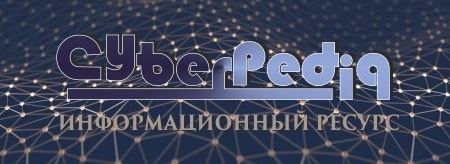
Семя – орган полового размножения и расселения растений: наружи у семян имеется плотный покров – кожура...
Состав сооружений: решетки и песколовки: Решетки – это первое устройство в схеме очистных сооружений. Они представляют...
Топ:
Отражение на счетах бухгалтерского учета процесса приобретения: Процесс заготовления представляет систему экономических событий, включающих приобретение организацией у поставщиков сырья...
Устройство и оснащение процедурного кабинета: Решающая роль в обеспечении правильного лечения пациентов отводится процедурной медсестре...
Определение места расположения распределительного центра: Фирма реализует продукцию на рынках сбыта и имеет постоянных поставщиков в разных регионах. Увеличение объема продаж...
Интересное:
Лечение прогрессирующих форм рака: Одним из наиболее важных достижений экспериментальной химиотерапии опухолей, начатой в 60-х и реализованной в 70-х годах, является...
Как мы говорим и как мы слушаем: общение можно сравнить с огромным зонтиком, под которым скрыто все...
Инженерная защита территорий, зданий и сооружений от опасных геологических процессов: Изучение оползневых явлений, оценка устойчивости склонов и проектирование противооползневых сооружений — актуальнейшие задачи, стоящие перед отечественными...
Дисциплины:
![]() |
![]() |
5.00
из
|
Заказать работу |
Содержание книги
Поиск на нашем сайте
|
|
Э. В. Осипов, Э. Ш. Теляков, М. А. Закиров
КОНСТРУКТИВНОЕ ОФОРМЛЕНИЕ ПРОЦЕССОВ ПЕРВИЧНОЙ ПЕРЕРАБОТКИ НЕФТИ
Учебное пособие
Министерство образования и науки России
Федеральное государственное бюджетное образовательное учреждение высшего образования
«Казанский национальный исследовательский технологический университет»
Э. В. Осипов, Э. Ш. Теляков, М. А. Закиров
КОНСТРУКТИВНОЕ ОФОРМЛЕНИЕ ПРОЦЕССОВ ПЕРВИЧНОЙ ПЕРЕРАБОТКИ НЕФТИ
Учебное пособие
Казань
Издательство КНИТУ
2017
УДК 66.02 (075.8)
ББК
Осипов Э.В. Конструктивное оформление процессов переработки нефти: Учебное пособие /Э. В. Осипов, Э. Ш. Теляков, М. А. Закиров; М-во образ. науки России, Казан. нац. исслед. технол. ун-т. – Казань: Изд-во КНИТУ, 2017. – 130 с.
Рассмотрено технологическое и аппаратурное оформление ректификационных блоков установок первичной переработки нефти.
Предназначено для курсового и дипломного проектирования бакалавров по направлениям подготовки 15.03.02 «Технологические машины и оборудование» и 18.03.02 «Энерго - и ресурсосберегающие процессы в химической технологии, нефтехимии и биотехнологии» очной и заочной форм обучения, а также магистрантов, обучающихся по направлению 15.04.02 «Технологические машины и оборудование».
Подготовлено на кафедре машин и аппаратов химических производств.
Печатается по решению редакционно-издательского совета Казанского национального исследовательского технологического университета.
