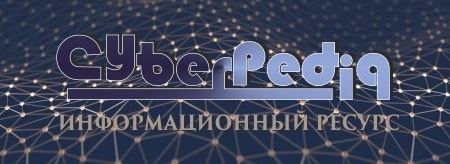
Опора деревянной одностоечной и способы укрепление угловых опор: Опоры ВЛ - конструкции, предназначенные для поддерживания проводов на необходимой высоте над землей, водой...
История развития пистолетов-пулеметов: Предпосылкой для возникновения пистолетов-пулеметов послужила давняя тенденция тяготения винтовок...
Топ:
Определение места расположения распределительного центра: Фирма реализует продукцию на рынках сбыта и имеет постоянных поставщиков в разных регионах. Увеличение объема продаж...
Когда производится ограждение поезда, остановившегося на перегоне: Во всех случаях немедленно должно быть ограждено место препятствия для движения поездов на смежном пути двухпутного...
Марксистская теория происхождения государства: По мнению Маркса и Энгельса, в основе развития общества, происходящих в нем изменений лежит...
Интересное:
Инженерная защита территорий, зданий и сооружений от опасных геологических процессов: Изучение оползневых явлений, оценка устойчивости склонов и проектирование противооползневых сооружений — актуальнейшие задачи, стоящие перед отечественными...
Отражение на счетах бухгалтерского учета процесса приобретения: Процесс заготовления представляет систему экономических событий, включающих приобретение организацией у поставщиков сырья...
Принципы управления денежными потоками: одним из методов контроля за состоянием денежной наличности является...
Дисциплины:
![]() |
![]() |
5.00
из
|
Заказать работу |
Содержание книги
Поиск на нашем сайте
|
|
В любой машине свыше 60 % деталей имеют резьбу. При эксплуатации машин резьба изнашивается, витки сминаются, деформируются и срываются. Причем изнашиванию и повреждениям подвергаются прежде всего резьбовые отверстия. Незначительные повреждения резьбы (смятие, деформации отдельных витков) устраняют калибровкой ее метчиком или плашкой. При срыве более двух ниток и других серьезных повреждениях применяют различные методы восстановления резьбы в зависимости от конструкции детали, типа резьбы (наружная или внутренняя) и т.д.
Наружную резьбу (на валах, осях и т.д.) восстанавливают следующими способами:
-нарезанием резьбы ремонтного размера;
-наплавкой и нарезанием резьбы номинального размера;
-электроконтактной приваркой проволоки;
-заменой изношенной резьбовой части детали.
Старую резьбу срезают на токарном станке и нарезают новую резьбу меньшего размера.
Для восстановления резьбы до номинального размера применяют механизированную наплавку, чаще вибродуговую и в среде С02, реже под флюсом и в среде пара. Перед наплавкой старую резьбу срезают. После наплавки деталь протачивают и нарезают резьбу номинального размера.
Восстанавливают резьбы также электроконтактной приваркой проволоки. После приварки проволоки деталь обтачивают и нарезают резьбу номинального размера.
Иногда конец детали с изношенной резьбой отрезают, изготовляют новую часть детали, которую свертывают или сваривают с оставшейся частью. Затем нарезают резьбу номинального размера. При большом диаметре резьбы иногда ее не отрезают, а обтачивают, затем напрессовывают кольцо и нарезают резьбу номинального размера.
Внутреннюю резьбу восстанавливают чаще всего в корпусных и других базисных деталях, изготовленных из чугуна и алюминиевых сплавов. При этом независимо от материала деталей характер износа резьбовых отверстий одинаков: наибольший износ и срывы имеют первые два-три витка резьбы, остальные витки изнашиваются значительно меньше. Это объясняется различной нагрузкой на витки резьбового соединения: первый виток нагружен в пять-шесть раз больше последнего.
|
Внутреннюю резьбу восстанавливают следующими способами:
-нарезанием резьбы ремонтного размера;
-нарезанием резьбы номинального размера на новом месте;
-заваркой отверстия и последующим сверлением и нарезанием резьбы номинального размера;
-с применением полимерных композиций;
-постановкой резьбовой пробки (ввертыша);
-установкой резьбовой спиральной вставки.
