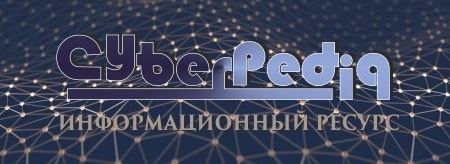
Архитектура электронного правительства: Единая архитектура – это методологический подход при создании системы управления государства, который строится...
Двойное оплодотворение у цветковых растений: Оплодотворение - это процесс слияния мужской и женской половых клеток с образованием зиготы...
Топ:
Когда производится ограждение поезда, остановившегося на перегоне: Во всех случаях немедленно должно быть ограждено место препятствия для движения поездов на смежном пути двухпутного...
Методика измерений сопротивления растеканию тока анодного заземления: Анодный заземлитель (анод) – проводник, погруженный в электролитическую среду (грунт, раствор электролита) и подключенный к положительному...
Особенности труда и отдыха в условиях низких температур: К работам при низких температурах на открытом воздухе и в не отапливаемых помещениях допускаются лица не моложе 18 лет, прошедшие...
Интересное:
Аура как энергетическое поле: многослойную ауру человека можно представить себе подобным...
Распространение рака на другие отдаленные от желудка органы: Характерных симптомов рака желудка не существует. Выраженные симптомы появляются, когда опухоль...
Влияние предпринимательской среды на эффективное функционирование предприятия: Предпринимательская среда – это совокупность внешних и внутренних факторов, оказывающих влияние на функционирование фирмы...
Дисциплины:
![]() |
![]() |
5.00
из
|
Заказать работу |
Содержание книги
Поиск на нашем сайте
|
|
Машины для среднего и мелкого измельчения
Изрезывающие машины. Применяются для измельчения высушенного растительного лекарственного сырья, которое изрезывается до размера частиц 2—8 мм (для получения сборов или производства экстракционных препаратов) с помощью траво- и корнерезок. Рабочим инструментом изрезывающих машин является нож или система ножей, совершающих возвратно-поступательное или вращательное движение. В некоторых случаях машина имеет две системы ножей. Один нож в этих системах двигается, другие смонтированы неподвижно Траво- и корнерезки. В зависимости от строения ножей различают траворезки дисковые и барабанные. В дисковых траворезках ножи имеют изогнутое лезвие и насажены на спицы рабочего колеса, в барабанных ножи помешаются на боковой поверхности барабана, вращающегося вокруг своей оси.
Для измельчения плотных частей растений (корни, корневища, коры) применяются корнерезки. Отличительной их особенностью является наличие гильотинных ножей. Растительное сырье подается с помощью транспортера, представляющего собой брезентовую ленту или металлическую сетку, натянутую на два валика, из которых один совершает вращательное движение, обеспечивающее перемещение ленты. Транспортер помещается в глубоком лотке для создания направления движения материала. Прессующие и направляющие валики с рифленой поверхностью, которых бывает две или три пары, вращающиеся навстречу друг другу, создают компактный слой материала и продвигают его на определенную длину. Электродвигатель приводит во вращение маховик кривошипного вала. Кривошипом приводится в движение гильотинный нож, совершающий возвратно-поступательное движение; растительное сырье подается между нижним неподвижным и верхним падающим ножом, разрезается на куски определенной регулируемой величины.
|
Раздавливающие машины. Валковая дробилка состоит из двух параллельных цилиндрических валков, которые, вращаясь навстречу друг другу, измельчают материал главным образом путем раздавливания. Валки размещены на подшипниках в корпусе, причем валок вращается в неподвижно установленных, а валок — в скользящих под-шинниках, которые удерживаются в заданном положенин (в зависимости от требуемой ширины зазора) с помощью пружины. При попадании в дробилку куска материала чрезмерной твердости пружины ее сжимаются, подвижный валок отходит от неподвижного и кусок выпадает из дробилки, при этом устраняется возможность ее поломки.
