные механизмы отделения и цеха, обеспечивающие транспортировку растворов, пульп и реагентов.
Устройство центробежного насоса представлено на рис.15.
Техническая характеристика насосов ГМО приведена в таблице №2.
Насосная станция состоит из горизонтального одноступенчатого центробежного насоса и электродвигателя переменного тока, смонтированных на общей раме (плите). Крутящий момент от вала электродвигателя к валу насоса передается через муфту.
Насос состоит из рабочего колеса (турбинки), неподвижно закрепленного на конце вала и вращающегося внутри “улитки” насоса. Вал насоса вращается в двух подшипниковых опорах, расположенных в корпусе. Внутренняя полость корпуса заполняется маслом для смазки подшипников вала.
Пульпа к рабочему колесу подводится через всасывающий патрубок, горизонтально расположенный по оси насоса. Напорный патрубок расположен вертикально (по касательной к улитке).
При вращении колеса насоса пульпа, находящаяся внутри насоса, под действием центробежной силы отбрасывается от центра колеса к образующей улитки. Вследствие этого у всасывающего патрубка создается напряжение, которое затягивает из всасывающей трубы новую партию пульпы. Так как центробежная сила вращающегося колеса действует непрерывно, то и пульпа поступает в насос непрерывно.
Уплотнение между валом и “улиткой” осуществляется с помощью сальниковой набивки. Набивка укладывается в сальниковую коробку и прижимается грунд-буксой. Подтягивание гаек для крепления грунд-буксы осуществляется равномерно, так как чрезмерная затяжка и перекос грунд-буксы вызывает сильный нагрев сальника и преждевременное его стирание.
Для того чтобы образующееся в “улитке” насоса разряжение обеспечивало бесперебойное затягивание суспунзии, насосы устанавливаются как можно ближе к напорному резервуару. В напорном резервуаре постоянно должно находиться некоторое количество пульпы, так как при недостаточном объеме пульпы в резервуаре насос подсасывает воздух, что приводит к нарушению нормальной работы.
Перед включением насоса в работу убеждаются в наличии заземления на эл. двигателе, ограждения полумуфт, проверяется уровень масла по маслоуказателю, производят проворачивание вала насоса и электродвигателя на 1-1,5 об. за полумуфты для проверки свободного вращения без заклинивания.
Пуск насоса в работу осуществляется в следующей последовательности: открывают задвижку на всасывающем трубопроводе насоса, запускается в работу электродвигатель привода насоса, медленно открывается задвижка на напорном трубопроводе. В процессе работы необходимо следить за состоянием подшипников и сальниковым уплотнением, чтобы они не грелись. Правильно набитый сальник должен пропускать жидкость в виде отдельных капель.
Остановка насоса производится в обратной последовательности: сначала закрывают задвижку на нагнетающем трубопроводе, выключают эл. двигатель привода насоса и закрывают задвижку на всасывающем трубопроводе.
Во время работы контролируется работа насосной станции по показаниям амперметра и нагреву электродвигателя.
3.5.2. НАСОС ПДР 4/25-I.
Плунжерный диафрагмовый регулируемый; 4-подача, регулируемая в сторону уменьшения до 60%, м3/час; 25-максимальное давление, кгс/см2; 1-размер твердых частиц, не более мм.
Агрегат насосный одноплунжерный диафрагмовый предназначен для подачи химически активных и нейтральных пульп в колонны автоклавной установки.
Насос отличается от обычных плунжерных тем, что он оснащен специальной диафрагмовой головкой, благодаря которой плунжер при работе не соприкасается с перекачиваемой пульпой. Это предохраняет плунжер от абразивного износа и коррозии. Воздействию суспензии подвергаются лишь легкосъемные клапанные узлы диафрагмовой головки, чулочная диафрагма и коллекторы (всасывающий и нагнетающий).
На рис. 16 изображена принципиальная схема насоса. Основными рабочими органами являются плунжер 12, гидравлический блок (в дальнейшем гидроблок) 17, диафрагмовая головка 16.
