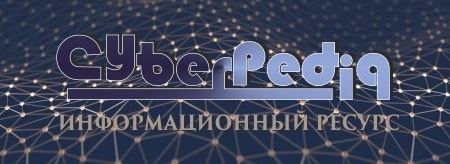
Особенности сооружения опор в сложных условиях: Сооружение ВЛ в районах с суровыми климатическими и тяжелыми геологическими условиями...
Состав сооружений: решетки и песколовки: Решетки – это первое устройство в схеме очистных сооружений. Они представляют...
Топ:
Характеристика АТП и сварочно-жестяницкого участка: Транспорт в настоящее время является одной из важнейших отраслей народного...
Эволюция кровеносной системы позвоночных животных: Биологическая эволюция – необратимый процесс исторического развития живой природы...
Интересное:
Уполаживание и террасирование склонов: Если глубина оврага более 5 м необходимо устройство берм. Варианты использования оврагов для градостроительных целей...
Наиболее распространенные виды рака: Раковая опухоль — это самостоятельное новообразование, которое может возникнуть и от повышенного давления...
Распространение рака на другие отдаленные от желудка органы: Характерных симптомов рака желудка не существует. Выраженные симптомы появляются, когда опухоль...
Дисциплины:
![]() |
![]() |
5.00
из
|
Заказать работу |
Содержание книги
Поиск на нашем сайте
|
|
РЭ - Руководство по эксплуатации - документ, содержащий сведения о конструкции, принципе действия, характеристиках (свойствах) изделия, его составных частях и указания, необходимые для правильной и безопасной эксплуатации изделия (использования по назначению, технического обслуживания, текущего ремонта, хранения и транспортирования) и оценок его технического состояния при определении необходимости отправки его в ремонт, а также сведения по утилизации изделия и его составных частей.
ИМ - Инструкция по монтажу, пуску, регулированию и обкатке изделия- документ, содержащий сведения, необходимые для монтажа, наладки, пуска, регулирования, обкатки и сдачи изделия и его составных частей в эксплуатацию на месте его применения.
ФО – Формуляр - документ, содержащий сведения, удостоверяющие гарантии изготовителя, значения основных параметров и характеристик (свойств) изделия, сведения, отражающие техническое состояние данного изделия, сведения о сертификации и утилизации изделия, а также сведения, которые вносят в период его эксплуатации (длительность и условия работы, техническое обслуживание, ремонт и другие данные).
ПС – Паспорт - документ, содержащий сведения, удостоверяющие гарантии изготовителя, значения основных параметров и характеристик (свойств) изделия, а также сведения о сертификации и утилизации изделия.
ЭТ – Этикетка - документ, содержащий гарантии изготовителя, значения основных параметров и характеристик (свойств) изделия, сведения о сертификации изделия.
КДС - Каталог деталей и сборочных единиц- документ, содержащий перечень деталей и сборочных единиц изделия с иллюстрациями и сведения об их количестве, расположении в изделии, взаимозаменяемости, конструктивных особенностях, материалах и др.
|
НЗЧ - Нормы расхода запасных частей- документ, содержащий номенклатуру запасных частей изделия и их количество, расходуемое на нормируемое количество изделий за период их эксплуатации.
НМ - Нормы расхода материалов- документ, содержащий номенклатуру материалов и их количество, расходуемое на нормированное количество изделий за период их эксплуатации.
ЗИ - Ведомость комплекта запасных частей, инструмента и принадлежностей- документ, содержащий номенклатуру, назначение, количество и места укладки запасных частей, инструментов, принадлежностей и материалов, расходуемых за срок службы изделия.
ИС - Инструкции эксплуатационные специальные- документы, содержащие специальные требования, относящиеся к использованию по назначению, техническому обслуживанию, текущему ремонту, хранению, транспортированию и утилизации, оформленные в виде самостоятельных частей ЭД или в виде приложений к ним.
ВЭ - Ведомость эксплуатационных документов- документ, устанавливающий комплект эксплуатационных документов и места укладки документов, поставляемых с изделием или отдельно от него.
19. Сдача и отчетность о проведенных ремонтах.
Производственные цехи (участки) ежемесячно отчитываются перед отделом главного механика предприятия о проведении ремонтов оборудования, выполненных за месяц.