В промышленности используются валковые дробилки, отличающиеся по числу, форме и скорости вращения валков. Приводной механизм состоит из двухпеременных передач от отдельного двигателя на шкив каждого валка, окружная скорость которых составляет 2—4,5 м/с. Наибольший размер кусков измельчаемого в валковой дроби дробилке материала зависит от диаметра валков и зазора между ними. Для того чтобы куски измельчаемого материала вследствие трения втягивались между гладкими валками, их диаметр должен быть приблизительно в 20 раз больше диаметра максимального куска измельчаемого материала. Поэтому гладкие валки применяются только для среднего и мелкого измельчения.
Для хрупких материалов (соли и др.) применяют зубчатые валковые дробилки, которые измельчают их раскалыванием и частично раздавливанием и могут захватывать куски размером 'Д—'Л диаметра валка. Валковые дробилки компактны и надежны в работе. Вследствие однократного сжатия материал не переизмельчается. Они наиболее эффективны для материалов умеренной твердости.
Ударно-центробежные мельницы. Дисмембратор и дезинтегратор. Рабочими частями дисмембратора являются диски: вращающийся — со скоростью до 3000 об/мин и неподвижный. Роль последнего выполняет внутренняя стенка корпуса. На внутренней поверхности дисков укреплены по концентрическим окружностям пальцы. При этом диски поставлены один против другого так, что пальцы вращающегося диска входят в свободное про странство между пальцами неподвижного диска. Число пальцев в концентрических окружностях увеличивается по направлению от центра к периферии. Материал, подлежащий измельчению, через загрузочный бункер поступает в центр дисмембратора, в зону между вращающимися и неподвижными пальцами, где и происходит его измельчение. Под действием центробежной силы частицы перемещаются от центра к периферии рабочего органа дисмембратора, многократно ударяются о пальцы, поверхность дисков, испытывают взаимные удары и разрушаются. Измельченные частицы отбрасываются в улитку, откуда, ударяясь о корпус дисмембратора и вращающийся диск, падают вниз и выводятся из машины. Для предотвращения попадания в зоны измельчения механических предметов исходное сырье проходит предварительно через магнитный сепаратор, который устанавливается в нижней части бункера.
|
Дезинтегратор конструктивно отличается от дисмембратора тем, что его рабочие части состоят из двух входящих друг в друга, вращаюшчхся со скоростью до 1200 об/мин в противоположном направлении дисков и с пальцами.. Каждый диск (ротор) закреплен на отдельных валах, которые приводятся во вращение от индивидуальных электродвигателей через шкивы. Материал подается в машину сбоку через воронку вдоль оси дисков, отбрасывается к периферии, подхватывается пальцами и, подвергаясь многочисленным ударам, измельчается и удаляется через разгрузочную воронку в нижней части корпуса.
Машины для тонкого измельчения
Барабанные мельницы. Материал измельчается внутри вращающегося корпуса (барабана) под воздействием мелющих тел. В зависимости от вида мелющих тел различают шаровые и стержневые мельницы. В зависимости от формы барабана и отношения его длины / к диаметру d различают короткие (l/d — = 1,5—2,0), трубные (l/d = 3,0—6,0), цилиндро-кони-ческие мельницы (барабан имеет форму двух усеченных конусов, широкие основания которых соединены цилиндрической частью) и др.
|
Шаровые мельницы. В химико-фармацевтической промышленности для тонкого измельчения наиболее широко применяются шаровые мельницы периодического действия. Они представляют собой пустотелый вращающийся барабан, в который через люк с плотно прижатой к барабану специальной скобой-крышкой загружают измельчаемый материал и мелющие тела — стальные шары диаметром от 25 до 150 мм (приблизительно на 40—45% объема барабана). Наилучший эффект измельчения в шаровых мельницах достигается, когда скорость вращения (число оборотов барабана) является оптимальной и соответствует определенному режиму ее работы. В этот период на шар, находящийся во вращающейся мельнице действует центробежная сила и вес шара. Шары, поднявшись на максимальную высоту, падают по параболическим траекториям. Материал в процессе соударения с шарами измельчается в основном ударом, а также истиранием и раздавливанием. При скорости вращения меньше оптимальной шары поднимаются на незначительную высоту и скатываются параллельными слоями вниз, измельчая материал лишь раздавливанием и истиранием, без участия удара.
