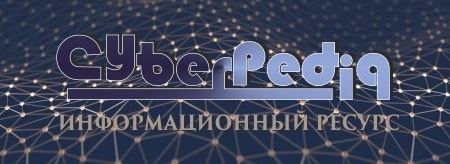
Поперечные профили набережных и береговой полосы: На городских территориях берегоукрепление проектируют с учетом технических и экономических требований, но особое значение придают эстетическим...
Двойное оплодотворение у цветковых растений: Оплодотворение - это процесс слияния мужской и женской половых клеток с образованием зиготы...
Топ:
Процедура выполнения команд. Рабочий цикл процессора: Функционирование процессора в основном состоит из повторяющихся рабочих циклов, каждый из которых соответствует...
Установка замедленного коксования: Чем выше температура и ниже давление, тем место разрыва углеродной цепи всё больше смещается к её концу и значительно возрастает...
Интересное:
Отражение на счетах бухгалтерского учета процесса приобретения: Процесс заготовления представляет систему экономических событий, включающих приобретение организацией у поставщиков сырья...
Распространение рака на другие отдаленные от желудка органы: Характерных симптомов рака желудка не существует. Выраженные симптомы появляются, когда опухоль...
Уполаживание и террасирование склонов: Если глубина оврага более 5 м необходимо устройство берм. Варианты использования оврагов для градостроительных целей...
Дисциплины:
![]() |
![]() |
5.00
из
|
Заказать работу |
Содержание книги
Поиск на нашем сайте
|
|
Кулачковые механизмы широко востребованы в современных машинах, несмотря на все преимущества сервоприводов. Профилируя кулачок или копир, можно обеспечить самые разные законы движения толкателя с заданными параметрами перемещения, скорости, ускорения, градиента. Пожалуй, главным недостатком этих механизмов, по сравнению с сервоприводами, является сложность изменения закона движения. В механизме надо перепрофилировать кулачок или копир, в сервоприводе та же задача решается программным путем.
В рассматриваемых механизмах кулачок или копир могут вращаться (рис. 6.6, а, б) или двигаться поступательно (рис. 6.6, в) или быть неподвижными (рис. 6.6, г). Толкатель может совершать вращательное или поступательное движение по одной или нескольким координатам.
Замыкание механизма может быть силовое (рис. 6.6, а, в), путем прижатия ролика толкателя к профилю кулачка или копира силами веса или пружинами (растяжения, сжатия, кручения, пневмопружинами) или геометрическое (рис. 6.6, б, г, д), когда ролик толкателя перемещается по профильному пазу или два ролика взаимодействуют с двухдисковым кулачком.
Рис. 6.6. Механизмы с кулачком и копиром:
а – дисковый вращающийся кулачок и качающийся толкатель с силовым замыканием; б – торцевой вращающийся кулачок и качающийся толкатель с геометрическим замыканием; в – движущийся поступательно копир (кулачок) и качающийся толкатель с силовым замыканием; г – неподвижный копир и движущийся поступательно по двум координатам толкатель с геометрическим замыканием; д – двухдисковый вращающийся кулачок и качающийся толкатель с геометрическим замыканием
Силовое замыкание обеспечивает безударную работу механизма, но сила замыкания увеличивает контактные напряжения в паре кулачок-ролик. Геометрическое замыкание свободно от этого недостатка, но здесь ролик катится то по одной, то по другой стороне паза, имеют место микроудары и проскальзывания ролика из-за реверса его вращения.
|
Типовой, простейший закон движения толкателя – закон постоянных ускорений (рис. 6.7).
Здесь ускорения минимальны, но имеют место «мягкие» удары-скачки ускорений, которые вызывают колебательные процессы в быстроходных механизмах. В этом случае, например в механизме газораспределения двигателя автомобиля, применяют сложные законы, описываемые многостепенными полиномами. При этом исключают все виды ударов и минимизируют скорости, ускорения и более высокие производные перемещения.
Рис. 6.7. Перемещение, скорость и ускорение толкателя:
а – график перемещения поступательно движущегося толкателя в функции времени, S = f (t); б – график скорости, V = f (t); в – график ускорения, a = f (t)
Рассмотрим прямой ход толкателя, который обозначим как ход подъема. При заданных (например, технологическим процессом) величинах хода толкателя S п и времени подъема t п = t p + t т, где t p – время разгона, t т – время торможения, и при равных ускорениях при разгоне и торможении имеем путь, пройденный при разгоне
, (6.19)
откуда ускорение при подъеме толкателя
(6.20)
Максимальная скорость при подъеме толкателя
(6.21)
Согласно геометрии кулачкового механизма (взаимное расположение опор, форма и размеры звеньев и т. п.), которая определяет передаточные отношения в механизме, и графику S = f (t) (рис. 6.7, а) вычисляются координаты профиля кулачка, составляется программа для станка с УЧПУ и изготавливается кулачок или копир.
При выборе геометрии механизма и профилировании кулачка важно обеспечить благоприятную, с высоким КПД, передачу сил от кулачка к толкателю, контактные давления в паре кулачок-ролик в пределах допускаемых давлений, требуемую жесткость механизма и точность движения толкателя. КПД механизма, в значительной степени, определяется углами давления γ в паре кулачок-ролик (рис. 6.8).
|
Рис. 6.8. Силы взаимодействия в паре кулачок-ролик
Угол давления - это угол между вектором силы F, действующей со стороны кулачка на ролик (сила F направлена по нормали к профилю кулачка) и вектором скорости V оси ролика. Силу F можно разложить на две составляющие. Полезной, движущей толкатель, составляющей является сила F дв. Чем меньше угол γ, тем больше F дв и меньше движущий момент M к на валу кулака при известном моменте сопротивления M т движению толкателя, следовательно, выше КПД. Угол γ при движении механизма не является величиной постоянной. Его максимум, обычно, стараются ограничить значением γmax = 20…40°.