Отдел главного механика предприятия систематически следит за правильной эксплуатацией и техническим обслуживанием оборудования, контролирует выполнение плановых ремонтов в соответствии с графиком ППР и ежемесячно информирует вышестоящую организацию (ВПО или республиканские органы управления) о работе ремонтно-механической службы предприятия, об уровнях эксплуатации и ремонта основного оборудования (по произвольной форме).
Предприятия представляют республиканским органам управления и промышленным объединениям полугодовые отчеты и ежегодно - сведения о деятельности ремонтно-механической службы.
|
Республиканские органы управления и промышленные объединения представляют годовые сводные отчеты Управлению главного механика
Специализированные подрядные ремонтные организации отчитываются перед своими вышестоящими организациями ежемесячно и ежегодно
20. Списание оборудования.
На балансе предприятия, как правило, числится изношенное и потерянное оборудование, которое подлежит обязательному списанию. Процедура списания предполагает:
1. Определение технического состояния каждой единицы основных средств.
2. Оформление соответствующей документации.
3. Получение разрешения на списание оборудования.
4. Осуществление демонтажа и разборки оборудования.
5. Утилизацию объектов основных средств и постановку на учет материалов, полученных от их ликвидации.
Для определения степени изношенности и возможности дальнейшего использования оборудования, а также для оформления документации при списании изношенного или потерянного оборудования на предприятии приказом руководителя создается специальная комиссия, в состав которой входят должностные лица, в т. ч. главный бухгалтер и лица, ответственные за сохранность объектов. Руководитель предприятия несет ответственность за результаты работы комиссии, главный бухгалтер – за полноту и достоверность информации в документах и правильность заполнения форм на списание основных средств. В обязанности комиссии входит:
Непосредственный осмотр оборудования с целью определения его технического состояния и возможности дальнейшего применения по назначению.
Во время осмотра может быть использована техническая документация (технический паспорт, проект, чертежи, технические условия, инструкции по эксплуатации) и данные бюджетного учета. Результатом осмотра должно стать заключение о непригодности (пригодности) объекта к восстановлению и дальнейшему применению. Установление конкретных причин изношенности оборудования (физический износ, моральный износ, авария, нарушение условий эксплуатации, низкое качество ремонта и др.). Выявление лиц, по вине которых произошло преждевременное выбытие оборудования, и внесение предложения о привлечении этих лиц к ответственности в соответствии с законодательством. Определение возможности использования отдельных узлов, деталей, конструкций и материалов выбывающего объекта в деятельности предприятия, их оценка исходя из текущей рыночной стоимости на дату принятия к учету. Об уничтожении непригодных материалов, не подлежащих сдаче в металлолом, составляется акт. Выбытие оборудования оформляется следующими первичными документами: актом о списании объекта основных средств (кроме автотранспортных средств); актом о списании групп объектов основных средств (кроме автотранспортных средств). К актам о списании могут прилагаться следующие документы: Копии приказа руководителя предприятия о создании постоянно действующей комиссии по списанию основных средств. Копии инвентарных карточек учета основных средств. Отчеты об оценке рыночной стоимости имущества, подготовленные в соответствии с законодательством РК об оценочной деятельности, копия лицензии оценщика. Заключения о техническом состоянии, выданные организациями, имеющими лицензии на данный вид деятельности, подтверждающие непригодность объекта к восстановлению и дальнейшему использованию. Копии технических паспортов и др.
|
21. Оперативное управление электромеханической службой предприятия.
Оперативное управление производством включает комплекс работ по организации: разработки и выполнения оперативно-календарных планов производства продукции; сменно-суточных заданий на уровне цехов, участков и рабочих мест; обеспечения рабочих мест всем необходимым; контроля и регулирования хода производства.