Значительное увеличение числа оборотов приводит к тому, что центробежная сила становится настолько большой, что прекращает падение шаров, которые вращаются вместе с барабаном, не производя измельчения.
стоинствами шаровой мельницы являются простота конструкции и эксплуатации, отсутствие распыления порошка при работе. К недостаткам относится неоднородность конечного продукта (гранулометрического состава). Это требует проведения дополнительных операций — просеивания и измельчения.
Стержневые мельницы. По конструкции эти мельницы близки к шаровым, но отличаются формой мелющих тел. Они имеют короткий барабан, в который вместе с материалом, подлежащим измельчению, загружают стальные стержни диаметром 40—100 мм и длиной на 25—50 мм меньше длины барабана. При небольшом числе оборотов барабана (12—30 об/мин) стержни не падают, а перекатываются в нем, измельчая материал раздавливанием, ударом и истиранием. При этом стержни соприкасаются с материалом во многих точках и в первую очередь дробят крупные его частицы, защищая от переизмельчения мелкие. Поэтому продукт в стержневой мельнице получается более равномерной крупности, чем в шаровой.
|
Мельницы для сверхтонкого измельчения
Вибрационные мельницы. Цилиндрический корпус мельницы примерно на 80% объема заполнен мелющими телами — шарами, иногда стержнями. Внутри корпуса установлен вибратор. Это вал с дебалансом или эксцентриковый механизм, который при работе мельницы совершает 1500— 3000 колебаний в минуту при амплитуде 2—4 мм. При этом мелющие тела и измельчаемый материал приводятся в интенсивное движение. Частицы материала, вибрируя во взвешенном слое, измельчаются под действием частых соударений с мелющими телами и истираются. Для предотвращения вибрации пола корпус мельницы установлен на пружинах.
Мельницы могут измельчать как сухие, так и влажные продукты. В вибрационных мельницах весьма быстро достигается высокая дисперсность и большая однородность размеров частиц измельчаемого продукта. Недостатком их является низкая производительность, быстрый износ мелющих тел.
Струйные мельницы. Измельчение материала происходит в струе энергоносителя (воздух, инертный газ, перегретый пар), подаваемого в мельницу со скоростью, достигающей нескольких сотен метров в секунду.
В струйной мельнице с плоской помольной камерой энергоноситель из распределительного коллектора, через сопла отдельными струями поступает в помольно-разделительную камеру. Оси сопел расположены под некоторым углом относительно соответствующих радиусов камеры, вследствие чего струи газа внутри камеры пересекаются. Материал на измельчение подается инжектором (струйный компрессор) через штуцер, увлекается струями газа, получает усконение и измельчается под действием многократных соударений и частично истиранием частиц в точках пересечения струй. Так как струи энергоносителя входят в зону измельчения под некоторым углом, вся масса пылегазовой смеси приобретает вращательное движение в направлении струй. В результате такого движения частицы оказываются в поле центробежных сил и разделяются на фракции. При этом более крупные сосредоточиваются в периферийной части зоны измельчения, а мелкие оттесняются к центру. Измельчившись до определенных размеров (1—6 мкм), частицы вместе с нисходящим газовым потоком, непрерывно вращаясь, вытекают из зоны измельчения в корпус циклона-осадителя, осаждаются на его внутренней поверхности и удаляются в приемник. Наиболее мелкие частицы, содержание которых 5—10 % увлекаются восходящим потоком отработанного воздуха, уносятся через штуцер и улавливаются в дополнительных циклонах или матерчатых фильтрах.
