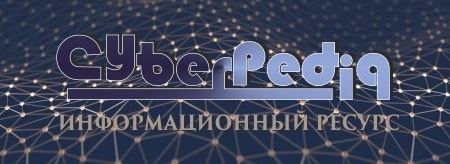
Автоматическое растормаживание колес: Тормозные устройства колес предназначены для уменьшения длины пробега и улучшения маневрирования ВС при...
Архитектура электронного правительства: Единая архитектура – это методологический подход при создании системы управления государства, который строится...
Топ:
Техника безопасности при работе на пароконвектомате: К обслуживанию пароконвектомата допускаются лица, прошедшие технический минимум по эксплуатации оборудования...
Когда производится ограждение поезда, остановившегося на перегоне: Во всех случаях немедленно должно быть ограждено место препятствия для движения поездов на смежном пути двухпутного...
Выпускная квалификационная работа: Основная часть ВКР, как правило, состоит из двух-трех глав, каждая из которых, в свою очередь...
Интересное:
Искусственное повышение поверхности территории: Варианты искусственного повышения поверхности территории необходимо выбирать на основе анализа следующих характеристик защищаемой территории...
Что нужно делать при лейкемии: Прежде всего, необходимо выяснить, не страдаете ли вы каким-либо душевным недугом...
Мероприятия для защиты от морозного пучения грунтов: Инженерная защита от морозного (криогенного) пучения грунтов необходима для легких малоэтажных зданий и других сооружений...
Дисциплины:
![]() |
![]() |
5.00
из
|
Заказать работу |
Содержание книги
Поиск на нашем сайте
|
|
I группа сложности
1. Условия работы технологических машин и оборудования.
Успешная работа машин и оборудования заключается в обеспечении надёжности и работоспособности при заданных нагрузках.
НАДЁЖНОСТЬЮ называют свойство объекта сохранять во времени в установленных пределах значения всех параметров, характеризующих способность выполнять требуемые функции в заданных режимах и условиях применения, технического обслуживания, ремонтов, хранения и транспортирования.
Недостаточная надежность оборудования приводит к огромным затратам на ремонт, к простою оборудования, к авариям, связанным с большими экономическими потерями, разрушениями и человеческими жертвами.
Надежность состоит из сочетаний следующих частных свойств: безотказности, долговечности, ремонтопригодности и сохраняемости.
БЕЗОТКАЗНОСТЬ (надежность в узком смысле)– способность сохранять свои эксплуатационные показатели в течение заданной наработки без вынужденных перерывов. Это свойство особенно важно для машин, отказ в работе которых связан с опасностью для жизни людей или с остановкой автоматизированного производства.
ДОЛГОВЕЧНОСТЬ (РЕСУРС)– свойство изделия длительно сохранять работоспособность до предельного состояния с необходимыми перерывами для технического обслуживания и ремонтов. «Предельное состояние» характеризуется невозможностью его дальнейшей эксплуатации, снижением эффективности или безопасности (выбраковка каната, min ремонтный размер шеек коленвала и т.д.).
РЕМОНТОПРИГОДНОСТЬ – приспособленность изделия к предупреждению, обнаружению и устранению отказов и неисправностей посредством техобслуживания и ремонта. В конструкцию многих современных машин закладывают систему диагностики неисправностей, иначе машина неконкурентоспособна.
|
СОХРАНЯЕМОСТЬ – способность сохранять требуемые эксплуатационные показатели после установленного срока хранения и транспортирования.
2. Виды износа оборудования.
С момента начала эксплуатации машины и любое оборудование подвергаются износу, который нарастает с увеличением срока эксплуатации объектов и приводит к потере ими части своей полезности и, как следствие, определенной части стоимости.
Иными словами, износ - потеря стоимости (обесценение) оборудования в процессе эксплуатации под действием различных факторов устаревания и природно-временного воздействия.
В качестве основных факторов обесценения (устаревания) обычно рассматриваются физический износ, функциональное и экономическое устаревание.
Физический износ - ухудшение первоначальных технико-экономических свойств, обусловленное естественным изнашиванием конкретного объекта в процессе эксплуатации и под воздействием различных природных факторов. Другими словами, это износ материалов, из которых создан объект, потеря его первоначальных качеств, постепенное разрушение конструкций и т.д.
