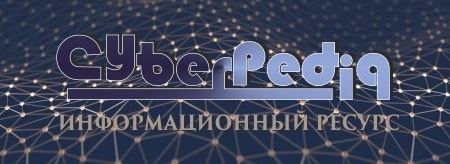
Общие условия выбора системы дренажа: Система дренажа выбирается в зависимости от характера защищаемого...
Таксономические единицы (категории) растений: Каждая система классификации состоит из определённых соподчиненных друг другу...
Топ:
Организация стока поверхностных вод: Наибольшее количество влаги на земном шаре испаряется с поверхности морей и океанов...
Проблема типологии научных революций: Глобальные научные революции и типы научной рациональности...
Техника безопасности при работе на пароконвектомате: К обслуживанию пароконвектомата допускаются лица, прошедшие технический минимум по эксплуатации оборудования...
Интересное:
Аура как энергетическое поле: многослойную ауру человека можно представить себе подобным...
Что нужно делать при лейкемии: Прежде всего, необходимо выяснить, не страдаете ли вы каким-либо душевным недугом...
Лечение прогрессирующих форм рака: Одним из наиболее важных достижений экспериментальной химиотерапии опухолей, начатой в 60-х и реализованной в 70-х годах, является...
Дисциплины:
![]() |
![]() |
5.00
из
|
Заказать работу |
|
|
1.1.1. Кривая однократного испарения (ОИ)
Наиболее простым приемом характеризации состава непрерывных смесей (нефти и нефтяных фракций) стала непрерывная простая перегонка нефти или нефтепродукта, называемая в отрасли однократным испарением (ОИ). Лабораторные данные по ОИ нефти и ее дистиллятов являются основой технологических расчетов практически всех процессов переработки нефти. В настоящее время известно достаточно много расчетных методов построения кривых ОИ для нефтепродуктов, однако для нефтей, особенно для нефтей новых месторождений, а также для смесей нефтей разных месторождений лабораторные данные по ОИ являются наиболее надежными.
Типичные аппараты ОИ схематично показаны на рис. 1.1а,б. Первый из них - это аппарат, в котором зона нагрева потока сырья и зона его испарения и сепарации фаз разделены. Сырье из емкости 1 через змеевик 3, находящийся в воздушной бане нагревателя 4, нагретое до заданной температуры, поступает в теплоизолированный сепаратор 6. Паровая и жидкая фазы по патрубкам 7 и 8 отводятся в приемники 9 и 10, соединенные с системой, создающей вакуум. Патрубки охлаждаются или обогреваются в зависимости от того, какое сырье подвергается анализу. Температуры обеих фаз измеряются термометрами, показания которых должны быть практически одинаковыми, поскольку паровая и жидкая фазы системы должны находиться в состоянии термодинамического равновесия.
Модернизированным вариантом аппарата ОИ явился аппарат Лесли и Гуда (рис. 1.1б), в котором нагревательный змеевик и испаритель помещены в общую баню, заполненную маслом, свинцом или тугоплавкими солями в зависимости от того, какую температуру нужно обеспечить в бане.
|
С помощью рассмотренных аппаратов определяют кривую ОИ нефтей в заданном интервале температур. Опыт проводится в следующей последовательности. Предварительно нагревают баню до температуры на 5-10 °С превышающей заданную (t1). Затем включают подачу сырья (F) со скоростью около 400 мл/ч и в течение 30-40 мин устанавливают стационарный режим, при котором температуры паровой и жидкой фаз равны или близки к t1 (отклонение не более 1 °С). Фиксируют время и начинают измерять количество отбираемых паровой (G) и жидкой (L) фаз, составляя баланс G + L = F. Продолжительность этой части опыта составляет не менее 1 часа. Аналогично проводят опыты при других (трех-четырех) температурах (t2 t3 и т. д.), а затем в виде таблицы или кривой в соответствующих осях координат получают функцию Е = G/F = f(t) (зависимость доли отгона сырья от температуры его нагрева).