|
Метод измельчения материалов в струйных мельницах имеет ряд существенных преимуществ по сравнению с другими, так как позволяет сочетать измельчение и классификацию с сушкой, смешиванием и другими технологическими процессами. К достоинствам метода относится: возможность получения продукта.с очень высокой степенью измельчения; при измельчении элементы мельницы практически не изнашиваются (отсутствуют вращающиеся детали и мелю щие тела) и, следовательно, не вносят примеси в готовый продукт; материал в процессе измельчения не изменяет своей начальной температуры, что позволяет перерабатывать термолабильные вещества. Недостатком струйных мельниц является большой расход энергоносителя и, следовательно, высокая энергоемкость процессов, необходимость равномерной подачи материала и поддерживания постоянного аэродинамического режима работы.
6. Способы разделения измельчённого материала. В результате дробления в измельченном материале образуются частицы самой разнообразной величины.Для достаточно точного определения размера этих существуют следующие методы:1. Воздушная сепарация - разделение частиц в псевдоожи-женном слое. Более крупные частицы в этом случае располагаются внизу, менее крупные - в центре, мелкие - вверху. В фармацевтической практике этот метод разделения применяется редко.2. Гидравлическая классификация - разделение частиц по скорости их оседания. Также редко применяют в фармацевтической практике.3. Ситовая классификация - разделение материала на фракции с помощью сит. Является основным методом работы в фармацевтической технологии.В результате простого просеивания, т. е. просеивания через одно, исходный материал делится на две фракции: 1) просев)-материал, прошедший сквозь сито; 2) отсев -материал, не прошедший сквозь сито.Форма отверстий сита выбирается в соответствии с природой просеиваемого материала и зависит от способа получения сита.В зависимости от способа получения различают следующие виды сит: 1) сетчатые, 2) перфорированные (штампованные), 3) колосниковые. Качающиеся сита (трясунки). Эти механизмы совершают принудительное качание сита, к-ое обеспечивается жесткой связью коленчатого вала, шатун-но-кривошипного или эксцентрикового механизмов скорпусом сита. Сито устанавливается в горизонтальном или наклонном положении на роликах двигающихся по направляющим. Число качаний в минуту составляет от 50 до 400, а амплитуда колебаний от 5 до 200 мм. Материал, подлежащий просеиванию, насыпается на рабочую поверхность через воронку. Просеянный порошок ссыпается в воронку, а оттуда в тару. Во избежание распыления материала во время работы тара устанавливается в специальный кожух, прикрепленный к корпусу и закрываемый дверцами. Поэтому вибрационные сита пригодны для просеивания разнообразных материалов, обеспечивают высокую производительность и точность просеивания. Вращательно-вибрационное сито- Просеиваемый материал засыпают в бункер поступает на сито, где за счет работы двух грузов вибратора создается такое колебание, к-ое приводит всю массу порошка во вращательное движение по ситу и конусу приемника.Частоту колебаний регулируют ременной передачей привода.Готовый продукт просев и отсев поступают в разные лотки, с которых ссыпаются в заранее приготовленную тару. Производительность сита составляет 80—300 кг/ч. Вибрационное сито. Устройство вибрационного многоярусного В корпусе размещено сито, имеющее три сетки, расположенные одна над другой, верхняя имеет наибольшие отверстия, а нижняя наименьшие. Просеиваемый материал из бункера непрерывно подается на рабочую поверхность сита.Ситовая ткань и генератор колебаний соединены между собой по форме замыкания через толкатель, что обеспечивает возбуждение отдельных точек ткани сита. Каждая просеивающая поверхность имеет несколько точек возбуждения.Сито разделяет просеиваемый материал по крупности частиц на три фракции.Электромагнитное сито в результате быстрого ускорения ткани обеспечивает высокую производительность и повышенную точность разделения.