Функциональный износ - обесценение оборудования в результате несоответствия его параметров и(или) характеристик оптимальному технико-экономическому уровню. Причиной функционального устаревания может быть как недостаток в оптимальной полезности, так и ее неиспользуемый избыток.
В качестве примера функционального устаревания можно рассматривать излишек производственных мощностей, конструктивную избыточность или недостаточность, большие затраты на вспомогательное производство и т.д.
Внешний износ (экономическое устаревание) - обесценение оборудования, обусловленное влиянием внешних факторов, а именно: изменение в оптимальном использовании, законодательные нововведения, изменение соотношения спроса и предложения, ухудшение качества сырья, квалификации рабочей силы и т.д.
|
Экономическое устаревание почти всегда считается неустранимым, поскольку величина потенциальных затрат на ликвидацию внешних элементов, вызвавших это устаревание, всегда, за редким исключением, превышает добавленную к собственности стоимость.
Поскольку любой объект может подвергаться одновременно разным видам износа, то при оценке учитывается совокупный износ.
Совокупный износ объекта оценки определяется как сумма потерь стоимости под действием всех факторов устаревания (износа).
В зависимости от технической возможности и экономической целесообразности устранения различают следующие виды износа: устранимый и неустранимый.
Способом устранения физического износа является ремонт, а функционального - модернизация.
3. Методы диагностики отказов.
Техническая диагностика имеет целью получение и анализ информации, позволяющей оценить техническое состояние машины в целом или ее элементов без разборки, а также составить прогноз возможного появления тех или иных неисправностей и времени возникновения отказов. Она позволяет своевременно принять меры по устранению выявленных неисправностей и выполняется опытными слесарями-ремонтниками или механиками в процессе плановых профилактических осмотров, а также перед ремонтами с целью установления подлежащих ликвидации дефектов.
Методами технической диагностики являются:
1. Субъективный метод определения повреждений по возникновению стуков и посторонних шумов, повышенному нагреву отдельных частей машины, увеличению вибраций, появлению запахов гари, масла, газа, наличию стружки в масле, а также визуально.
2. Диагностика с помощью различных приборов и стендов, повышающая степень объективности оценки истинной картины дефектов машины. Она производится с помощью стендов диагностики отдельных узлов, механизмов, систем и машины в целом, приборов для контроля подшипников, дистанционного контроля температуры, термодиагностических приборов, стетоскопов и других приборов для обнаружения шумов (акустическая диагностика), приборов виброметрического контроля и других приспособлений.
3. Термическая индикация неисправностей для регистрации изменения температуры с помощью температурных датчиков, термоиндикаторных красок, изменяющих в этом случае свой цвет.
|
4. Ароматическая диагностика по появлению запаха при критическом износе детали с помощью ампулы с пахучими веществами, заделываемой в данную деталь.
5. Визуальный метод с использованием световодов для обнаружения дефектов в труднодоступных местах.
6. Метод анализа качества (отклонения размеров, формы и расположения поверхностей) изделия, производимого на данном оборудовании.
4. Методы обнаружения дефектов в узлах машин.
Очищенные детали подвергают дефектации с целью оценки их технического состояния, выявления дефектов и установления возможности дальнейшего использования, необходимости ремонта или замены. При дефектации выявляют: износы рабочих поверхностей в виде изменений размеров и геометрической формы детали; наличие выкрошиваний, трещин, сколов, пробоин, царапин, рисок, задиров и т. п.; остаточные деформации в виде изгиба, скручивания, коробления; изменение физико-механических свойств в результате воздействия теплоты или среды.
Дефектацию промытых и просушенных деталей производят после их комплектования по узлам, которую необходимо выполнять аккуратно и внимательно. Каждую деталь сначала осматривают, затем соответствующим поверочным и измерительным инструментом проверяют ее размеры. В отдельных случаях проверяют взаимодействие данной детали с другими, сопряженными с ней.
Способы выявления дефектов:
1. Внешний осмотр. Позволяет определить значительную часть дефектов: пробоины, вмятины, явные трещины, сколы, выкрошивания в подшипниках и зубчатых колесах, коррозию и др.