Для оперативного управления производством в цехах характерна строгая регламентация выполнения работ во времени по каждой позиции производственной программы и номенклатурно-календарного плана в зависимости от фактически складывающейся производственной ситуации. Работы по оперативному управлению производством выполняются в реальном масштабе времени, не допускающем перерывов в процессе изготовления деталей и сборки изделий. Временной горизонт оперативного управления для цеха может быть в пределах месяца, участка (бригады) и рабочих мест - в интервале недели - смены. Для межцехового уровня этот интервал расширяется от месяца до года.
|
Таким образом, оперативное управление производством осуществляется на основе непрерывного (повседневного) слежения за ходом производства, оказывая целенаправленное воздействие на коллективы цехов, участков, а также на рабочих для обеспечения безусловного выполнения утвержденных производственных программ. Это достигается выполнением следующих условий:
· строгим распределением работ на короткие периоды времени (декада, неделя, сутки, смена) в цехах, на производственных участках (бригадах) - в подетальном и узловом разрезах, а для рабочих мест в подетально-пооперационном виде;
· четкой организацией сбора и обработки информации о ходе производства;
· комплексным использованием средств вычислительной техники для подготовки вариантов управленческих решений;
· повседневным анализом и владением управленческим персоналом производственной ситуацией в каждом звене предприятия;
· своевременным принятием решений и организацией работы по предупреждению нарушений в ходе производства или для быстрого его восстановления в случае отклонения от запланированных заданий.
22. Восстановление деталей сваркой.
Сваркой называется процесс соединения металлических частей в одно неразъемное целое при помощи нагрева металла в местах соединения. Многие дефекты и повреждения устраняются сваркой, в том числе различные трещины, отколы, пробоины, срыв или износ резьбы и т. п. При ремонте деталей нагрев металла осуществляют газовым пламенем или электрической дугой. Так как детали изготавливаются из различных металлов (сталь, серый и ковкий чугун, цветные металлы и сплавы), то применяют соответствующий способ сварки.
Сварка стальных деталей. Детали оборудования изготавливают из углеродистых и легированных сталей. Малоуглеродистые и среднеуглеродистые стали хорошо свариваются газовой сваркой. Труднее сваривать газовым пламенем стали с содержанием углерода более 0,4%, термически обработанные и легированные стали. Это связано с тем, что с повышением содержания углерода температура плавления углеродистой стали понижается и пламенем газовой горелки легко ее пережечь.
При сварке легированных сталей образуются тугоплавкие окислы, которые остаются в сварных швах и придают им хрупкость. Поэтому для деталей, изготовленных из высокоуглеродистых, термически обработанных и легированных сталей, рекомендуется применять сварки электрической дугой, так как температура сварочной зоны у нее ниже, чем у газовой сварки.
Сварка чугунных деталей имеет определенные трудности, так как серый чугун из твердого состояния сразу переходит в жидкое. При местном нагреве возникают большие внутренние напряжения, которые могут привести к появлению трещин в основном металле. Быстрое охлаждение деталей, особенно тонкостенных, ведет к отбеливанию чугуна в зоне сварки. Это придает чугуну высокую твердость и хрупкость, и деталь становится непригодной для механической обработки.
|
Сварку чугуна можно выполнять двумя способами: холодным, т. е. без предварительного нагрева детали, и горячим, при котором деталь предварительно подогревают в печи.
При горячей сварке деталь медленно нагревают до температуры 600—650°С в специальных печах или горнах. Чем больше содержание углерода в чугуне, тем медленнее должна быть скорость нагрева. Предварительный нагрев осуществляют при сварке и заварке трещин в ответственных деталях и деталях сложной конфигурации. После подогрева деталь помещают в термоизоляционный кожух со специальными задвижками или закрывают листовым асбестом, оставляя открытым только место сварки.
В процессе сварки допускается охлаждение детали до температуры 350—400°С. Если за это время сварка не закончена, то необходимо деталь вновь нагреть и продолжать сварку. После сварки деталь следует медленно охлаждать. Рекомендуется предусмотреть отпуск для деталей сложной конфигурации и разной толщины стенок. Для этого их нагревают до температуры 600—650°С и медленно охлаждают.
Сварку можно вести электрической дугой или газовым пламенем. При газовой сварке применяют нейтральное пламя или пламя с небольшим избытком ацетилена. В качестве присадочного материала используют чугунные прутки диаметром 6—8 мм или малоуглеродистую сварочную проволоку. При сварке чугунными прутками применяют флюсы следующего состава; бура; смесь, состоящая из 50% буры, 47% двууглеродистого натрия и 3% окиси кремния; смесь, состоящая из 56% буры, 22% углекислого натрия и 22% углекислого калия. Флюс вносят в сварочную ванну путем погружения в него нагретого конца присадочного прутка.