7 Смешивание порошкообразных лек-х в-в и измельчённого растительного сырья. Принцип работы смесителей с вращающимся корпусом, вращающимися лопастями, центробежных смесителей. Если составные компоненты порошка прописаны в разных количествах, смешение начинают с ингредиентов, прописанных в меньших количествах, постепенно добавляя остальные препараты.При надлежащем смешении не должно наблюдаться частиц, отличающихся от массы порошка размерами илиокраской.В зависимости отколичественной характеристики прописи, свойств и соотношений отдельных ингредиентов возможны отклонения от общих правил смешения. Все ингредиенты смеси для приготовления порошка высыпают в крышку-ступку, накрывают мельницей в положении сверху вниз, затем мельницу переворачивают, включают электродвигатель и в течение 1—2 мин производят измельчение с одновременным смешением. При использовании сухого экстракта смешение осуществляют по общим правилам приготовления порошков с сильнодействующими веществами. При смешении некоторых сухих веществ наблюдается более или менее сильное увлажнение (отсыревание) порошкообразной массы, приводящее к слипанию частиц порошка, а иногда к химическому взаимодействию между его компонентами. Все вещества, предназначенные для таблетирования, перемешивают в смесителях для сухого смешения (качающиеся, циркуляционные, барабанные или пневматические), а затем загружают в какую-либо другую емкость, где увлажняют раствором склеивающего вещества, что необходимо для последующей грануляции. По другому способу смешение и увлажнение производят в обычно используемом с этой целью смесителе с сигмообразными лопастями (двух- или одновальном) или в шнековом смесителе, причем сначала перемешивают сухие порошки (5—10 мин), а затем увлажненную смесь (15—20 мин). Смешивание растительного сырья производится с учетом его объема. Соответственно измельченное сырье осторожно и тщательно смешивают.
Аппараты в которых происходит процесс смешения называются смесители. По принципу действия смесители можно подразделить на аппараты: С вращающимся корпусом. Смесевые барабаны выполняются с корпусом различной формы (цилиндрической, граневой, бицилиндрической, биконической), вращающимся в цапфах на горизонтальном валу. Наиболее экономичным является биконический смеситель. Кроме того, качество смесей, получаемых в нем несколько выше. смесевые барабаны цилиндрической формы могут приводиться во вращение с помощью опорных роликов. В этом случае внутри цилиндра размещаются спиральные ребра и лопатки для лучшего перемешивания смесей. В лопастных (шнековых) смесителях рабочими органами являются валы-шнеки с т-образными винтовыми лопастями. В зависимости от свойств смешиваемых материалов и технологических условий процесса смесители комплектуются винтовыми лопастями различной формы. смесители центробежного типа. Одним из перспективных методов переработки сыпучих материалов основан на использовании их тонкослойного движения и разреженного состояния. В этом случае удается значительно увеличить поверхность контакта между смешиваемыми компонентами и существенно уменьшить энергозатраты. Кроме того, для смесителей этого типа характерна интенсивная циркуляция сыпучего материала, позволяющая существенно улучшить качество смеси.