Рис. 1.1. Аппарат ОИ с выносным (а) и совмещенным (б) сепараторами:
1 - емкость для сырья; 2 - изоляция; 3 - змеевик; 4 - нагреватель;
5 - термометры; 6 - сепаратор; 7, 8 - патрубки; 9, 10 -приемники паровой и жидкой фаз; 11 - вакуумметр; 12 - буферная емкость;
13 - баня; 14 - решетка с кольцами Рашига; 15 - конденсатор
Разработаны и другие, менее инерционные в лабораторных условиях, конструкции аппаратов ОИ, однако принцип их работы остается неизменным. Поскольку тяжелые углеводороды с температурой кипения выше 350 oC характеризуются термической нестабильностью и разлагаются при нагреве, разгонку нефти ведут в два этапа: разгонку до температуры 300 oC проводят при атмосферном давлении, а разгонку высококипящего остатка или высококипящих фракций нефтепереработки проводят под вакуумом. Полученные значения температур кипения для тяжелых фракций затем пересчитывают на атмосферное давление и строят приведенную кривую ОИ. В отечественной практике для построения кривой ОИ нефти и нефтепродуктов применяют перегонку в стандартной колбе по ГОСТ 2084-77.
1.1.2. Кривая истинных температур кипения (ИТК)
|
Более качественную информацию о фракционном составе нефти дает разгонка нефти в лабораторной колонне периодической ректификации. В этом случае испарительный узел (колба) дополняется укрепляющей ректификационной колонной, обладающей большой разделительной способностью (не менее 30 теоретических тарелок), работающей с орошением верха колонны дистиллятным продуктом при достаточно большом флегмовом числе. Схема отечественного лабораторного аппарата АРН-2 (ГОСТ 11011-85) показана на рис. 1.2.
Аппарат включает стальную ректификационную колонну диаметром 50мм и высотой 1016мм, заполненную насадкой в виде пружинок из нихромовой проволоки 12. Нижний и верхний торцы колонны выполнены в виде сферических шлифованных поверхностей, к которым с помощью накидных гаек 2 и 10 прижаты ответные шлифы головки 6 и горловины куба 1. Металлическая головка имеет кран (К1) для регулирования количества отбираемых с верха колонны фракций в приемник 5 и регулирования расхода орошения. Каждая фракция при этом отбирается в свой приемник. Между верхом колонны и кубом через ловушку 11 подключен дифференциальный манометр 14 для фиксации перепада давления по высоте насадочной колонны, что позволяет косвенно учесть нагрузки колонны по пару и флегме. Вакуум-насос 15 подключен к приемнику 5 через систему трехходовых кранов, Для измерения температур имеется пять термопар (в кубе, на верху колонны и три - по высоте колонны на ее наружной поверхности), показания которых регистрируются потенциометром.
В нефти обычно содержится 0,5-2,0% растворенных газов (С1-С4). Для улавливания газов отключают верхнюю ловушку 11 и подключают баллон 8, заполненный рассолом. Сброс воды из баллона регулируют так, чтобы показание манометра 7 было близким к нулю (атмосферное давление). После того как поступление газа прекратится (по показанию манометра 7), систему приема газа отключают и вновь подключают ловушку 11. Обогрев куба регулируют так, чтобы температура верха колонны установилась через 1,5-2,0 часа после включения аппарата, и по падению первой капли конденсата в приемник фиксируют температуру верха колонны (паров, покидающих колонну). Данная температура соответствует точке начала кипения исследуемого продукта по кривой ИТК.