Сварка деталей, изготовленных из сплавов цветных металлов. Латунные детали сваривают газовой сваркой. Применяют окислительное пламя с небольшим избытком кислорода. В качестве присадочного материала используют латунные прутки, содержащие кремний и алюминий, снижающие выгорание цинка из сварочной ванны.
Бронзовые детали также сваривают газовой сваркой. Сварочное пламя должно быть нейтральным. В качестве присадочного материала применяют бронзовые прутки с содержанием фосфора до 0,4%. Последний хорошо раскисляет металл шва и затрудняет выгорание олова и других примесей. После сварки деталь нагревают до 450—500°С, а затем быстро охлаждают.
Детали из алюминия и его сплавов лучше сваривать ацетилен о - кислородным пламенем. При плавлении на поверхности сварочной ванны образуется тугоплавкая пленка окиси алюминия, которая препятствует процессу сварки. Температура плавления пленки окиси алюминия составляет 2050°С, ч.то значительно превышает температуру плавления сплава или алюминия, равную 660°С. Для растворения окислов и удаления их из сварочного шва применяют специальные флюсы. Наиболее распространенными являются два вида флюсов, имеющие в составе (%): первый— хлористого натрия—17, хлористого калия— 83; второй — хлористого калия — 45, хлористого натрия — 30, хлористого лития — 15, фтористого калия — 7, сернокислого натрия — 3.
23. Восстановление деталей наплавкой.
Наплавкой называется процесс нанесения одного расплавленного металла (называемого присадочным) на поверхность другого (называемого основным). При этом основной металл также расплавляется на небольшую глубину для образования гомогенного соединения. Цель наплавки может быть различной: восстановление утраченной геометрии детали или придание ей новой формы, образование поверхностного слоя с заданными физико-механическими свойствами (такими как повышенная твердость, износостойкость, антифрикционность, коррозионная стойкость, жаростойкость и пр.), упрочнение наплавкой.
Наплавку можно производить на любые поверхности - плоские, конические, цилиндрические, сферические. В больших пределах может меняться и ее толщина - от нескольких долей миллиметра до сантиметра и более.
В основных своих моментах технология наплавки сходна с технологией сварки.
При наплавке следует соблюдать основные принципы, заключающиеся в ряде требований:
· Необходимо стремиться к минимальному проплавлению основного металла. Это достигается путем наклона электрода в сторону, обратную ходу наплавки.
· Должно быть как можно меньшее перемешивание наплавленного металла с основным.
· Нужно стараться достичь минимальных остаточных напряжений и деформаций в детали. Это требование во многом обеспечивается соблюдением двух предшествующих.
· Необходимо снижать до приемлемых значений припуски на последующую обработку детали. Говоря другими словами, нужно наплавлять металла ровно столько, сколько необходимо, и не больше.
Применяются различные способы наплавки металла - электродуговая, газовая, электрошлаковая, индукционная, плазменная, импульсно-дуговая, вибродуговая, порошковая наплавки. Наибольшее распространение получила дуговая наплавка.
Материалы для наплавки существуют в различных формах. Это могут быть присадочные прутки, порошкообразные смеси, наплавочные покрытые электроды, порошковая и цельностержневая проволока. В электродуговой наплавке применяются в основном покрытые электроды, присадочные прутки и проволока.
Наплавка покрытыми наплавочными электродами относится к основным способам, применяемым как в промышленности, так и в быту, в силу ее простоты, удобства, отсутствия необходимости в специальном оборудовании.
Наплавка деталей из стали осуществляется, как правило, постоянным током обратной полярности (на электроде "плюс") в нижнем положении.
Детали из низкоуглеродистых и низколегированных сталей наплавляют обычно без предварительно нагрева. Но нередко требуется предварительный подогрев и последующая термообработка с целью снятия внутренних напряжений. Более детальные требования к наплавке сообщаются в документации на применяемые наплавочные электроды. Например, для электрода ОЗИ-3 приводятся следующие технологические особенности: "Наплавку производят в один-четыре слоя с предварительным подогревом до температуры 300-600°С. После наплавки рекомендуется медленное охлаждение. Возможна наплавка ванным способом на повышенных режимах. Прокалка перед наплавкой: 350°С, 1 ч."
Поверхность детали перед наплавкой очищается от масла, ржавчины и других загрязнений.