В случае нарезания резьбы ремонтного размера часто приходится изготавливать ступенчатую шпильку. Нарезание резьбы на новом месте возможно в том случае, если конструкция деталей соединения позволяет изменить расположение резьбового отверстия без нарушения взаимозаменяемости (ступицы, фланцы и др.). Перед заваркой обязательно удаляют старую резьбу.
В качестве полимерных композиций при восстановлении резьбовых соединений обычно используют составы на основе эпоксидной смолы.
При постановке резьбовой пробки изношенное резьбовое отверстие рассверливают или растачивают, нарезают в нем резьбу и ввертывают в него пробку. Затем в ней сверлят отверстие и нарезают резьбу номинального размера. Часто резьбовые пробки дополнительно закрепляют посредством клеевых композиций или стопорными шпильками, ввернутыми на границе пробки с деталью.
Для ремонта резьбовых отверстий разработали и применяют способ установки резьбовых спиральных вставок. Вставку изготавливают в виде пружинящей спирали из нержавеющей проволоки ромбического сечения с острым углом 60°. Наружная и внутренняя поверхности вставки представляют собой метрическую резьбу разных размеров. На одном конце вставки размещен технологический поводок с насечкой, с помощью которого специальным ключом вставку ввертывают в отверстие. Затем этот поводок удаляют специальным бородком.
|
Основнымнедостатком наплавки следует считать снижение усталостной прочности детали (от 10 до 30%) и возможность прожога тонкостенных деталей. Резьбовые отверстия имеют следующие основные дефекты: срыв, забитость, смятие и выкрашивание отдельных витков, износ по внутреннему и среднему диаметрам и др. Для их ремонта применяют различные способы.
Основной недостаток заварки отверстий с последующим сверлением и нарезанием резьбы номинального размера - большая зона термического влияния, что приводит к отбелу чугуна, образованию трещин и короблению, изменению структуры материала и снижению прочности резьбы почти в два раза. Нарезание резьбового отверстия на новом месте возможно только в том случае, когда его расположение может быть изменено без нарушения взаимозаменяемости соединения (ступицы барабана и т. п.).
Стабилизацию резьбовых соединений полимерной композицией используют при суммарном износе соединения шпилька - корпус не более 0,3 мм. Установка спиральной вставки при ремонте ответственных деталей и агрегатов получила широкое применение.
Нарезание резьбового отверстия на новом месте возможно только в том случае, когда его расположение может быть изменено без нарушения взаимозаменяемости соединения (ступицы барабана и т. п.), Стабилизацию резьбовых соединений полимерной композицией используют при суммарном износе соединения шпилька - корпус не более 0,3 мм, Установка спиральной вставки при ремонте ответственных деталей и агрегатов получила широкое применение. Вставку изготовляют из нержавеющей проволоки Х18М10Т ромбического сечения. Изношенную резьбу в отверстии деталей восстанавливают постановкой спиральных вставок, используя комплект приспособления ПИМ-5331. Технология состоит из рассверливания отверстия под требуемый размер (М8 на А110, М10 на М12, М12 на М14 и т.д.), нарезания резьбы с тем же шагом; установки спиральной установки необходимого размера технологически поводком вниз в монтажный инструмент
Ремонт зубчатых передач.
В сборочных единицах машин часто применяют открытые передачи, в которых зубчатые колеса и звездочки испытывают большие нагрузки и не защищены от действия влаги и пыли. Это является причиной сравнительно быстрого износа зубчатых колес. Кроме того, используют закрытые зубчатые передачи в виде отдельных сборочных единиц: редукторов, коробок передач и др. При работе передач в подобных условиях возникают в зацеплении дополнительные динамические нагрузки, вызываемые деформациями зубчатых колес и валов, а также опор и корпусов вследствие неизбежных неисправностей изготовления и монтажа. Помимо того, передачи могут работать со значительными знакопеременными кратковременными перегрузками.
|
Для замены зубчатых колес в закрытых передачах часто требуется демонтаж с полной разборкой сборочной единицы.
Зубчатые колеса относятся к категории дорогостоящих деталей. Поэтому на ремонтных базах, не оснащенных необходимым оборудованием для изготовления колес, возможно восстановление наплавкой изношенных зубьев, напрессовкой зубчатых венцов, вдавливанием и другими способами.
Способ восстановления зубчатых колес выбирают в зависимости от характера неисправности, материала, класса точности и производственных возможностей ремонтного предприятия.