Рецензенты:
Зав. каф. «Технология воды и топлива» КГЭУ д-р техн. наук, проф. А.Г. Лаптев
Зав. лаборатории технологии нефтегазопереработки ОАО «ВНИИУС» д-р техн. наук, ст. науч. сотр. Р.Г. Шакирзянов
|
ISBN
© Осипов Э. В., Теляков Э. Ш., Закиров М.А., 2017
© Казанский национальный исследовательский технологический ун-т., 2017
Содержание
УСЛОВНЫЕ ОБОЗНАЧЕНИЯ | ||
ВВЕДЕНИЕ | ||
1. | ХАРАКТЕРИСТИКА СЫРЬЯ УСТАНОВОК АВТ И МЕТОДЫ ПРЕДСТАВЛЕНИЯ ФРАКЦИОННОГО СОСТАВА НЕФТИ И НЕФТЕПРОДУКТОВ | |
1.1. | Фракционный состав нефти и нефтепродуктов | |
1.1.1. | Кривая однократного испарения (ОИ) | |
1.1.2. | Кривая истинных температур кипения (ИТК) | |
1.1.3. | Соотношения между кривыми ОИ и ИТК | |
1.2. | Характеризация физико-химических свойств (ФХС) узких нефтяных фракций (псевдокомпонентов) | |
2. | ТЕХНОЛОГИЧЕСКОЕ ОФОРМЛЕНИЕ ПРОЦЕССА ПЕРВИЧНОЙ ПЕРЕРАБОТКИ НЕФТИ | |
2.1. | Атмосферный блок установки АВТ | |
2.2. | Вакуумный блок установки АВТ | |
3. | АППАРАТУРНОЕ ОФОРМЛЕНИЕ ПРОЦЕССА ПЕРВИЧНОЙ ПЕРЕРАБОТКИ НЕФТИ | |
3.1. | Тарельчатые контактные устройства | |
3.2. | Насадочные контактные устройства | |
3.2.1. | Регулярные насадки | |
3.2.2. | Распределители жидкости и устройства для сбора и отвода жидкости, стекающей из пакета насадки | |
3.2.3. | Перекрестноточные насадки (ПТН) | |
3.2.4. | Сопоставление контактных устройств | |
4. | РАСЧЕТ РЕКТИФИКАЦИОННЫХ БЛОКОВ УСТАНОВОК АВТ | |
4.1. | Технологический расчет ректификационных колонн установок АТ-АВТ | |
4.1.1. | Назначение величин отбора целевых фракций и распределение тарелок по секциям сложной колонны. | |
4.1.2. | Назначение профиля давлений в РК |
4.1.3. | Назначение количеств подводимого и отводимого тепла | |
4.2. | Конструкционный расчет элементов ректификационного оборудования установок АТ-АВТ | |
4.2.1. | Конструкционный расчет тарельчатых РК | |
4.2.1.1 | Выбор типа и конструкции КУ | |
4.2.1.2. | Расчет основных размеров РК и КУ | |
4.2.1.3. | Гидравлический расчет КУ | |
4.2.1.4. | Проверка работоспособности КУ | |
4.2.1.5. | Расчет эффективности КУ | |
4.2.2. | Конструкционный расчет насадочных РК | |
4.2.2.1 | Расчет диаметра аппарата | |
4.2.2.2 | Массообменная эффективность и гидравлическое сопротивление насадок | |
5. | ВАКУУМСОЗДАЮЩИЕ СИСТЕМЫ | |
5.1. | Предварительный конденсатор | |
5.2. | ВСС на базе пароэжекторного вакуумного насоса (ПЭН) | |
5.3. | Низконапорные гидроциркуляционные ВСС | |
5.4. | ВСС на базе жидкостного эжектора (вакуумные гидроциркуляционные агрегаты - ВГЦА) | |
5.5. | ВСС на базе жидкостно-кольцевого вакуумного насоса (ЖКВН) | |
ЗАКЛЮЧЕНИЕ | ||
ТЕСТОВЫЕ ВОПРОСЫ ДЛЯ САМОКОНТРОЛЯ | ||
ОТВЕТЫ НА ТЕСТОВЫЕ ВОПРОСЫ ДЛЯ САМОКОНТРОЛЯ | ||
ЛИТЕРАТУРА |
УСЛОВНЫЕ ОБОЗНАЧЕНИЯ
|
Fф | - F – фактор (фактор нагрузки), Па0,5 |
G | - расход парового потока, м3/ч, кг-моль/ч |
GМ | - массовый расход парового потока, кг/ч |
Hн Hк | -·энтальпии потока циркуляционного орошения соответственно на выходе из секции колонны и на возврате в колонну после охлаждения, кДж/кг-моль, кДж/кг. |
H/ | - эквивалентный уровень светлой (невспененной) жидкости в переливном устройстве, мм |
Hм,т | - высота межтарельчатого расстояния, мм |
hпор | - высота сливного порога, м |
hвсп | - высота вспененного слоя жидкости на тарелке, мм |
hп | - высота сливного порога, мм |
hс | - высота сепарационного пространства, мм |
Dh | -·превышение уровня жидкости над сливной планкой (подпор), мм |
Dhж.п. | -·гидравлическое сопротивление движению жидкости в переливе, мм |