8. Сборы лекарственные представляют собой смеси резанного или крупно измельченного растительного лекарственного сырья, к к-м иногда добавляют соли, эфирные масла и другие вещества. Многие сборы изготовляют по стандартным прописям на фармацевтических фабриках и заводах, в аптеки они поступают уже в готовом виде. В форме сборов применяют разные части растений. Сборы классифицируют по их дозированию и медицинскому применению. По медицинскому применению сборы подразделяют на сборы для наружного (Species ad usum externum) и для внутреннего употребления (Species ad usum internum). Сложные сборы для внутреннего употребления называют также чаями. По способу применения различают виды сборов: 1) сборы для припарок, или мягчительные (Species ad cataplasmata); 2) сборы для сухих припарок (Species ad fomintationes sicca); 3) сборы для приготовления настоя или отвара (Species ad infuso s. decocto) — наиболее распространенный вид сборов; 4) сборы для ванн (Species pro balneo) — эти сборы добавляют в лечебную ванну; в настоящее время применяют редко; 5) курительные сборы (Species fumales) — служат для непосредственного воздействия дымом, путем сжигания определенной порции смеси, а также в виде папирос и сигарет. Наиболее часто применяют как противоастматический сбор. С целью более полного извлечения действующих веществ сырье, входящее в состав сборов, измельчают по отдельности без остатка. Листья, травы и кору режут с помощью ножниц или ножей, корне- и траворезок (кожистые листья сначала режут, а затем превращают в ступке в крупный порошок). Корни и корневища в зависимости от формы, величины и твердости режут или дробят (толкут) в ступках. Кроме того, для их измельчения могут быть использованы также специальные мельницы. Плоды и семена пропускают через вальцы, бегуны или дисковые мельницы. При аптечной заготовке их можно измельчать (раздавливать и растирать) в большой фарфоровой или металлической ступке. Цветки и мелкие соцветия используют в неизмельченном, цельном виде, так как цветочная оболочка не препятствует извлечению действующих веществ (за исключением цветков липы, состоящих из плотной растительной ткани, их измельчают до размера 0,5—20 мм). Некоторые семена и ягоды также применяют целиком. Так, листья, цветки и траву измельчают до частиц размером не более 5 мм, стебли, кору, корневища и корни — не более 3 мм, плоды и семена — не более 0,5 мм. Растения, входящие в состав сборов для ванн и мягчительных сборов для припарок должны быть измельчены до размера не более 2 мм. Нужная степень измельчения сырья достигается применением специальных сит. При всех степенях измельчения пыль отсеивают сквозь сито с отверстиями размером 0,2 мм.Перемешивание сборов, приготовленных в малых количествах, осуществляется от руки на листе бумаги. Значительное количество измельченного растительного сырья смешивают в больших эмалированных чашках (ступках) с помощью целлулоидной пластинки или лопатки.Если в состав сборов входят эфирные масла, то их растворяют в спирте (в соотношении 1: 10) и полученным раствором опрыскивают перемешанное сырье.Соли растворяют в минимальном количестве воды и вводят в сбор также опрыскиванием.Готовые сборы не следует подвергать сотрясениям, ведущим к постепенному разделению смеси на составные части, отличающиеся по удельной массе и измельченности. Порошки - твердая лекарственная форма для внутреннего и наружного применения, обладающая свойством сыпучести.Различают порошки простые (pulveres simplices), состоящие из одного вещества, и сложные (pulveres compositi), состоящие из двух и более ингредиентов.Порошки бывают дозированные (pulveres divisi), т. е. разделенные на отдельные дозы для удобства и точности приема, и недозированные, неразделенные (pulveres indivisi), отпускаемые общим весом в единой упаковке.Как правило, порошки для внутреннего употребления прописываются в дозированном виде, т. е. являются разделенными. Порошки для наружного применения, наоборот, чаще всего отпускаются в неразделенном состоянии.Недозированные порошки: присыпки, порошки для вдувания,порошки для приготовления на дому примочек, полосканий, спринцеваний и других растворов и т. д. К преимуществам порошков -простота изготовления, фасовки и упаковки, точность дозирования, портативность, возможность отпуска медикаментов, несовместимых в иных лекарственных формах. Негативным свойством - длительность процесса изготовления, возможность отсыревания, уменьшение стабильности препарата при измельчении и увеличение его реакционной способности. Требования, предъявляемые к порошкам: сыпучесть, однородность, допустимые нормы отклонения в массе отдельных доз, цвет, вкус, запах, упаковка и оформление, соответствующие входящим в состав ингредиентам. Технологические операции пр-ва порошков: измельчение,рассеивание,смешивание,дозирование,фасовка,упаковка. Принцип работы фасовки: фасуемый порошок подается в загрузочную воронку. Мешалки, вращающиеся соответственно вокруг вертикальной и горизонтальной осей, обеспечивают равномерное распределение порошка в наполнительной камере. Из центра колеса в эти отверстия установлены на резьбе дозирующие поршни, определяющие объем наполнения.Порошок высыпается во флакон под воздействием короткого импульса сжатого воздуха.