![]() | Рис. 1.2. Схема аппарата АРН-2: 1 - куб; 2, 10 - накидные гайки; 3 - буферная емкость; 4 - термопары; 5 - приемники фракций; 6 - головка; 7 - водяной манометр; 8 - приемник газа; 9 - вакуумметр; 11 – ловушки; 12 - колонна с насадкой; 13 - нагреватели; 14-дифференциальный манометр; 15 - вакуум-насос; 16 – печь, 17 – конденсатор. |
|
Далее процесс ректификации ведут (с помощью крана К1 и обогрева печи) со скоростью 2,0-2,5 мл/мин или 3-4 мл/мин для исходной загрузки куба 1,9 и 3,0 литра соответственно и показании дифференциального манометра 10 от 50 до 100 мм водного столба. Фракции, выкипающие до 300°С, отбирают при атмосферном давлении, затем куб несколько охлаждают и переходят на остаточное давление 1,ЗЗ кПа. Для этого включают насос и перекрывают сообщение прибора с атмосферой на столько, чтобы поддерживать в системе указанное давление. После отбора фракций до 320°С давление вновь понижают до остаточного давления 0,25 кПа и ведут процесс до первых признаков начала термического разложения остатка в кубе (повышается остаточное давление в системе и температура в кубе). Пересчет температур, измеренных в эксперименте под вакуумом, на атмосферное давление производят по специальной номограмме, прилагаемой к прибору. В таком режиме производят последовательный отбор заданного количества фракций.
Каждая отобранная фракция характеризуется величиной относительного отбора (E = G/F) и температурами начала и конца выкипания (определяются по значениям температуры верха колонны). Естественно, температура конца кипения произвольной фракции является температурой начала кипения следующей сопряженной фракции. Отбор фракций измеряется в массовых или объемных долях, которые впоследствии с использованием специальных методик (программ) достаточно просто пересчитываются в мольные доли, которые и используются в расчетных процедурах. Одновременно для каждой фракции лабораторными методами могут определяться их основные характерные свойства (плотность, показатель преломления). Состав газовой фазы, отобранной в баллон 11, определяется отдельно, например, хроматографическим методом, а её выход определяют по изменению уровня рассола в баллоне. По полученным данным строится кривая ИТК в координатах: нарастающая доля отгона отдельных фракций (E) – температуры начала и конца кипения каждой фракции, причем газовая часть разгонки присоединяется к началу кривой ИТК в виде ступенчатой линии.
|
1.1.3. Соотношения между кривыми ОИ и ИТК
Кривые ОИ и ИТК конечно характеризуются внутренним сродством, поскольку обе кривые получены методом разгонки. Действительно при исключении из схемы аппарата АРН-2 ректификационной колонки 12 (см. рис. 1.2) схема прибора становится идентичной схеме аппарата ОИ. В то же время наличие ректификационной колонки, обладающей высокой разделительной способностью, приводит к тому, что дистиллят, отбираемый в приемник 5, существенно обогащается легкими фракциями в сравнении с составом паров, поступающих в колонку. При этом температура верха колонки (используется при построении кривой ИТК) окажется ниже температуры кипения смеси в кубе аппарата (используется при построении кривой ОИ). В идеале (бесконечно высокая разделительная способность колонки и бесконечно большое флегмовое число) при пренебрежении наличием в исследуемой смеси азеотропных соединений в колонке можно было бы обеспечить последовательный отбор компонентов в соответствии с нарастанием их температур кипения (теоретическая кривая ИТК).
а)
б)
Рис. 1.3. Сопоставление теоретической кривой ИТК (ряд 2) с лабораторными кривыми ИТК (ряд 3) и ОИ (ряд 1) для бинарной смеси
н. пентан – н. гексан (а) и четырехкомпонентной смеси
н. пентан – н. гексан – н. гептан – н. октан (б)
Для иллюстрации связи между кривыми ОИ и ИТК рассмотрим эти кривые на примере бинарной равномольной смеси н. пентан – н. гексан и четырехкомпонентной равномольной смеси н. пентан – н. гексан – н. гептан – н. октан (рис. 1.3). Лабораторные кривые ОИ и ИТК получены расчетным путем моделированием соответствующих лабораторных аппаратов.
Как видим, с увеличением числа компонентов смеси и с уменьшением относительных количеств каждого отдельного компонента лабораторная и теоретическая кривые ИТК сближаются. При переходе к непрерывной смеси (нефть и нефтепродукты), в которой число компонентов является чрезвычайно большим, различие между теоретической и лабораторной кривыми ИТК должно становиться пренебрежимо малым.