∆hэкв. | - ВЭТТ (высота эквивалентная теоретической тарелке), м |
L | - расход жидкостного потока, м3/ч, кг-моль/ч |
LМ | - массовый расход жидкостного потока, кг/ч |
LH | - удельная плотность орошения (на единицу длины сливной перегородки) по жидкости, м3/(м ч) |
LS | -·удельная плотность орошения (на единицу площади насадки) по жидкости, м3/(м2 ч) |
lж | - длина пути жидкости на тарелке, м |
lп | - длина сливного порога, м |
M | - молекулярная масса, кг/кг-моль. |
Pв | - давление верха РК, Па. |
Pк | - давление в кубе РК, Па. |
Pс | - давление в зоне ввода сырья в РК, Па. |
∆Рк.у. | - гидравлическое сопротивление КУ, Па. |
∆Рпол. | -·полезная (расходуемая на реализацию процесса массообмена) составляющая гидравлического сопротивления КУ. |
∆Рж.п. | - сопротивление движению жидкости в переливе, Па |
ΔPж | -·составляющая общего гидравлического сопротивления, затрачиваемая на преодоление сопротивления слоя жидкости на тарелке, Па |
ΔPсух | -·составляющая общего гидравлического сопротивления, затрачиваемая на преодоление сопротивления сухой тарелки, Па |
![]() | - гидравлическое сопротивление сухой тарелки, Па |
∆Pуд. | -·удельное (отнесенное к единице длины) гидравлическое сопротивление насадки, Па/м |
∆Pσ | -·потеря напора на преодоление сил поверхностного натяжения, Па |
N | - число КУ (тарелок) в вакуумной колонне, шт. |
Nт.т. | - число теоретических тарелок в колонне (секции колонны), шт |
Nр.т. | - число реальных тарелок в колонне (секции колонны), шт |
П | - суммарная длина периметра слива жидкости на тарелке, м |
S | -·полное сечение тарелки, м2 |
S1 | - рабочая площадь тарелки, м2 |
S2 | - сечение тарелки, занятое переливными устройствами, м2 |
Sсв | - свободное сечение тарелки, м2 |
SG | - сечение насадки, открытое для прохода пара, м2 |
SL | - сечение насадки, открытое для прохода жидкости; м2 |
Sкол | - площадь парового патрубка (колпачковая тарелка), м2 |
Sпатр | - площадь зазора между колпачком и патрубком, м2 |
tср | - средняя температура кипения фракции, оС. |
u | - скорость жидкости в переливном устройстве, м/с |
uдоп | - допустимая скорость жидкости в переливном устройстве, м/с |
Qц.о. | - величина теплосъема холодным орошением, кВт/м3. |
Y | - длина вылета струи в сливном устройстве, мм |
X | - максимальная ширина сливного кармана, мм |
![]() | - плотность, кг/м3. |
![]() | - плотность при температуре 15 оС, отнесенная к плотности воды при температуре 4 оС, кг/м3. |
![]() | - скорость пара в колонне, м/с. |
![]() | - максимально допустимая скорость пара в колонне, м/с. |
![]() | - минимально допустимая скорость пара в колонне, м/с. |
![]() | - допустимая скорость пара в колонне, м/с. |
![]() | - скорость пара в свободном сечении тарелки, м/с |
![]() | - коэффициент гидравлического сопротивления сухой тарелки |
eэфф. | -·относительная эффективная рабочая площадь тарелки (площадь, непосредственно занятая под барботажные элементы), м2/м2 |
mж | - динамическая вязкость жидкой фазы, Па·с |
![]() | -·коэффициент (показатель) преломления света при температуре 20 оС. |
![]() | - градиент уровня жидкости на тарелке, мм |
![]() | - средний градиент уровня жидкости на тарелке, мм |
![]() | - коэффициент сопротивления сухой тарелки |
![]() | - эффективность контактного устройства «по Мерфри» |
![]() | - эффективность контактного устройства «по Гаузену» |
![]() | - эффективность колонны |
КРИТЕРИИ ПОДОБИЯ
|
|
Re – Рейнольдса,
Sh – Шервуда,
Sc – Шмидта,
We – Вебера.