9 Таблетки как лек-ая форма. Определение физико-химических и технологич-х св-в порошков используемых в производстве таблеток. Таблетки твердая дозированная лекарственная форма, представляющая собой спрессованные одно или несколько ЛВ. Таблетки имеют вид плоских, и двояковыпуклых круглых, овальных дисков или иной формы пластинок.Диаметр таблеток колеблется от 3 до 25 мм. Таблетки с большим поперечником считаются брикетами. Высота таблеток должна быть в пределах 30—40% их диаметра. Одна таблетка обычно предназначается на один прием. Таблетки диаметром более 9 мм имеют риску (насечку), к-ая наносится на нее при прессовании штампом. По насечкам таблетки легко разламываются и могут делиться с достаточной точностью на 2 приема. В зависимости от назначения ЛП различают следующие группы таблеток.— таблетки, применяемые пероралыю. Вещества всасываются слизистой оболочкой желудка или кишечника. Таблетки принимают внутрь, запивая водой. Иногда их предварительно растворяют в воде. Пероральные таблетки являются основной группой таблеток.— таблетки, применяемые сублингвально. Вещества всасываются слизистой оболочкой рта.— таблетки, применяемые для имплантации. Рассчитаны на замедленное всасывание ЛВ с целью пролонгирования лечебного эффекта.- таблетки, приготовленные в асептических условиях, используемые для получения инъекционных растворов ЛВ.— таблетки, используемые для приготовления из прессованных веществ растворов разного фармацевтического назначения (полосканий, спринцеваний и др.). Физико-химические св-ва порошков Форма и размер частиц. Порошкообразные ЛП являются грубодисперсными системами и состоят из частиц различных форм и размеров. Большинство их является кристаллическими системами; аморфное состояние встречается редко. Плотность порошка- отношение массы к объему в килограммах на кубический метр. Смачиваемость- способность взаимодействовать с различными жидкостями (лиофильность) и прежде всего с водой(гидрофильность). Гигроскопичность. Если упругость паров в воздухе больше, чем их упругость на поверхности твердых частиц, тогда порошкообразная масса, приготовленная к таблетированию, начнет поглощать пары воды с воздуха и расплываться в поглощенной воде. Технологические св-ва порошков. Фракционный состав.Пористость порошкообразной массы. Пористость порошкообразной массы зависит от размера частиц и их формы. Чем меньше плотность укладки, тем больше пористость массы и тем больше ее объем, требующий большего объема матрицы. Насыпная масса —масса единицы объема свободно насыпанного порошкообразного препарата в килограммах на кубический метр. Она зависит от плотности порошка, пористости и влажности порошка. Текучесть (сыпучесть, подвижность) таблетируемых масс. Должная подвижность порошкообразных препаратов — основное условие равномерного заполнения матричного отверстия. Прессуемость порошков- это способность его частиц к когезии под давлением, к образованию прочных структурированных систем.