Гидроблок в верхней части соединен с диафрагмовой головкой, а снизу с уплотняющим устройством, через которое в него входит плунжер.
Диафрагмовая головка содержит резиновую чулочную диафрагму(4), клапан нагнетания (3) и клапан всасывания (15).
Гидроблок с присоединенной к нему диафрагмовой головкой образует общую полость, разделенную резиновой мембраной (13) на две части:
- камеру 1 - внутреннее пространство гидроблока от плунжера до мембраны;
- камеру 2 - (II) - пространство внутри корпуса диафрагмовой головки, окружающее чулочную диафрагму (4).
Камеры I и II заполнены буферной жидкостью (водой). Плунжер посредством ползуна (II) и шатуна (10) связан с эксцентриком (9), жестко закрепленным на валу (8). На коллекторе нагнетания установлен пневмогаситель (1), рабочая полость которого разделена эластичной куполообразной диафрагмой на две части, из которых нижняя сообщается с коллектором нагнетания, а верхняя герметически изолирована диафрагмой от суспензии.
Работа насоса осуществляется следующим образом: через клиноременную и зубчатую передачи вращение от привода эл. двигателя передается валу (8), от которого посредством эксцентрика (9), шатуна (10) и ползуна (11) сообщается возвратно-поступательное движение плунжеру (12), благодаря чему осуществляются такты нагнетания и всасывания.
Нагнетание осуществляется следующим образом: при движении плунжера вперед (к гидроблоку) он вызывает перемещение буферной жидкости, которая прогибает плоскую мембрану (13) в сторону камеры II и сжимает чулочную диафрагму (4). При этом объем ее внутренней полости уменьшается на величину, равную объему вытесненной плунжером жидкости. Пульпа, находящаяся внутри чулочной диафрагмы, через клапан нагнетания (3) вытесняется в коллектор нагнетания (2).
Всасывание осуществляется следующим образом: при движении плунжера назад (от гидроблока) объем общей полости отсека увеличивается, давление на чулочную диафрагму уменьшается и она расправляется. При этом мембрана прогибается в сторону камеры I. Благодаря возникающему внутри чулочной диафрагмы разряжению, клапан нагнетания закрывается и через него в диафрагму поступает порция пульпы из коллектора всасывания (14).
Давление, с которым осуществляется подача пульпы, ограничивается мощностью привода и прочностью.
Величина подачи регулируется изменением числа двойных ходов плунжера.
Т е х н и ч е с к а я х а р а к т е р и с т и к а насоса ПДР 4/ 25 - I.
Число двойных ходов, ход/с, не более 3
Подача, регулируемая в сторону уменьшения
до 60%, м3/час 4
Давление, кгс/см2, не более 25
Мощность, кВт, не более 4
Коэффициент полезного действия, %, не менее 70
Допускаемая продолжительность самовсасывания,
мин., не более 3
Установленная наработка до отказа,
ч, не менее 1200
Установленный ресурс до капитального ремонта,
ч, не менее 15000
Электродвигатель привода насоса
тип ЧА 160 6 УЗ
м
|
|
Опора деревянной одностоечной и способы укрепление угловых опор: Опоры ВЛ - конструкции, предназначенные для поддерживания проводов на необходимой высоте над землей, водой...
Автоматическое растормаживание колес: Тормозные устройства колес предназначены для уменьшения длины пробега и улучшения маневрирования ВС при...
Механическое удерживание земляных масс: Механическое удерживание земляных масс на склоне обеспечивают контрфорсными сооружениями различных конструкций...
Археология об основании Рима: Новые раскопки проясняют и такой острый дискуссионный вопрос, как дата самого возникновения Рима...
© cyberpedia.su 2017-2024 - Не является автором материалов. Исключительное право сохранено за автором текста.
Если вы не хотите, чтобы данный материал был у нас на сайте, перейдите по ссылке: Нарушение авторских прав. Мы поможем в написании вашей работы!