Сокращения, использованные в тексте:
АВТ – атмосферно–вакуумная трубчатка (ректификационная установка).
АТ – атмосферная трубчатка (ректификационная установка) или атмосферный блок установки АВТ.
ВСС - вакуумсоздающая система.
ВЭТТ – высота насадки, эквивалентная теоретической тарелке.
ИТК – кривая истинных температур кипения (ГОСТ 11011-85).
КУ – контактные устройства (массообменные тарелки).
МКС – многокомпонентные смеси.
ОИ – кривая однократного испарения (ГОСТ 2084-77).
ПТН – перекрестноточная насадка.
ПЭН – пароэжекторный насос.
ПГС – парогазовая смесь.
РК – ректификационная колонна.
ТЗ – техническое задание на проектирование.
ТФС – теплофизические свойства.
ТЭП – технико–экономические показатели.
УМП – универсальная моделирующая программа (Chem Cad, HYSYS, Pro-2 и т.д.).
ЭЛОУ◦–◦блок подготовки нефти (электрообезвоживание и обессоливание нефти).
Введение
Современный этап развития нефтегазоперерабатывающей и нефтехимической отраслей промышленности характеризуется значительным ростом единичной мощности технологических установок, увеличением ассортимента выпускаемой продукции и ужесточением требований к её качеству. Существенно возрастает стоимость энергетических ресурсов, что требует совершенствования технологии переработки нефти, аппаратурного оформления технологических процессов и систем управления производством. Все эти задачи должны решаться уже на стадии проектирования производственного процесса взаимосвязано и с использованием оптимизационных процедур, что предполагает проведение огромного числа расчетов.
Головными установками нефтеперерабатывающих заводов (НПЗ) являются блоки первичной переработки нефти – атмосферно-вакуумные трубчатки (АВТ). В названии установки сохранилось слово «трубчатка», подчеркивающее наличие в составе установки трубчатой печи, используемой для нагрева исходной нефти (сырья установки). Сам процесс разделения нефти основан на широком использовании процесса ректификации, предназначенном для разделения сырья на узкие нефтяные фракции. Данные фракции, прежде всего фракции моторных топлив, в настоящее время не являются товарными продуктами НПЗ, поскольку их качество не удовлетворяют современным требования потребителей, и нуждаются в дополнительной переработке, в том числе и химическими методами. Однако во многом качество конечной товарной продукции закладывается именно на установках АВТ.
|
Технология ректификации нефти основана на использовании «сложных» колонн, под которыми понимаются колоны, имеющие более одной точек ввода исходного сырья и (или) несколько точек отбора продуктовых потоков, а также несколько уровней подвода (отвода) тепловых потоков.
Сырье установки – нефть - также характеризуется весьма сложным составом: количество отдельных составляющих нефть углеводородов исчисляется десятками тысяч. Количества отдельных компонентов носят при этом дифференциальный характер, что не позволяет характеризовать эту смесь углеводородов как многокомпонентную. Поэтому нефть и отдельные её части (фракции) выделены в отдельный класс смесей, которые получили название «непрерывных». Состав этих смесей выражают через кривые разгонки, в процессе которой отгоняемые фракции обогащаются легкокипящими фракциями. Кривые разгонки представляются через кривые ОИ (однократного испарения) и ИТК (истинных температур кипения), которые поддаются взаимному пересчету. Следует также отметить, что тяжелые углеводороды, содержащиеся в нефти (температура кипения выше 350оС), при нагреве выше 350оС начинают разлагаться с заметной скоростью. Поэтому для исключения процесса термодеструкции температура допустимого нагрева нефти на установках АВТ не должна превышать (350-410) оС.