Применяются различные схемы расположения наплавочных швов. В случае плоских поверхностей различают два основных вида наплавки - использование узких валиков с перекрытием друг друга на 0,3-0,4 их ширины, и широких, полученных увеличенными поперечными движениями электрода относительно направления прохода.
Наплавка металла узкими валиками Наплавка металла на цилиндр
Другой способ - укладка узких валиков на некотором расстоянии один от другого. При этом шлак удаляют после наложения нескольких валиков. После этого валики наплавляются и в промежутках. Во избежание коробления деталей, наплавление рекомендуется проводить отдельными участками, "вразброс", а укладку каждого последующего валика начинать с противоположной стороны по отношению к предыдущему.
Наплавка цилиндрической поверхности выполняется тремя способами - валиками вдоль образующей цилиндра, валиками по замкнутым окружностям и по винтовой линии. Последний вариант (по винтовой линии) является особенно удобным в случае механизированной наплавки, при которой детали в процессе наплавки придается равномерное вращение.
Для восстановления и повышения срока службы режущего, штампового и измерительного инструмента, а также деталей механизмов, работающих при интенсивном износе, применяется наплавка рабочих поверхностей твердыми сплавами, представляющими собой соединения таких металлов, как титан, вольфрам, тантал, марганец, хром и других с бором, углеродом, кобальтом, железом, никелем и пр. Для получения более качественной наплавки, предупреждения образования трещин и снижения напряжений, во многих случаях целесообразен подогрев заготовок до температуры 300°C и выше.
Наплавка металлорежущего инструмента и штампов. Металлорежущие инструменты и штампы, работающие при холодной и горячей штамповке, наплавляют электродами ОЗИ-3, ОЗИ-5, ОЗИ-6, ЦС-1, ЦИ-1М и прочие марки. Металл, наплавленный этими электродами, обладает высокой сопротивляемостью к истиранию и смятию при больших удельных нагрузках и высоких температурах - до 650-850°C. Твердость наплавленного слоя без термообработки составляет от 52 HRC (ОЗИ-5) до 61 HRC (ОЗИ-3). Наплавляется 1-3 слоя общей толщиной 2-6 мм. Деталь перед наплавкой подогревают до температуры 300-700°С (в зависимости от марки электрода).
Наплавка деталей, работающих на истирание без ударных нагрузок. Если требуется получить наплавленный металл особо высокой твердости, можно использовать электроды для наплавки Т-590 и Т-620. Они специально предназначены для покрытия деталей, работающих на интенсивное истирание. Их стержень изготовлен из малоуглеродистой стали, зато в покрытия входят феррохром, ферротитан, ферробор, карбид бора и графит. Благодаря этим материалам твердость наплавленного металла может достигать 62-64 единиц по HRC.
Наплавка деталей, работающих на истирание с ударными нагрузками. Детали из марганцовистых сталей (110Г13Л и подобные ей), работающие в условиях интенсивного поверхностного износа и высоких ударных нагрузок (в частности, рабочие органы строительного и землеройного оборудования), наплавляют электродами ОМГ-Н, ЦНИИН-4, ОЗН-7М, ОЗН-400М, ОЗН-300М и прочие марки. При их использовании твердость наплавляемого металла во втором слое получается 45-65 HRC при высоких значениях вязкости.
Наплавка нержавеющих сталей. Для наплавки деталей из нержавеющих сталей применяются электроды ЦН-6Л, ЦН-12М-67 и прочие марки. Стержень этих электродов изготовлен из нержавеющей высоколегированной проволоки. Кроме высокой коррозионной стойкости, наплавленный металл имеет еще и устойчивость к задиранию, что позволяет использовать эти электроды для наплавки уплотнительных поверхностей в арматурных изделиях.
Наплавка меди и ее сплавов. Наплавка меди и ее сплавов (бронз) может осуществляться не только на медное или бронзовое основание, но также на сталь и чугун. В этом случае создаются биметаллические изделия, имеющие необходимые эксплуатационные качества (высокую стойкость против коррозии, низкий коэффициент трения и прочие ценные свойства, присущие меди и ее сплавам) и обладающие при этом гораздо более низкой стоимостью в сравнении с деталями, изготовленными полностью из меди или ее сплавов.