10.Группы вспомогательных веществ применяемые при изготовлении таблеток Вспомогательные вещества
Если лекарственные вещества, содержащиеся в таблетке, обеспечивают ее терапевтический эффект, то вспомогательные вещества выполняют двойную функцию: с одной стороны, помогают образованию легко дозируемой и прессуемой массы, с другой — обеспечивают освобождение лекарственного вещества из состава таблетки с необходимой скоростью Разбавители — вещества, вводимые в прописи таблетируемых масс с целью достижения необходимой массы таблетированных препаратов при незначительном содержании действующего ингредиента. В качестве разбавителей применяют крахмал, свекловичный сахар, молочный сахар, глюкозу Разрыхляющие вещества — это соединения, обеспечивающие механическое разрушение (распадение) таблетки в желудке или кишечнике при контакте с пищеварительными соками. От времени и характера распадаемости таблеток зависит действие лекарственных веществ. Разрушающие таблетку за счет набухания ультраамилопектин, агар-агар, желатинРазрушающие таблетку за счет газообразования — так называемые шипучие смеси (например, смеси гидрокарбоната натрия с лимонной или виннокаменной кислотой).Улучшающие смачиваемость и водопроницаемость таблетки (поверхностно-активные вещества — например, твины, спены, натрий лаурилсульфат, а также крахмал). Скользящие и смазывающие вещества. Их вводят в состав таблетируемой массы для улучшения свойств текучести и скольжения крахмал тонкоизмельченный, тальк, полиэтиленгликоли, обезжиренный молочный порошок, борная кислота, аэросил, силикат алюминия, смесь натрия бензоата и натрия ацетата, парафин и т.д Связывающие (склеивающие) вещества добавляют в таблетируемую массу для увеличения прочности гранул и таблеток. Все они должны удовлетворять определенным требованиям; обладать связывающей способностью, не ухудшать распадаемости таблеток, быть совместимыми с лекарственными веществами и индифферентными для организма, не быть дорогостоящими и сложными в применении. Глюкоза — бесцветный кристаллический порошок, без запаха, сладкого вкуса, хорошо растворимый в воде. Этилцеллюлоза — этиловый спирт целлюлозы. Представляет собой белый зернистый без запаха и вкуса порошок, нерастворимый в воде. Применяются 4—8% растворы этилцеллюлозы в безводном этиловом или изопропиловом спирте в качестве склеивающего средства при получений таблеток Альгиновая кислота — аморфный порошок, без запаха, кисловатого вкуса. В воде сильно набухает. Альгинатнатрия — белый или буровато-желтый порошок без запаха и вкуса, медленно растворимый в воде с образованием клейких, растворов. В качестве склеивающего средства используют обычно 1% раствор альгината натрия. Поливиниловый спирт представляет собой белое аморфное вещество, хорошо растворимое в воде, глицерине и нерастворимое в органических растворителях. Обычно в качестве склеивающего средства используют 5% раствор поливинилового спирта. Белая глина (каолин) — белый порошок, жирный на ощупь, с серовато-желтоватым оттенком, не растворяющийся в воде и органических растворителях. С водой способен давать пластичные массы. Магния карбонат основной представляет собой белый легкий порошок, нерастворимый в воде. Используется как разбавитель в таблеточном производстве и в качестве основы для присыпок. Тальк является чистым силикатом (солью кремниевой кислоты) магния. Это тончайший порошок белого или сероватого цвета, скользкий и жирный на ощупь. Не растворяется ни в воде, ни в органических растворителях. Широко используется в фармацевтической практике для таблетирования, дражирования, при обсыпке пилюль, как основа для присыпок и др.
|
|
Типы оградительных сооружений в морском порту: По расположению оградительных сооружений в плане различают волноломы, обе оконечности...
Историки об Елизавете Петровне: Елизавета попала между двумя встречными культурными течениями, воспитывалась среди новых европейских веяний и преданий...
Двойное оплодотворение у цветковых растений: Оплодотворение - это процесс слияния мужской и женской половых клеток с образованием зиготы...
Биохимия спиртового брожения: Основу технологии получения пива составляет спиртовое брожение, - при котором сахар превращается...
© cyberpedia.su 2017-2024 - Не является автором материалов. Исключительное право сохранено за автором текста.
Если вы не хотите, чтобы данный материал был у нас на сайте, перейдите по ссылке: Нарушение авторских прав. Мы поможем в написании вашей работы!