Отмеченная сложность технологии и особенности представления состава нефти определяют и сложность расчета самого процесса разделения. Можно утверждать, что более или менее точный расчет процесса в соответствии с современными требованиями нельзя реализовать без применения современных программных продуктов. К ним в первую очередь относятся так называемые универсальные моделирующие программы (УМП), предназначенные для моделирования сложных химико технологических систем (СХТС). УМП имеют модульную структуру и состоят из системного и функциональных наполнений, представляющих собой средства и объекты расчета, включают в себя разнообразные базы данных, а также характеризуются развитым графическим интерфейсом пользователя. Последнее обстоятельство обеспечивает относительную простоту использования УМП специалистам с инженерным образованием. При использовании УМП имеется возможность расчета как параметров технологического режима работы всех составных блоков СХТС, так и основных характеристик и размеров аппаратурного оформления блоков, что создает надежную базу для проведения последующих оптимизационных расчетов для обоснованного выбора проектного решения.
![]() |
В химическом отношении нефть – взаиморастворимая смесь газообразных, жидких и даже твердых углеводородов с примесями гетероорганических соединения серы, азота, кислорода и других элементов. В зависимости от состава нефть имеет цвет от буро-коричневого до черного. Элементарный состав нефти различен для разных типов и для разных месторождений. В среднем он может быть охарактеризован следующими цифрами: углерод – (82,5 – 87) %, водород – (11,5 – 14,5) %, кислород – (0,1 – 0,35) %, азот – до 1,8 %, сера – до 10 % [1].
Углеводороды в нефти представлены соединениями различных классов. В основном это парафиновые углеводороды (алканы) – CnH2n+2; нафтеновые углеводороды (цикланы) – CnH2n; ароматические соединения – углеводороды, содержащие в своем составе разнообразные гомологи бензола, а так же гибридные углеводородные соединения.
С ростом в молекуле углеводорода числа атомов углерода резко нарастает эффект изомеризации углеводородных соединений. Поэтому общее количество углеводородных соединений в нефти становится огромным: их общее количество измеряется десятками тысяч. В то же время основным процессом, используемым в процессе нефтепереработки, являются ректификация. В этом процессе обеспечивается разделение групп компонентов в соответствии с температурными пределами их выкипания. Эти факты обусловили то обстоятельство, что основной и наиболее широко используемой характеристикой состава нефти стал фракционный состав, определяемый методами лабораторной перегонки и ректификации.
АППАРАТУРНОЕ ОФОРМЛЕНИЕ ПРОЦЕССА ПЕРВИЧНОЙ ПЕРЕРАБОТКИ НЕФТИ
Массо- теплообмен между противоточно движущимися неравновесными паровой и жидкой фазами в ректификационных и абсорбционных колоннах осуществляется на контактных устройствах (КУ), которые часто называются “тарелками”. В ректификационных колоннах поток парового орошения создается нагревательными элементами (печь, ввод перегретого водяного пара), а жидкого – конденсационными устройствами (холодильники – конденсаторы, холодные циркуляционные орошения). В результате взаимодействия между паровой и жидкой фазами на КУ в соответствии с законами термодинамического парожидкостного равновесия паровая фаза обогащается легкокипящими, а жидкая – тяжелокипящими компонентами. Поэтому именно КУ и определяют в значительной мере общую эффективность процесса разделения.
Для нефтяных колонн вообще и для колонн АВТ, в частности, можно выделить ряд присущих им характерных особенностей:
· очень высокая производительность по сырью (до 1000 м3/ч для атмосферной колонны);
· подвод тепла в разделительную систему осуществляется огневым нагревом сырья в трубчатой печи (основная и вакуумная колонны АВТ), вводом перегретого водяного пара (практически все колонны) и циркуляцией «горячей струи» (отбензиневающая колонна АТ);
· последнее обстоятельство предполагает применение специальных сепарационных зон для разделения паровой и жидкой фаз;
· в схеме ректификации присутствуют выносные отпарные секции, а также циркуляционные орошения, что предполагает возможность организации на КУ боковых отборов жидкой фазы и подводов как паровой, так и жидкой фаз в нескольких точках по высоте колонны.
Эти особенности должны учитываться при выборе конструкций контактных устройств в задачах проектирования блоков разделения нефти.