2. Проверка на ощупь. Определяется износ и смятие резьбы на деталях, легкость проворота подшипников качения и цапф вала в подшипниках скольжения, легкость перемещения шестерен по шлицам вала, наличие и относительная величина зазоров сопряженных деталей, плотность неподвижных соединений и др.
3. Простукивание. Деталь легко остукивают мягким молотком или рукояткой молотка с целью обнаружения трещин, о наличии которых свидетельствует дребезжащий звук.
4. Керосиновая проба. Проводится с целью обнаружения трещины и ее концов. Деталь либо погружают на 15—20 мин в керосин, либо предполагаемое дефектное место смазывают керосином. Затем тщательно протирают и покрывают мелом. Выступающий из трещины керосин - увлажнит мел и четко проявит границы трещины.
|
5. Измерение. С помощью измерительных инструментов и средств определяется величина износа и зазора в сопряженных деталях, отклонение от заданного размера, погрешности формы и расположения поверхностей.
6. Проверка твердости. По результатам замера твердости поверхности детали обнаруживаются изменения, произошедшие в материале детали в процессе ее эксплуатации.
7. Гидравлическое (пневматическое) испытание. Служит для обнаружения трещин и раковин в корпусных деталях. С этой целью в корпусе заглушают все отверстия, кроме одного, через которое нагнетают жидкость под давлением 0,2— 0,3 МПа. Течь или запотевание стенок укажет на наличие трещины. Возможно также нагнетание воздуха в корпус, погруженный в воду. Наличие пузырьков воздуха укажет на имеющуюся неплотность.
8. Магнитный способ. Основан на изменении величины и направления магнитного потока, проходящего через деталь, в местах с дефектами. Это изменение регистрируется нанесением на испытуемую деталь ферромагнитного порошка в сухом или взвешенном в керосине (трансформаторном масле) виде: порошок оседает по кромкам трещины. Способ используется для обнаружения скрытых трещин и раковин в стальных и чугунных деталях. Применяются стационарные и переносные (для крупных деталей) магнитные дефектоскопы.
9. Ультразвуковой способ. Основан на свойстве ультразвуковых волн отражаться от границы двух сред (металла и пустоты в виде трещины, раковины, непровара). Импульс, отраженный от дефектной полости, регистрируется на экране установки, определяя место дефекта и его размеры. Применяется ряд моделей ультразвуковых дефектоскопов.
10. Люминесцентный способ. Основан на свойстве некоторых веществ светиться в ультрафиолетовых лучах. На поверхность детали кисточкой или погружением в ванну наносят флюоресцирующий раствор. Через 10—15 мин поверхность протирают, просушивают сжатым воздухом и наносят на нее тонкий слой порошка (углекислого магния, талька, силикагеля), впитывающего жидкость из трещин или пор. После этого деталь осматривают в затемненном помещении в ультрафиолетовых лучах. Свечение люминофора укажет расположение трещины. Используются стационарные и переносные дефектоскопы. Способ применяется в основном для деталей из цветных металлов и неметаллических материалов, так как их контроль другим способом невозможен.
5. Технология восстановления изношенных деталей.
|
Для разработчиков технологий восстановления деталей предлагается следующий порядок по выбору и определению рационального метода восстановления изношенных поверхностей.
1. На первом этапе необходимо получить информацию о восстанавливаемой детали:
Наименование и номер по каталогу завода изготовителя машины, применяемый материал, поверхностная твердость, шероховатость рабочих поверхностей, виды и коэффициенты повторяемости дефектов по каждой поверхности.
После получения необходимых технических данных делается логическая оценка способов восстановления с точки зрения показателя назначения: геометрических размеров, параметров поверхностного слоя, механических и физико-механических свойств, структуры материала химических и физико-механических характеристик восстановленных поверхностей.
2. Отобранные способы восстановления должны быть оценены по результатам сравнительных стендовых испытаний. В зависимости от условий работы сопряженной изношенной детали необходимо определить износостойкость, усталостную прочность, адгезионную прочность нанесенных покрытий.
Данные механические характеристики определяются на испытательных машинах с использованием существующих гостированных методик.
3. Определение коэффициента износостойкости.
Механические характеристики должны быть определены на образцах в зависимости от характера работы восстанавливаемой поверхности. Так для деталей, работающих в абразивной среде (лемех, лапа, диски и др.) необходимо подготавливать плоские образцы и проводить испытания на износостойкость на машинах трения с подачей абразива типа ИМ-01
Коэффициент износостойкости определяется по формуле
,
где Исв, Исн — средняя износостойкость каждой поверхности восстановленной и новой поверхности.