К настоящему времени разработано большое количество сравнительно простых и вместе с тем достаточно надежных методов пересчета кривых ОИ в кривые ИТК и наоборот. Наиболее часто для пересчета кривых используют связь между температурами выкипания 50% фракций (обычно вносят допущение об их совпадении для кривых ОИ и ИТК) с последующим пересчетом углов наклона исходной кривой на отдельных её участках. В большинство УМП (Chem Cad, HYSYS, Pro2) включены специальные процедуры взаимного пересчета кривых ОИ и ИТК, что существенно облегчает работу проектировщика. Следует отметить, что получение экспериментальных кривых разгонки для нефти и мазута во всем диапазоне изменения доли отгона (от 0 до 1) практически невозможно из-за сложности разгонки тяжелых остатков. В расчетных методиках, используемых в УМП, этот недостаток преодолен. На рис. 1.4 приведен результат пересчета экспериментальной кривой ОИ мазута (плотность при 20 оС составляет 935 кг/м3, эксперимент проведен до доли отгона E=0,7; T=547оС) в кривую ИТК, выполненный в УМП Chem Cad.
|
Используя кривую ИТК, можно провести разбивку смеси на целевые фракции, выделяемые в соответствующих колоннах. Так, на рис. 1.5 представлена разбивка мазута, разделяемого в вакуумной колонне установки АВТ на 5 целевых фракций. Представленная разбивка соответствует потенциальному содержанию фракции в сырье и характеризуется пределами выкипания (начала и конца кипения). Из за неизбежного наложения фракций друг на друга, которое будет иметь место при последующем разделении мазута в реальной ректификационной колонне, фактические кривые ИТК выделенных фракций будут отличаться от представленных на рис. 1.5. Начало кипения каждой фракции будет располагаться ниже, чем на рис. 1.5 (из за наложения соседней более легкой фракции), а конец кипения – выше (из за наложения соседней более тяжелой фракции).
Рис. 1.4. Пересчет кривой ОИ в кривую ИТК: ряд 1 – кривая ИТК,
ряд 2 – кривая ОИ
Для последующего расчета процессов разделения разбивка смеси на указанные пять фракций представляется очень грубой. Для повышения точности расчетов исходная кривая ИТК разбивается на значительно большее количество узких фракций. Целесообразно при этом использовать неравномерную разбивку кривой: на границах предполагаемого выделения целевых фракций использовать более узкие фракции (например, 5-градусные), а в средней области целевых фракций – более широкие (например, 15-градусные). Каждая узкая фракция представляется в дальнейшем в виде псевдокомпонента, который характеризуется своими специфическими свойствами, а целевая фракция будет состоять из смеси отдельных псевдокомпонентов. При таком подходе непрерывная смесь преобразуется в многокомпонентную, что дает возможность применения при проведении расчетов разделения (ректификации) хорошо разработанной теории многокомпонентной ректификации.
Рис. 1.5. Разбивка непрерывной смеси на фракции, которые предполагается выделять в вакуумной колонне: I – фракция вакуумного газойля; II, III и IV – узкие фракции масляных дистиллятов; V – гудрон
Характерные кривые разгонки нефти и отдельных нефтепродуктов представлены на рис. 1.6.
Рис. 1.6. Кривые стандартной разгонки бензина и нефти (ОИ и ИТК)
На рис. 1.6: 1 – кривая стандартной разгонки бензина (ОИ) атмосферной колонны; 2◦–◦кривая ИТК бензина атмосферной
колонны; 3 – кривая ИТК нефти (ордината справа); 4 – кривая ИТК прямогонного бензина; 5 – кривая стандартной разгонки (ОИ) фр. 118–212 °С; 6 – кривая стандартной разгонки (ИТК) фр. 118 – 212 °С.