Клапанные тарелки
![]() | (4.22) |
S – образные тарелки
![]() | (4.23) |
Струйные тарелки
![]() | (4.24) |
Унос жидкости
На первом этапе оценки эффективности принятых проектных решений рекомендуется проверить величину уноса жидкости, которая будет складываться на КУ. Величину уноса жидкости с тарелки рекомендуется рассчитывать по обобщенному уравнению:
![]() | (4.27) |
где hб – глубина барботажного слоя, мм;. eэф.– относительная эффективная рабочая площадь тарелки, м2/м2; m – коэффициент, определяемый по уравнению:
![]() | (4.28) |
ψ и A – коэффициенты:
при Hм.т .< 400 мм A = 9,48·107; b = 4,36
при Hм.т .≥ 400 мм A = 0,159; b = 0,95
Для колпачковых тарелок глубина барботажа определяется из условия полного открытия прорезей (hб ≥ 52 мм), для клапанных и ситчатых тарелок может приниматься высота сливной перегородки. Относительная эффективная рабочая площадь тарелки принимается как отношение S1/ S, а коэффициент y - в зависимости от скорости пара по данным, приведенным в табл. 4.6:
Таблица 4.6
Относительная эффективная рабочая площадь
Тип тарелки | При ![]() | При ![]() |
Колпачковая | 0,4 | 0,6 |
С S-образными элементами | 0,3 | 0,6 |
Клапанные | 0,6 | 0,8 |
Ситчатые | 0,8 | 0,9 |
Показано [54], что при проектировании КУ в соответствии с вышеизложенной методикой величина уноса составляет (табл. 4.7)
Таблица 4.7
Величина уноса
Тип процесса | Величина e, кг/кг |
В колоннах, работающих под давлением | 0,01-0,015 |
В атмосферных колоннах | 0,03-0,06 |
В вакуумных колоннах. | 0,25-0,54 |
Как видим, проверку КУ на межтарельчатый унос жидкости применительно к установкам АВТ надо проводить только для колонн вакуумного блока.
Сепарационное пространство
Составляющая ΔPж общего гидравлического сопротивления позволяет провести оценку высоты вспененного слоя жидкости на тарелке (hвсп), которая должна учитываться при назначении межтарельчатого расстояния в секциях колонны:
![]() | (4.29) |
где k - коэффициент вспенивания жидкости. Для мало и средне пенящихся жидкостей k =4-5.
Очевидно, что для беспереливных тарелок условие сепарации должно обеспечиваться при выполнении условия . Высота сепарационного пространства может быть определена исходя из заданной величины допустимого уноса жидкости (например 5%)
![]() | (4.30) |
Высота hc при этом не должна быть меньше 100 мм, для колонн промышленного размера рекомендуется принимать величину hc равной 250-300 мм.
Для КУ с переливными устройствами активную роль в сепарации газожидкостного потока играют сами переливные устройства, поскольку газожидкостная пенная структура с тарелки сливается в приемный карман, в котором и обеспечивается сепарация этой структуры. Степень насыщения жидкости паровыми пузырьками настолько велика, что в расчеты приходится вводить поправки на газонасыщенность жидкости. В то же время гидрозатвор в переливном устройстве в основном обеспечивается слоем светлой (невспененной) жидкости в самом переливном устройстве:
![]() | (4.31) |
где DР- гидростатическое давление столба светлой жидкости в переливе; DР ж.п. - сопротивление движению жидкости в переливе.
Сопротивление движению жидкости в переливном устройстве определяется по уравнениям:
![]() | (4.32) |
![]() | (4.32а) |
где a – линейный размер наиболее узкого сечения перелива (м) - см. рис. 4.1, П – длина периметра слива, k – коэффициент. Для тарелок без затворной планки k = 190, с затворной планкой k = 190. Ширина наиболее узкого сечения перелива должна составлять при этом не менее 40 мм. Однако величина a при этомне должна быть намного больше 40 мм, так как в этом случае будет нарушаться равномерность распределения жидкости по длине сливной планки.
Уравнение (4.32а) может быть использовано и для решения обратной задачи: задавшись значением сопротивления (например мм) определить необходимую длину периметра слива.
Аналогичным образом оценивается и длительность пребывания жидкости в сливном устройстве. Для обеспечения нормального режима сепарации потока она должна составлять 3-5 с.
![]() | (4.33) |
Рассчитанное значение времени пребывания сравнивается затем с допустимым значением:
![]() | (4.34) |
Для средне- и сильнопенящихся жидкостей допустимое время пребывания увеличивается в 1,5-2 раза. Для колонн с клапанными тарелками следует использовать уравнение
![]() | (4.35) |
где коэффициент f, характеризующий вспениваемость жидкости в переливе, определяется по данным, представленным в табл. 4.8.