Алюминиевые бронзы, в частности, обладающие высокими антифрикционными свойствами, очень хорошо работают в узлах трения, поэтому их наплавляют на червячные колеса, сухари и другие детали, работающие в условиях трения.
Наплавка деталей из технически чистой меди может производиться электродами "Комсомолец-100" или присадочными прутками из меди или ее сплавов. При наплавке меди на медь применяют предварительный подогрев до температуры 300-500°С.
24. Восстановления деталей электромеханическим методом.
Восстановление деталей электромеханической обработкой (ЭМО) основано на перераспределении поверхностного слоя материала восстанавливаемой детали, что обеспечивает значительное повышение использования металла, и наплавки добавочного материала к восстанавливаемой поверхности.
Технологический процесс восстановления посадочных поверхностей изношенных деталей при ЭМО состоит из двух операций: высадки металла и сглаживания посадочной поверхности до определенного размера.
Принципиальное отличие этих операций состоит в различии контактных напряжений. В первом случае обработка проводится пластиной (роликом) из твердого сплава, ширина поверхности контакта которой численно меньше или равна подаче, а во втором
случае обработка проводится твердосплавной пластиной (роликом), ширина контакта которой значительно превышает подачу.
При высадке на контактной поверхности образуется винтовой выступ, а при сглаживании этот выступ уменьшается до необходимого размера; первоначальный диаметр контактной поверхности увеличивается.
Профиль может создаваться как за счет увеличения силы р и величины силы тока, так и за счет увеличения числа рабочих ходов. По мере увеличения силы металл, контактирующий с пластиной, подвергается все большему пластическому деформированию и выдавливается наружу вдоль контура пластины, а последняя, внедряясь в металл, образует впадину, увеличивающуюся в своих размерах. Таким образом, по мере увеличения силы расстояние между неровностями, ограничивающими выступ, уменьшается.
Приложение электрического тока в месте контакта инструмента и заготовки позволяет значительно уменьшить прикладываемое усилие за счет того, что происходит разогрев металла детали и увеличение его пластичности.
Сглаживание обеспечивает; увеличение контактной поверхности сопрягаемой детали и снижение ее шероховатости; увеличение твердости и упругих свойств контактной поверхности; необходимый натяг сопряжения и его прочность.
После сглаживания в несколько рабочих ходов сечение сглаженного профиля приближается к прямоугольному.
Для реализации данного метода применяют установку для ЭМО на базе токарно- винторезного станка. В настоящее время указанная технология восстановления усовершенствована путем применения более интенсивных режимов, новых материалов и конструкций инструмента. В качестве инструмента используют универсальную телескопическую державку для восстановления деталей. Подвод тока осуществляют непосредственно к головкам (его прохождение по корпусу резцедержателя исключается).
При восстановлении размеров деталей машин в качестве инструмента применяются пластины, работающие в условиях трения скольжения, и ролики, работающие в условиях трения качения. Так как инструмент работает в очень жестких условиях - высокие давления и температуры, то в качестве материала для его изготовления применяют термостойкие бронзы, жаропрочные стали, твердые сплавы типа титанокобальтовых, псевдосплавы на основе карбида вольфрама и меди. Ко всем этим материалам предъявляют высокие требования но электропроводности, теплопроводности, жаропрочности.
Электромеханическое выдавливание позволяет эффективно восстанавливать размер наружных цилиндрических поверхностей с последующей доводкой на 0,02 - 0,1 мм.
При данном способе восстановления цилиндрических поверхностей на величину восстановленного размера большое влияние оказывает сила тока. Это вполне понятно и объясняется тем, что с увеличением силы тока повышается глубина проникновения высокой температуры, уменьшается предел текучести обрабатываемого материала, а следовательно, повышается интенсивность выдавливания.
При необходимости восстановления больших размеров применяются добавочные материалы, наносимые на восстанавливаемые поверхности различными способами.
Например, при восстановлении размеров деталей на величину до 0,2... 0,4 мм применяют в качестве добавочного материала различные порошки. Порошок наносят на восстанавливаемую поверхность несколькими способами: обмазкой, свободным просыпанием в зону контакта инструмента и заготовки, удержанием порошка в зоне контакта с помощью электромагнита.