Поступающие в ремонт зубчатые колеса могут иметь следующие неисправности:
изнашивание рабочей поверхности зубьев; выкрошивание и поломка зубьев; образование трещин, задиров, вмятин и раковин; износ посадочных мест зубчатых колес и шпоночных пазов; нарушение правильного положения зубчатых колес и дефекты сборки.
Степень износа зубьев определяют зубомером. Для этого по чертежу находят необходимую глубину замера и на этой глубине — размер зуба с помощью штангензубомера. Сравнивая полученный результат с номинальным размером (размер по чертежу), определяют величину износа.
Зубчатые передачи считаются непригодными для эксплуатации, если величина их износа превысила предельно допустимое значение, которое устанавливается для каждой передачи техническими условиями на ремонт данной машины.
Изношенная зубчатая передача может быть отремонтирована: наплавкой отдельных зубьев, сплошной наплавкой всего обода, методом деформации, методом ремонтных размеров и слесарно-механическими способами.
|
Зубья шестерен после обычной наварки зачищают и наплавляют тонким слоем твердого сплава сормайт. Размер зубьев после механической обработки перед наплавкой должен быть меньше номинального на величину до 1,5 мм. Наплавка зубьев производится в ванне с водой.
Для наплавки боковых поверхностей зубьев шестерню устанавливают в ванне и наплавку начинают со второго зуба от поверхности воды. Пламенем газовой горелки наплавляемый зуб разогревают, после чего прутком сормайта наносят флюс-буру и наплавляют зуб до требуемого размера. После этого шестерню поворачивают так, чтобы наплавленный зуб не касался поверхности воды, и наплавляют следующий (третий) зуб. После того, как наплавленный второй зуб охладится (до темно-вишневого цвета), его погружают в воду для закалки.
Таким же способом производится наплавка зубьев мартенситовым чугуном. Отремонтированные зубья после этого обрабатывают абразивным кругом с зернистостью 36…46. Профиль обработанных зубьев проверяется специальными шаблонами.
Износ и выкрошивание торцов зубьев шестерни из сталей марок 40Х и 45Х устраняют, наплавляя газовой горелкой в нейтральном пламени проволоку из стали марки 40Х. Наплавку можно производить также электродуговой сваркой, используя проволоку клапанной пружины со специальными обмазками.
Наварку сталинитом сильно изношенных зубьев необходимо вести методом комбинированного слоя. Слой шихты сталинита при этом насыпают в месте наварки и расплавляют металлическим электродом или же применяют металлические стержни с обмазкой сталинита.
При сборке зубчатых колес следует исходить из предусмотренных стандартами норм точности: кинематической, контакта зубьев и гарантированного зазора.
Для нормальной работы зубчатых колес должны быть соблюдены два основных условия: линия касания зубьев должна находиться на начальной окружности обоих колес; переход от одного зуба к другому должен быть плавным, без толчков и рывков. Зазор между зубьями имеет большое значение для правильной работы зубчатых колес. При сборке цилиндрических шестерен величину бокового зазора между зубьями измеряют щупом или прокаткой свинцовой пластинки, пропускаемой между зубьями, которая после этого измеряется. Замер величины бокового зазора производят между тремя парами сопряженных зубьев в трех местах под углом 120° и принимают наибольший зазор.
Нормальный боковой зазор между зубьями шестеренчатых передач выбирается по техническим условиям на сборку. Для строительных машин боковой зазор находится в пределах 0,06...0,1 модуля. Радиальный зазор должен быть не менее 0,16…0,20 модуля.
|
|
Типы сооружений для обработки осадков: Септиками называются сооружения, в которых одновременно происходят осветление сточной жидкости...
История развития хранилищ для нефти: Первые склады нефти появились в XVII веке. Они представляли собой землянные ямы-амбара глубиной 4…5 м...
Типы оградительных сооружений в морском порту: По расположению оградительных сооружений в плане различают волноломы, обе оконечности...
Двойное оплодотворение у цветковых растений: Оплодотворение - это процесс слияния мужской и женской половых клеток с образованием зиготы...
© cyberpedia.su 2017-2024 - Не является автором материалов. Исключительное право сохранено за автором текста.
Если вы не хотите, чтобы данный материал был у нас на сайте, перейдите по ссылке: Нарушение авторских прав. Мы поможем в написании вашей работы!