4. Определение коэффициента выносливости.
Важным показателем для деталей испытывающие знакопеременные нагрузки является предел выносливости, определяющий сопротивление усталостной прочности. Данный показатель определяется как правило на цилиндрических деталях при их испытании на усталостных машинах типа МУИ-6000 или УК-10м. В зависимости от действующих эксплуатационных нагрузок на деталь выбирают схему нагружения, или симметричный изгиб, или консольный изгиб или кручение.
Коэффициент выносливости определяется по формуле
,
Где σ-1в, σ-1н среднее значение придела выносливости каждой восстановленной и новой поверхности соответственно.
5. Определение коэффициента прочности сцепления покрытий.
Для газотермических, полимерных и гальванических методов нанесения покрытия важным показателем является прочность сцепления покрытий с основной детали (адгезия) и прочность нанесенных слоев между собой (когезия). Данные характеристики определяют способами на «отрыв» и на «сдвиг» с использованием «штифтового» метода.
Коэффициент прочности сцепления определяется по формуле
,
Где qв — среднее значение прочности сцепления покрытия каждой поверхности восстановленной детали по результатам испытания
qэ - эталон значения прочности сцепления.
6. Технико-экономический критерий.
После выбора метода восстановления по критерию долговечности необходимо для рассматриваемого метода определить технико-экономический критерий. Он может определятся по следующему уравнению:
,
Где Кэ — технико-экономический критерий;
Свi — себестоимость на восстановление i поверхности рассматриваемым методом;
Кq — коэффициент долговечности восстанавливаемой поверхности.
Приведенные этапы работы по выбору рационального метода позволяют получить объективные данные по эффективности восстановления изношенных поверхностей деталей.
6. Классификация видов ремонта.
Ремонт - это комплекс операций по восстановлению исправности или работоспособности и ресурсов оборудования либо его составных частей. По способу организации различают два вида ремонта:
1.Плановый ремонт, предусмотренный системой ППР и выполняемый после определенной наработки оборудования или при достижении им установленного нормами технического состояния. Он проводится в соответствии с требованиями нормативно-технической документации.
2.Неплановый ремонт, возможность которого также предусмотрена системой планово-предупредительного ремонта и который проводится при необходимости и с целью устранения последствий отказов или происшествий. К неплановому ремонту относится аварийный ремонт, вызванный дефектами конструкции или изготовления оборудования, дефектами предыдущего ремонта либо нарушением технических условий эксплуатации.
По составу и объему работ система ППР предусматривает два вида планового ремонта:
-Текущий ремонт (TP), который выполняется для обеспечения или восстановления работоспособности оборудования на период до установленного нормативами следующего ремонта.
Он состоит в замене и (или) восстановлении отдельных частей оборудования а также предполагает связанные с этим разборку, сборку и регулировку отдельных механизмов машин. Ремонт проводится силами обслуживающего персонала и ремонтными службами на месте установки оборудования.
-Капитальный ремонт (КР), который выполняется для восстановления исправности и полного или близкого к полному восстановлению ресурса оборудования с заменой или восстановлением любых его частей, включая базовые. Он предполагает полную разборку машины, определение дефектов деталей, их ремонт или замену, а также сборочные и регулировочные работы и последующее испытание машины. Выполняется ремонтными службами в ремонтно-механических цехах или на месте установки оборудования. Периодичность проведения технического обслуживания и ремонтов оборудования определяется величиной и структурой ремонтного цикла
7. Виды изнашивания деталей машин
Изнашивание – это процесс разрушения или отделения материала с поверхности детали при трении.
Износ – результат изнашивания, определяемый в установленных единицах (например, в мкм).
- Механическое изнашивание происходит в результате механических воздействий.
- Абразивное изнашивание проявляется вследствие попадания между трущимися поверхностями так называемых абразивных частиц. Эти частицы имеют большую твердость, чем твердость поверхности трения, пластически деформируют поверхность трения, образуя на них риски и царапины. Абразивные частицы попадают между поверхностями трения деталей вместе с атмосферным воздухом, топливом, смазочным материалом, техническими жидкостями или образуются из продуктов изнашивания. Абразивное изнашивание в автомобиле являются доминирующим. Происходит, например, в поршневых узлах, парах скольжения, шкворневых соединениях и т.д.