При нанесении дополнительного материала (порошка) на восстанавливаемую поверхность обмазкой, получается покрытие с очень большой пористостью, а иногда происходит даже отслаивание наплавленного слоя. Это вызвано наличием так называемого «третьего тела» - связующего компонента, который при наплавке из-за высоких температур выгорает в зоне контакта инструмента и слоя дополнительного материала.
Для улучшения качества восстановленного слоя (уменьшения его пористости и лучшего припекания к поверхности), избавляются от «третьего тела» путем нанесения порошка свободным просыпанием из бункера. Однако при таком способе нанесения дополнительного материала происходит очень большой его перерасход. Поэтому, для избежания данного недостатка, используют электромагнитное поле для удержания порошка в зоне наплавки.
При восстановлении еще больших размеров используют в качестве добавочного материала проволоку или ленту.
25. Виды ресурсов машин и оборудований.
Технический ресурс – показатель долговечности, характеризующий запас возможной наработки объекта.
Согласно ГОСТ 13377-75 ресурсом называют наработку объекта от начала или возобновления эксплуатации до наступления предельного состояния
Для разных механизмов ресурс может выражаться в различных единицах, например, в часах работы для двигателя, километрах пробега для автомобиля, количестве посадок для самолёта, количестве включений для релейных устройств и т. д.
Отличают следующие виды ресурса:
полный — срок службы изделия до конца его эксплуатации;
доремонтный (межремонтный) — срок от начала эксплуатации (после ремонта) до восстановительного ремонта;
израсходованный — от начала эксплуатации до рассматриваемой наработки;
остаточный — от рассматриваемой наработки и до отказа (для невосстанавливаемого изделия) или до ремонта (для изделия, подлежащего ремонту).
Моторесурс — ресурс двигателя. Измеряется в моточасах или километрах пробега.
26. Основные производственные отделения при ремонте.
В производственных отделениях выполняется ремонт деталей, приборов, узлов и агрегатов, снятых с машин. Эти работы составляют около 50% объема работ по ТР машин. В соответствии с характером выполняемых работ создаются следующие производственные отделения: агрегатное, слесарно-механическое, кузнечно-рессорное, сварочное, медницкое, электротехническое, аккумуляторное, топливной аппаратуры, шиномонтажное, кузовное, малярное, столярное, арматурное, обойное и др.
Агрегатное отделение предназначается для ремонта коробок передач, карданных передач, редукторов, тормозной системы, др. Характерными ремонтными работами по агрегатам трансмиссии являются: замена фрикционных накладок и подшипников сцепления, замена шестерен и подшипников в коробке передач и др.
Технологический процесс в агрегатном и других отделениях следующий: агрегаты и узлы после наружной мойки поступают на верстаки или соответствующие стенды. После частичной или полной разборки агрегата детали подвергаются мойке, контролю, сортировке. Затем они поступают на верстаки и стенды, где происходит сборка узлов и агрегатов. Ремонт в основном осуществляется путем замены неисправных деталей новыми или ранее отремонтированными. Окончательная сборка, обкатка, регулировка и доводка агрегатов обычно осуществляются на стендах.
Отремонтированные агрегаты возвращаются для установки на ту же машину или сдаются на склад. Неисправные детали сдаются на склад в обмен на новые или отремонтированные. Негодные детали списываются в утиль, а нуждающиеся в ремонте передаются в производство или направляются на специализированные ремонтные предприятия. На многих предприятиях ремонт двигателей и других основных агрегатов производится в агрегатном отделении.
Слесарно-механическое отделение предназначается для обработки деталей под ремонтные размеры, изготовления крепежных и других деталей (болтов, шпилек, втулок, пальцев и др.), для обработки деталей после термической обработки, подготовки их к сварке и обработке после сварки и т. п. Отделение выполняет эти работы по заявкам всех производственных подразделений.
В кузнечно-рессорном отделении производят ремонт и изготовление деталей с применением нагрева (правка, горячая клепка, ковка деталей) и ремонт рессор, имеющих пониженную упругость или поломку отдельных листов. Собранные рессоры испытывают под нагрузкой. Изготовленные или отремонтированные детали передаются непосредственно на посты обслуживания и ремонта автомобилей, для дальнейшей обработки в слесарно-механическое отделение или сдаются на склад.
Сварочное отделение предназначено для восстановления изношенных или поврежденных деталей наплавкой металла, осуществляет заварку трещин в металлических панелях кузова, кабины, оперения. Посты сварки отделяются от остальной части помещения металлическими экранами.