Силы в звеньях кулачкового механизма и, соответственно, контактные давления, деформации, точность движения толкателя существенно зависят от размеров механизма. С одной стороны, стараются создать компактный, быстродействующий (с минимальными массами звеньев) механизм, с другой стороны, уменьшение размеров приводит к повышению сил в звеньях и кинематических парах. Создание оптимального кулачкового механизма - сложная многофакторная задача.
Кулачковые механизмы позволяют не только обеспечить привод какого-либо исполнительного звена (рабочего органа) машины, но и создать на их основе устройство управления машиной. Структура машины с таким устройством изображена на рис. 6.9.
Рис. 6.9. Структура машины с кулачковыми механизмами
Здесь все рабочие органы машины получают движение от кулачковых механизмов. Кулачки посажены на кулачковый вал и развернуты друг относительно друга так, чтобы обеспечивалась необходимая последовательность движения рабочих органов. При этом законы движения определяются профилем кулачков. Таким образом, можно реализовать алгоритм (циклограмму) управления всеми рабочими органами машины. Важно отметить, что управление ведется по фазе - углу поворота кулачкового вала, поэтому алгоритм управления не зависит от скорости работы машины или показаний датчиков положения рабочих органов, как в других, не механических системах управления. В отличие от других устройств, здесь всегда обеспечивается синхронность движения рабочих органов машины.
Основными недостатками устройств управления, построенных на кулачковых механизмах, являются высокая сложность и, следовательно, стоимость механики машины, а также сложность в изменении алгоритма управления (нет «гибкости» управления). В настоящее время такие устройства применяются, в основном, в высокопроизводительных машинах-автоматах, например в роторных линиях, а также во всевозможных двигателях внутреннего сгорания.
|
Рычажные механизмы
Шарнирные четырехзвенники (рис. 6.10, а), кривошипно-ползунные (рис. 6.10, б) и кулисные механизмы (рис. 6.10, в) применяются в приводах машин для преобразования вращательного движения кривошипа в возвратно-качательное или возвратно-поступательное движение исполнительного звена.
Рис. 6.10. Рычажные механизмы:
а – шарнирный четырехзвенник; б – кривошипно-ползунный механизм;
в – кулисный механизм
В этих механизмах закон движения исполнительного звена полностью зависит от геометрии механизма – соотношения длин звеньев, взаимного расположения опор. Например, если в механизме, изображенном на рис. 6.10, б, опора О лежит на линии движения ползуна П и длина l ш шатуна много больше длины l к кривошипа (l ш >> l к), закон движения ползуна будет близок к гармоническому. Закон движения не зависит от масштаба механизма – длин звеньев, важно лишь их соотношение. Истинные значения длин звеньев выбираются исходя из множества факторов, главными из которых являются компоновка, силы в кинематических парах и звеньях, жесткость и точность механизма, динамика механизма, колебательные явления, технологичность деталей и стоимость изготовления и т. д. Создание оптимального механизма – сложная многофакторная задача, как и большинство задач в механике.
Передаточные отношения в рычажных механизмах u = wк/wиз (схемы а, в) или u = wк/ V из (схема б) переменны, u ¹ const и является функцией угла поворота кривошипа u = fu (jк). Также переменен и КПД механизма, h = = f h(jк). Минимум КПД наблюдается в положениях механизма с неблагоприятной передачей сил, а именно при больших углах давления. Поэтому при синтезе механизмов необходимо стремиться к минимизации углов давления, изменяя геометрию механизма. Допустимыми обычно считаются углы давления порядка 30...40°.
|
Рычажные механизмы широко распространены в технике; от детских игрушек (танцующий Дед Мороз и т. п.) до мощных поршневых машин. Особенно распространен кривошипно-ползунный механизм (рис. 6.10, б). В поршневых двигателях этот механизм преобразует поступательное движение ползуна-поршня во вращательное движение кривошипа-коленчатого вала. В поршневых насосах и компрессорах - все наоборот.
Типовым во множестве машин является механизм, схема которого представлена на рис. 6.11. Это самое простое устройство для преобразования поступательного движения двигателя 2 во вращательное движение исполнительного звена 1. Угол качания звена 1 здесь ограничен из-за низкого КПД при больших углах давления.
Рис. 6.11. Механизм для преобразования поступательного движения во вращательное:
1 - исполнительное звено – рычаг; 2 - двигатель (пневмоцилиндр, гидроцилиндр, соленоид и т. п.)
|
|
Семя – орган полового размножения и расселения растений: наружи у семян имеется плотный покров – кожура...
Эмиссия газов от очистных сооружений канализации: В последние годы внимание мирового сообщества сосредоточено на экологических проблемах...
Индивидуальные очистные сооружения: К классу индивидуальных очистных сооружений относят сооружения, пропускная способность которых...
Автоматическое растормаживание колес: Тормозные устройства колес предназначены для уменьшения длины пробега и улучшения маневрирования ВС при...
© cyberpedia.su 2017-2024 - Не является автором материалов. Исключительное право сохранено за автором текста.
Если вы не хотите, чтобы данный материал был у нас на сайте, перейдите по ссылке: Нарушение авторских прав. Мы поможем в написании вашей работы!