1.2. Характеризация физико-химических свойств (ФХС) узких нефтяных фракций (псевдокомпонентов)
При расчете процессов ректификации многокомпонентных смесей (МКС) необходимо использовать физико-химические и термодинамические свойства всех компонентов, составляющих разделяемую МКС. Поскольку в рассматриваемом случае декомпозиция исходной непрерывной смеси на псевдокомпоненты носит достаточно условный характер, процедура расчета физико-химических свойств отдельных псевдокомпонентов приобретает особое значение. Известно [2], что любое химическое вещество обладает совокупностью характеристических констант, причем значения характеристических констант зависят от химического строения молекул вещества. Это положение может быть распространено и на псевдокомпоненты, особенно если значения характеристических констант определены экспериментально.
В качестве основной и минимально необходимой характеристики псевдокомпонента принята его среднеарифметическая (между началом и концом выкипания фракции) температура кипения. Однако эта температура не в полной мере характеризует псевдокомпонент, поскольку она не учитывает особенности состава нефтей различного типа (различных месторождений). Для более точной оценки ФХС псевдокомпонентов в принципе необходима информация об углеводородном составе фракций. Эта информация в косвенной форме в кривых ОИ и ИТК содержится. Более того, по закону сохранения масс усредненные (среднеинтегральные) значения псевдохарактеристических констант и вероятного углеводородного состава для фракций, выделенных по сравниваемым кривым при одинаковых расходных пределах выкипания, должны совпадать (за исключением их температурных пределов выкипания) [2]. Поэтому для оценки углеводородного состава моторных топлив вполне допустимо использование кривой ОИ – как более простой и удобной при экспериментальном определении. Однако при расчете процессов разделения (прежде всего ректификации) необходимо использовать только кривую ИТК.
Для расчетов в качестве псевдохарактеристических констант всех компонентов (псевдокомпонентов) МКС используются стандартные свойства (температуры кипения, температуры фазовых переходов, давления насыщенных паров, плотности газовой и жидкой фаз при стандартных условиях, показатели преломления, вязкости, энтальпий и др.), а также критические свойства. Эти константы характеризуют химическую индивидуальность компонента, т.е. представляют «химический паспорт» вещества. Характеристические свойства являются функциями специфических химических параметров вещества: молярной массы и структуры молекулы вещества [2]:
Фij=f(Мi, химическая формула). | (1.1) |
Из (1.1) следует, что все стандартные свойства оказываются взаимосвязанными и могут быть выражены друг через друга. Так молярная масса какого либо углеводорода (псевдокомпонента) может быть выражена в виде функции от его стандартных свойств: температуры кипения, плотности, показателя преломления и прочих свойств, а также от комбинации этих свойств. В качестве примера можно привести формулы Б. П. Войнова [3], Крега [4] и Мамедова [4] для расчета молекулярной массы углеводородов:
![]() | (1.2) |
![]() | (1.3) |
![]() | (1.4) |
Поэтому количество вариантов расчета ТФС псевдокомпонентов оказывается достаточно большим, что в определенной мере затрудняет их практическое использование. Наиболее подробно принципы и методы расчета всех основных стандартных свойств для элементов углеводородных систем изложены в [2]. Для расчета ФХС широких нефтяных фракций, состоящих из нескольких псевдокомпонентов, используется правило аддитивности, т.е. вклад каждой узкой фракции в свойства более широкой фракции определяется относительной концентрацией узкой фракции в более широкой.
В УМП процедуры расчета ФХС для непрерывных смесей автоматизированы: пользователь в соответствии с принятой температурной разбивкой кривой ИТК на псевдокомпоненты задает пределы выкипания отдельных псевдокомпонентов (отдельных узких фракций), после чего заполняет спецификацию для каждого выбранного псевдокомпонента, задавая его характеристические свойства, известные пользователю. В качестве минимально необходимой информации, как уже указывалось, должна быть задана средняя температура кипения псевдокомпонента, а в качестве дополнительной задаются свойства (плотность, показатель преломления и т.д.), известные пользователю. Чем более полно определена эта информация, тем точнее будет охарактеризован каждый псевдокомпонент, а значит, и точнее будут результаты последующего моделирования. Для примера на рис. 1.7 приведены кривые распределения характеристических свойств (tср, p, n) для прямогонного гидроочищенного бензина [2].