- Изнашивание при пластическом деформировании сопровождается изменением макрогеометрических размеров детали без потери массы под действием передаваемой нагрузки и под влиянием сил трения, что сопровождается перемещением металлов в сторону скольжения. По пластическому механизму происходит изнашивание резьбовых соединений, вкладышей подшипников скольжения, различных втулок и т.д.
- Изнашивание при хрупком разрушении заключается в том, что поверхностный слой трущихся деталей в результате трения и деформирования подвергается интенсивному наклепу, становится хрупким и разрушается. Самый характерный пример – изнашивание беговых дорожек подшипников качения.
- Усталостное изнашивание (“питтинг”) заключается в образовании на поверхности трения усталостных трещин под действием повторных знакопеременных сил. Впоследствии микротрещины растут и выкрашиваются. При этом росту трещин и выкрашиванию в них материалов способствует смазка, работающая по механизму расклинивания. Этот вид изнашивания наиболее характерен для трущихся поверхностей газораспределительного механизма (ГРМ), зубчатых передач и т.д.
- Молекулярно-механическое изнашивание происходит в результате молекулярного взаимодействия трущихся поверхностей. Часто наблюдается при недостатке смазки, больших нагрузках, температурах и скоростях скольжения.
- Изнашивание схватыванием (схватывание первого рода). Заключается в микросваривании участков трущихся поверхностей, после последующего их взаимного перемещения возникшая связь разрушается.
- Адгезионное (тепловое) изнашивание (схватывание второго рода). Первые этапы идентичны предыдущему виду изнашивания, а далее схватывание контактирующих поверхностей разъединяется не в месте сваривания, а происходит с переносом части одного металла на поверхность другого (адгезия металла). При более жестких условиях трения трущиеся сварившиеся металлы вообще могут не разъединиться, что приводит к заклиниванию или полной потере подвижности контактирующих деталей. Результаты это вида изнашивания легко наблюдать, например, на шейках коленчатого вала, зеркале цилиндра и т.д. Часто заклинивают поршни в двигателях, коленчатые валы и пр.
- Эрозионное изнашивание заключается в вырывании частиц материалов деталей с поверхностей, омываемых газами с высокой температурой и скоростью. Примеры – поверхности деталей камер сгорания двигателей (в первую очередь поршней и головок цилиндров), поверхности выпускных клапанов. Подвидом эрозионного изнашивания является электроэрозионное изнашивание. Заключается в вырывании частиц металлов с поверхностей в результате воздействия дуги электрического разряда. Примеры – в контактах системы зажигания.
- Кавитационное изнашивание происходит при омывании твердого тела жидкостью. Обусловлено местными изменениями давлений и температур. Например, в двигателях этому виду изнашивания подвержены внешние поверхности мокрых гильз цилиндров, лопастей водяного насоса и т.д.
Каждый из видов изнашивания редко встречается в чистом виде, обычно они проявляются комплексно. Например, если лопасти водяного насоса подвержены только кавитационному изнашиванию, то на зеркале цилиндра наблюдается в большей или меньшей степени все виды изнашивания, кроме кавитационного.
8. Коррозионно-механическое изнашивание
Изнашивание – это процесс разрушения или отделения материала с поверхности детали при трении.
Износ – результат изнашивания, определяемый в установленных единицах (например, в мкм).
Коррозионно-механическое изнашивание. Это механическое изнашивание, усиленное явлениями коррозии.
1 Окислительное изнашивание. Под действием химически агрессивных сред (вода, неорганические и органические кислоты) на трущихся поверхностях образуются оксиды металлов. Износостойкость оксидов существенно ниже износостойкости основных металлов. После выработки оксидов металлы оголяются и опять окисляются. В результате общий износ поверхностей деталей интенсифицируется. Данный вид изнашивания наблюдается на всех трущихся поверхностях деталей, контактирующих с агрессивными средами.