Таблица 4.8
Коэффициент f
Характеристика системы | Коэффициент f |
Жидкость невспенивающаяся (бензин, сжиженные газы) | 1.0 |
Интенсивность пенообразования: | |
- слабая (колонны ГФУ, вторичная перегонка бензинов) | 0,9 |
- средняя (ДТ, растворы аминов) | 0,85 |
- сильная (темные углеводороды, растворы гликолей) | 0,73 |
Струя жидкости, сливающейся с полотна тарелки в переливное устройство, во избежание вторичного пенообразования не должна ударяться о стенку колонны (см. рис. 4.1). Поэтому между максимальной шириной сливного кармана X и длиной вылета струи Y для сливающейся жидкости должно соблюдаться условие: Y < 0.6X. Величину Y определяют по уравнениям
![]() | (4.36) |
или
![]() | (4.36а) |
В уравнениях (4.36) и (4.36а) линейные размеры выражены в м, а LH – в м3/(м·с).
Таким образом, для обеспечения нормальной эффективной работы КУ без захлебывания необходимо выполнение трех условий: , Y < 0.6·X и
.
4.2.1.5. Расчет эффективности КУ
К настоящему времени разработана достаточно строгая и стройная теория кинетического расчета эффективности КУ [54], основанная на использовании обобщений для расчета коэффициентов массоотдачи, полученных для различных типов КУ и для различных гидродинамических условий проведения процесса. Обобщения получены в основном экспериментальными методами на горячих стендах промышленного размера, хотя в некоторых случаях использованы и теоретические исследования. Как правило, обобщения проводятся на основе теории подобия с использованием критериальных уравнений типа:
![]() | (4.37) |
![]() | (4.38) |
где ;
;
;
;
Г1 и Г2 – критерии геометрического подобия; m, n, k – коэффициенты; b – коэффициент массоотдачи, м/с; D – коэффициент диффузии, м2/с; n – кинематическая вязкость, м2/с; l – определяющий линейный размер, м; w – скорость, м/с; s – коэффициент поверхностного натяжения, Н/м; индексы ж и п характеризуют жидкую и паровую фазы соответственно.
Конкретный вид и коэффициенты критериальных уравнений в разных обобщениях, конечно, различаются, но в литературе имеются достаточно авторитетные рекомендации по их выбору [63]. При использовании соответствующих преобразований [54] уравнения массоотдачи преобразуются в уравнения массопередачи с получением уравнений для расчета эффективности (к.п.д.) тарелки по Мерфри (), определяемой по уравнению (3.9).
Однако при использовании УМП, без чего, как уже отмечалось, невозможно провести квалифицированный расчет колонного оборудования установок АТ-АВТ, непосредственное включение этой характеристики в расчетные процедуры не предусмотрено возможностями большинства УМП (расчет проводится по теоретическим тарелкам). Поэтому в данном случае для перехода к реальным тарелкам большее распространение получила более общая характеристика – к.п.д. колонны (или её отдельной секции):
![]() | (4.39) |
где Nт.т . и Nр.т . – соответственно число теоретических тарелок в расчетной модели и число реальных тарелок в спроектированном аппарате.
Можно отметить, что и
достаточно удовлетворительно соотносятся друг с другом, что в принципе позволяет использовать среднее значение эффективности по Мерфри, полученное для тарелок произвольной секции колонны, в качестве к.п.д. этой же секции. Известны [54] и эмпирические зависимости для расчета
, которые могут быть использованы в реальных расчетах для перехода от числа теоретических тарелок к реальным тарелкам:
![]() | (4.40) |
и/или ![]() | (4.41) |
где μж – вязкость жидкой фазы, Па·с; – относительная летучесть легкого ключевого компонента (ЛКК) по отношению к тяжелому ключевому компоненту (ТКК). Введение понятия ключевых компонентов обеспечивает применимость уравнения (4.40) и для многокомпонентных, в том числе и нефтяных смесей. Под ЛКК при этом понимается граничный компонент, переходящий в пределах секции в основном в верхний (дистиллятный) продукт, но который в заметном количестве присутствует и в нижнем продукте, а под ТКК – компонент, наоборот концентрирующийся в нижнем продукте, но присутствующий и в верхнем продукте.