Рис. 1.7. Кривые распределения температуры кипения (tср), плотности (p)
и показателя преломления (n) фракции прямогонного гидроочищенного бензина
В соответствии с принятым условием достаточно плавного изменения характеристических свойств при изменении температуры кипения отдельных компонентов (число индивидуальных компонентов очень велико) зависимости всех свойств от доли отгона вещества (или от температуры отгона) должны быть также непрерывными.
На основе данной информации могут быть рассчитаны все основные свойства (Tкр, Pкр, Zкр, энтальпийные характеристики) как отдельных псевдокомпонентов, так и среднеинтегральные значения этих свойств для фракции в целом, а также определены вероятные брутто-формулы гипотетических псевдокомпонентов [2].
По сути такой же подход используется и при взаимном пересчете кривых ОИ и ИТК. При этом наличие даже неполной информации (только отдельных свойств для отдельных фракций даже в ограниченном диапазоне изменения доли отгона) позволяет заметно повысить адекватность обобщающей информации. Так, для примера, приведенного на рис. 1.4, учет только одного свойства по фракции в целом (плотность мазута) заметно уточняет вид конечной характеристики (кривая ИТК).
![]() |
2. ТЕХНОЛОГИЧЕСКОЕ ОФОРМЛЕНИЕ ПРОЦЕССА ПЕРВИЧНОЙ ПЕРЕРАБОТКИ НЕФТИ
Технология первичной переработки нефти основана на разделении нефти методом ректификации на узкие нефтяные фракции и определяется направлениями использования фракций, выделяемых на установках АВТ. Различают топливные (выделяемые фракции предназначены преимущественно для производства моторных топлив), масляные (предусматривается выделение узких масляных фракций) и топливно – масляные варианты работы этих установок. Поэтому отечественные установки переработки нефти (АТ и АВТ) характеризуются большим разнообразием используемых схем ректификации в зависимости от ассортимента выпускаемых фракций. Однако во всех случаях выдерживаются несколько основных принципов:
· Процесс первичной ректификации нефти проводится в сложных колоннах, характеризующихся наличием нескольких зон ввода питания и отбора целевых продуктов.
· В процессе ректификации для обеспечения теплоподвода в систему и снижения парциального давления нефтяных паров широко используется острое паровое орошение (в систему вводится перегретый водяной пар).
· Для промежуточной конденсации паровой фазы по высоте колонны используются выносные холодные циркуляционные орошения.
· В схемах ректификации используются выносные отпарные колонны (стриппинг – секции), что приводит к появлению в системе дополнительных рецикловых связей.
· Сырьевое обеспечение производств зачастую характеризуется наличием нескольких поставщиков нефти, а значит и колебаниями во времени фракционного состава исходного сырья.
· Требования к качеству выделяемых фракций, в первую очередь в части снижения эффекта наложения соседних фракций друг на друга, постоянно повышаются.
Указанные обстоятельства существенно усложняют как схему реализации процесса, так и его конструктивное оформление. Технология разделения (схема) и конструктивное оформление оказывают существенное влияние друг на друга и должны рассматриваться совместно. Поэтому расчетное исследование процесса и особенно процедура его оптимизации становится чрезвычайно сложной задачей, которую невозможно решать без использования УМП.
|
|
Папиллярные узоры пальцев рук - маркер спортивных способностей: дерматоглифические признаки формируются на 3-5 месяце беременности, не изменяются в течение жизни...
Археология об основании Рима: Новые раскопки проясняют и такой острый дискуссионный вопрос, как дата самого возникновения Рима...
Механическое удерживание земляных масс: Механическое удерживание земляных масс на склоне обеспечивают контрфорсными сооружениями различных конструкций...
Биохимия спиртового брожения: Основу технологии получения пива составляет спиртовое брожение, - при котором сахар превращается...
© cyberpedia.su 2017-2024 - Не является автором материалов. Исключительное право сохранено за автором текста.
Если вы не хотите, чтобы данный материал был у нас на сайте, перейдите по ссылке: Нарушение авторских прав. Мы поможем в написании вашей работы!