2 Фреттинг-коррозионное изнашивание характерно для поверхностей трущихся деталей, подверженных, помимо окисления, вибрациям, т.е. колебаниям с высокой частотой и малой амплитудой. Частицы оксидных пленок при этом не только истираются, но и отделяются (осыпаются) с поверхностей, таким образом увеличивается износ металлов. Продукты окисления к тому же являются абразивными частицами, интенсифицирующими абразивное изнашивание. Фреттинг-коррозия наблюдается в соединениях больших корпусных деталей, например в местах прилегания фланцев блока цилиндров и картера сцепления. Другой типичный пример – поверхности контакта вкладышей шеек коленчатого вала и постелей в картере двигателя.
9. Основные факторы процесса изнашивания и их влияние на износ деталей.
На интенсивность изнашивания оказывают влияние различные факторы, которые определяют вид изнашивания и характер нарастания износа. Факторы, влияющие на интенсивность изнашивания, можно подразделить на три основные группы: конструктивные, технологические и экслуатационные.
Конструктивные факторы: 1)Форма и размер сопрягаемых деталей, что определяет развиваемое удельное давление на поверхности трения и характер контактов. 2)Начальные зазоры и посадки сопряженных деталей, соприкасающихся в процессе трения и обеспечивающих наименьший износ; 3)Конструкции деталей и узлов, обеспечивающие наивыгоднейший тепловой режим при работе сопряженных деталей 4)выбор материалов для изготовления сопряженных деталей и системы их смазки в зависимости от условий работы; 5)величина и характер нагрузки, скорости взаимного перемещения детали, режимы работы и др. 6)условия доступа к узлам трения при техническом обслуживании и быстрой смены узлов и деталей в процессе ремонта.
Соответствие геометрических объектов деталей характеру их работы, рациональный подбор материалов трущихся поверхностей и начальных посадок в сопряжениях, выбор более надежной системы смазки узлов соответствии с режимом работы узлов – все это оказывает влияние на уменьшение износа.
Технологические факторы: 1)качество материала; 2)качество механической обработки поверхности; 3)вид и качество термической обработки; 4) соблюдения технологических процессов изготовления и сборки.
Эксплуатационные факторы: 1)соблюдение эксплуатационного режима работы; 2)качество применяемых сортов смазочных материалов; 3)соблюдение режима технологии смазки узлов и агрегатов; 4) своевременность и качество технического обслуживания.
Большое влияние на износ оказывают: удельное давление между трущимися поверхностями и скорость их относительного перемещения, качество обработки поверхностей, степень запыленности, температура окружающей среды, качество технического обслуживания.
В условиях приближающихся к сухому трению интенсивность изнашивания находится в прямой зависимости от удельного давления. Три полужидком или жидкостном трении рост удельного давления также вызывает увеличение износа, что объясняется более частыми разрывами пленки смазки, повышение температуры смазки, снижением ее вязкости и другими факторами.
Значительно влияют на износостойкость сопряженных деталей качество обработки сопряженных поверхностей: микрогеометрия, волнистость, шероховатость и направление штрихов
10. Методы оценки износа деталей машин
В результате износа изменяются размеры и форма деталей, увеличиваются зазоры в сопряжениях подвижных деталей, нарушается плотность посадки неподвижных деталей. Предельный износ детали наступает при условии невозможности дальнейшего ее использования из-за нарушения нормальной работы узла или машины и возможности аварии. Допустимый износ детали предполагает возможность ее установки в машину без ремонта и удовлетворительную работу в течение предстоящего межремонтного периода. Износ детали может быть определен по следующим признакам:
1. обнаружение дефектов (трещин, бороздок, забоин, вмятин) и изменений формы детали при ее внешнем осмотре;
2. изменение характера звука, издаваемого передачей, подшипником, соединением;
3. оценка качества и формы поверхности, обработанной на станке;
4. увеличение мертвого хода рукояток;
5. нагрев детали;
6. падение давления в гидро- или пневмосистеме.
Величина износа может быть определена одним из методов:
1. методом микрометрирования — по изменению размеров детали, устанавливаемому с помощью универсальных измерительных средств;
2. методом искусственных баз - по изменению размера углубления, нанесенного алмазным или твердосплавным инструментом на рабочую поверхность детали;
3. косвенным методом оценки - по изменению эксплуатационных характеристик сопряжения или узла (мертвого хода, температуры, уровня шума и давления).