В медницком отделении выполняют ремонт радиаторов, топливных баков, топливопроводов по заявкам, записанным в контрольных талонах, и по заявкам других подразделений.
В малярном отделении окрашивают (частично или полностью) машины и агрегаты. Предназначено для окраски машин безвоздушным распыливанием; оно оборудовано двумя гидрофильтрами.
В электротехническом отделении производят ТО и ремонт приборов электрооборудования. Приборы электрооборудования, неисправности которых невозможно устранить на постах обслуживания и ремонта машин, снимаются с машин и направляются в электротехническое отделение для диагностики и ремонта. Отремонтированные приборы проверяют на стендах. Рабочие отделения выполняют также работы в зонах ТО и ТР.
Рабочие аккумуляторного отделения выполняют ремонт и обслуживание аккумуляторных батарей.
В топливном отделении производят ТО и ремонт приборов системы питания карбюраторных и дизельных двигателей. В отделении выполняют регулировку карбюраторов на топливную экономичность, проверку и регулировку форсунок и топливных насосов дизелей. Выполненные регулировки на топливную экономичность учитываются в журнале.
Контроль качества ТО и ремонта машин является составной частью производственного процесса. Цель контроля - предупреждение брака и повышение качества ТО и ТР. Качество ТО и ремонта закладывается в процессе производства работ и оценивается путем непосредственного контроля и при работе машин на линии. Основным объективным показателем качества работы является продолжительность безотказной работы на линии после ТО и ремонта.
27. Назначение ремонтных баз.
Собственные ремонтные базы расположены непосредственно на промышленной площадке и обслуживают только его оборудование. Οʜᴎ могут включать: РММ, электроремонтные мастерские, центральные электромеханические мастерские, авторемонтные мастерские.
Производственно-ремонтные базы предназначены для хранения, технического обслуживания и ремонта машин и механизмов, необходимых на производстве.
В производственных корпусах типовой базы размещены отделения ежедневного, первого и второго технических обслуживании, текущего ремонта, агрегатное, слесарно-механическое, малярное, шиноремонтное, электротехническое, аккумуляторное, машин и механизмов, тепловое (сварочное и термические участки), гидромеханизмов, а также склады запасных частей, резины, смазочных материалов и другие.
Линия ежедневного обслуживания оборудована механизированной струенаправленной моечной установкой, конструкция которой обеспечивает хорошие условия для работы мойщика (при правильной эксплуатации установки исключена возможность попадания на него воды). Подача воды, воздуха, смазочных материалов и спуск отработавшего масла из машины при ТО-1, ТО-2 и текущем ремонте осуществляется через централизованную систему. Въезды и выезды машин оборудованы воздушными завесами.
В агрегатном отделении моют машину, контролируют ее техническое состояние и ремонтируют узлы и детали. Для моечных операций предусмотрена моечно-выварочная ванна, для испытания установлены соответствующие стенды. В слесарно-механическом отделении производят механическую обработку восстанавливаемых и изготовляемых запасных частей к машинам и специальным агрегатам. Слесарно-подгоночные работы выполняют на верстаках с помощью соответствующих приспособлений.
Малярное отделение предназначено для окраски машин безвоздушным распыливанием; оно оборудовано двумя гидрофильтрами.
В шиномонтажном отделении производят монтаж и демонтаж покрышек и электровулканизацию камер.
Отделение приборов питания и электрооборудования расположено
|
|
Организация стока поверхностных вод: Наибольшее количество влаги на земном шаре испаряется с поверхности морей и океанов (88‰)...
Поперечные профили набережных и береговой полосы: На городских территориях берегоукрепление проектируют с учетом технических и экономических требований, но особое значение придают эстетическим...
Эмиссия газов от очистных сооружений канализации: В последние годы внимание мирового сообщества сосредоточено на экологических проблемах...
История развития хранилищ для нефти: Первые склады нефти появились в XVII веке. Они представляли собой землянные ямы-амбара глубиной 4…5 м...
© cyberpedia.su 2017-2024 - Не является автором материалов. Исключительное право сохранено за автором текста.
Если вы не хотите, чтобы данный материал был у нас на сайте, перейдите по ссылке: Нарушение авторских прав. Мы поможем в написании вашей работы!