Результаты конструкционного расчета позволяют полностью определить конструкцию РК и уточнить параметры технологического режима работы колонны, прежде всего профили давлений по высоте колонны, приближенные значения которых были приняты в начале технологического расчета. Если принятые значения существенно отличаются от расчетных, то проводится дополнительный расчет параметров технологического режима работы колонны, а при необходимости – и конструкционного расчета. Расчетные профили давлений, температур, концентраций и расходов потоков по высоте колонны используются в дальнейшем при разработке системы автоматизированного управления процессом.
4.2.2. Конструкционный расчет насадочных РК
4.2.2.1. Расчет диаметра аппарата
Теория аналитического расчета насадочных ректификационных колонн разрабатывалась в основном применительно к нерегулярным насадкам (кольца Рашига, седла Берли и др.) [54]. Однако нерегулярные насадки в промышленных колоннах вообще и в колоннах установок АТ-АВТ в особенности в настоящее время не используются. В то же время, как уже отмечалось в главе 3, на установках АВТ, особенно в вакуумных блоках, активно внедряются регулярные насадки. Модели аналитического расчета регулярных насадок, учитывающие особенности конструкций конкретных насадок (число их постоянно растет), развиты до настоящего времени слабо.
Схема конструкционного расчета насадочных РК в целом близка к схеме расчета тарельчатых аппаратов. Так, диаметр колонн для каждой секции РК в обоих случаях рассчитывается исходя из максимальной нагрузки на секцию колонны по пару (определена технологическим расчетом) и допустимой скорости пара, рассчитанной на полное сечение колонны, – уравнение (4.8). Для насадочных колонн в качестве ωдоп . принимается скорость, выраженная в долях от скорости, соответствующей эффекту «захлебывания» колонны (подвисания жидкости в слое насадки и нарушения противоточного режима движения фаз). Скорость захлебывания для любых типов насадок может быть определена по полуэмпирическому уравнению:
![]() | (4.42) |
где ![]() | (4.43) |
![]() | (4.44) |
![]() | (4.45) |
В этих уравнениях ωзахл – скорость захлебывания; a – удельная поверхность насадки. м2/м3; μж – вязкость жидкости, Па·с; A и B – коэффициенты, зависящие от типа насадки. Зависимости (4.42), выраженные в графической форме для разных типов насадок, приведены в литературе [54,64,65].
Для регулярных насадок, изготовленных из гофрированных листов, также может быть применено уравнение (4.42), в котором A=0,55; B=0,57 и a=1/l, где l – расстояние между соседними гофрированными листами. Однако пользоваться этими уравнениями рекомендуется с большой осторожностью, поскольку число типов и тем более типоразмеров регулярных насадок растет достаточно быстро.
Характеристики этих насадок, как уже отмечалось, представляются фирмами – изготовителями в виде зависимостей
![]() | (4.46) |
![]() | (4.47) |
где ∆hэкв. – ВЭТТ (высота эквивалентная теоретической тарелки), ∆Pуд. – это удельное (отнесенное к единице длины) гидравлическое сопротивление насадки. Данные зависимости являются достаточно надежными и могут быть использованы в расчетных целях. Для этой цели на графике выделяется область зависимостей, соответствующая условию эффективной работы насадки, в которой выделяется среднее значение Fф, и ра
|
|
Индивидуальные и групповые автопоилки: для животных. Схемы и конструкции...
Индивидуальные очистные сооружения: К классу индивидуальных очистных сооружений относят сооружения, пропускная способность которых...
Таксономические единицы (категории) растений: Каждая система классификации состоит из определённых соподчиненных друг другу...
Историки об Елизавете Петровне: Елизавета попала между двумя встречными культурными течениями, воспитывалась среди новых европейских веяний и преданий...
© cyberpedia.su 2017-2024 - Не является автором материалов. Исключительное право сохранено за автором текста.
Если вы не хотите, чтобы данный материал был у нас на сайте, перейдите по ссылке: Нарушение авторских прав. Мы поможем в написании вашей работы!