11. Некоторые вредные процессы, вызывающие поломки оборудования
Неисправности появляются в результате постоянного или внезапного снижения физико-механических свойств материала, его истирания, деформирования, смятия, коррозии, старения, перераспределения остаточных напряжений и других причин, вызывающих, в конечном итоге разрушение конструкции.
Появление неисправностей обусловлено конструктивными, технологическими и эксплуатационными факторами.
К конструктивным факторам относятся: расчетные нагрузки, скорости относительного перемещения, давления, материалы, их физико-механические характеристики и структура, конструктивное исполнение деталей и сборочных единиц, шероховатость и твердость поверхностей.
Технологическими факторами являются приемы, способы, точность и стабильность получения деталей и заготовок, виды механической, термической, упрочняющей и финишной обработки при их изготовлении, правильность сборки, регулирования, приработки и испытания узлов, агрегатов и машин.
Эксплуатационные факторы оказывают решающее воздействие на сохранение работоспособности оборудования, обеспечиваемых их конструкцией и технологией изготовления. К эксплуатационным относятся факторы, определяемые назначением конструкции, ее нагрузочными и скоростными режимами, а также интенсивностью эксплуатации; не зависящие от назначения машины (условия эксплуатации, своевременность и полнота технического обслуживания и др.).
Различный срок службы (ресурс) деталей обусловлен многими причинами, основными из которых являются следующие:
1. Разнообразие функций деталей в машине [2].
2. Широкий диапазон изменения действующих на детали нагрузок.
3. Наличие как активных (движущихся), так и пассивных (неподвижных) деталей.
4. Разнообразие видов трения в сопряжениях, использование в сопряжениях деталей из разных материалов, вызванное необходимостью снижения сил трения.
5. Отклонения в свойствах материалов, точность и качество обработки сопрягаемых деталей; условия эксплуатации.
Неисправности оборудования можно разделить на три группы: износы, механические повреждения и химико-тепловые повреждения.
Износы деталей машин определяются давлением, циклическими нагрузками, режимом смазывания и степенью его стабильности, скоростью перемещения поверхностей трения, температурным режимом работы деталей, степенью агрессивности окружающей среды, качеством обработки и состоянием поверхностей трения и т.д.
В зависимости от условий работы все детали по виду изнашивания можно разбить на пять групп.
К первой группе — детали ходовой части мобильных машин, для которых основным фактором, определяющим их долговечность, является абразивное изнашивание.
Ко второй группе — детали, у которых основным фактором, лимитирующим долговечность, является износ вследствие пластического деформирования.
К третьей группе — детали, для которых доминирующим фактором является коррозионно-механическое или молекулярно-механическое изнашивание.
К четвертой группе — детали, долговечность которых лимитируется пределом выносливости.
К пятой группе—детали, у которых долговечность зависит одновременно от износостойкости трущихся поверхностей и предела выносливости материала деталей.
Предельным износом называют износ, соответствующий предельному состоянию изнашивающегося изделия.
Допускаемым износом называют износ, при котором изделие может сохранить работоспособность в течение межремонтного периода.
Механические повреждения. К таким повреждениям относятся трещины, пробоины, риски и задиры, выкрашивания, поломки и обломы, изгибы, вмятины и скручивания.
Трещины образуются в результате воздействия значительных местных нагрузок, ударов и пере нагружения. Трещины часто возникают на чугунных деталях и на деталях, изготовленных из листового материала. Кроме трещин, возникающих в результате воздействия сил ударного характера, появляются усталостные трещины в наиболее напряженных местах деталей (продолжительное воздействие знакопеременных нагрузок).
Пробоины появляются в результате ударов различных предметов о поверхности тонкостенных деталей.
Риски и надиры на рабочих поверхностях деталей чаще образуются вследствие загрязнения смазки или абразивного действия чужеродных частиц.
Выкрашивание — дефект, характерный для поверхностей деталей, подвергнутых химико-термической обработке, появляющийся вследствие динамических ударных нагрузок в процессе эксплуатации. Выкрашивание может происходить и в результате усталостных напряжений.
Поломки и обломы возникают при сильных ударах о детали; часто наблюдаются на литых деталях. Могут возникать также в результате усталости металла.
Изгибы и вмятины характеризуются нарушением формы деталей и происходят в результате ударных нагрузок.
Скручивание деталей возникает от воздействия большого крутящего момента, связанного с преодолением временных значительных сопротивлений при работе.
Химико-тепловые повреждения. По сравнению с другими повреждениями химико-тепловые повреждения деталей встречаются реже и возникают, как правило, в результате сложных взаимодействий при тяжелых условиях эксплуатации машин. К таким повреждениям относятся: коробление, коррозия, раковины, образование нагара и накипи, электроэрозионное разрушение и т. д.
Коробление деталей происходит в результате воздействия высоких температур (чаще при нарушении правил эксплуатации машин), приводящих к возникновению структурных изменений и больших внутренних напряжений.
Коррозия — процесс разрушения металлов вследствие химического или электрохимического взаимодействия их с коррозионной средой. Поскольку подавляющее большинство технологических сред представляет собой электролиты, то основным видом коррозии оборудования является электрохимическая коррозия. Для оборудования характерны сплошная (равномерная и неравномерная) и местная коррозии. Сплошная коррозия проявляется в постепенном уменьшении первоначальной толщины элементов сосудов, аппаратов и машин. Большую опасность представляет местная (избирательная) коррозия, т. е. коррозия, охватывающая отдельные участки поверхности деталей машин и аппаратов. Основными причинами появления местной коррозии являются как внутренние факторы (непостоянство структуры и свойств материала, состояние поверхности, неоднородное напряженное состояние в элементах конструкции и т. п.), так и внешние факторы, определяемые, прежде всего условиями взаимодействия металла со средой (температура, давление, время, условия контакта, состав коррозионной среды и т. п.).
Значительно снижают работоспособность конструкции такие виды избирательной коррозии, как межкристаллитная и ножевая коррозияя. Межкристаллитная коррозияя характерна для конструкций, изготовленных из коррозионно-стойких хромистой и хромоникелевой сталей.
Одним из видов разрушения являются коррозионные усталость и растрескивание. Коррозионная усталость возникает при одновременном воздействии циклических растягивающих напряжений и агрессивной среды и обусловлена значительным снижением предела выносливости в специфических условиях по сравнению с пределом выносливости этих металлов на воздухе. Коррозионное растрескивание наблюдается при одновременном воздействии коррозионной среды и внешних или внутренних растягивающих напряжений с образованием транскристаллитных или межкристаллитных трещин.
На склонность к образованию коррозионных трещин существенно влияют: среда, давление и температура, физико-химические свойства металла, величина и характер распределения растягивающих напряжений и т. п.
Наиболее распространенный вид разрушения оборудования-коррозионно-механическое изнашивание, происходящее в результате механических воздействий, сопровождающихся химическим или электрохимическим воздействием среды на металл.
Гидроабразивное изнашивание происходит под воздействием на поверхность металла абразивных частиц, взвешенных в жидкости и перемещающихся относительно изнашиваемой поверхности. Гидроабразивное изнашивание происходит при наличии значительного числа абразивных частиц в составе технологической среды. При воздействии скоростных потоков технологических сред на поверхность трубопроводов, деталей насосов, запорной и регулирующей арматуры и других поверхностей, возникает разрушение металла вследствие ударных воздействий турбулентных струй — гидроэрозионное изнашивание. Его разновидности — коррозия при гидравлических ударах и кавитационное изнашивание.
Кавитационное изнашивание металла происходит в результате воздействия на его поверхность микроударных нагрузок, возникающих при образовании и захлопывании кавитационных полостей и пузырьков.
Раковины (выгорание) образуются в результате местных температурных воздействий на поверхности детали, например раковины на ко
|
|
Кормораздатчик мобильный электрифицированный: схема и процесс работы устройства...
Состав сооружений: решетки и песколовки: Решетки – это первое устройство в схеме очистных сооружений. Они представляют...
Индивидуальные и групповые автопоилки: для животных. Схемы и конструкции...
Автоматическое растормаживание колес: Тормозные устройства колес предназначены для уменьшения длины пробега и улучшения маневрирования ВС при...
© cyberpedia.su 2017-2024 - Не является автором материалов. Исключительное право сохранено за автором текста.
Если вы не хотите, чтобы данный материал был у нас на сайте, перейдите по ссылке: Нарушение авторских прав. Мы поможем в написании вашей работы!